Ground Compaction: Guide to High Energy Impact Rollers
High Energy Impact Rollers (HEIR) have revolutionized the field of ground compaction technology with their unmatched efficiency and effectiveness. Designed to deliver concentrated energy deep into the soil, these machines significantly enhance ground density and stability, addressing key challenges in engineering and construction projects. Unlike traditional rollers, high energy impact roller offer the unique ability to compact soil layers to greater depths, ensuring a strong foundation for infrastructure projects. Their role in contemporary construction is indispensable, providing a robust solution for creating firm and level surfaces. As demands for more resilient and enduring structures grow, the reliance on high energy impact rollers continues to rise, underscoring their importance in building the foundations of the future.
Mechanisms of High Energy Impact Roller
High Energy Impact Rollers (HEIR) are rooted in complex and ingenious engineering principles. To fully appreciate the efficiency of these machines, it’s important to delve into their integral mechanisms.
How High Energy Impact Roller Works
The high energy impact roller represents a paradigm shift in ground compaction technology, primarily through its reliance on a non-traditional design that maximizes the natural force of gravity. At the heart of this innovative machinery is the non-cylindrical, multisided drum, or module, which eschews the need for motorized energy, a common requirement in traditional compaction equipment. This distinctive design enables the roller to utilize gravity as its main driving force, setting it apart in both efficiency and effectiveness.
As the roller traverses the terrain, its design plays a crucial role in the rapid introduction of energy into the soil. Unlike conventional rollers that rely on vibration or direct pressure, the high energy impact roller employs the sheer mass and form of its drum to impart energy. As the drum rotates over the surface, each multisided segment momentarily rises before gravity pulls it back down to the earth. This action creates a high-impact force at the point of contact. This force is transferred directly to the ground at targeted intervals, ensuring that energy is distributed rapidly and uniformly across the compaction area. This method of operation is not only innovative but also significantly more effective in densifying the soil, as it allows for deeper compaction without the need for additional, energy-consuming mechanisms.
The coherent design and operating principle of the high energy impact roller thus represent a significant advancement in ground compaction methods. By leveraging gravity and a specially designed drum, it introduces energy to the ground at rates unachievable by traditional means, paving the way for more efficient, deeper, and reliable soil compaction.
Impact and Energy Transfer
The operation of a high energy impact roller is a study in the art of precision engineering and the science of energy conversion. The key process involves an innovative action as the roller navigates the terrain.
Turning and Falling Action
Each turn of the roller’s multisided drum is choreographed to maximize the impact. The corners of the drum, known as the major radius, are engineered to temporarily elevate the drum above the soil. Then, by gravity, the roller rotates around these high points, and the drum falls onto its flat side or minor radius. This sequence of lifting and dropping results in a significant impact as the drum strikes the soil with force.
This repeated impact process is the cornerstone of the high energy impact roller’s functionality. As the drum corners contact the ground, the potential energy accumulated due to their elevated position is poised for conversion. Then, in a moment’s transition, as the roller tips and falls, this energy is unleashed onto the soil as kinetic energy — energy produced by motion.
Energy Conversion Dynamics
The high energy impact roller operates on a sophisticated blend of both potential and kinetic energy principles. When the drum is at its peak on the major radius, it stores potential energy, much like a coiled spring that’s been drawn tight. As the roller moves forward and the drum rolls past the tipping point, the potential energy is released, and the drum descends rapidly.
This swift movement converts the potential energy into kinetic energy. It’s the kinetic energy that is then transferred into the soil at the moment of impact. This conversion isn’t just efficient; it’s also created solely by the machine’s motion and gravity, not requiring external power.
Thus, the high energy impact roller’s effectiveness in compaction is the direct result of careful energy management. Each turn of the drum represents a cyclical exchange from potential to kinetic energy, with gravity assisting in delivering a high-impact force to the ground, ensuring deep and effective soil compaction.
Depth of Influence
High energy impact rollers possess an uncommon advantage that sets them apart from other compaction equipment: they demonstrate a significant depth of influence in soil compaction.
Varying Compaction Depths
High energy impact rollers excel in their capacity to compact soils at various depths. The unique drum design and the force it imparts allow the roller to influence significantly deeper layers compared to traditional vibrating rollers. For example, in cohesive soils, such as clay and silt, a high energy impact roller can achieve compaction depths ranging from 700mm to as much as 2500mm.
Non-cohesive materials, such as sand and gravel, offer even deeper compaction potential. Here, the high energy impact roller can reach impressive impact depths of up to 3 to 4 meters. This proficiency in compacting both cohesive and non-cohesive soils at such significant depths sets a high energy impact roller apart from its conventional counterparts and establishes it as an invaluable player in the realm of soil stabilization projects.
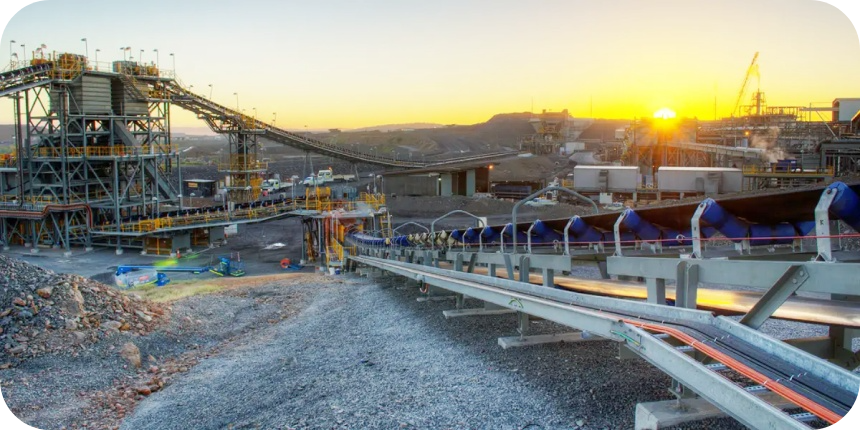
The Impact of Roller’s Shape and Size
The depth of impact a high energy impact roller has on soil compaction is intimately tied to the physical attributes of the drum — its shape and its size. A larger drum allows for a greater fall, which in turn provides a more substantial impact force. Similarly, the unique multisided shape of the drum allows for a more massive section of the roller to contact the ground, thereby increasing the depth of influence.
The drum’s shape further collaborates with the energy transfer principles to yield a powerful downwards thrust, which leads to deeper compaction. This fusion of size and shape, along with the energy transfer during the roller’s operation, allows the high energy impact roller to create a significant impact even at significant depth.
Through these principles, the high energy impact roller redefines the boundaries of soil compaction. It’s a testament to the critical role of innovative design and scientific principles in achieving superior soil compaction depths, largely outperforming traditional methods.
Comparison Criteria for High Energy Impact Roller
Defining and understanding the performance of a high energy impact roller calls for examining it in terms of energy generation and performance as well as its cost-effectiveness and efficiency.
Energy Generation and Performance
When selecting a high energy impact roller, one of the primary considerations is the amount of energy it can generate and how it performs under varying conditions.
Energy Ratings and Performance Efficiency
The energy rating often acts as a suitable benchmark for comparing models. This rating, usually quantified in kilojoules, indicates the amount of energy that a roller can deliver at the point of impact. Therefore, a high energy impact roller with a higher kilojoules rating indicates its superior capability to impart greater energy and, by extension, provide superior soil compaction. But energy generation is just one side of the comparison; assessing a high energy impact roller’s performance efficiency provides a more holistic understanding of its true capability. Factors such as energy transmission rate, soil type applicability, and compaction depth influence the overall performance efficiency.
Gravity and Rotational Velocity Impact
Two critical components that contribute significantly to the functionality and performance efficiency of a high energy impact roller are gravity and rotational velocity. The unique operation of a high energy impact roller does not rely on an engine or external sources of power. Instead, it harnesses gravity and link it with rotational velocity to generate impressive kinetic energy. The tactful combination of these two factors results in a powerful impact force with increased transmission efficiency, thus providing enhanced soil compaction levels.
Cost-Effectiveness and Efficiency
While assessing the value of a high energy impact roller, it is crucial to weigh its initial purchase and operation costs against the efficiency and savings it offers in the long term. The comparison is best illustrated in the form of a table below:
This comparison emphasizes that while the initial purchase cost of a high energy impact roller may be higher, its operational efficiency and reduced need for layer compaction significantly offset the initial investment. The roller’s ability to achieve comprehensive compaction with fewer passes saves considerable time and resources, translating into notable long-term cost savings and increased project efficiency when compared to traditional compaction methods.
Practical Applications of High Energy Impact Roller
The use of a high energy impact roller extends beyond conventional construction sites, marking its significance in various industries with diverse and challenging requirements. Below, we explore the myriad applications and the advantages it brings to problem sites.
Versatile Use Across Industries and Cases
Bulk Earthworks and Ground Improvement
A high energy impact roller plays a pivotal role in large-scale construction projects that encompass bulk earthworks. It is instrumental in improving the load-bearing capacity of soil, making it suitable for foundational support and overall ground stabilization. By delivering deep compaction, the high energy impact roller enhances soil density and shear strength, which are critical parameters in the sustainability of infrastructure.
Settlement and Sanitary Landfill Reclamation
When it comes to dealing with settlement issues or converting sanitary landfills into usable land, the high energy impact roller emerges as a key tool. Its intense compaction capability accelerates the settlement process, providing a quicker path to stable ground that can be repurposed effectively. Furthermore, it aids in the densification of landfills, which is necessary to reclaim the land for future development, ensuring that previously unusable spaces can be integrated into urban expansion efforts.
Advantages in Problem Sites
The high energy impact roller represents a game-changing tool when faced with difficult site conditions. The versatile machine brings a host of advantages, some of which are listed below:
- Overcoming Soil Quality Challenges: In sites with poor soil quality, a high energy impact roller can significantly increase ground stability by increasing soil density. This can reduce the need for expensive deep foundation techniques.
- Cost-Reduction in Foundation Treatment: Expensive conventional foundation treatments often make construction unfeasible in regions with challenging soil conditions. The use of a high energy impact roller can significantly cut down these costs by providing effective compaction that improves the ground strength.
- Case Studies Prove Efficiency: There are numerous cases across the globe where use of a high energy impact roller has led to substantial savings and efficient construction timelines. Whether dealing with soft clay layers or regions with other problematic soil types, the machine has proved inspiring results in areas that once seemed impervious to construction.
- Accelerated Construction Timeline: By circumventing the need for time-taking traditional solutions, the high energy impact roller expedites the project schedule and leads to faster completion, hitting multiple project goals simultaneously.
Conclusively, these points align to accentuate the cost-saving potential and superior efficiency of a high energy impact roller, making it an invaluable asset, especially when dealing with complex site conditions.
Purchasing Guide for High Energy Impact Roller
When in the market for a high energy impact roller, it’s essential to make an informed decision guided by a comprehensive understanding of what to look for, how to weigh the costs against the benefits, and which models are best suited to your needs.
Where to Find and How to Choose the Right High Energy Impact Roller for Sale
When seeking a high energy impact roller for sale, prospective buyers should begin their search with reputable construction equipment suppliers, specialty dealers, or directly from manufacturers known for their compaction equipment. It is also advisable to attend trade shows and industry expos, where the latest models are showcased.
Selecting the right high energy impact roller requires due consideration of several factors including:
- Project Scope: Evaluation of the project size and compaction requirements is vital to determine the appropriate model size and weight.
- Soil Conditions: The type of soil or material being compacted should influence the choice of compaction capacity and the kind of drum (smooth, padded, or sheepsfoot).
- Maneuverability: Considering the job site terrain and how the equipment will navigate is crucial. Ensure the roller is versatile enough for the project’s space constraints.
- After-Sales Support: Verify the availability of service and parts from the seller to ensure minimal downtime in case of maintenance or repairs.
Cost vs. Benefits Analysis of High Energy Impact Roller
The above cost and benefits analysis should aid in making an informed decision about investing in a high energy impact roller, giving you a clearer view of its long-term financial implications.
Recommendations for the Best High Energy Impact Roller in the Market
When it comes to procuring the best high energy impact roller, comprehensive research involving the examination of customer reviews and technical specifications is required. Evaluate the following:
- Performance Records: Look for rollers with a proven record of performance, reliability, and durability in the field.
- Customer Feedback: Scour through industry forums, online reviews, and testimonials for user experiences and ratings.
- Technical Specifications: Study the specifications of various rollers to ensure the machine meets all your operation needs.
- Industry Awards/Reputation: Acknowledgments from industry organizations or awards received can be a testament to the product’s excellence.
Make sure to collate information from various sources to ascertain the high energy impact roller that stands out in the market for being robust, efficient, and user-friendly while offering the best value for money.
High Energy Impact Roller Safety and Maintenance
The safety and maintenance of a high energy impact roller are paramount for the efficient and prolonged operation of this heavy machinery. Ensuring the well-being of operators and the durability of the equipment requires adherence to rigorous safety guidelines and maintenance schedules.
Avoiding High Energy Impact Injuries
The operation of a high energy impact roller, given its potential for high-energy impacts, necessitates stringent safety measures to prevent workplace accidents. Some key precautions and best practices include:
- Comprehensive Training: Operators must be fully trained in the use and potential hazards of the high energy impact roller. This training should cover operational techniques, emergency procedures, and correct safety gear usage.
- Use of Protective Gear: Operators and nearby workers must wear appropriate safety gear, including helmets, high-visibility vests, ear protection, and steel-toed boots, to mitigate the risk of injuries.
- Regular Safety Checks: Conducting pre-operation safety checks on the high energy impact roller can identify potential issues before they lead to accidents. Checks should focus on the machine’s physical condition, safety mechanisms, and any signs of wear or damage.
- Clear Communication: Establish and maintain clear lines of communication among all site workers. The use of flags, radios, and other signaling devices helps prevent accidents in noisy or visually obstructed environments.
Maintenance Tips
Proper maintenance is crucial in extending the lifespan and maintaining the efficiency of the high energy impact roller. By following these guidelines, operators can ensure consistent performance:
- Routine Inspections: Schedule regular inspections of the high energy impact roller to detect and address issues before they escalate. Focus on checking hydraulic systems, engines, and structural components for wear or damage.
- Lubrication: Regular lubrication of moving parts reduces friction, which can cause premature wear. Adhere to the manufacturer’s guidelines regarding lubrication intervals and recommended products.
- Cleaning: After each use, clean the high energy impact roller to remove dirt, debris, and any substances that might corrode metal surfaces or clog moving parts.
- Record Keeping: Maintain detailed logs of all maintenance activities, repairs, and inspections. These records can help identify recurring issues, guide future maintenance schedules, and ensure compliance with warranty requirements.
Adherence to these safety and maintenance practices not only safeguards the operators but also guarantees that the high energy impact roller remains in optimal condition, offering reliable service over its intended lifecycle.
Operational Guidelines for High Energy Impact Rollers
The use of high energy impact rollers in construction and compaction projects requires adherence to specific operational guidelines to ensure safety, efficiency, and project success. Understanding these guidelines is crucial for both novice and experienced operators to maximize the potential of their high energy impact roller while minimizing risks associated with heavy machinery operation.
Best Practices for Safety and Efficiency
When operating a high energy impact roller, incorporating best practices into daily operations is essential. Here are some of the top guidelines to follow:
- Prioritize Safety Training: Before operating the high energy impact roller, all personnel should undergo comprehensive safety training. This includes understanding the potential hazards, learning how to wear personal protective equipment (PPE) properly, and knowing the emergency stop procedures.
- Pre-Use Inspection: Conduct a thorough inspection of the high energy impact roller to ensure all parts are in working order, and there are no visible defects or damages. Pay special attention to the integrity of the roller drum, the hydraulic system, and safety devices.
- Operational Proficiency: Operators should be familiar with the high energy impact roller’s controls and features. This includes understanding how to efficiently transition between different speeds and compaction pressures according to the substrate they are working on.
- Job Site Assessment: Assess the job site for potential hazards such as overhead obstacles, underground utilities, and the overall ground conditions. Planning the roller’s path avoids unnecessary stops and starts, which can affect compaction quality and safety.
- Maintain Communication: Utilize communication tools and signals, especially in areas with high ambient noise, to maintain continuous coordination between the operator and spotters or ground crew. This ensures everyone is aware of the machine’s movements and can stay clear of its path.
Understanding the Operational Parameters
To effectively harness the capabilities of the high energy impact roller, operators must understand its operational parameters. These include:
- Adjusting Compaction Force: Knowing how to adjust the compaction force for different materials and depths is crucial. The appropriate force ensures optimal density without overcompaction or damage to the surface material.
- Speed and Efficiency: The operational speed of the high energy impact roller should match the project’s requirements. Faster speeds may be suitable for initial passes, but lower speeds often provide better compaction on subsequent passes.
- Understanding Limits: Each high energy impact roller has its operational limits, including maximum incline angles and compaction depths. Exceeding these limits can risk equipment failure or compromise project integrity.
- Environmental Considerations: Operating conditions such as temperature, moisture content of the material being compacted, and altitude can affect the high energy impact roller’s performance. Adjustments may be needed to accommodate for these factors.
Adhering to these operational guidelines ensures the high energy impact roller is used safely and efficiently, paving the way for successful completion of compaction projects while maintaining a safe working environment for all involved.
Choosing the Right High Energy Impact Roller
The selection of the appropriate high energy impact roller for your operations can notably improve job site productivity and work quality. Making that choice involves accounting for various factors and understanding the specifications of different high energy impact roller models.
Factors to Consider
When choosing a high energy impact roller, several factors should be taken into account to ensure it can meet your project’s specific needs. These considerations include:
- Project Requirements: Consider the scope and specifics of your project. Factors such as soil type, compaction depth requirement, and job site terrain will determine the kind of high energy impact roller you need.
- Machine Specifications: The high energy impact roller’s technical specifications like engine power, operating weight, and compaction energy should align with your job necessities.
- Operational Cost: Factor in fuel consumption, maintenance frequency, and the cost of replacement parts. A more efficient machine could lead to significant cost savings over time.
- Dealer Support: Local dealer support can be a crucial factor when considering the longevity of service and support for maintenance, repair, and replacement parts.
Overview of Different Models and their Specifications
High energy impact rollers come in a variety of models, each with its unique specifications tailored towards different operational needs. Here are some general categories:
- Light-Duty High Energy Impact Rollers: These are suitable for smaller projects or operations on delicate soil structures. They have lower operating weights and compaction force but can be used effectively in residential or light commercial projects.
- Medium-Duty High Energy Impact Rollers: A versatile choice, these high energy impact rollers have a balance of size, force, and adaptability. They are ideal for various soil structures and depths, particularly in road construction or larger commercial projects.
- Heavy-Duty High Energy Impact Rollers: Designed for massive operations, these machines deliver high compaction force and are equipped with powerful engines. They are ideal for large-scale projects on challenging terrains and heavy-duty compaction jobs.
Each of these models provides a unique combination of power, size, and compaction capabilities. Therefore, understanding your specific project requirements and how they align with these model categories can guide you towards choosing the right high energy impact roller.
Benefits of Using High Energy Impact Rollers
The use of high energy impact rollers in construction and geo-technical projects has significantly revolutionized soil compaction processes. This equipment offers a variety of benefits to users, which include the depth of influence on various soil types, increased efficiency in different soil conditions, and considerable advantages compared to traditional rollers.
Depth of Influence: Cohesive vs. Non-Cohesive Materials
One of the significant advantages of using a high energy impact roller is its capability to compact different materials with varying compaction depths effectively.
For Cohesive Materials such as clay soil, the high energy impact roller can reach deeper compaction levels than traditional rollers. This is due to its design, which generates a high energy impact that propagates through the soil layers, creating a more reliable and dense compaction.
In contrast, Non-Cohesive Materials such as sandy soils also benefit from this deep compaction ability. The vibratory force and weight of the high energy impact roller can rearrange soil particles, thereby increasing density and strength. The roller’s consistent high impact energy allows more effective compaction over greater depths for non-cohesive soils.
Efficiency in Various Soil Conditions
Another benefit of the high energy impact roller is its effectiveness across different soil conditions. Whether you’re dealing with wet, dry, or mixed soil conditions, the high energy impact roller can adjust its compaction force and work effectively. This efficiency translates to time-saving and cost-effectiveness as it reduces the need for additional machinery or changeovers.
Comparison with Traditional Rollers
When compared to traditional rollers, the high energy impact roller offers numerous advantages.
- Higher Impact Energy: A high energy impact roller generates more impact energy, facilitating deeper compaction and more homogenous soil structure, unlike traditional rollers which may struggle with compacting deeper layers.
- Speed and Efficiency: High energy impact rollers operate at higher speeds and cover large areas in less time than traditional rollers.
- Versatility: High energy impact rollers are designed to work across a wider range of soil types and conditions compared to traditional rollers.
- Cost-Effective: Their significant compaction power and efficiency often translate into fewer passes and less time on the job site, which leads to reduced fuel and operational costs.
The use of a high energy impact roller offers several benefits compared to traditional compaction methods and equipment. It combines depth, power, and versatility, making it a formidable tool in the field of soil compaction.
Request a sample of our High Energy Impact Rollers.
FAQs about High Energy Impact Roller
High energy impact roller compaction is a ground improvement technique that utilizes specialized heavy machinery called high energy impact rollers to densify soil and other materials. This type of roller creates a dynamic, high-energy impact load that is distributed across the roller’s width and penetrates deeply into the surface being compacted. Unlike traditional static or vibratory rollers, these machines rely on the rapid application and withdrawal of compaction force to rearrange and densify soil particles in both shallow and deep layers. The process is particularly effective for large project sites requiring significant compaction depth and is commonly used in road construction, airfield pavement, landfills, and dam construction. The method works on a variety of soil types, both cohesive and non-cohesive, and is efficient in achieving target densities and strength requirements.
High energy impact refers to the substantial kinetic energy applied to a material to alter its structure or composition. In the context of compaction, a high energy impact is typically delivered by machines designed to repetitively drop a heavy weight from a specific height onto the ground or by rolling a heavy drum equipped with protrusions over the surface. This force leads to the rearrangement of particles within the soil or material by breaking down aggregates, displacing air gaps, and pushing the particles closer together. The objective is to increase the density of the material, thereby enhancing its load-bearing capacity, stability, and overall performance as a foundation or building material. The high energy impact approach is characterized by its deep penetration and effectiveness over a broad area per pass, making it suitable for robust construction and engineering projects.
The primary difference between an impact roller and a vibratory roller lies in their mechanisms for compaction and their applications.
Impact Roller: An impact roller uses a high energy impact method, where it repeatedly drops a heavy mass onto the surface or uses a drum with projections to deliver discrete, powerful blows to the soil. The high impact force is ideal for deeper penetration and is usually employed for projects requiring substantial soil compaction at depth, like large-scale commercial land development or transport infrastructure projects.
Vibratory Roller: A vibratory roller employs vibrations generated by an eccentric shaft within the drum to compact the material. The rapid vibrations cause the particles in the soil to become reoriented in a denser configuration. Vibratory rollers are typically used for shallower compaction, such as finishing layers on roadways or small-scale projects. They work efficiently on granular soils where the vibration assists in settling the particles into a tighter configuration.
Each roller type is preferred for different project needs based on the nature of the soil, depth of compaction required, and final surface requirements.
The best roller for compaction depends entirely on the project requirements, including the type of soil or material being compacted, the desired depth and density, and the scale of the work. Here’s a brief guide:
Smooth Wheel (Static) Roller: Best for finishing layers on non-cohesive soils or asphalt compaction.
Sheepsfoot Roller: Ideal for compacting fine-grained soils like heavy clays and silty clays in embankments, road fills, and sub-grade layers.
Pneumatic-Tired Roller: Suitable for layers that require a kneading action and is often used for asphalt compaction or to seal the surface.
Vibratory Roller: Works well for a range of soil types, particularly granular soils requiring shallow to medium compaction depths.
High Energy Impact Roller: Perfect for large-scale projects where deep, uniform compaction of cohesive and non-cohesive soils is necessary.
Ultimately, selecting the most appropriate roller requires careful consideration by engineers and project managers to ensure the compaction work supports the structural needs of the project.
Last Updated on July 30, 2024 by Jordan Smith
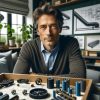
Jordan Smith, a seasoned professional with over 20 years of experience in the conveyor system industry. Jordan’s expertise lies in providing comprehensive solutions for conveyor rollers, belts, and accessories, catering to a wide range of industrial needs. From initial design and configuration to installation and meticulous troubleshooting, Jordan is adept at handling all aspects of conveyor system management. Whether you’re looking to upgrade your production line with efficient conveyor belts, require custom conveyor rollers for specific operations, or need expert advice on selecting the right conveyor accessories for your facility, Jordan is your reliable consultant. For any inquiries or assistance with conveyor system optimization, Jordan is available to share his wealth of knowledge and experience. Feel free to reach out at any time for professional guidance on all matters related to conveyor rollers, belts, and accessories.