How to Connect A Conveyor Belt Satisfactorily
The process of how to connect a conveyor belt is a fundamental aspect of setting up efficient, reliable, and safe conveyor systems. Proper installation and connection of conveyor belts are paramount to ensuring the seamless operation of the conveyor system, which plays a critical role in numerous industries, from manufacturing to logistics. The integrity of a conveyor belt’s connection directly impacts the system’s performance, longevity, and safety. Recognizing this importance, many businesses rely on professional installation companies that specialize in conveyor systems. These experts not only bring a wealth of experience and precision to the task but also ensure that the installation adheres to the highest standards of quality and safety. Additionally, for those opting for a more hands-on approach, detailed installation manuals are available, offering step-by-step guidance on how to connect a conveyor belt effectively. These resources are invaluable for ensuring that the conveyor belt is installed correctly, promoting optimal functionality and durability.
How to Connect A Conveyor Belt: Four Common Methods
How to connect a conveyor belt? Four common methods :Mechanical Fasteners, Vulcanization, Cold Bonding, Finger Splicing. Connecting a conveyor belt involves joining the ends of the belt to form a continuous loop, enabling it to move materials efficiently:
Mechanical Fasteners
- Description: Mechanical fasteners involve using metal or plastic clips, lacing, or hinges to physically attach the two ends of the belt.
- Advantages: This method is quick and easy to install, making it ideal for emergency repairs or temporary connections. It allows for easy disassembly when needed.
- Disadvantages: Mechanical fasteners can cause belt wear over time, and they may create a slight bump at the splice, affecting smooth operation.
Vulcanization
- Description: Vulcanization involves using heat, pressure, and sometimes chemicals to fuse the belt ends together, creating a seamless and strong bond.
- Advantages: This method produces a durable and smooth joint with no noticeable seam, making it ideal for heavy-duty applications and reducing wear on the belt.
- Disadvantages: Vulcanization requires specialized equipment and expertise, making it more time-consuming and expensive compared to other methods.
Cold Bonding
- Description: Cold bonding uses an adhesive to glue the belt ends together. The belt ends are prepared, the adhesive is applied, and the ends are pressed together until the bond is secure.
- Advantages: Cold bonding is easier and faster than vulcanization and does not require heat. It can be done on-site and is suitable for applications where heat cannot be applied.
- Disadvantages: The bond may not be as strong as a vulcanized joint, making it less suitable for high-stress or heavy-duty applications.
Finger Splicing
- Description: Finger splicing involves cutting the belt ends into interlocking “fingers” that are then bonded together. The fingers are usually glued or vulcanized, depending on the application.
- Advantages: This method creates a smooth, strong splice with minimal impact on belt performance. It is often used for high-tension belts and provides excellent durability.
- Disadvantages: Finger splicing is more complex and time-consuming to perform, requiring precise cutting and alignment, as well as the right tools and expertise.
Each of these methods has its own set of benefits and is chosen based on the specific requirements of the conveyor system, the type of belt, and the application environment.

How to Connect a Conveyor Belt: Types of Conveyor Belt Joints
Conveyor belt joints, also known as splices, are methods used to connect the ends of a conveyor belt to form a continuous loop. The choice of joint depends on the belt material, the application, and the required performance. Here are some of the different types of conveyor belt joints:
1. Mechanical Joints
- Description: Mechanical joints involve using metal or plastic fasteners to physically join the ends of the belt.
- Types:
- Hinged Fasteners: These are metal plates connected by a pin, forming a hinge. They are used for belts requiring frequent opening and closing.
- Plate Fasteners: Metal plates bolted or riveted onto the belt ends. Suitable for heavy-duty applications.
- Lacing: Metal or plastic laces are woven into the belt ends, creating a flexible yet strong joint.
- Applications: Ideal for quick repairs, belts with frequent maintenance, or temporary installations.
2. Vulcanized Joints
- Description: Vulcanized joints involve chemically bonding the belt ends using heat, pressure, and sometimes adhesives, creating a seamless and durable joint.
- Types:
- Hot Vulcanization: The belt ends are heated and pressed together, forming a strong and permanent bond. Commonly used for high-tension belts and critical applications.
- Cold Vulcanization: Adhesives are used to bond the belt ends without applying heat. Easier to perform on-site but less durable than hot vulcanization.
- Applications: Used in applications requiring high-strength and seamless splices, such as in mining, quarrying, and heavy-duty material handling.
3. Finger Splice Joints
- Description: Finger splicing involves cutting the belt ends into multiple interlocking “fingers” that are then bonded together.
- Types:
- Standard Finger Splice: Fingers are cut and then either vulcanized or glued together, creating a smooth and strong joint.
- Stepped Finger Splice: The fingers are cut in a stepped pattern, providing additional strength and stability to the joint.
- Applications: Commonly used in applications requiring a smooth surface, such as in food processing or cleanroom environments.
4. Scarf Joints
- Description: Scarf joints involve cutting the belt ends at a shallow angle and overlapping them before bonding. This method reduces the thickness at the splice, providing a smooth and strong joint.
- Applications: Often used in applications where belt thickness must be consistent, such as in light to medium-duty material handling.
5. Step Joints
- Description: Step joints are similar to scarf joints but involve cutting the belt ends in a stepped pattern. The layers of the belt are offset and overlapped before bonding.
- Applications: Used in applications where a strong, smooth, and flexible joint is required, such as in high-tension belts or where belt flexibility is essential.
6. Overlap Joints
- Description: In overlap joints, the belt ends are overlapped and bonded or fastened together. This method can create a thicker splice, which may affect belt tracking and performance.
- Applications: Suitable for applications where strength is prioritized over a seamless surface, often used in low to medium-tension belts.
7. Butt Joints
- Description: Butt joints involve aligning the belt ends edge-to-edge and then bonding them together, typically using a backing material to reinforce the joint.
- Applications: Used in applications where the belt needs to remain as thin as possible, such as in precision material handling or where space constraints exist.
Each of these joint types is selected based on specific operational requirements, including the type of material being transported, the tension and speed of the conveyor belt, and the environmental conditions of the application.
Understanding how to connect a conveyor belt using these methods ensures that the chosen solution best fits the application’s needs, optimizing the conveyor system’s performance and longevity.
How to Connect A Conveyor Belt: Mechanical Fasteners Or Endless Splicing
Here’s a comparison between Mechanical Fasteners and Endless Splicing for connecting a conveyor belt:
This table helps in understanding the key differences between using mechanical fasteners and endless splicing for connecting conveyor belts, allowing for an informed decision based on specific operational needs.

How to Connect a Conveyor Belt: A Comprehensive Guide
The process of how to connect a conveyor belt is a critical step in the installation of conveyor systems, which are integral to the operations of various industries. This section delves into the intricacies of conveyor belt installation, highlighting the pivotal role played by professional installation companies and the indispensable value of adhering to the conveyor belt installation manual.
Overview of the Conveyor Belt Installation Process
The installation of a conveyor belt involves several key steps, starting from the initial assessment of the site and the specific requirements of the conveyor system. This includes measuring the length of the conveyor, selecting the appropriate type of belt for the application, and preparing the site and equipment for installation. The actual process of how to connect a conveyor belt encompasses aligning the belt ends, cutting them to the precise length, and then joining them using one of the methods such as vulcanization, mechanical fastening, or cold bonding. Each step requires meticulous attention to detail to ensure the belt operates smoothly and efficiently.
The Role of Conveyor Belt Installation Companies
Professional conveyor belt installation companies offer a range of services designed to ensure the optimal setup and operation of conveyor systems. These services include:
- Site Evaluation: Assessing the installation site to determine the best conveyor layout and belt type.
- Custom Belt Selection: Helping clients choose the right conveyor belt material and design based on their specific needs.
- Installation: Providing skilled technicians to carry out the installation, ensuring that the process of how to connect a conveyor belt is done correctly.
- Training: Offering training sessions for the client’s staff on how to operate and maintain the conveyor system efficiently.
- After-Sales Support: Providing ongoing support and maintenance services to address any issues that may arise during the operation of the conveyor belt.
Importance of Following the Belt Conveyor Installation Manual
Adhering to the conveyor belt installation manual is crucial for a successful setup. The manual contains detailed instructions and guidelines that cover every aspect of the installation process, including:
- Safety Precautions: Ensuring that all safety protocols are followed to protect the installation team and the facility’s staff.
- Tool Requirements: Listing the specific tools and equipment needed for the installation, ensuring that the team is well-prepared.
- Step-by-Step Instructions: Providing clear, detailed steps on how to connect conveyor belt, reducing the risk of errors.
- Adjustment Procedures: Guiding the technicians on how to adjust the belt tension and alignment for optimal performance.
- Maintenance Tips: Offering advice on regular maintenance practices to prolong the life of the conveyor belt and prevent downtime.
By understanding the comprehensive process of how to connect a conveyor belt, including the role of professional installation companies and the importance of following the installation manual, businesses can ensure the efficient and safe operation of their conveyor systems.
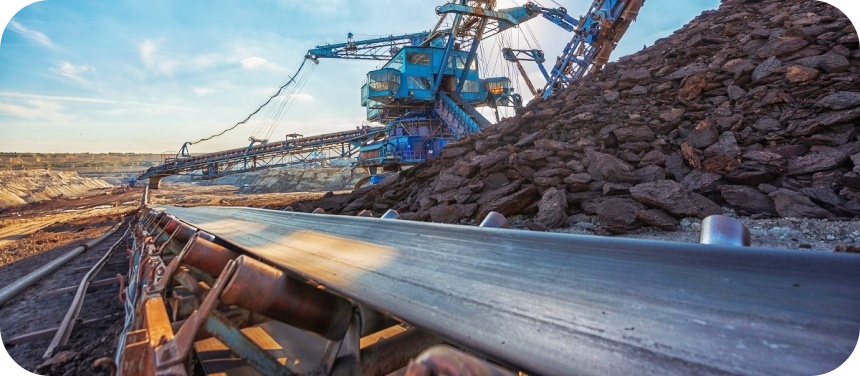
How to Connect a Conveyor Belt: A Step-by-Step Guide
Connecting a conveyor belt correctly is crucial for the operational efficiency and longevity of the conveyor system. This section outlines the practical steps for how to connect a conveyor belt, incorporating techniques from professional manuals and providing tips on selecting the right type of joint for various applications.
Step-by-Step Guide on Connecting a Conveyor Belt
Preparation: Begin by ensuring the conveyor belt ends are clean, straight, and square. This preparation is crucial for a strong, reliable joint.
Measurement: Measure the belt length needed, considering the tensioning and tracking adjustments.
Cutting: Cut the belt ends using a straight edge and a sharp cutting tool to ensure a clean, straight cut.
Choosing the Joint Type: Select the joint type based on the belt’s application, material, and operational requirements. The options include mechanical fastening, vulcanized splicing, or cold bonding.
Applying the Joint:
- For mechanical fasteners, position the fasteners on the belt ends, ensuring they are aligned correctly before using the installation tool to secure them.
- For vulcanized splicing, prepare the belt ends for vulcanization by skiving (if necessary) and apply the vulcanizing material before using a vulcanizing press to apply heat and pressure.
- For cold bonding, apply the adhesive to both belt ends, press them together, and allow sufficient time for the bond to cure.
Finishing Touches: After connecting the belt, inspect the joint closely for any irregularities and trim any excess material. Test the belt under light load to ensure proper alignment and tension.
Tips on Selecting the Right Type of Joint
The selection of the joint type is critical and should be based on the conveyor belt’s type and application. Here are five specific examples:
- Light-Duty Applications: For belts in light-duty applications, such as small product transfer, a simple mechanical fastener or cold bonding method may suffice.
- Food Processing: In food processing applications, where cleanliness and minimal crevices are crucial, an endless splice created through vulcanization is preferred.
- Heavy-Duty Operations: For heavy-duty applications involving high loads or sharp materials, a vulcanized splice offers the durability and strength needed.
- High-Speed Conveyors: High-speed applications benefit from the smooth operation of an endless splice, reducing vibration and wear on the conveyor system.
- Temporary Setups: For temporary or portable conveyor systems, mechanical fasteners provide the flexibility and ease of installation and removal needed.
By following these practical steps on how to connect a conveyor belt and selecting the appropriate joint type, you can ensure a successful installation that maximizes the conveyor belt’s performance and lifespan.

How to Connect A Conveyor Belt: Two Conveyor Belts
Connecting two conveyor belts involves careful planning to ensure smooth operation and minimal downtime. Here’s a detailed step-by-step guide in English:
Assess the Setup
- Determine the Type of Conveyor Belts: Identify the types of conveyor belts you are working with (e.g., flat belt, modular belt, roller belt).
- Measure the Belts: Measure the width, length, and thickness of both belts to ensure compatibility.
Align the Conveyors
- Positioning: Place the two conveyor belts in close proximity, ensuring that the end of one belt aligns perfectly with the beginning of the other.
- Check Alignment: Use a laser alignment tool or a straight edge to check that both belts are in perfect alignment to avoid material spillage and uneven wear.
Install a Transfer Device (If Necessary)
- Transfer Plates: Consider installing a transfer plate between the two conveyors if there’s a gap. This helps in smooth transition, especially for smaller items.
- Roller Transfers: For larger items, you might install a roller transfer bridge between the belts.
Connect the Belts Mechanically
- Belt Fasteners: Use appropriate belt fasteners or lacing to join the ends of the conveyor belts. Make sure the fasteners are compatible with the belt material.
- Splicing (if required): For a more permanent connection, you may splice the belts together. This involves cutting, skiving, and bonding the belt ends using adhesives or by heat.
Adjust Belt Tension
- Tensioning Mechanism: Adjust the tension on both belts using the tensioning mechanism to ensure smooth operation. Proper tension prevents belt slippage and ensures longevity.
- Check for Sag: Make sure there is no excessive sagging or overtightening, as both can cause operational issues.
Test the Connection
- Initial Run: Start the conveyor system at a low speed to observe the belt movement. Look for any misalignment, slippage, or material handling issues.
- Fine-Tuning: Make any necessary adjustments to the tension, alignment, or connection points based on the test run.
Safety Checks
- Guards and Covers: Ensure all safety guards and covers are in place before running the conveyor at full speed.
- Emergency Stops: Test emergency stop mechanisms to ensure they are functional and within reach.
Regular Maintenance
- Routine Inspections: Schedule regular inspections to check for wear, alignment, and tension.
- Lubrication: Ensure all moving parts, such as rollers and pulleys, are properly lubricated to reduce friction and wear.
Documentation
- Record the Setup: Document the connection process, including belt specifications, tension settings, and any special considerations. This will be useful for future maintenance or adjustments.
By following these steps, you can successfully connect two conveyor belts, ensuring a seamless and efficient transfer of materials between them.
How to Connect a Conveyor Belt: Ensuring Longevity and Safety
After understanding how to connect a conveyor belt, it’s crucial to focus on the maintenance and safety considerations that ensure the system’s longevity and protect the workers involved. This section highlights the importance of regular maintenance checks and outlines essential safety precautions during the installation and maintenance of conveyor belts.
Importance of Regular Maintenance Checks Post-Installation
Regular maintenance is vital for the optimal performance and durability of conveyor belts. Here are five specific examples of maintenance checks:
- Joint Integrity: Regularly inspect the integrity of the belt joints. Whether mechanical fasteners, vulcanized, or cold bonded, joints should be checked for signs of wear, damage, or loosening.
- Belt Alignment: Misalignment can lead to uneven wear, increased energy consumption, and potential damage. Ensure the belt runs centrally along the conveyor structure.
- Tension Checks: Incorrect tension can cause slippage or excessive wear. Regularly check and adjust the tension to manufacturer specifications.
- Surface Inspection: Inspect the belt surface for cuts, abrasions, or any material buildup that could affect the belt’s operation or cause conveyor belt damage.
- Pulley and Rollers: Check pulleys and rollers for proper rotation. Worn or seized rollers can damage the belt and affect the conveyor’s efficiency.
Safety Precautions During Installation and Maintenance
Safety is paramount during the installation and maintenance of conveyor belts. Here are five essential safety precautions:
- Lockout/Tagout (LOTO) Procedures: Always follow LOTO procedures before starting any installation or maintenance work to ensure the conveyor system is not accidentally powered on.
- Wear Appropriate PPE: Personal Protective Equipment (PPE) such as gloves, safety glasses, and steel-toed boots should be worn to protect against potential hazards.
- Use Proper Tools: Employ the correct tools and equipment for installation and maintenance tasks to prevent injuries and ensure the work is performed efficiently.
- Training: Ensure all personnel involved in the installation and maintenance of conveyor belts are properly trained in safe work practices and understand how to connect a conveyor belt safely.
- Emergency Stop Systems: Familiarize yourself with the location and operation of emergency stop systems on the conveyor, ensuring they are accessible and functional at all times.
By prioritizing regular maintenance checks and adhering to strict safety precautions, you can extend the life of your conveyor belt and safeguard the well-being of everyone involved in its operation. Understanding how to connect a conveyor belt is just the beginning; maintaining its integrity and ensuring safe practices are ongoing responsibilities that contribute to the system’s success.
How to Connect a Conveyor Belt: Selecting Expert Installers
The task of how to connect a conveyor belt requires precision, expertise, and experience. Choosing the right professionals for conveyor belt installation is crucial for ensuring the system’s efficiency, safety, and longevity. This section guides selecting a reputable conveyor belt installation company and highlights the significance of experienced professionals in executing efficient and safe conveyor belt installation jobs.
Choosing the Right Conveyor Belt Installation Company
When selecting a company to handle the installation of a conveyor belt, consider the following factors:
- Experience: Look for a company with a proven track record in installing conveyor belts similar to yours. Experienced professionals understand the nuances of how to connect a conveyor belt across various industries and applications.
- Reputation: Research the company’s reputation within the industry. Reviews, testimonials, and case studies can provide insight into their reliability and quality of work.
- Safety Record: A company’s commitment to safety is paramount. Inquire about their safety protocols and training, as well as their incident and accident history.
- Services Offered: Ensure the company offers a comprehensive range of services, from installation to maintenance and repair, to support the conveyor belt throughout its lifecycle.
- Technical Support: Post-installation support is crucial. The right professionals will offer ongoing technical support and emergency services to address any issues promptly.
Significance of Experienced Professionals
Experienced professionals bring invaluable benefits to conveyor belt installation jobs, including:
- Precision in Installation: They know precisely how to connect a conveyor belt, ensuring it is installed correctly to operate efficiently and last longer.
- Problem-Solving Skills: Experienced installers can anticipate and address potential issues before they become problematic, saving time and resources.
- Safety Assurance: With a deep understanding of safety standards and protocols, experienced professionals ensure the installation process is safe for everyone involved.
- Customized Solutions: They can provide customized installation solutions tailored to the specific needs of your operation, enhancing the system’s performance.
- Efficiency: Their expertise allows for the swift and efficient completion of installation projects, minimizing downtime and getting your conveyor system up and running faster.
Understanding how to connect conveyor belt is just one aspect of a successful conveyor system installation. The expertise of seasoned professionals is indispensable in ensuring the installation is performed efficiently, safely, and to the highest standards. By carefully selecting the right conveyor belt installation company, you can ensure your conveyor system operates smoothly and reliably for years to come.
Need durable and efficient belts? Contact us now!
FAQs About How to Connect a Conveyor Belt
Connecting a conveyor belt involves several steps to ensure a smooth, efficient, and safe operation. Initially, the conveyor system’s end pulleys must be aligned to maintain the belt’s straightness during operation. The belt ends are then cut to the desired length, ensuring they are straight and parallel to each other. Specialized tools are used to precisely measure and cut the belt material. After cutting, the belt ends are prepared for joining, which might involve skiving (thinning the ends) to make the joined area as flat as possible. The actual connection method depends on the belt type and application but often involves mechanical fastening, vulcanization, or cold bonding. Mechanical fasteners are quick to install and allow for easy disassembly, making them suitable for temporary or movable installations. Vulcanization and cold bonding provide a more permanent solution, offering a seamless and stronger bond that enhances the belt’s lifespan and performance.
Joining conveyor belts together is a critical process that can be achieved through various methods, depending on the belt type and application requirements. The three primary methods are:
Mechanical Fastening: This method uses metal or plastic fasteners to join the belt ends. It’s suitable for belts that require frequent removal or for applications where vulcanization is not feasible. Mechanical fastening is relatively easy and quick but may not be as smooth or durable as other methods.
Vulcanization: Vulcanization is a chemical process that uses heat and pressure to create a chemical bond between the belt ends. This method provides a very strong and smooth joint, making it ideal for high-strength and high-speed applications. However, it requires specialized equipment and skilled technicians.
Cold Bonding: Cold bonding uses adhesives to join the belt ends. This method is simpler and less expensive than vulcanization but requires precise application and curing times. The strength of the bond depends on the adhesive quality and the preparation of the belt ends.
Each method has its advantages and considerations, including the belt material, operational requirements, and environmental conditions.
The methods of joining conveyor belts include mechanical fastening, vulcanization, and cold bonding. Each method has its specific applications, advantages, and limitations.
Mechanical Fastening: Offers ease of installation and removal. Ideal for repairs or when vulcanization is not possible. However, it may introduce points of weakness or catch points for materials.
Vulcanization: Provides a seamless and strong bond that is ideal for high-speed and heavy-load applications. Requires specialized equipment and skilled labor, making it more costly and time-consuming.
Cold Bonding: A cost-effective and simpler alternative to vulcanization that uses adhesives to bond the belt ends. It requires careful surface preparation and curing time but is less durable than vulcanization.
Choosing the right joining method depends on the belt’s material, the operational environment, and the specific requirements of the conveyor system.
The connection used to connect a conveyor belt largely depends on the application, belt type, and operational requirements. Mechanical fasteners, vulcanization, and cold bonding are the most common methods.
Mechanical Fasteners are widely used for their ease of installation and the ability to quickly repair or adjust the belt. They are suitable for temporary setups or applications where belts need to be frequently removed or replaced.
Vulcanization is preferred for permanent installations where a strong, seamless bond is required. It is ideal for high-speed, high-load applications, offering superior durability and performance.
Cold Bonding is chosen for its simplicity and cost-effectiveness, suitable for applications where vulcanization is not practical or too expensive. It provides a good bond strength but may not be as durable as vulcanized joints.
Selecting the appropriate connection method is crucial for ensuring the conveyor belt’s optimal performance and longevity.
The ends of a belt conveyor are typically joined together using one of several methods, depending on the type of belt and the application:
Mechanical Fasteners: These are metal or plastic clips that physically attach the two ends of the belt. They are quick to install and ideal for temporary or emergency repairs but may cause some belt wear over time.
Vulcanization: This is a more permanent method where heat and pressure are used to bond the belt ends together, creating a strong, seamless joint. Vulcanization is preferred for heavy-duty applications and offers superior durability.
Cold Bonding: A chemical adhesive is used to bond the belt ends together. This method is less strong than vulcanization but easier to perform in the field.
Finger Splicing: The belt ends are cut into interlocking “fingers” and then bonded together, providing a smooth joint with minimal impact on belt performance.
Last Updated on August 20, 2024 by Jordan Smith
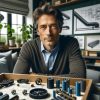
Jordan Smith, a seasoned professional with over 20 years of experience in the conveyor system industry. Jordan’s expertise lies in providing comprehensive solutions for conveyor rollers, belts, and accessories, catering to a wide range of industrial needs. From initial design and configuration to installation and meticulous troubleshooting, Jordan is adept at handling all aspects of conveyor system management. Whether you’re looking to upgrade your production line with efficient conveyor belts, require custom conveyor rollers for specific operations, or need expert advice on selecting the right conveyor accessories for your facility, Jordan is your reliable consultant. For any inquiries or assistance with conveyor system optimization, Jordan is available to share his wealth of knowledge and experience. Feel free to reach out at any time for professional guidance on all matters related to conveyor rollers, belts, and accessories.