High-Temperature And Heat Resistant Conveyor Belt
A heat resistant conveyor belt is essential in high-temperature environments where standard belts would quickly deteriorate. These specialized belts are designed to withstand extreme temperatures, ensuring the efficient and safe transport of materials. The need for a heat resistant conveyor belt arises in industries such as steel, cement, and chemical processing, where materials often exceed normal operating temperatures. Utilizing these helps prevent belt wear and tear, reduces the risk of accidents, and minimizes the frequency of belt replacements. By ensuring operational safety and extending the lifespan of the conveyor system, heat resistant conveyor belts are a critical component in maintaining productivity and reducing maintenance costs.
What is Heat Resistant Conveyor Belt
A heat resistant conveyor belt is essential for industries that involve high-temperature operations. These belts are designed to withstand extreme heat and are crucial in ensuring the durability and efficiency of conveyor systems in such environments. Understanding the differences between various grades of heat resistant conveyor belts can help in selecting the right belt for specific industrial applications.
In industrial settings where high temperatures are common, the use of a heat resistant conveyor belt is essential to ensure the safe and efficient transport of materials. This type of conveyor belt is specifically designed to withstand extreme temperatures, making it suitable for applications such as foundries, cement plants, and glass manufacturing. This detailed exploration will cover the different grades of conveyor belt covers, their properties, and the benefits of using heat resistant conveyor belts in various industries.
Conveyor Belt Cover Grades
Description of Different Conveyor Belt Cover Grades
Conveyor belts are typically categorized into different grades based on the materials used in their covers and their specific performance characteristics. These grades determine the suitability of the belts for various applications, including their resistance to heat, abrasion, and impact.
Grade M (General Purpose)
Grade M conveyor belts are designed for general-purpose use and are suitable for transporting materials with moderate temperatures and abrasion levels. These belts are made from a blend of natural and synthetic rubber, offering a balance between flexibility and durability. While they are not specifically designed for high-heat environments, they can handle intermittent exposure to moderately high temperatures.
Grade N (Moderate Heat Resistance)
Grade N conveyor belts are designed for environments where moderate heat resistance is required. These belts can withstand temperatures up to 100°C (212°F) and are ideal for applications such as recycling plants, where materials may be hot but not excessively so. The covers are typically made from a blend of synthetic rubbers that provide improved heat resistance compared to Grade M belts.
Grade T (High Heat Resistance)
Grade T conveyor belts are specifically designed for high-temperature environments and can withstand temperatures up to 150°C (302°F). These belts are commonly used in industries such as foundries, cement plants, and steel mills, where materials are exposed to extreme heat. The covers are made from specialized heat-resistant compounds that protect the belt from thermal degradation and maintain their structural integrity under high temperatures.
Grade H (Extra High Heat Resistance)
Grade H conveyor belts offer the highest level of heat resistance, capable of withstanding temperatures up to 200°C (392°F) and even higher in some cases. These belts are used in the most demanding applications, such as glass manufacturing and continuous casting operations, where materials can reach extremely high temperatures. The covers are made from advanced heat-resistant materials that provide exceptional durability and protection against thermal damage.

Grade 1 vs Grade 2 Conveyor Belt
Conveyor belts are also categorized into Grade 1 and Grade 2, which refer to their overall quality and performance characteristics, including heat resistance and durability.
Grade 1 Conveyor Belts
Grade 1 conveyor belts are designed to provide superior performance in demanding applications. They offer higher levels of heat resistance and durability compared to Grade 2 belts. These belts are suitable for environments where the conveyor system is exposed to continuous high temperatures and heavy loads. Key characteristics of Grade 1 conveyor belts include:
- High Heat Resistance: Grade 1 belts are made from materials that can withstand higher temperatures without degrading. They are suitable for applications where temperatures regularly exceed 100°C (212°F).
- Enhanced Durability: These belts offer superior resistance to abrasion, impact, and wear, making them ideal for heavy-duty applications. The robust construction ensures a longer lifespan, reducing the need for frequent replacements.
- Improved Performance: Grade 1 belts maintain their structural integrity and performance characteristics even under extreme conditions, ensuring reliable operation and minimizing downtime.
Grade 2 Conveyor Belts
Grade 2 conveyor belts are designed for general-purpose use and offer a balance between performance and cost. While they provide good heat resistance and durability, they are not as robust as Grade 1 belts. Key characteristics of Grade 2 conveyor belts include:
- Moderate Heat Resistance: Grade 2 belts can handle temperatures up to 100°C (212°F) but are not suitable for continuous exposure to higher temperatures. They are ideal for applications with intermittent heat exposure.
- Good Durability: These belts offer good resistance to abrasion and wear, making them suitable for a wide range of industrial applications. However, they may require more frequent maintenance and replacement compared to Grade 1 belts.
- Cost-Effective: Grade 2 belts provide a cost-effective solution for applications where extreme heat resistance and durability are not critical. They offer reliable performance at a lower cost, making them suitable for less demanding environments.
The classification of heat resistant conveyor belts into grade 1 and grade 2 is based on their ability to withstand different temperature ranges and their suitability for various industrial applications. Both grades offer significant benefits, but their performance and durability vary depending on the specific operational conditions.
In-depth Comparison of Grade 1 and Grade 2 Conveyor Belts
Analysis of Their Suitability for Different Temperature Ranges and Industrial Applications
Suitability for High-Temperature Ranges
Grade 1 heat resistant conveyor belts are ideal for applications where the temperature consistently reaches or exceeds 400°F. Industries such as foundries, steel mills, and glass manufacturing plants often require grade 1 belts due to the extreme heat involved in their processes. These belts are capable of maintaining their strength and functionality even under prolonged exposure to high temperatures, ensuring continuous and reliable operation.
In contrast, grade 2 belts are more suited to industries where the temperature does not consistently reach the higher end of the spectrum. Applications such as baking, drying, and lower-temperature metal processing are typical environments where grade 2 belts excel. These belts provide sufficient heat resistance while being more cost-effective for operations that do not require the highest level of thermal protection.
Industrial Applications
Grade 1 Conveyor Belts
Industries that deal with molten materials, such as aluminum, steel, and glass, often utilize grade 1 heat resistant conveyor belts. In these settings, the belts are exposed to direct heat and must endure the intense thermal environment without losing their mechanical properties. Grade 1 belts are also common in cement plants and chemical processing facilities, where high temperatures are a regular part of the production process.
For example, in a steel mill, the conveyor belt must transport red-hot steel parts. A grade 1 belt’s ability to resist temperatures up to 400°F ensures that it can handle this task without breaking down or becoming a safety hazard.
Grade 2 Conveyor Belts
Grade 2 heat resistant conveyor belts find their use in less extreme but still high-temperature environments. Food processing plants that operate baking ovens, for example, often use grade 2 belts to handle the movement of baked goods through the ovens. Similarly, wood processing plants that involve drying kilns utilize these belts to transport wood through the drying process at elevated temperatures.
Another application for grade 2 belts is in the rubber and plastics industries, where parts may need to be cured or processed at high temperatures. These belts provide the necessary heat resistance while being more economical than grade 1 belts for these specific needs.
Benefits of Using Heat Resistant Conveyor Belts
The use of heat resistant conveyor belts offers several advantages, particularly in industries where high temperatures are a constant challenge. These benefits include:
Extended Belt Life
Heat resistant conveyor belts are designed to withstand high temperatures, reducing the risk of thermal degradation and extending the belt’s lifespan. This results in fewer replacements and lower maintenance costs, improving overall operational efficiency.
Improved Safety
In high-temperature environments, the risk of belt failure due to thermal degradation can pose significant safety hazards. Heat resistant conveyor belts maintain their structural integrity under extreme conditions, reducing the likelihood of belt failures and enhancing workplace safety.
Enhanced Performance
Heat resistant conveyor belts maintain their performance characteristics, such as tensile strength and flexibility, even at high temperatures. This ensures reliable operation and consistent material handling, minimizing disruptions and downtime.
Versatility in Applications
Heat resistant conveyor belts are suitable for a wide range of high-temperature applications, from foundries and steel mills to glass manufacturing and cement plants. Their ability to handle extreme temperatures makes them versatile and essential for various industrial processes.
Cost Savings
While heat resistant conveyor belts may have a higher initial cost compared to standard belts, their extended lifespan and reduced maintenance requirements result in long-term cost savings. The reduced need for frequent replacements and repairs lowers overall operational costs.

Heat Resistant Conveyor Belt Specification
A heat resistant conveyor belt is designed to endure high temperatures and is essential in industries where operations involve extreme heat. These belts are crafted to maintain their integrity and performance under such conditions, ensuring smooth and efficient operations. Understanding the detailed specifications and temperature ratings of these belts can help in selecting the right belt for specific industrial applications.
The specifications of a heat resistant conveyor belt are crucial to its performance and suitability for different industrial environments. These specifications include material composition, temperature resistance, tensile strength, and durability.
Detailed Specifications of Heat Resistant Conveyor Belts
Material Composition:
- Rubber Compounds: Most heat resistant conveyor belts are made from specially formulated rubber compounds that can withstand high temperatures. These compounds include EPDM (Ethylene Propylene Diene Monomer), which offers excellent heat resistance and durability.
- Silicone: Silicone is another material commonly used in heat resistant belts due to its ability to withstand very high temperatures and its flexibility.
- Teflon (PTFE): Teflon belts are non-stick and can handle extremely high temperatures, making them ideal for specific applications like food processing where hygiene is critical.
Temperature Resistance:
- Heat resistant conveyor belts are categorized based on their ability to withstand different temperature ranges. This categorization helps in selecting the right belt for specific industrial processes.
- The temperature resistance of these belts typically ranges from 200°F to over 600°F, depending on the materials used and the belt’s construction.
Tensile Strength:
- The tensile strength of a heat resistant conveyor belt is a measure of its ability to withstand stretching and tension. High tensile strength is essential to ensure that the belt can carry heavy loads without breaking or deforming.
- Heat resistant belts often have reinforced layers to provide additional strength and durability.
Durability and Flexibility:
- Durability is a critical factor for heat resistant conveyor belts, as they must endure harsh conditions without degrading.
- Flexibility ensures that the belt can operate smoothly over pulleys and rollers without cracking or breaking, even under high temperatures.
Temperature Range of High-Temperature Materials
Here’s a detailed table displaying the temperature ranges of various high-temperature materials used in different industrial applications, including mining:
These temperature ranges indicate the maximum operating temperatures for each material, making them suitable for use in high-temperature environments such as mining, aerospace, and industrial furnaces.

Different Temperature Ratings Conveyor Belt
Temperature ratings are a crucial aspect of heat resistant conveyor belts. These ratings indicate the maximum temperature the belt can handle while maintaining its performance and integrity.
Temperature Rating Categories:
- Low Heat Resistant Belts: These belts are designed to withstand temperatures up to 200°F. They are suitable for applications where the heat exposure is minimal, such as in light manufacturing processes.
- Medium Heat Resistant Belts: Capable of handling temperatures up to 400°F, these belts are used in industries like baking, where ovens and dryers are common.
- High Heat Resistant Belts: These belts can withstand temperatures up to 600°F and are used in heavy industries like metal processing, glass manufacturing, and foundries.
Implications for Industrial Applications:
- Light Manufacturing:
- In industries with minimal heat exposure, such as packaging or light assembly, low heat resistant belts are sufficient. These belts ensure that the conveyor system remains operational without unnecessary expense.
- Food Processing:
- Medium heat resistant belts are ideal for food processing applications, including baking, cooking, and drying. The belts must comply with food safety standards and provide a non-stick surface to prevent contamination.
- Heavy Industry:
- In heavy industrial applications, where temperatures can reach extreme levels, high heat resistant belts are essential. Industries such as steel mills, glass plants, and foundries require belts that can endure continuous exposure to high heat without degrading.
- Chemical Processing:
- Chemical processing industries often involve high temperatures and corrosive substances. Heat resistant belts used in these environments must also be resistant to chemicals to ensure longevity and safety.
- Wood and Paper Processing:
- In wood and paper processing, belts must handle both high temperatures and abrasive materials. Medium to high heat resistant belts are often used to transport materials through drying and curing processes.
Selecting the Right Belt:
- Choosing the appropriate heat resistant conveyor belt involves assessing the specific needs of the industrial process. Factors such as maximum operating temperature, duration of heat exposure, and the nature of the materials being transported must be considered.
- Consulting with conveyor belt manufacturers can provide valuable insights and help in selecting a belt that meets all operational requirements.
Discover top-quality conveyor belts for your industrial needs.
How about Heat Resistant Conveyor Belt
A high temperature resistant conveyor belt is a critical component in industries where high temperatures are a regular part of the operation. These belts are designed to withstand extreme heat, ensuring that the conveyor system remains functional and durable under challenging conditions. Understanding the various temperature ratings and how to select the right belt for specific industrial needs is essential for maintaining efficiency and safety.
Conveyor Belt Temperature Rating
Temperature ratings are a crucial aspect of conveyor belts, particularly for those used in high-temperature environments. The temperature rating indicates the maximum temperature that the belt can withstand while maintaining its structural integrity and performance. Selecting the appropriate temperature rating for a heat resistant conveyor belt is vital to ensure that it can handle the operational conditions without degrading or failing prematurely.
Importance of Temperature Ratings for Conveyor Belts
Temperature ratings are essential for several reasons:
- Preventing Belt Degradation: Conveyor belts exposed to temperatures beyond their rated capacity can suffer from thermal degradation. This can manifest as cracking, hardening, or softening of the belt material, leading to reduced lifespan and increased maintenance costs.
- Ensuring Safety: Operating a conveyor belt at temperatures higher than its rating can pose significant safety risks. A compromised belt is more likely to fail, which can lead to production halts, material spills, or even accidents that could harm workers.
- Maintaining Performance: The performance of a conveyor belt is directly linked to its ability to withstand the operating environment. Belts that are rated appropriately for their temperature conditions maintain their flexibility, strength, and load-bearing capacity, ensuring smooth and efficient operation.
- Cost Efficiency: Using the right temperature-rated belt minimizes the need for frequent replacements and repairs, leading to cost savings over time. It also ensures that the conveyor system operates reliably, avoiding costly downtime.
Guide to Selecting the Right Temperature Rating for Specific Industrial Needs
Selecting the correct temperature rating for a heat resistant conveyor belt involves understanding the specific requirements of the application and the environment in which the belt will operate. Here are some key considerations:
1. Identify the Maximum Operating Temperature
The first step in selecting the right conveyor belt is to determine the maximum temperature that the belt will be exposed to during operation. This includes considering both the ambient temperature and the temperature of the materials being transported.
For example, in a steel mill, the conveyor belt might need to transport red-hot steel parts that reach temperatures up to 800°F. In contrast, a food processing plant might require a belt that can withstand the temperatures of baking ovens, typically around 400°F.
2. Consider the Duration of Exposure
It is also important to consider how long the belt will be exposed to high temperatures. Some belts are designed to handle short bursts of extreme heat, while others are intended for continuous exposure. The duration of exposure affects the choice of material and construction of the belt.
3. Evaluate the Belt Material and Construction
Different materials and constructions offer varying levels of heat resistance. Common materials for heat resistant conveyor belts include:
- Silicone: Known for its excellent heat resistance, silicone belts can withstand temperatures up to 500°F. They are suitable for applications where continuous exposure to high heat is required.
- EPDM (Ethylene Propylene Diene Monomer): EPDM belts offer good heat resistance and are typically used in applications up to 300°F. They are also resistant to ozone and weathering, making them suitable for outdoor applications.
- Teflon (PTFE): Teflon belts can handle temperatures up to 600°F and are non-stick, making them ideal for food processing applications where hygiene is crucial.
4. Assess the Application Requirements
Different industries have specific requirements for their conveyor belts. For instance:
- Metallurgical Industry: Requires belts that can handle very high temperatures and are resistant to abrasion and cutting.
- Food Industry: Needs belts that are heat resistant, non-stick, and compliant with food safety regulations.
- Glass Manufacturing: Demands belts that can withstand high temperatures and are resistant to thermal shock.
5. Consider Additional Environmental Factors
In addition to temperature, other environmental factors such as humidity, exposure to chemicals, and mechanical stresses must be considered. For example, a belt used in a chemical processing plant must be resistant to both heat and the specific chemicals it will encounter.
6. Consult with Manufacturers
Working with experienced conveyor belt manufacturers can provide valuable insights and recommendations based on the specific needs of the application. Manufacturers can offer customized solutions and ensure that the chosen belt meets all operational requirements.
The Keys of Heat Resistant Conveyor Belt
In industrial environments where high temperatures are prevalent, the use of a heat resistant conveyor belt is essential to ensure efficient and safe material handling. These specialized belts are designed to withstand extreme temperatures, making them ideal for applications such as foundries, cement plants, and glass manufacturing. This comprehensive examination will delve into the materials used in heat resistant conveyor belts and provide an overview of compounds like EPDM, silicone, and PTFE that provide exceptional thermal resistance.
Heat Resistant Conveyor Belt Material
Discussion on the Materials Used in Heat Resistant Conveyor Belts
The materials used in the construction of heat resistant conveyor belts are critical to their performance and durability. These materials are selected for their ability to endure high temperatures while maintaining their structural integrity and functionality. The primary materials used in heat resistant conveyor belts include synthetic rubbers and polymers, each offering unique properties that enhance the belt’s heat resistance.
Synthetic Rubbers
Synthetic rubbers are widely used in the production of heat resistant conveyor belt specification due to their excellent heat resistance, flexibility, and durability. The most common synthetic rubbers used are:
- EPDM (Ethylene Propylene Diene Monomer): Known for its outstanding heat resistance, EPDM can withstand temperatures up to 150°C (302°F) and higher in some formulations. It also offers excellent resistance to ozone, weathering, and aging, making it ideal for high-temperature applications in harsh environments.
- Silicone Rubber: Silicone rubber is renowned for its exceptional heat resistance, capable of withstanding temperatures up to 200°C (392°F) and beyond. It maintains its flexibility and mechanical properties across a wide temperature range, making it suitable for applications where thermal stability is crucial.
Polymers
In addition to synthetic rubbers, advanced polymers are also used to enhance the heat resistance of conveyor belts. These polymers provide superior thermal stability and resistance to chemical degradation.
- PTFE (Polytetrafluoroethylene): PTFE is a high-performance polymer known for its excellent heat resistance and low friction properties. It can endure continuous temperatures up to 260°C (500°F) and has outstanding resistance to chemicals, making it ideal for demanding industrial applications.
Overview of Compounds like EPDM, Silicone, and PTFE that Provide Thermal Resistance
EPDM (Ethylene Propylene Diene Monomer)
EPDM is a versatile synthetic rubber widely used in conveyor belt heat resistant due to its superior thermal and environmental resistance. It can endure high temperatures, making it suitable for applications in industries such as power generation, cement manufacturing, and metal processing. Key properties of EPDM include:
- Thermal Resistance: EPDM can withstand continuous exposure to temperatures up to 150°C (302°F) and short-term peaks even higher, depending on the specific formulation.
- Environmental Resistance: EPDM offers excellent resistance to ozone, UV radiation, and weathering, which prolongs the belt’s service life in outdoor applications.
- Flexibility and Durability: This material maintains its flexibility and mechanical strength over a wide temperature range, ensuring reliable performance in high-temperature environments.
Silicone Rubber
Silicone rubber is another crucial material used in the construction of heat resistant conveyor belts. Its unique properties make it highly effective in extreme temperature applications. Key characteristics of silicone rubber include:
- Exceptional Heat Resistance: Silicone rubber can handle continuous temperatures up to 200°C (392°F) and short-term exposure to even higher temperatures without losing its properties.
- Flexibility at High Temperatures: Unlike many other materials, silicone rubber retains its flexibility and elasticity at elevated temperatures, which is essential for maintaining the belt’s performance and preventing cracking or deformation.
- Chemical Resistance: Silicone rubber is resistant to a wide range of chemicals, oils, and solvents, making it suitable for diverse industrial applications where chemical exposure is a concern.
PTFE (Polytetrafluoroethylene)
PTFE is a high-performance polymer that offers unparalleled heat resistance and chemical inertness. It is used in the most demanding applications where extreme temperatures and harsh chemical environments are present. Key properties of PTFE include:
- Superior Thermal Stability: PTFE can withstand continuous temperatures up to 260°C (500°F) and has excellent resistance to thermal degradation, making it ideal for use in high-temperature conveyor belts.
- Low Friction and Non-stick Properties: PTFE’s low friction coefficient and non-stick surface reduce the risk of material buildup on the belt, enhancing efficiency and reducing maintenance needs.
- Chemical Resistance: PTFE is virtually inert to all chemicals, providing exceptional durability in environments where chemical exposure is a significant concern.
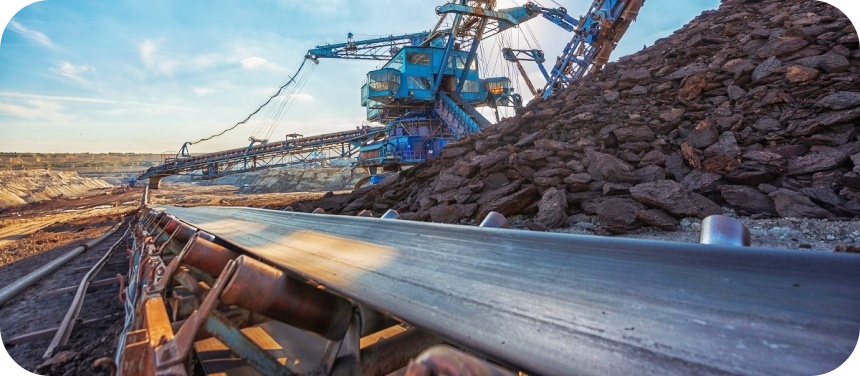
FAQS about Heat Resistant Conveyor Belt
A heat resistant conveyor belt is designed to transport materials that generate high temperatures during processing. These belts are made from specialized materials that can withstand high thermal environments, preventing degradation and maintaining performance. They are commonly used in industries such as metallurgy, cement, and foundries, where materials like clinker, sinter, and pellets need to be moved at temperatures that can reach up to 200°C or more. Heat resistant belts typically feature compounds like EPDM (ethylene propylene diene monomer) or SBR (styrene-butadiene rubber), which provide excellent thermal stability and resistance to heat-induced wear and tear.
For high-temperature applications, belts made from materials such as Teflon (PTFE), silicone, and woven fiberglass coated with PTFE or silicone are often used. These materials offer superior resistance to extreme temperatures, with PTFE belts capable of withstanding temperatures up to 260°C and silicone belts handling up to 200°C. In industrial settings, high-temperature conveyor belts are crucial for processes like baking, drying, and curing, where materials must be transported through ovens or other heat-intensive environments. These belts maintain their structural integrity and performance despite prolonged exposure to high heat.
The grades of heat-resistant conveyor belts are categorized based on their ability to withstand different temperature ranges. Common grades include HR-T1, HR-T2, and HR-T3:
HR-T1: Suitable for materials with temperatures up to 100°C.
HR-T2: Suitable for materials with temperatures up to 125°C.
HR-T3: Suitable for materials with temperatures up to 150°C. These grades help industries choose the appropriate belt for their specific thermal requirements, ensuring optimal performance and longevity. For extremely high temperatures, specialized grades like T4 may be used, which can handle temperatures up to 200°C or higher.
High-temperature belting materials include Teflon (PTFE), silicone, and fiberglass. PTFE belts, also known as Teflon belts, offer excellent heat resistance up to 260°C and are non-stick, making them ideal for applications involving sticky or gummy materials. Silicone belts are flexible and can withstand temperatures up to 200°C, providing good release properties and thermal stability. Woven fiberglass belts coated with PTFE or silicone are also used, combining the strength of fiberglass with the heat-resistant properties of the coatings, making them suitable for high-temperature industrial processes.
Heat belts, commonly used in therapeutic and industrial settings, are designed to provide consistent heat for various applications. In therapeutic use, heat belts help alleviate pain and muscle stiffness by improving blood circulation and relaxing muscles. These belts are effective when used correctly and for appropriate durations. In industrial contexts, heat-resistant conveyor belts effectively transport materials through high-temperature environments, maintaining their integrity and functionality. Their effectiveness depends on proper selection based on the specific thermal requirements of the application.
A heat belt, in the context of therapeutic use, is a flexible, often adjustable, belt equipped with heating elements designed to provide localized heat therapy. It is used to relieve muscle pain, stiffness, and improve blood circulation. These belts typically have adjustable temperature settings and are powered by electricity. In industrial terms, a heat belt refers to a heat-resistant conveyor belt used in manufacturing processes to transport materials through high-temperature environments. These belts are constructed from specialized materials capable of withstanding and operating effectively in extreme heat conditions.
Last Updated on August 9, 2024 by Jordan Smith
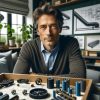
Jordan Smith, a seasoned professional with over 20 years of experience in the conveyor system industry. Jordan’s expertise lies in providing comprehensive solutions for conveyor rollers, belts, and accessories, catering to a wide range of industrial needs. From initial design and configuration to installation and meticulous troubleshooting, Jordan is adept at handling all aspects of conveyor system management. Whether you’re looking to upgrade your production line with efficient conveyor belts, require custom conveyor rollers for specific operations, or need expert advice on selecting the right conveyor accessories for your facility, Jordan is your reliable consultant. For any inquiries or assistance with conveyor system optimization, Jordan is available to share his wealth of knowledge and experience. Feel free to reach out at any time for professional guidance on all matters related to conveyor rollers, belts, and accessories.