Maximizing Efficiency: The Advantages of HDPE Rollers
HDPE rollers, constructed from High-Density Polyethylene (HDPE), represent a significant advancement in conveyor technology. Their innovative design leverages the robustness and lightweight nature of HDPE, offering a durable yet efficient alternative to traditional rollers. These rollers stand out for their resilience against environmental stressors such as corrosion, abrasion, and chemical exposure, making them an ideal choice for various industrial applications. The core advantage of the hdpe roller lies in its ability to reduce the operational strain on conveyor systems, enhancing both longevity and throughput. By integrating HDPE rollers into conveyor systems, industries benefit from a reduction in maintenance requirements and energy consumption, underscoring the role of these components in promoting sustainable and cost-effective material handling solutions. This introduction sets the stage for a deeper exploration into the specifications, applications, and benefits of HDPE rollers in modern conveyor setups.
HDPE Roller Specifications
HDPE rollers, made from high-density polyethylene, are renowned for their exceptional durability and efficiency in various industrial applications. These rollers are designed with a focus on minimizing the maintenance requirements and extending the lifespan of conveyor systems. Let’s explore the detailed specifications that make HDPE rollers a preferred choice for businesses looking to optimize their operations.
Material Properties and Design Features
The cornerstone of the high performance of an HDPE roller lies in its material properties and design features. High-density polyethylene (HDPE) is a thermoplastic polymer known for its high strength-to-density ratio, which provides the rollers with excellent durability and wear resistance. Additionally, HDPE is characterized by its resistance to chemicals, impacts, and abrasion, making it suitable for harsh industrial environments.
HDPE rollers are typically designed with a smooth surface that reduces the friction between the roller and the conveyor belt. This not only helps in decreasing the wear and tear on the belt but also contributes to a more efficient operation with lower energy consumption. The internal structure of these rollers can be reinforced with steel or other materials to enhance their load-bearing capacity and ensure stability under heavy loads.
Operational Benefits
Incorporating HDPE rollers into conveyor systems translates into significant operational benefits. One of the key advantages is the reduced wear on conveyor belts. The smooth surface and material properties of HDPE minimize the friction and abrasion on belts, leading to extended belt life and reduced maintenance costs.
Moreover, HDPE rollers offer increased resistance to environmental factors such as moisture, UV radiation, and temperature fluctuations. This makes them particularly valuable in outdoor or challenging industrial settings, where other materials might degrade more quickly. The inherent corrosion resistance of HDPE further ensures that these rollers remain operational even in the presence of chemicals or salty water, common in mining or marine applications.
Another significant benefit is the weight reduction compared to traditional metal rollers. HDPE rollers are considerably lighter, making them easier to handle and install. This not only reduces the labor cost but also minimizes the operational load on the conveyor system, leading to energy savings and potentially longer equipment life.
The HDPE roller combines its material properties and innovative design features to offer a range of operational benefits. From reduced wear on conveyor belts to improved resistance against environmental challenges, these rollers stand out as a cost-effective solution for enhancing the efficiency and reliability of conveyor systems.
Various Sizes of HDPE Rollers
The versatility of HDPE rollers is significantly enhanced by the wide range of sizes available, catering to diverse industrial requirements. This adaptability ensures that regardless of the application, there’s likely an HDPE roller that fits the specific needs of any conveyor system. Let’s delve into the spectrum of sizes for HDPE rollers and how these dimensions influence their application and functionality within conveyor systems.
Range of Sizes
HDPE rollers are manufactured in a variety of diameters and lengths to accommodate different conveyor belt widths and load requirements. The diameter of an HDPE roller can vary widely, typically ranging from as small as 20mm for light-duty applications to over 200mm for heavy-duty industrial uses. The length of these rollers can also be customized, ensuring a perfect fit for the width of the conveyor belt they are intended to support. This customization allows for precise control over the roller spacing, which is crucial for optimizing the conveyor’s performance and the distribution of the load across the belt.
Impact of Size on Application and Functionality
The size of an HDPE roller plays a critical role in determining its application and effectiveness within a conveyor system. Smaller diameter rollers are generally used in applications where space is limited or for conveyors that handle lightweight materials. These rollers are ideal for intricate machinery where precision and maneuverability are paramount. On the other hand, larger diameter rollers are favored in heavy-duty applications where they can support greater loads and reduce the belt’s curvature, which minimizes wear and extends the life of the conveyor system.
The length of the roller is equally important as it needs to match the width of the conveyor belt. Properly sized rollers ensure even weight distribution, reducing the risk of belt misalignment and slippage, which are common issues that lead to operational inefficiencies and increased maintenance costs. Furthermore, selecting the appropriate roller size can enhance the conveyor system’s energy efficiency by reducing friction and the required drive power.
In addition to the diameter and length, the spacing between rollers must also be considered. Optimal spacing ensures that the conveyor belt is adequately supported across its entire width, minimizing sagging and the potential for material spillage. This not only improves the conveyor’s operational efficiency but also its safety and reliability.
The variety of sizes in which HDPE rollers are available allows for their extensive use across many industries, each with its own set of requirements and challenges. By carefully selecting the appropriate size, businesses can significantly enhance the performance, efficiency, and longevity of their conveyor systems. The adaptability provided by the various sizes of HDPE rollers is a testament to their versatility and effectiveness in meeting the demands of modern industrial operations.
Looking for efficient conveyor rollers? Get in touch now!
Leading HDPE Roller Manufacturers
The market for HDPE rollers is served by several leading manufacturers globally, each bringing a unique set of strengths, innovations, and a commitment to quality and customer service. Among these, companies like Rulmeca stand out for their extensive experience, technological leadership, and comprehensive range of products tailored to meet the diverse needs of industries. Here, we delve into six top manufacturers specializing in HDPE rollers, highlighting what sets them apart in the industry.
Rulmeca
Rulmeca is renowned for its robust and high-quality HDPE rollers, designed to enhance the efficiency and longevity of conveyor systems. This company sets the industry benchmark with its focus on durability, low maintenance, and energy efficiency. Rulmeca’s commitment to innovation is evident in their continuous improvement of product designs and materials to reduce environmental impact and improve operational efficiency. Their global presence ensures accessible customer service and support, making them a preferred partner for many industries worldwide.
Precision Pulley & Idler (PPI)
PPI stands out for its engineering-driven approach to designing and manufacturing HDPE rollers. With a focus on precision and reliability, their products are engineered to meet the specific demands of various applications, ensuring optimal performance. PPI’s dedication to quality is matched by their investment in technology and R&D, aiming to provide solutions that reduce downtime and operational costs.
Martin Sprocket & Gear
Martin Sprocket & Gear is known for its comprehensive range of material handling solutions, including high-quality HDPE rollers. Their products are celebrated for their reliability and performance in demanding environments. Martin’s commitment to customer service, alongside its ability to provide customized solutions, makes it a go-to manufacturer for specialized industrial needs.
Fenner Dunlop
Specializing in conveyor solutions, Fenner Dunlop offers HDPE rollers that are designed for durability and efficiency. Their products are a testament to the company’s dedication to innovation, focusing on reducing the total cost of ownership for their clients. Fenner Dunlop’s rollers are engineered to perform in the most challenging conditions, ensuring reliability and longevity.
Melco Conveyor Equipment
Melco is a leading manufacturer of HDPE rollers, known for their high-quality design and manufacturing standards. Their rollers are tailored to minimize operational costs and enhance conveyor efficiency. Melco’s commitment to sustainability and innovation is evident in their eco-friendly products and practices, making them a favorite among environmentally conscious businesses.
Kinder Australia
Kinder Australia is recognized for its focus on safety and operational efficiency. Their HDPE rollers are designed to enhance conveyor performance while ensuring the safety of operations. Kinder’s commitment to customer service, quality, and innovation, along with their extensive industry knowledge, positions them as a trusted advisor and supplier in the material handling sector.
These manufacturers set themselves apart through their commitment to quality, innovation, customer service, and environmental sustainability. Their focus on developing products that meet the specific needs of their clients ensures that industries can rely on HDPE rollers for their conveyor systems, contributing to operational efficiency, safety, and cost savings.
HDPE Roller Price Points
Understanding the pricing of HDPE rollers is crucial for businesses looking to invest in durable and efficient conveyor systems. The cost of these rollers can vary widely based on several key factors, from the physical dimensions of the rollers to the reputation of their manufacturers. Let’s explore the various aspects that influence HDPE roller price points and why it’s essential to consider the overall value they offer over their operational lifespan.
Factors Influencing HDPE Roller Costs
- Size: The dimensions of the HDPE roller, including length and diameter, directly impact the price. Larger rollers, designed for heavy-duty applications, typically cost more due to the increased amount of material and the manufacturing complexity involved.
- Specifications: Custom specifications, such as unique bearing types, specialized material formulations for extreme environmental conditions, or additional features for enhanced wear resistance, can also elevate the cost.
- Manufacturer Reputation: Brands known for their quality, innovation, and customer service often command higher prices. Their products, however, usually offer better performance, reliability, and support, justifying the premium.
- Quantity: Bulk orders can significantly affect unit pricing, with discounts often available for larger quantities. This is due to the economies of scale in production and shipping.
- Customization: Any modifications tailored to specific industrial applications or conveyor systems can add to the cost. Customized rollers are engineered to meet precise operational needs, requiring additional design and testing.
- Material Quality: The purity and grade of HDPE used can influence prices. High-grade materials offer better durability and performance but come at a higher cost.
- Technology and Design Innovation: Rollers that incorporate advanced technologies or innovative designs for reduced maintenance and energy consumption might be priced higher but offer cost savings in the long run.
- Market Conditions: Fluctuations in raw material costs and changes in market demand can also impact pricing. Economic conditions and trade policies may affect the cost of materials and thus the final price of the rollers.
- Distribution Channels: The route through which the rollers are purchased (direct from the manufacturer vs. through distributors or resellers) can also affect the price, with direct purchases often resulting in cost savings.
The Importance of Considering Lifespan and Operational Savings
When evaluating the price of HDPE rollers, it’s imperative to look beyond the initial cost and consider the total cost of ownership. A higher-priced roller may offer a longer lifespan, reducing the need for frequent replacements and thereby lowering long-term operational costs. Additionally, rollers that promise lower maintenance requirements and energy consumption can lead to significant operational savings.
Investing in quality HDPE rollers can also result in improved efficiency and productivity, as well as reduced downtime, all of which contribute to a better bottom line for businesses. Therefore, when assessing the cost of HDPE rollers, it’s crucial to weigh the initial price against the anticipated lifespan, maintenance needs, and the potential for operational savings.
While the price of HDPE rollers can vary based on a range of factors, the key to making a cost-effective decision lies in understanding the value they bring over their operational life. Considering the broader context of long-term savings and performance benefits can help businesses justify the investment in higher-quality rollers, ultimately ensuring a more efficient, reliable, and cost-effective conveyor system.
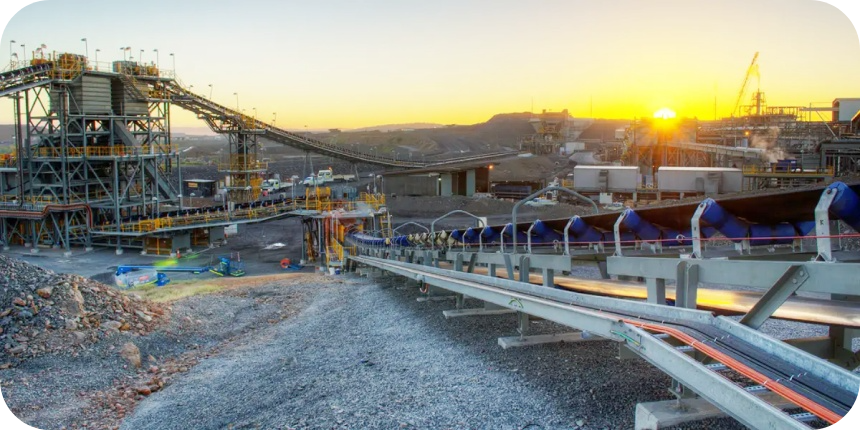
Components and Parts of HDPE Rollers
HDPE rollers, integral to the efficient operation of conveyor systems, comprise several critical components. Each part plays a pivotal role in ensuring the roller’s performance, durability, and longevity. Below is a detailed look at eight key components that constitute an HDPE roller and the specific function of each in the overall mechanism.
HDPE Tube
The HDPE tube forms the outer shell of the roller and is the component that comes into direct contact with the conveyor belt. Made from high-density polyethylene, this tube is prized for its low friction, high wear resistance, and remarkable durability against environmental factors. Its smooth surface helps to minimize wear on the conveyor belt, contributing significantly to the system’s overall efficiency.
Steel Reinforcement
For HDPE rollers exceeding lengths of 600mm, steel reinforcement is crucial to prevent bending and maintain structural integrity under the weight of heavy loads. This reinforcement, typically a steel shaft that runs through the roller’s center, adds strength and stability, ensuring the roller can support substantial weights without deformation.
Bearing Housings
Bearing housings are critical components that encase the roller bearings, providing a secure and stable environment that shields them from contaminants and damage. They are essential for the smooth and efficient rotation of the roller, minimizing friction and wear on the bearings.
Bearings
Bearings are perhaps the most vital components within HDPE rollers, facilitating smooth rotation with minimal friction. High-quality bearings can significantly extend the life of the roller, reduce maintenance requirements, and enhance the conveyor system’s efficiency.
End Caps
End caps are fitted at both ends of the HDPE tube to protect the internal components from dirt, moisture, and other environmental contaminants. They also help to contain the bearing and bearing housings within the roller, ensuring they remain in place and function correctly.
Seals
Seals are used in conjunction with end caps to further protect the bearing housings and bearings from ingress of contaminants. Good sealing is critical in harsh or dirty environments to ensure the longevity and reliability of the roller.
Shaft
The shaft runs through the center of the roller, providing the structural support necessary for the bearing housings and the entire roller assembly. In reinforced rollers, this shaft is a key component that adds rigidity and strength, enabling the roller to bear heavy loads.
Lubrication
Though not a physical component like the others, lubrication is essential for the maintenance and performance of HDPE rollers. Proper lubrication of bearings reduces friction, wear, and heat build-up, extending the life of the roller and maintaining its efficiency.
Each of these components plays a critical role in the functionality and longevity of HDPE rollers. From the HDPE tube’s wear resistance to the bearings’ smooth operation and the structural integrity provided by steel reinforcement and shafts, every part contributes to the roller’s performance. Understanding these components and their functions helps in selecting the right roller for specific applications and in maintaining the rollers for optimal operation and longevity.
Applications in HDPE Rollers in Conveyor Systems
HDPE rollers are a versatile and essential component in the world of conveyor systems, offering unparalleled benefits across a variety of types and industrial settings. Their unique properties, such as high wear resistance, low friction, and resistance to corrosion, make them particularly suitable for a wide range of applications. Below, we explore how HDPE rollers are applied in different conveyor systems and highlight six specific industries and scenarios where they provide the most benefit.
Types of Conveyor Systems Utilizing HDPE Rollers
- Belt Conveyors: HDPE rollers are commonly used in belt conveyors where their low friction surface helps in reducing the wear on conveyor belts and the energy required to drive them. This application is widespread in sectors ranging from mining to food processing, where efficiency and longevity are crucial.
- Roller Conveyor Belts: For systems that rely on gravity or manual pushing to move goods, HDPE rollers offer a lightweight yet durable solution. Their resistance to impacts and abrasion makes them ideal for handling packages, baggage, or any goods with substantial weight.
Industries Benefiting from HDPE Rollers
- Mining and Bulk Material Handling: In the rugged and demanding environment of mining, HDPE rollers stand out for their ability to withstand abrasive materials, moisture, and extreme temperatures, significantly reducing the downtime caused by roller failures.
- Agriculture: The agricultural industry benefits from HDPE rollers in the handling of bulk materials like grains or fertilizers. Their resistance to chemicals and moisture helps in preventing contamination and ensures a longer service life.
- Food Processing: HDPE rollers are favored in the food processing industry due to their hygienic properties. Being easy to clean and resistant to bacterial growth, they are ideal for applications where sanitation is a priority.
- Marine and Port Facilities: The high corrosion resistance of HDPE makes these rollers perfect for the marine environment, where saltwater and humidity can quickly degrade metal components. They are often used in conveyor systems for loading and unloading ships.
- Manufacturing and Packaging: In manufacturing and packaging lines, the smooth operation and low maintenance requirements of HDPE rollers help in minimizing disruptions and maintaining a steady flow of materials.
- Waste Management and Recycling: The durability and resistance to harsh chemicals make HDPE rollers suitable for conveyors used in waste management and recycling facilities, where they can handle a wide variety of materials without degrading.
HDPE rollers are celebrated for their contribution to operational efficiency, safety, and cost-effectiveness across these diverse industries. Their ability to perform under harsh conditions, combined with their environmental resistance, makes them a preferred choice for enhancing the functionality and longevity of conveyor systems. Whether in the processing of raw materials, handling of finished products, or any application in between, HDPE rollers offer a reliable and high-performance solution.
Optimize your workflow with our conveyor rollers. Reach out!
Review of Rulmeca’s Rollers Catalogue and HDPE Rollers
Rulmeca, a leading name in the world of conveyor components, presents an extensive catalogue that showcases a wide variety of rollers and idlers, with a significant emphasis on their HDPE rollers. These offerings are designed to cater to a broad spectrum of industrial conveyor system needs, providing solutions that are both efficient and durable. This review highlights the key aspects of Rulmeca’s HDPE rollers and idlers and how their product range addresses various industrial requirements.
Rulmeca’s HDPE Rollers and Idlers
Rulmeca’s catalogue features HDPE rollers that stand out for their exceptional quality and performance. These rollers are engineered from high-density polyethylene, a material chosen for its strength, low weight, and resistance to wear, chemicals, and environmental conditions. The HDPE rollers are specifically designed to reduce the conveyor system’s energy consumption due to their low friction properties and to extend the service life of conveyor belts by minimizing wear.
The HDPE idlers in the catalogue are presented with various configurations to suit different load requirements and operational conditions. This versatility ensures that Rulmeca can provide solutions for a wide range of applications, from light-duty packaging lines to heavy-duty mining conveyors.
Catering to Industrial Needs
Rulmeca’s product range is meticulously designed to meet the diverse needs of various industries. For instance:
- Mining and Bulk Material Handling: The catalogue includes HDPE rollers and idlers that are optimized for heavy loads and abrasive materials, typical of mining operations. These components are designed to withstand harsh environments, reducing maintenance needs and downtime.
- Agriculture: Rulmeca offers HDPE rollers that are suitable for the agricultural sector, where durability and resistance to moisture and chemicals are necessary for handling bulk materials like grains and fertilizers.
- Food Processing: The hygiene requirements of the food processing industry are addressed with HDPE rollers that are easy to clean and resistant to bacterial growth, ensuring that the conveyance of food products is both safe and efficient.
- Marine and Port Facilities: Given the corrosive nature of marine environments, Rulmeca’s HDPE rollers are designed to resist saltwater and humidity, making them ideal for conveyor systems used in ports and shipping facilities.
- Manufacturing and Packaging: The catalogue also caters to the manufacturing sector, offering HDPE rollers that enhance conveyor efficiency and reliability, essential for smooth operations in packaging lines.
- Waste Management and Recycling: For the demanding conditions of waste management and recycling facilities, Rulmeca provides durable HDPE rollers capable of handling a variety of materials without succumbing to wear or chemical damage.
Rulmeca’s commitment to quality and innovation is evident across their entire range of HDPE rollers and idlers. Their catalogue not only showcases a variety of products but also emphasizes the company’s dedication to addressing the specific needs of different industries with high-performance solutions. By offering components that reduce operational costs, enhance system longevity, and ensure reliability, Rulmeca solidifies its position as a trusted partner for industrial conveyor system requirements.
FAQs about Hdpe Roller
The full form of HDPE roller is “High-Density Polyethylene Roller.” HDPE rollers are components used in conveyor systems, designed to support the conveyor belt and the material being transported. They are made from high-density polyethylene, a type of thermoplastic polymer that is recognized for its strength, durability, and resistance to wear and environmental factors.
HDPE rollers offer several advantages over traditional materials, including reduced weight, which makes them easier to handle and install, and decreased friction, which can lead to lower energy consumption and extended lifespan for the conveyor belt. Their resistance to chemicals, impact, and abrasion makes them suitable for a wide range of industrial applications, from mining and bulk material handling to food processing and waste management. The use of HDPE significantly enhances the performance and reliability of conveyor systems while also offering potential cost savings in terms of maintenance and operational efficiency.
Determining the “best” plastic material for rollers depends largely on the specific requirements of the application, including load capacity, environmental conditions, and cost considerations. However, High-Density Polyethylene (HDPE) is widely regarded as one of the most versatile and efficient materials for manufacturing rollers used in conveyor systems. HDPE’s popularity stems from its excellent combination of strength, durability, and resistance to wear, chemicals, and moisture. This makes HDPE rollers suitable for a broad spectrum of industries, including mining, agriculture, food processing, and more.
Another notable plastic material used for rollers is Ultra-High Molecular Weight Polyethylene (UHMWPE), which offers even greater wear resistance and a lower coefficient of friction than HDPE. UHMWPE is ideal for applications requiring the smoothest possible movement of materials with minimal effort.
Polyvinyl Chloride (PVC) and Polypropylene (PP) are also used in specific applications, each offering their own set of advantages. PVC rollers, for instance, are well-suited for lighter loads and have good chemical resistance, while PP rollers offer excellent mechanical properties and are particularly resistant to fatigue.
In choosing the best plastic material for rollers, factors such as load requirements, environmental conditions, and the specific properties of the material must be carefully considered. HDPE stands out for its balance of performance, cost-effectiveness, and adaptability to a wide range of applications, making it a preferred choice for many industries.
Last Updated on June 27, 2024 by Jordan Smith
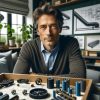
Jordan Smith, a seasoned professional with over 20 years of experience in the conveyor system industry. Jordan’s expertise lies in providing comprehensive solutions for conveyor rollers, belts, and accessories, catering to a wide range of industrial needs. From initial design and configuration to installation and meticulous troubleshooting, Jordan is adept at handling all aspects of conveyor system management. Whether you’re looking to upgrade your production line with efficient conveyor belts, require custom conveyor rollers for specific operations, or need expert advice on selecting the right conveyor accessories for your facility, Jordan is your reliable consultant. For any inquiries or assistance with conveyor system optimization, Jordan is available to share his wealth of knowledge and experience. Feel free to reach out at any time for professional guidance on all matters related to conveyor rollers, belts, and accessories.