Specialty Heat Resistant Conveyor Belt Material for High Temperatures
Heat resistant conveyor belts are crucial in various industrial sectors where operations involve high temperatures, such as metallurgy, cement production, and food processing. These belts are designed to withstand extreme heat without losing integrity, which is essential for maintaining continuous production and ensuring operational safety. The term heat resistant conveyor belt material refers specifically to the specialized compounds and fabrics used to construct these belts, including materials like Teflon, silicone, and rubber textiles enhanced with heat-resistant properties. The heat-resistant conveyor belt, with multiple protective layers, endures continuous temperatures up to 160°C and peaks at 180°C, ensuring durability in high-temperature environments. Understanding the different materials and technologies that go into making these belts can help industries choose the right type of conveyor belt to meet their specific heat tolerance requirements and enhance efficiency.
Key Features of Heat Resistant Conveyor Belt Material
Heat resistant conveyor belt material is specially formulated to withstand high temperatures while maintaining performance. The key attribute that defines this material’s heat resistance is its ability to operate effectively under the stress of hot environments without degradation. This resilience is crucial in industries such as mining, foundries, and steel mills where materials processed can reach extreme temperatures.
The composition of heat resistant conveyor belt material typically involves rubber blends with high-grade polymers, Teflon, or silicone, which enhance the belt’s thermal stability and durability. These materials are selected for their ability to resist the deteriorative effects of high temperatures such as cracking, hardening, and loss of strength. Furthermore, these belts often incorporate a structure of multiple layers that include heat-resistant fabrics and coatings to provide additional protection.
Common specifications and standards for heat resistant conveyor belts include ISO 4195 and DIN 22102. These standards help to categorize heat resistant conveyor belts based on their maximum operating temperatures and the duration for which they can endure these conditions. For example, belts designed to handle up to 150°C continuously are often classified differently than those that can withstand intermittent spikes up to 400°C. This classification aids in ensuring that the selected conveyor belt meets the specific needs of an application, optimizing both safety and longevity.
By adhering to these specifications, heat resistant conveyor belt material provides a reliable solution for conveying materials across various industries, reducing downtime and maintenance costs associated with belt failure due to heat exposure.
Types of Heat Resistant Conveyor Belt Materials
The diversity in heat resistant conveyor belt material allows for its use in a variety of high-temperature industrial applications. Each type of material offers specific benefits and is suitable for different thermal conditions and operational needs.
Teflon Conveyor Belts
Teflon conveyor belts are a prime choice for heat resistant conveyor belt material, especially in environments where temperatures can soar extremely high. Teflon, known for its non-stick properties and thermal stability, can handle temperatures from -70° to 450°F (-57° to 232°C). This makes Teflon belts ideal for heat-sealing machines, drying tunnels, and food processing applications where minimal adhesive interaction and high temperature resistance are crucial. The material’s resistance to chemicals and low friction surface also significantly reduces maintenance needs and prolongs the belt’s lifespan.
Rubber Textile Conveyor Belts

Rubber textile conveyor belts incorporate various rubber compounds, such as EPDM (ethylene propylene diene monomer) and chlorobutadiene, which provide excellent thermal and chemical resistance. These belts are categorized into different temperature grades: T1, T2, and T3. T1 grade belts are capable of withstanding continuous material temperatures up to 150°C with occasional peaks up to 180°C, making them suitable for handling materials like biomass and recycling materials. T2 grade belts handle up to 180°C continuously and peaks up to 200°C, ideal for cement clinker or sinter. The T3 grade is designed for the most extreme conditions, supporting continuous temperatures up to 200°C and peaks up to 400°C, used frequently in the metal and steel manufacturing industries.
Silicone Conveyor Belts
Silicone conveyor belts stand out in the roster of heat resistant conveyor belt material due to their superb performance in extreme temperatures, ranging from -50° to 200°C (-58° to 392°F). These belts feature high flexibility and are highly resistant to thermal degradation and sticky substances, making them suitable for applications in food production, pharmaceuticals, and electronics manufacturing. Silicone’s inherent non-stick surface makes it ideal for processes involving adhesives or other tacky materials.
Each type of heat resistant conveyor belt material offers unique characteristics and benefits, making them indispensable in modern industrial operations where high temperatures are a norm. Understanding the properties and appropriate applications of these materials ensures optimal performance and efficiency in any given industrial setting.
Heat Resistant Conveyor Belt Specifications
Heat resistant conveyor belts are designed to perform efficiently and reliably in high-temperature environments. Each material type offers unique properties that cater to specific industrial requirements. Understanding the specifications of these belts is crucial for selecting the right type for your application.
Temperature Ranges
- PTFE Belts: Polytetrafluoroethylene (PTFE) belts are known for their excellent heat resistance and non-stick properties. These belts can withstand continuous temperatures up to 260°C, making them suitable for applications involving direct contact with hot materials. PTFE belts are often used in industries such as food processing, where the non-stick surface aids in the easy release of products and simplifies cleaning processes.
- Kevlar Belts: Kevlar, or aramid fiber, is renowned for its exceptional strength and heat resistance. Kevlar belts can handle continuous temperatures up to 400°C, making them ideal for extremely high-temperature applications. These belts are commonly used in industries such as metalworking, glass manufacturing, and automotive production, where they transport materials like hot glass, molten metals, and automotive parts through high-temperature processes.
- Stainless Steel Belts: Stainless steel conveyor belts are the most heat-resistant option, capable of withstanding temperatures up to 800°C. These belts are used in the most demanding environments, such as metal smelting, furnace conveyors, and other high-temperature industrial processes. Stainless steel belts are also resistant to corrosion, making them suitable for harsh chemical environments as well.
Material Properties
- Durability: Heat resistant conveyor belts must be highly durable to withstand the rigors of high-temperature environments. PTFE belts are durable due to their resistance to chemicals and physical wear. Kevlar belts offer outstanding tensile strength and durability, making them resistant to punctures, cuts, and abrasions. Stainless steel belts provide unparalleled durability, capable of enduring extreme temperatures and heavy mechanical loads without deforming or degrading.
- Flexibility: Flexibility is a crucial property for conveyor belts, allowing them to handle various loads and speeds without compromising performance. PTFE belts are highly flexible and can be customized to suit different conveyor systems. Kevlar belts, while extremely strong, also offer good flexibility, making them suitable for complex conveyor layouts. Stainless steel belts are less flexible but can be engineered with specific designs, such as mesh patterns, to provide the necessary flexibility for specific applications.
- Chemical Resistance: Compatibility with industrial chemicals is essential for conveyor belts used in environments where they are exposed to various substances. PTFE belts are chemically inert and resistant to most chemicals, including acids, bases, and solvents, making them ideal for food processing and chemical industries. Kevlar belts are resistant to most chemicals but can be affected by strong acids and alkalis. Stainless steel belts offer excellent chemical resistance, withstanding exposure to corrosive substances, making them suitable for applications in chemical processing and other harsh environments.
Understanding these specifications helps in selecting the right heat resistant conveyor belt material for your specific needs, ensuring optimal performance, longevity, and safety in high-temperature industrial applications.
Manufacturers and Suppliers of Heat Resistant Conveyor Belt Material
The market for heat resistant conveyor belt materials is populated with numerous manufacturers and suppliers, each offering products designed to withstand extreme temperatures and demanding industrial environments. This section provides a detailed overview of eight leading manufacturers and suppliers specializing in heat resistant conveyor belt material, followed by twelve practical tips on how to choose the right supplier for your needs.
Leading Manufacturers and Suppliers
GRAM Conveyor – GRAM Conveyor stands out with their ‘GRAM Nylon Series,’ offering high-quality nylon material belts that are lightweight, corrosion-resistant, and designed for easy maintenance. These heat-resistant conveyor belts are ideal for industries like chemical manufacturing and cleanrooms, showcasing GRAM’s commitment to innovation and quality in the conveyor belt market.
ContiTech AG – A major player in the rubber industry, ContiTech offers a wide range of heat-resistant conveyor rubber belts renowned for their durability and high-temperature resistance, suitable for cement factories and steel mills.
Bridgestone Corporation – Bridgestone’s high-performance heat-resistant belts are designed to prevent deformation and degradation at high temperatures, making them ideal for mining and quarry applications.
Fenner Dunlop Conveyor Belting – Specializing in ultra-high-strength materials, Fenner Dunlop provides heat-resistant conveyor belts that excel in heat tolerance and longevity, particularly in the mining and energy sectors.
Habasit AG – Known for their innovative solutions, Habasit offers customized heat-resistant belts that cater to a variety of industries, including food processing and manufacturing.
Yokohama Rubber Co., Ltd. – Yokohama manufactures premium heat-resistant belts capable of handling extremely high temperatures, suitable for cement kilns and chemical plants.
Sempertrans Conveyor Belt Solutions GmbH – Sempertrans is recognized for their robust conveyor belt solutions that offer superior heat resistance and operational reliability in harsh conditions.
Zhejiang Double Arrow Rubber Co., Ltd. – A leading Asian manufacturer, Double Arrow provides a diverse range of heat-resistant conveyor belts that meet rigorous international standards.
Ammeraal Beltech – Ammeraal Beltech excels in providing technologically advanced belts, including heat-resistant options perfect for automotive and other high-temperature industrial applications.
Tips for Choosing the Right Supplier

- Assess Temperature Requirements – Ensure the supplier’s heat resistant conveyor belt material can withstand your specific operational temperatures.
- Evaluate Product Range – Look for suppliers offering a variety of belt materials and configurations to find the best match for your application.
- Check Industry Reputation – Research each supplier’s reputation within your industry. Positive reviews and testimonials can indicate reliability and quality.
- Consider Location – Proximity to the supplier can reduce shipping times and costs, and facilitate easier communication.
- Analyze Cost Efficiency – While initial costs are important, consider long-term durability and maintenance expenses when choosing a belt.
- Request Samples – If possible, obtain product samples to test in your own operations before making a large purchase.
- Examine Customization Options – Some operations may require customized solutions; check if suppliers offer these services.
- Review Technical Support – Good suppliers should offer robust support, including installation, maintenance, and troubleshooting.
- Ensure Compliance with Standards – Verify that the heat resistant conveyor belt materials meet relevant safety and quality standards.
- Discuss Warranty and Service Terms – Understanding warranty coverage and service terms can help mitigate future risks and unexpected costs.
- Inspect Supplier Certifications – Certifications like ISO can indicate a high level of operational and product standards.
- Prioritize Environmental Compliance – If sustainability is a concern, choose suppliers that adhere to environmental regulations and offer eco-friendly products.
By carefully evaluating these factors and the capabilities of various suppliers, you can effectively select the right provider of heat resistant conveyor belt material for your industrial needs.
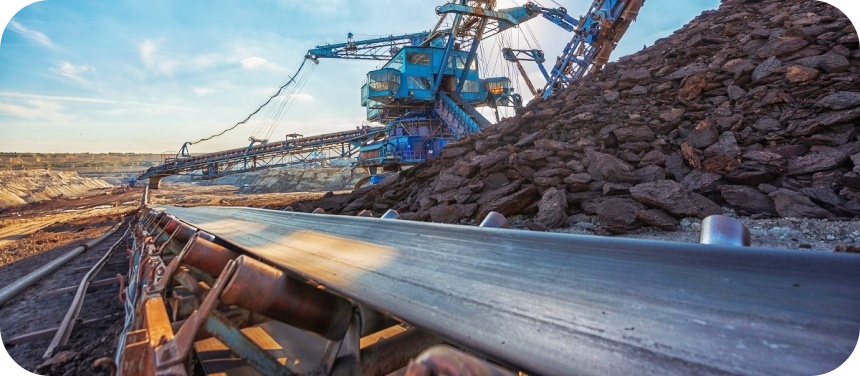
Choosing the Right Heat Resistant Conveyor Belt Material
Selecting the appropriate heat resistant conveyor belt material is crucial for maintaining efficiency and safety in high-temperature industrial applications. Below, we outline seven key factors to consider when choosing a conveyor belt for environments that involve elevated temperatures, followed by a discussion on the various grades of conveyor belts and their suitability for different industrial processes.
Key Factors in Selecting Heat Resistant Conveyor Belt Material
- Temperature Range – The foremost consideration is the temperature range the conveyor belt will be exposed to. Heat resistant conveyor belts are designed to withstand different maximum temperatures, so it’s essential to choose a belt that can handle the specific thermal conditions of your operation without degrading.
- Material Handled – The type of materials being transported on the belt can influence the choice of conveyor belt material. Abrasive materials require belts with tougher surfaces to prevent wear, while sticky or viscous materials might need belts with special coatings.
- Conveyor Belt Thickness and Durability – Thicker belts generally offer greater durability and heat resistance, but they may also require more powerful motors and stronger support structures. The thickness should be chosen based on the application’s specific needs for longevity and resistance to tearing and puncturing.
- Chemical Resistance – In environments where chemicals are present along with high temperatures, it’s important to select a conveyor belt material that is resistant to both heat and chemical attack to ensure longevity and prevent material degradation.
- Flexibility and Tension – The belt’s ability to maintain flexibility at high temperatures affects its performance. Materials that retain flexibility under heat are less likely to crack. Additionally, consider the tension strength of conveyor belt, as high temperatures can affect the tension and elongation properties of the material.
- Maintenance Requirements – Consider how easy it is to maintain and repair the conveyor belt. Heat resistant belts might require more frequent inspections and maintenance to ensure they remain in optimal condition.
- Cost-Effectiveness – Finally, while it might be tempting to opt for the cheapest option, it’s important to weigh the initial cost against the expected lifespan and maintenance needs. A more expensive belt that lasts longer and requires less maintenance could offer greater value over time.
Grades of Heat Resistant Conveyor Belts and Their Suitability
Heat resistant conveyor belts come in various grades, each designed to meet specific industrial needs:
- T1 Grade – Suitable for temperatures up to 125°C, ideal for industries like baking and drying applications where moderate heat is involved.
- T2 and T3 Grades – These belts can handle up to 150°C and 180°C respectively, making them suitable for chemical processing and metalworking where higher temperatures are common.
- T4 Grade – Designed for extremely high temperatures up to 210°C, these belts are typically used in cement clinker, calcination plants, and steel processing where the highest levels of heat resistance are required.
Each grade of heat resistant conveyor belt material is specifically engineered to perform under certain temperature conditions and operational demands. When choosing a conveyor belt, consider not only the maximum temperature but also the operational environment and the physical and chemical properties of the materials being transported. This comprehensive approach will ensure that you select the most suitable heat resistant conveyor belt material for your industrial process, optimizing both performance and cost-effectiveness.
Applications of Heat Resistant Conveyor Belt Material
Heat resistant conveyor belt materials are essential in a variety of industries where high temperatures are a regular part of the production process. These specialized belts are designed to withstand the stress of high heats while maintaining operational integrity and efficiency. Below, we explore detailed examples of industries and processes that rely heavily on heat resistant conveyor belts, including high temperature belt conveyor furnaces, canning conveyors, and high heat conveyor systems.
High Temperature Belt Conveyor Furnaces
Belt conveyor furnaces are extensively used in industries like metallurgy, ceramics, and electronics, where controlled heating processes are critical. These furnaces often require conveyor belts that can operate at temperatures up to 500°C. The heat resistant conveyor belt material used in these applications must not only withstand the high temperatures but also support the weight and abrasive nature of the materials being processed. For instance, in the heat treatment of metals for hardening or annealing, the conveyor belt material must resist thermal shock and distortion.
Canning Conveyors
The canning industry relies on conveyor belts for the efficient transport of cans through various stages of filling, cooking, and sterilization. Heat resistant conveyor belts in these applications are crucial as they must endure the steam and heat used during the sterilization process which typically reaches temperatures above 100°C. The material used for these conveyor belts must also be compliant with food safety regulations, ensuring that it does not contaminate the food product and is resistant to microbial growth and easy to clean.
High Heat Conveyor Systems

Industries such as cement manufacturing and road construction use high heat conveyor systems to transport materials like hot asphalt or clinker. These materials often exceed temperatures of 250°C. The heat resistant conveyor belt materials in these settings must be exceptionally durable and capable of handling not just high temperatures but also the abrasive nature of the materials transported. The performance of these conveyor belts directly impacts the efficiency and cost-effectiveness of the production process, making the selection of the right heat resistant material critical.
Additional Industrial Applications
- Chemical Processing: Chemical plants often utilize heat resistant conveyor belts to move chemicals and other materials through processes that involve high temperatures or reactive conditions.
- Foundries and Steel Mills: These facilities transport hot metals and slag, which require belts that can handle extreme heat without degrading.
- Glass and Ceramic Industries: Conveying of hot glass or ceramics demands belts that can withstand temperatures without losing strength or shape.
The use of heat resistant conveyor belt material is integral to these industries. Their ability to maintain functional integrity under extreme temperature conditions ensures continuous production flow, reduces maintenance downtime, and extends the operational lifespan of the conveyor system. Selecting the right heat resistant conveyor belt material, therefore, becomes a pivotal decision in high-temperature industrial applications, impacting both productivity and operational costs.
Innovations in Heat Resistant Conveyor Belts
Innovation in heat resistant conveyor belts is driven by the need for improved performance, durability, and environmental sustainability. Recent advancements have focused on developing new materials and technologies that meet the rigorous demands of high-temperature applications while reducing environmental impact and enhancing efficiency.
New Materials and Technologies
- Emerging Materials:
- Advances in PTFE: Polytetrafluoroethylene (PTFE) continues to evolve with the introduction of new composites that enhance its already impressive heat resistance and non-stick properties. These advanced PTFE materials provide even greater durability and chemical resistance, making them suitable for more demanding applications in the food processing, packaging, and chemical industries.
- Kevlar Enhancements: Kevlar, known for its exceptional strength and heat resistance, has seen improvements in its structural integrity and flexibility. New Kevlar blends and coatings increase its durability against wear and tear, making it an even more reliable choice for high-temperature environments such as automotive manufacturing and metal processing.
- Metal Alloys: Innovations in metal alloys have led to the development of stainless steel conveyor belts that can withstand even higher temperatures and corrosive environments. These new alloys offer improved resistance to oxidation and scaling, extending the belt’s service life in extreme conditions found in metal smelting and furnace operations.
- Technological Improvements:
- Enhanced Durability: New manufacturing techniques, such as precision weaving and advanced vulcanization processes, have significantly improved the durability of heat resistant conveyor belts. These techniques ensure uniform material distribution and stronger bonding, resulting in belts that can endure prolonged exposure to high temperatures and mechanical stress.
- Flexibility Improvements: Innovations in belt design, such as the incorporation of flexible joints and modular constructions, have enhanced the flexibility of heat resistant belts. These designs allow for better adaptability to various conveyor system configurations, reducing the risk of belt damage and increasing operational efficiency.
- Resistance Enhancements: The introduction of advanced coatings and surface treatments has improved the resistance of conveyor belts to wear, chemical exposure, and thermal degradation. These enhancements ensure that the belts maintain their performance and integrity even under the harshest conditions.
Environmental and Efficiency Considerations
- Energy Efficiency:
- Reduced Energy Consumption: Modern heat resistant conveyor belts are designed to operate more efficiently, reducing the overall energy consumption of conveyor systems. Innovations such as lightweight materials, low-friction surfaces, and optimized belt designs contribute to lower energy use, which is crucial in high-temperature applications where energy costs can be significant.
- Efficient Heat Management: New materials with improved thermal conductivity help manage and dissipate heat more effectively, preventing overheating and reducing the need for additional cooling systems. This not only saves energy but also enhances the belt’s lifespan and reliability.
- Sustainability:
- Eco-friendly Materials: The development of eco-friendly materials, such as biodegradable polymers and recycled components, has become a priority in the manufacturing of heat resistant conveyor belts. These materials reduce the environmental impact of production and disposal, aligning with global sustainability goals.
- Green Manufacturing Processes: Manufacturers are adopting greener production methods, such as reducing emissions, recycling waste materials, and using renewable energy sources. These processes not only lower the environmental footprint but also improve the overall sustainability of the conveyor belt industry.
- Longevity and Reduced Waste: By enhancing the durability and lifespan of heat resistant conveyor belts, manufacturers can reduce the frequency of belt replacements. This results in less waste and a lower environmental impact over the product’s lifecycle. Innovations that improve the belt’s resistance to wear, heat, and chemical exposure contribute significantly to this sustainability effort.
The continuous innovations in heat resistant conveyor belts are addressing the dual demands of high performance and environmental sustainability. By leveraging new materials, advanced technologies, and eco-friendly practices, the conveyor belt industry is paving the way for more efficient, durable, and environmentally responsible solutions for high-temperature applications. These advancements not only enhance the operational efficiency of industrial processes but also contribute to a greener and more sustainable future.
Reliable and efficient conveyor belts available. Submit an inquiry!
FAQs about Heat Resistant Conveyor Belt Material
A heat resistant conveyor belt is a type of conveyor belt that is designed to withstand high temperatures. These belts are essential in industries where materials being transported have elevated temperatures, potentially causing damage to standard conveyor belts. Heat resistant conveyor belts can operate efficiently under high-temperature conditions, making them suitable for use in industries such as mining, metallurgy, cement, and power generation. These belts are engineered to resist cracking, hardening, and other types of damage associated with heat exposure, thereby ensuring operational efficiency and extended belt life.
High-temperature belting often employs specialized materials that can endure excessive heat without deteriorating. The materials used include EPDM rubber, silicone, Teflon, and glass fiber among others. EPDM rubber and silicone are known for their excellent heat resistance and are widely utilized in the manufacturing of these conveyor belts. Teflon may be coated on the belt surface for its non-stick properties, especially when transporting sticky materials. High temperature belts can also feature a carcass made of heat-resistant fibers such as Kevlar or glass fiber to enhance structural integrity and longevity.
The grade of belt used for temperature resistance often depends on the maximum operating temperature it is designed to withstand. These grades vary and are typically standardized across the industry. Common grades include:
T1 grade, designed for temperatures up to 120°C.
T2 grade, capable of withstanding up to 150°C.
T3 grade, suitable for temperatures up to 210°C.
There are also specialized grades like UHR (Ultra Heat Resistant) that can handle temperatures up to and occasionally exceeding 200°C. The specific grade chosen will depend on the temperature range within which the conveyor system will operate.
Conveyor belts can be made from various materials, each selected based on the application’s specific needs. Common materials include rubber, PVC, polyurethane, neoprene, nylon, polyester, leather, and steel. Rubber belts are favored for their durability and versatility, making them suitable for vast applications, including high-temperature environments. PVC conveyor belts are preferred in industries requiring high levels of hygiene. Polyurethane belts are employed in food processing due to their resistance to oils, fats, and chemicals. The choice of material significantly influences the belt’s performance, particularly in terms of wear resistance, temperature tolerance, and maintenance needs.
Last Updated on June 21, 2024 by Jordan Smith
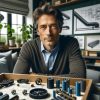
Jordan Smith, a seasoned professional with over 20 years of experience in the conveyor system industry. Jordan’s expertise lies in providing comprehensive solutions for conveyor rollers, belts, and accessories, catering to a wide range of industrial needs. From initial design and configuration to installation and meticulous troubleshooting, Jordan is adept at handling all aspects of conveyor system management. Whether you’re looking to upgrade your production line with efficient conveyor belts, require custom conveyor rollers for specific operations, or need expert advice on selecting the right conveyor accessories for your facility, Jordan is your reliable consultant. For any inquiries or assistance with conveyor system optimization, Jordan is available to share his wealth of knowledge and experience. Feel free to reach out at any time for professional guidance on all matters related to conveyor rollers, belts, and accessories.