Choosing the Heavy Duty Powered Roller Conveyor for Your Needs
The heavy duty powered roller conveyor stands as a cornerstone in the infrastructure of modern industrial applications, providing an indispensable solution for the efficient transportation of large and heavy loads. Engineered to withstand the rigorous demands of heavy manufacturing, warehousing, and distribution environments, these conveyors are built with durability and strength at their core. The use of heavy duty powered roller conveyors brings about a transformative improvement in operational efficiency, significantly reducing the manual labor required to move bulky items. Furthermore, their robust construction ensures reliability and longevity, minimizing downtime and maintenance requirements. By integrating heavy duty powered roller conveyors into their operations, industries can achieve a seamless flow of goods, enhancing productivity and facilitating the smooth execution of complex logistical tasks. The advantages of deploying such advanced material handling systems are clear, marking them as an essential asset for businesses looking to optimize their heavy load management processes.
What is Heavy Duty Powered Roller Conveyors
The heavy duty powered roller conveyor is a robust version of the standard powered conveyor systems, designed specifically to transport heavy loads across various industrial settings. Unlike their lighter counterparts, these conveyors are built with stronger materials and more powerful motors to handle the additional weight and stress of heavy goods. The basic operation principle involves motorized rollers that propel items along the conveyor belt, providing a continuous flow of materials with minimal manual intervention.
Distinction Between Standard and Heavy Duty Versions
The key differences between standard powered roller conveyors and heavy duty versions are evident in their design, capacity, and application:
- Material Construction: Heavy duty conveyors are constructed with thicker steel frames and rollers to withstand heavier loads, whereas standard conveyors might use lighter materials for efficiency and cost savings.
- Motor Power: The motors used in heavy duty powered roller conveyors are more powerful to move heavy items without strain, unlike the less powerful motors found in standard versions.
- Roller Diameter: Larger roller diameters are a feature of heavy duty conveyors to support the weight of heavy items, providing stability and reducing the risk of deformation under load.
- Load Capacity: Heavy duty conveyors are designed to handle significantly higher load capacities, often exceeding thousands of pounds, compared to the lighter capacities suitable for standard conveyors.
- Application Environments: Heavy duty versions are often found in environments like mining, heavy manufacturing, and construction, where the materials handled are bulkier and heavier, whereas standard conveyors are more common in packaging, light manufacturing, and distribution centers.
Types of Powered Roller Conveyors
Powered roller conveyors come in various types to suit different operational needs, including:
- 24VDC Powered Roller Conveyor: Utilizes 24-volt direct current motors embedded within the conveyor rollers to provide quiet, efficient, and safe movement of goods. Ideal for applications requiring precise control and flexibility.
- Chain Driven Roller Conveyor: Features rollers that are driven by a chain system, making it suitable for heavy loads and harsh environments. This type is particularly effective for moving pallets, drums, and other large items.
- Heavy Duty Gravity Roller Conveyor: Though not motorized, this type relies on gravity and is built to support heavy items as they move down an incline. It’s often used in conjunction with powered systems to create a comprehensive material handling solution.
Understanding the nuances of heavy duty powered roller conveyors and their distinctions from standard models is crucial for businesses that handle heavy or bulky items. By selecting the appropriate type and specifications, industries can significantly enhance their operational efficiency and safety, ensuring the smooth and reliable transport of goods across their facilities.
Key Features and Technical Specifications of Heavy Duty Powered Roller Conveyor
The heavy duty powered roller conveyor is engineered to meet the rigorous demands of industries that handle heavy loads daily. Its design and features are tailored to ensure durability, reliability, and efficiency in transporting heavy materials across various operational environments. Here’s a closer look at the characteristics that define these robust systems.
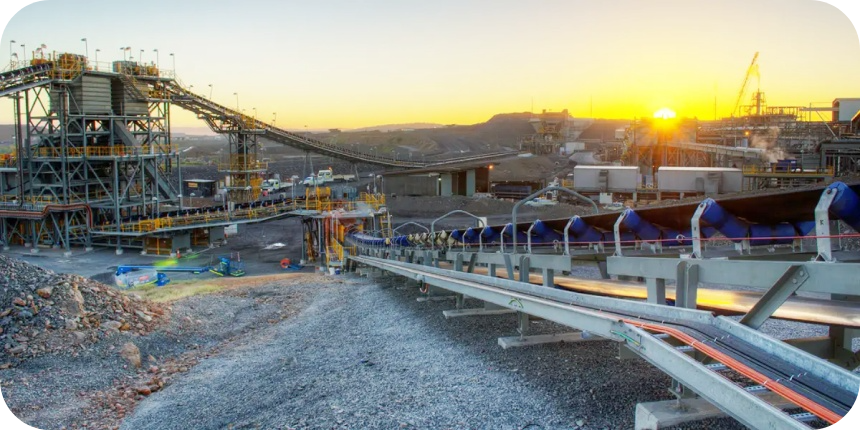
Design and Features
- Industrial Rollers: The rollers in a heavy duty powered roller conveyor are made from high-grade steel or reinforced plastics designed to withstand heavy loads. For example, rollers may have a diameter of 2.5 inches or more to support heavier weights.
- Load Capacity: These conveyors are designed to handle loads that can exceed 5000 pounds, depending on the specific model and configuration. This high load capacity is achieved through reinforced frame construction and roller design.
- Enhanced Motorization: Heavy duty conveyors are equipped with powerful motors to ensure consistent movement of heavy items without lag or strain. Motors are often rated for continuous use under full load conditions.
- Robust Frame Construction: The frames are constructed from heavy-gauge steel or aluminum, providing the necessary support and stability for heavy loads. This might include additional cross-bracing or thicker side rails.
- Advanced Control Systems: To manage the movement of heavy loads efficiently, these conveyors incorporate advanced control systems. These can include variable speed controls, direction change capabilities, and integration with warehouse management systems.
Technical Specifications
- Roller Diameter: The diameter of the rollers is a critical specification, with heavy duty conveyors often featuring rollers 2.5 inches in diameter or larger to distribute the weight of heavy loads more evenly.
- Frame Construction: The frames of heavy duty conveyors are built with thicker materials, such as steel plates that are 1/4 inch thick or more, to ensure durability and longevity under heavy use.
- Motorization: Motors used in these conveyors are high-torque and high-horsepower models, capable of moving heavy loads at consistent speeds. Specifications might include motors rated for 1 HP or more.
- Bearing and Axle Strength: Bearings and axles are designed to withstand the stress of heavy loads, with specifications that exceed standard conveyor systems. This might include double-sealed bearings and axles made from hardened steel.
- Control and Automation Features: Technical specifications also include advanced control features, such as PLC integration, sensor-based load detection, and programmable operation modes to optimize efficiency and safety.
Insights into Design PDFs
For those seeking a deeper understanding of the engineering behind heavy duty powered roller conveyors, design PDFs offer comprehensive insights. These documents detail the materials, dimensions, and engineering principles that contribute to the conveyor’s strength and functionality:
- Detailed diagrams illustrating frame construction and roller placement.
- Specifications for motors, including power ratings and operational efficiency.
- Load capacity charts that help users select the right conveyor for their needs.
- Installation and maintenance guides to ensure long-term reliability.
- Customization options for specific industrial applications.
By examining these design PDFs, potential users and engineers can gain a thorough understanding of what makes a heavy duty powered roller conveyor capable of handling the most demanding material transport tasks. This knowledge is crucial for selecting a system that meets the specific needs of heavy industrial operations.
Selecting the Right Heavy Duty Powered Roller Conveyor for Industrial Needs
Choosing the right heavy duty powered roller conveyor is pivotal for optimizing industrial operations, ensuring the seamless movement of goods, and maintaining high productivity levels. Several critical factors must be considered to select a conveyor system that meets the specific needs of your industrial application effectively.
Factors to Consider
- Material Type: The nature of the materials being transported plays a significant role in conveyor selection. For instance, abrasive materials may require conveyors with specially coated rollers, while magnetic materials might benefit from conveyors with magnetic rollers to prevent slippage.
- Weight Capacity: It’s essential to choose a conveyor that can handle the maximum weight of your products. Heavy machinery parts, for example, necessitate a conveyor with a high weight capacity, reinforced frame construction, and robust rollers.
- Environmental Conditions: The operating environment can greatly affect the longevity and functionality of a conveyor. Conveyors used in cold storage facilities must withstand low temperatures, whereas those in chemical plants need to be resistant to corrosive substances.
- Operational Speed: The required speed of the conveyor should align with your production rates. High-speed conveyors are ideal for fast-paced assembly lines, while slower speeds might be necessary for applications involving detailed assembly or inspection processes.
- Integration with Existing Systems: The ability to integrate the conveyor with existing material handling systems is crucial. This includes compatibility with warehouse management software, automated sorting systems, and other conveyors.
Importance of Custom Conveyor Solutions
Custom conveyor solutions are often necessary to meet the unique demands of different industries and applications. Here are five examples illustrating the importance of customization:
- Automotive Assembly: Custom conveyors with precise speed control and integration capabilities are essential for synchronizing the movement of parts through various assembly stages.
- Food Processing: Conveyors designed with food-grade materials and easy-to-clean surfaces are crucial for maintaining hygiene standards in food processing applications.
- Pharmaceuticals: In pharmaceutical manufacturing, conveyors must ensure gentle handling to prevent damage to delicate products and accommodate cleanroom conditions.
- E-commerce Fulfillment: Customized conveyors with advanced sorting and tracking capabilities can significantly enhance the efficiency of e-commerce fulfillment centers, handling a high volume of orders with varying sizes and weights.
- Heavy Manufacturing: Industries involved in heavy manufacturing require conveyors that are customized for extreme weight capacities, with durable construction to handle heavy components like steel beams or automotive engines.
Selecting the right heavy duty powered roller conveyor involves careful consideration of the materials to be transported, the operational environment, weight capacity, and the need for integration with existing systems. Customization plays a key role in ensuring that the conveyor system not only meets the specific requirements of the application but also contributes to the overall efficiency and productivity of the industrial operation. By addressing these factors, businesses can invest in a conveyor solution that offers reliability, durability, and a high return on investment.
Top Manufacturers and Buying Guide for Heavy Duty Powered Roller Conveyor
Selecting the right heavy duty powered roller conveyor is crucial for industrial operations that require the transportation of heavy loads. This section provides an overview of leading manufacturers, essential tips for choosing the best conveyor, and guidance on purchasing options.
Leading Manufacturers
- Hytrol Conveyor Company: Hytrol is renowned for its comprehensive range of conveyor solutions, including heavy duty powered roller conveyors designed for durability and efficiency. What sets Hytrol apart is its commitment to innovation and customer service, offering tailored solutions to meet specific industry needs.
- Interroll Group: Interroll is recognized for its modular conveyor platforms that provide flexibility and scalability. Their heavy duty conveyors are known for energy efficiency and low maintenance requirements, making them a cost-effective choice for many businesses.
- Dematic: Specializing in integrated automated technology, Dematic offers heavy duty powered roller conveyors that are robust and designed for seamless integration into complex logistics systems, enhancing operational efficiency.
- Titan Conveyors: Titan is distinguished by its custom conveyor solutions, particularly for heavy industrial applications. Their heavy duty conveyors are built to withstand harsh environments and heavy loads, ensuring long-term reliability.
- Conveyor Systems Ltd (CSL): CSL stands out for its bespoke conveyor designs, including heavy duty options that cater to specific operational challenges. Their focus on solving unique material handling problems makes them a preferred choice for industries with specialized needs.
Tips for Selecting the Best Conveyor
- Assess Your Load Requirements: Consider the maximum weight your conveyor will need to handle and ensure the system’s load capacity exceeds this to avoid overloading and potential damage.
- Consider the Operating Environment: Whether your operation is in a clean room, a wet environment, or exposed to harsh chemicals, make sure the conveyor material and design are suitable for these conditions.
- Evaluate Integration Capabilities: If you’re integrating the conveyor into an existing system, check for compatibility, especially regarding control systems and material handling automation.
- Look for Customization Options: Manufacturers that offer customization can tailor the conveyor to your specific needs, whether it’s adjustable speeds, special coatings for rollers, or specific conveyor lengths.
- Prioritize Safety and Ease of Maintenance: Choose conveyors designed with safety features and easy access for maintenance. This ensures not only the safety of your operations but also the longevity and reliability of the conveyor system.
Purchasing Options and Price Considerations
Heavy duty powered roller conveyors can be found through direct manufacturer sales, specialized industrial equipment distributors, and online marketplaces. When considering the price, it’s important to look beyond the initial purchase cost and evaluate the total cost of ownership, which includes maintenance, energy consumption, and potential downtime costs. Requesting quotes from multiple suppliers and inquiring about financing options or leasing agreements can also help manage the investment. Additionally, consider the warranty and after-sales support offered, as these can significantly impact the long-term value of your conveyor system.
By carefully evaluating manufacturers, assessing your specific needs, and considering long-term costs and benefits, you can select the best heavy duty powered roller conveyor that will serve your business reliably for years to come.
Installation, Maintenance, and Safety of Heavy Duty Powered Roller Conveyor
The heavy duty powered roller conveyor is a critical component in industrial operations, designed to handle heavy loads with efficiency and reliability. Proper installation, regular maintenance, and adherence to safety protocols are essential to maximize its performance and ensure the safety of the workforce.
Installation Guidance
- Site Preparation: Before installation, ensure the site is level and capable of supporting the weight of the conveyor and the products it will carry. This may involve reinforcing the floor or constructing a dedicated platform.
- Integration with Existing Systems: If integrating the heavy duty powered roller conveyor into an existing system, carefully plan the layout to ensure seamless material flow. This might include aligning conveyor heights and speeds and ensuring compatibility with existing control systems.
- Electrical Requirements: Verify that the electrical supply matches the conveyor’s requirements. Professional installation of electrical components is crucial to prevent overloads and ensure efficient operation.
- Assembly and Testing: Follow the manufacturer’s instructions for assembly, paying close attention to the alignment of rollers and the tension of belts or chains. Conduct thorough testing with load samples to ensure the conveyor operates as expected before full-scale operation.
- Training: Train staff on the operation of the heavy duty powered roller conveyor, emphasizing control panel functions, emergency stops, and proper loading techniques.
Maintenance Best Practices
- Regular Inspections: Conduct routine inspections to identify wear and tear, especially on rollers, bearings, and motor units. Early detection of issues can prevent costly downtime.
- Lubrication: Regularly lubricate moving parts according to the manufacturer’s recommendations. Proper lubrication reduces friction, wear, and extends the life of the conveyor.
- Cleaning: Keep the conveyor clean from debris and dust that can accumulate on rollers and in the conveyor track, potentially hindering performance.
- Belt and Chain Tension: Regularly check and adjust the tension of belts and chains to prevent slippage and ensure smooth operation.
- Record Keeping: Maintain detailed records of maintenance activities, inspections, and any repairs. This documentation can help identify recurring issues and inform future maintenance schedules.
Safety Protocols and Features
- Emergency Stops: Ensure that emergency stop buttons are accessible along the length of the conveyor. Regularly test these features to confirm they are in working order.
- Guardrails and Covers: Install guardrails and covers where necessary to protect workers from moving parts and prevent accidental contact with the conveyor.
- Warning Signs and Labels: Clearly label operational controls, load capacities, and safety warnings. Use visible signage to remind workers of safety practices.
- Personal Protective Equipment (PPE): Require the use of appropriate PPE, such as gloves and safety glasses, when operating or maintaining the conveyor.
- Safety Training: Conduct regular safety training sessions that cover the correct operation of the heavy duty powered roller conveyor, emergency procedures, and the importance of PPE.
By adhering to these guidelines for installation, maintenance, and safety, businesses can ensure that their heavy duty powered roller conveyor operates efficiently, lasts longer, and contributes to a safe working environment. These practices not only protect the investment in material handling equipment but also safeguard the well-being of employees.
Case Studies and Applications of Heavy Duty Powered Roller Conveyor
The heavy duty powered roller conveyor has proven to be an invaluable asset across a wide range of industries, demonstrating versatility and efficiency in handling heavy loads. Below are real-world examples and benefits realized by businesses that have implemented these robust systems.
Request more information on our Heavy Duty Powered Roller Conveyor by filling out the form.
Real-World Examples
- Automotive Manufacturing: A leading automotive manufacturer integrated heavy duty powered roller conveyors into their assembly line to transport engine components. The system’s durability and ability to handle heavy loads streamlined the assembly process, reducing manual handling and increasing production speed.
- E-commerce Fulfillment Centers: An e-commerce giant utilized heavy duty powered roller conveyors to manage the high volume of orders. The conveyors efficiently moved large and heavy packages through the sorting and packaging areas, significantly improving order processing times.
- Food and Beverage Distribution: A national food and beverage distributor implemented heavy duty powered roller conveyors in their distribution center. The conveyors were used to transport pallets of canned goods and beverages, enhancing the speed and efficiency of loading and unloading trucks.
- Heavy Machinery Manufacturing: A manufacturer of construction equipment used heavy duty powered roller conveyors to move large parts through the welding and assembly stages. The conveyors’ robust design and load capacity ensured the safe and smooth transport of heavy components.
- Pharmaceutical Warehousing: A pharmaceutical company employed heavy duty powered roller conveyors in their warehousing facility to handle bulk drug shipments. The system’s reliability and gentle handling of sensitive products ensured compliance with safety standards while optimizing storage and retrieval processes.
Benefits Realized
- Increased Productivity: Businesses reported a significant increase in productivity due to the automation of material handling processes. The heavy duty powered roller conveyors allowed for continuous operation, reducing downtime and manual labor requirements.
- Enhanced Safety: Implementing heavy duty powered roller conveyors reduced workplace injuries associated with manual handling of heavy items. The automated system minimized human interaction with heavy loads, leading to a safer working environment.
- Improved Efficiency: The precision and speed of heavy duty powered roller conveyors streamlined operations, allowing for faster processing and turnaround times. This efficiency was particularly beneficial in industries with high-volume or time-sensitive requirements.
- Cost Savings: Over time, businesses experienced cost savings from reduced labor costs, lower maintenance expenses, and minimized product damage during handling. The durability and reliability of heavy duty powered roller conveyors contributed to lower total cost of ownership.
- Scalability: The modular design of many heavy duty powered roller conveyors allowed businesses to easily expand or reconfigure their systems as their operational needs changed. This scalability ensured that the conveyor system could grow in tandem with the business, providing a long-term material handling solution.
These case studies and benefits highlight the transformative impact of heavy duty powered roller conveyors across various industries. By optimizing material handling processes, enhancing safety, and improving operational efficiency, these systems offer a compelling solution for businesses looking to handle heavy loads more effectively.
FAQs About Heavy Duty Powered Roller Conveyor
A powered roller conveyor is a material handling system designed to transport goods across short or long distances within industrial settings. Unlike manual or gravity conveyors, powered roller conveyors use electric motors to move the rollers, propelling items placed on them forward. This automation allows for the efficient, consistent, and controlled movement of products, making it an essential component in manufacturing lines, distribution centers, and warehouses. Powered roller conveyors are highly adaptable and can handle a wide range of products, from small packages to large pallets, with varying weights and sizes. They are particularly valued for their ability to improve operational efficiency, reduce labor costs, and enhance workplace safety by minimizing manual handling of goods.
A heavy-duty conveyor is designed to handle especially heavy or bulky loads, often in challenging industrial environments. These conveyors are built with robust materials and components to withstand the rigors of heavy use, including the transport of metal parts, large pallets, or construction materials. Heavy-duty conveyors come in various types, including belt conveyors, roller conveyors, and chain conveyors, each tailored to specific tasks such as assembly, sorting, or transportation. Features like reinforced frames, thicker belts, larger motors, and high-capacity rollers distinguish them from standard conveyors. They are crucial in industries like mining, construction, automotive, and heavy manufacturing, where durability and reliability under heavy loads are paramount.
Conveyors are categorized based on their mechanism of operation and the specific applications they serve. The three primary types are:
Belt Conveyors: These use a continuous belt looped over a series of pulleys to transport materials. They are versatile and can carry a wide range of items, from loose materials to packaged goods.
Roller Conveyors: Comprising a series of rollers mounted on a frame, roller conveyors move goods either by gravity (for inclined systems) or through motorized rollers for flat or variable incline applications.
Chain Conveyors: These utilize a chain or multiple chains to move pallets or other large, heavy items. Chain conveyors are particularly useful for heavy-duty applications where durability and the ability to move large loads are required.
Each type offers unique advantages and is suited to specific tasks and environments, from gentle handling of delicate items to the transport of heavy goods.
Roller conveyors are differentiated by their method of propulsion and the applications they are designed for. The main types include:
Gravity Roller Conveyors: Use the force of gravity to move items down an incline. Ideal for lightweight packages and require manual assistance for movement on flat sections.
Powered Roller Conveyors: Equipped with motorized rollers to move items along the conveyor path. Suitable for a wide range of product sizes and weights, offering controlled speed and direction.
Flexible Roller Conveyors: Feature segments that can be extended, curved, and contracted, allowing for versatile layouts. They can be gravity-powered or motorized for increased flexibility in dynamic environments.
Accumulation Roller Conveyors: Allow products to accumulate along the conveyor path without contact, reducing product damage. They can be designed with sensors and controls to manage product flow efficiently.
Chain-Driven Roller Conveyors: Use chains attached to a series of rollers to move heavy loads. They are robust and ideal for heavy-duty applications requiring high load capacity and durability.
Each type of roller conveyor offers specific benefits, making them suitable for various industrial applications, from simple transportation tasks to complex material handling systems.
Last Updated on July 31, 2024 by Jordan Smith
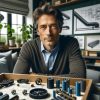
Jordan Smith, a seasoned professional with over 20 years of experience in the conveyor system industry. Jordan’s expertise lies in providing comprehensive solutions for conveyor rollers, belts, and accessories, catering to a wide range of industrial needs. From initial design and configuration to installation and meticulous troubleshooting, Jordan is adept at handling all aspects of conveyor system management. Whether you’re looking to upgrade your production line with efficient conveyor belts, require custom conveyor rollers for specific operations, or need expert advice on selecting the right conveyor accessories for your facility, Jordan is your reliable consultant. For any inquiries or assistance with conveyor system optimization, Jordan is available to share his wealth of knowledge and experience. Feel free to reach out at any time for professional guidance on all matters related to conveyor rollers, belts, and accessories.