Advanced Design in Gudgeon Bolt Screw Conveyors
A Gudgeon Bolt Screw Conveyor is a specialized mechanical device crucial in the operation of bulk material handling. Characterized by a helical screw blade, also known as a flighting, enclosed in a tube or trough, it efficiently transports materials horizontally, inclined, or vertically. The gudgeon bolt plays a pivotal role in this system, acting as a critical fastening element that ensures the structural integrity and smooth operation of the conveyor.
The importance of gudgeon bolt screw conveyors spans across a multitude of industries. In agriculture, they are instrumental in the handling and processing of grains and feeds. The manufacturing sector utilizes these conveyors for the efficient movement of raw materials, components, and finished products, ensuring a streamlined production process. In the mining and construction industries, they are used for transporting a variety of mined materials, from coal to crushed ores.
In the food processing and pharmaceutical industries, gudgeon bolt screw conveyors play a vital role in maintaining hygienic and contamination-free transportation of products. They are also pivotal in environmental and waste management industries, where they contribute to the efficient handling and processing of waste materials, aiding in recycling efforts.
The versatility of these conveyors is further demonstrated by their ability to handle a wide range of materials, from powders and pellets to liquids. This adaptability, combined with their efficiency and reliability, makes gudgeon bolt screw conveyors an indispensable tool in the modern industrial landscape. Their contribution to the operational efficiency of various industries is a testament to their significance in the global economy.
Descripting Gudgeon Bolt Screw Conveyor
A gudgeon bolt screw conveyor is a specialized type of screw conveyor designed for handling and transporting bulk materials. This conveyor utilizes a screw mechanism, which consists of a helical (spiral-shaped) blade coiled around a shaft (the gudgeon bolt), enclosed in a tube or trough. The turning of the screw blade moves the material along the conveyor’s length. This design is particularly effective for moving granular, powder, or similar materials. Here’s a detailed exploration of its concepts, advantages, disadvantages, and applications:
Concepts
- Design and Operation: The core of a gudgeon bolt screw conveyor is the screw mechanism. The gudgeon bolt serves as the central shaft around which the helical blade is wound. When the shaft rotates, the blade pushes material along the conveyor from the feed point to the discharge point.
- Versatility in Configuration: These conveyors can be designed in various configurations, including horizontal, vertical, and inclined orientations, to suit different operational needs.
- Customization: The size, pitch, and design of the screw, as well as the conveyor’s length and shape, can be customized based on the specific material handling requirements, making it a versatile solution for many industries.
Advantages
- Efficiency in Material Handling: Gudgeon bolt screw conveyors are highly efficient at moving materials, especially powders and granules, with precision and control.
- Low Maintenance: The simplicity of their design contributes to lower maintenance requirements compared to more complex material handling systems.
- Safety and Cleanliness: Being fully enclosed, these conveyors minimize material spillage and dust generation, enhancing workplace safety and cleanliness.
- Versatile Applications: Their ability to handle a wide range of materials and configurations allows them to be used in diverse industrial settings.
Disadvantages
- Material Degradation: The mechanical action of the screw can sometimes lead to material degradation, particularly with fragile materials, affecting the quality of the product being transported.
- Limited Distance: Screw conveyors are generally not suitable for long-distance transportation as efficiency decreases and the potential for material degradation increases over longer lengths.
- Wear and Tear: The internal components, especially the screw blade, are subject to wear and tear from abrasive materials, necessitating regular inspections and replacements.
Applications
- Agriculture: Used for moving grain, feed, and other agricultural products during processing and storage operations.
- Chemical Industry: Effective for handling chemicals in powder or granular form, where precise control and containment are critical.
- Food Processing: Utilized for transporting ingredients, such as flour and spices, through various stages of processing and packaging.
- Pharmaceuticals: In the pharmaceutical industry, these conveyors transport powdered ingredients and formulations in a controlled, contamination-free environment.
- Waste Management: Employed for the movement of waste materials in treatment and recycling facilities, offering a solution for handling a variety of waste products efficiently.
Gudgeon bolt screw conveyors offer a practical and efficient method for transporting bulk materials, especially in situations where space is limited, and material containment is crucial. Their simplicity, efficiency, and versatility make them a favored choice across many industries, despite the limitations related to material degradation, distance, and wear.
The Roux Gudgeon Bolt: A Key Component in Gudgeon Bolt Screw Conveyor Systems
Detailed Exploration of The Roux Gudgeon Bolt (#20)
Description of the Roux Gudgeon Bolt: The Roux Gudgeon Bolt (#20) stands as a quintessential example of precision engineering in the realm of gudgeon bolt screw conveyor components. This bolt is meticulously designed to fulfill a critical role in the assembly and operation of gudgeon bolt screw conveyor systems. Characterized by its robust construction and precision dimensions, the Roux Gudgeon Bolt is an embodiment of durability and reliability. It is crafted to ensure optimal performance, particularly in environments where the screw conveyor systems are subjected to continuous use and varying operational conditions.
Application in Conveyor Systems: The application of the Roux Gudgeon Bolt extends beyond its basic functionality as a fastening element. In the context of gudgeon bolt screw conveyors, this bolt plays a pivotal role in maintaining the structural integrity and operational efficiency of the conveyor system. It is specifically designed to withstand the mechanical stresses typically encountered in screw conveyor operations, including rotational forces and material load variations. This makes the Roux Gudgeon Bolt an indispensable component in ensuring the smooth and uninterrupted functioning of gudgeon bolt screw conveyors.
Compatibility with Roux Pistol Grip Syringe
Integration with Roux Pistol Grip Syringe: The Roux Gudgeon Bolt (#20) is not only a significant component in the domain of gudgeon bolt screw conveyors but also finds its specialized application in the veterinary field. It is uniquely compatible with the Roux Pistol Grip Syringe, an essential tool used in veterinary medicine for administering treatments to animals. This compatibility highlights the versatile nature of the Roux Gudgeon Bolt, showcasing its utility across diverse operational settings.
Ensuring Operational Synergy: The precise design of the Roux Gudgeon Bolt allows it to seamlessly integrate with the Roux Pistol Grip Syringe, ensuring that the syringe functions effectively and reliably. This synergy is crucial in veterinary practices where precision and reliability are paramount. The bolt’s role in this context is to provide a secure and stable connection, thereby enhancing the overall efficacy of the syringe in delivering treatments.
Product Identification and Branding
Unique Identification (#142013): Each Roux Gudgeon Bolt is marked with a distinct product number, #142013, serving as its unique identifier. This identification is crucial for users and suppliers in accurately tracking, ordering, and replacing the bolt as needed. It ensures that the correct part is utilized for the appropriate application, especially critical in maintaining the performance standards of gudgeon bolt screw conveyors and Roux Pistol Grip Syringes.
Branding (APE Roux): The Roux Gudgeon Bolt carries the prestigious APE Roux branding, a mark of quality and trust in the industry. This branding signifies that the bolt adheres to the high standards set by APE Roux in manufacturing and design. Users can trust in the reliability and excellence that come with the APE Roux name, a reassurance especially significant in industries where the performance of gudgeon bolt screw conveyors is integral to overall operational success.
The Roux Gudgeon Bolt (#20) is not just a mere component; it is a critical element in the efficient functioning of gudgeon bolt screw conveyors and is vital in various other applications, including its unique role in veterinary medicine. Its precise design, robust construction, and versatility across different platforms underscore its importance in the seamless operation of these systems.

Changrong’s Horizontal Screw Conveyor: An Epitome of Innovation and Flexibility in Gudgeon Bolt Screw Conveyor Technology
In-depth Analysis of Changrong’s Conveyor Features
Oil-Impregnated Bearing: A standout feature of Changrong’s horizontal screw conveyor is its incorporation of oil-impregnated bearings. These bearings are a technological marvel in the world of gudgeon bolt screw conveyors, offering a significant advancement in lubrication technology. The oil-impregnated bearings are designed to release lubricant gradually over time, ensuring consistent and efficient operation. This self-lubricating feature not only enhances the longevity of the conveyor system but also minimizes the need for frequent maintenance. It’s particularly beneficial in demanding industrial environments where reliability and low maintenance are paramount.
Flexible Technology Integration: Changrong’s conveyors are a testament to flexible design in the realm of gudgeon bolt screw conveyors. This flexibility is evident in the conveyor’s ability to adapt to various operational needs. Whether it’s adjusting to different material types, handling capacities, or environmental conditions, Changrong’s conveyors demonstrate a remarkable adaptability. This flexible technology approach allows for a tailored solution that can meet specific industrial requirements, making it a versatile choice for diverse applications.
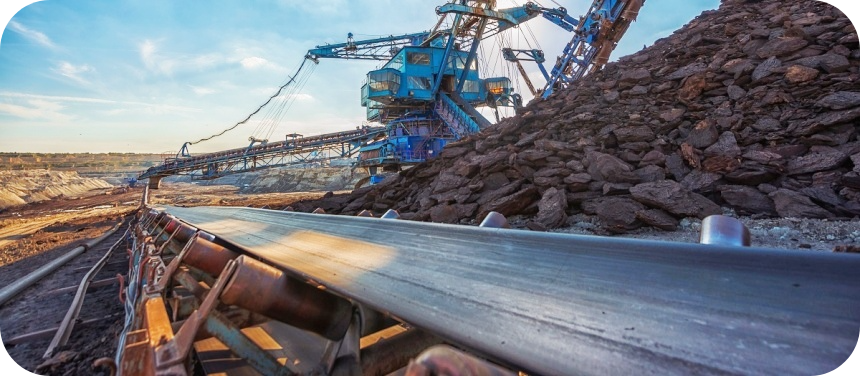
Variety and Customization Options
Diverse Varieties: In terms of variety, Changrong’s horizontal screw conveyor range is impressively diverse. They offer conveyors in left, right, and other configurations, catering to a wide array of operational requirements. This variety is crucial in ensuring that the conveyor system can be integrated seamlessly into different production lines, irrespective of the spatial constraints or directional requirements. The availability of multiple types ensures that industries can select a conveyor that aligns perfectly with their unique operational framework.
Customization Capabilities: Beyond the standard models, Changrong’s approach to customization in gudgeon bolt screw conveyor systems is noteworthy. They recognize that every industrial setting has its unique challenges and requirements. Consequently, they offer customization options that allow clients to modify aspects of the conveyor system, such as dimensions, material handling capacity, and even the materials used in construction, to best fit their specific needs.
Operation Characteristics and Maintenance
Ease of Operation: The operation of Changrong’s horizontal screw conveyors is designed with user-friendliness in mind. These conveyors are engineered to deliver smooth and consistent performance, which is essential for maintaining an uninterrupted production flow. The design considerations include user interface simplicity, ensuring that the operators can manage the system efficiently with minimal training.
Maintenance Simplified: Maintenance ease is another hallmark of Changrong’s conveyors. Thanks to features like the oil-impregnated bearings, the need for regular maintenance is significantly reduced. Moreover, the design of the conveyor system allows for easy access to key components, making any necessary maintenance or repairs less cumbersome. This ease of maintenance not only reduces downtime but also extends the lifespan of the conveyor system, thereby ensuring a better return on investment.
Changrong’s horizontal screw conveyors represent a blend of innovation, flexibility, and practicality in the field of gudgeon bolt screw conveyors. Their advanced features like oil-impregnated bearings, the variety in conveyor types, and the emphasis on ease of operation and maintenance make them a formidable choice for industries looking to optimize their material handling processes.
Gudgeon Bolt Screw Conveyor from IBT Industrial Solutions: Tailored Excellence in Material Handling
Custom-Engineered Systems for Specific Operations
Bespoke Design Approach: IBT Industrial Solutions excels in providing custom-engineered gudgeon bolt screw conveyor systems, specifically designed to meet the unique demands of various industrial operations. Understanding that each industry has its distinct material handling challenges, IBT Industrial Solutions approaches each project with a bespoke design mentality. Whether it’s for agriculture, pharmaceuticals, manufacturing, or waste management, their gudgeon bolt screw conveyors are tailored to optimize efficiency and reliability in these diverse operational contexts.
Adaptability to Operational Needs: The customization extends to all aspects of the conveyor system, including size, shape, material throughput, and even the environmental conditions under which the system will operate. This adaptability ensures that the gudgeon bolt screw conveyor system is not just a fitting addition but a vital cog in the client’s operational machinery, enhancing productivity and minimizing bottlenecks.
Selection of Parts and Accessories
Wide Range of Components: The strength of IBT Industrial Solutions in the realm of gudgeon bolt screw conveyors also lies in their extensive selection of parts and accessories. They provide a comprehensive range of components that are crucial for the assembly and maintenance of screw conveyors. This includes everything from gudgeon bolts, shafts, and couplings to hangers, bearings, and troughs.
Quality and Compatibility: Each part and accessory offered by IBT Industrial Solutions is selected for its quality and compatibility with different types of screw conveyors. This ensures that clients have access to components that not only fit their specific conveyor model but also contribute to the overall efficiency and longevity of their material handling system.
Partnerships with Industry Brands
Collaborations with Leading Brands: A key aspect of IBT Industrial Solutions’ prowess in the gudgeon bolt screw conveyor market is their strategic partnerships with leading industry brands. By collaborating with companies like Conveyors Inc., Martin, and KWS Manufacturing, IBT Industrial Solutions is able to offer a wide range of high-quality, reliable conveyor solutions.
Benefit from Expertise and Innovation: These partnerships enable IBT Industrial Solutions to benefit from the expertise and innovation of these renowned manufacturers. Conveyors Inc., Martin, and KWS Manufacturing are known for their advanced technology and engineering excellence in conveyor systems. By aligning with these brands, IBT Industrial Solutions ensures that their customers have access to the latest developments and highest standards in gudgeon bolt screw conveyor technology.
Comprehensive Conveyor Solutions: The collaboration with these industry giants allows IBT Industrial Solutions to provide comprehensive solutions that encompass not just the conveyors themselves but also the necessary support in terms of parts, accessories, and expert guidance. This holistic approach positions IBT Industrial Solutions as a one-stop-shop for all gudgeon bolt screw conveyor needs, from initial design and customization to ongoing maintenance and support.
The gudgeon bolt screw conveyor offerings from IBT Industrial Solutions represent a fusion of custom engineering, comprehensive parts selection, and strategic industry partnerships. This triad of strengths enables them to provide tailor-made, efficient, and reliable conveyor systems, backed by the expertise and innovation of some of the leading names in the industry. Their approach ensures that each conveyor system is not just a product but a solution, intricately woven into the operational fabric of their clients’ industries.
Advanced Design and Material Choices in Gudgeon Bolt Screw Conveyor Systems
Adhering to CEMA Standards in Size and Design
Compliance with Industry Standards: One of the critical aspects of gudgeon bolt screw conveyor systems is their adherence to the Conveyor Equipment Manufacturers Association (CEMA) standards. These standards are a benchmark in the industry, ensuring that all screw conveyors, including those with gudgeon bolts, are designed and constructed to meet essential safety, reliability, and operational efficiency criteria.
Variety in Sizes: The gudgeon bolt screw conveyor systems come in a range of sizes, catering to different industrial needs. These sizes typically range from smaller diameters suitable for light and fine materials to larger diameters designed for heavy-duty and bulk material handling. This variation in size, in compliance with CEMA standards, ensures that industries can select a screw conveyor that perfectly aligns with their specific material handling requirements.
Diversity in Design and Materials
Material Selection for Durability and Efficiency: The design of gudgeon bolt screw conveyors is not limited to functionality alone but also encompasses the choice of materials used in their construction. Common materials include various grades of steel, stainless steel, and specialized alloys. These materials are chosen for their durability, strength, and suitability for different operational environments.
Customized Solutions for Specific Needs: Depending on the industry and the type of materials being handled, the construction of the screw conveyor can be customized. For instance, stainless steel might be preferred in food processing or pharmaceutical applications for its resistance to corrosion and ease of cleaning. In contrast, carbon steel or hardened alloys might be more suitable for industrial environments handling abrasive or high-temperature materials.
Special Features for Handling Abrasive Materials
Design Considerations for Abrasive Materials: Gudgeon bolt screw conveyors handling abrasive materials are equipped with special design features. These features are intended to prolong the life of the conveyor and minimize wear and tear. They include thicker flights, reinforced troughs, and hardened or coated surfaces that resist abrasion.
Innovative Engineering for Longevity: The engineering of these conveyors focuses on reducing the impact of abrasive materials on the system. This might involve the strategic placement of wear-resistant liners, the use of heavy-duty bearings, and the incorporation of easy-to-replace sections in high-wear areas. These innovations ensure that gudgeon bolt screw conveyors remain efficient and reliable even in the most challenging industrial environments.
The design and material choices in gudgeon bolt screw conveyor systems are pivotal in defining their efficiency and suitability for various industrial applications. Compliance with CEMA standards, diversity in design and materials, and specialized features for abrasive materials collectively ensure that these conveyors meet the highest standards of performance, safety, and durability. This comprehensive approach to design and material selection makes gudgeon bolt screw conveyors a versatile and indispensable tool in material handling across a wide spectrum of industries.
Essential Components and Their Roles in Gudgeon Bolt Screw Conveyor Systems
Conveyor Screws: The Heart of the System
Function and Operation: Conveyor screws are the central working component of any gudgeon bolt screw conveyor system. These helical blades, mounted on a shaft, are designed to move materials along the length of the conveyor trough. As the screw rotates, material is pushed forward through the trough, creating an efficient and continuous flow. The design of the screw – including its pitch, diameter, and blade thickness – varies depending on the type of material being conveyed and the required conveying capacity.
Customization for Specific Needs: Conveyor screws can be tailored to suit specific operational needs. For instance, a variable pitch screw helps in evenly distributing the load along the conveyor length, while a tapered screw is used for uniform discharge or intake along the conveyor. These customizations ensure optimal performance of the gudgeon bolt screw conveyor in diverse industrial settings.
Shafts and Coupling Bolts
Vital Connectors: Shafts and coupling bolts, including Gudgeon bolts, are crucial in assembling and maintaining the structural integrity of screw conveyors. The shaft runs the length of the conveyor and supports the helical blades. Coupling bolts, such as Gudgeon bolts, are used to connect multiple sections of the shaft and ensure a smooth transfer of rotational force.
Durability and Precision: These components are typically made from high-strength materials to withstand the stresses of operation. Precision in their design and manufacturing is key to maintaining the alignment and efficiency of the conveyor system.
Hangers and Bearing Materials
Support and Alignment: Hangers in gudgeon bolt screw conveyors are used to provide support and maintain the alignment of the screw shaft. Positioned along the length of the conveyor, these hangers ensure that the shaft rotates smoothly with minimal friction and wear.
Material Choices for Bearings: The bearings within these hangers can be made from various materials like bronze, hardened steel, or synthetic materials like UHMW (Ultra High Molecular Weight Polyethylene). The choice of bearing material depends on factors such as load, speed of operation, and environmental conditions like temperature and moisture.
Trough Designs and Applications
Diverse Trough Configurations: The trough is the outer casing of the screw conveyor, within which the screw operates. Trough designs in gudgeon bolt screw conveyors vary greatly to accommodate different materials and applications. Standard U-shaped troughs are common, but there are also tubular, rectangular, or flared designs.
Adaptation to Material and Environment: Each trough design has its advantages and is chosen based on the material being conveyed and the operating environment. For example, a fully enclosed tubular design is ideal for handling fine or hazardous materials as it prevents material escape and contamination. In contrast, an open U-shaped trough is easier to clean and maintain, making it suitable for materials that do not require containment.
Each component in a gudgeon bolt screw conveyor system – from the conveyor screws to the troughs – plays a vital role in its overall operation and efficiency. The careful selection and design of these components ensure that the conveyor system meets the specific needs of various industrial applications, ensuring reliability, efficiency, and longevity.
Enhancing Gudgeon Bolt Screw Conveyor Systems with Special Features and Accessories
Trough Ends, Seals, and Bearings: Ensuring Integrity and Efficiency
Trough Ends: In gudgeon bolt screw conveyor systems, trough ends play a critical role in supporting and enclosing the ends of the conveyor trough. These are specifically designed to house bearings and seals, providing a secure and stable base for the rotating screw. The robust construction of trough ends contributes significantly to the overall durability and efficiency of the conveyor system.
Seals for Protection: Seals at the trough ends are essential for preventing material leakage and protecting the bearings from contamination. These seals are designed to withstand the specific conditions of the conveyor’s operation, whether it’s handling fine powders, sticky materials, or abrasive substances.
Bearing Selection: Bearings within the trough ends support the rotational movement of the screw. The selection of bearings is crucial and depends on factors like load capacity, operational speed, and environmental conditions. High-quality bearings ensure smooth operation and reduce maintenance requirements, enhancing the longevity of the gudgeon bolt screw conveyor system.
Trough Covers, Clamps, and Shrouds: Safety and Containment
Trough Covers: Trough covers are an essential accessory in gudgeon bolt screw conveyor systems, especially when handling materials that need to be contained or protected from external elements. These covers can be customized to fit various trough designs and can include features like inspection doors for easy access and maintenance.
Clamps and Shrouds: Clamps are used to securely fasten the covers to the trough, ensuring that the covers remain in place during operation. Shrouds, on the other hand, provide additional protection, especially around the loading and discharge areas, to prevent material spillage and dust emissions.
Find the perfect conveyor belt for your application. Contact us for a consultation!
Supporting Feet and Saddles: Stability and Alignment
Supporting Feet: These are the foundation elements that provide stability to the gudgeon bolt screw conveyor system. They are designed to evenly distribute the weight of the conveyor and its contents, ensuring steady operation. The design of the feet can vary depending on the installation requirements and the conveyor’s size and weight.
Saddles for Alignment: Saddles are mounted along the length of the conveyor to support the trough and maintain its alignment. Proper alignment is crucial for the efficient and smooth operation of the conveyor, preventing undue stress on the system and reducing wear.
Inlets, Discharge Spouts, and Gates: Controlled Material Handling
Inlets and Discharge Spouts: These components are integral to the control and direction of material flow in a gudgeon bolt screw conveyor system. Inlets are designed for efficient material feeding, while discharge spouts are tailored for controlled material exit, ensuring precise handling of the conveyed materials.
Gates for Flow Regulation: Gates, often installed at inlets or discharge points, provide additional control over the material flow. They can be manually or automatically operated to regulate the amount of material entering or leaving the conveyor.
Drive Reducers and Screw Conveyor Drives: Power and Efficiency
Drive Reducers: Drive reducers are critical in optimizing the power transmission to the screw conveyor. They ensure that the motor’s power is effectively converted into the required rotational speed and torque for the conveyor screw. This not only improves efficiency but also extends the life of the motor and conveyor.
Screw Conveyor Drives: The drives are the powerhouse of the gudgeon bolt screw conveyor system. They must be robust and reliable, capable of handling the demands of continuous operation. The design of the drive system, including motor selection and gearing, is tailored to match the specific requirements of the conveyor’s application.
The incorporation of these special features and accessories is vital in enhancing the performance, safety, and efficiency of gudgeon bolt screw conveyor systems. From the structural integrity provided by trough ends, seals, and bearings to the controlled material handling enabled by inlets, discharge spouts, and gates, each component plays a crucial role in the optimal functioning of the conveyor system. These enhancements not only improve the system’s operational capabilities but also contribute to its longevity and reliability.
Screw Conveyor Coupling Bolts: Essential Connectors in Gudgeon Bolt Screw Conveyor Systems
Key Role in Connecting Conveyor Parts
Crucial for Structural Integrity: Screw conveyor coupling bolts, including gudgeon bolts, are fundamental components in gudgeon bolt screw conveyor systems. They play a pivotal role in connecting various sections of the conveyor, particularly the screw sections to the driving shaft and the end shafts. This connection is crucial for maintaining the structural integrity and operational cohesiveness of the conveyor system.
Transmission of Rotational Force: These coupling bolts are designed not only to physically connect parts but also to transmit the rotational force from the motor to the screw. The efficient transfer of this force is essential for the consistent movement of materials along the conveyor. The strength and durability of these bolts are paramount, as they need to withstand the continuous stress and torque of the conveyor’s operation.
Availability and Customization Options
Wide Range of Availability: The market offers a broad selection of screw conveyor coupling bolts, catering to the diverse needs of different conveyor systems. These bolts come in various sizes and materials to match the specifications of various screw conveyors. The availability of a wide range ensures that maintenance and replacement of these components can be done with minimal downtime.
Customization to Meet Specific Needs: In addition to the standard options, there is also the possibility of customizing these bolts to meet specific requirements. Customization can include alterations in size, material composition, and even bolt design. This is particularly important in applications where standard bolts may not meet the unique demands of a particular conveyor system, such as in extreme temperatures, abrasive environments, or with unusual load capacities.
Material Options for Different Environments: The material of the coupling bolts can vary depending on the operational environment of the conveyor. For instance, stainless steel bolts may be preferred in food processing or pharmaceutical applications for their corrosion resistance, while hardened steel or alloy bolts could be more suitable for industrial applications involving abrasive or heavy materials.
Ease of Replacement and Maintenance: One of the key considerations in the design of screw conveyor coupling bolts is the ease of maintenance and replacement. These bolts are typically designed to be easily accessible and replaceable, minimizing the effort and time required for maintenance. This design consideration ensures that conveyor downtime is kept to a minimum, enhancing overall operational efficiency.
Screw conveyor coupling bolts are integral to the functionality and durability of gudgeon bolt screw conveyor systems. Their role in connecting conveyor parts and transmitting rotational force is critical to the system’s efficiency. The wide availability and customization options of these bolts ensure that they can meet the varied demands of different conveyor systems, contributing to the reliability and longevity of these essential industrial components.

Tubular Screw Conveyors by Guttridge: Pioneering Gudgeon Bolt Screw Conveyor Solutions
Target Markets and Global Usage
Diverse Industry Reach: The tubular screw conveyors developed by Guttridge have established a solid presence in various target markets around the globe. These gudgeon bolt screw conveyor systems are widely utilized in industries where precise and efficient handling of bulk materials is crucial. Key sectors include heavy-duty grain storage, animal feed milling, and general industrial markets such as biomass, waste, and recycling.
Global Footprint: Guttridge’s tubular screw conveyors have a significant global usage, with installations in numerous storage and processing plants worldwide. The versatility and reliability of these conveyors have made them a preferred choice in diverse geographical locations, catering to the unique material handling needs of different regions and industries.
Design Features and Material Options
Robust and Modular Design: The tubular screw conveyors by Guttridge are designed with a robust and modular approach, facilitating ease of assembly, installation, and maintenance. This design flexibility is crucial for adapting to various industrial requirements and environmental conditions.
Material Options for Durability and Efficiency: These gudgeon bolt screw conveyor systems are available in a variety of materials, including mild steel (painted or galvanized) and stainless steel. The choice of material is critical for ensuring the conveyor’s durability and efficiency under different operational conditions. For instance, stainless steel is often used in environments requiring high levels of hygiene and corrosion resistance, like food and pharmaceutical industries.
Specialized Conveyors for Specific Industries
Customization for Industry-Specific Needs: Guttridge offers specialized versions of their tubular screw conveyors, tailored to meet the specific needs of various industries. For instance, the company provides easy-clean stainless steel conveyors designed for the stringent requirements of the food and pharmaceutical sectors.
Silo Discharge Conveyors: Another specialized variant is the silo discharge conveyor. Optimized for silo discharge applications, these conveyors typically feature a robust extended inlet and flow control adjuster. They are designed to handle the demanding task of moving materials from storage silos to processing or distribution areas.
Adaptability to Environmental Conditions: The design of these specialized conveyors also takes into account environmental factors. For example, conveyors used in underground applications may have a different finish, such as a bitumen paint finish, for enhanced durability and corrosion resistance.
Guttridge’s tubular screw conveyors exemplify innovation and versatility in the realm of gudgeon bolt screw conveyor systems. Their global reach across various industries, coupled with their robust design and material options, make them a leading choice for businesses seeking efficient and reliable material handling solutions. The availability of specialized conveyors further underscores Guttridge’s commitment to providing industry-specific solutions, ensuring that their conveyors meet the unique demands of each sector they serve.

Acquiring and Tailoring Gudgeon Bolt Screw Conveyor Systems: A Guide to Purchase and Customization
Steps to Purchase and Customize Gudgeon Bolt Screw Conveyors
Initial Consultation and Requirement Analysis: The process of purchasing or customizing a gudgeon bolt screw conveyor system begins with an initial consultation. This involves discussing specific needs and requirements with the manufacturer or supplier. Customers need to provide details such as the type of material to be conveyed, capacity requirements, environmental conditions, and any specific challenges or constraints.
Design and Customization Process: Based on the initial consultation, the supplier or manufacturer will propose a design. For customization, this might include specific adjustments to the gudgeon bolts, the conveyor screw, the trough design, or the overall system layout. The goal is to tailor the conveyor system to perfectly fit the operational context of the customer.
Prototype and Approval: In some cases, especially for highly customized systems, a prototype or detailed design drawings may be provided. This step allows customers to visualize the final product and request any further modifications before final production.
Manufacturing and Quality Assurance: Once the design is finalized and approved, the manufacturing process begins. Quality assurance plays a critical role at this stage, ensuring that all components, including the gudgeon bolts and other parts of the screw conveyor, meet the specified standards and requirements.
Warranty, Quality, and Additional Product Information
Warranty Terms: Most manufacturers and suppliers of gudgeon bolt screw conveyors offer a standard warranty period, typically covering 12 months from the date of purchase or installation. This warranty generally includes coverage for defects in materials and workmanship. Customers can often negotiate for extended warranty terms based on their specific needs.
Quality Assurance: Quality is a paramount concern in the manufacture of gudgeon bolt screw conveyors. Reputable suppliers adhere to industry standards and certifications, ensuring that each component of the conveyor system is robust, reliable, and capable of withstanding the rigors of its intended use.
Information on Additional Products: Suppliers often have a range of additional products and accessories related to gudgeon bolt screw conveyors. These may include various types of screws, hangers, bearings, motors, and drive systems. Customers should inquire about these additional products to ensure a comprehensive solution that encompasses all aspects of their material handling needs.
After-Sales Support and Services: Reliable suppliers also offer after-sales support, including installation assistance, maintenance services, and spare parts supply. This support is crucial to ensure the long-term efficiency and reliability of the gudgeon bolt screw conveyor system.
Purchasing or customizing a gudgeon bolt screw conveyor system involves a series of steps from initial consultation to final installation. Understanding the warranty, ensuring quality, and exploring additional products and after-sales support are crucial aspects of this process. By carefully navigating these steps, customers can acquire a screw conveyor system that is precisely tailored to their operational requirements and built to last.
Interested in superior conveyor belts? Fill out the form and our experts will assist you!
FAQs about Gudgeon Bolt Screw Conveyors
Standard Pitch Screw: The most common type, ideal for conveying free-flowing materials like grains, food products, chemicals, and minerals. The pitch equals the diameter of the screw.
Short Pitch Screw: Used for more controlled and precise material flow. The pitch is shorter than the standard, ideal for conveying sticky or viscous materials.
Variable Pitch Screw: Has an increasing or decreasing pitch along the length. It’s used to provide a uniform draw of material along the conveyor length.
Ribbon Screw: Features a ribbon-like, thin helix design. Suitable for handling sticky or fibrous materials.
Paddle Screw: Contains paddles in place of a continuous helix. Good for mixing and agitating materials as they are conveyed.
Tapered Screw: The diameter of the screw decreases towards the discharge end. Useful for providing a uniform draw of material from bins or hoppers.
Shaftless Screw: Lacks a central shaft and is ideal for handling sticky or entwined materials.
The best material for a screw conveyor depends on the application and the type of material being conveyed. Common materials include:
Carbon Steel: Durable and cost-effective, suitable for most general applications.
Stainless Steel: Best for food-grade applications or corrosive environments. Offers high resistance to corrosion and is easy to clean.
Abrasion-Resistant Alloys: Ideal for handling abrasive materials like sand, gravel, and certain chemicals.
Polymer or Plastic: Used in applications requiring low friction and protection against mild corrosive materials.
The thrust load of a conveyor screw is the axial force exerted by the screw on the bearings and drive components. It is influenced by factors like the type of material being conveyed, screw diameter, pitch, and conveyor length. Calculating the exact thrust load requires detailed knowledge of these parameters and the operational conditions.
The capacity of a screw conveyor is calculated using the following formula:
[ Capacity (Cu ft/hr) = Area of screw (Sq ft) \times Speed (RPM) \times Fill Percentage \times Material Density (lbs/Cu ft) ]
To compute this:
Calculate the Area of the Screw:
[ Area = (\pi/4) \times (Diameter)^2 ]
Determine the Speed (RPM): The rotational speed of the screw.
Fill Percentage: Typically ranges from 15% (for materials that are likely to flow well) to 45% (for more sluggish materials).
Material Density: The weight of the material per cubic foot.
Remember, this is a general calculation and may need to be adjusted based on the specific characteristics of the material being conveyed and the operational parameters of the screw conveyor.
Last Updated on June 7, 2024 by Jordan Smith
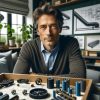
Jordan Smith, a seasoned professional with over 20 years of experience in the conveyor system industry. Jordan’s expertise lies in providing comprehensive solutions for conveyor rollers, belts, and accessories, catering to a wide range of industrial needs. From initial design and configuration to installation and meticulous troubleshooting, Jordan is adept at handling all aspects of conveyor system management. Whether you’re looking to upgrade your production line with efficient conveyor belts, require custom conveyor rollers for specific operations, or need expert advice on selecting the right conveyor accessories for your facility, Jordan is your reliable consultant. For any inquiries or assistance with conveyor system optimization, Jordan is available to share his wealth of knowledge and experience. Feel free to reach out at any time for professional guidance on all matters related to conveyor rollers, belts, and accessories.