Essential Guide: How to Roll Steel Without a Roller
Rolling steel without specialized equipment like rollers can be a challenging task, requiring ingenuity and precision. However, understanding how to roll steel without a roller is crucial for many DIY enthusiasts and professionals. Rolled steel and sheet metal play versatile roles in countless projects, from ductwork to structural components, making them indispensable. Whether it’s crafting a sleek cylindrical shape or simply creating gentle curves, achieving these shapes without a roller demands creative alternative methods. In this guide, you’ll learn practical techniques to shape steel by hand, setting realistic expectations for bending and curving steel sheets using basic tools, while still obtaining precise, functional results for your projects.
To Understand How to Roll Steel Without a Roller: Sheet Metal Rolling Basics
When approaching the task of how to roll steel without a roller, it’s vital to grasp the core concepts of sheet metal manipulation. This section will clarify the distinctions between rolling and bending and detail the essential factors that influence the shaping of metal.
Difference Between Rolling and Bending
Rolling and bending, though often used interchangeably, involve distinct processes:
Objectives When Rolling or Curving Sheet Metal
When considering how to roll steel without a roller, achieving precision and functionality in the finished product is crucial. The common objectives include:
- Uniformity in Shape: Ensuring the metal sheet forms into a consistent and uniform cylindrical shape without irregularities.
- Aesthetic Appeal: Achieving smooth curves that are visually pleasing, especially important in decorative and architectural applications.
- Structural Integrity: Maintaining the strength of the metal throughout the curve to ensure it can withstand intended uses.
- Precision in Dimensions: Achieving exact measurements as specified for fitting into assemblies or as standalone pieces.
- Efficiency in Production: Minimizing waste and maximizing speed in shaping processes, even without specialized machinery.
- Minimization of Material Stress: Avoiding cracks or splits from overstressing the metal during the bending process.
- Adaptability: Allowing the metal to be reshaped if necessary, without significant degradation of material.
- Cost-effectiveness: Reducing costs associated with processing while still achieving the desired form and function.
Importance of Material and Thickness Considerations
The choice of material and its thickness are critical when exploring how to roll steel without a roller:
- Material Type: Different metals like steel, aluminum, and copper behave differently under stress and require specific techniques for effective rolling.
- Grain Direction: Metal sheets have grains that can influence the bending process; understanding these can help in achieving cleaner bends.
- Thickness (Gauge): Thicker materials are harder to bend by hand and may require additional force or heat.
- Ductility and Malleability: Materials that are more ductile are easier to roll into cylindrical shapes without breaking.
- Springback: Metals tend to return slightly toward their original shape after bending, which must be compensated for in the design.
- Surface Finish: The surface treatment of the metal can affect its ability to be rolled smoothly without damage.
- Size and Scale: Larger sheets like 4×8 metal sheets pose additional challenges in handling and evenness in rolling.
- Tool Compatibility: Ensuring the tools and methods chosen are suitable for the type and thickness of the metal to avoid damage and ensure effective shaping.
By understanding these basics, you can better navigate the complexities of how to roll steel without a roller and achieve professional-grade results even with limited resources.
Essential Tools and Materials for How to Roll Steel Without a Roller
Understanding the proper tools and materials is crucial when you’re learning how to roll steel without a roller. Each material and tool plays a specific role in enabling you to manually shape steel or aluminum into desired forms. Here, we outline the key materials and tools required for effective hand rolling, ensuring both safety and precision in your projects.
Materials
The choice of material significantly affects the ease and quality of the rolling process. Different types of metals, such as steel or aluminum, offer varying degrees of flexibility and strength, impacting how they can be manipulated without mechanical rollers. It’s important to select the right material based on the specific requirements of your project, whether it involves heavy-duty structural applications or lighter, more decorative tasks.
- Steel Sheets: High-strength steel sheets offer durability and are often chosen for structural projects where strength is key.
- Aluminum Sheets: Lightweight and corrosion-resistant, aluminum sheets are easier to bend by hand, ideal for non-structural or decorative uses.
- 4×8 Sheets: Standard 4×8 sheets are commonly available and can be cut down or used whole, providing ample material for large or small projects.
- Sheet Metal Scraps: Useful for testing angles and rolling techniques before working on full-sized sheets.
- Protective Gear: Safety gloves, eye protection, and protective clothing help prevent injuries during bending.
Tools
The right set of tools is essential for successfully bending metal sheets without the use of rollers. Each tool serves a specific purpose in the process, from measuring and marking to physically manipulating the metal. Ensuring you have the appropriate tools ready can make the difference between a project that is feasible by hand and one that requires additional mechanical assistance.
- Wooden or Metal Form Blocks: Form blocks provide the foundational shape around which the steel is bent. Wooden blocks are gentler on the metal, while metal blocks are stronger for tough bends.
- Hardwood Block and Hammer/Mallet: Hardwood blocks are used in conjunction with a hammer or mallet to gently bend the metal around the form blocks. Rawhide or rubber mallets are preferred for delicate work.
- Tape Measure, Ruler, and Protractor: These measuring tools are essential for accurately marking bend lines and calculating angles.
- Marker for Drawing Bend Lines: Use a permanent marker to mark the bend lines clearly on the steel surface, as shown in the conveyor roller drawing, ensuring accuracy in the bending process.
- Vise: A heavy-duty vise securely holds the steel sheet in place while bending, keeping the metal steady for more consistent curves.
- Clamps: Clamps further stabilize the metal on the form block, especially for larger sheets that might otherwise shift.
- Bend Allowance Calculator: Handy for calculating the additional length needed to create precise bends without distortion.
- Blowtorch: Applying heat with a blowtorch can help ease the bending of thicker sheets, making it easier to manipulate without a roller.
By fully understanding and utilizing these materials and tools, you’ll be better equipped to handle the challenge of how to roll steel without a roller, achieving professional results with basic equipment.
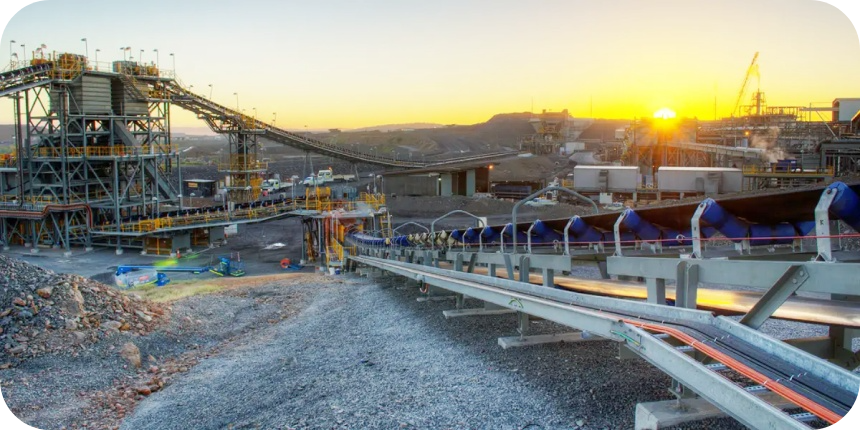
Step-by-Step Guide to Hand-Rolling Steel Sheets: How to Roll Steel Without a Roller
When you need to manipulate sheet metal but don’t have access to a roller, following a clear, step-by-step guide can help you achieve precise results with basic tools. This guide will explain how to roll steel without a roller by manually shaping the steel into desired forms using simple hand tools.
Measure and Cut the Sheet
- Start by using a tape measure or a ruler to carefully measure and mark the steel or aluminum sheet according to the project specifications. Accurate measurements are crucial for ensuring the final piece fits your design requirements.
- Using appropriate cutting tools like metal shears or a nibbler, cut the metal to the desired dimensions. Remember to leave a little extra on the edges for final trimming and adjustments.
Mark Bend Lines
- Use a protractor to determine the exact angles at which you’ll need to bend the sheet. A marker should then be used to draw these bend lines directly onto the metal. This step is vital for guiding the subsequent bending process and ensuring the bends occur at the correct locations.
- Double-check the measurements between bend lines to ensure they match your design plans, as this will influence the uniformity and symmetry of the final product.
Secure Metal with Form Blocks and Vise
- Position the form blocks so that they align with the bend lines you’ve marked. Form blocks should reflect the internal radius and angle you wish to achieve.
- Clamp the sheet metal in a sturdy vise, ensuring that the metal is held firmly against the form blocks. The setup should prevent the metal from moving during the bending process, providing stability.
Begin Bending
- Using a hammer or mallet, start gently tapping along the bend lines. Begin with light taps to gradually start forming the bend, focusing on maintaining even pressure across the line.
- As the metal begins to conform to the shape of the form block, you may increase the force of your taps slightly. Continuously check that the bend follows the curve of the form block and adjust your force accordingly.
Check the Shape
- After making the initial bends, periodically release the metal from the vise to check the shape of the curve or cylinder. This step is crucial to ensure that the metal is shaping as intended and to correct any deviations early on.
- If adjustments are needed, re-secure the metal in the vise and continue to bend or tap until the desired curvature is achieved. This iterative process allows for fine-tuning the shape to precise specifications.
By following these steps, you can successfully bend and shape steel or aluminum sheets into cylindrical or curved shapes without a roller, using straightforward hand tools and techniques.
Tips and Troubleshooting: How to Roll Steel Without a Roller
Rolling steel without a roller presents unique challenges that require a strategic approach. Even with proper planning and the right tools, it’s essential to anticipate potential difficulties to minimize errors and achieve the desired results. The following tips and troubleshooting advice will guide you in handling common issues that arise during hand rolling, such as inaccurate bends, improper securing of materials, and uneven pressure application. By understanding these key points, you can confidently approach the process and refine your technique in how to roll steel without a roller.
- Heat Application: For particularly thick sheets, apply heat cautiously with a blowtorch to soften the steel, making it easier to bend manually. Be careful not to overheat, as this can warp or damage the metal.
- Vise Security: Ensure the vise is firmly bolted to your workbench or another sturdy surface. If it shifts or loosens, it will lead to inaccurate bends or, worse, damage to the metal or your tools.
- Precision Bending: Double-check your angles with a protractor to guarantee the complementary angles are accurate. An error of even a few degrees could affect the entire curvature, leading to an inconsistent result.
- Gradual Force Application: Apply bending force gradually and consistently across the bend line. Quick or uneven force may result in cracked or uneven bends that require restarting the process.
- Support Excess Material: Support any material extending from the vise or form blocks with clamps or your hands to prevent it from bending due to gravity.
- Test on Scrap Metal: Before bending your final piece, practice on a scrap metal piece to perfect the bending technique, ensure the accuracy of your tools, and refine the measurements.
- Use Protective Gear: Wearing safety gloves, goggles, and sturdy clothing will protect you from sharp edges, sparks from heating, and other potential hazards during the bending process.
- Maintain a Steady Workspace: Ensure that your workspace is level and free from obstructions that could interfere with your bending. A smooth, controlled process leads to consistent results.
- Check Bend Allowance Calculations: If your bends don’t align with your intended dimensions, verify the bend allowance calculations to ensure that the metal isn’t too short or long at the bends.
With these tips and troubleshooting techniques, you can refine your skills and achieve quality results while learning how to roll steel without a roller.
Alternative Methods and Considerations: How to Roll Steel Without a Roller
When traditional rolling equipment is unavailable, exploring alternative methods and considerations can not only provide viable solutions but also enhance your metalworking flexibility. This approach is especially useful when you’re tackling projects where precision and efficiency are paramount, yet you lack access to specialized equipment. Delving into tools like slip rollers and engaging professional rolling services can significantly boost the quality and scope of your projects. By understanding and utilizing these alternatives, you can continue to learn and apply effective techniques in how to roll steel without a roller, ensuring that your lack of traditional equipment doesn’t limit your creativity or the scale of your work.
Slip Roller
Using a slip roller represents a practical alternative to traditional rolling methods, especially when precise, consistent cylindrical shapes are needed. Slip rollers are versatile machines designed to form sheet metal into curved panels or cylinders. They are particularly useful for small to medium projects where precision is critical but a full-sized roller is not feasible.
- Uniformity and Control: Slip rollers allow for adjustable settings to control the radius of the curve, enabling uniformity across multiple pieces.
- Adaptability: They can be adjusted to accommodate different widths and thicknesses of metal, making them highly adaptable for various projects.
- Reduction in Labor: The mechanical advantage provided by slip rollers reduces the physical effort required compared to manual methods.
- Enhanced Safety: By mechanizing the bending process, slip rollers minimize the risks associated with manual handling of sharp metals.
- Consistency: This equipment is designed to produce consistent results, which is particularly beneficial for repetitive tasks.
- Time Efficiency: Slip rollers speed up the process, enabling quicker completion of projects compared to manual rolling.
- Space-Efficient: Unlike larger industrial rollers, slip rollers are more compact and can fit into smaller workshops or garages.
- Skill Level Adjustment: They require less technical skill to operate than more complex rolling machinery, making them accessible to hobbyists and professionals alike.
Rolling Services
When the project demands surpass the capabilities of your available tools, turning to professional rolling services can be an excellent decision. Professional rolling services offer access to high-end equipment and expertise, ensuring top-notch results for projects that require precise metal forming. These services are ideal for large-scale or complex projects where professional quality is essential.
- Access to Advanced Techniques: Professional services often use state-of-the-art techniques and machinery, offering capabilities that go beyond basic rolling.
- High Precision: The precision achievable by professional rollers can significantly impact the structural integrity and appearance of the final product.
- Custom Projects: They can handle custom specifications that require detailed attention and specialized skills.
- Efficiency at Scale: For large batches or particularly large pieces, professional services can handle the volume efficiently, saving you time and resources.
- Resource Management: Utilizing a service helps manage resources better by focusing your efforts on other aspects of the project while experts handle the rolling.
- Risk Mitigation: By relying on professionals, you reduce the risk of errors and material waste that can occur with less experienced handling.
- Enhanced Capabilities: They can often work with a broader range of materials and sheet sizes, providing more options for your projects.
- Project Consultation: Most services provide expert consultation, offering advice on the best materials and approaches for specific applications.
By considering slip rollers for smaller, precise tasks and engaging professional rolling services for larger or more complex projects, you can effectively learn how to roll steel without a roller. These alternatives ensure that your projects remain on track, meeting both quality standards and deadlines, thus overcoming the limitations posed by the absence of traditional rolling equipment.
Fill out the form for pricing and details on our conveyor rollers.
FAQs about How to Roll Steel Without a Roller
How do you curve sheet metal by hand?
Curving sheet metal by hand is a practical skill in metalworking, especially useful when you do not have access to specialized machinery. The process involves using a combination of manual force and tools to create desired curves. Firstly, you need to clearly mark the line where you intend to curve the metal using a marker and a ruler or a template for consistency.
The simplest method to curve sheet metal by hand is to use a mallet and a form block. Place the metal sheet over a sturdy, curved form block that matches the desired curvature. Secure the sheet in place using clamps if necessary to prevent it from moving. Starting from one end, gently tap the metal along the marked line with a rubber or wooden mallet. Work your way along the line gradually, applying even pressure with each tap to bend the metal around the block. Frequently check the progress and adjust the force accordingly to avoid over-bending or creating sharp bends, which could weaken the metal. Safety gloves and eye protection are recommended to protect from sharp edges and flying debris.
Rolling steel is a metal forming process that involves passing the metal through one or more pairs of rolls to reduce its thickness and to make the thickness uniform. This process is typically performed in industrial environments using heavy-duty machinery known as rolling mills. However, if you need to roll steel on a smaller scale, a manual rolling mill can be used.
For small-scale applications, begin by selecting the appropriate thickness and type of steel for your project. Adjust the rollers of your manual rolling mill to accommodate the thickness of your steel sheet. Gradually feed the steel through the rollers while maintaining steady pressure to avoid slippage and ensure uniform thickness. It may be necessary to pass the steel through the rollers multiple times, incrementally adjusting the roller distance each time to achieve the desired thickness. Always use proper safety gear, such as gloves and eye protection, to prevent injuries during this process. Keep the workspace organized and free of obstructions to smoothly roll the steel without interruptions.
Bending sheet metal without a bender is entirely feasible with the right techniques and tools. One effective method is to use a sturdy workbench edge or a similar straight edge to create a clean bend. First, mark the line where you wish to bend the metal. Place the sheet metal on the edge of the workbench so that the line aligns exactly with the edge of the bench. Secure the metal to the bench using strong clamps to hold it firmly in place.
Next, apply firm, steady pressure downwards on the free side of the sheet metal. Use a piece of wood or a soft mallet to help apply even force along the bend line, which can help prevent the metal from warping or bending unevenly. Gradually increase the force until the metal bends to the desired angle. For thicker metal sheets, heating the bend line with a blowtorch can soften the metal and make the bending process easier. Always take safety precautions to wear protective gloves and eyewear to avoid burns or injuries.
The primary tool used to roll metal is called a rolling mill. Rolling mills are designed to compress and elongate the metal between two rollers rotating in opposite directions. There are several types of rolling mills, including two-high, three-high, four-high, cluster, and tandem mills, each suited for specific purposes and scale of operation.
For smaller projects or more precise work, a slip roller (also known as a sheet metal roller) is commonly used. Slip rollers are smaller and more manageable than industrial rolling mills and can be manually operated or motor-driven. They consist of three rollers that create bends and curves by adjusting the distance between the rollers, allowing for precise control over the curvature and diameter of the metal being rolled. These tools are essential for tasks involving sheet metal fabrication, such as forming tubes, cylinders, or other curved metal surfaces. Always ensure that the tool you choose is suitable for the gauge and type of metal you plan to work with to achieve the best results.
Last Updated on August 1, 2024 by Jordan Smith
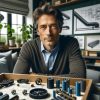
Jordan Smith, a seasoned professional with over 20 years of experience in the conveyor system industry. Jordan’s expertise lies in providing comprehensive solutions for conveyor rollers, belts, and accessories, catering to a wide range of industrial needs. From initial design and configuration to installation and meticulous troubleshooting, Jordan is adept at handling all aspects of conveyor system management. Whether you’re looking to upgrade your production line with efficient conveyor belts, require custom conveyor rollers for specific operations, or need expert advice on selecting the right conveyor accessories for your facility, Jordan is your reliable consultant. For any inquiries or assistance with conveyor system optimization, Jordan is available to share his wealth of knowledge and experience. Feel free to reach out at any time for professional guidance on all matters related to conveyor rollers, belts, and accessories.