Specialized Guide Rollers Manufacturers: Finding the Right Fit
Guide rollers play a pivotal role in the seamless operation of machinery across a multitude of industries, from automotive manufacturing to material handling and beyond. These components are crucial for guiding, supporting, and positioning moving parts, ensuring that processes run smoothly and efficiently. With such a wide range of applications, the demand for high-quality guide rollers is significant, making the choice of guide rollers manufacturers a critical decision for businesses aiming to optimize their operations. This blog post aims to navigate the complex world of guide rollers manufacturers, offering insights and guidance to help you make informed decisions. By understanding the landscape of manufacturers, you can select a partner that not only meets but exceeds your expectations, ensuring the longevity and reliability of your machinery and processes.
To Understand Guide Rollers from Top Guide Rollers Manufacturers
Guide rollers are essential components in various mechanical systems, designed to control the movement and direction of moving parts. These rollers ensure smooth operation, reduce friction, and guide materials or parts along a predetermined path. The choice of guide rollers manufacturers is crucial, as it directly impacts the efficiency, durability, and reliability of the rollers in application-specific environments.
Common Applications Across Industries
The versatility of guide rollers is evident in their wide range of applications across different industries. Here’s a table showcasing at least eight common applications:
The Role of Guide Rollers in Enhancing Production Efficiency and Reducing Maintenance
Selecting the right guide rollers manufacturers can significantly impact production efficiency and maintenance requirements. Here are at least eight points highlighting the role of guide rollers:
- Reduced Friction: High-quality guide rollers minimize friction between moving parts, leading to smoother operations and lower energy consumption.
- Increased Durability: Well-manufactured rollers resist wear and tear, extending the lifespan of machinery and reducing the need for frequent replacements.
- Improved Precision: Precision-engineered guide rollers ensure accurate movement and alignment, crucial for industries where precision is paramount.
- Enhanced Speed: Efficient guide rollers can increase the speed of conveyance systems, boosting overall production rates.
- Lower Maintenance Costs: Durable and reliable guide rollers require less maintenance, saving on downtime and repair expenses.
- Versatility: Guide rollers manufacturers offer products tailored to specific industry needs, ensuring optimal performance across various applications.
- Noise Reduction: Quality rollers operate quietly, improving the working environment and complying with noise regulations.
- Safety: Properly designed guide rollers contribute to safer operations by reducing the risk of malfunctions and accidents.
The selection of guide rollers manufacturers plays a pivotal role in the operational efficiency and maintenance needs of industries relying on these components. By choosing a manufacturer that specializes in high-quality, application-specific guide rollers, businesses can achieve improved performance, reliability, and cost savings.
How to Choose the Right Guide Rollers Manufacturers
Selecting the appropriate guide rollers manufacturers is a critical decision that can significantly impact the efficiency and reliability of your operations. Here are key factors to consider and the importance of aligning with a manufacturer that meets your specific project needs.
Factors to Consider
When embarking on the selection of guide rollers for your operations, the decision extends far beyond mere product specifications. It involves a comprehensive evaluation of the manufacturers behind these essential components. The right choice can significantly enhance your operational efficiency, reduce downtime, and ensure a smoother production process. Here are critical factors to consider when choosing guide rollers manufacturers, each playing a pivotal role in aligning the product’s performance with your operational needs and expectations.
- Material Quality: The durability and performance of guide rollers depend on the quality of materials used. High-grade materials ensure longevity and reliability.
- Manufacturing Process: Advanced manufacturing processes contribute to the precision and quality of the final product. Look for manufacturers utilizing the latest technologies.
- Industry Experience: Manufacturers with extensive experience in your industry are likely to offer products that meet your specific requirements.
- Product Range: A wide product range allows for more options and customizations to suit your needs.
- Customization Capabilities: The ability to customize products is crucial for unique applications.
- Quality Assurance: Certifications and quality control processes are indicators of the manufacturer’s commitment to quality.
- Customer Support: Responsive and knowledgeable customer support can be invaluable for product selection, troubleshooting, and maintenance advice.
- Lead Times and Delivery: Efficient production and delivery times ensure that your operations are not disrupted.
Importance of Selecting a Manufacturer That Aligns with Specific Project Needs
The importance of selecting a manufacturer that closely aligns with your specific project needs cannot be overstated. This strategic decision is pivotal in ensuring that the guide rollers you procure are not just adequate but are perfectly tailored to meet the unique demands of your applications. Here’s a deeper dive into why this alignment is crucial:
Tailored Solutions for Enhanced Performance: Manufacturers that understand your specific industry and application can provide guide rollers that are optimized for your exact requirements. This customization goes beyond mere dimensions and materials; it encompasses a holistic approach to design, functionality, and performance, ensuring that the rollers contribute to the efficiency and effectiveness of your operations.
Reduced Maintenance and Downtime: Guide rollers designed with your specific needs in mind are more likely to withstand the rigors of your operational environment, leading to fewer failures and less wear and tear. This reliability translates into reduced maintenance requirements, less downtime for repairs, and, ultimately, a more streamlined and uninterrupted production process.
Cost Efficiency Over Time: While the initial cost of custom-tailored guide rollers might be higher than off-the-shelf options, the long-term savings are significant. Optimized performance leads to lower operational costs, fewer replacements, and reduced maintenance expenses. Over time, these savings can amount to a substantial financial advantage, making the investment in a well-aligned manufacturer financially prudent.
Access to Expertise and Support: Manufacturers that align with your project needs often provide more than just products; they offer their expertise and support. This can be invaluable in navigating challenges, optimizing your systems, and making informed decisions about upgrades or expansions. Their insights can help you avoid common pitfalls and leverage industry best practices.
Future-Proofing Your Operations: As your operations evolve, having a manufacturer that understands your business can help you adapt and grow. Whether it’s scaling up production, integrating new technologies, or responding to changing market demands, a manufacturer aligned with your needs can be a strategic partner in your growth, offering solutions that accommodate your evolving requirements.
Strengthening Supply Chain Reliability: In today’s global economy, supply chain disruptions can have a profound impact on your operations. Working with a manufacturer that is attuned to your specific needs helps ensure a more reliable supply chain, with better communication, faster response times, and a mutual commitment to maintaining stock levels and meeting delivery timelines.
The decision to select a guide rollers manufacturer that aligns with your specific project needs is a strategic one, with implications for performance, cost, reliability, and growth. It’s about finding a partner that not only supplies a product but also contributes to the success and efficiency of your operations. This partnership can become a competitive advantage, enabling your business to operate more smoothly, adapt more quickly, and grow more sustainably.
Spotlight on Top Guide Rollers Manufacturers
In the realm of industrial operations, the quality and reliability of guide rollers can significantly impact the efficiency and longevity of machinery. As such, choosing the right guide rollers manufacturer is not just a matter of convenience but a critical strategic decision. This section shines a spotlight on top guide rollers manufacturers, each distinguished by their commitment to quality, innovation, and customer satisfaction. These manufacturers have been carefully selected based on their industry reputation, product quality, and ability to meet a wide range of customer needs. By exploring the offerings and strengths of these leading companies, you can gain insights into which manufacturer might best align with your operational requirements and project specifications. Let’s delve into the specifics of these top-tier guide rollers manufacturers, highlighting their unique contributions to the industry and how they stand out in the competitive landscape.
American Urethane, Inc. and Other U.S. Based Manufacturers
American Urethane, Inc. stands out for its robust offerings in urethane guide rollers, known for their durability and performance. Here are key highlights:
- Specialization in Urethane: Offers superior resistance to wear and tear.
- Custom Solutions: Capable of producing customized rollers for specific applications.
- Industry-Leading Quality: Adheres to high-quality standards for all products.
- Diverse Applications: Serves a wide range of industries from automotive to conveyor systems.
- Rapid Prototyping: Provides quick prototypes for testing and validation.
- Experienced Staff: Employs knowledgeable staff to assist with selection and customization.
- After-Sales Support: Offers excellent customer service and support post-purchase.
Other notable U.S.-based manufacturers include companies like Weaver Industries, Inc., and REDCO Rubber Engineering & Development Company, each bringing their own strengths and specializations to the table, from rubber to polyurethane guide rollers.
Global Manufacturers: Imao Corporation, FATH GmbH, and More
On the global stage, Imao Corporation and FATH GmbH are among the leaders in the guide rollers market. Imao Corporation is renowned for its precision engineering and innovative designs, while FATH GmbH excels in providing robust solutions for the automotive and construction industries. These manufacturers offer unique advantages such as:
- Global Reach: Ability to serve customers worldwide.
- Innovative Products: Continual investment in R&D for cutting-edge solutions.
- Comprehensive Product Lines: Wide range of guide rollers to meet diverse global standards.
- Customization: Tailored solutions for specific regional needs.
- Technical Expertise: Deep understanding of global industry challenges.
- Logistical Capabilities: Efficient distribution networks.
- Cultural Understanding: Ability to navigate cultural differences in business practices.
Specialty Manufacturers
Specialty manufacturers focus on guide rollers for extreme conditions or specific industries, offering products that are not commonly found in the broader market. These manufacturers excel in areas such as high-temperature environments, corrosive conditions, or ultra-precise applications. They distinguish themselves by:
- Niche Expertise: Deep knowledge in specialized applications.
- Innovative Materials: Use of materials that are tailored for extreme conditions.
- Custom Engineering: Ability to design products for highly specific requirements.
- Advanced Testing: Rigorous testing protocols for niche applications.
- Collaborative Design Process: Working closely with clients to develop bespoke solutions.
- Rapid Response: Agility in responding to unique industry challenges.
- Global Partnerships: Collaborations with experts and institutions to advance technological capabilities.
Choosing the right guide rollers manufacturer involves a careful evaluation of your specific needs against the capabilities and offerings of potential suppliers. Whether you’re looking for a versatile provider like American Urethane, Inc., a global powerhouse like Imao Corporation, or a specialty manufacturer, the key is to partner with a company that can deliver the quality, reliability, and innovation your operations require.
How to Find Guide Rollers Manufacturers Near You
In today’s globalized market, the quest to find the right supplier for essential components like guide rollers can seem daunting. However, focusing your search locally can unveil a plethora of advantages, from logistical efficiencies to enhanced collaboration opportunities. Here are eight practical tips for locating guide rollers manufacturers in your vicinity, ensuring you can capitalize on the benefits of local sourcing.
Tips for Locating Guide Rollers Manufacturers
Navigating the industrial landscape to find a reliable guide rollers manufacturer near you requires a strategic approach. Employing a combination of digital tools and traditional networking methods can uncover valuable local manufacturing partners. Here’s how:
- Online Industrial Directories: Start with a thorough search in online directories dedicated to industrial manufacturers to find local guide rollers manufacturers.
- Trade Shows and Expos: Industry-specific trade shows are goldmines for connecting with manufacturers showcasing their latest products and capabilities.
- Industry Associations: Membership in relevant industry associations can open doors to a network of manufacturers and suppliers in your area.
- Local Business Listings: Don’t overlook local business listings and chambers of commerce, which are excellent resources for identifying nearby manufacturers.
- Search Engines: A targeted search using specific keywords and your location can yield surprisingly specific results.
- Social Media and Forums: Engage with industry forums and social media platforms where professionals share recommendations and experiences.
- Supplier Databases: Utilize comprehensive supplier databases that provide detailed profiles on manufacturers, including their geographic location.
- Networking: Tap into your existing professional network for personal endorsements of guide rollers manufacturers.
Benefits of Partnering with Local vs. International Manufacturers
Choosing between local and international manufacturers involves weighing various factors, including cost, communication, and logistical considerations. Here’s why local might be the way to go:
The decision to source guide rollers from local manufacturers as opposed to international ones comes with a host of benefits that can significantly impact your project’s success. From logistical advantages to fostering stronger business relationships, the choice of a local supplier can be a strategic move. Here are the key benefits of partnering with local guide rollers manufacturers, highlighting the strategic advantages of local sourcing.
- Reduced Shipping Costs and Times: Opting for a local manufacturer can drastically cut shipping costs and delivery timelines, directly benefiting project schedules and budgets.
- Easier Communication: Proximity facilitates smoother communication, allowing for real-time discussions and quicker resolutions to any arising issues.
- Quicker Response to Changes: Local suppliers can adapt more rapidly to changes in demand or project specifications, offering a level of agility that is often needed in fast-paced industries.
- Quality Control Visits: Being nearby enables more frequent quality checks and face-to-face meetings, ensuring product standards are consistently met.
- Supporting Local Economy: Choosing local manufacturers boosts the local economy, potentially leading to mutual growth and community benefits.
- Easier Verification of References: Assessing the reliability and quality of a local manufacturer is often more straightforward, thanks to accessible references and the possibility of site visits.
- Cultural Alignment: Sharing a similar business culture can simplify negotiations and foster a more cohesive working relationship.
- Environmental Benefits: Local sourcing reduces the carbon footprint associated with transportation, aligning with eco-friendly business practices.
In essence, leveraging local guide rollers manufacturers not only supports your immediate project needs but also contributes to broader economic and environmental goals. By following these tips and considering the benefits, businesses can make informed decisions that align with their strategic objectives and operational requirements.
To Select Used Guide Rollers Manufacturers
Opting for used guide rollers can be a savvy business decision, offering significant cost savings without necessarily sacrificing quality. However, the key to success lies in choosing the right manufacturers or suppliers of used equipment. This decision is nuanced and requires careful consideration of several critical factors. Below, we delve into the essential aspects to consider when selecting used guide rollers manufacturers, ensuring you make a choice that aligns with your operational needs and quality standards.
Considerations When Opting for Used Guide Rollers
The decision to purchase used guide rollers comes with its own set of challenges and considerations. Unlike new equipment, used rollers have a history, and understanding that history is crucial to making an informed purchase. Here are nine vital considerations to guide you through selecting reputable used guide rollers manufacturers:
- Quality Assurance: It’s imperative to ensure that any used equipment, especially guide rollers, meets your operational standards and requirements.
- Warranty: A warranty on used equipment speaks volumes about the manufacturer’s confidence in their product.
- Support: Adequate support from the manufacturer can mitigate many of the risks associated with purchasing used equipment.
- Reputation: The manufacturer’s reputation in the market can give you insight into the likely quality and reliability of their used guide rollers.
- Condition and History: Understanding the specific history and condition of the equipment you’re considering is crucial.
- Compatibility: Ensuring that the used guide rollers will work with your existing systems is a must.
- Certification: Certifications can provide assurance that the equipment meets certain standards.
- Return Policy: Knowing you have the option to return the equipment if it doesn’t meet your needs offers peace of mind.
- Cost-Benefit Analysis: Finally, weighing the upfront savings against potential future costs is a critical step in the decision-making process.
Recommended Practices for Vetting Suppliers of Used Equipment
Finding a trustworthy supplier of used guide rollers manufacturers requires diligence and a strategic approach. To ensure you’re making the best investment for your needs, follow these recommended practices for vetting suppliers:
- Visit in Person: There’s no substitute for seeing the equipment and the operation in person.
- Request Documentation: Documentation can provide a transparent history of the equipment’s condition and maintenance.
- Seek References: References from other customers can offer invaluable insights into the supplier’s reliability and the equipment’s performance.
- Ask for a Demonstration: A demonstration can reveal much about the equipment’s current operational state.
- Inquire About After-Sales Support: Understanding the level of support available after purchase can influence your decision.
- Negotiate Warranty Terms: A favorable warranty can protect your investment and provide additional security.
- Assess the Supplier’s Expertise: The supplier’s knowledge can be a resource in itself, offering added value to your purchase.
- Compare Multiple Suppliers: Finally, comparing options allows you to ensure you’re getting the best value and fit for your needs.
Selecting used guide rollers manufacturers is a process that demands attention to detail and a thorough evaluation of your options. By considering these factors and employing these vetting practices, you can confidently navigate the market for used guide rollers, securing equipment that meets your needs while optimizing your investment.
Best Practices in Choosing Guide Rollers Manufacturers
Selecting the right guide rollers manufacturers is a critical decision that can significantly impact the efficiency and longevity of your machinery. The process involves more than just finding a supplier; it requires a strategic approach to ensure that the guide rollers you choose are perfectly suited to your needs. Here are some best practices to consider when making this important decision, ensuring you get the best value and performance from your chosen manufacturer.
Assessing Your Project’s Requirements
Before initiating contact with guide rollers manufacturers, a thorough understanding of your project’s unique demands is paramount. This foundational step is not just about quantifying the number of rollers needed but delving into the specifics of their application. Here are key aspects to consider:
- Operational Load: Evaluate the maximum load the rollers will need to support. This includes both static and dynamic loads, as underestimating can lead to premature failure of the rollers.
- Environmental Conditions: The operating environment plays a crucial role in selecting the right type of guide rollers. High temperatures, exposure to chemicals, or corrosive conditions necessitate rollers made from materials specifically designed to withstand these challenges.
- Operational Speed: The speed at which the rollers will operate affects their design and material selection. High-speed applications may require rollers with special bearings or lubrication to ensure longevity and efficiency.
- Application Specifics: Consider the specific application of the guide rollers within your machinery. Are they part of a conveyor system, guiding materials through a production line, or used in a precision application where alignment is critical? The application will dictate the roller design, material, and surface finish.
- Maintenance and Accessibility: Assess how easily the rollers can be accessed for maintenance or replacement. Rollers that are difficult to reach or require significant downtime to replace may benefit from materials with longer life spans or designs that facilitate easier maintenance.
- Compatibility with Existing Systems: Ensure that the new rollers are compatible with your existing machinery. This includes physical dimensions, mounting configurations, and integration with the overall system.
- Regulatory and Safety Requirements: Be aware of any industry-specific regulations or safety standards that the guide rollers must comply with. This can include food safety standards for processing equipment or explosion-proof requirements for rollers used in hazardous environments.
- Future Scalability: Consider future needs and potential scalability. Will the rollers need to accommodate increased loads or speeds? Selecting a manufacturer that can provide solutions for both current and future needs can save time and resources in the long run.
By meticulously assessing these factors, you can ensure a comprehensive understanding of your project’s requirements. This not only facilitates more effective communication with potential guide rollers manufacturers but also ensures that the solutions provided are perfectly tailored to meet the operational demands of your machinery, thereby optimizing performance and extending the lifespan of your equipment.
To Understand the Variety of Rollers Available and Their Applications
The world of guide rollers is diverse, with each type designed to meet specific operational needs. Familiarizing yourself with the different types of rollers and their intended applications is essential in making an informed decision. Let’s explore some common varieties:
Guide rollers come in various designs, materials, and sizes, each suited to different applications. Here are six examples of guide rollers to help you understand the variety available:
- Urethane Rollers: Ideal for high-friction environments where durability and resistance to wear are crucial.
- Steel Rollers: Best suited for heavy-duty applications where high load-bearing capacity is needed.
- Nylon Rollers: Offer a lightweight option with good wear resistance, suitable for light to medium load applications.
- Stainless Steel Rollers: Perfect for corrosive environments, offering durability and resistance to rust.
- Plastic Rollers: Useful in applications requiring low weight and low noise, with moderate durability.
- Rubber-Coated Rollers: Provide excellent grip and noise reduction, ideal for conveying systems.
Tips for Ensuring You Get the Best Value and Performance
Choosing the right guide rollers manufacturers is about more than just finding a supplier; it’s about securing a partnership that will contribute to the success and efficiency of your operations. To ensure you get the best value and performance from your chosen manufacturer, consider the following tips:
- Research and Compare: Don’t settle for the first guide rollers manufacturers you find. Research and compare multiple suppliers to ensure you’re getting the best value.
- Check References and Reviews: Look for reviews and ask for references to gauge the manufacturer’s reliability and the quality of their products.
- Inquire About Customization: If your application requires it, ensure the manufacturer can provide customized solutions.
- Ask About Material Options: Different applications may require different materials. Discuss your needs with the manufacturer to find the best material for your rollers.
- Consider Lead Times: Ensure the manufacturer can meet your timeline without compromising quality.
- Evaluate Technical Support: A manufacturer that offers excellent technical support can be invaluable in ensuring your rollers perform optimally.
- Discuss Warranty and Return Policies: Understanding the warranty and what happens if the product doesn’t meet your expectations is crucial.
- Focus on Total Cost of Ownership: Look beyond the initial purchase price to consider the total cost of ownership, including maintenance, replacement, and operational efficiency.
By following these best practices in choosing guide rollers manufacturers, you can ensure that you select a partner that not only meets but exceeds your expectations. This strategic approach will help you achieve optimal performance and value from your guide rollers, contributing to the overall success and efficiency of your operations.
FAQs about Guide Rollers Manufacturers
Guide rollers are essential components in various mechanical systems, designed to control the movement and direction of moving parts. They play a pivotal role in guiding, supporting, and positioning materials or objects along a predetermined path in machinery. These rollers are commonly found in conveyor systems, printing machines, and in applications requiring precise motion control. The effectiveness of guide rollers is determined by their design, material composition, and the specific application they are intended for. By minimizing friction and providing a smooth surface for materials to move over, guide rollers enhance operational efficiency, reduce wear on machinery, and help maintain the accuracy of movement, contributing significantly to the reliability and longevity of mechanical systems.
The manufacturing process of rollers varies depending on the material used and the specific requirements of the application. Generally, it involves several key steps: material selection, machining, surface treatment, and assembly. For metal rollers, the process starts with cutting and shaping the metal to the desired dimensions, followed by machining operations to achieve the precise shape and surface finish. Plastic and rubber rollers often begin with the mixing of raw materials, followed by molding or extrusion to form the roller shape. Surface treatments, such as coating or texturing, are applied to enhance performance characteristics like friction, wear resistance, or chemical resistance. Finally, components such as bearings are assembled with the roller body to complete the manufacturing process. Advanced manufacturing techniques, including CNC machining and injection molding, allow for high precision and customization in roller production.
The HS (Harmonized System) code for guide rollers is a standardized international code used to classify traded products. The specific HS code for guide rollers can vary depending on the country and the detailed classification of the product. Generally, guide rollers fall under a category related to machinery parts, with codes often starting with 84, which denotes machinery and mechanical appliances. For precise classification, it’s important to consult the customs tariff codes in the specific country of import or export. These codes are crucial for determining import duties, taxes, and for compliance with local regulations. Businesses involved in the trade of guide rollers should ensure they use the correct HS code to avoid customs delays and penalties.
Rubber rollers are made from various types of rubber, depending on their intended use and the properties required for the application. The most common materials include natural rubber, neoprene, nitrile, silicone, and polyurethane. Each type of rubber offers distinct characteristics. For example, natural rubber is prized for its elasticity and tensile strength, making it suitable for applications requiring flexibility and durability. Neoprene offers good chemical stability and resistance to heat, oil, and weathering, suitable for industrial applications. Nitrile rubber is resistant to oil and acids, making it ideal for use in printing and industrial applications. Silicone rubber provides excellent high-temperature resistance and is often used in food processing and medical equipment. Polyurethane rollers offer outstanding abrasion resistance and load-bearing capacity. The selection of rubber material is critical to the roller’s performance, lifespan, and compatibility with the application environment.
Last Updated on April 12, 2024 by Jordan Smith
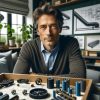
Jordan Smith, a seasoned professional with over 20 years of experience in the conveyor system industry. Jordan’s expertise lies in providing comprehensive solutions for conveyor rollers, belts, and accessories, catering to a wide range of industrial needs. From initial design and configuration to installation and meticulous troubleshooting, Jordan is adept at handling all aspects of conveyor system management. Whether you’re looking to upgrade your production line with efficient conveyor belts, require custom conveyor rollers for specific operations, or need expert advice on selecting the right conveyor accessories for your facility, Jordan is your reliable consultant. For any inquiries or assistance with conveyor system optimization, Jordan is available to share his wealth of knowledge and experience. Feel free to reach out at any time for professional guidance on all matters related to conveyor rollers, belts, and accessories.