Importance of High Temperature Rubber Conveyor Belt
High temperature rubber conveyor belts are crucial for industries that operate in extreme heat environments. These belts are designed to withstand high temperatures, ensuring the smooth and safe transport of materials. The high temperature rubber conveyor belt helps maintain efficiency and prevent damage to both the conveyor system and the materials being transported. Industries such as food processing, metalworking, and manufacturing rely heavily on these belts to handle high-heat applications. By using a high temperature rubber conveyor belt, businesses can reduce downtime, increase productivity, and ensure a safer working environment, making them an essential component in high-temperature operations.
About the High Temperature Rubber Conveyor Belt
High temperature rubber conveyor belt is designed to perform in the most demanding conditions where high temperatures and heavy loads are commonplace. These belts are essential in industries such as metal processing, cement production, and chemical manufacturing, where conveyor systems must withstand extreme heat without compromising on performance or safety. This article delves into the specifications, applications, and benefits of using high temperature rubber conveyor belt.
Heat Resistant Conveyor Belt Specifications
Heat resistant conveyor belts are manufactured with specific technical specifications to ensure they can handle high temperatures effectively. These specifications typically include the following:
Temperature Limits
High temperature rubber conveyor belts are engineered to operate at temperatures up to 400°C. Depending on the type of rubber and the belt’s construction, different grades are available to match the thermal requirements of various applications. For instance, standard heat resistant belts can withstand temperatures of up to 200°C, while more advanced versions can tolerate continuous exposure to temperatures as high as 400°C.
Thickness
The thickness of high temperature rubber conveyor belts is crucial for their performance and durability. These belts usually range from 5mm to 15mm in thickness, depending on the specific application and required durability. The multi-layer construction often includes a heat-resistant cover and a robust carcass that provides the necessary strength and flexibility.
Durability
Durability in high temperature rubber conveyor belts is achieved through a combination of advanced materials and manufacturing techniques. The rubber compounds used are formulated to resist thermal degradation, oxidation, and chemical attack, ensuring that the belts maintain their integrity and performance over extended periods. Reinforcement materials such as polyester, nylon, or steel cords are incorporated to enhance the tensile strength and impact resistance of the belts.
Ensuring Optimal Performance
To ensure high temperature rubber conveyor belts perform optimally under extreme conditions, several factors must be considered:
Material Selection
Selecting the right rubber compound is critical for high temperature applications. Different compounds offer varying levels of heat resistance, flexibility, and durability. For example, EPDM (Ethylene Propylene Diene Monomer) rubber is known for its excellent heat resistance, making it ideal for applications where temperatures frequently exceed 200°C. Similarly, silicone rubber is used in applications requiring higher thermal stability.
Proper Installation
Proper installation is essential to the performance and longevity of high temperature rubber conveyor belts. This includes ensuring the belt is aligned correctly, maintaining the right tension, and using appropriate fastening methods. Incorrect installation can lead to premature wear, reduced efficiency, and potential safety hazards.
Regular Maintenance
Regular maintenance is vital to keep high temperature rubber conveyor belts in optimal condition. Maintenance tasks include inspecting the belt for signs of wear or damage, ensuring the conveyor system is free from debris, and lubricating moving parts. Regular checks and timely repairs can significantly extend the life of the belt and prevent costly downtime.
Applications of High Temperature Rubber Conveyor Belts
High temperature rubber conveyor belts are used across various industries due to their ability to withstand extreme conditions. Some of the primary applications include:
Metal Processing
In metal processing industries, conveyor belts are exposed to molten metal and extreme heat. High temperature rubber conveyor belts are used to transport materials such as ore, metal scrap, and finished products through furnaces and other high-heat areas. These belts ensure smooth and efficient operation despite the harsh conditions.
Cement Production
Cement production involves handling materials at high temperatures, especially during the kiln process. High temperature rubber conveyor belts are employed to transport raw materials, clinker, and finished cement. Their heat-resistant properties prevent belt damage and ensure continuous operation.
Chemical Manufacturing
Chemical manufacturing processes often involve high temperatures and aggressive chemicals. High temperature rubber conveyor belts are resistant to both heat and chemical attack, making them suitable for transporting various chemical products and raw materials. Their durability and reliability help maintain production efficiency and safety.
Benefits of High Temperature Rubber Conveyor Belts
Using high temperature rubber conveyor belts offers several advantages, including:
Increased Safety
Safety is paramount in high-temperature environments. High temperature rubber conveyor belts reduce the risk of belt failure and subsequent accidents. Their robust construction and heat-resistant properties ensure they can handle the demands of extreme conditions without compromising safety.
Enhanced Durability
The durability of high temperature rubber conveyor belts means they can withstand prolonged exposure to high temperatures without degrading. This translates to longer belt life, reduced replacement frequency, and lower maintenance costs.
Improved Efficiency
High temperature rubber conveyor belts are designed to maintain their performance even under extreme conditions. This consistency ensures that production processes run smoothly, minimizing downtime and improving overall efficiency.
What is High Temperature Rubber Conveyor Belt
Materials Used in Heat Resistant Conveyor Belts
High temperature rubber conveyor belts are essential in industries where materials are transported under high heat conditions. These belts must withstand extreme temperatures while maintaining their structural integrity and performance. To achieve this, manufacturers utilize specific materials that offer exceptional heat resistance, durability, and flexibility. Let’s explore the various materials used in the construction of high temperature rubber conveyor belts, including silicone, Teflon (PTFE), fiberglass, and Kevlar, and understand why these materials are suitable for high-temperature applications.
Silicone
Silicone is a widely used material in the manufacturing of high temperature rubber conveyor belts. Known for its outstanding heat resistance, silicone can withstand temperatures ranging from -75°F to 500°F (-59°C to 260°C). This makes it ideal for environments where extreme temperature variations are common. Silicone belts also exhibit excellent flexibility, which helps in maintaining the belt’s performance over prolonged periods of usage. Additionally, silicone’s non-stick properties make it resistant to the adhesion of transported materials, ensuring smooth and efficient operation. Its resistance to chemicals and UV radiation further enhances its durability, making silicone a preferred choice for high temperature rubber conveyor belts.
Teflon (PTFE)
Teflon, or polytetrafluoroethylene (PTFE), is another material extensively used in the production of heat-resistant conveyor belts. PTFE is renowned for its ability to endure extremely high temperatures, up to 600°F (316°C), without losing its properties. This makes it suitable for applications involving intense heat. Teflon belts are known for their low friction coefficient, which ensures minimal wear and tear and reduces the energy required for belt operation. Furthermore, Teflon’s non-reactive nature makes it resistant to most chemicals, oils, and solvents, which can be beneficial in harsh industrial environments. Its smooth surface also prevents the accumulation of transported materials, maintaining cleanliness and operational efficiency.
Fiberglass
Fiberglass is often used as a reinforcement material in high temperature rubber conveyor belts due to its excellent thermal stability and strength. Fiberglass belts can withstand temperatures up to 1000°F (538°C), making them ideal for the most demanding heat applications. The material is lightweight yet strong, providing the necessary support and durability for heavy-duty operations. Fiberglass is also resistant to corrosion and chemical damage, which extends the lifespan of the conveyor belt. In addition to its thermal properties, fiberglass offers good dimensional stability, ensuring that the belt retains its shape and performance even under continuous exposure to high temperatures.
Kevlar
Kevlar, a synthetic fiber known for its exceptional strength and heat resistance, is another critical material used in high temperature rubber conveyor belts. Kevlar belts can endure temperatures up to 800°F (427°C) while maintaining their structural integrity. This material is five times stronger than steel on an equal weight basis, providing superior durability and resistance to abrasion. Kevlar’s lightweight nature does not compromise its ability to handle heavy loads, making it suitable for rigorous industrial applications. Moreover, Kevlar is inherently flame-resistant, adding an extra layer of safety in high-temperature environments. Its low thermal conductivity helps in minimizing heat transfer to other components, thereby protecting the entire conveyor system.
Applications and Benefits
The selection of materials such as silicone, Teflon (PTFE), fiberglass, and Kevlar in high temperature rubber conveyor belts offers numerous advantages across various industries. These materials ensure that the belts can operate efficiently in environments with extreme heat, reducing downtime and maintenance costs. Industries such as metal processing, glass manufacturing, food processing, and chemical production benefit from the reliability and longevity of these conveyor belts. The specific properties of each material—such as heat resistance, flexibility, strength, and chemical resistance—make them suitable for customized applications, ensuring optimal performance and safety.
The Key of High Temperature Rubber Conveyor Belt
High temperature rubber conveyor belts are essential in industries where extreme heat and demanding operational conditions are prevalent. These belts are specifically designed to handle high temperatures without compromising on their performance, durability, or safety. This article will explore the importance of conveyor belt temperature ratings and how they determine the suitability of a belt for specific applications.
Conveyor Belt Temperature Ratings
Conveyor belt temperature ratings are critical in selecting the right belt for high-temperature applications. These ratings indicate the maximum temperature that a conveyor belt can withstand without degrading or losing its functionality. Understanding these ratings helps in choosing a high temperature rubber conveyor belt that ensures safety, efficiency, and longevity in various industrial applications.
Importance of Temperature Ratings
The temperature rating of a high temperature rubber conveyor belt is a crucial factor in determining its suitability for different applications. Belts with appropriate temperature ratings prevent heat-induced damage, maintain structural integrity, and ensure continuous operation. Incorrect temperature ratings can lead to belt failure, operational downtime, and increased maintenance costs.
Types of Heat Resistant Belts and Their Temperature Ranges
Different types of heat resistant belts are available, each designed to withstand specific temperature ranges. Here are some examples:
- Standard Heat Resistant Belts: These belts are suitable for temperatures up to 200°C. They are commonly used in industries such as food processing, packaging, and light manufacturing where temperatures are elevated but not extreme.
- Medium Heat Resistant Belts: Designed for temperatures up to 300°C, these belts are used in more demanding environments like cement plants, steel mills, and foundries. They offer a balance between heat resistance and flexibility.
- High Heat Resistant Belts: These belts can handle temperatures up to 400°C and are used in the most extreme conditions, such as in metal processing and glass manufacturing. Their robust construction ensures they can endure prolonged exposure to intense heat.
Ensuring Optimal Performance with High Temperature Rubber Conveyor Belts
To ensure a high temperature rubber conveyor belt performs optimally under extreme conditions, several key factors must be considered:
Material Composition
The material composition of the high temperature rubber conveyor belt plays a vital role in its performance. Different rubber compounds provide varying levels of heat resistance. For example, EPDM (Ethylene Propylene Diene Monomer) rubber is known for its excellent heat resistance, making it ideal for applications with frequent exposure to temperatures above 200°C. Silicone rubber is another option for applications requiring even higher thermal stability.
Proper Installation and Alignment
Proper installation and alignment are crucial for the performance and longevity of high temperature rubber conveyor belts. Ensuring the belt is correctly aligned, maintaining the right tension, and using suitable fastening methods can prevent premature wear and operational issues. Incorrect installation can lead to belt misalignment, increased wear, and potential safety hazards.
Regular Maintenance and Inspection
Regular maintenance and inspection are essential to keep high temperature rubber conveyor belts in optimal condition. Maintenance tasks include checking for signs of wear or damage, ensuring the conveyor system is free from debris, and lubricating moving parts. Regular inspections and timely repairs can significantly extend the life of the belt and prevent costly downtime.
Applications of High Temperature Rubber Conveyor Belts
High temperature rubber conveyor belts are used in various industries due to their ability to withstand extreme conditions. Some primary applications include:
Metal Processing
In the metal processing industry, conveyor belts are exposed to molten metal and extreme heat. High temperature rubber conveyor belts are used to transport materials such as ore, metal scrap, and finished products through furnaces and other high-heat areas. These belts ensure smooth and efficient operation despite the harsh conditions.
Cement Production
Cement production involves handling materials at high temperatures, especially during the kiln process. High temperature rubber conveyor belts are employed to transport raw materials, clinker, and finished cement. Their heat-resistant properties prevent belt damage and ensure continuous operation.
Chemical Manufacturing
Chemical manufacturing processes often involve high temperatures and aggressive chemicals. High temperature rubber conveyor belts are resistant to both heat and chemical attack, making them suitable for transporting various chemical products and raw materials. Their durability and reliability help maintain production efficiency and safety.
The Types of the High Temperature Rubber Conveyor Belt
High temperature rubber conveyor belts are a critical component in industries that operate under extreme conditions. These belts are specifically designed to handle high temperatures without compromising on their performance, durability, or safety. This article will explore the applications of high temperature rubber conveyor belts, highlighting various industries and their specific needs.
Applications of High Temperature Rubber Conveyor Belts
High temperature rubber conveyor belts are indispensable in a wide range of industries where they must perform reliably under extreme heat and demanding conditions. Here, we highlight some of the key applications:
Food Processing
In the food processing industry, high temperature rubber conveyor belts are crucial for handling products that require heat treatment. These belts are used in baking, cooking, and drying processes where temperatures can soar. For instance, in baking ovens, conveyor belts must withstand constant exposure to high temperatures while maintaining food safety standards. The belts must also be resistant to oils, fats, and other food-related substances to ensure hygiene and prevent contamination.
Metalworking
The metalworking industry involves processes such as smelting, casting, and forging, all of which require handling materials at extremely high temperatures. High temperature rubber conveyor belts are used to transport molten metals, metal ores, and finished metal products. These belts must endure continuous exposure to high temperatures and abrasive materials without deteriorating. In addition, they need to be strong enough to handle the heavy loads typically associated with metalworking operations.
Manufacturing
Manufacturing processes often involve high temperatures, especially in sectors like automotive, aerospace, and electronics. High temperature rubber conveyor belts are used to move components through various stages of production, including heat treatment, painting, and curing. For example, in the automotive industry, conveyor belts transport parts through paint ovens and curing chambers where temperatures are high. The belts must resist heat, chemical exposure, and mechanical stress to ensure smooth and efficient operations.
Chemical Processing
Chemical processing plants handle a variety of chemicals, many of which are processed at high temperatures. High temperature rubber conveyor belts are essential in these environments, where they transport raw materials, intermediates, and finished chemical products. These belts must be resistant to both high temperatures and chemical exposure to prevent degradation and ensure safe operation. In addition, they need to maintain their structural integrity and flexibility to accommodate different processing stages.
Glass Manufacturing
In the glass manufacturing industry, conveyor belts are exposed to extremely high temperatures during the melting and forming processes. High temperature rubber conveyor belts are used to transport glass products through furnaces and cooling areas. These belts must withstand the intense heat of molten glass and the thermal shock of rapid cooling. Durability and heat resistance are critical to prevent belt failure and ensure continuous production.
Cement Production
Cement production involves high-temperature processes such as kiln operation, where raw materials are heated to form clinker. High temperature rubber conveyor belts are used to transport raw materials, clinker, and finished cement. These belts must resist the abrasive nature of the materials and the high temperatures within the kiln and cooling systems. Their durability ensures that they can operate efficiently without frequent maintenance or replacement.
Power Generation
In power generation plants, especially those using coal or biomass, high temperature rubber conveyor belts are used to transport fuel and ash. These belts must endure high temperatures and the abrasive nature of the materials being transported. Additionally, they need to be fire-resistant to prevent the risk of combustion. Their robust construction ensures reliable operation in the demanding environment of power plants.
Benefits of High Temperature Rubber Conveyor Belts
Using high temperature rubber conveyor belts offers several advantages, including:
Increased Safety
Safety is paramount in high-temperature environments. High temperature rubber conveyor belts reduce the risk of belt failure and subsequent accidents. Their robust construction and heat-resistant properties ensure they can handle the demands of extreme conditions without compromising safety.
Enhanced Durability
The durability of high temperature rubber conveyor belts means they can withstand prolonged exposure to high temperatures without degrading. This translates to longer belt life, reduced replacement frequency, and lower maintenance costs.
Improved Efficiency
High temperature rubber conveyor belts are designed to maintain their performance even under extreme conditions. This consistency ensures that production processes run smoothly, minimizing downtime and improving overall efficiency.
What about High Temperature Rubber Conveyor Belt
Fire Resistant Conveyor Belts
In industrial settings where high temperatures are a daily challenge, the risk of fire is a significant concern. High temperature rubber conveyor belts are designed not only to handle extreme heat but also to prevent fires and ensure safety. Fire resistant conveyor belts are a critical component in environments where the presence of combustible materials or high-temperature processes could lead to fire hazards. These specialized belts are engineered to resist ignition and minimize the spread of flames, thereby safeguarding both equipment and personnel.
Characteristics of Fire Resistant Conveyor Belts
Fire resistant conveyor belts are crafted from materials that possess inherent flame-retardant properties. These materials are selected based on their ability to withstand high temperatures and prevent the propagation of fire. The following characteristics define the fire resistant nature of these belts:
- Heat and Flame Resistance: The primary feature of fire resistant conveyor belts is their ability to resist high temperatures and flames. These belts are made from specially formulated rubber compounds that do not ignite easily and can endure temperatures well above the normal operating ranges. This ensures that the belt can function effectively in environments where high temperatures are prevalent.
- Low Smoke and Toxicity: In the event of a fire, the generation of smoke and toxic gases can pose significant risks to workers and equipment. Fire resistant conveyor belts are designed to produce minimal smoke and low levels of toxic gases when exposed to flames. This is crucial for maintaining visibility and reducing health hazards during emergencies.
- Durability and Strength: Despite their specialized fire-resistant properties, these conveyor belts do not compromise on durability and strength. They are constructed to withstand the mechanical stresses of industrial operations, including abrasion, impact, and heavy loads. This ensures that the belts maintain their integrity and performance over extended periods.
- Self-Extinguishing Properties: One of the most important characteristics of fire resistant conveyor belts is their self-extinguishing ability. This means that once the source of ignition is removed, the belt material will not continue to burn. This property helps in controlling fires quickly and preventing them from spreading to other areas.
- Compliance with Safety Standards: Fire resistant conveyor belts are manufactured to meet stringent safety standards and regulations. These standards ensure that the belts provide adequate protection against fire hazards and are suitable for use in environments where fire safety is paramount.
Benefits of Fire Resistant Conveyor Belts
The use of fire resistant conveyor belts offers several benefits that enhance safety and operational efficiency in high-temperature environments. These benefits include:
- Enhanced Safety: The foremost benefit of fire resistant conveyor belts is the enhanced safety they provide. By resisting ignition and minimizing the spread of flames, these belts protect workers and equipment from fire-related incidents. This is particularly crucial in industries such as mining, metal processing, and chemical manufacturing, where the risk of fire is high.
- Prevention of Downtime: Fires can cause significant downtime in industrial operations, leading to substantial financial losses. Fire resistant conveyor belts help in preventing fires, thereby reducing the risk of operational interruptions. This ensures continuous production and minimizes downtime, contributing to overall productivity.
- Protection of Assets: Industrial equipment and materials are valuable assets that need protection from fire damage. Fire resistant conveyor belts act as a barrier, preventing fires from spreading and causing damage to machinery, inventory, and infrastructure. This protection helps in preserving the value of assets and reducing repair and replacement costs.
- Compliance with Regulations: Many industries are required to comply with fire safety regulations and standards. The use of fire resistant conveyor belts ensures that companies meet these regulatory requirements, avoiding potential fines and legal issues. Compliance also demonstrates a commitment to workplace safety and corporate responsibility.
- Improved Worker Morale: Providing a safe working environment is essential for maintaining high levels of worker morale and productivity. Fire resistant conveyor belts contribute to a safer workplace, giving workers confidence that their safety is prioritized. This can lead to increased job satisfaction and better performance.
- Versatility and Adaptability: Fire resistant conveyor belts are versatile and can be adapted to various industrial applications. They are available in different configurations and sizes, making them suitable for a wide range of high-temperature environments. This adaptability ensures that industries can implement fire-resistant solutions tailored to their specific needs.
Applications of Fire Resistant Conveyor Belts
Fire resistant conveyor belts are used in a variety of industries where the risk of fire is a concern. Some common applications include:
- Mining: In mining operations, conveyor belts are used to transport materials such as coal, which can be highly flammable. Fire resistant belts are essential in preventing fires in underground mines and other high-risk areas.
- Metal Processing: The metal processing industry involves high-temperature processes such as smelting and forging. Fire resistant conveyor belts ensure safe material handling in these environments, reducing the risk of fire outbreaks.
- Chemical Manufacturing: Chemical plants often handle volatile and flammable substances. Fire resistant belts provide an added layer of safety by preventing fires and controlling the spread of flames in case of an incident.
- Power Generation: Thermal power plants use conveyor belts to transport coal and other fuels. Fire resistant belts are crucial in preventing fires and ensuring safe fuel handling in power generation facilities.
- Food Processing: In food processing plants, high temperatures are used for cooking and baking. Fire resistant conveyor belts help in maintaining safety standards by preventing fires in these heat-intensive processes.
- Waste Management: Waste management facilities handle a variety of materials, some of which can be flammable. Fire resistant belts ensure safe transportation and processing of waste materials, minimizing the risk of fire.
High Temperature Rubber Conveyor Belt
Key Features of Heat Resistant Rubber Conveyor Belts
High temperature rubber conveyor belt is engineered to withstand the extreme conditions found in various industrial applications. These belts are vital for transporting materials in high-temperature environments, ensuring smooth and efficient operations without compromising safety or performance. The key features that make these belts effective include high thermal resistance, durability, and resistance to wear and tear. Understanding these features helps in appreciating how high temperature rubber conveyor belts perform exceptionally well in challenging conditions.
High Thermal Resistance
The primary feature of high temperature rubber conveyor belts is their exceptional thermal resistance. These belts are constructed from specially formulated rubber compounds that can endure continuous exposure to high temperatures without degrading. The ability to resist temperatures ranging from 100°C to 400°C makes these belts suitable for various industrial applications, such as metal processing, glass manufacturing, and chemical production.
Thermal resistance is achieved through the use of heat-resistant materials such as silicone, Teflon (PTFE), and fiberglass. These materials have unique properties that allow them to maintain structural integrity and performance under extreme heat. For instance, silicone belts can withstand temperatures up to 260°C, while Teflon belts can handle temperatures as high as 316°C. Fiberglass reinforcement further enhances the thermal stability of these belts, making them capable of operating in the harshest environments.
The high thermal resistance of these belts ensures that they do not soften, melt, or become brittle when exposed to elevated temperatures. This reliability is crucial for maintaining consistent performance and preventing operational disruptions caused by belt failure.
Durability
Durability is another critical feature of high temperature rubber conveyor belts. These belts are designed to withstand the rigors of heavy-duty industrial operations, providing long-lasting service life even in demanding conditions. The durability of these belts is a result of their robust construction and the use of high-quality materials that resist physical damage.
High temperature rubber conveyor belts are reinforced with layers of synthetic fabrics, such as polyester, nylon, and Kevlar, which provide additional strength and stability. These fabrics enhance the belt’s ability to handle heavy loads and resist stretching, tearing, and puncturing. Kevlar, in particular, is known for its superior tensile strength and resistance to abrasion, making it an ideal reinforcement material for high-temperature applications.
The durable construction of these belts ensures that they can withstand mechanical stresses, such as impact and abrasion, which are common in industrial settings. This resistance to physical damage reduces the frequency of belt replacements and maintenance, leading to cost savings and improved operational efficiency.
Resistance to Wear and Tear
Wear and tear are inevitable in industrial environments, but high temperature rubber conveyor belts are designed to resist these effects effectively. The wear resistance of these belts is attributed to the use of abrasion-resistant rubber compounds that protect the belt surface from damage caused by friction and contact with transported materials.
In addition to abrasion resistance, these belts exhibit excellent resistance to chemical exposure. In industries where chemicals, oils, and solvents are present, high temperature rubber conveyor belts are formulated to resist degradation from these substances. This chemical resistance extends the lifespan of the belts and ensures consistent performance in environments where chemical exposure is a concern.
The resistance to wear and tear also includes the belts’ ability to withstand UV radiation and ozone exposure. UV and ozone can cause rubber materials to crack and degrade over time, but high temperature rubber conveyor belts are formulated with additives that protect against these environmental factors. This protection ensures that the belts remain flexible and functional, even when exposed to outdoor or high-ozone environments.
Contribution to Performance in High-Temperature Conditions
The key features of high thermal resistance, durability, and resistance to wear and tear collectively contribute to the exceptional performance of high temperature rubber conveyor belts in high-temperature conditions. These features ensure that the belts can operate reliably and efficiently, even under extreme heat and challenging industrial environments.
- Consistent Performance: The high thermal resistance of these belts ensures that they maintain their physical properties and performance under elevated temperatures. This consistency is crucial for preventing operational disruptions and ensuring smooth material transport.
- Extended Service Life: The durability and resistance to wear and tear of these belts result in a longer service life. This reduces the need for frequent replacements and maintenance, leading to cost savings and improved operational efficiency.
- Safety and Reliability: High temperature rubber conveyor belts are designed to resist the adverse effects of heat, chemicals, and mechanical stresses. This reliability enhances safety by preventing belt failures that could lead to accidents or production downtime.
- Versatility: These belts can be customized to meet specific requirements of different industrial applications. The availability of various materials and reinforcement options allows for tailored solutions that address the unique challenges of each application.
- Cost-Effectiveness: The extended service life and reduced maintenance requirements of high temperature rubber conveyor belts make them a cost-effective choice for industries that operate in high-temperature environments. The initial investment in these belts is offset by the long-term savings in maintenance and replacement costs.
FAQS about High Temperature Rubber Conveyor Belt
High temperature conveyor belts are typically made from materials that can withstand extreme heat without degrading. Common materials include silicone, Teflon (PTFE), fiberglass, and Kevlar. Silicone and Teflon are known for their excellent heat resistance and durability. Fiberglass belts are often coated with Teflon to enhance their heat-resistant properties. Kevlar belts offer exceptional strength and can endure high temperatures while maintaining their structural integrity. These materials are chosen because they do not melt, burn, or deform under high temperatures, making them ideal for industrial processes involving heat.
The temperature range of a conveyor belt varies depending on the material used in its construction. Standard conveyor belts can typically handle temperatures from -20°C to 80°C (-4°F to 176°F). However, specialized high-temperature conveyor belts are designed to operate in much higher temperature environments. Heat-resistant conveyor belts can endure temperatures up to 260°C (500°F), while some extreme high-temperature belts can withstand temperatures as high as 400°C (752°F). The exact temperature range will depend on the belt’s material composition and the specific application requirements.
For high-temperature applications, belts made from materials like silicone, Teflon (PTFE), fiberglass, and Kevlar are commonly used. Silicone belts are flexible and can handle temperatures up to 200°C (392°F). Teflon belts are non-stick and can withstand temperatures up to 260°C (500°F). Fiberglass belts, often coated with Teflon, offer excellent heat resistance and durability. Kevlar belts are known for their high strength and ability to endure temperatures up to 400°C (752°F). These belts are used in industries such as food processing, packaging, and manufacturing, where high temperatures are a part of the process.
A heat resistant conveyor belt is a type of belt specifically designed to withstand high temperatures. These belts are made from materials that do not degrade, melt, or burn when exposed to high heat. They are typically used in industries where the conveyor belt must transport materials through high-temperature environments, such as in baking, curing, or drying processes. Heat resistant conveyor belts ensure that the conveyor system operates efficiently and safely, even under extreme temperature conditions. They are available in various grades and specifications to suit different industrial applications and temperature ranges.
Last Updated on December 5, 2024 by Jordan Smith
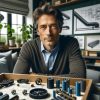
Jordan Smith, a seasoned professional with over 20 years of experience in the conveyor system industry. Jordan’s expertise lies in providing comprehensive solutions for conveyor rollers, belts, and accessories, catering to a wide range of industrial needs. From initial design and configuration to installation and meticulous troubleshooting, Jordan is adept at handling all aspects of conveyor system management. Whether you’re looking to upgrade your production line with efficient conveyor belts, require custom conveyor rollers for specific operations, or need expert advice on selecting the right conveyor accessories for your facility, Jordan is your reliable consultant. For any inquiries or assistance with conveyor system optimization, Jordan is available to share his wealth of knowledge and experience. Feel free to reach out at any time for professional guidance on all matters related to conveyor rollers, belts, and accessories.