The Ultimate Guide to Hardened Steel Rollers
Hardened steel rollers are pivotal components in the machinery of various industries, playing a crucial role in manufacturing, processing, and transportation systems. Their unparalleled durability and resistance to wear and tear make them indispensable for operations that demand high strength and reliability. These rollers come in a myriad of sizes, tailored to specific applications, ensuring optimal performance across different sectors. Whether you’re in the market to purchase these essential parts, seeking examples of their applications, or looking for specifications and maintenance tips to prolong their service life, understanding the nuances of hardened steel rollers is key. This guide aims to shed light on their significance, versatility, and the considerations necessary for their selection and upkeep, providing a comprehensive overview for professionals and enthusiasts alike.
What Are Hardened Steel Rollers
Hardened steel rollers stand as the backbone of numerous industrial operations, embodying strength, durability, and reliability. These components are crafted from steel that has been subjected to a hardening process, significantly enhancing their mechanical properties and suitability for challenging environments. Below, we explore the intricate details of hardened steel rollers, from their composition and manufacturing to the myriad of benefits they bring to industrial applications.
Definition and Explanation of Hardened Steel Rollers:
Hardened steel rollers are more than just industrial components; they are the result of sophisticated engineering designed to meet the rigorous demands of modern machinery. Here’s a closer look at their characteristics:
- Material Composition: At their core, hardened steel rollers are made from alloy or carbon steel, chosen for its ability to undergo transformation through heat treatment, enhancing its hardness and structural integrity.
- Manufacturing Process: These rollers are produced through precise heating and quenching methods, tailored to alter the steel’s internal structure, optimizing it for high-performance applications.
- Application Diversity: From the conveyor belts in manufacturing plants to the rolling lines in metal fabrication, these rollers are versatile, supporting various sectors with their robustness.
- Size Variability: Available in a spectrum of sizes, they are engineered to fit a wide range of machinery, each dimension serving a specific operational purpose.
- Surface Treatment: To further augment their durability, many rollers receive additional treatments like coating or plating, enhancing their resistance to wear and environmental factors.
- Load Capacity: Designed to bear substantial loads, their high strength-to-weight ratio ensures they can support significant weight without compromising performance.
- Maintenance Requirements: Despite their toughness, maintaining these rollers is crucial for longevity, necessitating regular checks for lubrication and wear.
- Customization Options: Recognizing the unique needs of different industries, manufacturers offer customized solutions, providing rollers that perfectly match specific operational requirements.
The Process of Hardening Steel and Its Benefits:
The journey from raw steel to a hardened roller is a testament to the marvels of modern metallurgy, involving several critical steps:
- Heating: Initially, the steel is heated to a temperature that allows its crystal structure to transform, preparing it for hardening.
- Quenching: The steel is then rapidly cooled, a process known as quenching, which locks the carbon within its structure, significantly increasing its hardness.
- Tempering: To ensure the steel isn’t too brittle, it’s reheated to a lower temperature and cooled again, striking a perfect balance between hardness and flexibility.
- Stress Relieving: Optionally, the steel may undergo stress relieving to minimize internal tensions that could lead to warping.
- Surface Finishing: Processes like grinding or polishing are applied to achieve a smooth surface, minimizing friction and enhancing wear resistance.
- Coating: Additional coatings may be applied to bolster the steel’s resistance to rust and corrosion, extending its usable life in harsh conditions.
- Inspection: Rigorous quality checks ensure each roller meets stringent standards for hardness, dimensions, and overall performance.
The hardening process imbues steel rollers with a suite of benefits:
- Increased Durability: This primary advantage means rollers are less susceptible to damage and wear, ensuring a longer lifespan.
- Enhanced Performance: Their capacity to handle high pressures and loads makes them indispensable for heavy-duty machinery.
- Improved Efficiency: The smooth, hardened surface reduces friction, allowing for more efficient operation and energy savings.
- Resistance to Deformation: Maintaining their shape under stress, these rollers guarantee consistent performance.
- Corrosion Resistance: Properly coated rollers can withstand corrosive environments, maintaining their integrity over time.
- Low Maintenance: The need for replacements and repairs drops significantly, thanks to their enhanced durability.
- Versatility: With customization options, they can be adapted to a wide array of industrial tasks.
- Cost-Effectiveness: The long-term savings in maintenance and replacement costs make these rollers a wise investment for any operation.
Hardened steel rollers are indispensable in the industrial world, offering unmatched durability and efficiency. Their production process and the resulting benefits highlight their critical role in maintaining the smooth operation of machinery across various sectors.
Types of Hardened Steel Rollers
The realm of industrial machinery is diverse, and so are the components that ensure its smooth operation. Among these, hardened steel rollers are pivotal, offering unmatched durability and efficiency across various applications. Let’s delve into the specifics of different types of hardened steel rollers, each tailored for distinct industrial needs.
Through-Hardened Stainless Steel Rollers
Through-hardened stainless steel rollers are renowned for their exceptional corrosion resistance and strength, making them ideal for use in harsh environments.
- Composition: Made from high-grade stainless steel, these rollers undergo a thorough hardening process to enhance their durability.
- Hardening Process: The steel is heated to a high temperature and then cooled rapidly, ensuring hardness throughout the entire cross-section.
- Corrosion Resistance: Their stainless steel composition provides excellent resistance against rust and chemical exposure.
- Applications: Widely used in food processing, chemical industries, and anywhere hygiene and corrosion resistance are paramount.
- Maintenance: Requires minimal maintenance due to their corrosion-resistant properties.
- Durability: Offers a longer lifespan in corrosive environments compared to other types of rollers.
- Customization: Available in various sizes and designs to meet specific application requirements.
Quench and Tempered Rolls
Quench and tempered rolls are known for their balanced properties of toughness and hardness, suitable for heavy-duty applications.
- Material: Typically made from medium to high carbon steel or alloy steels.
- Heat Treatment: These rollers are quenched for hardness and then tempered at a lower temperature to achieve toughness.
- Strength: Exhibits high tensile strength, making them capable of withstanding significant stress.
- Toughness: The tempering process ensures they are less brittle, allowing them to absorb impacts without cracking.
- Versatility: Used in applications requiring a balance of strength and durability, such as manufacturing and metal processing.
- Wear Resistance: Offers excellent wear resistance, prolonging the service life of machinery.
- Customization Options: Can be customized in terms of size, hardness level, and surface finishing to suit specific needs.
High Temperature Quench and Tempered Rolls
Designed to withstand extreme temperatures, high temperature quench and tempered rolls are essential for high-heat applications.
- Composition: Crafted from alloys that maintain their properties at elevated temperatures.
- Heat Treatment: Undergo a specialized quenching and tempering process to enhance their high-temperature performance.
- High-Temperature Resistance: Capable of operating efficiently in environments where other materials would weaken.
- Applications: Ideal for use in heat treatment plants, steel mills, and other high-temperature settings.
- Durability: Maintains structural integrity and hardness even under extreme heat.
- Maintenance: Requires regular inspection to ensure performance is not compromised by prolonged exposure to high temperatures.
- Customization: Available in various dimensions and materials tailored for high-temperature applications.
Tool Steel Rolls
Tool steel rolls are crafted for precision and wear resistance, making them suitable for specialized applications that require intricate detailing.
- Material: Made from high-quality tool steels, known for their hardness and resistance to abrasion.
- Hardening Process: These rollers undergo a precise hardening process to achieve a high level of wear resistance.
- Wear Resistance: Exceptionally resistant to wear and deformation, ensuring precise operation over time.
- Applications: Commonly used in cold rolling mills, tube forming, and applications requiring high precision.
- Toughness: Despite their hardness, they maintain sufficient toughness to prevent cracking under stress.
- Surface Finish: Often finished to a high degree of smoothness to ensure the quality of the processed material.
- Customization: Can be produced in various sizes and hardness levels, depending on the specific requirements of the application.
Each type of hardened steel roller offers unique properties and benefits, making them indispensable in their respective fields. From withstanding corrosive environments to enduring high temperatures and providing precision in manufacturing, these rollers are key to the efficiency and longevity of industrial machinery.
Sizes and Specifications of Hardened Steel Rollers
In the industrial world, hardened steel rollers are indispensable components, playing a pivotal role in the functionality and efficiency of various machines. The effectiveness of these rollers is largely determined by their sizes and specifications, which need to be meticulously matched to the demands of specific applications. Below, we delve into the common sizes and dimensions of hardened steel rollers, followed by an exploration of the hardened steel number and its significance in terms of material properties.
Common Sizes and Dimensions
The dimensions of hardened steel rollers are critical to their performance, influencing factors such as load capacity, durability, and compatibility with machinery. Here are key aspects to consider:
- Diameter Range: The diameter of hardened steel rollers can vary significantly, tailored to the scale of operations, from precision applications requiring small rollers to heavy-duty industrial machines needing large diameters.
- Length Variability: Lengths of these rollers are just as diverse, designed to accommodate the width of materials they transport or process, ensuring uniform application of force or pressure.
- Wall Thickness: The thickness of the roller walls is engineered to withstand the operational loads, with thicker walls offering greater strength for heavier duties.
- Axle Sizes: Axle dimensions are standardized to some extent to ensure compatibility with existing machinery, bearings, and installation setups, facilitating easy integration or replacement.
- Surface Finish: The finish on the surface of hardened steel rollers can be customized to meet the needs of the application, affecting friction, material handling, and longevity.
- Tolerance Levels: Precision in manufacturing ensures that these rollers meet exacting tolerance specifications, crucial for applications where accuracy and minimal deviation are paramount.
- Custom Dimensions: For unique applications, custom-sized rollers can be manufactured, providing solutions that precisely meet the specific requirements of specialized machinery.
Hardened Steel Number and Material Properties
The hardened steel number is a key identifier that provides insights into the steel’s composition and its suitability for various applications. Understanding this number is essential for selecting the right material for hardened steel rollers:
- Definition: This number classifies the steel based on its alloy composition and heat treatment potential, guiding the selection process for specific industrial uses.
- Carbon Content: A higher number typically signifies greater carbon content, which is directly linked to the steel’s hardness and strength after heat treatment.
- Alloying Elements: Elements such as chromium, molybdenum, and vanadium, indicated by the steel number, enhance the material’s properties, including hardenability and resistance to wear.
- Heat Treatment Compatibility: The steel grade, as suggested by its number, informs about its adaptability to heat treatment processes, crucial for achieving desired hardness levels.
- Tensile Strength: The grade can also hint at the steel’s tensile strength, indicating how well the roller can resist breaking under tension.
- Impact Resistance: Some steel grades are engineered for superior impact resistance, making them suitable for high-stress applications.
- Wear Resistance: The composition detailed by the steel number plays a significant role in the material’s resistance to wear, essential for rollers in abrasive environments.
- Corrosion Resistance: While not always directly indicated, certain alloying elements suggest the steel’s ability to withstand corrosive conditions, an important consideration for rollers exposed to harsh elements.
By carefully considering the sizes, dimensions, and material properties indicated by the hardened steel number, engineers and designers can ensure that the selected hardened steel rollers are perfectly suited to their application, optimizing performance and extending the lifespan of the machinery they are a part of.
Applications in Industry of Hardened Steel Rollers
Hardened steel rollers are integral to the operations of a myriad of industries, providing the robustness and reliability needed for continuous, high-stress processes. Their unparalleled durability and precision make them indispensable in environments where performance and longevity are paramount. Below, we explore eight industries that significantly benefit from the use of hardened steel rollers, highlighting the specific applications and machinery that rely on these essential components.
Aerospace: In the aerospace industry, hardened steel rollers are crucial for manufacturing and maintenance processes. They are used in the production of aircraft components, where precision and strength are non-negotiable. Rollers are found in machinery that shapes and cuts aerospace materials, including metals and composites, ensuring components meet the exacting standards required for airworthiness.
Food Processing: The food processing industry relies on hardened steel rollers for the conveyance and processing of food products. These rollers are used in equipment ranging from conveyor belts to machines that shape and mold food items. Their resistance to corrosion and ease of cleaning make them ideal for maintaining the strict hygiene standards required in food production.
Paper and Plastic Manufacturing: In paper and plastic manufacturing, hardened steel rollers play a pivotal role in the pressing, cutting, and finishing processes. They ensure uniform thickness and smoothness of the final product, whether it’s paper, plastic film, or packaging materials. The rollers’ hardness and precision are critical for controlling the quality and consistency of these widely used materials.
Steel Service Centers: Steel service centers, which provide steel processing services, utilize hardened steel rollers in a variety of applications, including cutting, shaping, and finishing steel products. These rollers are essential for ensuring the steel meets specific size and finish requirements before it is distributed for further manufacturing.
Automotive Manufacturing: The automotive industry benefits from hardened steel rollers in the production of vehicle components. Rollers are used in the stamping, forming, and assembly lines, contributing to the manufacture of parts ranging from body panels to engine components, where durability and precision are crucial.
Textile Industry: In the textile industry, hardened steel rollers are used in the weaving, treating, and finishing of fabrics. They ensure the consistent tension and alignment of threads, contributing to the high-quality finish of textiles used in clothing, upholstery, and industrial applications.
Printing and Packaging: Hardened steel rollers are vital in the printing and packaging industries for the precise application of inks and the production of packaging materials. They ensure even pressure distribution during the printing process, resulting in high-quality, consistent prints for various applications.
Material Handling and Logistics: For material handling and logistics, hardened steel rollers are used in conveyor systems and sorting machinery, facilitating the efficient movement and organization of goods. Their durability ensures reliable operation in high-throughput environments, where downtime can significantly impact productivity and costs.
Discussion on Usage in Specific Machinery and Processes
The utilization of hardened steel rollers extends into nuanced applications across various sectors, each with its distinct operational challenges and requirements. This expanded discussion explores additional machinery and processes, emphasizing the unique contributions of hardened steel rollers to industrial efficiency and innovation.
High-Speed Printing Equipment
In the realm of high-speed printing, hardened steel rollers are pivotal for ensuring the smooth transfer of ink and precise alignment of paper or other media. These rollers must exhibit exceptional surface smoothness and hardness to prevent any deformation under high operational speeds, which could lead to printing errors or inconsistencies. Their role in maintaining tension and feeding paper uniformly is critical in achieving high-quality print outputs at rapid production rates.
Laminating Machines
Laminating machines, which apply protective films to various materials, rely on hardened steel rollers to apply even pressure across the material being laminated. These rollers must resist adhesive build-up and maintain their dimensional integrity at elevated temperatures, ensuring a bubble-free and uniform application of laminating films. The hardness of the steel prevents surface marring, which is crucial for optical clarity in laminated products.
Cable and Wire Drawing Equipment
In the production of cables and wires, hardened steel rollers guide and shape metal strands with precision. These rollers face constant friction and must withstand the wear from metal wires being drawn at high tensions. The specific hardness of the rollers is critical to prevent grooving or damage that could impair the wire’s quality or cause breaks during the drawing process.
Pharmaceutical Tablet Presses
In the pharmaceutical industry, hardened steel rollers are employed in tablet presses where precision and hygiene are paramount. These rollers must withstand the compressive forces used to form tablets while maintaining a contaminant-free surface that meets stringent health and safety standards. The hardness of the steel ensures longevity and reliability in these critical applications.
Automated Sorting Systems
Automated sorting systems in logistics and distribution centers utilize hardened steel rollers for the reliable movement and sorting of packages. These systems demand rollers that can support heavy loads and operate flawlessly over extended periods. The durability of hardened steel rollers minimizes maintenance downtime, crucial for operations that run around the clock.
Robotic Manufacturing Arms
In advanced manufacturing settings, robotic arms equipped with hardened steel rollers perform tasks such as material handling, assembly, and finishing. The rollers enable these robotic systems to manipulate objects with precision, applying controlled pressure or movement without damaging the materials. The use of hardened steel ensures that these rollers can endure repetitive tasks without wear, maintaining the accuracy and efficiency of robotic operations.
Agricultural Machinery
Hardened steel rollers find applications in agricultural machinery, such as tractors, harvesters, and processing equipment, where they must endure exposure to elements, dirt, and abrasive materials. These rollers facilitate the movement and processing of agricultural products, from grain handling to baling equipment, where their robustness and wear resistance contribute to the machinery’s overall performance and durability.
Hardened steel rollers are a cornerstone of modern manufacturing and processing industries, offering the strength, precision, and durability required to meet the demands of a wide range of applications. Their versatility and performance make them indispensable in the continuous pursuit of efficiency, quality, and innovation across sectors.
Where to Find Hardened Steel Rollers for Sale
In the industrial sector, the quest for components that offer durability, efficiency, and precision is ongoing. Hardened steel rollers, known for their robustness and longevity, are essential in various machinery across multiple industries. However, sourcing these components can be challenging without the right knowledge and understanding of what to look for. Below, we provide comprehensive guidance on purchasing hardened steel rollers, including essential tips for ensuring quality and specifications, followed by a curated list of reputable suppliers and manufacturers.
Tips for Purchasing Hardened Steel Rollers
Selecting the right hardened steel rollers involves more than just finding a suitable price point; it requires a deep dive into the specifics of material quality, manufacturing precision, and supplier reliability. Here are essential considerations to guide your purchase:
- Assess Material Quality: The foundation of a durable roller lies in the quality of steel used. High-grade steel with proper hardening ensures the roller can withstand demanding industrial environments.
- Verify Hardness Specifications: The hardness of the roller dictates its resistance to wear and deformation. Ensure the specifications align with your operational needs for optimal performance.
- Consider Surface Finish: The right surface finish on a roller can significantly affect its function, especially in processes where material handling and precision are critical.
- Evaluate Load Capacity: Understanding the load capacity of the rollers is crucial to prevent premature failure and ensure they can handle the demands of your applications.
- Inspect Manufacturing Precision: Precision in the roller’s dimensions and fit is vital for seamless integration into your machinery and smooth operation.
- Check for Customization Options: Customization can be key for specific applications. Determine if the supplier can accommodate unique size requirements or special features.
- Inquire About Durability and Wear Resistance: A roller’s lifespan and its ability to resist wear are paramount. Discuss these aspects with the supplier to gauge the roller’s suitability for your environment.
- Request References and Reviews: Testimonials from other customers can provide insights into the supplier’s reliability and the product’s real-world performance.
- Compare Pricing and Value: While initial cost is a factor, assess the overall value the rollers bring, considering their durability, maintenance needs, and potential to improve operational efficiency.
Reputable Suppliers and Manufacturers
Finding a trustworthy supplier is as important as the product itself. Here are several renowned companies known for their quality hardened steel rollers and customer service:
- Hi-Hard Corporation: Esteemed for their range of through-hardened and quench and tempered rolls, catering to diverse industrial needs with emphasis on durability.
- isheaves.com: Specializing in both UHMW-PE and hardened steel rollers, they serve industries looking for products with high wear resistance.
- McMaster-Carr: A well-known distributor offering a vast selection of industrial components, including hardened steel rollers, with a reputation for fast delivery.
- Precision Rollers: Dedicated to crafting rollers with exacting standards, they provide custom solutions to meet specific operational requirements.
- Industrial Roller Corporation: Known for their heavy-duty rollers, they focus on products designed for high performance and longevity.
- Roller Technologies, LLC: A specialist in rollers for the printing, packaging, and material handling sectors, offering custom fabrication to meet unique needs.
- Steel Roller Co.: Catering to the steel processing, automotive, and conveyor industries with rollers that prioritize strength and durability.
By adhering to these purchasing tips and considering the highlighted suppliers, businesses can secure hardened steel rollers that enhance their machinery’s performance and reliability, ensuring smooth operations and long-term productivity gains.
Hardened Steel Examples and Recipes for Hardened Steel Rollers
Hardened steel rollers are pivotal in numerous industrial applications, offering unmatched durability and performance under high-stress conditions. The secret behind their exceptional properties lies in the specific types of hardened steel used and the precise “recipes” or compositions that prepare these steels for the rigors of industrial use. Below, we explore several examples of hardened steel used in roller manufacturing, followed by an overview of the composition factors that make steel suitable for hardening and use in roller applications.
Examples of Hardened Steel Used in Roller Manufacturing
The choice of steel significantly impacts the performance and longevity of hardened steel rollers. Here are some of the most commonly used steels in roller manufacturing, each with its unique attributes:
- AISI 4140: This chromium-molybdenum alloy steel is celebrated for its outstanding toughness and tensile strength, making it a popular choice for rollers that require high fatigue strength and resistance to wear.
- AISI 4340: Featuring a rich mix of nickel, chromium, and molybdenum, AISI 4340 alloy steel is known for its high strength and toughness. It’s ideal for applications where rollers are subjected to severe stresses.
- D2 Tool Steel: Distinguished by its high carbon and chromium content, D2 tool steel offers exceptional wear resistance. This makes it suitable for rollers in machinery that must endure abrasive conditions.
- AISI 52100: This high carbon, chromium alloy steel is renowned for its excellent hardness and wear resistance, qualities that are essential for bearing and high-load roller applications.
- C45 Steel: As a medium carbon steel, C45 offers a balanced toughness and strength, suitable for rollers in applications that demand durability without the extreme conditions of high wear or impact.
- A2 Tool Steel: With a good balance between hardness and toughness, A2 tool steel is used in rollers where both wear resistance and impact strength are necessary, providing a versatile solution for various machinery.
- S7 Tool Steel: Known for its shock-resisting properties, S7 tool steel is the go-to for rollers in equipment experiencing high impact or shock loads, ensuring resilience and longevity under tough conditions.
Each of these steel types brings specific advantages to hardened steel rollers, from wear resistance and toughness to shock absorption. The selection of steel is a critical step in the manufacturing process, directly influencing the roller’s ability to perform under the demanding conditions of industrial applications. By choosing the appropriate steel type, manufacturers can ensure their rollers meet the highest standards of durability and efficiency, contributing to the overall performance and reliability of the machinery.
Composition and Recipe for Hardening Steel for Roller Applications
The process of creating hardened steel suitable for rollers involves a careful selection of base materials and a controlled heat treatment process. Here are key points in the composition and recipe for hardening steel:
- Carbon Content: The foundation of hardening, carbon content significantly affects the steel’s potential hardness. Higher carbon content allows for greater hardness after heat treatment.
- Alloying Elements: Elements like chromium, molybdenum, nickel, and vanadium are added to improve hardenability, wear resistance, and toughness.
- Heat Treatment: Proper heat treatment is crucial, involving heating the steel to a specific temperature before quenching it rapidly to lock in the hardness.
- Tempering: After quenching, steel is tempered by reheating to a lower temperature to reduce brittleness while maintaining hardness.
- Stress Relieving: This optional step can be performed to reduce internal stresses caused by the hardening process, improving the steel’s dimensional stability.
- Surface Treatment: Additional treatments like carburizing or nitriding can be applied to enhance surface hardness and resistance to wear.
- Microstructure Control: The heat treatment process aims to achieve a specific microstructure, typically martensite, that provides the desired combination of hardness and toughness.
- Quality Control: Throughout the manufacturing process, rigorous quality control measures ensure that the steel meets the specific requirements for hardness, toughness, and wear resistance.
The recipe for hardening steel for rollers is a complex balance of chemistry, heat treatment, and finishing processes. Each step is meticulously controlled to produce hardened steel rollers capable of withstanding the demanding conditions of industrial applications. By understanding the composition and processes involved in creating these materials, manufacturers can tailor the properties of hardened steel rollers to meet the precise needs of their machinery and processes, ensuring optimal performance and longevity.
Maintenance and Care of Hardened Steel Rollers
The durability and efficiency of hardened steel rollers are critical for the smooth operation of various industrial applications. However, to ensure these rollers maintain their optimal performance and longevity, a structured maintenance and care regimen is essential. Below, we delve into the practices necessary to maintain and extend the life of hardened steel rollers, followed by a discussion on the feasibility and considerations involved in softening or reworking hardened steel.
How to Maintain and Extend the Life of Hardened Steel Rollers
Maintaining hardened steel rollers is not just about preserving their physical condition; it’s about ensuring the continuous productivity and efficiency of the machinery they are part of. Here are key practices:
- Regular Cleaning: Dust, debris, and other contaminants can accelerate wear. Regular cleaning prevents buildup that can damage the roller surface.
- Lubrication: Proper lubrication reduces friction, one of the primary causes of wear. Use the correct lubricant as specified by the manufacturer and apply it at recommended intervals.
- Inspection: Routine inspections can identify issues like cracks, wear, or misalignment early, before they lead to significant damage or operational failures.
- Load Management: Adhering to the specified load capacities prevents overloading, which can cause deformation or cracking of the rollers.
- Environmental Protection: Shielding rollers from harmful environmental conditions such as moisture and corrosive chemicals helps prevent rust and corrosion.
- Surface Treatment Checks: Regularly inspect any coatings or treatments for signs of wear or damage, as these can offer critical protection against corrosion and wear.
- Alignment and Calibration: Ensuring rollers are correctly aligned within the machinery prevents uneven wear and operational inefficiencies.
- Replacement of Worn Parts: Timely replacement of rollers or their components that show excessive wear helps maintain the overall health of the machinery.
Can You Soften Hardened Steel? Addressing Common Questions and Misconceptions
The possibility of softening or reworking hardened steel raises several questions about the practicality and implications of such processes. Here, we address common inquiries and misconceptions:
- Reversibility of Hardening: Annealing can soften hardened steel by altering its microstructure, though this may not always be advisable or practical for all components.
- Welding and Hardness: Welding can locally alter the hardness of steel, potentially necessitating post-weld treatments to restore original properties.
- Repairability: While minor repairs are often feasible, significant damage may compromise the structural integrity, making replacement a safer option.
- Rehardening Considerations: Rehardening repaired areas is possible but requires careful control to avoid introducing new stresses or distortions.
- Risks of Softening: Altering the hardness of steel can impact its mechanical properties, potentially diminishing its suitability for the original application.
- Professional Reworking: Any attempts to soften, repair, or reharden hardened steel should be undertaken by professionals familiar with the material science and heat treatment processes involved.
Understanding the maintenance needs of hardened steel rollers and the complexities of softening or reworking such materials is crucial for industrial operators. Proper care ensures these components continue to function effectively, while knowledge of their material properties informs decisions regarding repairs and modifications, ultimately contributing to the longevity and reliability of the machinery they support.
Last Updated on July 11, 2024 by Jordan Smith
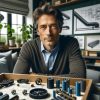
Jordan Smith, a seasoned professional with over 20 years of experience in the conveyor system industry. Jordan’s expertise lies in providing comprehensive solutions for conveyor rollers, belts, and accessories, catering to a wide range of industrial needs. From initial design and configuration to installation and meticulous troubleshooting, Jordan is adept at handling all aspects of conveyor system management. Whether you’re looking to upgrade your production line with efficient conveyor belts, require custom conveyor rollers for specific operations, or need expert advice on selecting the right conveyor accessories for your facility, Jordan is your reliable consultant. For any inquiries or assistance with conveyor system optimization, Jordan is available to share his wealth of knowledge and experience. Feel free to reach out at any time for professional guidance on all matters related to conveyor rollers, belts, and accessories.