Steps and Tips on How to Design Belt Conveyor
Belt conveyors play a pivotal role in various industries, including mining, manufacturing, and logistics, by efficiently transporting materials over long distances. Understanding how to design belt conveyor systems is essential for optimizing operational efficiency and productivity. A well-designed belt conveyor ensures seamless integration with other machinery and processes, minimizing downtime and maintenance costs. The necessity for custom design arises from the diverse requirements of different operations, such as varying material types, load capacities, and environmental conditions. Tailoring the design to specific needs enhances performance, safety, and longevity of the conveyor system. This guide provides a comprehensive overview of the fundamental principles and best practices in how to design belt conveyor systems.
How to Design Belt Conveyor System Overview
Designing a belt conveyor system involves understanding the essential components and their roles in the overall functionality of the system. Each component, from electric drives to pulleys and idlers, plays a critical role in ensuring efficient and reliable operation.
What is a Belt Conveyor?
A belt conveyor is a material handling system that uses a continuous belt to transport materials from one point to another. Belt conveyors are widely used in various industries due to their efficiency, reliability, and versatility. Here are five examples highlighting their importance in different sectors:
- Mining Industry: Belt conveyors are used to transport raw materials such as coal, ores, and aggregates from extraction points to processing plants. They handle large volumes and long distances efficiently, reducing the need for manual labor and vehicles.
- Manufacturing Industry: In manufacturing plants, belt conveyors move products and components between different stages of production. They streamline processes, reduce handling times, and improve overall productivity.
- Agriculture: Belt conveyors are used to transport harvested crops, seeds, and fertilizers. They are essential in sorting, packaging, and loading operations, ensuring smooth and efficient agricultural processes.
- Food Industry: In food processing and packaging plants, belt conveyors transport raw materials, processed foods, and packaged goods. They maintain hygiene and efficiency, minimizing manual handling and contamination risks.
- Logistics and Warehousing: Belt conveyors play a critical role in the logistics and warehousing sector. They are used for sorting, packing, and transporting goods within distribution centers, improving order fulfillment and reducing lead times.
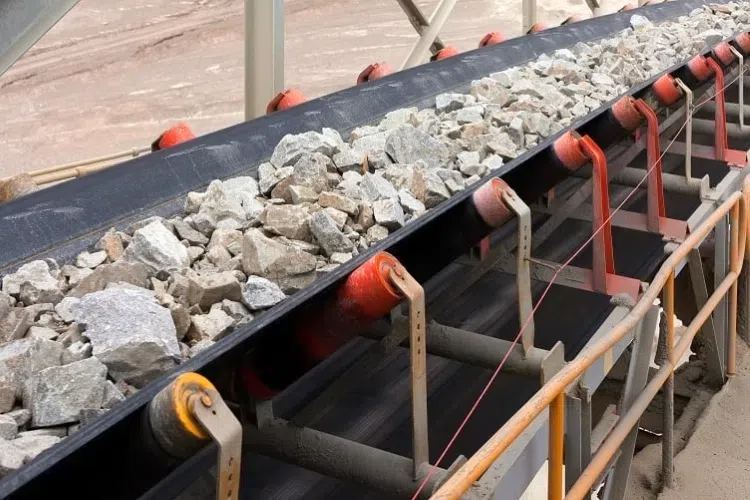
Belt Conveyor System Definition and Components
A belt conveyor system is an apparatus designed to transport materials from one point to another along a continuous belt. The key components of a belt conveyor system include:
- Electric Drives: These are the motors that power the conveyor belt, ensuring it moves at the required speed. They convert electrical energy into mechanical energy, driving the belt forward.
- Pulleys: Pulleys are the wheels over which the conveyor belt is looped. They serve as the driving force, guiding the belt’s movement and maintaining tension. There are two main types of pulleys: head pulleys (drive pulleys) that pull the belt and tail pulleys that provide tension.
- Idlers: These are rollers placed at intervals along the conveyor’s length to support the belt and its load. Idlers reduce friction and wear, ensuring smooth operation.
- Conveyor Belt: The conveyor belt is the continuous loop on which materials are transported. It is typically made of rubber or synthetic materials and comes in various widths and strengths to suit different applications.
- Frames and Structure: The frames provide support and stability to the entire system. They ensure the alignment and proper functioning of all components.
The Role of Each Component
Each component is crucial in how to design belt conveyor systems:
- Electric Drives: Determine the speed and efficiency of the conveyor system. Proper selection of the motor is vital for energy efficiency and longevity.
- Pulleys: Ensure that the belt runs smoothly and maintains proper tension. Incorrect pulley size or placement can lead to slippage and increased wear.
- Idlers: Support the belt and its load, minimizing friction and wear. Proper spacing and alignment of idlers are essential to prevent belt sagging and misalignment.
- Conveyor Belt: The heart of the system, transporting materials efficiently. The belt’s material and design must match the specific requirements of the transported material, such as weight, abrasiveness, and temperature resistance.
- Frames and Structure: Provide the necessary support for all components. Robust construction and precise alignment are crucial for system stability and performance.
Understanding how to design belt conveyor systems involves a detailed knowledge of these components and their roles. By ensuring each part is appropriately selected and integrated, the overall system can achieve optimal performance and reliability. This chapter provides the foundational knowledge needed to begin the design process, setting the stage for more advanced topics in subsequent sections.
The Process of How to Design Belt Conveyor
Designing a belt conveyor system involves several critical steps that ensure the final product meets specific operational requirements. Here, we outline a comprehensive step-by-step guide on how to design belt conveyor systems.
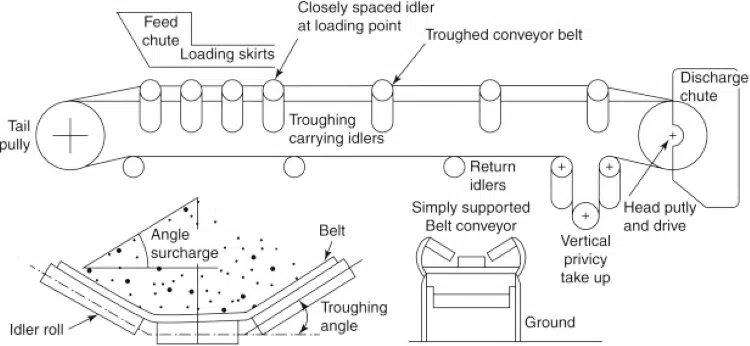
Assessing Material Handling Requirements
The first step in how to design belt conveyor systems is to assess the material handling requirements. This involves understanding the nature of the materials being transported, including their size, weight, temperature, abrasiveness, and any special handling needs. Key considerations include:
- Material Characteristics: Knowing the type of material (bulk, granular, etc.), conveyor belts density, and flowability.
- Throughput Requirements: Determining the volume of material to be moved per hour.
- Environmental Conditions: Considering factors such as temperature, humidity, and exposure to chemicals or outdoor elements.
Selection of Conveyor Type Based on Material and Application
Based on the material handling requirements, the next step in how to design belt conveyor systems is selecting the appropriate conveyor type. Different materials and applications may require specific conveyor designs, such as:
- Flat Belt Conveyors: Ideal for general-purpose material handling.
- Incline/Decline Belt Conveyors: Used when materials need to be moved to different heights.
- Cleated Belt Conveyors: Suitable for transporting loose or granular materials at steep angles.
- Sanitary Belt Conveyors: Designed for food or pharmaceutical applications requiring high levels of hygiene.
Determination of Conveyor Length and Incline
Determining the appropriate length and incline of the conveyor is crucial in how to design belt conveyor systems. This step involves:
- Conveyor Length: Measuring the distance between the loading and unloading points. It’s important to account for any obstacles or changes in direction.
- Incline/Decline: Calculating the angle of incline or decline needed for the conveyor. Steeper inclines may require special belts or additional power to move materials effectively.
Calculation of Belt Tension and Selection of Belt Material
Calculating the belt tension and selecting the appropriate belt material are essential steps in how to design belt conveyor systems. This involves:
- Belt Tension Calculation: Determining the forces acting on the belt, including the weight of the materials, the friction between the belt and the idlers, and any additional forces from inclines or declines.
- Belt Material Selection: Choosing a belt material that can withstand the operational conditions. Options include rubber, PVC, and metal, each with specific advantages depending on the application.
Belt Conveyor Design Calculations
Accurate calculations are fundamental to how to design belt conveyor systems. These calculations ensure that the conveyor operates efficiently and safely. Key calculations include tension, power requirements, and motor sizing.
- Tension Calculations
Tension calculations involve determining the force needed to move the conveyor belt and the load it carries. Essential variables include:
- Load Due to Idlers (mi): The load imposed by the idlers on the belt.
- Belt Weight (mb): The weight of the belt itself.
- Material Load (mm): The weight of the material being transported.
The total tension (T) is calculated using the formula:
[ T = (mi + mb + mm) × g ×cos(θ) ]
where ( g ) is the acceleration due to gravity and ( \theta ) is the angle of incline.
- Power Requirements
Calculating the power requirements involves determining the amount of power needed to drive the conveyor. This includes considering the friction between the belt and the idlers, the weight of the belt, and the material load. The power at the drive pulley (Pp) is calculated using the formula:
[ Pp = T × v ]
where ( T ) is the total tension and ( v ) is the belt speed.
- Motor Sizing
Motor sizing ensures that the selected motor can handle the power requirements of the conveyor. This involves selecting a motor with the appropriate horsepower (HP) and torque to drive the conveyor efficiently.
By following these detailed steps and calculations, you can ensure that your belt conveyor system is designed to meet specific operational requirements. Proper design not only enhances the efficiency and reliability of the conveyor system but also extends its lifespan, providing long-term value and performance.
This chapter provides a comprehensive overview of the critical steps involved in how to design belt conveyor systems, setting the foundation for more advanced topics and considerations in subsequent chapters.
How to Design Belt Conveyor Parts and Their Functions
Designing a belt conveyor system requires a deep understanding of its individual components and their specific functions. Each part plays a crucial role in ensuring the efficient and reliable operation of the system. In this section, we will explore the main components involved in how to design belt conveyor systems and their significance.
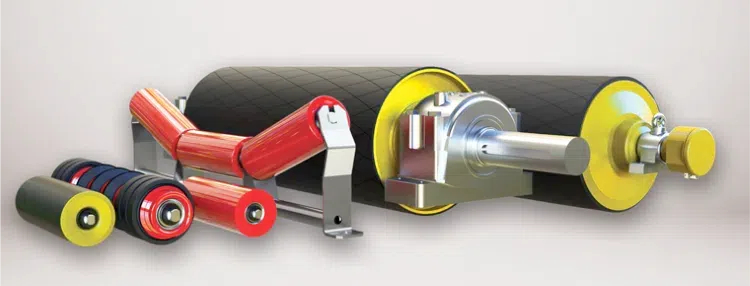
Deep Dive into the Parts
The head pulley, also known as the drive pulley, is typically located at the discharge end of the conveyor. It is driven by an electric motor and is responsible for moving the belt and the materials on it. The tail pulley conveyor, located at the loading end, maintains the necessary tension in the belt. Together, these pulleys ensure smooth operation and help prevent belt slippage.
- Idler Rollers
Idler rollers support the conveyor belt and the load it carries. They are strategically placed along the length of the conveyor to minimize sagging and reduce friction. Idlers come in various configurations, including troughing idlers, return idlers, and impact idlers, each serving a specific purpose.
- Conveyor Frame
The conveyor frame provides the structural support for the entire system. It ensures that all components are aligned and securely held in place. The frame must be robust enough to withstand the operational stresses and environmental conditions.
- Belt
The belt is the core component that carries the materials. It must be selected based on the specific requirements of the application, such as load capacity, material type, and environmental conditions. Belts can be made from various materials, including rubber, PVC, and metal.
- Drive System
The drive system, typically comprising an electric motor, gearbox, and coupling, provides the necessary power to move the belt. The drive system must be carefully matched to the conveyor’s operational requirements to ensure efficient performance.
The Significance of Each Part in Ensuring Efficient Operation
Understanding the role of each component is crucial in how to design belt conveyor systems. Each part must be correctly specified and integrated to achieve optimal performance. For instance, selecting the right idler roller configuration can reduce maintenance costs and extend the lifespan of the belt. Similarly, a well-designed drive system can enhance energy efficiency and minimize operational disruptions.
Utilization of Belt Conveyor Diagrams to Illustrate Components and Assembly
Visual aids are invaluable in understanding how to design belt conveyor systems. Diagrams can clearly illustrate the placement and interaction of each component, aiding in both the design and assembly processes.
- Component Layout
Diagrams showing the layout of components such as head and tail pulleys, idler rollers, and the conveyor frame provide a visual representation of the system. This helps in planning the installation and ensuring that all parts are correctly positioned.
- Assembly Instructions
Step-by-step diagrams detailing the assembly process are crucial for ensuring that the conveyor is built correctly. These diagrams can show the sequence of installing components, the tools required, and any specific alignment procedures.
Visual Aids to Complement Step-by-Step Design Instructions
Incorporating visual aids such as exploded views, cross-sectional diagrams, and 3D models can significantly enhance the understanding of how to design belt conveyor systems. These tools provide a clearer perspective on the internal workings and interactions of components.
By thoroughly understanding the detailed components and their functions, and utilizing clear diagrammatic representations, you can effectively design belt conveyor systems that are efficient, reliable, and tailored to specific operational needs. This chapter provides the foundational knowledge necessary for making informed design decisions and ensuring successful implementation.
How to Design Belt Conveyor: Material and Application
When learning how to design belt conveyor systems, it is crucial to consider the specific materials being transported and the application context. Different materials and applications can significantly impact design choices, influencing the selection of conveyor belt types, components, and overall system configuration.
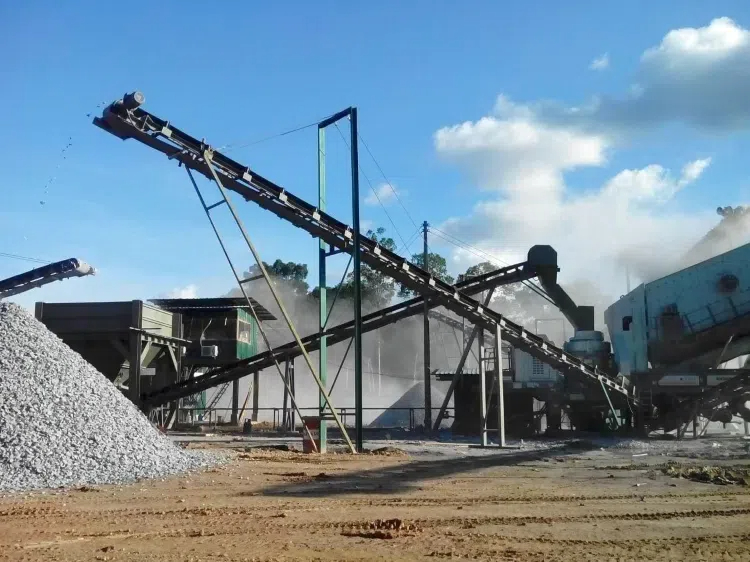
Discussing How Different Materials and Applications Affect Design Choices
Material Type and Characteristics
The type of material being transported is a primary consideration in how to design belt conveyor systems. Materials can range from fine powders to large, heavy objects, and each type presents unique challenges:
- Granular and Powdered Materials: These materials, such as sand, grain, or cement, require belts with features to prevent leakage and dust generation. Cleated belts or sidewalls can be added to contain the material.
- Large and Heavy Objects: Items like rocks, metals, or machinery parts need robust belts with high tensile strength and impact resistance to withstand the load and potential impacts.
- Delicate or Perishable Goods: Food items, electronics, or fragile products require gentle handling. Belts with smooth surfaces and soft materials can minimize damage and contamination.
Application Context
The application context further influences design decisions in how to design belt conveyor systems:
- Inclined or Declined Conveying: If the conveyor must move materials up or down, the belt must have adequate grip and strength. Inclined applications might require cleated belts or specially textured surfaces to prevent slippage.
- High-Temperature Environments: In industries like metal forging or glass manufacturing, conveyors may operate in high-temperature environments. Heat-resistant belts made from materials like silicone or Teflon are necessary to maintain performance and longevity.
- Chemical Exposure: In chemical processing or pharmaceutical industries, belts may come into contact with harsh chemicals. Chemical-resistant materials like PVC or stainless steel are essential to prevent degradation and ensure safety.
The Impact of Material Characteristics on Conveyor Belt Selection and Design Parameters
Material characteristics directly affect conveyor belt selection and the design parameters. Understanding the specific needs of the materials ensures the belt conveyor system operates efficiently and safely.
- Abrasiveness: Materials that are highly abrasive require belts with high wear resistance. Rubber belts with reinforced surfaces can withstand the constant friction without significant wear.
- Moisture Content: Materials with high moisture content, like wet clay or agricultural products, need belts with drainage features to prevent water accumulation and ensure smooth operation.
- Temperature Sensitivity: Materials that are sensitive to temperature changes, such as certain chemicals or food products, require belts that can maintain consistent temperatures. Insulated or temperature-controlled belts may be necessary.
Design Documentation
Importance of Creating a Comprehensive Belt Conveyor Design Handbook PDF
Creating a comprehensive belt conveyor design handbook PDF is essential for ensuring that all aspects of the design process are thoroughly documented and easily accessible. This handbook serves as a valuable reference for designers, engineers, and maintenance personnel, providing detailed information on system specifications, design calculations, and best practices.
- Centralized Information Source
A design handbook consolidates all relevant information into a single document, making it easier to reference and share. It ensures that everyone involved in the project has access to consistent and accurate data, reducing the risk of errors and misunderstandings.
- Standardization and Best Practices
By documenting standard procedures and best practices, the handbook promotes consistency and efficiency in how to design belt conveyor systems. It serves as a training tool for new team members and a guide for maintaining quality across different projects.
Guidelines for Documenting Belt Conveyor Design Calculations PDF for Future Reference
Documenting belt conveyor design calculations in a PDF format is crucial for future reference and ongoing maintenance. Accurate records of design calculations help ensure that the system operates as intended and provides a basis for troubleshooting and modifications.
- Detailed Calculation Records
Every design calculation should be meticulously recorded, including the formulas used, input values, and results. This detailed documentation allows engineers to verify the accuracy of the calculations and make informed decisions when adjustments are needed.
- Clear and Organized Format
The design calculations PDF should be organized logically, with sections for different types of calculations (e.g., tension, power requirements, motor sizing). Clear headings and a table of contents enhance usability, making it easy to find specific information.
- Visual Aids and Diagrams
Including visual aids and diagrams in the design calculations PDF can help illustrate complex concepts and provide additional context. Diagrams showing component layouts, force distributions, and other relevant details can enhance understanding and support accurate calculations.
- Version Control and Updates
Maintaining version control is essential for keeping the design documentation up to date. Any changes to the system or new calculations should be documented with the date and description of the updates. This ensures that the documentation reflects the current state of the system and provides a reliable reference for future projects.
By considering the specific materials and application contexts and maintaining thorough documentation, you can effectively design belt conveyor systems that are efficient, reliable, and tailored to meet operational needs. This chapter highlights the critical considerations and best practices in how to design belt conveyor systems, ensuring successful implementation and long-term performance.
How to Design Belt Conveyor: Common Design Challenges and Solutions
When learning how to design belt conveyor systems, encountering design challenges is inevitable. Addressing these challenges effectively ensures optimal performance and longevity. Here, we discuss common design issues and provide solutions to resolve them, along with optimization tips.
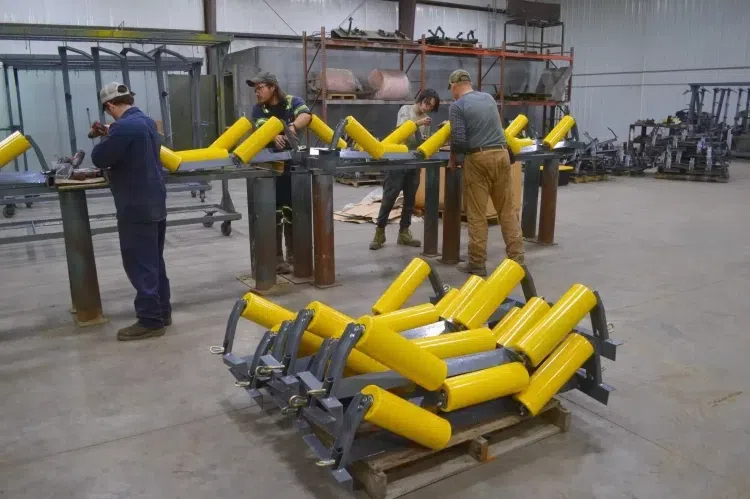
Belt Misalignment
One of the most common issues in how to design belt conveyor systems is belt misalignment. This occurs when the belt deviates from its intended path, leading to increased wear and potential damage.
- Solution: Regularly inspect and adjust the alignment of pulleys and idlers. Implement tracking devices and use self-aligning idlers to keep the belt on track. Properly tensioning the belt is also crucial to prevent misalignment.
Belt Slippage
Belt slippage occurs when the conveyor belt drive pulley cannot grip the belt adequately, causing the belt to slip and reducing efficiency.
- Solution: Increase the tension of the belt to enhance the grip on the drive pulley. Use lagging on pulleys to improve friction. Ensure the belt and pulleys are clean and free from contaminants that could reduce traction.
Material Spillage
Material spillage can result from overloading the belt or improper belt selection, leading to material loss and potential safety hazards.
- Solution: Select the appropriate belt width and type based on material characteristics and load requirements. Install skirt boards and conveyor sealing systems to contain the material on the belt. Regularly monitor and adjust loading and unloading points to prevent overloading.
Excessive Wear
Excessive wear on the belt and components can be caused by abrasive materials or improper tensioning, leading to reduced lifespan and increased maintenance costs.
- Solution: Choose belts made from wear-resistant materials for handling abrasive substances. Ensure proper tensioning to minimize unnecessary wear. Implement regular maintenance schedules to inspect and replace worn components promptly.
Inefficient Power Usage
Inefficient power usage can result from incorrect motor sizing or excessive friction within the system, leading to higher operational costs.
- Solution: Accurately calculate power requirements based on load and operational conditions. Use energy-efficient motors and drives. Regularly lubricate moving parts and reduce friction by maintaining proper alignment and tension.
Optimization Tips for Enhancing Conveyor Efficiency and Longevity
- Preventive Maintenance: Establish a regular maintenance schedule to inspect and service all components, ensuring early detection and resolution of potential issues.
- Real-Time Monitoring: Implement real-time monitoring systems to track the performance and condition of the conveyor. This enables proactive maintenance and reduces downtime.
- Energy Efficiency: Optimize the drive system for energy efficiency by using variable frequency drives (VFDs) to control motor speed and reduce energy consumption.
- Load Management: Avoid overloading the conveyor by carefully managing load distribution and ensuring that the system operates within its design capacity.
- Training: Provide thorough training for operators and maintenance personnel on how to design belt conveyor systems and handle common issues effectively.
FAQs About How to Design Belt Conveyor
Designing a belt conveyor system involves several critical steps to ensure efficiency and reliability. The process begins with assessing the material handling requirements, which include understanding the type and characteristics of the materials being transported. Next, select the appropriate conveyor type based on these requirements and the application context. This involves deciding on factors such as belt width, length, and speed. Calculations for belt tension, power requirements, and motor sizing are essential to ensure the system can handle the load and operate efficiently. Additionally, consider the environmental conditions, such as temperature and exposure to chemicals, to select suitable materials for the belt and components. Proper alignment and tensioning of the belt, along with regular maintenance, are crucial to prevent issues like misalignment and slippage. By following these steps and considering all relevant factors, you can design a belt conveyor system that meets your specific operational needs.
The basic conveyor belt design consists of several key components that work together to transport materials from one point to another. These components include the conveyor belt itself, which is typically made of rubber, PVC, or other durable materials. The belt is looped around pulleys, which drive and guide the belt’s movement. The head pulley, located at the discharge end, is powered by an electric motor and is responsible for moving the belt. The tail pulley, located at the loading end, maintains tension in the belt. Idler rollers are placed at intervals along the conveyor’s length to support the belt and its load, reducing friction and wear. The conveyor frame provides the structural support for the entire system, ensuring all components are aligned and securely held in place. Understanding these basic components is essential for designing and maintaining an efficient belt conveyor system.
Calculating the specifications for a conveyor belt involves determining several key parameters to ensure the system operates efficiently. The primary calculations include determining the belt tension, power requirements, and motor sizing. Belt tension is calculated by considering the load due to the materials, the weight of the belt, and the friction between the belt and the idlers. The formula for calculating total tension (T) is:T=(mi+mb+mm)×g×cos(θ)
where mi is the load due to idlers, mb is the belt weight, mm is the material load, 𝑔 is the acceleration due to gravity, and 𝜃 is the angle of incline. Power requirements are calculated by determining the force needed to move the belt and load at the desired speed. The power at the drive pulley (Pp) is given by:Pp=T×vwhere 𝑇 is the total tension and 𝑣 is the belt speed. Accurate calculations ensure that the conveyor operates smoothly and efficiently, preventing issues like slippage and excessive wear.
Sizing a conveyor belt involves determining the appropriate belt width, length, and thickness based on the material handling requirements. The width of the belt should be sufficient to accommodate the materials being transported without spillage. Typically, the belt width is selected based on the largest material size and the desired throughput. The length of the conveyor belt is determined by the distance between the loading and unloading points, plus any additional length required for inclines or curves. The belt thickness is selected based on the weight and abrasiveness of the materials, ensuring durability and resistance to wear. Additionally, consider the conveyor speed, which should be matched to the application’s requirements to balance efficiency and material flow. Properly sizing the conveyor belt is crucial to ensure it can handle the load and operate efficiently without excessive wear or maintenance issues.
Last Updated on June 21, 2024 by Jordan Smith
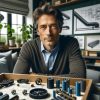
Jordan Smith, a seasoned professional with over 20 years of experience in the conveyor system industry. Jordan’s expertise lies in providing comprehensive solutions for conveyor rollers, belts, and accessories, catering to a wide range of industrial needs. From initial design and configuration to installation and meticulous troubleshooting, Jordan is adept at handling all aspects of conveyor system management. Whether you’re looking to upgrade your production line with efficient conveyor belts, require custom conveyor rollers for specific operations, or need expert advice on selecting the right conveyor accessories for your facility, Jordan is your reliable consultant. For any inquiries or assistance with conveyor system optimization, Jordan is available to share his wealth of knowledge and experience. Feel free to reach out at any time for professional guidance on all matters related to conveyor rollers, belts, and accessories.