Maximizing Efficiency with Guide Rollers for Conveyors
Guide rollers for conveyors play a pivotal role in the efficient operation of conveyor systems across various industries. These components are crucial for the smooth and precise movement of materials along the conveyor belt, reducing friction and wear on both the belt and the materials being transported. In industries ranging from mining and agriculture to packaging and logistics, guide rollers for conveyors ensure that goods are moved safely and effectively, minimizing downtime and maximizing productivity. This introduction aims to shed light on the fundamental concept of guide rollers and their indispensable role within conveyor systems. By understanding how these rollers function and their impact on the conveyor’s performance, businesses can make informed decisions on the implementation and maintenance of their conveyor systems, leading to improved operational efficiency and reduced operational costs.
The Basics of Guide Rollers for Conveyors
Guide rollers for conveyors are essential components designed to guide conveyor belts and ensure their stable and aligned movement. Unlike standard conveyor rollers that primarily support and move the belt and the materials it carries, guide rollers are specifically tasked with maintaining the belt’s path to prevent misalignment, which can lead to uneven wear, belt damage, and potentially hazardous situations. These rollers are strategically placed along the sides of conveyor systems, serving as a guiding force that keeps the belt running smoothly and efficiently.
The primary function of conveyor guide rollers is to provide lateral stability. This is crucial in applications where the conveyor path changes direction, such as in curved sections of the system, or where external forces might push the belt off course. By preventing the belt from drifting sideways, guide rollers help to reduce friction and wear on the belt edges, thus extending the life of the conveyor belt and reducing maintenance and replacement costs.
Here’s a simple comparison between guide rollers and standard conveyor rollers:
This distinction highlights how both types of rollers work together to ensure the conveyor system operates efficiently. Guide rollers for conveyors, with their specific role in maintaining belt alignment, are indispensable for the smooth and effective functioning of the entire conveyor system. Understanding the basics and the importance of these components can significantly contribute to optimizing conveyor performance and durability.
Types of Guide Rollers for Conveyors
Conveyors are essential components in numerous industrial settings, facilitating the efficient transport of materials across various stages of production and handling. Central to the functionality of these conveyors are the roller guides for conveyors, which ensure that the conveyor belts operate smoothly and consistently. This section will explore different types of guide rollers used in conveyor systems, focusing on their specifications, applications, and unique benefits.
Guide Roller Wheels
Guide roller wheels are a crucial type of conveyor guide rollers, designed to provide precise direction and alignment to conveyor belts, preventing them from drifting or slipping off their tracks. These rollers are typically mounted on the sides of the conveyor frames and can vary greatly in size, material, and design based on their specific applications.
Description and Application
Guide roller wheels are generally smaller than other types of rollers and are constructed from materials such as nylon, polyurethane, or steel. These materials are chosen for their durability, friction properties, and resistance to wear and environmental factors. The application of guide roller wheels includes:
- Food and Beverage Industry: Employed in conveyor systems to handle bottles, cans, and other packaging materials without contaminating the products.
- Pharmaceuticals: Used to guide sensitive medical supplies through the packaging process with minimal contact and low risk of contamination.
- Manufacturing: Integral in the assembly lines for electronics where precision and care are paramount.
- Packaging: Utilized in conveyor systems that require gentle handling of delicate products to prevent damage during movement.
- Material Handling: Helps in the smooth transportation of heavy goods and materials across warehouses and loading areas.
These rollers not only guide the belt but also help in maintaining the tension, which is critical for the efficient operation of the conveyor.
Heavy Duty Guide Rollers
Heavy duty guide rollers are designed to withstand extreme conditions and loads, making them ideal for industrial applications where durability and reliability are critical. These rollers are more robust than standard rollers and are capable of handling heavier weights and higher forces.
Overview and Importance
Heavy duty guide rollers are typically made from hardened steel or cast iron, with some models featuring reinforced bearings and enhanced sealing mechanisms to extend their operational life. The importance of these rollers in industrial applications includes:
- Mining and Quarrying: Essential for the transport of heavy and abrasive materials such as ores and minerals.
- Construction: Used in the handling of large building materials, including prefabricated components and heavy tools.
- Agriculture: Integral in the movement of large quantities of agricultural produce or materials, often under harsh environmental conditions.
- Steel Mills: Employed in the handling of hot, heavy, and rough steel products, where standard rollers would rapidly deteriorate.
- Heavy Machinery Manufacturing: Crucial in the assembly lines for heavy machines, where they must support substantial loads over long periods.
The robust construction of heavy duty guide rollers ensures that they can perform under the stress of heavy loads and abrasive conditions without failure, providing a reliable and smooth operation.
PPI Guide Rollers
PPI (Precision Pulley & Idler) is a renowned manufacturer of high-quality conveyor components, including guide rollers that are widely recognized in the industry for their durability and performance. PPI guide rollers, in particular, are designed to meet the highest standards of quality and are tailored to specific industrial needs.
Insight and Market Standout Features
PPI guide rollers are distinguished by their:
- High-Quality Materials: Utilizing superior-grade steels and composites for enhanced durability.
- Engineered Design: Each roller is precisely engineered to provide optimal performance in specific applications.
- Versatility: Suitable for a wide range of industrial applications, from mining to general manufacturing.
- Innovative Features: Many PPI rollers incorporate advanced features such as self-aligning capabilities, which reduce maintenance needs and increase efficiency.
- Customer-Centric Solutions: PPI offers customized solutions that can be tailored to the unique needs of different industries, enhancing the overall effectiveness of their guide rollers.
PPI’s commitment to quality and customer satisfaction makes their guide rollers a preferred choice in markets worldwide, standing out for their reliability, efficiency, and adaptability to various industrial environments.
Whether you are looking for standard guide roller wheels, heavy duty guide rollers, or specialized products like PPI guide rollers, understanding the specific needs of your conveyor system is key to selecting the right type of conveyor guide roller. Each category offers unique benefits tailored to different industrial applications, ensuring the longevity and efficiency of your conveyor system.
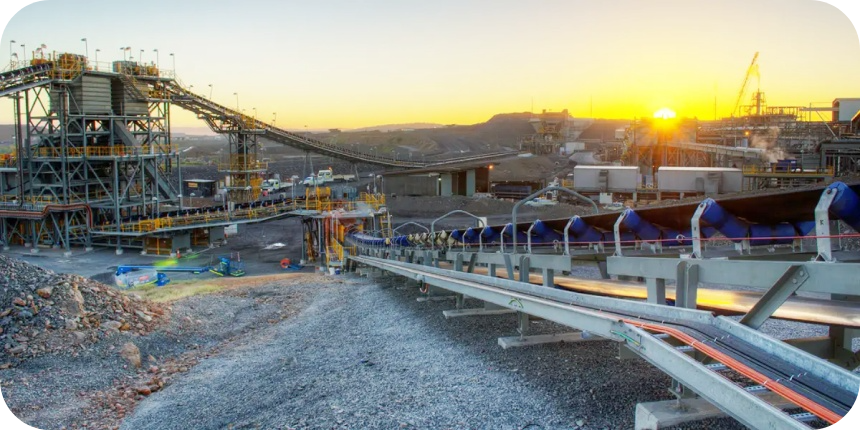
Key Components of Guide Rollers for Conveyors
The efficiency and functionality of conveyor systems heavily depend on the performance of the guide rollers for conveyors. These systems are comprised of several key components that work together to ensure optimal operation and durability. Each component plays a specific role in the conveyor’s overall function, from guiding the belts to supporting the entire system under various loads. This section delves into the critical components of guide roller systems, highlighting their configurations, functions, and significance in maintaining the conveyor path.
Guide Roller Assembly
The guide roller assembly is a principal component in the design of conveyor systems, consisting of various sub-components such as the roller itself, shafts, bearings, and mounting brackets. This assembly is critical as it dictates the smooth operation and alignment of the conveyor belt.
Configuration and Significance
A typical guide roller assembly includes:
- Roller: The cylindrical part that directly contacts and guides the conveyor belt.
- Shaft: A metal rod that connects the roller to the mounting brackets and provides an axis of rotation.
- Bearings: Positioned inside the roller, allowing it to rotate smoothly around the shaft with minimal friction.
- Mounting Brackets: Used to secure the roller assembly to the conveyor frame and can be adjusted to maintain belt tension and alignment.
The configuration of these components is essential for the following reasons:
- Precision in Belt Guidance: Ensures that the conveyor belt is accurately guided along the intended path without lateral movements that could lead to wear and tear or belt derailment.
- Reduction of Friction and Wear: High-quality bearings and smooth rollers reduce the resistance encountered by the conveyor belt, which in turn lowers the stress on the motor and increases the longevity of the belt.
- Adjustability for Tensioning: Adjustable mounting brackets help in maintaining the correct tension, which is crucial for consistent performance and to avoid slippage or snapping of the belt.
- Durability and Reliability: Guide roller assemblies are designed to withstand the operational demands of the conveyor system, including load variations and environmental challenges.
Roller Guide Rails
Roller guide rails are essential for maintaining the lateral position of guide rollers, ensuring that the conveyor belt remains within its intended path. These rails are typically constructed from materials like steel, stainless steel, or aluminum, providing a smooth and durable surface for the rollers to move against.
Function and Examples
The primary function of roller guide rails is to guide and support the rollers, thereby ensuring stable and efficient operation of the conveyor. Examples of applications include:
- Automated Warehouses: Used to guide automated carts and forklifts along predetermined paths.
- Food Processing Plants: Ensure that conveyor systems do not sway or deviate, which is crucial for maintaining hygiene and preventing contamination.
- Automotive Assembly Lines: Guide parts and assemblies through various stages of production, ensuring precise alignment and positioning.
- Pharmaceutical Manufacturing: Used in environments requiring high levels of precision and cleanliness.
- Packaging Facilities: Help maintain the flow of packages to be sorted, sealed, and labeled without interruptions.
These guide rails are not only pivotal in guiding the rollers but also play a critical role in supporting the weight of the conveyed materials, particularly in heavy-duty industrial applications.
Conveyor Side Guide Rollers
Conveyor side guide rollers are strategically placed along the edges of conveyor systems to ensure that the belt does not slip sideways, which could cause operational disruptions and damage to the belt.
Role and Examples
The specific roles of side guide rollers include:
- Preventing Belt Misalignment: They keep the conveyor belt aligned with the central axis of the conveyor system.
- Reducing Wear and Tear: By maintaining alignment, these rollers minimize the wear on the edges of the belt, which extends its service life.
- Enhancing Operational Efficiency: Properly aligned belts reduce the need for corrective maintenance and downtime.
- Supporting Loaded Belts: Especially useful in applications where the belt carries heavy or uneven loads.
- Improving Safety: Prevent belt slippage that could potentially lead to hazardous situations.
Applications showcasing the importance of side guide rollers:
- Mining Operations: They ensure that the rugged and heavy belts used for transporting ores stay on path without drifting.
- Cement Production: Maintain the alignment of belts carrying raw materials like limestone and clay.
- Grain Handling Facilities: Help in keeping the belts aligned while transferring bulk grain loads.
- Postal Sorting Offices: Used to ensure that sorting belts run smoothly to handle high volumes of mail and packages.
- Airport Baggage Systems: Keep the luggage belts aligned, thus preventing luggage from falling off the conveyor.
The guide roller assembly, roller guide rails, and conveyor side guide rollers are integral components of guide rollers for conveyors. Each plays a distinct role in enhancing the efficiency, reliability, and safety of conveyor systems, making them indispensable in industrial and commercial applications. Understanding these components and their functions can
Specialized Guide Rollers for Conveyors
Specialized conveyor guide roller are designed to meet unique operational needs of different industrial setups. These rollers enhance the functionality of conveyor systems by accommodating specific requirements such as alignment, product handling characteristics, and environmental conditions. In this section, we explore the uses and benefits of vertical guide rollers, as well as a variety of conveyor belt roller types, each paired with their corresponding guide rollers to ensure optimal performance.
Vertical Guide Rollers
Vertical guide rollers are used in conveyor systems where lateral movement of the belt must be strictly controlled. These rollers are mounted perpendicularly to the usual flat conveyor setup, providing stability and precise directional guidance to the belt.
Uses and Benefits
Vertical guide rollers are particularly beneficial in the following scenarios:
Inclined Conveying:
- Use: These rollers are crucial in steep incline conveyor systems to prevent the belt from sagging or slipping off.
- Benefit: Enhances safety and reliability by providing additional lateral support.
Box Sorting Conveyors:
- Use: In systems used for sorting boxes, vertical guide rollers help to align items correctly as they move to different chutes.
- Benefit: Increases sorting accuracy and reduces item misplacement.
Automotive Assembly Lines:
- Use: They are used to guide parts through various processes without shifting position on the belt.
- Benefit: Maintains precise positioning of automotive parts, which is crucial for automated assembly processes.
Recycling Facilities:
- Use: In conveyor systems designed for recycling operations, vertical guide rollers help ensure materials are evenly distributed along the conveyor width.
- Benefit: Prevents pile-ups and ensures consistent material flow for better sorting and processing.
Packaging Conveyors:
- Use: Vertical guide rollers aid in maintaining the path of fragile items through the packaging lines, preventing them from toppling over.
- Benefit: Reduces product damage and loss, increasing operational efficiency and customer satisfaction.
Vertical guide rollers, therefore, not only help in maintaining the conveyor belt’s path but also play a critical role in ensuring the quality and efficiency of the conveyor system’s output by preventing deviations and disturbances.
Conveyor Belt Roller Types
Conveyor systems utilize various types of belt rollers, each designed to fulfill different requirements. The matching of conveyor belt roller types with the appropriate guide rollers is essential for achieving the desired performance.
Overview of Types and Match-ups
Flat Belt Rollers:
- Roller Type: These are the most common type of conveyor belt rollers, designed to support the flat surface of standard belts.
- Guide Rollers: Standard horizontal guide rollers are used to ensure that the belt runs smoothly without lateral movements.
Trough Rollers:
- Roller Type: Trough rollers are designed with a curved surface to hold the conveyor belt in a trough-like formation, increasing its carrying capacity.
- Guide Rollers: Vertical guide rollers are often paired with trough rollers to maintain the belt’s position within the trough, especially in heavy-duty operations.
Impact Rollers:
- Roller Type: Positioned at loading points, impact rollers absorb the shock and impact of loading material on the conveyor belts, which extends the belt’s lifespan.
- Guide Rollers: Reinforced horizontal guide rollers are used here to withstand the additional forces and help keep the belt aligned after the impact.
Return Rollers:
- Roller Type: These rollers support the return path of the belt, ensuring it does not sag or scrape against the conveyor frame.
- Guide Rollers: Simple, smooth guide rollers are suitable for return sections, as the belt in these areas typically carries no load.
Snub Rollers:
- Roller Type: Snub rollers are used to increase the angle of contact between the belt and the main rollers, enhancing friction and tension.
- Guide Rollers: These sections may use compact, horizontally mounted guide rollers to prevent the belt from slipping off the increased curvature created by the snub rollers.
Each of these conveyor belt roller types plays a pivotal role in the conveyor’s operation, and when matched with the correct guide rollers, they ensure the system’s efficiency, longevity, and safety. By understanding the specific needs of their conveyor setups and employing the appropriate types of guide roller conveyor, businesses can significantly enhance their operational capabilities.
Importance of Heavy Duty and Custom Solutions in Guide Rollers for Conveyors
In the industrial world, where durability and precision are paramount, the importance of specialized solutions such as heavy duty conveyor roller guides and their customization cannot be overstated. These components are crucial for ensuring the reliability and efficiency of conveyor systems under extreme operational conditions. This section details why heavy duty guide rollers are essential for certain applications and discusses the various customization options available to meet specific industrial needs.
Heavy Duty Guide Rollers
Heavy duty guide rollers are designed to withstand the severe stress and environmental challenges of industrial applications. These rollers ensure the conveyor systems operate smoothly and continuously, even under the toughest conditions.
Why Heavy Duty Guide Rollers are Crucial
Mining and Mineral Processing:
- Use: Transporting raw extracted materials, which are often abrasive and heavy.
- Importance: Heavy duty rollers resist wear and tear from abrasive particles and bear the heavy load of mined materials, preventing breakdowns and minimizing maintenance needs.
Pulp and Paper Industry:
- Use: Moving large volumes of wood chips and pulp through processing areas.
- Importance: The rollers need to handle the high weight and volume without deforming or failing, ensuring consistent production flow.
Steel Manufacturing:
- Use: Carrying hot, heavy steel products, like coils and slabs, through the manufacturing process.
- Importance: They must withstand high temperatures and heavy loads without distortion, supporting continuous operations and preventing accidents.
Construction Materials Handling:
- Use: Conveying heavy building materials such as cement, bricks, and tiles.
- Importance: Heavy duty rollers are essential to support the substantial weight of these materials, reducing the risk of conveyor failure and material spillage.
Agricultural Bulk Handling:
- Use: Transporting grain, feed, and other agricultural products in bulk.
- Importance: These rollers ensure the conveyor can handle the significant weight and bulk of agricultural produce efficiently, especially during peak harvest times.
These examples illustrate that heavy duty guide rollers are indispensable in industries requiring the transport of heavy, abrasive, or voluminous materials. Their robust design not only prolongs the life of conveyor systems but also enhances safety and efficiency by preventing equipment failures.
Customization in Guide Rollers
Customization in guide rollers is key to optimizing the performance of conveyor systems tailored to specific industrial applications. Customized guide rollers can be designed in terms of size, material, and other specifications to meet unique operational demands.
Customization Options Available
Materials:
- Polyurethane: Best for applications where durability, and noise reduction are needed.
- Steel: Ideal for high-strength requirements and is widely used in heavy-duty applications.
- Nylon: Offers excellent wear resistance and is suitable for chemical and impact resistance applications.
- Rubber-Coated: Used to increase grip and decrease noise and wear on the conveyor belt.
Sizes:
- Diameter: Custom diameters can be produced to accommodate the specific tension and weight requirements of the conveyor belt.
- Length: The length of the rollers can also be adjusted to spread the load more evenly or fit into custom-designed conveyor systems.
Bearing and Shaft Configurations:
- Sealed Bearings: For environments that are dusty or wet, sealed bearings prevent dirt, dust, and moisture from affecting performance.
- Special Shaft Materials: Shafts made from stainless steel or coated with corrosion-resistant materials can be used in corrosive environments.
Surface Treatments:
- Textured Surfaces: To increase traction and reduce slippage of the conveyor belt.
- Corrosion Resistant Coatings: Such as zinc or nickel plating to prevent rust and extend the life of the rollers in harsh environments.
Load Capacity:
- Enhanced Designs: Custom rollers can be designed to support higher load capacities without increasing the size or number of rollers, which is crucial for heavy-duty applications.
Customizing guide rollers for conveyors allows for a more tailored approach, ensuring that each conveyor system operates at its highest efficiency, regardless of the industry or the specific challenges it faces. This customization not only improves the longevity and functionality of the conveyor systems but also significantly reduces maintenance time and costs by precisely meeting the application requirements.
Application Insights for Guide Rollers for Conveyors
Guide rollers for conveyors are pivotal in various industrial sectors, facilitating smooth and efficient transport processes both indoors and outdoors. These rollers are highly versatile and adaptable, designed to meet the diverse needs of different environments and operational demands. Below, we explore specific applications of guide rollers in different industries and highlight their flexibility across various settings.
Industry Applications of Guide Rollers
Sorting Facilities:
- Application: In sorting facilities, such as those used by postal services or logistics companies, guide rollers are essential for accurately directing containers or packages to the correct chutes or belts for further processing or dispatch.
- Importance: They ensure precise and reliable movement of goods, which is crucial for maintaining efficiency in high-volume sorting operations.
Production Plants:
- Application: Production plants, especially those in automotive, electronics, and garment manufacturing, utilize guide rollers to ensure that components move seamlessly through different stages of the production line.
- Importance: They help in maintaining the pace of production and prevent the misalignment of materials, which can lead to product defects or machinery downtime.
Offshore Cranes:
- Application: Offshore cranes used in oil rigs and maritime operations employ guide rollers to manage the movement and placement of heavy loads and supplies transferred from ships to oil platforms or from one ship to another.
- Importance: These rollers are critical in such high-stakes environments as they enhance safety by stabilizing movements and reducing the risk of accidents due to load shifts.
Versatility and Adaptability of Guide Rollers
Guide rollers for conveyors demonstrate remarkable versatility and adaptability, functioning effectively in various scenarios:
Extreme Weather Conditions:
- Indoor/Outdoor: Outdoor mining operations
- Adaptability: Guide rollers made from materials like high-grade steel or coated with specialized weather-resistant finishes ensure longevity and reliability, even in extreme weather conditions such as heavy rain, snow, or intense heat.
Chemically Aggressive Environments:
- Indoor/Outdoor: Chemical processing plants
- Adaptability: Utilizing stainless steel or plastic composite guide rollers can resist corrosion and chemical degradation, maintaining their function and structure in harsh environments.
High-Temperature Areas:
- Indoor/Outdoor: Steel mills and foundries
- Adaptability: Guide rollers designed with heat-resistant materials and cooling mechanisms are essential to withstand and operate under high temperatures.
Wet and Humid Conditions:
- Indoor/Outdoor: Food processing facilities
- Adaptability: Employing stainless steel guide rollers with water-resistant bearings and seals ensures that the rollers do not rust or seize up, which is crucial in maintaining hygiene and operational efficiency.
Dusty or Sandy Conditions:
- Indoor/Outdoor: Cement manufacturing and desert-based operations
- Adaptability: Guide rollers fitted with sealed bearings and dust covers protect the internal mechanics from fine particles, thereby prolonging their operational life and reducing maintenance costs.
These examples highlight the essential role that conveyor roller guides play in not only ensuring the efficient and safe transport of materials across various industries but also in adapting to the specific conditions of each environment. Whether it is resisting harsh weather, avoiding corrosion, tolerating high temperatures, combating humidity, or keeping out dust, guide rollers are ingeniously designed to meet these challenges head-on. Their ability to perform reliably in diverse settings is what makes them indispensable components of modern conveyor systems.
Have questions about our Guide Rollers? Fill out the form, and our team will respond promptly.
Choosing the Right Guide Rollers for Conveyors
Selecting the appropriate guide rollers for conveyors is crucial for ensuring efficient, reliable, and cost-effective operations in various industrial setups. The right guide rollers not only extend the lifespan of conveyor systems but also enhance their performance and safety. This section explores the critical factors to consider when choosing guide rollers and the importance of consulting experts for custom solutions tailored to specific needs.
Factors to Consider
When choosing guide rollers for conveyors, several factors must be taken into account to ensure they are well-suited for their intended applications. These factors include load capacity, environmental conditions, and specific application needs. Below are five examples detailing these considerations:
Load Capacity:
- Example: In a mining application where heavy and abrasive materials like ore are transported, choosing guide rollers with a high load capacity and robust construction (such as those made from reinforced steel or heavy-duty polyurethane) is essential to withstand the intense strain and prevent premature wear.
Environmental Conditions:
- Example: For conveyor systems used outdoors, especially in coastal areas where salty air presents a corrosion risk, stainless steel guide rollers or those with corrosion-resistant coatings (like zinc or nickel plating) are preferable to enhance durability and resist rust.
Temperature Extremes:
- Example: In applications within steel mills where high temperatures are a constant, using guide rollers crafted from heat-resistant materials with special high-temperature bearings can prevent malfunctions and degradation of the system.
Chemical Exposure:
- Example: Conveyors used in chemical processing plants need guide rollers made from materials that can resist chemical corrosion, such as certain plastics, composites, or specially coated metals, to ensure longevity and safe operations.
Speed Requirements:
- Example: High-speed manufacturing processes, such as in automotive assembly lines, require guide rollers that are designed to handle higher rotational speeds. Using rollers with precision bearings and balanced construction ensures they can operate effectively at higher speeds without generating excessive heat or noise.
These examples underscore the importance of carefully considering the operational demands and environmental challenges when selecting guide rollers for conveyors to optimize both performance and cost-effectiveness.
Contacting Experts for Custom Solutions
For many industrial applications, standard guide rollers may not meet all the specific requirements of a conveyor system. In such cases, reaching out to experts for custom solutions becomes essential. Here’s how to approach experts for tailored guide roller solutions:
Step-by-Step Process to Engage with Experts
Identify Specific Needs:
- Assess the unique requirements of your conveyor system, including load type, speed, environmental factors, and any special operational conditions.
Research Potential Suppliers:
- Look for manufacturers who specialize in conveyor systems and have a good track record of providing high-quality, custom solutions. Check their certifications, reviews, and past project examples.
Prepare Detailed Specifications:
- Compile a comprehensive list of specifications that include all necessary dimensions, material preferences, load capacities, and environmental tolerances to ensure the custom products meet all application demands.
Request Consultation:
- Contact the selected experts to discuss your requirements. Provide them with the detailed specifications and any challenges you are facing with your current system.
Review Proposals:
- Evaluate the custom designs proposed by the suppliers. Consider their compatibility with existing systems, ease of installation, maintenance requirements, and cost-effectiveness.
Prototype Testing:
- If possible, test a prototype of the custom guide roller to ensure it meets the required specifications and performs satisfactorily under actual operational conditions.
Finalize Supplier Agreement:
- Once a suitable design is confirmed, finalize the agreement with the supplier for the manufacture and supply of the custom guide rollers. Ensure that the agreement includes provisions for quality assurance and post-installation support.
Benefits of Custom Guide Rollers
- Optimized Performance: Tailored solutions ensure that the guide rollers perfectly meet the operational needs of the conveyor system, enhancing efficiency and reliability.
- Reduced Maintenance Costs: Custom guide rollers designed to fit specific requirements and conditions tend to have a longer lifespan and lower maintenance needs.
- Increased System Longevity: By meeting the exact needs of the conveyor, custom guide rollers can help extend the overall life of the entire system.
Consulting with experts for custom guide rollers for conveyors not only facilitates a more tailored approach to meet specific industrial needs but also enhances the operational capabilities and longevity of conveyor systems, making it a worthwhile investment for complex and demanding applications.
FAQs About Guide Rollers for Conveyors
Guide rollers are specialized rollers designed to control the movement and position of conveyor belts or to provide linear motion guidance. These rollers are strategically placed along the sides of conveyor belts to ensure proper alignment and to prevent the belt from slipping off the tracks. Guide rollers play a crucial role in maintaining the efficiency and longevity of a conveyor system by minimizing wear and tear on the belt and reducing operational disruptions.
Key Points:
Functionality: Guide rollers keep the conveyor belt in line and help to adjust tension within the belt.
Materials Used: Typically made from metals such as steel or aluminum, plastics like nylon, or composites, depending on the application requirements.
Applications: Widely used in various industries including mining, manufacturing, and packaging, as well as in applications involving automated machinery and material handling systems.
These rollers are essential in applications where precise belt movement is critical to the operation’s success, ensuring that materials are handled smoothly across the production line.
Conveyors utilize various types of rollers, each designed to fulfill specific functional requirements of the system. The primary types of rollers found in conveyor systems include:
Drive Rollers: Propel the conveyor belt by providing power to it.
Idler Rollers: Support the belt and materials being transported along the length of the conveyor.
Guide Rollers: Ensure that the conveyor belt does not stray off its intended path.
Return Rollers: Support the return section of the belt as it loops back to the beginning.
Impact Rollers: Positioned at loading zones to absorb the forces exerted by incoming materials.
Composition and Design:
Rollers are typically constructed from materials like steel, stainless steel, or heavy-duty plastics, and may include features such as rubber coatings to improve grip and reduce noise.
Understanding the types of rollers used in a conveyor system is crucial for optimizing the system’s performance and extending its operational lifespan.
Elevator roller guides are used in elevator systems to ensure smooth, stable, and precise movement of the elevator car within the shaft. These rollers help in maintaining the alignment of the elevator car, preventing lateral movements and vibrations during operation.
Components and Function:
Location: Mounted on the sides of the elevator car, interacting with guide rails installed along the elevator shaft.
Materials: Typically made from durable materials like steel or polyurethane to withstand the constant friction and forces while providing a smooth ride.
Advantages:
Smooth Operation: Minimize vibrations and noise, enhancing passenger comfort.
Increased Safety: Reduce the risk of the elevator car swaying or jamming in the shaft.
Durability: Designed to last the lifetime of the elevator system with minimal maintenance.
Elevator roller guides are crucial for the safety and efficiency of elevator systems, ensuring that the elevator operates smoothly and securely within the confines of the elevator shaft.
Last Updated on July 25, 2024 by Jordan Smith
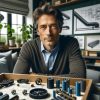
Jordan Smith, a seasoned professional with over 20 years of experience in the conveyor system industry. Jordan’s expertise lies in providing comprehensive solutions for conveyor rollers, belts, and accessories, catering to a wide range of industrial needs. From initial design and configuration to installation and meticulous troubleshooting, Jordan is adept at handling all aspects of conveyor system management. Whether you’re looking to upgrade your production line with efficient conveyor belts, require custom conveyor rollers for specific operations, or need expert advice on selecting the right conveyor accessories for your facility, Jordan is your reliable consultant. For any inquiries or assistance with conveyor system optimization, Jordan is available to share his wealth of knowledge and experience. Feel free to reach out at any time for professional guidance on all matters related to conveyor rollers, belts, and accessories.