Innovations in HDPE Conveyor Roller Technology
HDPE conveyor roller has become integral to modern material handling, leveraging high-density polyethylene’s robust characteristics. These rollers offer significant benefits over traditional materials in conveyor technology, including enhanced durability and reduced wear under continuous operation. Notably, their light weight and resistance to corrosion make them particularly suitable for a range of industrial environments—from mining to food processing. This adaptability ensures that HDPE rollers play a crucial role in improving operational efficiencies across various sectors, providing a reliable solution in demanding industrial applications.
Features of HDPE Conveyor Roller
HDPE conveyor rollers are crafted from ultra-high molecular weight polyethylene, a material chosen for its exceptional endurance and performance under strain. These rollers are designed with multiple layers that enhance their structural integrity and longevity. The core is typically fortified to resist deformation, while the outer shell is smooth to minimize friction and wear on the conveyor belt.
- Construction Flexibility: HDPE conveyor rollers are custom-designed to meet specific requirements, allowing for a range of configurations in terms of length, diameter, and wall thickness. This adaptability makes them suitable for various conveyor setups across different industries.
- Seamless Integration: The ability to integrate HDPE rollers into any existing conveyor system without significant modifications is a critical advantage, ensuring that businesses can upgrade their systems without extensive downtime or retrofitting costs.
- Impact Resistance: Constructed to absorb sudden shocks efficiently, HDPE rollers significantly reduce the risk of damage to the conveyor belt and the rollers themselves during operations involving heavy or uneven loads.
- Chemical Resistance: HDPE’s resistance to aggressive chemicals ensures that these rollers can be employed in environments where corrosive substances are present, such as in chemical processing plants or mining operations where acidic or alkaline materials are handled.
- Moisture Barrier: The non-porous nature of HDPE prevents moisture penetration, which is particularly beneficial in industries like food processing or in geographic areas prone to high humidity, protecting against swelling and structural integrity loss.
- UV Resistance: HDPE rollers are well-suited for outdoor applications as they resist degradation from ultraviolet light, maintaining their performance and appearance over time despite exposure to sunlight.
- Temperature Tolerance: These rollers maintain operational integrity in a diverse range of thermal conditions, from freezing cold to moderate heat, without losing flexibility or strength.
- Low Noise Operation: The density and composition of HDPE help in muffling operational noise, contributing to a more comfortable and compliant work environment, especially in industries where noise pollution is a concern.
The lightweight nature of HDPE conveyor rollers ensures easier handling and installation, reducing labor costs and time. Their abrasion resistance means less material wear and tear, extending the service life of both the rollers and the conveyor belt. Anti-corrosion properties prevent rust and other corrosive damage, enhancing the rollers’ usability in environments like mining or salt processing, where such conditions are prevalent. These properties collectively underscore the HDPE conveyor roller’s suitability for a wide range of industrial applications, reinforcing their status as a versatile and practical choice for modern conveyance needs.
Comparative Analysis: HDPE vs. Traditional Steel Rollers
When comparing HDPE conveyor rollers to traditional steel rollers, several advantages emerge, particularly in terms of noise reduction, energy efficiency, and environmental benefits:
- Noise Reduction: HDPE conveyor rollers operate significantly quieter than steel rollers, reducing noise pollution in work environments. This is crucial for compliance with workplace safety standards.
- Energy Efficiency: The lighter weight of HDPE rollers requires less energy to rotate and move, which lowers energy costs for conveyor systems.
- Reduced Lubrication Needs: HDPE rollers do not require as much lubrication as steel rollers, minimizing maintenance time and costs.
- Corrosion Resistance: Unlike steel, HDPE does not rust or corrode, which is beneficial in wet or corrosive environments.
- Lower Wear and Tear: The softer surface of HDPE causes less wear to conveyor belts compared to the harder steel surfaces.
- Recyclability: HDPE is more environmentally friendly as it is often recyclable, reducing the environmental footprint of the manufacturing process.
- Better at Dampening Vibration: HDPE’s material properties allow it to absorb vibrations better, protecting the conveyor system from the effects of vibration-related wear.
- Cost-Effectiveness: Initially, HDPE rollers may be more expensive, but their longer lifespan and reduced maintenance needs provide cost savings over time.
- Enhanced Safety: The lighter weight of HDPE makes rollers easier and safer to handle during installation and maintenance.
In harsh conditions, HDPE rollers also demonstrate significant operational advantages:
- Chemical Stability: HDPE’s chemical resistance makes it ideal for industries like chemical processing or places where exposure to harsh substances is common.
- Moisture Resistance: HDPE does not absorb moisture, which prevents swelling and structural damage in humid or wet conditions.
- UV Stability: HDPE withstands UV exposure without degrading, making it suitable for outdoor use.
- Non-sparking: Unlike metal, HDPE does not spark, which is critical in explosive environments.
- Temperature Flexibility: HDPE rollers can operate under a broader range of temperatures without losing performance.
- Impact Resistance: HDPE can withstand impacts that would typically dent or deform steel rollers.
- Reduced Conveyor Weight: The light weight of HDPE reduces the overall load and strain on the conveyor infrastructure.
- Low Friction Coefficient: HDPE’s low friction surface enhances the efficiency of the conveyor system.
- Ease of Handling and Installation: The material’s lightness simplifies the processes of handling and installing rollers, reducing labor costs and improving safety.
This comparative analysis highlights the versatility and robustness of hdpe roller conveyor, making them a preferable option in many industrial scenarios over traditional steel rollers.
Key Components and Assembly of HDPE Conveyor Roller
HDPE conveyor rollers are designed with specialized components that significantly enhance their durability and functionality for diverse industrial applications. These rollers are constructed to withstand various environmental conditions, making them ideal for sectors such as mining, food processing, and material handling.
- Core Tube: The core tube, made from high-density polyethylene, offers excellent resistance to chemicals and moisture, preventing degradation and ensuring structural integrity under heavy loads.
- Shaft: Constructed from hardened steel, the shaft provides the necessary support and stability, allowing the roller to handle high axial and radial loads without bending.
- Bearings: High-performance bearings are selected for their ability to reduce friction and withstand high speeds, critical for maintaining smooth roller operations over prolonged periods.
- Seal System: Advanced sealing systems are used to protect the internal components from dust, water, and contaminants, crucial for maintaining the roller’s efficiency in dirty or wet environments.
- End Caps: These components, typically crafted from steel or durable HDPE, help to maintain the roller’s structural integrity by securing the bearings and shaft within the tube.
- Outer Shell: Some HDPE rollers include an outer shell for additional wear resistance, protecting the core tube from direct contact with abrasive materials.
- Snap Rings: Snap rings ensure a secure fit of the end caps, preventing disassembly during operation and maintaining the alignment of internal components.
- Lubrication: Minimal yet essential, the correct lubrication of bearings reduces wear and extends the lifespan of the roller, contributing significantly to the maintenance of its performance.
The assembly of HDPE conveyor rollers involves several precise steps, often detailed in specific manuals that accompany the product:
- Inserting the Shaft: The shaft is inserted into the core tube and aligned correctly.
- Bearing Installation: Bearings are then installed at both ends of the shaft.
- Sealing: Seals are applied to protect the bearings.
- Attaching End Caps: End caps are attached and secured with snap rings.
- Quality Inspection: Rollers are inspected to ensure they meet all operational standards.
- Lubrication: The appropriate lubricant is applied according to the manufacturer’s specifications.
- Testing: Rollers are tested under load and speed to simulate actual working conditions.
- Packaging: Once tested, rollers are packaged for shipment.
- Installation Guide: Detailed installation instructions are provided, ensuring correct setup and integration into the conveyor system.
This careful attention to both component quality and assembly ensures that HDPE conveyor rollers are reliable and efficient for various industrial applications. For detailed maintenance and setup instructions, referring to the specific manufacturer’s manual is recommended.
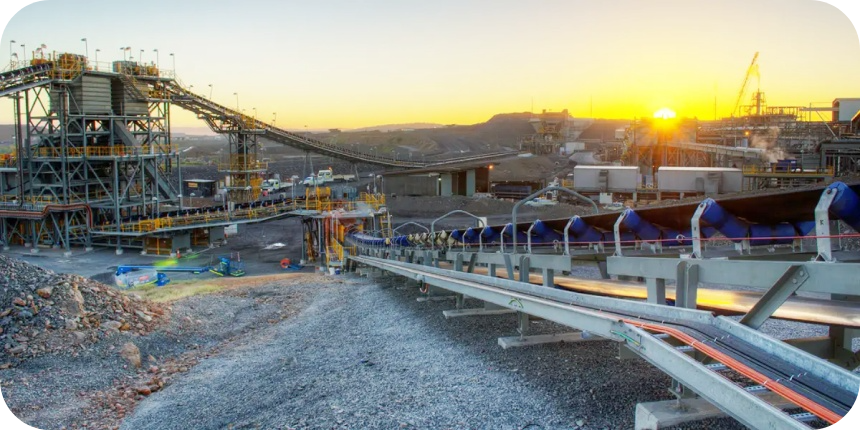
Pricing and Availability of HDPE Conveyor Roller
When considering hdpe roller conveyor, the pricing can be influenced by various factors:
- Material Costs: The cost of high-density polyethylene, the primary material, fluctuates based on crude oil prices, affecting roller prices directly.
- Manufacturing Complexity: Rollers with complex designs or specialized functional requirements can increase production costs due to more intricate manufacturing processes.
- Market Demand: Increases in infrastructure projects can drive up demand and prices; conversely, low demand can decrease them.
- Economies of Scale: Buying in larger quantities typically results in lower per-unit costs due to economies of scale, beneficial for large projects or ongoing needs.
- Customization: Customized dimensions or performance features such as enhanced UV resistance or anti-static properties will lead to higher costs.
- Supplier Location: Suppliers located farther from the point of use may have higher shipping and handling costs which will affect the overall cost.
- Economic Factors: International trade tariffs, import taxes, and the strength of the purchasing currency can impact costs.
- Technological Advances: Innovations in manufacturing technology that increase efficiency and reduce waste can ultimately reduce costs.
To ensure a wise purchase of HDPE conveyor roller, here are some tips:
- Vendor Comparison: Evaluate offerings from multiple suppliers to ensure competitive pricing.
- Bulk Purchasing: Negotiate lower prices for larger orders, which can be especially beneficial for extensive conveyor systems.
- Direct from Manufacturer: Purchasing directly from the manufacturer can eliminate costs associated with distributors or retailers.
- Warranty Offers: Select products with warranties that provide value beyond the initial purchase period, protecting against potential future defects.
- Seasonal Deals: Take advantage of off-peak discounts or end-of-year sales to make purchases.
- Quality vs. Price: Investing a bit more in higher-quality rollers can reduce long-term maintenance and replacement costs.
- Shipping Costs: Include potential shipping costs in budgeting, especially for international orders, which might also include customs duties.
- Long-term Suppliers: Developing long-term relationships with suppliers can lead to better service terms and pricing.
- Industry Reviews: Research reviews and testimonials to assess the reliability and cost-effectiveness of the rollers from different suppliers.
By carefully considering these factors, you can make informed decisions that balance cost, quality, and service, ensuring optimal functionality and value from your HDPE conveyor rollers.
Catalogue Insights and Selection Tips for HDPE Conveyor Roller
When utilizing catalogues like the Rulmeca rollers catalogue for selecting HDPE conveyor roller, here are detailed insights:
- Specification Details: Catalogues typically list detailed technical specifications, including roller diameter, length, and the type of HDPE material used, which are crucial for matching roller capabilities to system requirements.
- Load Capacity: They provide load capacity ratings, helping you choose rollers that can support the weight and stress of your conveyed materials without deforming.
- Speed Ratings: Important for ensuring the rollers can handle the operational tempo of your conveyor system without excessive wear.
- Environmental Suitability: Some rollers are specifically designed for extreme temperatures or corrosive environments, making them ideal for specialized applications.
- Installation Requirements: Detailed setup instructions help ensure that rollers are installed correctly to function optimally and safely.
- Maintenance Guidelines: Maintenance schedules and procedures to prolong the life of the rollers and maintain their efficiency.
- Customization Options: Information on how rollers can be tailored, such as specific bearing types or surface treatments, to meet unique operational needs.
- Comparison Tools: Features like comparison charts or configurators that help you evaluate different roller options side-by-side.
Guidelines for selecting the right HDPE conveyor roller include:
- Assess Load Requirements: Understand the maximum load the conveyor will carry to select rollers that can handle this without failure.
- Evaluate Environmental Conditions: Choose rollers that are built to last in your specific environmental conditions, whether exposed to chemicals, moisture, or UV light.
- Consider Belt Compatibility: Rollers must be compatible with the conveyor belt’s material and design to avoid premature wear or damage.
- Operational Speed Needs: Match the roller’s design speed with the operational speed of your conveyor to ensure efficient performance.
- Longevity and Durability Needs: Consider the expected lifespan and durability of the rollers, especially in abrasive or harsh operational conditions.
- Energy Efficiency Considerations: Opt for rollers that contribute to the overall energy efficiency of the conveyor system by reducing drag and power consumption.
- Ease of Maintenance: Select rollers that offer easy access for maintenance and cleaning to reduce downtime.
- Safety Features: Prioritize rollers with features that enhance safety, such as non-slip surfaces or safety guards.
- Budget Constraints: Balance the initial investment against potential savings from reduced maintenance costs and longer service life.
Using these expanded insights and tips can help you navigate the complexities of selecting the appropriate HDPE conveyor roller, ensuring optimal functionality and cost-effectiveness.
Need Assistance with HDPE Conveyor Roller Selection? Contact Us.
Detailed Insights into HDPE Conveyor Roller
HDPE conveyor rollers are increasingly being implemented across diverse industries, showcasing substantial benefits in performance and cost-effectiveness. Their robust material properties enhance system durability and operational efficiency, making them an attractive alternative to traditional materials like steel. As industries strive for more sustainable and efficient operations, the adoption of HDPE rollers is on the rise, driven by their numerous advantages over conventional options.
Real-World Examples of Industries Benefiting from HDPE Rollers:
HDPE rollers have made a significant impact in various sectors, showcasing their versatility and efficiency:
- Mining: In the harsh environments of mining, HDPE rollers stand up to abrasive materials and heavy loads, reducing the frequency of replacements.
- Food Processing: The non-toxic and easily cleaned surface of HDPE makes these rollers suitable for food conveyance, aligning with industry hygiene standards.
- Packaging: HDPE rollers facilitate a smoother and quieter operation in packaging lines, enhancing workplace conditions and product handling.
- Pharmaceuticals: Their resistance to contamination and easy cleaning supports the strict cleanliness requirements of pharmaceutical manufacturing.
- Recycling Facilities: Known for their durability, HDPE rollers can withstand the challenging conditions of recycling operations, handling heavy and abrasive recyclables with less wear.
- Agriculture: HDPE rollers’ resistance to environmental factors like moisture and chemicals makes them ideal for agricultural applications, where exposure to elements is common.
Impact on Performance and Cost-Effectiveness:
The performance enhancements and cost-saving potentials of HDPE rollers are substantial:
- Reduced Maintenance Costs: The inherent durability of HDPE reduces the need for frequent maintenance checks, lowering long-term operational costs.
- Improved Conveyor Efficiency: Lightweight HDPE rollers require less energy to operate, contributing to lower power consumption and enhanced efficiency.
- Enhanced Longevity: HDPE’s wear-resistant properties extend the operational life of the rollers, decreasing the need for replacements.
- Decreased Downtime: Robust construction minimizes breakdowns, ensuring continuous production flow and reducing idle time.
- Lower Replacement Costs: Longer-lasting rollers mean fewer purchases over time, significantly cutting down replacement expenditures.
- Safety Improvements: HDPE’s non-sparking characteristics enhance safety in explosive-prone environments, adding an extra layer of security.
- Environmental Impact: Using recyclable HDPE contributes positively to environmental sustainability initiatives, aligning with eco-friendly business practices.
These case studies and insights illustrate the broad applicability and significant advantages of incorporating HDPE conveyor roller into various industrial setups, highlighting their role in improving efficiency and reducing costs.
FAQs bout HDPE Conveyor Roller
The rollers on a conveyor are commonly referred to as conveyor rollers. These are the moving parts attached to the conveyor frame, which support and propel the belt or materials being conveyed along the system. They play a critical role in the efficiency and functionality of a conveyor system, influencing speed, load capacity, and the overall smoothness of the material handling process.
Roller conveyors can be classified into several types based on their functionality and the applications they serve. The primary types include gravity roller conveyors, where rollers are inclined or flat and items move by gravity or manual force; powered roller conveyors, which use motors to move the rollers; and accumulation conveyors, designed to allow items to accumulate without manual intervention. Each type is suited to specific operational needs, ranging from light to heavy-duty transport.
The materials used for making conveyor rollers vary depending on their application and load requirements. Common materials include metal (such as steel or aluminum), plastic, and rubber. Metal rollers are durable and suitable for heavy loads, while plastic rollers are lighter and used for lighter loads and quieter operations. Rubber-coated rollers are used for their grip and noise reduction properties. Additionally, high-density polyethylene (HDPE) is often used for its durability and resistance to corrosion and abrasion.
The formula for designing a conveyor roller typically involves calculations to determine the correct roller dimensions, spacing, and material based on the conveyor’s load, speed, and environmental conditions. A basic formula includes considerations for the load per roller, the center distance between the rollers, and the roller diameter. Engineers use these calculations to ensure that the rollers are adequate to support the conveyor belt and the materials being transported, ensuring efficiency and preventing premature wear or failure.
Last Updated on July 24, 2024 by Jordan Smith
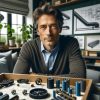
Jordan Smith, a seasoned professional with over 20 years of experience in the conveyor system industry. Jordan’s expertise lies in providing comprehensive solutions for conveyor rollers, belts, and accessories, catering to a wide range of industrial needs. From initial design and configuration to installation and meticulous troubleshooting, Jordan is adept at handling all aspects of conveyor system management. Whether you’re looking to upgrade your production line with efficient conveyor belts, require custom conveyor rollers for specific operations, or need expert advice on selecting the right conveyor accessories for your facility, Jordan is your reliable consultant. For any inquiries or assistance with conveyor system optimization, Jordan is available to share his wealth of knowledge and experience. Feel free to reach out at any time for professional guidance on all matters related to conveyor rollers, belts, and accessories.