Enhance Productivity: Benefits of Gravity Roller Conveyor Rental
Gravity roller conveyors are an indispensable tool in the material handling industry, offering a simple yet effective means to move goods across short to medium distances within a facility. These conveyors utilize the force of gravity to propel items forward, making them an energy-efficient option for transporting products. They are widely used across various industries, including manufacturing, distribution, and packaging, to streamline operations and enhance workflow efficiency. Given their versatility and utility, gravity roller conveyor rental services have become increasingly popular among businesses looking for temporary material handling solutions. Renting these conveyors provides a flexible and cost-effective alternative to purchasing, allowing companies to adapt to seasonal peaks, project-based demands, or testing phases without committing to a permanent investment.
Whhat Is Gravity Roller Conveyor Rental
Gravity roller conveyors are a fundamental component in the material handling sector, designed to facilitate the movement of goods across a defined path using the force of gravity. These systems consist of rollers mounted on a frame, where items are manually pushed along or simply move due to a slight incline. Here, we delve into the mechanics and benefits of gravity roller conveyor rental, providing a comprehensive insight into their functionality and advantages.
How Gravity Roller Conveyors Work
Gravity roller conveyors harness the simple yet effective force of gravity to move items across a designated area. This ingenious use of natural force allows for the transportation of goods with minimal effort and complexity. Here’s a closer look at the mechanics behind this system:
- Simple Mechanism: They operate on the principle of gravity, where the conveyor is slightly inclined, allowing goods to move from a higher to a lower point without the need for power.
- Rollers: The conveyor’s surface is made up of rollers, which are spaced at regular intervals to support the goods being transported.
- Manual Assistance: In flat setups, operators can manually push items along the conveyor, requiring minimal effort due to the rollers’ smooth movement.
- Adjustable Incline: The angle of incline can be adjusted to control the speed of movement, accommodating different types of goods and operational requirements.
- Modular Design: Many systems are modular, allowing for easy expansion or reconfiguration according to the specific needs of a business.
- Load Capacity: Designed to handle a wide range of load capacities, from lightweight packages to heavier items, making them versatile for various applications.
- Speed Control: Although they rely on gravity, the speed at which items move can be controlled using breaks or stops installed along the conveyor.
- Integration: Easily integrates with other conveyor systems or material handling equipment, creating a cohesive and efficient workflow.
Advantages of Using Gravity Roller Conveyors for Material Handling
Opting for gravity roller conveyors in material handling operations brings a multitude of benefits. Beyond their basic functionality, these systems offer enhancements in efficiency, cost savings, and operational flexibility. Let’s explore the key advantages they provide:
- Cost-Effectiveness: Eliminates the need for power, reducing operational costs significantly.
- Ease of Installation: Their simple design allows for quick and easy installation, minimizing downtime.
- Low Maintenance: Requires minimal maintenance due to fewer moving parts and the absence of complex machinery.
- Flexibility: Can be used in a variety of settings and applications, from warehouses to retail backrooms.
- Efficiency: Improves the efficiency of material handling processes, allowing for faster movement of goods and streamlined operations.
- Safety: Reduces the risk of injury as manual handling of goods is minimized, and the systems are generally very safe to operate.
- Scalability: The modular nature allows businesses to scale their conveyor system up or down as needed, making gravity roller conveyor rental an ideal solution for temporary or changing needs.
- Environmental Impact: Being a non-powered system, it has a lower environmental impact compared to motorized conveyors, aligning with sustainability goals.
Incorporating gravity roller conveyor rental into your material handling strategy offers a blend of efficiency, cost savings, and adaptability, making it a go-to solution for businesses looking to optimize their operations without the hefty investment in permanent installations.
The Comprehensive Benefits of Gravity Roller Conveyor Rental
In the dynamic landscape of modern industry, the agility to adapt to changing demands and operational scales is paramount. Gravity roller conveyor rental offers a versatile, cost-effective, and operationally flexible solution that caters to a wide array of business needs. This section delves into the multifaceted benefits of renting gravity roller conveyors, highlighting their strategic value across various sectors.
Financial and Operational Flexibility: The Core of Gravity Roller Conveyor Rental
The decision to rent a gravity roller conveyor system is underpinned by the significant financial and operational flexibility it offers, making it an attractive option for businesses navigating the complexities of fluctuating market demands and project-specific requirements. This flexibility is not just a matter of convenience but a strategic tool that can lead to substantial cost savings and operational efficiencies.
Cost-Effectiveness for Short-Term Needs: The most immediate benefit of gravity roller conveyor rental is its cost-effectiveness, particularly for short-term applications. Renting eliminates the large upfront investment required for purchasing new equipment, which can be prohibitive for many businesses. This financial flexibility allows companies to preserve their capital for other areas of their operations that may yield a higher return on investment. Moreover, the rental model avoids the long-term financial commitments and the depreciation costs associated with owning equipment. Businesses can also save on maintenance, repair, and storage costs, as these are typically covered by the rental provider, further reducing the total cost of operation.
Adaptability to Budget Constraints: For startups and SMEs, budget constraints are a constant reality. The rental of gravity roller conveyors offers a predictable and manageable expense, fitting neatly into short-term budgets and financial planning. This adaptability ensures that businesses can still benefit from efficient material handling solutions without compromising their financial health.
Operational Scalability: Beyond the financial aspects, the operational flexibility provided by renting gravity roller conveyors is invaluable. Businesses can quickly scale their material handling capacity up or down in response to seasonal peaks, project demands, or unexpected changes in production volume. This scalability ensures that operations remain efficient and responsive to the needs of the business without the need for permanent or costly infrastructure changes.
Responsive to Market and Project Demands: In industries where demand can be unpredictable or subject to significant fluctuations, the ability to adjust operational capacity quickly is crucial. Gravity roller conveyor rental allows businesses to respond to these changes with agility, ensuring they can meet customer demands without the risk of over-investment in permanent equipment. This responsiveness is particularly beneficial for businesses that experience seasonal surges, engage in project-based work, or need to test new operational strategies without committing to long-term investments.
Strategic Asset Management: Renting also enables businesses to manage their assets more strategically. By choosing rental solutions, companies can avoid the pitfalls of equipment obsolescence and ensure they are always using the most up-to-date and efficient technology available. This approach not only maximizes operational efficiency but also supports continuous improvement and innovation within the company’s logistics and material handling strategies.
The financial and operational flexibility offered by gravity roller conveyor rental provides businesses with a strategic advantage. It allows for cost-effective management of material handling needs, adaptable to the ever-changing demands of the market and individual projects, without the significant capital outlay and long-term commitments associated with purchasing equipment. This flexibility is a cornerstone of modern business operations, enabling companies to remain competitive and agile in a fast-paced and unpredictable market environment.
Industry-Specific Applications
Gravity roller conveyor rentals find their utility in a broad spectrum of industries, each benefiting from the adaptability and cost efficiency of temporary conveyor solutions:
- E-Commerce and Retail: Addressing the logistical challenges of peak shopping seasons, rentals provide the necessary capacity to manage increased order volumes efficiently.
- Manufacturing: Supporting temporary production lines or accommodating short-term increases in demand, rentals offer a solution without the need for permanent facility changes.
- Agriculture: Facilitating the movement of produce during peak harvest times, rentals enhance efficiency without the commitment to long-term equipment.
- Construction and Demolition: Offering a practical solution for moving materials in variable site conditions, rentals adapt to the project’s duration and specific needs.
- Event Management: Simplifying logistics for temporary events, rentals ensure smooth setup and breakdown processes.
- Warehousing and Distribution: Providing scalability during inventory peaks or operational reconfigurations, rentals improve handling efficiency temporarily.
Additional Strategic Advantages
- Risk Mitigation: Rentals offer a low-risk option for businesses to address their immediate material handling needs without the commitment to a permanent solution, allowing for future flexibility.
- Access to Latest Technology: Rental agreements enable businesses to utilize the latest in conveyor technology, ensuring operational efficiency with the most up-to-date equipment without the concerns of obsolescence.
- Customized Solutions for Unique Projects: The flexibility of rental options allows for tailored solutions that fit the specific requirements of unique projects, ensuring optimal efficiency.
- Sustainability: By choosing rentals, companies can align with environmental sustainability goals through shared resource utilization, reducing the need for new equipment production and minimizing waste.
Gravity roller conveyor rental presents a compelling proposition for businesses aiming to enhance operational efficiency, adapt to fluctuating demands, and manage financial resources effectively. This flexible, cost-effective solution supports a wide range of industries in meeting their short-term and project-based material handling needs, ensuring peak operational performance without the long-term commitment and capital expenditure of purchasing.
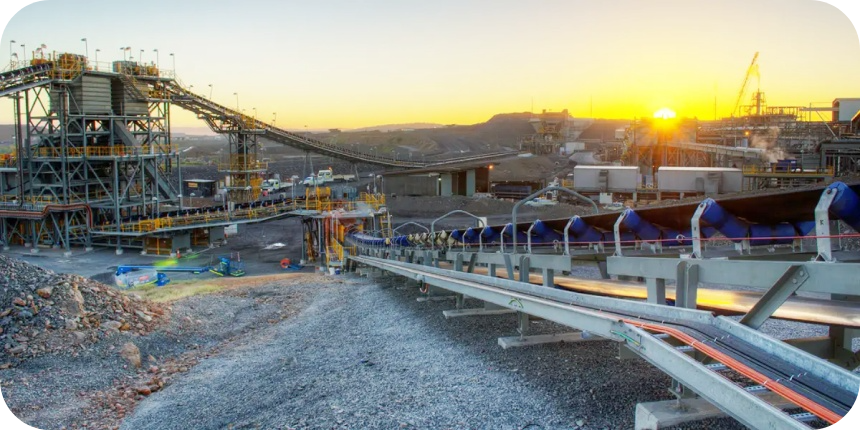
To Explore the Diversity of Gravity Roller Conveyor Rental Options
The versatility of gravity roller conveyor rental options caters to a wide range of industry needs, offering both standard and specialized solutions to enhance operational efficiency. Understanding the types of rentals available, including the distinctions between used and new equipment, as well as the specialized options, is crucial for businesses aiming to optimize their material handling processes. This section delves into the various gravity roller conveyor rental possibilities and outlines considerations for selecting the most suitable type for your specific requirements.
Used vs. New Gravity Roller Conveyor Rentals
When considering gravity roller conveyor rental, businesses have the option to choose between used and new equipment. Each choice comes with its own set of advantages and considerations:
Specialized Gravity Roller Conveyor Rental Options
Beyond the basic distinction between used and new, there are specialized gravity roller conveyor rental options designed to meet specific operational needs:
- Portable Conveyor Belts: Ideal for dynamic work environments requiring mobility and flexibility in material handling.
- Roofing Conveyor Belts: Specifically designed for the safe and efficient transport of roofing materials to elevated work sites.
- Construction Conveyor Belts: Built to withstand rugged conditions, these conveyors are perfect for moving construction materials across sites.
- Expandable and Flexible Conveyors: These can be extended, curved, and manipulated to fit the specific layout of a workspace, offering versatility in setup.
- Heavy-Duty Conveyors: Engineered for handling heavy loads, suitable for industrial environments with demanding material handling needs.
Considerations for Choosing the Right Type of Conveyor
Selecting the appropriate gravity roller conveyor rental involves several key considerations to ensure the solution aligns with operational requirements:
- Project Duration: Short-term projects may benefit more from used rentals, while new equipment may be better for longer-term needs.
- Budget Constraints: Assess financial flexibility to determine if a more cost-effective used option or a higher-cost new option is feasible.
- Operational Environment: Consider the work environment (indoor vs. outdoor, temperature, terrain) to select a conveyor that can withstand specific conditions.
- Load Requirements: Evaluate the weight and size of materials to be handled to ensure the conveyor can accommodate these loads efficiently.
- Mobility Needs: For operations requiring frequent changes in material handling routes, portable or flexible conveyors may be the ideal choice.
- Space Constraints: Measure the available space to ensure the conveyor fits and operates effectively within the designated area.
- Integration with Existing Systems: Consider how the rental will integrate with current material handling systems for seamless operation.
- Sustainability Goals: Align the choice with sustainability objectives, considering the environmental impact of rental versus purchase.
- Future Scalability: Anticipate future needs to choose a conveyor option that can grow or adapt as the business evolves.
The decision to opt for a gravity roller conveyor rental involves careful consideration of the specific needs of your operation, including the choice between used and new equipment and the selection of specialized conveyor solutions. By thoroughly evaluating these considerations, businesses can ensure they select the most appropriate, efficient, and cost-effective material handling solution for their unique requirements.
To Locate Gravity Roller Conveyor Rental Near You
Finding the right gravity roller conveyor rental for your business’s specific needs can seem daunting, especially when trying to locate services nearby. However, with the right approach and resources, you can easily find a rental service that fits your requirements. This section provides comprehensive tips on locating gravity roller conveyor rental services, highlights the role of major home improvement stores, and lists online resources and directories to aid in your search.
Tips on Locating Rental Services
- Use Specific Search Terms: When searching online, use specific phrases like “gravity roller conveyor rental near me” or “conveyor rentals near me” to filter results to those most relevant to your location and needs.
- Local Business Directories: Check local business directories, both online and in print, for listings of equipment rental companies that offer conveyor systems.
- Industry Forums and Websites: Participate in forums and visit websites related to material handling and logistics. Members often share recommendations for rental services based on their experiences.
- Trade Associations: Contact trade associations related to warehousing, logistics, and manufacturing. They can often provide referrals to reputable rental companies.
- Social Media Groups: Join social media groups and communities focused on industrial equipment rental or specific industries like construction, agriculture, or manufacturing. These can be great places to ask for recommendations.
- Ask for Referrals: Network with peers in your industry for personal referrals. Often, the best recommendations come from those who have had direct experience with rental services.
- Local Trade Shows and Expos: Attend trade shows and expos related to material handling, construction, and logistics. Many rental companies exhibit at these events, offering a direct way to gather information and make contacts.
- Consult with Suppliers: If you’re already working with suppliers for other equipment, ask them for recommendations. They might have partnerships with rental companies or know which ones offer the best service.
- Check Local Construction Sites: Sometimes, a direct approach works best. If you see a construction site or a warehouse operation in your area, stop by and ask where they rent their conveyor systems from.
The Role of Major Home Improvement Stores in Gravity Roller Conveyor Rental
Major home improvement stores have increasingly become pivotal players in the equipment rental market, including offering solutions for gravity roller conveyor rental. These stores, such as Home Depot, Lowe’s, and others, provide an accessible and convenient option for businesses and individuals in need of temporary material handling solutions. Their role in facilitating conveyor belt rentals is significant for several reasons:
Wide Geographic Footprint: With locations spread across many regions, major home improvement stores offer the advantage of proximity. This widespread presence means that businesses can often find a rental option within a short distance from their operation sites, reducing transportation costs and logistical complexities.
Diverse Inventory: These stores typically maintain a diverse inventory of rental equipment, including gravity roller conveyors suitable for a variety of tasks. Whether the project involves light-duty work or requires more robust material handling capabilities, there’s a good chance a suitable option is available.
Flexible Rental Terms: Understanding the varying needs of their customers, these stores offer flexible rental terms. From hourly rentals for quick tasks to weekly and even monthly options for longer projects, customers can select the duration that best fits their project’s timeline, ensuring they’re not paying for equipment when it’s not in use.
Online and In-Store Support: Major home improvement stores provide comprehensive support, both online and in-store. Customers can reserve equipment, check availability, and arrange for pickup or delivery through the store’s website. Additionally, in-store associates are often knowledgeable about the equipment and can provide advice on the best options for specific projects.
Competitive Pricing: Due to their large scale and purchasing power, these stores can offer competitive pricing on rentals. This affordability makes gravity roller conveyor rental more accessible to a wider range of businesses, from small startups to larger corporations looking to manage costs effectively.
Additional Resources: Beyond just providing rental equipment, many of these stores offer resources such as tutorials, safety tips, and project guides. These resources can be invaluable for businesses looking to maximize the efficiency of their rental equipment and ensure safe operation.
One-Stop Shopping: For businesses undertaking projects that require more than just conveyor systems, these stores can be a one-stop-shop. In addition to conveyor rentals, customers can find a wide range of tools, equipment, and supplies necessary for their projects, streamlining the procurement process.
The role of major home improvement stores in providing gravity roller conveyor rental options represents a significant convenience and resource for businesses. Their widespread availability, diverse inventory, flexible rental terms, and additional support services make them an attractive option for those in need of temporary material handling solutions.
Online Resources and Directories
- Rental Company Websites: Many companies have comprehensive websites detailing their rental fleets, including specifications and rental terms.
- Online Rental Marketplaces: Platforms like RentItToday.com or EquipmentRental.com aggregate rental options from various providers, allowing you to compare offerings.
- Business Review Sites: Websites like Yelp and Google Reviews can provide insights into customer experiences with different rental services.
- Industry-Specific Directories: Directories such as ThomasNet or IndustryNet list companies by service and location, including those offering rental services.
- LinkedIn: The professional networking site can be a resource for finding rental companies and reading reviews or testimonials from other businesses.
- Yellow Pages Online: The digital version of the classic directory lists local businesses, including those offering gravity roller conveyor rentals.
- Local Chamber of Commerce: Many chambers of commerce maintain directories of local businesses, including equipment rental companies.
- Rental Broker Services: Some services act as brokers, finding the equipment you need to rent from their network of providers.
By leveraging these tips and resources, businesses can efficiently locate gravity roller conveyor rental services that meet their specific operational needs, ensuring a smooth and efficient material handling process for their projects.
Cost Considerations for Gravity Roller Conveyor Rental
When planning to rent a gravity roller conveyor, understanding the various cost factors and budgeting appropriately is crucial for making informed decisions. This section delves into the primary cost considerations associated with gravity roller conveyor rental, providing insights into what influences rental prices and additional costs that might not be immediately apparent.
Factors Influencing Rental Costs
Several factors can affect the cost of renting a gravity roller conveyor. Being aware of these can help you navigate rental agreements more effectively:
- Length of Rental: The duration of the rental period is a primary factor. Longer rental terms often have lower daily rates but higher overall costs.
- Type of Conveyor: Specialized conveyors, such as those designed for heavy-duty applications or with specific features like adjustable heights, can be more expensive than standard models.
- Condition: Newer or well-maintained conveyors typically command a premium over older or more worn equipment.
- Capacity and Size: Larger conveyors with higher weight capacities can increase rental costs.
- Brand and Model: High-end brands or models with advanced features may be more costly to rent.
- Demand and Availability: Rental costs can fluctuate based on demand, especially during peak industry periods.
- Location: Rental prices may vary by geographic location, reflecting local market conditions and transportation costs.
- Insurance and Liability Coverage: Optional or mandatory insurance coverage can add to the rental cost, providing protection against damage or accidents.
Estimating Rental Costs and Budgeting
To effectively budget for a gravity roller conveyor rental, consider the following points:
- Define Project Scope: Clearly outline the duration and scale of your project to determine how long you’ll need the conveyor.
- Get Multiple Quotes: Contact several rental companies to compare prices and services, ensuring you get the best value.
- Consider the Total Cost of Ownership (TCO): Factor in not just the rental rate but also delivery, setup, and any potential downtime costs.
- Negotiate Terms: Don’t hesitate to negotiate the rental terms. Some providers may offer discounts for longer rental periods or repeat business.
- Plan for Contingencies: Set aside a portion of your budget for unexpected costs, such as extended rental needs or additional equipment.
- Review Contracts Carefully: Understand what’s included in the rental agreement and what might incur additional charges.
- Monitor Usage: Keeping track of how and when the conveyor is used can help avoid overage fees or penalties for misuse.
Additional Costs to Consider
Beyond the base rental rate, several additional costs can impact the overall expense of renting a gravity roller conveyor:
- Delivery and Pickup Fees: Depending on the distance and logistics, these fees can significantly affect the total cost.
- Setup and Installation: Some rental companies charge extra for setup and installation services.
- Maintenance and Repairs: While maintenance is typically covered, damage caused by misuse may result in repair fees.
- Insurance: Optional insurance coverage can protect against accidental damage but will increase the overall cost.
- Training: If the rental company provides training on how to use the equipment, there may be an additional charge.
By carefully considering these cost factors and additional expenses, businesses can more accurately budget for a gravity roller conveyor rental, ensuring that they make cost-effective decisions that align with their project’s needs and financial constraints.
Ready to enhance your conveyor system? Contact us here!
To Prepare for Your Gravity Roller Conveyor Rental
Successfully integrating a gravity roller conveyor rental into your operations requires careful planning and preparation. By thoroughly assessing your needs and understanding the rental process, you can ensure that the equipment you rent enhances your operational efficiency without unnecessary complications. This section outlines the essential steps to take before renting and key questions to ask rental companies.
Essential Steps Before Renting
Before embarking on a gravity roller conveyor rental, it’s crucial to lay the groundwork to ensure that the equipment you rent aligns perfectly with your operational needs and spatial constraints. This preparation phase is foundational, not only to optimize the functionality of the conveyor within your processes but also to ensure financial efficiency and safety compliance. Here are the pivotal steps to consider:
- Assess Your Material Handling Needs: Clearly define what you need the conveyor for, including the types of items to be transported and their weights. This will help determine the size and capacity of the conveyor required.
- Evaluate Space Requirements: Measure the available space where the conveyor will be installed to ensure a proper fit. Consider the layout and any obstacles that might affect installation and operation.
- Determine Rental Duration: Estimate how long you will need the conveyor to complete your project. Being precise can help manage costs effectively.
- Understand Load Capacity: Match the conveyor’s load capacity with your operational needs to ensure it can handle your typical material volumes without overloading.
- Consider Portability and Flexibility: If your operations require moving the conveyor between different locations or adjusting its configuration, look for models that offer portability and flexibility.
- Review Safety Requirements: Ensure the conveyor meets all necessary safety standards and that your team knows how to operate it safely.
- Plan for Delivery and Setup: Coordinate with the rental company to arrange a convenient delivery time and understand what, if any, setup assistance they provide.
- Budget Appropriately: Incorporate the rental cost, delivery fees, potential setup charges, and any other associated expenses into your project budget.
Questions to Ask Rental Companies
Engaging with rental companies requires a strategic approach to extract maximum value from your gravity roller conveyor rental. The right questions can illuminate the suitability of the rental agreement to your specific needs, uncovering details about service quality, support, and financial obligations. This dialogue is essential for forging a partnership that enhances your operational capacity without unforeseen complications. Here are critical inquiries to make:
- Availability: Is the specific type of gravity roller conveyor you need available for the dates required?
- Rental Terms and Conditions: What are the rental agreement’s terms, including the rental period, costs, and any penalties for early termination or extension?
- Support Services: Does the company offer customer support during the rental period in case of operational questions or issues?
- Maintenance and Repairs: Who is responsible for maintenance and repairs during the rental period? What is the process for addressing equipment malfunctions?
- Delivery and Pickup: Are delivery and pickup services included in the rental price? If not, what are the costs?
- Setup and Training: Does the company provide setup services and operational training for the conveyor? Is there an additional cost for these services?
- Insurance and Liability: What kind of insurance is required? Does the rental company provide insurance, or must you arrange it separately?
By meticulously preparing for your gravity roller conveyor rental and asking the right questions, you can ensure a smooth integration of the equipment into your operations, maximizing efficiency and minimizing any potential disruptions. This proactive approach will help you leverage the full benefits of the rental to meet your material handling needs effectively.
Safety and Operational Training for Gravity Roller Conveyor Rental
Ensuring the safe and efficient operation of a gravity roller conveyor rental is paramount for maintaining a productive work environment and safeguarding your workforce. This section emphasizes the critical importance of adhering to safety protocols and securing proper operational training, alongside exploring the extent of training support rental companies offer.
Importance of Safety Protocols and Training for Operators
- Preventing Accidents: Proper training and adherence to safety protocols significantly reduce the risk of workplace accidents, protecting operators and bystanders from potential injuries.
- Compliance with Regulations: Familiarity with and adherence to industry safety standards and regulations ensure legal compliance, helping avoid fines and legal issues.
- Enhancing Efficiency: Well-trained operators use equipment more efficiently, minimizing downtime and maximizing productivity.
- Reducing Equipment Damage: Understanding how to operate a gravity roller conveyor correctly reduces the likelihood of costly damages and prolongs the equipment’s lifespan.
- Improving Morale: A safe working environment boosts employee morale and confidence, knowing their well-being is a priority.
- Customized Safety Measures: Different models and setups of gravity roller conveyors may require specific safety measures; comprehensive training addresses these nuances.
- Emergency Preparedness: Training should cover emergency procedures, ensuring operators know how to respond swiftly and effectively to prevent accidents or mitigate their impact.
- Maintenance Awareness: Basic maintenance knowledge helps operators identify and report potential issues before they escalate, ensuring the equipment remains in safe working condition.
- Certification Requirements: Some jurisdictions or industries may require operators to have specific certifications to operate material handling equipment, including conveyors.
Training Provision by Rental Companies
- Inclusion in Rental Agreement: Many rental companies include basic operational training as part of the rental agreement, ensuring operators can safely use the equipment.
- On-Site Training Options: Some providers offer on-site training sessions for operators, which can be customized to the specific model rented and the client’s operational environment.
- Online Resources: Rental companies may provide access to online tutorials, manuals, and safety videos as part of their service offerings.
- Additional Training Services: For more comprehensive needs, rental companies might offer extended training programs, which could include safety protocols, maintenance, and troubleshooting, possibly at an additional cost.
- Certification Programs: If required, check whether the rental company facilitates or offers certification programs for operators, ensuring compliance with industry standards.
- Training Materials: Upon rental, companies should provide manuals and safety guidelines specific to the rented equipment, aiding in self-guided learning.
- Support Hotlines: Access to support hotlines for immediate assistance with operational or safety questions can be a crucial resource provided by the rental company.
- Responsibility Clarification: It’s essential to clarify who is responsible for training within the rental agreement. If the company does not provide comprehensive training, arrangements may need to be made separately.
Understanding the importance of safety protocols and ensuring operators receive adequate training are critical steps in the gravity roller conveyor rental process. By partnering with a rental company that offers robust training and support, businesses can ensure their operations run smoothly, safely, and efficiently.
To Maximize the Efficiency of Your Gravity Roller Conveyor Rental
To fully leverage the benefits of a gravity roller conveyor rental, it’s essential to integrate best practices into your operations and be adept at troubleshooting common issues. This ensures not only the smooth running of your operations but also the safety and productivity of your workforce. Here are comprehensive strategies and solutions for optimizing the use of your gravity roller conveyor rental.
Best Practices for Efficient Use
- Proper Installation: Ensure the conveyor is installed on a level surface to prevent materials from slipping or rolling uncontrollably. Proper alignment is crucial for efficient operation.
- Regular Inspections: Conduct daily inspections to check for any signs of wear and tear or damage. Promptly addressing minor issues can prevent them from escalating into major problems.
- Load Distribution: Evenly distribute loads across the conveyor surface to maintain balance and prevent overloading on one side, which could lead to malfunctions or inefficiencies.
- Speed Regulation: Adjust the conveyor speed according to the type of materials being transported. Proper speed ensures smooth operation and reduces the risk of items toppling over.
- Operator Training: Ensure all operators are thoroughly trained in using the conveyor, including safety protocols, load capacities, and emergency stop procedures.
- Preventive Maintenance: Follow the rental company’s recommended maintenance schedule to keep the conveyor in optimal working condition and extend its lifespan.
- Utilize Accessories: Make use of available accessories such as guides, rails, and stops to enhance the functionality of the conveyor and accommodate different types of materials.
- Clear Pathways: Keep the area around the conveyor clear of obstructions to allow for easy access and to prevent accidents.
Troubleshooting Common Issues
- Conveyor Not Moving: Check for obstructions or debris in the rollers and ensure the conveyor is correctly positioned on a level surface. Verify that all connections and supports are secure.
- Materials Slipping: Adjust the conveyor’s incline or speed, and check if the load is evenly distributed. Consider using mats or coatings designed for extra grip.
- Excessive Noise: Lubricate the rollers and check for loose components. Noise often indicates a need for maintenance or adjustment.
- Roller Damage: Replace damaged rollers immediately to prevent further damage to the conveyor or the materials being transported.
- Load Capacity Issues: Ensure the weight and size of the materials do not exceed the conveyor’s specifications. Overloading can lead to significant damage and safety hazards.
- Stuck Rollers: Clean the rollers to remove any buildup of dirt, dust, or debris that may be causing them to stick.
- Misalignment: Regularly check the alignment of the conveyor and adjust as necessary to prevent uneven wear and tear on the rollers.
- Emergency Stops Not Working: Test emergency stop mechanisms regularly to ensure they are functioning correctly. Immediate repair or replacement is necessary if they are not working.
By implementing these best practices and being prepared to address common issues swiftly, businesses can maximize the efficiency and productivity of their gravity roller conveyor rental. This proactive approach not only ensures smooth operations but also contributes to the safety and well-being of all personnel involved.
Explore our range of conveyor rollers for all applications.
FAQs about Gravity Roller Conveyor Rental
A gravity roller conveyor is a versatile material handling tool used across various industries to facilitate the movement of goods. It operates on the principle of gravity, where the conveyor is slightly inclined, allowing items to move from a higher point to a lower point without the need for motor power. This type of conveyor is particularly useful for transporting packages, boxes, and even bulky items across short to medium distances within facilities such as warehouses, manufacturing plants, and distribution centers. Its applications range from sorting, assembly, and packaging processes to loading and unloading goods. The simplicity of its design not only makes it cost-effective but also easy to install and maintain, making it an ideal solution for businesses looking to improve their operational efficiency without significant investment.
The capacity of a gravity roller conveyor can vary widely depending on the model, the diameter of the rollers, the width of the conveyor, and the material from which the rollers are made. Typically, these conveyors can handle loads ranging from a few pounds per roller to several hundred pounds per roller. For instance, light-duty conveyors might support up to 50 pounds per roller, while heavy-duty models are designed to carry loads up to 250 pounds per roller or more. The total capacity of the conveyor system also depends on the spacing of the rollers, with closer spacing allowing for the transportation of heavier items. Businesses must assess their specific needs, considering the weight and size of the items to be transported, to select a gravity roller conveyor system that meets their requirements effectively.
The price of a motorized roller conveyor can vary significantly based on several factors, including the length of the conveyor, the width of the rollers, the type of motor used, and any additional features or customizations. Generally, prices can range from a few thousand dollars for basic, small-scale models to tens of thousands of dollars for larger, more complex systems designed for specific industrial applications. Factors such as the inclusion of advanced control systems, the quality of materials used in construction, and the conveyor’s capacity also play a crucial role in determining the final cost. Businesses interested in purchasing a motorized roller conveyor should consider obtaining quotes from multiple suppliers to compare options and ensure they are getting a system that meets their needs at a competitive price.
No, gravity conveyors do not require electricity to operate. As the name suggests, these conveyors rely on the force of gravity to move items along the rollers. They are typically installed with a slight decline from the loading end to the unloading end, allowing items to move smoothly across the surface with minimal manual assistance. This not only makes gravity conveyors an energy-efficient option but also reduces operational costs associated with electricity consumption. However, for operations that require more control over the speed and direction of the items being transported, additional equipment such as brake rollers or manual push-off diverters may be integrated into the system, which could require manual operation but still not electricity.
Last Updated on July 9, 2024 by Jordan Smith
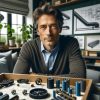
Jordan Smith, a seasoned professional with over 20 years of experience in the conveyor system industry. Jordan’s expertise lies in providing comprehensive solutions for conveyor rollers, belts, and accessories, catering to a wide range of industrial needs. From initial design and configuration to installation and meticulous troubleshooting, Jordan is adept at handling all aspects of conveyor system management. Whether you’re looking to upgrade your production line with efficient conveyor belts, require custom conveyor rollers for specific operations, or need expert advice on selecting the right conveyor accessories for your facility, Jordan is your reliable consultant. For any inquiries or assistance with conveyor system optimization, Jordan is available to share his wealth of knowledge and experience. Feel free to reach out at any time for professional guidance on all matters related to conveyor rollers, belts, and accessories.