Industrial Applications of Hot Conveyor Belt Systems
Timely replacement of a hot conveyor belt is crucial for maintaining operational efficiency in high-temperature environments. Hot conveyor belts are essential in industries such as foundries, glassworks, and metal processing. Regular inspection and timely replacement help prevent unexpected downtimes and ensure safety. Common signs indicating the need for replacement include visible wear and tear, cracking, hardening of the belt material, and reduced flexibility. Monitoring these signs ensures that the hot conveyor belt functions effectively, minimizing the risk of operational disruptions and maintaining consistent production quality.
Hot Conveyor Belt: Key Features of Heat Resistant Conveyor Belt Specification
When it comes to high-temperature industrial applications, the selection of an appropriate conveyor belt is critical. Heat resistant conveyor belts are specially designed to withstand high temperatures without compromising their structural integrity or performance. In this section, we will delve into the essential specifications of heat resistant conveyor belts and explain how these features ensure durability and efficiency in demanding environments.
Temperature Resistance
One of the most crucial specifications of heat resistant conveyor belts is their ability to withstand elevated temperatures. Typically, these belts are rated for continuous operation at temperatures ranging from 200°C to 400°C. For applications involving intermittent or peak temperatures, some belts can endure up to 600°C for short periods. This high-temperature resistance is achieved through the use of specially formulated rubber compounds and reinforcements that maintain their properties under thermal stress.
Material Composition
The material composition of heat resistant conveyor belts is fundamental to their performance. These belts are often made from specially engineered rubber compounds that include high-temperature resistant additives. Common materials used include:
- EPDM (Ethylene Propylene Diene Monomer): Known for its excellent heat, ozone, and weather resistance, making it ideal for high-temperature applications.
- SBR (Styrene-Butadiene Rubber): Provides good abrasion resistance and heat stability.
- PTFE (Polytetrafluoroethylene): Offers exceptional heat resistance and chemical inertness, suitable for extreme temperature conditions.
These materials are chosen based on their ability to resist thermal degradation, maintain flexibility, and provide sufficient strength to handle the loads and stresses encountered in industrial operations.
Reinforcement Layers
Heat resistant conveyor belts are reinforced with layers of materials such as polyester, nylon, or aramid fibers. These reinforcement layers enhance the belt’s tensile strength and dimensional stability, ensuring that the belt can handle heavy loads without stretching or breaking. The number of reinforcement layers can vary depending on the application, with multi-ply belts offering superior strength and durability.
Abrasion and Wear Resistance
In high-temperature applications, conveyor belts are often exposed to abrasive materials and harsh conditions. Therefore, abrasion and wear resistance are critical specifications. Heat resistant conveyor belts are designed with robust covers that can withstand abrasive materials, reducing the rate of wear and extending the belt’s lifespan. This feature is particularly important in industries such as mining, cement, and steel production, where belts are subjected to constant wear and tear.
Flexibility and Elongation
Maintaining flexibility at high temperatures is essential for the smooth operation of conveyor belts. Heat resistant belts are engineered to retain their flexibility and minimize elongation under thermal stress. This property ensures that the belts can navigate through various conveyor system configurations, including curves and inclines, without experiencing significant deformation or loss of performance.
Fire Resistance
In addition to heat resistance, fire resistance is a crucial specification for conveyor belts used in environments where there is a risk of fire. Fire-resistant conveyor belts are designed to prevent the spread of flames and withstand exposure to fire. These belts are tested and certified according to international fire safety standards, providing an added layer of safety for industrial operations.
Chemical Resistance
Heat resistant conveyor belts are often exposed to chemicals and oils that can degrade standard rubber belts. Therefore, chemical resistance is an important specification. These belts are formulated to resist a wide range of chemicals, ensuring that they maintain their integrity and performance even in chemically harsh environments. This feature is particularly beneficial in industries such as chemical processing, food processing, and pharmaceuticals.
Surface Finish
The surface finish of heat resistant conveyor belts can also vary based on the application requirements. Some belts have a smooth surface finish to facilitate the easy movement of materials, while others have a textured or patterned surface to provide additional grip and reduce slippage. The choice of surface finish depends on the type of materials being conveyed and the specific needs of the operation.
Heat resistant conveyor belts are designed with a range of specifications that ensure their durability and performance in high-temperature applications. By understanding these key features, businesses can select the right belt for their needs, ensuring efficient and reliable material handling in demanding environments.
Hot Conveyor Belt: Selecting the Right High Temperature Conveyor Belt
Choosing the right high temperature conveyor belt for specific industrial applications is a crucial decision that impacts the efficiency, safety, and longevity of the material handling system. Several factors must be considered to ensure that the selected belt meets the operational requirements and withstands the challenging conditions of high-temperature environments. In this section, we will provide guidance on selecting the appropriate high temperature conveyor belt, discussing essential factors such as temperature range, material composition, and load capacity.
Temperature Range
The first and foremost consideration when selecting a high temperature conveyor belt is the temperature range of the application. It is essential to choose a belt that can handle the maximum operating temperature of the environment. Different belts are rated for various temperature ranges, and selecting a belt that matches the specific thermal conditions of the application ensures optimal performance and longevity. For instance:
- Standard Heat Resistant Belts: Suitable for temperatures up to 200°C.
- High Heat Resistant Belts: Designed for temperatures ranging from 200°C to 400°C.
- Ultra High Heat Resistant Belts: Capable of withstanding temperatures above 400°C.
Understanding the temperature requirements of the application helps in selecting a belt that will not degrade or fail under thermal stress.
Material Composition
The material composition of the conveyor belt is another critical factor to consider. As discussed earlier, heat resistant belts are made from specialized rubber compounds and reinforcements. The choice of material depends on the specific needs of the application, such as resistance to chemicals, oils, and abrasion. For example:
- EPDM Belts: Ideal for applications requiring excellent heat and weather resistance.
- SBR Belts: Suitable for general high-temperature applications with good abrasion resistance.
- PTFE Belts: Best for extreme temperature conditions and environments with exposure to chemicals.
Selecting the right material ensures that the belt can handle the operational demands and provides long-lasting performance.
Load Capacity
The load capacity of the conveyor belt is a crucial consideration, especially in industrial settings where heavy materials are transported. The belt must have sufficient tensile strength to handle the weight of the materials without stretching or breaking. Factors such as the number of reinforcement layers, the type of fabric used, and the overall construction of the belt contribute to its load-bearing capacity. It is essential to choose a belt that can comfortably handle the maximum load of the application to prevent premature failure and ensure efficient operation.
Application Environment
The specific environment in which the conveyor belt will operate also influences the selection process. Factors such as the presence of abrasive materials, exposure to chemicals, and the risk of fire must be taken into account. For example:
- Abrasive Environments: Require belts with high abrasion resistance to minimize wear and extend the belt’s lifespan.
- Chemical Exposure: Needs belts with excellent chemical resistance to prevent degradation and maintain performance.
- Fire Risk: Demands fire-resistant belts to enhance safety and comply with fire safety regulations.
Considering the environmental conditions ensures that the selected belt can withstand the challenges and deliver reliable performance.
Belt Configuration
The configuration of the conveyor system also plays a role in selecting the right belt. Factors such as the belt’s width, length, and thickness must be compatible with the conveyor system’s design. Additionally, the belt’s surface finish should match the material handling requirements. For instance, smooth surface belts are ideal for conveying fine materials, while textured or patterned surface belts provide better grip for transporting larger or bulkier items.
Maintenance Requirements
Maintenance is an essential aspect of conveyor belt operation, and selecting a belt with manageable maintenance requirements can save time and costs. Heat resistant conveyor belts that are easy to clean, inspect, and repair contribute to the overall efficiency of the material handling system. Considering the maintenance needs during the selection process ensures that the belt can be easily maintained, reducing downtime and extending its lifespan.
Cost-Effectiveness
While it is important to select a belt that meets all operational requirements, cost considerations also play a role in the decision-making process. It is essential to balance the initial investment with the long-term benefits of the belt. High-quality heat resistant conveyor belts may have a higher upfront cost but offer superior performance, durability, and reduced maintenance costs, making them a cost-effective choice in the long run.
Manufacturer Reputation
Finally, choosing a conveyor belt from a reputable manufacturer ensures that you receive a high-quality product backed by technical support and warranty. Established manufacturers have a track record of producing reliable and durable conveyor belts, providing peace of mind and confidence in the product’s performance.
Selecting the right high temperature conveyor belt involves careful consideration of various factors, including temperature range, material composition, load capacity, application environment, belt configuration, maintenance requirements, cost-effectiveness, and manufacturer reputation. By evaluating these factors, businesses can make informed decisions that ensure efficient and reliable material handling in high-temperature applications.
Hot Conveyor Belt: Advantages of Heat Resistant Conveyor Belt Material
Heat resistant conveyor belts are engineered to perform under high-temperature conditions, and the materials used in their construction play a vital role in their effectiveness. In this section, we will outline the benefits of using heat resistant materials in conveyor belts and discuss the common materials employed in their manufacture and their properties.
Enhanced Durability
One of the primary advantages of heat resistant conveyor belt materials is their enhanced durability. These materials are specifically formulated to withstand the thermal stresses associated with high-temperature environments. Unlike standard conveyor belts, which may degrade, crack, or lose their structural integrity when exposed to heat, heat resistant belts maintain their properties, ensuring long-term performance. This durability translates to reduced downtime, fewer replacements, and lower maintenance costs, making them a cost-effective solution for industries operating in high-temperature conditions.
Superior Heat Resistance
Heat resistant materials are designed to endure high temperatures without compromising their performance. This superior heat resistance is achieved through the use of advanced rubber compounds and additives that prevent thermal degradation. For instance, EPDM (Ethylene Propylene Diene Monomer) and PTFE (Polytetrafluoroethylene) are commonly used materials
known for their excellent heat resistance. EPDM can handle temperatures up to 200°C, while PTFE can withstand temperatures exceeding 260°C. This heat resistance ensures that the conveyor belt can operate continuously in high-temperature environments without losing its effectiveness.
Improved Safety
Safety is a critical concern in industrial settings, and heat resistant conveyor belts contribute to a safer working environment. These belts are designed to reduce the risk of fire and other heat-related hazards. For example, fire-resistant conveyor belts are manufactured using materials that can prevent the spread of flames, providing an added layer of protection. Additionally, the use of heat resistant materials minimizes the risk of belt failure due to thermal stress, reducing the likelihood of accidents and ensuring safe operation.
Chemical Resistance
In many industrial applications, conveyor belts are exposed to chemicals and oils that can degrade standard rubber belts. Heat resistant materials, such as PTFE, offer excellent chemical resistance, ensuring that the belt maintains its integrity and performance even in chemically harsh environments. This chemical resistance is particularly beneficial in industries such as chemical processing, food processing, and pharmaceuticals, where exposure to various substances is common.
Flexibility and Performance
Maintaining flexibility under high temperatures is essential for the smooth operation of conveyor belts. Heat resistant materials are engineered to retain their flexibility, ensuring that the belts can navigate through various conveyor system configurations without experiencing significant deformation. This flexibility is crucial for maintaining consistent performance, reducing the risk of material spillage, and ensuring efficient material handling.
Resistance to Abrasion and Wear
Heat resistant conveyor belts are often exposed to abrasive materials and harsh conditions, making abrasion and wear resistance critical properties. Materials like SBR (Styrene-Butadiene Rubber) provide good abrasion resistance, ensuring that the belts can withstand constant wear and tear. This resistance to abrasion extends the lifespan of the belt, reducing the frequency of replacements and minimizing downtime.
Versatility
The versatility of heat resistant materials allows them to be used in a wide range of industrial applications. Whether it’s for high-temperature ovens, furnaces, or chemical processing plants, these materials can be tailored to meet the specific requirements of different environments. The availability of various material options, such as EPDM, SBR, and PTFE, provides businesses with the flexibility to choose the best material for their specific needs, ensuring optimal performance and efficiency.
Energy Efficiency
Using heat resistant conveyor belts can also contribute to energy efficiency. These belts are designed to operate efficiently under high temperatures, reducing the amount of energy required for material handling. Additionally, the reduced need for frequent replacements and maintenance results in lower energy consumption associated with production downtime and repairs. This energy efficiency translates to cost savings and a reduced environmental impact.
Cost-Effectiveness
While the initial cost of heat resistant conveyor belts may be higher than standard belts, their long-term benefits make them a cost-effective investment. The enhanced durability, reduced maintenance requirements, improved safety, and energy efficiency of heat resistant materials contribute to lower overall operational costs. Businesses can achieve significant savings by investing in high-quality heat resistant conveyor belts that deliver reliable and efficient performance over an extended period.
Common Heat Resistant Materials
Several materials are commonly used in the manufacture of heat resistant conveyor belts, each offering unique properties and benefits:
- EPDM (Ethylene Propylene Diene Monomer): Known for its excellent heat, ozone, and weather resistance, EPDM is ideal for applications requiring long-term exposure to high temperatures.
- SBR (Styrene-Butadiene Rubber): Provides good abrasion resistance and heat stability, making it suitable for general high-temperature applications.
- PTFE (Polytetrafluoroethylene): Offers exceptional heat resistance and chemical inertness, making it suitable for extreme temperature conditions and chemically harsh environments.
- Silicone Rubber: Known for its excellent thermal stability and flexibility, silicone rubber is used in applications requiring resistance to both high temperatures and low temperatures.
The advantages of using heat resistant materials in conveyor belts are numerous. Enhanced durability, superior heat resistance, improved safety, chemical resistance, flexibility, and performance are just a few of the benefits that these materials offer. By understanding the properties and advantages of common heat resistant materials, businesses can select the right conveyor belt for their specific high-temperature applications, ensuring efficient and reliable material handling.
Heat Resistant Belt Applications
Heat resistant conveyor belts, such as the hot conveyor belt, are integral to numerous industrial applications where high temperatures are a constant challenge. These belts are designed to withstand extreme heat, ensuring uninterrupted and efficient operation in harsh conditions. Below, we explore various industrial applications that necessitate the use of heat resistant belts and provide examples of industries that significantly benefit from these specialized conveyor belts.
Industrial Furnaces and Ovens
In industries where materials are processed at high temperatures, such as in industrial furnaces and ovens, heat resistant conveyor belts are essential. These belts transport materials through various heating stages, ensuring smooth and continuous production. Industries such as metal processing, ceramics, and glass manufacturing heavily rely on hot conveyor belts to withstand the high temperatures involved in melting, sintering, and annealing processes. For example, in glass manufacturing, conveyor belts must endure temperatures exceeding 600°C to facilitate the seamless movement of molten glass through different stages of production.
Cement and Asphalt Production
The cement and asphalt production industries operate under extremely high temperatures, making the use of heat resistant belts crucial. In cement manufacturing, raw materials are heated in kilns at temperatures around 1450°C. Hot conveyor belts are used to transport these materials through the kiln and subsequent cooling stages. Similarly, in asphalt production, materials are heated to over 150°C, requiring belts that can maintain their structural integrity and performance in such conditions. Heat resistant belts ensure that the production process remains efficient and that the belts themselves have a prolonged lifespan despite the harsh operating environment.
Foundries and Steel Mills
Foundries and steel mills are another example of industries that benefit from heat resistant conveyor belts. These facilities handle molten metals and other high-temperature processes, necessitating belts that can endure the intense heat. Hot conveyor belts are used to transport materials such as scrap metal, molten steel, and castings through various stages of production, including furnaces, casting areas, and cooling zones. The durability and heat resistance of these belts are critical in preventing downtime and maintaining efficient production workflows.
Chemical Processing
The chemical processing industry often involves high-temperature reactions and material handling, making heat resistant conveyor belts indispensable. These belts are used to transport chemicals and materials that are subjected to heating processes, ensuring safe and efficient handling. For instance, in the production of chemicals like sulfuric acid or phosphoric acid, materials are heated to high temperatures, requiring belts that can resist thermal degradation and maintain their performance under such conditions. Heat resistant belts ensure the integrity of the chemical processing line and enhance overall operational safety.
Food Processing
In the food processing industry, heat resistant conveyor belts are used in applications where materials are exposed to high temperatures, such as baking, frying, and roasting. These belts ensure the safe and efficient movement of food products through ovens, fryers, and other heating equipment. For example, in bakeries, conveyor belts are used to transport dough and baked goods through high-temperature ovens, maintaining consistent baking quality. The use of heat resistant belts in food processing not only enhances efficiency but also ensures compliance with food safety standards.
Pulp and Paper Mills
Pulp and paper mills involve processes where materials are subjected to high temperatures, such as drying and curing. Heat resistant conveyor belts are used to transport pulp, paper, and other materials through drying machines and curing ovens. These belts ensure the efficient handling of materials, preventing bottlenecks and enhancing production throughput. The durability and heat resistance of the belts are crucial in maintaining the smooth operation of the mill and ensuring the quality of the final product.
Automotive Manufacturing
In the automotive manufacturing industry, heat resistant conveyor belts are used in processes such as paint drying, heat treatment, and curing. These belts transport automotive parts through high-temperature ovens and heat treatment areas, ensuring consistent quality and performance. For example, in paint drying applications, conveyor belts must withstand temperatures of up to 200°C to facilitate the drying and curing of automotive paints. Heat resistant belts ensure that the manufacturing process remains efficient and that the parts are handled safely and effectively.
Textile Industry
The textile industry also benefits from the use of heat resistant conveyor belts, particularly in processes such as dyeing, printing, and finishing. These belts transport textiles through high-temperature dyeing and printing machines, ensuring consistent color application and finishing quality. For instance, in the dyeing process, fabrics are exposed to temperatures exceeding 100°C, requiring belts that can maintain their integrity and performance. Heat resistant belts enhance the efficiency of textile production and ensure the quality of the finished products.
Heat resistant conveyor belts, such as the hot conveyor belt, play a vital role in various industrial applications where high temperatures are a constant challenge. Industries such as metal processing, cement production, chemical processing, food processing, pulp and paper mills, automotive manufacturing, and the textile industry significantly benefit from these specialized belts. By understanding the unique requirements of each application, businesses can select the appropriate heat resistant conveyor belt to ensure efficient, safe, and reliable material handling in high-temperature environments.
Hot Conveyor Belt: PTFE Conveyor Belt Benefits
PTFE (Polytetrafluoroethylene) conveyor belts are renowned for their exceptional performance in high-temperature settings. These belts offer unique advantages that make them an ideal choice for industries requiring reliable and efficient material handling under extreme heat conditions. In this section, we highlight the benefits of PTFE conveyor belts in high-temperature applications and discuss the properties of PTFE that contribute to their superiority.
Exceptional Heat Resistance
One of the most significant advantages of PTFE conveyor belts is their exceptional heat resistance. PTFE can withstand continuous operating temperatures up to 260°C and intermittent temperatures up to 315°C. This makes PTFE belts ideal for applications involving prolonged exposure to high temperatures, such as industrial ovens, furnaces, and heat treatment processes. The ability to maintain structural integrity and performance under extreme heat ensures that PTFE conveyor belts deliver reliable and efficient operation in demanding environments.
Non-Stick Surface
PTFE conveyor belts have a non-stick surface that offers several benefits in material handling applications. This non-stick property prevents materials from adhering to the belt, reducing the risk of material buildup and contamination. In industries such as food processing and chemical manufacturing, where cleanliness and hygiene are paramount, PTFE belts ensure that materials move smoothly without sticking to the surface. This non-stick feature also simplifies cleaning and maintenance, enhancing overall operational efficiency.
Chemical Resistance
PTFE is chemically inert and resistant to a wide range of chemicals, making PTFE conveyor belts suitable for applications involving exposure to corrosive substances. These belts can withstand contact with acids, bases, solvents, and other harsh chemicals without degrading or losing their performance. This chemical resistance is particularly beneficial in industries such as chemical processing, pharmaceuticals, and food processing, where conveyor belts are often exposed to various chemicals during production. PTFE belts ensure safe and efficient material handling in chemically harsh environments.
Low Friction
PTFE conveyor belts exhibit low friction, which reduces wear and tear on both the belt and the materials being conveyed. This low friction property minimizes the energy required to move materials, contributing to energy efficiency and cost savings. In addition, the reduced friction reduces the risk of belt slippage and ensures smooth and consistent material flow. This feature is particularly advantageous in high-speed conveyor systems, where maintaining consistent movement is critical to operational efficiency.
High Tensile Strength
Despite their flexibility and low friction, PTFE conveyor belts have high tensile strength, making them suitable for handling heavy loads and high-stress applications. The high tensile strength ensures that the belts can endure the mechanical stresses associated with material handling without stretching or breaking. This durability is essential in industries such as automotive manufacturing, metal processing, and heavy-duty industrial applications, where conveyor belts are subjected to significant loads and forces.
Versatility
PTFE conveyor belts are versatile and can be used in a wide range of applications beyond high-temperature environments. Their unique properties make them suitable for applications requiring chemical resistance, non-stick surfaces, and low friction. PTFE belts are used in industries such as textiles, packaging, electronics, and aerospace, where their specific advantages meet the unique requirements of different processes. This versatility ensures that PTFE belts can be adapted to various industrial applications, providing reliable and efficient material handling solutions.
Longevity and Durability
The combination of exceptional heat resistance, chemical resistance, low friction, and high tensile strength contributes to the longevity and durability of PTFE conveyor belts. These belts are designed to withstand harsh operating conditions and maintain their performance over extended periods. The durability of PTFE belts reduces the need for frequent replacements, minimizing downtime and maintenance costs. This long lifespan makes PTFE conveyor belts a cost-effective investment for businesses seeking reliable and durable material handling solutions.
Hygiene and Safety
In industries where hygiene and safety are critical, such as food processing and pharmaceuticals, PTFE conveyor belts offer significant advantages. The non-stick surface and chemical resistance of PTFE ensure that the belts can be easily cleaned and sanitized, reducing the risk of contamination. Additionally, PTFE belts do not emit harmful fumes or degrade when exposed to high temperatures, ensuring a safe working environment. These hygiene and safety benefits make PTFE belts an ideal choice for applications where maintaining high standards of cleanliness and safety is essential.
Environmental Impact
PTFE conveyor belts have a relatively low environmental impact compared to other materials. PTFE is a non-toxic material that does not release harmful substances during production or use. The durability and longevity of PTFE belts reduce the need for frequent replacements, minimizing waste and resource consumption. Additionally, the energy efficiency of PTFE belts contributes to lower energy usage and reduced carbon footprint. These environmental benefits make PTFE conveyor belts a sustainable choice for businesses seeking to minimize their environmental impact.
PTFE conveyor belts offer unique advantages in high-temperature applications and beyond. Exceptional heat resistance, non-stick surface, chemical resistance, low friction, high tensile strength, versatility, longevity, hygiene, and environmental benefits make PTFE belts an ideal material handling solution for various industries. By understanding the properties and benefits of PTFE conveyor belts, businesses can select the right belt for their specific needs, ensuring efficient, reliable, and sustainable operations in demanding environments.
Hot Conveyor Belt: Maintenance Tips for Heat Resistant Conveyor Belts
Maintaining heat resistant conveyor belts, such as the hot conveyor belt, is essential to ensure their longevity and optimal performance. Proper maintenance practices can prevent premature failure, reduce downtime, and enhance the efficiency of material handling operations. In this section, we offer practical tips for maintaining heat resistant conveyor belts, including advice on regular inspections, cleaning methods, and preventative maintenance practices.
Regular Inspections
Conducting regular inspections is a critical aspect of maintaining heat resistant conveyor belts. Regular inspections help identify potential issues early, allowing for timely repairs and preventing major failures. Key areas to focus on during inspections include:
- Belt Surface: Check for signs of wear, cracks, or damage on the belt surface. Look for areas where the belt may be thinning or showing signs of thermal degradation.
- Belt Alignment: Ensure that the belt is properly aligned and centered on the conveyor system. Misalignment can cause uneven wear and reduce the belt’s lifespan.
- Tension: Verify that the belt tension is within the recommended range. Over-tensioned or under-tensioned belts can lead to premature wear and reduced performance.
- Rollers and Pulleys: Inspect rollers and pulleys for wear, damage, or misalignment. Ensure that they rotate smoothly and are free from debris.
- Splices and Joints: Examine splices and joints for signs of weakness or separation. Properly maintained splices and joints are crucial for the belt’s integrity and performance.
Cleaning Methods
Keeping heat resistant conveyor belts clean is essential for maintaining their performance and longevity. Regular cleaning prevents material buildup, reduces the risk of contamination, and ensures smooth operation. Effective cleaning methods include:
- Dry Cleaning: Use brushes or air blowers to remove loose debris and dust from the belt surface. This method is suitable for dry and dusty environments.
- Wet Cleaning: For applications involving sticky or greasy materials, wet cleaning with water and mild detergents may be necessary. Ensure that the cleaning agents used are compatible with the belt material and do not cause degradation.
- Chemical Cleaning: In environments where the belt is exposed to chemicals, use appropriate chemical cleaners to remove residues. Always follow the manufacturer’s recommendations for chemical cleaning to avoid damaging the belt.
- High-Temperature Cleaning: In high-temperature applications, ensure that cleaning methods do not subject the belt to thermal shock. Gradually cool down the belt before cleaning to prevent damage from sudden temperature changes.
Preventative Maintenance Practices
Implementing preventative maintenance practices can significantly extend the lifespan of heat resistant conveyor belts and enhance their performance. Key preventative maintenance practices include:
- Lubrication: Ensure that bearings, rollers, and other moving parts are properly lubricated to reduce friction and wear. Use high-temperature lubricants suitable for the operating environment.
- Belt Tension Adjustment: Regularly check and adjust belt tension to ensure it is within the recommended range. Proper tensioning prevents slippage, reduces wear, and enhances performance.
- Replacement of Worn Components: Replace worn or damaged components, such as rollers, pulleys, and splices, promptly to prevent further damage to the belt and ensure smooth operation.
- Monitoring System: Implement a monitoring system to track belt performance and detect early signs of wear or issues. Monitoring systems can include sensors, cameras, and software that provide real-time data and alerts for maintenance needs.
- Training: Provide training for maintenance personnel to ensure they are knowledgeable about proper maintenance procedures and best practices for heat resistant conveyor belts.
Handling and Storage
Proper handling and storage of heat resistant conveyor belts are essential to prevent damage and maintain their performance. Key handling and storage tips include:
- Avoid Sharp Bends: When handling and installing belts, avoid sharp bends and excessive twisting, as these can cause damage to the belt’s structure.
- Store in a Cool, Dry Place: Store belts in a cool, dry environment away from direct sunlight, heat sources, and chemicals. Proper storage conditions prevent degradation and extend the belt’s lifespan.
- Protect from Mechanical Damage: Ensure that belts are protected from mechanical damage during storage and handling. Use appropriate packaging and handling equipment to prevent cuts, abrasions, and other physical damage.
Troubleshooting Common Issues
Being able to troubleshoot common issues with heat resistant conveyor belts can help maintenance personnel address problems quickly and effectively. Common issues and troubleshooting tips include:
- Belt Slippage: Check belt tension and adjust if necessary. Ensure that pulleys and rollers are clean and free from debris.
- Uneven Wear: Inspect belt alignment and adjust as needed. Check for misaligned rollers and pulleys that may be causing uneven wear.
- Belt Cracking or Hardening: Assess the operating temperature and ensure it is within the belt’s specified range. Consider upgrading to a belt with higher heat resistance if the current belt is not suitable for the application.
- Splice Failure: Examine splices for proper installation and integrity. Re-splice or repair joints as needed to maintain belt performance.
Replacement Planning
Despite regular maintenance, heat resistant conveyor belts will eventually need replacement. Planning for belt replacement helps minimize downtime and ensures seamless transitions. Key considerations for replacement planning include:
- Lifespan Monitoring: Track the belt’s usage and lifespan based on operational conditions and manufacturer recommendations. Plan for replacements before the belt reaches the end of its useful life.
- Inventory Management: Maintain an inventory of replacement belts to ensure quick access when a replacement is needed. Stock belts that match the specifications of the existing system.
- Scheduled Downtime: Schedule belt replacements during planned maintenance shutdowns to minimize disruption to production. Coordinate with production teams to ensure smooth transitions.
Maintaining heat resistant conveyor belts, such as the hot conveyor belt, requires regular inspections, effective cleaning methods, and proactive preventative maintenance practices. Proper handling and storage, troubleshooting common issues, and planning for belt replacement are also essential to ensure the longevity and optimal performance of these belts. By following these maintenance tips, businesses can enhance the efficiency and reliability of their material handling operations, reduce downtime, and achieve long-term cost savings.
FAQs about Hot Conveyor Belt
The term “warm conveyor belt” refers to a specific meteorological phenomenon associated with extratropical cyclones. It is a stream of warm, moist air that ascends from the surface and rises along the cold front of the cyclone. This warm air mass contributes to the formation of clouds and precipitation as it cools and condenses while rising. In the context of conveyor belts in meteorology:
Warm Air Movement:
The warm conveyor belt transports warm air from the low levels of the atmosphere up to higher altitudes. This movement is crucial for the development and intensification of weather systems.
Cloud Formation:
As the warm air rises, it cools and condenses, leading to cloud formation and often resulting in widespread precipitation, such as rain or snow.
Weather Impact:
Understanding the warm conveyor belt is essential for predicting weather patterns, particularly the development of storms and heavy precipitation events. It plays a significant role in shaping weather conditions in mid-latitude regions.
A heat resistant conveyor belt is designed to withstand high temperatures without degrading or losing its structural integrity. These belts are essential in industries where materials are transported at elevated temperatures, such as foundries, glassworks, and metal processing plants. Key features of heat resistant conveyor belts include:
Material Composition:
These belts are typically made from materials that can endure high temperatures, such as specially formulated rubber compounds, Teflon, or silicone. These materials provide excellent heat resistance and durability.
Temperature Range:
Heat resistant conveyor belts can withstand temperatures ranging from 100°C to 200°C or higher, depending on the specific belt design and material composition.
Applications:
Common applications include transporting hot materials in foundries, handling heated parts in automotive manufacturing, and moving hot glass in glass production facilities.
Benefits:
Using heat resistant conveyor belts helps prevent belt damage and reduces the risk of fire or thermal degradation. This ensures safe and efficient material handling in high-temperature environments.
Conveyor belt fires can be catastrophic, leading to significant damage, operational downtime, and safety hazards. Several factors can cause conveyor belt fires, and understanding these causes is crucial for implementing preventative measures. Key causes of conveyor belt fires include:
Friction:
Excessive friction between the conveyor belt and components, such as rollers or pulleys, can generate enough heat to ignite the belt material. This is often due to misalignment, improper tension, or worn-out components.
Hot Work:
Activities such as welding, cutting, or grinding near the conveyor belt can produce sparks or hot debris that can ignite the belt, especially if it is made of flammable materials.
Electrical Issues:
Electrical faults, such as short circuits or overheating motors, can create sparks or excessive heat, leading to fires. Proper maintenance and monitoring of electrical components are essential to prevent such incidents.
Material Spillage:
Spilled materials, especially flammable substances, can accumulate on or around the conveyor belt. These materials can catch fire due to heat from the conveyor system or external sources.
Static Electricity:
Static electricity buildup can create sparks that ignite the conveyor belt. This is more common in environments with dry conditions or materials prone to generating static charges.
Conveyor belts are essential components in various industries, designed to transport materials efficiently and safely. Different types of conveyor belts cater to specific applications and operational requirements. Key types of conveyor belts include:
Flat Belt Conveyors:
The most common type, flat belt conveyors, are used to transport items of various sizes and shapes. They consist of a flat, continuous belt driven by pulleys. These belts are ideal for general-purpose material handling and can be found in industries like manufacturing, logistics, and packaging.
Modular Belt Conveyors:
Made from interlocking plastic or metal modules, modular belt conveyors offer flexibility and ease of maintenance. They are suitable for applications requiring frequent cleaning or belt replacement, such as food processing and packaging.
Cleated Belt Conveyors:
Cleated belts have raised sections (cleats) that help in the transport of materials at steep angles or inclines. These conveyors are used in industries like agriculture, mining, and construction to move bulk materials.
Incline/Decline Belt Conveyors:
Designed to move materials between different levels, incline and decline belt conveyors are used in applications where materials need to be transported up or down a slope. They are commonly used in warehousing and distribution centers.
Roller Bed Conveyors:
These conveyors consist of a series of rollers over which the belt moves. Roller bed conveyors are ideal for heavy loads and applications requiring long distances. They are often used in manufacturing and assembly lines.
Specialty Belts:
Specialty belts are designed for specific applications, such as heat resistant, chemical resistant, or flame retardant belts. These belts are tailored to meet the unique demands of industries like metal processing, chemical manufacturing, and firefighting equipment transport.
Last Updated on June 6, 2024 by Jordan Smith
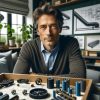
Jordan Smith, a seasoned professional with over 20 years of experience in the conveyor system industry. Jordan’s expertise lies in providing comprehensive solutions for conveyor rollers, belts, and accessories, catering to a wide range of industrial needs. From initial design and configuration to installation and meticulous troubleshooting, Jordan is adept at handling all aspects of conveyor system management. Whether you’re looking to upgrade your production line with efficient conveyor belts, require custom conveyor rollers for specific operations, or need expert advice on selecting the right conveyor accessories for your facility, Jordan is your reliable consultant. For any inquiries or assistance with conveyor system optimization, Jordan is available to share his wealth of knowledge and experience. Feel free to reach out at any time for professional guidance on all matters related to conveyor rollers, belts, and accessories.