Enhancing Your System with Gravity Roller Track Accessories
Gravity roller tracks are a cornerstone of modern logistics and manufacturing, offering a simple yet effective means of moving goods across short to medium distances within a variety of settings. These systems leverage the force of gravity to facilitate the movement of items, significantly reducing the need for manual labor or electrical power in transporting goods. Particularly valued across industries such as warehousing, distribution, and assembly lines, gravity roller tracks embody efficiency and versatility. This guide will delve into not only the basics of gravity roller tracks and their pivotal role in streamlining operations but also explore DIY projects, purchasing options, and important pricing considerations. Choosing the right components is crucial for constructing an efficient conveyor system, whether for upgrading existing operations or building from scratch. Our focus will be on guiding you through the selection process to ensure your setup meets your specific needs while maintaining cost-effectiveness and operational efficiency.
What are Gravity Roller Tracks
Gravity roller tracks are a fundamental component in the material handling and logistics industries, providing an efficient, low-cost, and straightforward solution for moving goods across short to medium distances. This type of conveyor system utilizes the natural force of gravity to move items, making it a popular choice for a variety of applications.
Definition and Basic Explanation
A gravity roller track is a series of rollers set in a frame at a slight incline, allowing items placed on it to roll down from one end to the other under the force of gravity. These tracks do not require power to operate, making them an economical and environmentally friendly option for businesses. The rollers are typically made from metal, plastic, or a combination of both, and are designed to support a wide range of goods in terms of size, weight, and material.
Principle of Operation
The principle of operation behind a gravity roller track is simple yet effective. By placing the track at a slight incline, gravity pulls the items down the rollers from the higher end to the lower end. The incline angle and the roller type can be adjusted based on the weight and type of items being transported to ensure smooth movement. This system leverages gravity to minimize the need for manual handling or electric power, thereby reducing operational costs and energy consumption.
Common Applications in Material Handling and Logistics
- Warehouse Picking Systems: Gravity roller tracks are widely used in warehouses to facilitate the quick and easy movement of goods between different areas, especially in picking and packing zones.
- Loading and Unloading Areas: These tracks are ideal for loading docks and unloading areas, where goods can be moved into and out of transportation vehicles with minimal effort.
- Assembly Lines: In manufacturing settings, gravity roller tracks can be used to move parts and products through various stages of assembly, allowing for a seamless production process.
- Sortation Systems: They are also employed in sortation systems to direct packages to different areas based on destination or other criteria.
- Distribution Centers: Gravity roller tracks play a crucial role in distribution centers, where they facilitate the movement of goods from storage areas to loading docks for distribution.
- Retail Stock Rooms: In the retail sector, these tracks can be used in stock rooms to move merchandise from storage areas to the sales floor efficiently.
- Parcel Delivery Services: Courier and parcel delivery services use gravity roller tracks to sort and move packages quickly through their sorting facilities.
- Food and Beverage Industries: They are also utilized in the food and beverage industries for transporting products through processing, packaging, and distribution areas.
- Pharmaceuticals: In the pharmaceutical industry, gravity roller tracks can be used to move ingredients, products, and supplies through various stages of production and packaging.
Gravity roller tracks are a testament to the ingenuity of simple mechanical principles applied to modern industrial and logistics challenges. By leveraging gravity, businesses can achieve efficient, cost-effective, and versatile material handling solutions that can be customized to a wide range of applications and environments.
DIY Gravity Roller Track Projects
The implementation of gravity roller tracks isn’t confined to industrial settings alone. Enthusiasts and professionals alike can bring the efficiency and simplicity of these systems into their own DIY projects. Whether it’s for optimizing a home workshop, creating a unique storage solution, or even constructing a fun and educational toy for children, gravity roller tracks offer a versatile foundation for countless projects.
How to Implement Gravity Roller Tracks in DIY Projects
Gravity roller track projects can vary widely, from simple, small-scale applications to more complex and larger systems. These projects harness the natural force of gravity to move objects along a predetermined path with minimal effort and no need for electrical power. This not only makes such systems environmentally friendly but also cost-effective and easy to maintain. For those who like to tinker, build, and optimize, crafting a custom gravity roller track system can be an engaging and rewarding endeavor.
Tips and Considerations for Designing and Assembling a Custom Gravity Roller Track System
- Define the Purpose: Clearly define what you want your gravity roller track to accomplish. Is it for sorting, storage, transportation, or entertainment?
- Select the Right Materials: Choose materials that are suitable for the items you plan to transport on the track. Metals are durable and can support heavier loads, while plastics can be more cost-effective and sufficient for lighter items.
- Consider the Size and Weight of Items: Ensure the rollers and the track are capable of supporting the size and weight of the items you intend to move.
- Adjust the Incline: The incline angle is critical for ensuring items move smoothly without manual intervention. Test different angles to find the most effective one for your needs.
- Space Rollers Appropriately: Rollers should be spaced closely enough to support the smallest item you plan to transport but not so close as to unnecessarily increase the cost and complexity of the project.
- Ensure Stability: The track must be stable and securely mounted to prevent wobbling or tipping, which could disrupt the movement of items or cause accidents.
- Incorporate Stops and Guides: Depending on your project, you might need stops at the end of the track to prevent items from falling off, or guides along the sides to keep them on track.
- Plan for Easy Assembly and Disassembly: Design your system in a way that makes it easy to assemble, disassemble, and modify. This flexibility will be helpful for maintenance or future expansions.
- Safety First: Ensure all parts of your gravity roller track are smooth and free of sharp edges to prevent injuries during use.
- Experiment with Curves and Junctions: For more complex systems, consider incorporating curves and junctions to direct items to different locations.
- Think About Expansion: Design your system with the potential for future expansion in mind. Modular designs can be easily extended or reconfigured as your needs evolve.
- Test and Iterate: Before finalizing your design, conduct thorough testing with actual items. Observe how they move along the track and make adjustments as necessary to optimize performance.
By following these tips and considerations, DIY enthusiasts and professionals can design and assemble custom gravity roller track systems tailored to their specific needs and preferences. Whether the project is utilitarian or purely for enjoyment, the principles of gravity roller tracks provide a solid foundation for innovation and creativity.
Buying Guide for Gravity Roller Tracks
When in the market for gravity roller tracks, the array of options available can be overwhelming. Whether for expanding a current system, setting up a new operation, or embarking on a DIY project, understanding the key factors that influence the performance and cost-effectiveness of these systems is crucial. This guide aims to arm you with the necessary information to make informed purchasing decisions, focusing on material quality, load capacity, compatibility with existing systems, and more.
Factors to Consider When Looking for Gravity Roller Tracks
- Material Quality: The durability and longevity of a gravity roller track heavily depend on the quality of materials used. Steel rollers are ideal for heavy-duty applications, while aluminum and plastic rollers might suffice for lighter loads.
- Load Capacity: Each gravity roller track system has a specific load capacity. Assess the weight of the items you intend to transport and choose a system that can handle that weight comfortably.
- Roller Diameter and Width: The size of the rollers affects the types of items the track can handle. Larger rollers are better for heavy or large items, while smaller rollers are suitable for smaller loads.
- Frame Construction: The frame should be sturdy enough to support the weight of both the rollers and the load. Check the construction material and design for durability.
- Length and Flexibility: Consider the length of the track you need and whether you require a flexible track that can be adjusted or extended.
- Compatibility with Existing Systems: If you’re adding to an existing system, ensure the new tracks are compatible in terms of roller size, height, and connection points.
- Ease of Assembly and Installation: Look for tracks that come with clear instructions and can be easily assembled and installed without professional help, especially for DIY projects.
- Maintenance Requirements: Opt for tracks that are easy to clean and maintain, with replaceable parts readily available.
- Safety Features: Safety is paramount. Check for tracks with built-in safety features like end stops, side guides, and non-slip surfaces.
- Supplier Reputation and Support: Purchase from reputable suppliers that offer good customer support, warranties, and return policies.
A Comparison of Gravity Roller Track Prices
Gravity roller track prices can vary widely based on the factors mentioned above. Here’s a general guide to help you navigate pricing:
- Basic Plastic Rollers: These are the most cost-effective option, suitable for light applications. Prices can start from as low as a few dollars per foot.
- Aluminum and Light-Duty Steel Rollers: Mid-range options that offer a good balance between cost and durability. Prices may range from $10 to $30 per foot, depending on the specifications.
- Heavy-Duty Steel Rollers: Designed for industrial applications with high load capacities. These can cost anywhere from $30 to over $100 per foot, based on size, load capacity, and design complexity.
Remember, the cheapest option isn’t always the most cost-effective in the long run. Consider the total cost of ownership, including maintenance, replacement parts, and potential downtime. Comparing prices from multiple suppliers and looking for bulk discounts or wholesale prices can also lead to significant savings, especially for larger projects.
By taking into account these factors and doing thorough research, you can ensure that you select a gravity roller track system that meets your needs at a price that aligns with your budget, ensuring both efficiency and cost-effectiveness.
Where to Purchase Gravity Roller Tracks
Finding the right supplier for gravity roller tracks can significantly impact the success of your material handling projects. With the rise of digital marketplaces and specialized suppliers, purchasing these systems has become more accessible than ever. Below are eight recommended places to start your search, including both online marketplaces and specialized conveyor parts suppliers, followed by the advantages of opting for online purchases.
Recommendations on Where to Buy Gravity Roller Tracks
- RS Components: A leading distributor of industrial components, RS Components offers a wide range of gravity roller tracks suitable for various applications, from light to heavy-duty.
- McMaster-Carr: Known for its vast inventory, McMaster-Carr is a go-to for engineers and project managers looking for specific parts, including gravity roller tracks.
- Amazon Business: For quick and easy access to a variety of gravity roller track options, Amazon Business provides both convenience and competitive pricing, with options for fast shipping.
- eBay Business & Industrial: eBay’s business and industrial section can be a treasure trove for finding both new and used gravity roller tracks, often at competitive prices.
- Global Industrial: Specializing in industrial equipment, Global Industrial offers a curated selection of gravity roller tracks and systems designed for efficiency and durability.
- Uline: Known for its extensive range of material handling equipment, Uline stocks gravity roller tracks that cater to a broad spectrum of industrial needs.
- Conveyor Parts Suppliers: Many specialized suppliers focus exclusively on conveyor systems and components. These suppliers can offer customized solutions and expert advice on selecting the right gravity roller track for your specific needs.
- Direct from Manufacturers: Contacting manufacturers directly can sometimes yield the best prices and allow access to the latest products and technologies in the gravity roller track market.
Advantages of Purchasing Conveyor Rollers Online
- Wide Range of Products: Online platforms offer access to a vast array of products from different brands and manufacturers, making it easier to compare and find the perfect solution.
- Convenience: Shopping online allows you to research and purchase gravity roller tracks from the comfort of your home or office, saving time and effort.
- Competitive Pricing: Online marketplaces often offer competitive pricing due to lower overhead costs and the ability to easily compare prices across different sellers.
- Customer Reviews: Access to customer reviews and ratings can provide valuable insights into the quality and performance of different gravity roller track systems.
- Technical Specifications and Support: Online listings usually include detailed product specifications, and many suppliers offer online chat support to answer any questions.
- Flexible Shopping Hours: Unlike physical stores, online marketplaces are open 24/7, offering the flexibility to shop according to your schedule.
- Direct Shipping: Purchased items can be shipped directly to your location, which is particularly advantageous for large or bulky items like gravity roller tracks.
- Access to Global Suppliers: Online shopping breaks down geographical barriers, allowing you to purchase from suppliers around the world if you’re looking for something specific or cost-effective not available locally.
Purchasing gravity roller tracks online offers unparalleled convenience, variety, and value, making it an excellent option for businesses and individuals alike. Whether you’re outfitting a large industrial operation or working on a personal project, the right supplier is just a few clicks away.
Types of Conveyor Rollers in Gravity Roller Track Systems
Conveyor rollers are pivotal in defining the efficiency, durability, and application suitability of gravity roller track systems. Among these, metal and plastic rollers stand out due to their widespread usage and distinct characteristics. Here, we delve into an overview of these rollers, focusing on plastic rollers and their specific benefits, followed by a comparative analysis with metal rollers to guide selection based on operational needs.
Different Types of Conveyor Rollers
The table below highlights the key features and benefits of plastic conveyor rollers, emphasizing their advantages in specific applications within gravity roller track systems.
Plastic conveyor rollers, made from durable types of plastics like polypropylene, polyethylene, or nylon, offer a lightweight and cost-effective solution for many conveyor system applications. They are particularly valued for their corrosion resistance and quieter operation, making them a suitable choice for specific environments, such as those prone to moisture, chemical exposure, or where noise reduction is beneficial.
Comparison Between Metal and Plastic Conveyor Rollers
This comparative analysis between metal and plastic conveyor rollers highlights the key differences in durability, cost, and suitability for various operational environments, aiding in the selection process for gravity roller track systems.
This comparison elucidates that while metal rollers are unparalleled in terms of durability and are ideal for heavy-duty applications, plastic rollers offer significant advantages in environments where corrosion resistance, lower operational noise, and cost savings are critical. The choice between metal and plastic conveyor rollers for a gravity roller track system should thus be guided by the specific needs of the operational environment, the nature of the materials being transported, and budget considerations.
Additional Conveyor Components and Accessories for Gravity Roller Track Systems
Gravity roller track systems are vital in various industries for efficient material handling. However, the efficiency and functionality of these systems can be significantly enhanced with the right selection of additional conveyor components and accessories. Understanding these supplementary parts is crucial for optimizing your conveyor system.
Essential Conveyor Parts and Accessories
To complement gravity roller tracks, several key components and accessories are commonly used:
- Roller Belts: While gravity roller tracks primarily rely on gravity, roller belts can be added to control the speed of movement or to assist in uphill sections of a conveyor system.
- Conveyor Supplies: This broad category includes items like lubricants for rollers, replacement parts, and tools for maintenance and repair.
- Conveyor Accessories: Accessories such as side guides, end stops, and transfer plates help in directing, controlling, or transferring goods safely and efficiently across the conveyor system.
Guidance on Selecting the Right Conveyor Accessories
- Understand Your System Requirements: Before selecting accessories, thoroughly analyze your system’s needs, considering factors such as the types of goods handled, volume, and the specific challenges of your operational environment.
- Compatibility: Ensure that the accessories you choose are fully compatible with your existing gravity roller track system. Incompatibility can lead to inefficiencies or even damage to the system.
- Quality Matters: Opt for high-quality components and accessories. While they may come at a higher initial cost, they tend to offer better durability and reliability, reducing the need for frequent replacements.
- Maintenance Needs: Consider the maintenance requirements of any additional components. Easy-to-maintain accessories can save significant time and money in the long run.
- Safety First: Safety accessories, such as guards and emergency stops, are crucial for protecting workers and goods. Never compromise on safety features.
- Efficiency Enhancements: Look for accessories that can enhance the efficiency of your gravity roller track system, such as speed controllers or automated sorters.
- Space Considerations: Be mindful of the space available. Some accessories might require additional space or specific environmental conditions to operate effectively.
- Supplier Reliability: Purchase from reputable suppliers who offer reliable customer support and warranties for their products. Good after-sales support can be invaluable in case of any issues.
- Future Flexibility: Consider the flexibility of the accessories for future system expansions or modifications. Choosing modular components that can be easily adjusted or expanded can offer greater operational flexibility.
Incorporating the right additional components and accessories into your gravity roller track system can significantly enhance its performance, safety, and efficiency. By carefully considering the above guidance, you can ensure that your conveyor system is optimized for your specific needs, offering reliable and effective material handling solutions.
FAQs about Gravity Roller Track
A gravity roller conveyor is a type of conveyor system that relies on gravity to move materials across a flat or slightly inclined path. It consists of a series of cylindrical rollers mounted parallel to each other on a frame. As items are placed on the rollers, gravity pushes them down the line. This type of conveyor is an efficient, cost-effective solution for transporting goods over short to medium distances within warehouses, manufacturing plants, and distribution centers. The simplicity of its design—lacking motors or complex mechanisms—makes it not only economical to install and maintain but also versatile and easy to reconfigure as needed. Gravity roller conveyors are ideal for handling a wide range of product sizes and weights, making them a staple in many material handling setups.
A roller track is an integral component of conveyor systems, consisting of a series of rollers mounted within a frame. These tracks provide the pathway along which goods, packages, or materials are moved from one location to another. Roller tracks can be powered or unpowered, with gravity roller tracks being a common unpowered variant that utilizes the force of gravity to facilitate movement. The design of a roller track varies based on its intended use, including the type of rollers used (metal, plastic, etc.), the spacing between rollers, and the track’s overall length and width. Roller tracks are widely used in various industries for sorting, assembling, transporting, and accumulating items, offering flexibility and efficiency in operations.
Gravity rollers are manufactured from several types of materials, each selected based on the specific requirements of the application, including the weight of items being conveyed, the environment in which the conveyor will operate, and cost considerations. Common materials include:
Steel: Known for its durability and strength, steel rollers are used in heavy-duty applications where the conveyor must withstand significant wear and tear.
Aluminum: Lighter than steel, aluminum rollers are easier to install and maneuver, suitable for lighter loads and providing good corrosion resistance.
Plastic: Offering the benefits of low noise and corrosion resistance, plastic rollers are ideal for lighter applications and environments where moisture or chemical exposure is a concern.
The choice of material impacts the conveyor’s performance, maintenance needs, and longevity, making it a crucial consideration during the design and selection process.
Conveyor rollers can be categorized based on their construction material, bearing type, and the specific applications they are designed for. The main types include:
Metal Rollers: Typically made of steel or aluminum, metal rollers are chosen for their strength and durability, suitable for heavy loads and industrial applications.
Plastic Rollers: Used in applications requiring corrosion resistance and quieter operation. They are lighter and often more cost-effective than metal rollers but are best suited for lighter loads.
Grooved Rollers: Designed with grooves to accommodate drive belts or ropes, grooved rollers are used in powered conveyor systems to move items more efficiently.
Tapered Rollers: Utilized in curves and corners of conveyor systems, tapered rollers help maintain the orientation and alignment of items as they navigate turns.
Impact Rollers: Positioned at loading points where items are dropped onto the conveyor, impact rollers are designed to absorb the shock and reduce the damage to the conveyor belt.
Selecting the right type of conveyor roller is essential for ensuring optimal performance and longevity of the conveyor system, tailored to the specific needs of the operation and the characteristics of the materials being transported.
Last Updated on May 23, 2024 by Jordan Smith
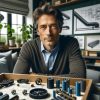
Jordan Smith, a seasoned professional with over 20 years of experience in the conveyor system industry. Jordan’s expertise lies in providing comprehensive solutions for conveyor rollers, belts, and accessories, catering to a wide range of industrial needs. From initial design and configuration to installation and meticulous troubleshooting, Jordan is adept at handling all aspects of conveyor system management. Whether you’re looking to upgrade your production line with efficient conveyor belts, require custom conveyor rollers for specific operations, or need expert advice on selecting the right conveyor accessories for your facility, Jordan is your reliable consultant. For any inquiries or assistance with conveyor system optimization, Jordan is available to share his wealth of knowledge and experience. Feel free to reach out at any time for professional guidance on all matters related to conveyor rollers, belts, and accessories.