Buying Guide: Gravity Roller Conveyor Parts and Accessories
Gravity roller conveyors are a staple in industrial settings, where they facilitate the movement of goods across factories, warehouses, and distribution centers with simplicity and efficiency. These conveyors operate without the use of power, relying on gravity or manual force to propel items along rollers. The effectiveness and longevity of these systems heavily depend on the quality and suitability of specific gravity roller conveyor parts. Selecting the right parts not only ensures optimal functionality but also minimizes downtime caused by maintenance issues. It is crucial for businesses to invest in compatible components that align with their system’s specifications to maintain the smooth operation of their material handling processes. This introduction underscores the importance of understanding the integral parts that make up gravity roller conveyors and highlights the need for careful selection to enhance and preserve conveyor efficiency.
Comprehensive Parts List for Gravity Roller Conveyors
When assembling or maintaining a gravity roller conveyor, it is crucial to have a comprehensive understanding of the various components that make up the system. This detailed guide will help you identify and utilize the essential gravity roller conveyor parts to ensure your conveyor operates efficiently and effectively.
Identifying Essential Components: Key Gravity Roller Conveyor Parts
A gravity roller conveyor simplifies the process of moving goods across an area with minimal effort. The efficiency of this system depends heavily on its individual components. Here’s a breakdown of the crucial gravity roller conveyor parts:
- Rollers: These are the most conspicuous parts of the conveyor system. Rollers are cylindrical tubes that rotate freely on their axis and are mounted within the conveyor frame. They are designed to support and transport goods from one point to another with minimal friction. Rollers can vary in size, material, and coating, depending on their application.
- Frames: The frame provides the structure and support for the rollers. It is typically made from steel, aluminum, or heavy-duty plastics. The choice of material depends on the desired strength and environmental conditions the conveyor will be exposed to.
- Supports: Conveyor supports hold the frame up and can be adjusted for height to create the necessary gravity flow. They are essential for maintaining the integrity and alignment of the roller system.
- End Stops: These components are used to prevent goods from falling off the conveyor at either end. End stops can be simple plates or complex sensors depending on the operation’s automation level.
- Shafts and Bearings: Shafts connect the rollers to the frame, allowing smooth rotation. Bearings reduce rotational friction and support axial and radial loads.
- Drive Belts and Sprockets (if applicable): Although not required in a non-powered setup, these are used in powered roller systems to move rollers according to the desired speed and direction.
- Load Guides: Guides are used to ensure materials stay on track as they move along the conveyor and can be adjusted according to the width of the materials being transported.
Parts Catalog Overview: Interpreting Gravity Roller Conveyor Parts Specifications
Understanding how to read and interpret parts catalogs is essential for selecting the right components for your gravity roller conveyor. Catalogs typically provide detailed specifications, including:
- Material Descriptions: Information on the construction materials used for different parts such as steel, aluminum, or thermoplastics.
- Dimensions: Detailed measurements of parts, which are critical for ensuring compatibility and efficient operation.
- Load Capacities: Each part’s weight handling capability, which is crucial for designing a system that meets operational demands without risking structural integrity.
- Part Numbers and Images: Helpful for identifying specific parts and understanding their appearance and installation process.
When choosing parts from a catalog, consider the environment in which the conveyor will operate (e.g., temperature, exposure to chemicals) and the nature of the materials it will transport (e.g., weight, size, abrasiveness). These factors significantly influence the selection of appropriate parts to enhance performance and durability.
By familiarizing yourself with these gravity roller conveyor parts and how to interpret a parts catalog, you can effectively plan, assemble, or maintain your conveyor system. This knowledge ensures a reliable setup that can handle your logistical needs with ease.
Finding Gravity Roller Conveyor Parts
Ensuring that you have a reliable source for gravity roller conveyor parts is essential for maintaining the efficiency and reliability of your conveyor system. Whether you need to quickly replace a roller, frame, or any specific part, knowing where to find the right components can save both time and expense. Below, explore effective strategies for locating parts suppliers both locally and online.
Locating Parts Suppliers Near Me: Tips for Finding Local Gravity Roller Conveyor Parts
Finding local suppliers for gravity roller conveyor parts can drastically reduce downtime. Here are 8 tips to help you find reliable parts suppliers in your area:
- Use Search Engines: Simply entering “gravity roller conveyor parts near me” into search engines will provide a list of nearby suppliers. Look for companies with good ratings and reviews.
- Industry Directories: Utilize directories such as ThomasNet or IndustryNet to find suppliers that specialize in conveyor systems and components. These directories often offer information about the types of parts a company stocks.
- Trade Shows and Expos: Attend industry trade shows and expos. These events provide a great opportunity to meet suppliers, compare products, and establish relationships.
- Local Industrial Parks: Often, suppliers and distributors are located in industrial parks. Visiting these areas can lead to direct encounters with suppliers who can provide quick delivery times.
- Referrals: Ask for referrals from other businesses that use gravity roller conveyors. Industry contacts can provide trusted recommendations.
- Hardware Stores: While not specialized, large hardware stores or industrial hardware suppliers might carry basic conveyor components or be able to order specific parts for you.
- Chamber of Commerce: Your local chamber of commerce can be a valuable resource for identifying nearby industrial suppliers.
- Service Companies: Companies that service conveyors often have parts on hand or can order them for you. They can be a quick and reliable resource.
Online Catalogs and Stores: Top Resources for Gravity Roller Conveyor Parts
For a more comprehensive range of options, online catalogs and stores are ideal for finding gravity roller conveyor parts. Here are 6 recommendations where you can browse extensive catalogs for all your conveyor needs:
- McMaster-Carr: Offers a wide array of conveyor parts including rollers, frames, and hardware. Their website is user-friendly and provides detailed specifications and CAD models.
- Grainger: Known for industrial and maintenance supplies, Grainger has a comprehensive list of conveyor parts that cover various specifications and requirements.
- Amazon Business: For quick purchases and reviews, Amazon Business offers a range of gravity roller conveyor parts with user reviews and ratings to help make informed decisions.
- eBay Business & Industrial: A great source for both new and used conveyor parts, eBay offers competitive pricing and a wide selection from various sellers around the world.
- Direct Manufacturer Websites: Many manufacturers sell directly from their websites and provide support and resources to help you choose the right parts. Websites like Hytrol Conveyor Accessories and Conveyor Dynamics offer detailed product catalogs.
- AutomationDirect: They provide a range of mechanical components including those for conveyors. Their site offers good technical information, making it easier to select the right parts.
By utilizing these local and online resources, you can ensure that you find the best gravity roller conveyor parts quickly and efficiently, minimizing downtime and maintaining productivity in your operations. Whether sourcing locally for speed or online for a comprehensive selection, these strategies will guide you to the best suppliers for your needs.
Purchasing Gravity Roller Conveyor Parts
The process of purchasing gravity roller conveyor parts involves critical decisions that affect both the performance and longevity of your conveyor system. Deciding between new and used parts, as well as understanding what to look for in terms of compatibility and quality, are pivotal steps. This section provides insights into making informed purchasing decisions for gravity roller conveyor parts.
Parts for Sale: Buying New vs. Used Gravity Roller Conveyor Parts
When it comes to purchasing gravity roller conveyor parts, one of the first decisions is whether to buy new or used components. Both options have their advantages and considerations:
Buying New Parts:
- Warranty and Support: New parts often come with a manufacturer’s warranty and support services.
- Latest Technology: Opting for new parts ensures access to the latest technology and improvements in efficiency and safety.
- Longevity: New components are likely to last longer, providing better long-term value.
- Customization: Manufacturers may offer customization options for new parts to meet specific operational needs.
Buying Used Parts:
- Cost-Effective: Used parts are typically more affordable, making them a good option for budget constraints.
- Eco-Friendly: Purchasing used parts is a form of recycling, which contributes to environmental sustainability.
- Availability: In some cases, used parts may be more readily available than new ones, especially for discontinued models or brands.
- Inspection and History: When buying used, inquire about the history and condition of the part, and if possible, inspect it for wear and tear.
Guide to Choosing the Right Parts: Ensuring Compatibility and Quality
Selecting the right gravity roller conveyor parts requires careful consideration of several factors to ensure compatibility with your existing system and uphold quality standards. Here are 7 factors to consider:
- Compatibility: Ensure the parts are compatible with your conveyor’s make and model. Incompatibility can lead to operational failures and safety risks.
- Specifications: Check the specifications, including size, material, and load capacity, to ensure they meet your operational needs.
- Quality and Material: Look for parts made of durable materials suited for your specific usage conditions, such as moisture, temperature, and load weight.
- Manufacturer Reputation: Purchase parts from reputable manufacturers known for quality and reliability.
- Certifications: Parts that have been certified or meet industry standards offer assurances of quality and safety.
- Maintenance and Support: Consider the availability of maintenance services and support from the supplier or manufacturer.
- Return Policy: Understand the return policy in case the parts do not meet your expectations or are incompatible with your system.
By carefully evaluating these factors, you can make informed decisions when purchasing gravity roller conveyor parts. Balancing the advantages of new versus used parts with a thorough consideration of compatibility and quality factors will ensure that your conveyor system operates efficiently and safely, providing the best possible return on investment.
Specialized Gravity Roller Conveyor Parts and Their Applications
In addition to standard components, there are specialized gravity roller conveyor parts designed to meet the specific needs of various industrial applications. Understanding these specialized parts and their benefits is crucial for optimizing your conveyor system for specific, challenging tasks. This section covers heavy-duty parts and narrow/custom rollers, which are essential for certain operational environments.
Heavy Duty Parts: Enhanced Performance for Rigorous Use
Heavy duty parts are designed to withstand higher loads and more intensive use compared to standard gravity roller conveyor parts. These components are crucial for industries such as mining, automotive, and other heavy manufacturing sectors where durability and reliability are paramount. Here are 9 benefits of using heavy duty parts in your conveyor system:
- Increased Load Capacity: Designed to handle heavier loads without deformation or failure.
- Enhanced Durability: Built with stronger materials that can withstand harsh conditions and abrasive materials.
- Longer Lifespan: The robust construction significantly extends the life of the conveyor parts.
- Reduced Downtime: Their resilience leads to fewer breakdowns, reducing downtime and maintenance costs.
- Improved Safety: Sturdy parts are less likely to fail, thus enhancing the safety of the operation.
- Versatility: Can be used in a variety of environments, from dry to moist, without rusting or corroding.
- Cost-Effectiveness: Although more expensive upfront, their longevity and reliability provide better value over time.
- High Performance: Maintains performance levels under greater strains and speeds.
- Customizability: Many manufacturers offer customization options for heavy-duty parts to meet specific operational requirements.
Narrow and Custom Rollers: Specialized Solutions for Unique Setups
Narrow and custom rollers are specialized gravity roller conveyor parts tailored to fit unique and restricted spaces within production lines. These rollers are particularly useful in applications requiring precise handling and positioning of small or delicate items. Here’s how these specialized rollers are used:
- Space Efficiency: Narrow rollers are ideal for systems installed in limited spaces where traditional rollers would not fit.
- Precision Handling: Their reduced size allows for more precise control of the items being conveyed, which is crucial for delicate or intricately shaped products.
- Custom Shapes and Sizes: Custom rollers can be designed to accommodate non-standard sizes and shapes, providing solutions for unique operational challenges.
- Integration Flexibility: These rollers can be easily integrated into existing conveyor systems to enhance their functionality or to replace worn-out parts with better-fitting alternatives.
- Specialized Materials: Depending on the application, narrow and custom rollers can be made from a variety of materials, including plastics, hardened steel, or coated surfaces to handle sensitive materials gently.
Utilizing these specialized gravity roller conveyor parts—whether heavy duty for high-load capacities or narrow/custom for specific applications—ensures that your conveyor system is optimized for both efficiency and effectiveness in challenging industrial environments. By selecting the appropriate parts, you can enhance operational throughput, reduce maintenance costs, and achieve superior product handling.
Enhancing Conveyor Efficiency with Gravity Roller Conveyor Parts
The Role of Gravity Roller Conveyor Parts in Upgrading to Powered Systems
The transition from traditional gravity roller conveyors to powered roller conveyors represents a significant leap in industrial efficiency and productivity. This transformation revolves around the innovative use of gravity roller conveyor parts, not only as components of a passive material handling system but also as integral parts of an upgraded, powered conveyor system.
Integrating Powered Roller Conveyors:
Powered roller conveyors stand in contrast to their gravity-fed counterparts by introducing motors and controls into the system. This fundamental difference allows for a more controlled and consistent movement of goods across the production floor. Unlike gravity roller conveyors, which rely on a slight decline and gravity to move items, powered roller conveyors use electricity and mechanical power to transport goods. This transition brings several advantages:
- Consistent Flow: Powered conveyors provide a steady, controllable flow of materials, eliminating the stop-and-go movement often seen in gravity systems.
- Increased Efficiency: They are capable of moving products faster and with less effort, significantly increasing throughput.
- Versatility: Powered systems can easily transport a wide variety of goods, including those that are too heavy or too light to move effectively on a gravity conveyor.
- Improved Ergonomics: By automating the movement of goods, powered conveyors reduce the physical strain on workers, leading to a safer and more efficient workplace.
The integration of gravity roller conveyor parts into powered systems is not just about replacing a non-powered roller with a powered one. It involves a comprehensive approach to redesigning the material handling process, incorporating sensors, controls, and software to manage the flow of goods more effectively.
Conversion Kits and Upgrades:
For facilities looking to enhance their existing gravity roller conveyor infrastructure, conversion kits and upgrades offer a practical solution. These kits typically include powered roller assemblies, motors, control units, and sometimes, software enhancements. By integrating these powered components, a traditional gravity conveyor can be transformed into a more efficient powered system.
The process of upgrading involves several steps:
- Assessment: Evaluating the existing gravity conveyor setup to determine compatibility with powered parts.
- Selection: Choosing the appropriate gravity roller conveyor parts and powered components based on the specific needs of the operation.
- Installation: Retrofitting the existing conveyor with powered rollers, motors, and control systems.
- Testing: Ensuring that the upgraded conveyor operates smoothly and meets the desired efficiency improvements.
This upgrade not only extends the life of existing equipment but also introduces a level of control and efficiency previously unattainable with gravity systems alone. Facilities that undergo this transformation can expect a significant boost in productivity, with a reduced need for manual intervention and an increased capacity for handling a diverse range of products.
The strategic integration of gravity roller conveyor parts into powered systems and the availability of conversion kits for upgrading existing conveyors are pivotal in enhancing conveyor efficiency. By embracing these powered components, industries can achieve a more dynamic, flexible, and efficient material handling process, paving the way for increased productivity and operational excellence.
Cost Considerations and Budget Planning for Gravity Roller Conveyor Parts
Effectively managing costs is crucial when purchasing gravity roller conveyor parts, whether upgrading an existing system or building a new one from scratch. This section provides detailed guidance on estimating costs and planning your budget, along with strategies for comparing prices and assessing the value of parts from different suppliers.
Estimating Costs for Gravity Roller Conveyor Parts
When planning to purchase gravity roller conveyor parts, the first step is to develop a clear understanding of the potential costs involved. Here’s how to effectively estimate these costs and manage your budget:
- Identify Required Parts: List all the components you need, including rollers, frames, supports, and any specialized parts like motorized rollers for upgrades.
- Quantify Parts: Determine the quantity of each part required to avoid under or over purchasing, which can lead to unnecessary expenses.
- Average Prices: Research the average costs of these parts. Prices can vary based on material (steel, plastic), size, and whether the part is standard or custom-made.
- Supplier Quotes: Obtain quotes from multiple suppliers for the parts you need. Be sure to include shipping costs, taxes, and any other fees in your calculations.
- Installation Costs: If you are not installing the parts yourself, include the cost of professional services for installation.
- Contingency Budget: Always include a contingency budget of about 10-15% more than your estimated costs to cover unexpected expenses.
- Long-Term Costs: Consider the long-term operational costs involved, such as maintenance and potential downtime, which can affect your overall budgeting.
- Financing Options: Explore financing options if upfront costs are significant. Some suppliers offer leasing arrangements or payment plans that can spread out the expense.
Price Comparison and Value Analysis: Evaluating Gravity Roller Conveyor Parts
Comparing prices and evaluating the value of gravity roller conveyor parts require careful consideration. Here are 10 tips to help you make the best choices when comparing options from different suppliers:
- Compare Identical Parts: Ensure that the specifications of the parts from different suppliers are exactly the same when making price comparisons.
- Bulk Discounts: Ask suppliers about discounts for bulk purchases. Buying more may significantly lower the price per unit.
- Quality vs. Price: Higher-priced parts are not always better. Evaluate the quality of materials and construction when comparing prices.
- Supplier Reputation: Consider the supplier’s reputation for quality and service. A lower price might result in poorer quality or customer service.
- Warranty Offers: Look for parts that come with a warranty. A good warranty can provide value that justifies a higher upfront cost.
- Check Reviews: Read customer reviews and case studies to see how the parts have performed for other buyers.
- Total Cost of Ownership: Include maintenance, repair, and operational efficiency in your value analysis.
- Return Policy: Understand the return policy. Being able to return ineffective parts can save money.
- Compatibility: Ensure parts are fully compatible with your existing system to avoid additional costs for modifications or adapters.
- Long-Term Benefits: Consider how the parts will contribute to system efficiency and productivity in the long term, potentially offering greater value through cost savings.
By thoroughly estimating costs and conducting detailed price and value comparisons, you can effectively manage your budget and ensure that you acquire high-quality gravity roller conveyor parts that offer the best value for your investment. This strategic approach not only helps in maintaining the efficiency of your conveyor system but also controls costs, enhancing overall operational effectiveness.
Maintenance and Installation Tips for Gravity Roller Conveyor Parts
Ensuring the longevity and efficiency of your material handling system requires meticulous attention to the maintenance and correct installation of gravity roller conveyor parts. This section delves into practical tips and best practices for both these critical aspects, ensuring your gravity roller conveyors operate at peak efficiency with minimal downtime.
Proper Installation of Gravity Roller Conveyor Parts
The correct installation of gravity roller conveyor parts is foundational to the operational efficiency and safety of the conveyor system. A step-by-step guide ensures that each component is installed correctly, reducing the risk of malfunction or accidents.
- Preparation: Before beginning the installation, ensure all parts are present and inspect them for any damage. Lay out the components according to the installation plan.
- Frame Assembly: Start with the frame, ensuring it is level and square. This serves as the backbone of the conveyor, so precision here is crucial.
- Roller Placement: Install the rollers into the frame. Make sure they are evenly spaced and securely fastened. Each roller should spin freely without wobbling.
- Drive Assembly (if applicable): For sections of the conveyor that require a drive mechanism, carefully install and align the drive units according to the manufacturer’s instructions.
- Testing: After the assembly, manually test the rollers and drive units (if any) for smooth operation. This is also the time to adjust the tension and alignment if necessary.
Maintenance Best Practices for Gravity Roller Conveyor Parts
Routine maintenance is vital to extend the life and maintain the efficiency of gravity roller conveyors. Here are eight best practices:
- Regular Inspections: Conduct thorough inspections of the conveyor and its parts periodically to identify wear and tear or any potential issues.
- Lubrication: Properly lubricate moving parts according to the manufacturer’s recommendations to ensure smooth operation and prevent rust or corrosion.
- Cleaning: Keep the conveyor clean from debris and dust that can accumulate on rollers and hinder their movement or cause premature wear.
- Alignment Checks: Regularly check and adjust the alignment of the conveyor and rollers to prevent uneven wear and ensure efficient operation.
- Tension Adjustments: If your conveyor uses a belt, check the tension regularly and adjust as needed to prevent slippage or excessive wear.
- Replacement of Worn Parts: Replace any parts that show signs of wear or damage promptly to avoid further damage to the conveyor system.
- Documentation: Keep detailed records of inspections, maintenance activities, and part replacements to track the conveyor’s condition over time.
- Training: Ensure that staff responsible for maintenance are properly trained in the specifics of gravity roller conveyor parts and safety practices.
Adhering to these installation and maintenance tips can significantly impact the performance and lifespan of your gravity roller conveyor system. Proper installation ensures that the system is set up for success from the beginning, while a commitment to regular maintenance can prevent minor issues from becoming major problems, ensuring smooth and efficient operation day after day.
FAQs about Gravity Roller Conveyor Parts
A roller conveyor is a versatile conveyor system based on rollers mounted within a frame. In general, these conveyors are used to move items across a horizontal pathway with minimal effort. Here are the main components:
Rollers: These are the cylindrical parts that objects slide over. They are spaced evenly across the length of the conveyor and can be made from metal, plastic, or rubber, depending on the application.
Frame: The frame supports the rollers and is typically constructed from steel or aluminum for durability. Frames must be strong enough to handle the load capacity of the items being transported.
Bearings: Bearings allow the rollers to spin freely, reducing friction between the rollers and the frame, which helps in smoother rolling of the conveyor.
Shafts: Shafts are mounted within the bearings and serve as the axles for the rollers.
Drive Belt/Chain: Some roller conveyors are powered by a belt or chain that connects to motors, which move the rollers and thus transport items. In gravity conveyors, this component is absent as motion is driven by gravity.
Motor (for powered conveyors): Provides the necessary power to turn the rollers and move the items along the conveyor. The motor’s power output needs to match the conveyor’s load and speed requirements.
Understanding these components is crucial for optimizing the efficiency and maintenance of a roller conveyor system.
A gravity conveyor roller is a part of a gravity conveyor system, which uses the force of gravity to move products across flat or slightly inclined paths. Unlike powered conveyors, gravity conveyors do not require electrical power, making them a cost-effective and energy-saving option for material handling. Items are manually pushed along these rollers or moved by the force of gravity in a downward direction. The simplicity of its design makes it not only affordable but also easy to install and maintain. Gravity conveyor rollers are popular in warehouses, manufacturing plants, and distribution centers where products need to be moved short distances without the need for automation.
A conveyor system comprises various components designed to transport materials from one spot to another efficiently. The primary components include:
Belt or Rollers: The medium on which the materials are carried. Rollers are used in roller conveyor systems, while a continuous belt is used in belt conveyor systems.
Pulleys and Motors: For powered systems, pulleys are used to drive the belt, with motors supplying the power.
Frames: These support the system and can range from metal structures for heavy-duty industrial use to lighter materials for less intensive applications.
Controls: Controls can range from simple on/off switches to complex programmable logic controllers (PLCs) that manage the speed and direction of the system.
Loading and Unloading Points: Specific areas designed for efficient loading of materials onto the conveyor and unloading at the destination.
Safety Features: Emergency stops, guards, and other safety features are essential to protect operators and the materials being transported.
Understanding the components of a conveyor system is crucial for designing an effective material handling solution tailored to specific operational needs.
The size of gravity conveyor rollers can vary significantly based on the application and the materials they are intended to transport. Common diameters for these rollers range from as small as ¾ inch to as large as 3.5 inches or more for heavy-duty applications. The length of the rollers is also variable, depending on the width of the conveyor system they are part of; it’s not uncommon to see lengths ranging from a few inches to over 10 feet to accommodate various product sizes.
The roller material and size are chosen based on the weight and type of goods they will carry, the environment in which they operate (e.g., corrosive, temperature extremes), and the speed at which the system operates. Smaller rollers are typically used for lightweight items and packages, while larger, durable rollers are used for heavier loads and industrial applications. Understanding the specific requirements of your operation is essential when selecting the right size and type of gravity conveyor rollers.
Last Updated on May 29, 2024 by Jordan Smith
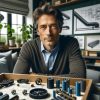
Jordan Smith, a seasoned professional with over 20 years of experience in the conveyor system industry. Jordan’s expertise lies in providing comprehensive solutions for conveyor rollers, belts, and accessories, catering to a wide range of industrial needs. From initial design and configuration to installation and meticulous troubleshooting, Jordan is adept at handling all aspects of conveyor system management. Whether you’re looking to upgrade your production line with efficient conveyor belts, require custom conveyor rollers for specific operations, or need expert advice on selecting the right conveyor accessories for your facility, Jordan is your reliable consultant. For any inquiries or assistance with conveyor system optimization, Jordan is available to share his wealth of knowledge and experience. Feel free to reach out at any time for professional guidance on all matters related to conveyor rollers, belts, and accessories.