Heavy Duty Conveyor Belt Material Options
Heavy duty conveyor belts are pivotal in various sectors, including mining, construction, and large-scale manufacturing. These belts facilitate the efficient transport of bulky and heavy materials over distances, playing a crucial role in production and operational workflows. The materials used in these belts must withstand extreme conditions, such as heavy impacts, sharp materials, and varying temperatures. Commonly, heavy duty conveyor belt material includes robust rubber compounds, durable fabric layers, and sometimes, metals or synthetic materials for added strength and resilience. This introduction delves into the key materials and their properties, laying the groundwork for understanding their critical applications across different industries. By choosing the right material, companies can significantly improve their operational efficiency and reduce maintenance costs.
What are Heavy Duty Conveyor Belt Materials
Heavy-duty conveyor belts are the backbone of numerous industries, tasked with the critical role of transporting heavy, abrasive, or bulky materials across various operational environments. These belts must endure significant mechanical stress, resist wear and tear, and function reliably under harsh conditions. The choice of materials used in these conveyor belts is therefore crucial, ensuring they meet the demanding requirements of industries such as mining, construction, manufacturing, and logistics. This section delves into the primary materials used in heavy-duty conveyor belts, highlighting their properties, advantages, and typical applications.
Rubber Conveyor Belt Materials
Rubber is the most widely used heavy duty conveyor belt material, valued for its exceptional durability, flexibility, and resilience. The rubber used in these belts is often natural or synthetic, with variations tailored to specific industrial needs.
- Natural Rubber: Known for its excellent flexibility and resistance to wear, natural rubber belts are commonly used in general-purpose applications. They are well-suited for environments where the belt must bend and flex repeatedly without cracking.
- Synthetic Rubbers: Materials like SBR (Styrene-Butadiene Rubber), Nitrile, and EPDM (Ethylene Propylene Diene Monomer) are often used to enhance the belt’s performance under specific conditions. SBR offers superior abrasion resistance, making it ideal for handling rough materials like sand, gravel, and crushed stone. Nitrile rubber provides excellent resistance to oils and fats, making it suitable for food processing and industrial applications where exposure to such substances is frequent. EPDM is prized for its outstanding resistance to weathering, ozone, and chemicals, making it ideal for outdoor applications.
To further increase the strength and load-bearing capacity of rubber conveyor belts, they are often reinforced with layers of fabric or steel cords. This reinforcement not only boosts the belt’s tensile strength but also improves its ability to handle heavy loads without stretching or deforming.
Fabric Conveyor Belt Materials
Fabric conveyor belts are another critical category in the realm of heavy-duty materials, constructed from multiple layers of fabric that are coated and bonded with synthetic materials to form a robust and reliable belt. The choice of fabric plays a significant role in determining the belt’s performance, with common materials including polyester, nylon, and cotton.
- Polyester Fabric: Polyester is known for its low stretch characteristics, making it an excellent choice for long-distance conveying where minimal elongation is crucial. This low stretch property ensures that the belt maintains its shape and tension over extended periods, reducing the need for frequent adjustments and maintenance.
- Nylon Fabric: Nylon is highly resilient and offers superior shock and impact resistance, making it ideal for applications where the belt is subjected to sudden or heavy loads. Nylon belts are also known for their excellent flexibility, which allows them to navigate complex conveyor layouts with ease.
- Cotton Fabric: While less common in modern heavy-duty applications, cotton was historically used for its natural strength and durability. Today, cotton may still be found in specialized belts where natural materials are preferred, such as in certain food processing environments.
Fabric conveyor belts are available in a wide range of specifications, tailored to meet the specific needs of different industries. These specifications include the type of fabric weave, which can influence the belt’s flexibility and strength; the thickness of the fabric layers, which determines the overall durability and load capacity of the belt; and the type of coating material, which can be selected based on the operating environment. For example, a PVC (Polyvinyl Chloride) coating might be used for its resistance to chemicals and moisture, while a polyurethane coating might be chosen for its abrasion resistance and ease of cleaning.
Steel Reinforced Conveyor Belts
For the most demanding applications, such as in mining or heavy material handling, steel-reinforced conveyor belts are often the material of choice. These belts incorporate steel cords or cables embedded within the rubber or fabric layers, providing unparalleled tensile strength and resistance to elongation. This construction allows them to handle extremely heavy loads over long distances without sagging or stretching, making them indispensable in industries where reliability and durability are paramount.
- Steel Cord Belts: These belts are designed for high-tension applications and are commonly used in mining operations, where they transport large volumes of heavy materials over long distances. The steel cords provide exceptional strength and stability, ensuring that the belt remains stable under heavy loads.
- Stainless Steel Belts: In environments that require resistance to high temperatures, corrosion, or where hygiene is critical, such as in food processing or pharmaceutical industries, stainless steel belts are used. They offer excellent durability and are easy to clean, making them suitable for applications where contamination is a concern.
Hybrid and Composite Materials
In some cases, hybrid or composite materials are used to create conveyor belts that combine the best properties of different materials. For example, a belt might feature a rubber surface with a fabric or steel reinforcement layer, providing both flexibility and strength. These hybrid belts are designed to offer superior performance in specific applications, such as high-temperature environments, chemical processing, or where belts are exposed to extreme abrasion.
The materials used in heavy-duty conveyor belts are as diverse as the industries they serve. From the rugged durability of rubber to the strength of steel, and the specialized properties of synthetic fabrics, each material is chosen to meet the unique demands of its application. By understanding the properties and advantages of these materials, industries can select the right conveyor belt to ensure efficient, reliable, and long-lasting performance.
Benefits of Using Recycled Materials
Incorporating recycled materials, such as used conveyor belt rubber, into new conveyor belts presents multiple benefits:
- Cost-Effectiveness: Recycled materials are often more affordable than virgin materials, reducing manufacturing costs.
- Environmental Impact: Using recycled rubber helps reduce waste and the environmental footprint associated with disposal and production processes.
- Energy Conservation: Recycling materials requires less energy compared to producing new materials from scratch.
- Durability: Recycled rubber often retains much of the original material’s durability and wear resistance.
- Resource Efficiency: Utilizing recycled materials promotes resource efficiency and sustainability in industrial practices.
- Customization: Recycled materials can be processed and tailored to meet specific industrial needs.
- Market Demand: There is a growing market demand for environmentally friendly products, which can be met by using recycled materials.
- Regulatory Compliance: Using recycled materials can help companies comply with certain environmental regulations and standards.
The use of heavy duty conveyor belt materials such as rubber and fabric, coupled with the strategic integration of recycled materials, ensures operational efficiency, sustainability, and cost-effectiveness in industries that rely on robust conveying solutions. This blend of materials not only supports the operational goals but also aligns with global sustainability efforts.
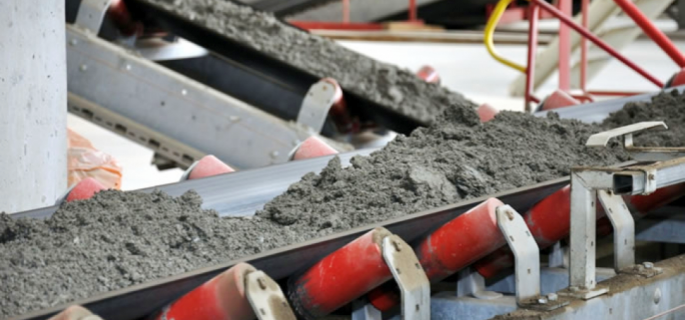
Top Materials for Heavy Duty Conveyor Belt Materials
When it comes to heavy duty conveyor belt materials, selecting the right type is crucial for ensuring performance, durability, and cost-effectiveness. This section provides a comparative analysis of the top materials used in heavy duty conveyor belts: rubber, fabric, and composites. Each of these materials offers distinct properties that make them uniquely suited for specific industrial tasks.
Comparative Analysis of Heavy Duty Conveyor Belt Materials
To clearly demonstrate the differences and advantages of each material type, a comparative analysis is presented in the table below:
Unique Properties of Materials
Rubber
Rubber is perhaps the most widely used material in heavy duty conveyor belts due to its high durability and flexibility. It can absorb shocks and impacts, which are common in industries such as mining and minerals processing. Rubber is especially effective in environments where the conveyor belt is exposed to extreme wear and tear. Additionally, the versatility of rubber allows it to be customized with various textures and additives to enhance performance against specific environmental challenges like oils, heat, and chemicals.
Fabric
Fabric belts are highly favored for their specific qualities like low stretch and excellent tensile strength, which make them ideal for stable, long-distance conveying. Typically made from materials such as polyester, nylon, or a blend of both, fabric belts are suitable for industries that require precise movement and alignment of goods, such as in the packaging or electronics industries. The fabric is often coated or treated to improve resistance to environmental factors like moisture, heat, and chemicals.
Composites
Composite materials are a newer development in heavy duty conveyor belt materials and include layers of different materials such as rubber, plastic, and fabric. These belts are engineered to combine the best properties of each component, resulting in belts that are lightweight yet durable, and resistant to a wide range of chemicals and temperatures. Composite belts are particularly advantageous in industries where reduced weight can lead to energy savings, such as in food processing or pharmaceuticals.
The choice of heavy duty conveyor belt material greatly depends on the specific needs of the industry and the operational environment. Rubber offers unmatched durability and flexibility for harsh conditions, fabric provides precision and stability for long distances, and composites offer a high-tech solution with multiple resistances for specialized applications. Understanding these unique properties allows industries to optimize their conveyor systems for performance, efficiency, and longevity.
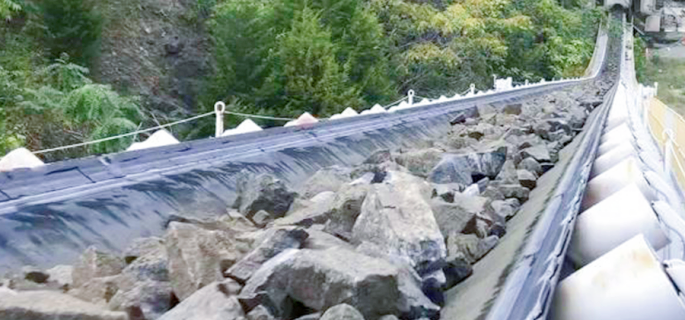
Heavy Duty Conveyor Belt Material for Demanding Applications
Heavy-duty conveyor belts for demanding applications must be specifically engineered to handle extreme conditions, whether that means heavy loads, abrasive materials, high temperatures, or corrosive environments. Below are the key materials and features that make a conveyor belt suitable for such challenging scenarios:
1. Steel Cord Belts
- Construction: These belts are reinforced with steel cords, which are embedded within the rubber or synthetic material layers. The steel cords provide exceptional tensile strength and resistance to elongation, making these belts ideal for very long distances and extremely heavy loads.
- Applications: Commonly used in mining, quarrying, and heavy material handling, where belts must transport large volumes of material over extended distances with minimal stretching.
2. Aramid/Kevlar-Reinforced Belts
- Construction: Aramid fibers, such as Kevlar, are used to reinforce conveyor belts, offering high strength while maintaining a relatively lightweight structure. These fibers are also known for their resistance to heat and wear.
- Applications: Ideal for high-temperature applications, heavy loads, and environments where the belt is exposed to sharp or abrasive materials. These belts are used in industries like steel production, cement manufacturing, and metal processing.
3. High-Temperature Resistant Belts
- Materials: Belts made from materials like silicone, Teflon (PTFE), or special heat-resistant rubbers (e.g., EPDM or fluorocarbon rubbers) are designed to withstand extreme temperatures.
- Applications: Used in environments where the belt must endure high temperatures, such as in baking, ceramics, or metal processing. These belts maintain their structural integrity and do not degrade when exposed to heat.
4. Oil and Chemical Resistant Belts
- Materials: Nitrile rubber or other synthetic compounds resistant to oils, chemicals, and solvents are used to construct these belts. This resistance ensures that the belts do not degrade when exposed to harsh chemicals or oils.
- Applications: Essential in industries like chemical processing, food processing, and recycling, where belts come into contact with oily or chemical-laden materials.
5. Flame Retardant Belts
- Materials: These belts are made from flame-retardant rubber compounds, often combined with steel or fabric reinforcements that also offer high tensile strength.
- Applications: Critical in underground mining, power generation, and other industries where fire hazards are a significant concern. These belts are designed to prevent the spread of fire and withstand high temperatures without combusting.
6. Abrasion-Resistant Belts
- Materials: Typically made from highly durable rubbers like SBR (Styrene-Butadiene Rubber) or a specially formulated compound with superior abrasion resistance.
- Applications: Used in quarrying, construction, and bulk material handling industries where belts are subject to continuous wear from abrasive materials like gravel, sand, or ores.
7. Heavy Duty Fabric-Reinforced Belts
- Construction: These belts are made with multiple layers of high-strength fabric, such as polyester or nylon, coated with rubber or other durable materials. The fabric layers provide flexibility while enhancing the belt’s strength and load-bearing capacity.
- Applications: Suitable for applications requiring high strength and flexibility, such as in aggregate processing, construction, and heavy manufacturing industries.
8. Specialty Hybrid Belts
- Construction: Hybrid belts combine different materials to create a belt with tailored properties for specific demanding applications. For instance, a belt might combine steel cords with a top layer of polyurethane for added durability and chemical resistance.
- Applications: Used in custom or highly specialized industrial processes where off-the-shelf solutions may not meet all the requirements.
9. Stainless Steel Belts
- Construction: These belts are made entirely from stainless steel, offering unmatched durability, resistance to corrosion, and ability to withstand extreme temperatures.
- Applications: Found in industries such as food processing, pharmaceuticals, and high-temperature material processing where hygiene, corrosion resistance, and temperature tolerance are critical.
When selecting a heavy-duty conveyor belt material for demanding applications, it’s crucial to consider the specific operational challenges, such as load capacity, temperature extremes, exposure to chemicals, or abrasive conditions. Each of these specialized materials offers distinct advantages that ensure reliable performance, extended service life, and safety in some of the most rigorous industrial environments. By matching the belt material to the demands of the application, industries can optimize their conveyor systems for efficiency, durability, and minimal downtime.
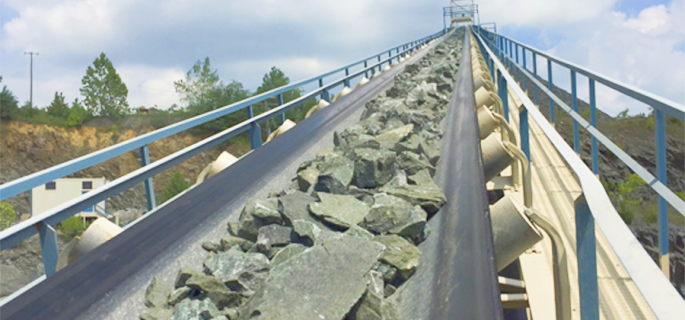
How to Choose the Right Heavy Duty Conveyor Belt Material
Choosing the right heavy-duty conveyor belt material is critical for ensuring the efficiency, longevity, and reliability of a conveyor system. The selection process involves considering several factors related to the operating environment, the materials being transported, and the specific requirements of the application. Here’s a step-by-step guide to help you choose the right heavy-duty conveyor belt material:
1. Understand the Application Requirements
- Material Type: Identify the type of materials being transported (e.g., abrasive, sharp, heavy, oily, or corrosive). The nature of the material directly influences the choice of belt material.
- Load Capacity: Determine the maximum load the conveyor belt will carry. Heavier loads may require reinforced belts, such as those with steel cords or multiple fabric layers.
- Conveyor Length and Speed: Consider the length and speed of the conveyor system. Long-distance and high-speed conveyors might need belts with low stretch properties and high tensile strength.
2. Assess the Operating Environment
- Temperature: Consider the operating temperature range. For high-temperature environments, materials like silicone or steel may be necessary. Conversely, rubber or PVC may be better for standard temperature ranges.
- Chemical Exposure: Identify any chemicals the belt will be exposed to. Chemical-resistant materials like nitrile rubber or certain polymers may be required in such environments.
- Environmental Conditions: Consider exposure to moisture, UV light, or extreme weather conditions. Materials like EPDM or stainless steel are ideal for outdoor or corrosive environments.
3. Evaluate Durability and Wear Resistance
- Abrasion Resistance: For applications involving abrasive materials, choose belts made from rubber with high abrasion resistance (e.g., SBR or natural rubber).
- Tear and Impact Resistance: In environments where the belt might be subject to tearing or heavy impact, materials like nylon or reinforced rubber provide added durability.
- Flexibility and Fatigue Resistance: For conveyors with frequent bends or flexing, a belt material that maintains flexibility without cracking, like natural rubber or polyester fabric, is essential.
4. Consider Special Requirements
- Oil and Grease Resistance: In food processing or industrial settings where the belt may come into contact with oils or fats, nitrile rubber or polyurethane belts are recommended.
- Fire Resistance: In environments with high fire risk, such as underground mining, choose a belt material that meets fire resistance standards.
- Sanitation and Hygiene: For food processing, pharmaceutical, or any application requiring high levels of hygiene, opt for materials that are easy to clean and resist bacterial growth, such as polyurethane or food-grade stainless steel.
5. Check Regulatory and Industry Standards
- Industry-Specific Regulations: Ensure the chosen belt material complies with industry-specific regulations, such as FDA approval for food-grade belts or MSHA (Mine Safety and Health Administration) approval for mining belts.
- Safety Standards: Confirm that the belt meets all relevant safety standards for the specific application, such as flame retardancy or anti-static properties.
6. Consult with Suppliers and Experts
- Supplier Recommendations: Engage with belt suppliers and manufacturers to get recommendations based on your specific application. They can offer insights into the latest materials and technologies available.
- Custom Solutions: In some cases, a standard belt material may not meet all your needs. Discuss the possibility of custom-engineered belts that combine materials to achieve the desired performance.
7. Test and Evaluate
- Prototyping: If possible, test a prototype of the selected belt material under real operating conditions. This can help identify any potential issues before full-scale implementation.
- Performance Monitoring: Once installed, monitor the belt’s performance over time. Adjustments may be necessary based on wear patterns, load changes, or environmental factors.
8. Cost Considerations
- Initial Cost vs. Longevity: While some materials may have a higher initial cost, they could offer longer service life, reducing the total cost of ownership.
- Maintenance and Downtime: Consider the ease of maintenance and the potential cost of downtime if the belt fails. Choosing a more durable material might save money in the long run by reducing maintenance needs and avoiding costly shutdowns.
Choosing the right heavy-duty conveyor belt material is a multifaceted process that requires careful consideration of the application, environment, and specific operational requirements. By thoroughly evaluating these factors and consulting with industry experts, you can select a conveyor belt material that provides optimal performance, durability, and cost-effectiveness for your application.
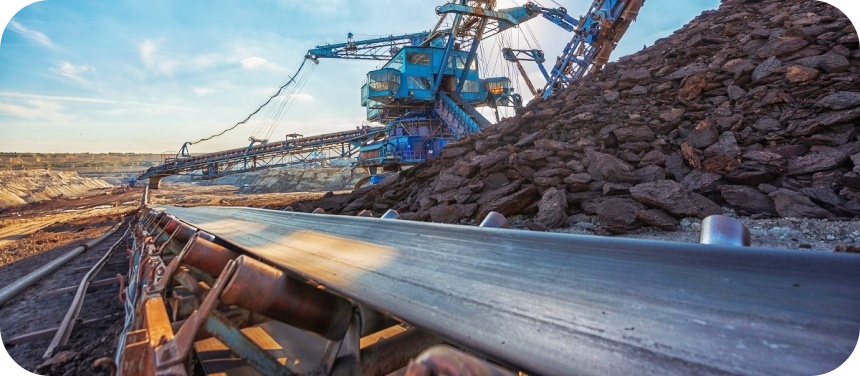
Manufacturers and Suppliers of Heavy Duty Conveyor Belt Material
When sourcing heavy duty conveyor belt material, selecting the right manufacturer and supplier is crucial for operational efficiency and cost management. Below is a detailed exploration of leading suppliers and key considerations for making the best choice.
Leading Manufacturers and Suppliers
- ContiTech AG – A global leader in rubber and plastics technology, ContiTech offers high-quality heavy duty conveyor belts that are robust and designed for extreme environments.
- Bridgestone Corporation – Known for innovation, Bridgestone produces durable heavy duty conveyor belt material suitable for mining and other heavy industries.
- Fenner Group Holdings Ltd – Fenner is recognized for its engineered conveyor solutions and ultra-strong belt materials tailored to heavy-duty applications.
- Yokohama Rubber Co., Ltd. – Specializing in high-tensile strength belts, Yokohama offers materials that withstand harsh conditions while maintaining longevity.
- Zhejiang Double Arrow Rubber Co., Ltd. – A leading Asian manufacturer known for cost-effective and reliable conveyor belt materials.
- Semperit AG Holding – Provides high-performance belt materials that are specifically designed to handle the toughest conveying tasks.
- Intralox – Offers innovative and sustainable conveyor solutions including heavy duty belt materials that reduce operational costs.
- Bando Chemical Industries, Ltd. – Known for high-quality materials and advanced technology, Bando’s conveyor belts are widely used in various heavy industries.
How to Choose the Right Supplier
Choosing the right supplier for heavy duty conveyor belt material involves considering several factors to ensure that the material quality, price, and customer service meet your specific needs. Here are 10 tips to guide your selection process:
- Material Quality – Ensure the materials used are top-grade and suitable for your specific industrial applications, with resistance to wear and tear.
- Customization Options – Check if suppliers offer bespoke solutions that can be tailored to your specific requirements.
- Price Comparison – Evaluate the pricing of different suppliers to find a cost-effective solution without compromising on quality.
- Technical Support – Choose suppliers who provide excellent technical support and can assist with any issues regarding the conveyor belts.
- Warranty and Guarantees – Look for suppliers that offer solid warranties and guarantees on their products, which indicates confidence in their quality.
- Supply Chain Reliability – Assess the reliability of the supplier’s supply chain to ensure timely deliveries and minimal downtime.
- Customer Reviews and Testimonials – Research customer reviews and seek testimonials to gauge the satisfaction of other clients.
- Certifications and Standards – Verify that the supplier adheres to international standards and holds relevant certifications.
- After-Sales Service – Consider the quality of after-sales service, which is crucial for maintenance and potential replacements.
- Experience in the Industry – Preference should be given to suppliers with extensive experience and a proven track record in heavy industries.
By following these guidelines, you can establish a reliable and cost-effective supply chain for your conveyor needs.
Cost Analysis of Heavy Duty Conveyor Belt Material
Evaluating the costs associated with heavy duty conveyor belt material is crucial for businesses looking to optimize their investments in conveyor systems. This section provides an overview of the pricing for new versus used conveyor materials and offers practical tips to ensure best value for money.
Pricing Overview: New vs. Used Conveyor Belt Materials
New Conveyor Belt Materials
- Price Range: The cost of new heavy duty conveyor belt material can vary significantly based on the type of material, belt width, and specific features required for different industrial applications. Prices typically range from $15 to $100 per foot.
- Advantages: New materials come with the latest technology and innovations, ensuring maximum efficiency and longevity. They are less likely to require early repairs or replacements, offering better reliability.
- Considerations: Higher initial investment is required, and depending on the specifications, the lead time for delivery might be longer.
Used Conveyor Belt Materials
- Price Range: Used heavy duty conveyor belts can cost as little as 35-50% of the price of new belts, depending on their condition and age.
- Advantages: Lower initial cost and often immediately available from stock. Suitable for businesses with limited budgets or those in need of a quick replacement.
- Considerations: Shorter lifespan, potential hidden damages, and reduced performance. Inspection and possible refurbishment might be needed.
Tips for Getting the Best Value for Money
- Assess Requirements Carefully: Define the exact requirements of your conveyor system to avoid over-specifying and paying for unnecessary features.
- Consider Total Cost of Ownership: Look beyond initial purchase prices to include maintenance, energy consumption, and expected lifespan.
- Compare Suppliers: Get quotes from multiple suppliers to compare prices and offerings for both new and used heavy duty conveyor belt materials.
- Negotiate Bulk Discounts: If purchasing in large quantities, negotiate for bulk discounts or additional services like free installation.
- Opt for Quality Over Price: Investing in higher-quality, durable materials can reduce long-term costs associated with repairs and downtime.
- Consider Customization Costs: Customization can significantly increase costs; ensure any modifications are essential for your operation.
- Evaluate Used Materials Thoroughly: When considering used belts, thoroughly evaluate their condition and suitability for your needs to avoid future expenditures.
- Plan for Long-Term Relationships: Building a long-term relationship with a reliable supplier could lead to better prices, terms, and priority service over time.
By following these tips, businesses can make informed decisions that balance cost with functionality, ultimately achieving better value for their investment in conveyor systems.
Enhance productivity with our reliable conveyor belts. Reach out today!
Where to Buy Heavy Duty Conveyor Belt Material
Finding reliable sources for heavy duty conveyor belt material, whether new or used, is crucial for maintaining the efficiency and longevity of industrial operations. This section provides detailed information on where to find these materials and offers advice on searching for suppliers both locally and online.
Where to Find Heavy Duty Conveyor Belt Materials
- Manufacturer Direct Sales: Many manufacturers sell conveyor belts directly to businesses, which can be a reliable source of both new and high-quality used belts.
- Industrial Supply Companies: Companies like Grainger and McMaster-Carr offer a wide range of conveyor materials and can provide quick delivery.
- Specialized Conveyor Suppliers: Look for suppliers specializing in industrial conveyor systems; they often have expert advice and a comprehensive inventory.
- Online Marketplaces: Websites like Alibaba, eBay, or Amazon can be sources for both new and used belts, often at competitive prices.
- Local Dealers: Checking with local dealers may provide the opportunity to inspect materials firsthand and reduce shipping costs.
- Surplus and Salvage Yards: These yards can be excellent sources for used heavy duty conveyor belt material at reduced prices.
- Trade Shows and Industrial Expos: These events are great for meeting multiple suppliers, comparing products, and negotiating deals in person.
- Referral from Industry Contacts: Networking within the industry can lead to recommendations for reputable suppliers.
- Used Equipment Dealers: Specific dealers focus on selling used industrial equipment and can be a good source for heavy duty conveyor belts.
- Factory Outlets and Liquidators: These outlets often sell off excess stock from manufacturers at discounted rates.
Advice on Searching for Suppliers
- Define Your Requirements: Know the specifications you need, including material type, belt width, and load capacity, to narrow down potential suppliers.
- Use Search Engines: Utilize search engines by entering specific keywords like “heavy duty conveyor belt material suppliers near me” to find local options.
- Check Supplier Reputation: Look for online reviews, testimonials, and case studies to assess the reliability and quality of suppliers.
- Visit Supplier Websites: Detailed information on product ranges, pricing, and company policies is often available on the official websites.
- Ask for Quotes: Contact multiple suppliers for quotes to compare prices and services offered.
- Check Certification: Ensure that the suppliers are certified by relevant industrial standards, which can be a mark of quality and reliability.
- Consider Delivery Options: Evaluate the delivery terms and costs, as conveyor belts can be bulky and expensive to ship.
- Utilize Online Directories: Online directories and industry-specific platforms can provide lists of suppliers, often with filtering options to find those closest to you.
By utilizing these tips and information, businesses can effectively locate and purchase the right conveyor belt materials, ensuring the optimal function and efficiency of their operations.
Case Studies and Applications of Heavy Duty Conveyor Belt Materials
Heavy duty conveyor belt materials play a pivotal role in various industries by enhancing operational efficiency and durability. This section delves into six real-world applications of these materials in sectors such as mining, manufacturing, and recycling. Additionally, it presents case studies that highlight the effectiveness and efficiency improvements achieved through the use of the appropriate conveyor belt materials.
Real-World Applications
- Mining Industry: In the mining sector, heavy duty conveyor belts made from reinforced rubber are used to transport large volumes of ore over great distances. These belts are designed to withstand the harsh conditions of mining environments, including the abrasive nature of the materials and the exposure to extreme weather conditions.
- Manufacturing: In automotive manufacturing, fabric conveyor belts are used to move parts through assembly lines. The low stretch and high tensile strength of fabric belts ensure precise positioning of components, which is crucial for automation and assembly precision.
- Recycling Facilities: Recycling operations often use rubber conveyor belts with specific modifications to handle various recyclables. These belts are treated to resist the abrasive and cutting action of metal, glass, and other sharp objects found in recycling streams.
- Agriculture: Heavy duty conveyor belts are also essential in the agricultural industry for the transport of grains and other bulk materials. These belts often use composites to resist the wear and tear caused by rough materials and exposure to outdoor elements.
- Cement Production: The cement industry relies on very durable rubber conveyor belts to move limestone, clay, and other materials into and through the production process. These belts are equipped with high heat-resistant properties to cope with the high temperatures of kilns.
- Food Processing: In food processing, composite conveyor belts are used due to their ability to resist corrosion, ease of cleaning, and compliance with food safety regulations. These belts can handle rapid temperature changes and aggressive cleaning protocols, making them ideal for food handling applications.
Case Studies
Mining Operation Efficiency
A major mining company switched to a customized rubber conveyor belt designed to handle extreme loads and abrasive materials. This change resulted in a 20% increase in material throughput and a significant reduction in maintenance downtime, demonstrating the belt’s enhanced durability and performance under tough conditions.
Automotive Assembly Line Improvement
An automotive manufacturer introduced fabric conveyor belts in their assembly lines. The new belts provided better stability and reduced the margin of error in component placement by 15%. This improvement led to a smoother production line flow and increased the overall efficiency of the assembly process.
Recycling Facility Upgrade
A recycling facility upgraded their conveyor system to a specialized rubber belt that was better suited for handling sharp and abrasive recycled materials. The upgrade led to a 30% reduction in belt damage incidents and a longer lifespan for the conveyor system, thereby decreasing operational costs and increasing processing speeds.
These case studies and applications illustrate the critical role that heavy duty conveyor belt materials play in various industrial settings. By choosing the right conveyor belt material, companies can achieve greater operational efficiency, reduce maintenance costs, and extend the lifespan of their equipment, ultimately leading to improved business outcomes.
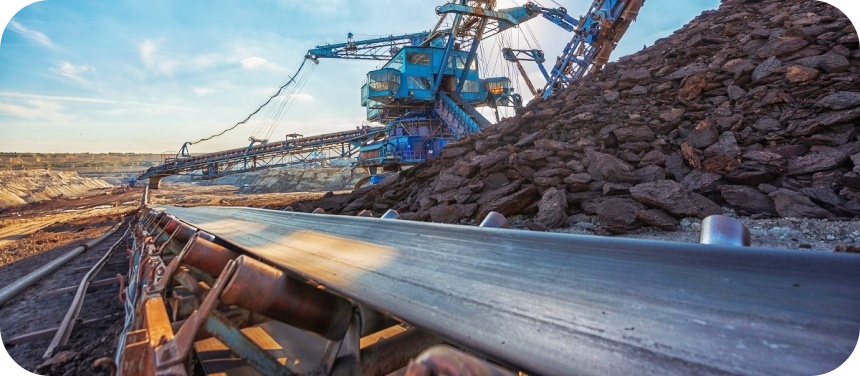
Future Trends and Innovations in Heavy Duty Conveyor Belt Material
The landscape of industrial machinery, especially heavy duty conveyor belt material, is rapidly evolving with advances in technology and new materials. This section discusses future developments in conveyor belt technology and potential advancements that could significantly enhance the durability and functionality of these essential industrial components.
Future Developments in Conveyor Belt Technology
- Smart Conveyor Belts: Integration of IoT sensors to monitor the health and performance of conveyor belts in real-time, predicting maintenance needs before failures occur.
- Eco-friendly Materials: Increased focus on sustainability will lead to the development of more environmentally friendly materials that are both durable and cost-effective.
- Improved Energy Efficiency: Advances in material science may produce belts that require less energy to operate, reducing the overall carbon footprint of industrial operations.
- Enhanced Durability: New compounds and weaving techniques are expected to significantly increase the lifespan of belts under extreme conditions.
- Customizability and Flexibility: Future belts might come with improved customization options, allowing for quicker adaptations to different uses and settings.
- Temperature and Chemical Resistance: Development of materials that can withstand higher temperatures and harsh chemicals, expanding the scope of applications.
- Lightweight Designs: Lighter belt materials that maintain strength and durability could revolutionize the efficiency of transport systems.
- Advanced Wear Detection: Technologies that visually or through sensors detect wear and tear, alerting operators to the precise need for belt maintenance or replacement.
Potential Advancements Enhancing Durability and Functionality
- Self-Healing Materials: Introduction of materials that can automatically repair minor cuts and abrasions, prolonging belt life.
- High-Temperature Resilience: New materials capable of enduring extreme temperatures without losing structural integrity.
- Anti-Static Technology: Development of belts that inherently prevent static build-up, crucial in industries handling flammable materials.
- Improved Splice Techniques: Advanced splicing methods that enhance the strength and longevity of belt joints.
- Greater Load Capacity: Innovations that allow belts to carry heavier loads without compromising speed or requiring wider belts.
- Modular Design: Conveyor belts with modular sections that can be easily replaced or modified as needed, enhancing flexibility and repairability.
- Enhanced Impact Resistance: Materials designed to absorb impacts and resist punctures, critical in heavy-duty mining and recycling applications.
- Better Lateral Stability: Conveyor belts with improved design to maintain lateral stability under high-speed and high-load conditions.
- Smart Tracking Features: Embedded tracking features that automatically adjust the belt alignment, reducing wear and increasing efficiency.
- Hybrid Materials: Combining different materials to create composite belts that offer the best properties of each, such as rubber with reinforced fibers or metals.
These future trends and innovations in are set to transform the efficiency, sustainability, and operational capabilities of industries worldwide. By embracing these advancements, companies can expect not only to enhance their conveyor systems but also to contribute positively to environmental sustainability and economic efficiency.
FAQs about Heavy Duty Conveyor Belt Material
Conveyor belts are constructed from various materials, tailored to their application and the industry they serve. The choice of material impacts the belt’s strength, durability, flexibility, and suitability for specific tasks. Commonly, conveyor belts are made from materials like rubber, plastics (such as PVC or polyurethane), fabric (including polyester, nylon, and cotton), and metals (for structural support or specific functionality).
Rubber belts, often reinforced with materials like steel, are popular for their durability and versatility. They’re used in everything from mining operations to grocery checkout lines. Plastic belts are lightweight and can be designed for easy cleaning, making them ideal for food processing or pharmaceutical industries. Fabric belts, usually combined with other materials to add strength, offer flexibility and are used in a range of environments. Additionally, high-performance materials like Kevlar are used when extra strength or thermal resistance is needed.
A heavy-duty conveyor belt is designed for the toughest applications, capable of transporting heavy loads, abrasive materials, or operating under extreme conditions. These belts are built to withstand significant wear and tear, offering higher durability, tensile strength, and impact resistance compared to standard conveyor belts. They typically feature thick, robust materials like reinforced rubber or metals, and may include specific design elements like high-grade cover compounds to resist abrasion, heat, and other harsh environmental factors.
Heavy-duty belts are essential in industries like mining, construction, and metals processing, where they handle materials such as ores, rock, and heavy manufactured goods. The performance characteristics of heavy-duty belts also include high resistance to tearing, puncturing, and damage from oils and chemicals, ensuring longevity and reliability in demanding settings.
The title of the “strongest” conveyor belt could be attributed to ultra-heavy-duty belts used in mining and quarrying operations, where they transport massive loads over long distances. One standout example includes belts made from layers of specially engineered fabrics like Kevlar or other high-performance materials, reinforced with steel cables or meshes. These belts are designed not only for strength but also for flexibility, impact resistance, and durability under heavy loads.
Moreover, the strongest conveyor belts feature advanced design technologies, such as rip-stop mechanisms that prevent tears from spreading, and heat-resistant compounds capable of withstanding extreme temperatures. These belts are pivotal in applications that require the moving of extraordinarily heavy or abrasive materials, proving essential in maintaining efficient, continuous operations in some of the world’s most challenging industrial environments.
For heavy-duty conveyor belts, materials that provide exceptional strength, durability, and resistance to harsh conditions are used. These include:
Reinforced Rubber: Thick, durable rubber often reinforced with steel cables or fabric layers for added strength and resistance to tearing.
Steel Cables and Mesh: Used for reinforcement, these materials offer unmatched tensile strength, making the belt capable of handling very heavy loads.
High-Performance Fabrics: Materials such as Kevlar are used for their extraordinary strength-to-weight ratio, providing the belt with resistance to impacts, cuts, and abrasions.
Specialty Compounds: Cover compounds designed to withstand heat, chemicals, oils, and abrasion are used in heavy-duty conveyor belts to enhance performance and service life.
Such materials ensure that heavy-duty conveyor belts can sustain the operational demands of industries requiring the transportation of heavy or abrasive materials, such as mining, construction, and aggregate production.
Industrial belts are typically made from a variety of materials, depending on their intended application. Common materials include rubber, neoprene, polyurethane, nylon, polyester, and kevlar. Rubber is often reinforced with layers of fabric or steel cords to provide added strength and durability. Polyurethane belts are favored for their flexibility and resistance to wear and chemicals, while nylon and polyester are used for their strength and resistance to stretching. In more demanding applications, kevlar or steel-reinforced belts are used for added tensile strength and longevity.
For handling bulk materials, belt conveyors are the most commonly used type. Specifically, troughed belt conveyors are designed to handle large volumes of bulk materials like coal, ore, grain, sand, and gravel. The belt is shaped into a trough by idlers or rollers, which helps to contain the material as it is transported. Other conveyors used for bulk material handling include screw conveyors, drag chain conveyors, and bucket elevators, depending on the nature of the material and the specific application.
Rubber conveyor belts are typically made from natural rubber or synthetic rubber compounds, such as neoprene or nitrile rubber, which provide flexibility and durability. These rubber layers are often reinforced with materials like polyester, nylon, cotton, or steel cords to enhance the belt’s strength, resistance to stretching, and overall durability. The choice of rubber and reinforcement materials depends on the specific requirements of the application, such as resistance to heat, chemicals, or abrasion.
Roller conveyors and chain conveyors are commonly used for transporting heavy unit loads. Roller conveyors consist of a series of rollers supported in a frame over which objects are moved manually, by gravity, or by power. They are ideal for transporting heavy items like pallets, containers, and machinery. Chain conveyors use chains to drive heavy items, often in assembly lines, and are well-suited for moving items such as automotive components or large industrial parts.
Conveyor belts are made rough to increase the friction between the belt and the materials being transported, preventing slippage. The rough texture provides a better grip on the items, especially when transporting goods on an incline or when handling materials that might shift during transport. The rough surface also aids in moving materials that are prone to sliding or rolling, ensuring consistent and safe transportation along the conveyor system.
A conveyor belt’s ply material typically consists of layers of fabric such as nylon, polyester, or cotton, which are embedded within the rubber. These fabric layers, known as plies, provide tensile strength and flexibility to the belt. The number of plies in a conveyor belt varies depending on the required strength and flexibility for the application. For more demanding applications, steel cords or kevlar can be used as reinforcement layers instead of or in addition to fabric plies.
Last Updated on August 9, 2024 by Jordan Smith
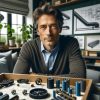
Jordan Smith, a seasoned professional with over 20 years of experience in the conveyor system industry. Jordan’s expertise lies in providing comprehensive solutions for conveyor rollers, belts, and accessories, catering to a wide range of industrial needs. From initial design and configuration to installation and meticulous troubleshooting, Jordan is adept at handling all aspects of conveyor system management. Whether you’re looking to upgrade your production line with efficient conveyor belts, require custom conveyor rollers for specific operations, or need expert advice on selecting the right conveyor accessories for your facility, Jordan is your reliable consultant. For any inquiries or assistance with conveyor system optimization, Jordan is available to share his wealth of knowledge and experience. Feel free to reach out at any time for professional guidance on all matters related to conveyor rollers, belts, and accessories.