How to Align a Conveyor Belt? 6 Easy Steps
Understanding how to align a conveyor belt is crucial for the efficient operation of conveyor systems, which are integral to the smooth functioning of various industries, from manufacturing to logistics. Proper alignment of a conveyor belt ensures that the system operates smoothly, reduces wear and tear on the belt, and minimizes the energy consumption of the motor driving the belt. Misalignment, on the other hand, can lead to several issues, including uneven belt wear, increased strain on the conveyor structure, premature belt failure, and potential product damage or loss during transport. These consequences not only result in unnecessary downtime but also lead to significant maintenance and replacement costs. Therefore, mastering how to align conveyor belt is not just about maintaining the equipment; it’s about sustaining operational efficiency, safety, and profitability in your operations.
The Basics of How to Align a Conveyor Belt
Understanding the basics of how to align a conveyor belt is fundamental to ensuring the longevity and efficiency of your conveyor system. Much like the alignment of tires is critical to the performance of a vehicle, ensuring that your conveyor belt is properly aligned is essential for the smooth and efficient operation of your operation. Misalignment can lead to a host of problems, including uneven wear on the belt, increased energy consumption, and even damage to the conveyor itself.
The process of aligning a conveyor belt involves adjusting the belt and conveyor components to ensure that the belt runs straight and true along the conveyor’s length. This is crucial not only for the efficiency of the conveyor’s operation but also for the safety of the workers and the protection of the materials being transported. An aligned conveyor belt reduces the risk of the belt slipping or catching, which can cause significant downtime and potentially hazardous situations.
The significance of learning how to align a conveyor belt cannot be overstated. In operations where materials must be moved efficiently and reliably, the alignment of the conveyor belt plays a pivotal role. It ensures that the system operates at peak efficiency, minimizing wear and tear on the belt and the conveyor’s mechanical components. This, in turn, reduces maintenance costs and prolongs the life of the conveyor system.
Comparing conveyor belt alignment to vehicle tire alignment helps underscore its importance. Just as misaligned tires can cause a car to veer off course, consume more fuel, and lead to premature tire wear, a misaligned conveyor belt can lead to product spillage, increased energy consumption, and premature belt failure. Both scenarios highlight the critical nature of proper alignment for optimal performance and longevity.
Mastering how to align conveyor belt is an essential skill for anyone responsible for the maintenance and operation of a conveyor system. It ensures the system runs smoothly, efficiently, and safely, ultimately contributing to the overall success of the operations it supports.
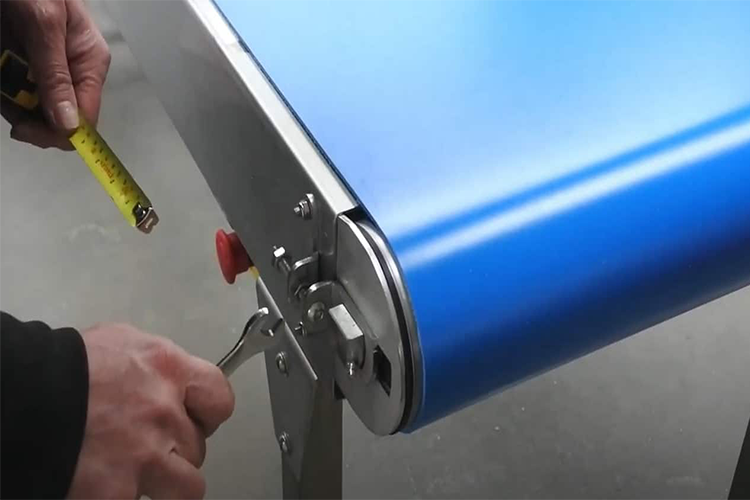
Tools Required for How to Align a Conveyor Belt
When tackling the task of how to align a conveyor belt, having the right tools at your disposal is crucial. Each tool plays a specific role in ensuring the alignment process is carried out accurately and efficiently. Here’s a detailed look at the tools needed for conveyor belt alignment and a brief introduction to each:
Surveyor’s Transit
A surveyor’s transit is essential for establishing straight lines and angles with precision. When aligning a conveyor belt, it helps in determining the exact position of the belt and components in relation to the desired path. This tool is invaluable for ensuring that the head and tail pulleys are perfectly aligned with each other and perpendicular to the conveyor’s direction.
Carpenter’s Level
A carpenter’s level is used to check that all parts of the conveyor, including the frame and rollers, are level. A level conveyor is foundational to how to align a conveyor belt, as even slight inclines or declines can cause the belt to track incorrectly. This simple tool can prevent a multitude of alignment issues.
Chalk and Chalk Line
Chalk and a chalk line are used to mark reference lines along the conveyor. These lines serve as guides for aligning the conveyor components and the belt itself. By snapping a chalk line across the length of the conveyor, you create a visual aid that helps ensure all adjustments keep the belt on its intended path.
Tape Measure
A tape measure is indispensable for precise measurements during the alignment process. It’s used to measure distances between the conveyor belt and fixed points to ensure symmetry and balance. Accurate measurements are critical in adjusting the conveyor to the correct alignment.
Plumb Bob
A plumb bob is a weighted object suspended from a string used to establish a vertical reference line. This tool is particularly useful for transferring measurements from the conveyor structure to the ground or floor, ensuring vertical alignment of the pulleys and rollers with the belt’s path.
Rigid Steel (2 x 2 Box Tubing or Angle Iron)
Rigid steel, such as 2 x 2 box tubing or angle iron, is used as a straight edge or guide when aligning the conveyor belt. It can be placed along the conveyor’s length to provide a physical reference for straightness. This tool helps in checking the alignment of rollers and the conveyor frame, ensuring they are parallel to the belt’s direction.
Equipped with these tools, the process of how to align a conveyor belt becomes a systematic and achievable task. Each tool contributes to a step in the alignment process, helping to diagnose and correct misalignment issues, ensuring the conveyor operates efficiently and effectively.
Enhance efficiency with our high-quality conveyor belts. Contact us now!
How to Align A Conveyor Belt In 6 Easy Steps
Aligning a conveyor belt properly is essential for ensuring efficient operation and preventing premature wear and potential system failures.Aligning a conveyor belt is a meticulous process that requires precision and patience. Following a systematic approach ensures that the belt operates efficiently and extends its service life. Here’s a detailed guide on how to align a conveyor belt:
Step 1: Level All of the Rollers
The first step in how to align a conveyor belt involves leveling all the rollers. Using a carpenter’s level, check each roller to ensure it is perfectly horizontal. Rollers that are not level can cause the belt to drift off to one side. Adjust the roller brackets as necessary until the bubble in the level is centered, indicating that the roller is level. It’s crucial that all rollers are parallel to each other and perpendicular to the conveyor’s direction to prevent the belt from tracking incorrectly.
Step 2: Define the Center Line of Your Conveyor
Defining the center line of your conveyor is essential for proper alignment. Use a rigid piece of steel, such as a 2 x 2 box tubing or angle iron, and a plumb bob to mark the conveyor’s center line on the floor along its length. This line serves as a reference for aligning the conveyor components. The center line should be straight and run parallel to the conveyor’s direction, ensuring that all adjustments are made in relation to this fixed point.
Step 3: Set Up the Transit
Setting up the transit is critical for ensuring the conveyor components are aligned correctly. Place the transit at one end of the conveyor and sight across the end roll to the other end. Use the transit to mark alignment lines on the floor perpendicular to the center line. These lines will guide you in aligning the head and tail pulleys, as well as the rollers, ensuring they are square with the conveyor’s path.
Step 4: Align the Head and Tail Pulleys
The head and tail pulleys must be parallel to each other and perpendicular to the conveyor’s center line. Use the tape measure to check the distance from the pulleys to the alignment lines established in Step 3. Adjust the pulleys as needed until they are correctly aligned. Ensuring that these pulleys are properly aligned is crucial for the belt to run straight.
Step 5: Align the Snub Rolls
Snub rolls, which help in maintaining tension and guiding the belt, also need alignment. Align these rolls in relation to the main end rolls, ensuring they are parallel to the head and tail pulleys. Use the tape measure to check their alignment against the center line and make adjustments as necessary. Proper alignment of the snub rolls is essential for consistent belt tension and tracking.
Step 6: Final Inspection and Recommendations
After completing the alignment adjustments, conduct a final inspection to ensure everything is correctly aligned. Check the level and alignment of all rollers, pulleys, and the belt itself. Look for any signs of wear or damage that could affect the conveyor belt’s operation. Test run the conveyor belt and observe its tracking along the center line. Make any final adjustments as needed to ensure optimal alignment.
By following these detailed steps on how to align a conveyor belt, you can ensure your conveyor system operates efficiently, minimizing wear and extending the lifespan of the belt. Regular inspections and maintenance are key to keeping the conveyor in top condition.
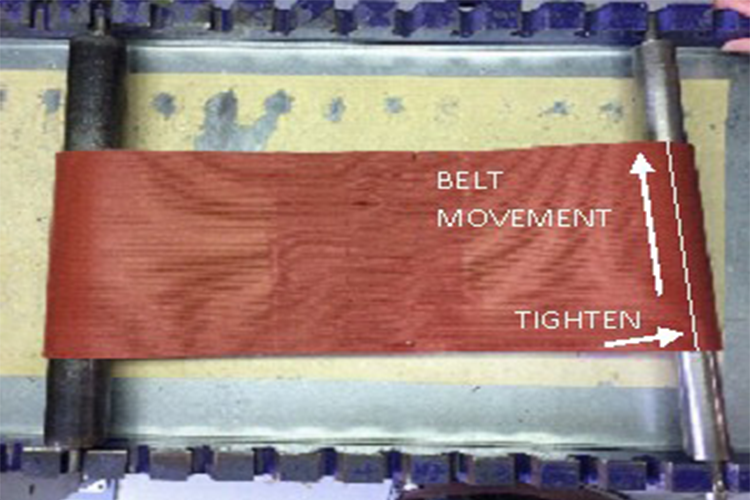
Conveyor Belt Tracking Tips for How to Align a Conveyor Belt
Achieving and maintaining the alignment of a conveyor belt is crucial for the operational efficiency of a conveyor system. The CITA process (Clean, Inspect, Tension, Adjust) provides a structured approach to ensure that conveyor belts are properly aligned and tracking correctly. Here’s how to align a conveyor belt by following the CITA process:
CLEAN: Importance of Starting with a Clean Conveyor
A clean conveyor is foundational to proper belt alignment. Dirt, debris, and residues can cause the conveyor belt to misalign or wear unevenly. Here are five specific examples emphasizing the importance of cleanliness:
- Remove Build-up: Clean off any material build-up on the rollers and along the belt path. Accumulated material can cause the belt to drift off course.
- Wipe Down Pulleys: Clean the pulleys to remove any residue that could reduce friction and cause slippage.
- Clear the Tracks: Ensure the tracks or guides are free from obstructions that could push the belt off alignment.
- Inspect for Spillage: Clean up any spillage around the conveyor to prevent it from getting onto the belt or moving parts.
- Regular Cleaning Schedule: Implement a regular cleaning schedule to maintain a debris-free conveyor, which aids in easier alignment and tracking.
INSPECT: Checking for Wear and Ensuring All Parts are in Working Order
Regular inspections are key to identifying potential issues before they lead to misalignment:
- Check for Wear: Look for signs of wear on the belt edges, surface, and the conveyor’s moving parts. Uneven wear can indicate misalignment.
- Examine Rollers and Pulleys: Ensure they turn freely without resistance. Stuck or dragging rollers can cause the belt to misalign.
- Structural Integrity: Inspect the conveyor frame for signs of damage or warping, which can affect the belt’s path.
- Belt Edges: Look for fraying or damage to the belt edges, as these can be early indicators of tracking issues.
TENSION: Applying the Correct Amount of Tension to the Belt
Proper tension is critical for belt alignment:
- Measure Tension: Use a tension meter to measure the belt’s tension and adjust according to the manufacturer’s specifications.
- Even Tension: Ensure the tension is even across the width of the belt. Uneven tension can cause the belt to track off to one side.
- Adjust Take-up: Use the take-up adjustment to fine-tune the belt tension. This helps in maintaining the correct tension over time.
ADJUST: Fine-Tuning Adjustments to Keep the Belt Running Straight
Making precise adjustments is essential for keeping the belt aligned:
- Track the Belt: Make small adjustments to the rollers or pulleys to steer the belt back to the center. Adjust one side at a time and observe the effect.
- Use Tracking Bars: Install tracking bars or guides to help maintain the belt’s path.
- Monitor and Adjust: Continuously monitor the belt’s position and make adjustments as needed. Remember, small, incremental adjustments are more effective than large ones.
By following these detailed tips on how to align conveyor belt through the CITA process, you can ensure your conveyor belt remains aligned and operates efficiently. Regular maintenance, combined with these proactive steps, will help extend the life of your conveyor system and minimize operational disruptions.
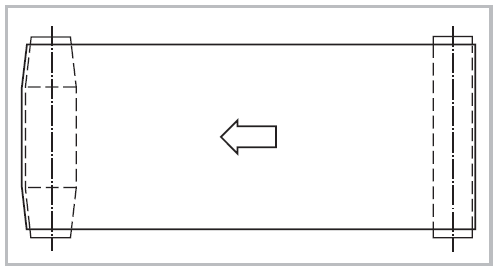
The Importance of Aligning A Conveyor Belt
Aligning a conveyor belt is crucial for several reasons, all of which contribute to the efficient, safe, and cost-effective operation of a conveyor system. Here are the main reasons why proper belt alignment is so important:
- Minimizes Wear and Tear: Proper alignment reduces uneven wear on the belt and conveyor components. Misaligned belts can rub against fixed parts of the conveyor system, leading to rapid wear and tear of the belt edges and the structural components, potentially resulting in costly repairs and replacements.
- Prevents Belt Mis-tracking: Mis-tracking is a common issue where the belt drifts from its intended path. This can lead to belt edges being damaged against the conveyor structure, materials spilling off the sides, and can even cause the belt to derail completely.
- Reduces Downtime: A misaligned belt can cause frequent stoppages to adjust or repair the belt and other damaged components. Keeping the belt aligned helps in maintaining continuous and efficient operation, minimizing downtime.
- Increases Safety: A misaligned conveyor belt can pose various safety risks. For instance, it can lead to spillage of materials from the belt, creating slip hazards. In severe cases, misalignment can lead to catastrophic failures, endangering workers near the system.
- Enhances Material Handling Efficiency: Properly aligned belts ensure that materials are transported smoothly along the conveyor path without spillage or collecting at certain points, which can affect the weight distribution and balance of the belt.
- Saves Energy: A well-aligned belt reduces the energy consumption of the conveyor system. Misalignment causes increased friction and resistance, which in turn requires more power to move the belt and the conveyed materials.
- Extends Equipment Lifespan: Besides reducing wear and tear on the belt itself, alignment prevents excessive stress on bearings, motors, and other mechanical components of the conveyor system, thereby extending the overall lifespan of these components.
To maintain optimal alignment, regular inspections and adjustments should be part of a conveyor system’s maintenance routine. Using specialized alignment tools and technologies can help in accurately aligning the conveyor belt and sustaining its alignment over time. This proactive approach ensures the conveyor system runs smoothly, which is essential for operational efficiency and longevity.
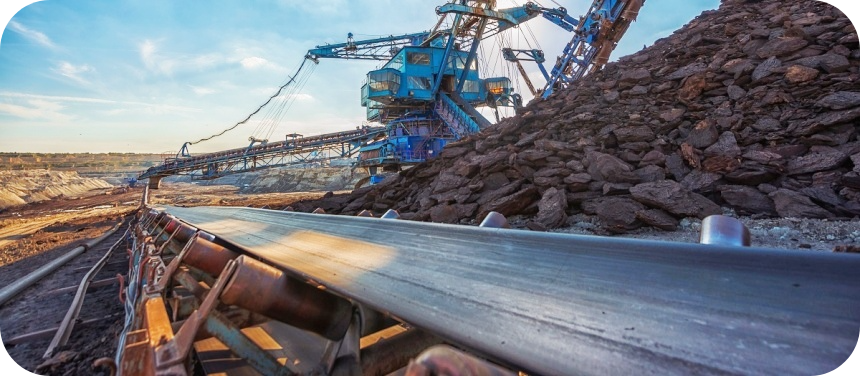
Troubleshooting Common Conveyor Belt Tracking Issues in How to Align a Conveyor Belt
Ensuring a conveyor belt remains aligned requires addressing common tracking issues effectively. Here are solutions for typical problems encountered during the process of how to align a conveyor belt, along with an introduction to automatic conveyor belt tracking systems as a modern solution.
Solutions for Common Problems
- Belt Tracking to One Side: This issue often arises due to uneven tension across the belt’s width. To correct it, adjust the tension on the side the belt is tracking towards. This can be done by tightening the take-up on the opposite side to gently guide the belt back to center.
- Excessive Wear on Edges: When the belt edges wear more than the center, it’s a sign that the belt is not running straight. Inspect and realign the rollers and pulleys to ensure they are perpendicular to the belt’s path.
- Slippage on the Drive Pulley: This can occur when there’s insufficient tension or the pulley is worn and lacks grip. Increase the tension slightly and consider replacing the pulley lagging to improve grip.
- Material Spillage Influencing Belt Path: Material build-up on rollers or along the conveyor path can cause the belt to misalign. Regular cleaning and installing proper containment devices can prevent spillage from affecting belt alignment.
- Seized Rollers Leading to Misalignment: Regularly inspect rollers and replace any that are seized or not rotating freely. Seized rollers can create drag points, causing the belt to track off-center.
Introduction to Automatic Conveyor Belt Tracking Systems
Automatic conveyor belt tracking systems procedure offer a modern solution to belt misalignment issues by continuously monitoring and automatically adjusting the belt’s position. Here are five examples:
- Pneumatic Trackers: These systems use air pressure to position a tracking roller, which gently steers the belt back to the center path.
- Electronic Sensors: Mounted along the conveyor frame, these sensors detect when the belt begins to drift and automatically adjust the tension or roller angle to realign the belt.
- Self-Aligning Idlers: These idlers pivot in response to the belt’s movement, guiding the belt back to its correct path without manual intervention.
- Active Roller Belt Technology: This involves rollers embedded in the conveyor belt surface, which can rotate to adjust the belt’s direction, ensuring it stays aligned.
- Edge Detection Systems: Using optical or mechanical sensors, these systems detect when the belt edges deviate from the intended path and trigger adjustments to realign the belt.
By addressing common tracking issues and considering the adoption of automatic conveyor belt tracking systems, maintaining proper alignment becomes more manageable. These modern solutions not only reduce the need for manual adjustments but also enhance the overall efficiency and reliability of the conveyor system. Understanding how to align a conveyor belt and troubleshooting common issues are essential skills for ensuring the longevity and productivity of your conveyor operations.
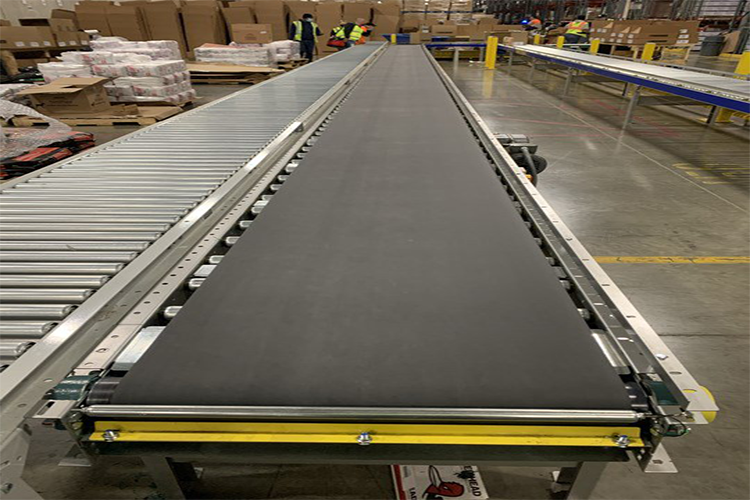
Additional Resources for How to Align a Conveyor Belt
For those seeking to deepen their understanding of how to align a conveyor belt, a wealth of additional resources is available. These materials can provide further insights into best practices, troubleshooting, and advanced techniques for ensuring optimal conveyor belt performance.
Conveyor Belt Alignment and Tracking PDFs and Diagrams
A variety of PDFs and diagrams offer detailed guidance on conveyor belt alignment and tracking. These resources typically include:
- Step-by-Step Guides: Comprehensive documents that walk you through the process of how to align a conveyor belt, from initial assessment to final adjustments.
- Troubleshooting Charts: Diagrams and flowcharts that help diagnose common alignment issues, offering potential solutions based on symptoms observed.
- Maintenance Checklists: Checklists that outline regular maintenance tasks to keep your conveyor belt properly aligned and functioning efficiently.
- Technical Specifications: Detailed specifications and measurements for components related to conveyor belt alignment, ensuring compatibility and precision in adjustments.
- Safety Protocols: Guidelines to ensure that alignment procedures are conducted safely, protecting both personnel and equipment.
These resources are invaluable for both novice and experienced technicians, providing a solid foundation for understanding the complexities of conveyor belt alignment.
Consulting with Technical Experts
For complex alignment issues or when implementing new conveyor systems, consulting with technical experts is highly recommended. These professionals can offer:
- Customized Solutions: Expert insights tailored to your specific conveyor system, addressing unique challenges and operational requirements.
- On-site Assessments: Comprehensive evaluations of your conveyor belt alignment, identifying potential issues and recommending corrective actions.
- Training Workshops: Hands-on training sessions for maintenance teams, focusing on the skills needed to effectively align and maintain conveyor belts.
- Latest Innovations: Information on the latest tools, technologies, and methodologies for conveyor belt alignment, ensuring your operations benefit from cutting-edge practices.
- Ongoing Support: Access to professional support for troubleshooting and fine-tuning alignment, ensuring long-term reliability and efficiency.
Leveraging these additional resources and expert consultations can significantly enhance your ability to maintain proper conveyor belt alignment. Whether you’re looking to resolve specific issues or aiming to improve your overall maintenance strategy, these resources provide valuable insights and support. Remember, effective conveyor belt alignment is key to optimizing the performance and longevity of your conveyor system, making it crucial to invest time in learning how to align a conveyor belt correctly and efficiently.
Eliminate downtime with our superior conveyor belts. Act fast and connect!
FAQs About How to Align a Conveyor Belt
Fixing a misaligned conveyor belt involves several steps to identify and correct the root cause of the misalignment. Initially, inspect the entire conveyor structure to ensure it is level and square. This includes checking the frame, rollers, and pulleys for any signs of wear or damage that could contribute to misalignment. If the conveyor is not level, adjust the legs or supports to bring it into alignment. Next, examine the rollers and pulleys to ensure they are correctly installed, parallel to each other, and perpendicular to the direction of the belt travel. Misaligned rollers and pulleys can be adjusted according to the manufacturer’s specifications. Additionally, check the belt tension, as improper tension can lead to misalignment. Adjust the tension evenly on both sides of the conveyor to prevent the belt from tracking off to one side. Regular maintenance and inspections are crucial to prevent future misalignments and ensure the conveyor operates efficiently.
Aligning a conveyor requires a systematic approach to ensure all components work harmoniously, preventing belt misalignment. For optimal tracking, roller belt contact should be ¼ width, with a 5°-10° incline, and diagonal measurements must match. Adjust the supports or legs as necessary. Next, align the head and tail pulleys to be square with the frame. This can be done by measuring from fixed points on the conveyor to the pulleys and adjusting until the measurements are equal. Rollers should also be checked for alignment and adjusted to be parallel with the belt’s path. For belt tension adjustments, use the take-up units to apply even tension across the belt width, which helps in keeping the belt aligned. Regularly inspecting and maintaining these components is key to keeping the conveyor aligned over time.
Adjusting a conveyor belt to run straight involves several key adjustments to the conveyor system. First, ensure that the conveyor frame is level and square. An unlevel frame can cause the belt to drift off to one side. Use a level to check the frame and adjust the legs as necessary. Next, inspect the rollers and pulleys to ensure they are correctly installed and aligned. Misaligned rollers or pulleys can cause the belt to track incorrectly. Adjustments can be made to the roller brackets or pulley mounts to correct any misalignment. Additionally, check the belt tension, as uneven tension can cause the belt to run off-center. Adjust the tension evenly across the belt by using the take-up mechanism. Finally, consider installing belt tracking devices or guides that can help keep the belt centered. Regular maintenance and adjustments are crucial to prevent the belt from running off-track.
Keeping a conveyor belt centered requires regular maintenance and adjustments to the conveyor system. Ensure the conveyor frame is level and square, as an unlevel frame can cause the belt to drift. Use a level to check and adjust the frame’s alignment. Rollers and pulleys should be inspected for proper installation and alignment. They should be parallel to the conveyor’s direction and perpendicular to the belt’s path. Misaligned rollers or pulleys can be adjusted to correct the belt’s path. Belt tension should also be monitored and adjusted evenly across the belt width to prevent it from drifting to one side. Installing belt tracking devices or guides can provide additional support in keeping the belt centered. These devices can be adjusted to apply gentle pressure to the belt edges, guiding it back to the center. Regular inspections and adjustments to these components will help maintain the belt’s centered position over time, ensuring efficient operation of the conveyor system.
Last Updated on June 6, 2024 by Jordan Smith
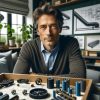
Jordan Smith, a seasoned professional with over 20 years of experience in the conveyor system industry. Jordan’s expertise lies in providing comprehensive solutions for conveyor rollers, belts, and accessories, catering to a wide range of industrial needs. From initial design and configuration to installation and meticulous troubleshooting, Jordan is adept at handling all aspects of conveyor system management. Whether you’re looking to upgrade your production line with efficient conveyor belts, require custom conveyor rollers for specific operations, or need expert advice on selecting the right conveyor accessories for your facility, Jordan is your reliable consultant. For any inquiries or assistance with conveyor system optimization, Jordan is available to share his wealth of knowledge and experience. Feel free to reach out at any time for professional guidance on all matters related to conveyor rollers, belts, and accessories.