How to Select Conveyor Belt for Optimal Performance
Selecting the right conveyor belt is crucial for ensuring cost-effectiveness, reliability, and efficiency in your operations. When learning how to select conveyor belt, it is important to consider several key factors and calculations that will guide you to the best choice. The correct conveyor belt can significantly reduce maintenance costs, enhance operational efficiency, and prevent downtime. This guide will introduce you to the critical aspects of how to select conveyor belt, including material considerations, environmental factors, and application-specific needs. By understanding these elements, you can make an informed decision that supports your operational goals and enhances overall productivity.
How to Select Conveyor Belt: Importance of Conveyor Belt Selection
Choosing the right conveyor belt is an essential step in optimizing the efficiency and cost-effectiveness of your operations. Understanding how to select conveyor belt properly can make a significant difference in operational performance, maintenance costs, and overall productivity. In this section, we will explore the critical importance of selecting the appropriate conveyor belt and the potential consequences of making the wrong choice.
The Impact of Choosing the Incorrect Conveyor Belt
When you fail to understand how to select conveyor belt that fits your specific needs, several negative outcomes can arise. One major consequence is increased maintenance costs. An improperly selected conveyor belt may wear out faster, leading to frequent replacements and repairs. This not only increases direct costs but also demands additional labor and time to address these issues.
Reduced efficiency is another significant impact. If the conveyor belt is not suitable for the materials being transported or the environment in which it operates, it can result in slower processing times and decreased throughput. For example, a belt that is too narrow for the load might lead to spillage and product damage, while a belt that is too wide can cause unnecessary friction and energy consumption.
Potential operational downtime is perhaps the most critical consequence. Downtime can occur due to belt failure, misalignment, or other issues arising from improper selection. This can halt production lines, delay shipments, and ultimately affect customer satisfaction and revenue. Downtime is particularly costly in industries where continuous operation is essential, such as manufacturing, mining, and food processing.
Key Considerations in Conveyor Belt Selection
When learning how to select conveyor belt, it is crucial to consider several key factors that will influence your decision. These include material, environment, and application needs. Let’s discuss five examples to illustrate the importance of these considerations:
- Material Properties:
Different materials have varying characteristics that affect conveyor belt selection. For instance, abrasive materials like sand or gravel require a belt made of durable, wear-resistant materials. Conversely, food-grade materials need belts that are FDA-approved and easy to clean. Understanding the properties of the materials you will be transporting is critical in choosing the right belt. - Environmental Conditions:
The operating environment plays a significant role in how to select conveyor belt. In a high-temperature environment, a heat-resistant belt is necessary to prevent degradation and ensure longevity. In contrast, in a cold storage facility, a belt that can withstand low temperatures without becoming brittle is essential. Additionally, exposure to chemicals or moisture might require belts with specific resistance properties. - Load Requirements:
The weight and size of the load are fundamental considerations. A belt must be capable of supporting the maximum load weight without stretching or breaking. For example, heavy-duty belts are required for transporting large, heavy items such as construction materials, while lighter belts may be sufficient for smaller, lighter products like packages or electronics. - Speed and Throughput:
The speed at which materials need to be conveyed and the required throughput rate are also critical factors. High-speed operations may demand belts with high tensile strength and reduced friction to prevent slippage and maintain efficiency. Conversely, slower operations might prioritize belts that offer better control and stability. - Application-Specific Needs:
Different applications have unique requirements that influence how to select conveyor belt. For example, in inclined or declined conveying, belts with cleats or ribs can prevent materials from sliding back. In automated systems, belts with precise tracking capabilities are essential to ensure synchronization with other machinery. Each application may present specific challenges that the chosen belt must address.
Understanding how to select conveyor belt is essential for ensuring the smooth and efficient operation of your conveyor system. By considering the material properties, environmental conditions, load requirements, speed and throughput needs, and application-specific factors, you can make an informed decision that minimizes maintenance costs, enhances efficiency, and reduces the risk of operational downtime. Proper conveyor belt selection is not just about choosing a belt that fits your conveyor; it is about selecting a belt that fits your entire operation’s needs and goals.
How to Select Conveyor Belt: Conveyor Belt Selection and Calculation
Selecting the right conveyor belt involves a detailed technical process that ensures the belt fits the operational requirements and enhances overall efficiency. Understanding how to select conveyor belt correctly requires a thorough knowledge of various terms, concepts, and calculations involved in the selection process.
Overview of the Technical Process
The technical process of selecting and calculating the right conveyor belt begins with a comprehensive analysis of the operational requirements and the environment in which the belt will operate. Key considerations include tensile strength, belt width, speed requirements, and the nature of the materials being transported. Each of these factors plays a crucial role in determining the most suitable conveyor belt for your needs.
Tensile Strength: This refers to the maximum stress a belt can withstand without breaking. It is essential to choose a belt with adequate tensile strength to handle the load it will carry. A belt with insufficient tensile strength can lead to frequent breakages and operational disruptions.
Belt Width: The width of the belt must be appropriate for the materials being conveyed. A belt that is too narrow may lead to spillage and inefficiency, while a belt that is too wide may result in unnecessary friction and energy consumption.
Speed Requirements: The speed at which the belt needs to operate is another critical factor. High-speed operations require belts with high tensile strength and reduced friction to maintain efficiency and prevent slippage.
Determining the Operational Requirements
Understanding how to select conveyor belt involves defining the operational requirements based on the product to be conveyed. This includes considering the weight, size, and material properties of the items being transported.
Example 1: Heavy machinery parts require a belt with high tensile strength and durability to handle the weight and prevent wear and tear.
Example 2: Food products necessitate a food-grade belt that is easy to clean and resistant to contamination.
Example 3: Electronics require a belt that minimizes static electricity to prevent damage to sensitive components.
Example 4: Chemical products demand a belt that can resist chemical interactions and corrosion.
Example 5: Frozen goods need a belt that can withstand low temperatures without becoming brittle.
It is also crucial to understand the purpose and environment in which the conveyor system will operate. This includes considerations of temperature, humidity, and exposure to chemicals.
Material and Design Considerations
Selecting the appropriate material for the conveyor belt is crucial for ensuring longevity and performance. Different materials have varying properties that affect their suitability for different applications.
Example 1: Rubber belts are ideal for heavy-duty applications due to their durability and resistance to abrasion.
Example 2: PVC belts are suitable for food processing due to their hygiene and ease of cleaning.
Example 3: Metal belts are perfect for high-temperature applications as they can withstand heat without degrading.
Example 4: Fabric belts are used for lightweight applications where flexibility and low cost are important.
Example 5: PU belts offer excellent chemical resistance and are used in environments with exposure to oils and chemicals.
Design elements such as belt thickness, width, and special features like cleats for inclined conveyors also affect performance. A thicker belt provides more durability, while the inclusion of cleats helps in transporting materials on inclined planes by preventing slippage.
Conveyor Belt Types
There are several common types of conveyor belts, each suited for different applications.
Flat Belts: Ideal for general-purpose conveying of items on a flat surface. They are widely used in packaging and assembly lines.
Modular Belts: Made of interlocking plastic pieces, these belts are easy to clean and maintain, making them suitable for the food industry.
Cleated Belts: These belts have vertical cleats or barriers that prevent materials from slipping, making them ideal for inclined or declined conveying.
Wire Mesh Belts: Used in high-temperature applications and for materials that require air circulation, such as in baking or cooling processes.
Fabric Belts: Lightweight and flexible, these belts are used in light-duty applications where cost efficiency is important.
Guidance on when to choose a specific type of conveyor belt depends on the operational needs and product characteristics. For example, flat belts are suitable for flat surface transport, while cleated belts are necessary for inclines. Modular belts are chosen for easy maintenance, and wire mesh belts are used for high-temperature or drying processes.
Understanding how to select conveyor belt involves careful consideration of these factors to ensure the belt meets the specific requirements of your operation, ultimately enhancing efficiency, reducing costs, and minimizing downtime.
How to Select Conveyor Belt: Advanced Factors in Conveyor Belt Selection
When understanding how to select conveyor belt, it is essential to consider advanced factors that can significantly impact performance, safety, and efficiency. Technological advancements in conveyor belt design and manufacturing have introduced smart systems and innovative materials that offer improved performance and safety. Additionally, considerations for energy efficiency and integration with Industry 4.0 technologies are becoming increasingly important in modern conveyor systems.
Technological Advancements in Conveyor Belts
Technological advancements have revolutionized the way conveyor belts are designed and operated. These innovations enhance the functionality, durability, and efficiency of conveyor systems, making them more adaptable to various industrial needs.
Smart Systems: One of the most significant advancements in conveyor belt technology is the integration of smart systems. These systems use sensors, IoT (Internet of Things) devices, and automation to monitor the conveyor belt’s performance in real-time. Smart conveyor belts can detect issues such as misalignment, wear and tear, and load imbalances, allowing for proactive maintenance and reducing the risk of unexpected downtime.
Innovative Materials: The development of new materials has led to conveyor belts that are stronger, more flexible, and more resistant to harsh environmental conditions. For example, polyurethane and thermoplastic elastomers offer excellent resistance to abrasion, chemicals, and extreme temperatures. These materials enhance the belt’s longevity and reduce maintenance costs.
Safety Features: Technological advancements have also improved safety features in conveyor belts. For instance, flame-retardant materials are now commonly used in belts operating in environments where fire hazards are a concern. Additionally, anti-static belts prevent the build-up of static electricity, which can be crucial in industries dealing with flammable materials or sensitive electronic components.
Energy Efficiency and Industry 4.0 Integration
Energy efficiency and the integration of Industry 4.0 technologies are critical considerations when selecting a conveyor belt. These factors not only contribute to sustainability but also enhance operational efficiency and cost-effectiveness.
Energy Efficiency: Conveyor belts that are designed for energy efficiency can significantly reduce operational costs. Features such as low-friction materials, optimized belt profiles, and energy-efficient motors help in minimizing energy consumption. For example, belts with a low coefficient of friction reduce the amount of energy required to move products, thus lowering overall energy costs.
Variable Speed Drives (VSDs): Integrating VSDs with conveyor belts allows for the adjustment of belt speed according to the operational needs. This flexibility helps in optimizing energy use, especially during periods of low demand or when transporting lighter loads. VSDs also contribute to the longevity of the conveyor system by reducing mechanical stress on the belt and associated components.
Industry 4.0 Technologies: The integration of Industry 4.0 technologies, such as advanced data analytics, machine learning, and artificial intelligence, has transformed conveyor belt operations. These technologies enable predictive maintenance, which uses data from sensors and monitoring systems to predict potential failures before they occur. Predictive maintenance reduces downtime and extends the lifespan of the conveyor belt.
Automation and Robotics: Automation and robotics are increasingly being integrated into conveyor systems to enhance efficiency and precision. Automated systems can handle repetitive tasks with greater accuracy and speed, reducing the likelihood of human error and increasing throughput. Robotic systems can also be used for tasks such as sorting, packaging, and palletizing, further improving operational efficiency.
Connectivity and Data Integration: Modern conveyor belts are designed to be part of a connected ecosystem. They can communicate with other machines and systems within a production facility, enabling seamless data exchange and coordination. This connectivity supports real-time decision-making and process optimization, ensuring that the conveyor system operates at peak efficiency.
Understanding how to select conveyor belt involves more than just considering basic factors like material and load requirements. Advanced factors, such as technological advancements, energy efficiency, and Industry 4.0 integration, play a crucial role in optimizing conveyor belt performance. By leveraging smart systems, innovative materials, and modern technologies, you can enhance the efficiency, safety, and cost-effectiveness of your conveyor system. These advancements not only improve operational performance but also contribute to sustainability and long-term reliability, making them essential considerations in the selection process.
How to Select Conveyor Belt: Additional Considerations
When determining how to select conveyor belt, several additional factors must be taken into account to ensure the belt performs optimally under various operational conditions. These considerations include external factors such as incline dynamics, resistance due to specific product properties, and other resistance factors that can impact the efficiency and longevity of the conveyor belt system.
Incline Dynamics
Incline dynamics refer to the changes in the conveyor belt’s operation when it is used in an inclined or declined setup. The angle of inclination can significantly affect the belt’s performance and the choice of belt type.
Incline Angles and Belt Traction: The steeper the incline, the greater the need for a belt with enhanced traction. Cleated belts or belts with high-friction surfaces are often required to prevent materials from slipping backward. For example, in industries such as mining or agriculture, where materials need to be transported up steep slopes, cleated belts provide the necessary grip to move materials efficiently.
Load Distribution: Incline dynamics also impact load distribution on the conveyor belt. As the angle of inclination increases, the force exerted by the load on the belt changes, potentially leading to increased wear and tear. It’s crucial to choose a belt with sufficient tensile strength and durability to withstand these forces without excessive stretching or damage.
Energy Consumption: Transporting materials on an incline requires more energy compared to a flat surface. This increased energy demand must be factored into the selection process, ensuring that the belt and the conveyor system are capable of handling the additional power requirements. Energy-efficient belts and systems can help mitigate these increased costs.
Resistance Due to Specific Product Properties
Different products have unique properties that affect how they interact with the conveyor belt. Understanding these properties is essential for selecting the right belt.
Abrasion Resistance: Materials that are abrasive, such as sand, gravel, or ore, can cause significant wear on the conveyor belt. Selecting a belt made from abrasion-resistant materials, like rubber or specialized polymers, can help extend the belt’s lifespan and reduce maintenance costs.
Chemical Resistance: In industries where chemicals are transported, such as pharmaceuticals or chemicals manufacturing, the belt material must be resistant to chemical interactions. For instance, belts made from PVC or PU are often used in these environments due to their chemical resistance.
Temperature Sensitivity: Products that are sensitive to temperature changes require belts that can maintain their integrity under varying temperature conditions. For example, belts used in food processing might need to handle both freezing and high-temperature environments, necessitating the use of belts that can withstand these extremes without degrading.
Moisture Resistance: In environments where the conveyor belt will be exposed to moisture, such as in food processing or outdoor operations, selecting a moisture-resistant belt is critical. Belts made from materials like PVC or certain synthetic rubbers offer good moisture resistance and help prevent issues like mold growth or belt degradation.
Static Electricity: Certain products, particularly electronic components, are sensitive to static electricity. Anti-static belts are essential in these cases to prevent damage to the products and ensure safe operation.
Assessing Additional Resistance Factors
In addition to the product-specific properties and incline dynamics, there are other resistance factors that must be considered when selecting a conveyor belt.
Friction: The friction between the belt and the conveyor components, as well as the materials being transported, plays a significant role in determining the belt’s efficiency. Low-friction belts can reduce energy consumption and increase the system’s overall efficiency, while high-friction belts may be necessary for applications requiring additional grip.
Flexibility and Flexural Strength: The flexibility of the belt is crucial in applications where the conveyor system includes curves or bends. A belt that is too rigid may not navigate these turns efficiently, leading to increased wear and potential system failures. Conversely, a belt with adequate flexural strength can handle these conditions without compromising performance.
Weight of the Conveyor Belt: The weight of the conveyor belt itself can impact the overall system performance. Heavier belts may require more robust support structures and more powerful drive systems, increasing the overall cost and complexity of the system. Lighter belts, while easier to handle and install, must still provide the necessary durability and strength for the application.
Understanding how to select conveyor belt involves a comprehensive analysis of various additional considerations beyond the basic operational requirements. Incline dynamics, resistance due to specific product properties, and other resistance factors significantly influence the selection process. By carefully evaluating these factors, you can choose a conveyor belt that not only meets the immediate needs of your operation but also enhances long-term efficiency, reduces maintenance costs, and improves overall system performance. This holistic approach to conveyor belt selection ensures that your system operates smoothly and effectively, regardless of the unique challenges it may face.
FAQs About How to Select Conveyor Belt
Choosing the right conveyor belt involves understanding your specific operational requirements and the environment in which the belt will operate. Start by considering the type of material you will be transporting, including its weight, size, and any special properties such as abrasiveness or temperature sensitivity. Next, evaluate the environment: is it hot, cold, wet, or dry? Does it involve exposure to chemicals or require food-grade materials? Understanding these factors helps in selecting a belt material that will perform well under those conditions. Additionally, consider the configuration of your conveyor system, including any inclines, declines, or curves, and the speed at which the belt needs to operate. Finally, think about maintenance and longevity. Choose a belt that not only fits your immediate needs but also offers durability and ease of maintenance to minimize downtime and repair costs over its lifespan.
Selecting a belt for a belt conveyor starts with understanding the nature of the material being conveyed. Identify key characteristics such as weight, dimensions, and material properties (e.g., abrasiveness, moisture content, temperature sensitivity). Next, assess the environmental conditions where the conveyor will be used. Factors like temperature, humidity, and exposure to chemicals will influence the type of belt material required. You should also consider the operational dynamics of the conveyor system, including the length of the conveyor, the speed of operation, and any incline or decline in the conveyor path. The belt’s tensile strength, thickness, and width must be suitable for these conditions to ensure efficient and reliable performance. Finally, review the maintenance requirements and lifespan expectations of the belt options. Choosing a belt that balances performance, durability, and ease of maintenance will ensure optimal operation and cost-efficiency over time.
Calculating a conveyor belt involves determining several key parameters to ensure it meets your operational needs. Start with the length of the conveyor belt, which can be calculated based on the conveyor’s layout and path. Next, calculate the belt’s load capacity by considering the weight and size of the materials it will transport. This involves determining the belt’s width and thickness, as well as its tensile strength, which must be adequate to handle the maximum load without excessive stretching or breaking. Additionally, calculate the belt speed by considering the desired throughput and the conveyor system’s operational speed. To ensure the belt runs efficiently, consider the drive pulley diameter and the belt’s required tension. The calculations should also factor in the belt’s friction coefficient, which affects energy consumption and overall efficiency. By accurately determining these parameters, you can select a conveyor belt that will operate effectively and reliably under your specific conditions.
Sizing a conveyor belt involves several steps to ensure it fits your conveyor system and meets operational requirements. First, measure the width of the conveyor bed and the product being conveyed to determine the necessary belt width. The belt should be wide enough to accommodate the product without spillage but not so wide as to create unnecessary friction. Next, calculate the length of the conveyor belt needed based on the conveyor’s path, including any inclines, declines, and curves. This can be done by measuring the conveyor’s total run and factoring in the belt’s return path. Additionally, consider the thickness of the belt, which should be sufficient to handle the load and provide durability. The belt’s tensile strength must also be appropriate for the maximum load and operating conditions. Lastly, ensure the belt’s material and design match the environmental conditions and specific requirements of the conveyed materials. Properly sizing the conveyor belt is crucial for efficient and reliable operation.
Last Updated on June 4, 2024 by Jordan Smith
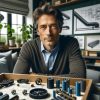
Jordan Smith, a seasoned professional with over 20 years of experience in the conveyor system industry. Jordan’s expertise lies in providing comprehensive solutions for conveyor rollers, belts, and accessories, catering to a wide range of industrial needs. From initial design and configuration to installation and meticulous troubleshooting, Jordan is adept at handling all aspects of conveyor system management. Whether you’re looking to upgrade your production line with efficient conveyor belts, require custom conveyor rollers for specific operations, or need expert advice on selecting the right conveyor accessories for your facility, Jordan is your reliable consultant. For any inquiries or assistance with conveyor system optimization, Jordan is available to share his wealth of knowledge and experience. Feel free to reach out at any time for professional guidance on all matters related to conveyor rollers, belts, and accessories.