The Versatility of Hytrol Gravity Roller Conveyor
Hytrol stands at the forefront of the conveyor industry, renowned for its innovative solutions that streamline operations across various sectors. Among its extensive product lineup, the Hytrol gravity roller conveyor emerges as a pivotal tool, designed to facilitate the effortless movement of goods. Leveraging the force of gravity, these conveyors play a crucial role in material handling, offering a simple yet effective means to transport items across short distances within warehouses, distribution centers, and manufacturing facilities. Their significance is underscored by their ability to enhance efficiency, reduce manual labor, and optimize workflow, making them an indispensable asset in the modern industrial landscape.
What Is Hytrol Gravity Roller Conveyor
The Hytrol gravity roller conveyor is a non-powered conveyor system that relies on gravity to move materials along its path. Unlike motorized conveyor systems, the Hytrol gravity roller conveyor utilizes the natural force of gravity to facilitate the movement of goods, making it an energy-efficient and cost-effective solution for material handling. Here are the key aspects that define the operation and advantages of the Hytrol gravity roller conveyor:
Basic Operation Principles:
- Gravity-Driven: Utilizes the natural force of gravity to move items, requiring a slight incline to initiate movement.
- Roller Mechanism: Consists of a series of rollers that provide a smooth surface for goods to travel over.
- Manual Assistance: In level applications, goods may require a manual push to start their journey along the conveyor.
- Adjustable Incline: The angle of incline can be adjusted to control the speed and flow of materials.
- Load Capacity: Designed to handle a wide range of load weights, from lightweight packages to heavier industrial products.
- Modular Design: Allows for easy expansion or reconfiguration to meet changing operational needs.
- Simple Installation: Engineered for ease of installation, reducing downtime and labor costs.
- Low Maintenance: Requires minimal maintenance due to the lack of complex mechanical parts.
Key Features and Benefits:
- Cost-Effectiveness: The absence of motorized parts significantly reduces operational costs.
- Energy Efficiency: Operates without electricity, making it an eco-friendly material handling solution.
- Ease of Integration: Seamlessly integrates with existing conveyor systems and material handling setups.
- Versatility: Suitable for a wide range of industries, including warehousing, manufacturing, and distribution.
- Durability: Constructed with high-quality materials, ensuring longevity and reliability in demanding environments.
- Safety: Minimizes the risk of injury associated with manual handling and reduces the potential for product damage.
- Flexibility: Can be customized with various roller sizes, widths, and materials to accommodate different product types.
- Scalability: Easily expandable to accommodate growth or changes in operational requirements.
- Improved Workflow: Enhances efficiency by streamlining the movement of goods, leading to faster processing and throughput times.
Incorporating a Hytrol gravity roller conveyor into material handling operations offers a blend of efficiency, reliability, and adaptability, making it a valuable asset for businesses looking to optimize their logistics and supply chain processes.
Types and Applications of Hytrol Gravity Roller Conveyor
The Hytrol gravity roller conveyor system is a cornerstone in the material handling industry, offering a variety of models to accommodate the diverse needs of different sectors. These conveyors are designed to enhance efficiency and productivity, whether in warehousing, manufacturing, or distribution centers.
Types of Hytrol Gravity Roller Conveyor:
- Medium-Duty Steel Conveyors: These conveyors are built with steel frames and rollers, making them suitable for handling packages, parcels, and other items with moderate weight. They are commonly used in distribution centers and assembly lines where durability and reliability are key.
- Heavy-Duty Conveyors: Designed for industrial applications, heavy-duty conveyors can handle heavier loads such as pallets, drums, and large containers. They feature robust construction with thicker gauge rollers and frames to withstand harsh environments.
- Expandable Conveyors: Flexible and portable, expandable conveyors can be extended, curved, and contracted to fit various spaces and applications, ideal for temporary setups or dynamic workspaces like loading docks.
- Skatewheel Conveyors: Comprising a series of small wheels, skatewheel conveyors are lightweight and ideal for moving items with smooth bottoms. They are particularly useful for quick and easy handling of light to medium loads.
- Curved Conveyors: These conveyors are designed to change the direction of material flow within a facility, allowing for flexible layout designs and efficient use of space.
- Spiral Chutes: Used for lowering products from higher elevations, spiral chutes are a form of gravity conveyor that provides a controlled descent, minimizing potential damage to the products.
- Ball Transfer Tables: These units allow for multi-directional movement of products, making them ideal for workstations where items need to be rotated or precisely positioned.
Applications:
- Warehousing: Hytrol gravity roller conveyors streamline the movement of goods from receiving to storage and shipping, enhancing the efficiency of warehousing operations.
- Shipping Departments: In shipping areas, these conveyors expedite the movement of packed goods to loading docks, ensuring timely dispatch and delivery.
- Assembly Areas: They facilitate the smooth transition of parts and products along assembly lines, contributing to streamlined manufacturing processes.
- Distribution Centers: Gravity roller conveyors improve the sorting and distribution of goods, aiding in faster order fulfillment and inventory management.
- Retail Backrooms: In retail, they are used for stock management, moving merchandise from delivery areas to storage or sales floors efficiently.
- Packaging Lines: Conveyors are integral to packaging operations, moving products through various stages of packaging with minimal manual intervention.
- Loading and Unloading Zones: Expandable and flexible conveyor types are particularly useful in loading docks for efficient loading and unloading of goods from trucks or containers.
The versatility and adaptability of the Hytrol gravity roller conveyor make it an invaluable tool across a wide range of industries, proving its effectiveness in improving operational workflows and productivity.
Hytrol Gravity Roller Conveyor Components
The Hytrol gravity roller conveyor is a testament to sophisticated engineering, comprising several key components that work in harmony to ensure efficient material handling. Each Hytrol Conveyor Accessories of the Hytrol gravity roller conveyor plays a pivotal role in its operation, contributing to the system’s overall effectiveness and reliability.
Key Components:
- Frames: The backbone of the Hytrol gravity roller conveyor, frames provide structural support, holding the rollers in place and ensuring the system’s rigidity and stability under load.
- Rollers: These cylindrical elements create the rolling surface for materials to move across. Hytrol’s rollers are designed for smooth rotation, minimizing friction and facilitating effortless material flow.
- Axles: Axles secure the rollers to the frame and allow for their rotation. Precision-engineered for durability, they ensure the rollers spin freely without wobble, contributing to a smooth conveyor operation.
- Guard Rails: Installed along the edges of the conveyor, guard rails prevent items from falling off, ensuring that materials stay on track as they move along the conveyor.
- Support Legs: These components provide elevation and stability to the conveyor, allowing for height adjustments to achieve the desired slope for gravity movement.
- End Stops: Positioned at the ends of the conveyor, end stops prevent materials from sliding off, ensuring safe handling and accumulation where necessary.
- Spacers: Spacers are used between rollers to maintain consistent spacing, ensuring that materials of various sizes can be transported efficiently without getting stuck.
- Bearing Covers: These protect the roller bearings from dust, debris, and other contaminants, prolonging the life of the rollers and ensuring smooth operation.
Importance of Each Component:
- Frames: Ensure the structural integrity of the conveyor, capable of withstanding various loads while maintaining alignment and stability.
- Rollers: The primary contact point for materials, their smooth surface and rotation efficiency directly impact the conveyor’s ability to move items with minimal effort.
- Axles: Critical for the rotational movement of rollers, their precision and strength prevent misalignment that could disrupt the conveyor’s flow.
- Guard Rails: Enhance safety and efficiency by keeping materials contained within the conveyor path, reducing the risk of spillage and ensuring consistent material flow.
- Support Legs: Allow for the customization of conveyor height and slope, enabling the system to be tailored to specific operational needs and optimizing gravity-driven movement.
- End Stops: Provide a necessary barrier to control the flow of materials, essential for batch processing, accumulation, and at loading/unloading points.
- Spacers: Maintain uniform roller spacing, crucial for the consistent and reliable movement of a wide range of material sizes and shapes.
- Bearing Covers: Protect the internal components of rollers from environmental factors, reducing wear and tear and extending the operational lifespan of the conveyor.
Each component of the Hytrol gravity roller conveyor is meticulously designed to contribute to the system’s overall functionality, ensuring smooth operation, durability, and efficient material handling across various applications.
Pricing and Availability of Hytrol Gravity Roller Conveyor
When considering the integration of a Hytrol gravity roller conveyor into your material handling system, understanding the pricing and availability is crucial. The cost of a Hytrol gravity roller conveyor can vary widely based on several factors, and knowing where to find these systems for sale is equally important.
Factors Influencing Cost:
- Length and Width: The size of the conveyor significantly impacts the price, with larger conveyors requiring more materials and thus costing more.
- Roller Material and Diameter: Choices between steel, aluminum, or plastic rollers, as well as the diameter of the rollers, can affect the price due to material and manufacturing costs.
- Frame Material: The type of material used for the frame (e.g., steel, aluminum) influences the overall cost due to differences in material prices and durability.
- Load Capacity: Conveyors designed to handle heavier loads typically cost more due to the need for stronger materials and construction.
- Customization: Any custom features or specifications to meet specific operational needs can increase the price.
- Quantity: Purchasing multiple units often allows for bulk pricing, reducing the cost per unit.
- Brand New vs. Used: New conveyors come at a premium price compared to used or refurbished models, which can be more cost-effective.
- Shipping and Installation: The cost of shipping and professional installation can add significantly to the overall investment.
- Supplier: Prices can vary between suppliers based on their pricing strategies, location, and additional services offered.
Tips on Finding and Choosing the Right Model:
- Authorized Dealers: Purchase from authorized Hytrol dealers to ensure authenticity and quality service.
- Online Marketplaces: Check industrial equipment marketplaces online for new and used options.
- Trade Shows: Industry trade shows often feature the latest conveyor models and offer the opportunity to negotiate deals directly with suppliers.
- Referrals: Seek recommendations from industry peers who have purchased Hytrol gravity roller conveyors.
- Customization Services: Look for suppliers that offer customization services to ensure the conveyor meets your specific needs.
- Warranty and Support: Consider the warranty and after-sales support services, which can be crucial for maintenance and repairs.
- Product Reviews: Read reviews and case studies to understand the performance and reliability of different models.
- Consultation: Utilize free consultations offered by suppliers to get expert advice on the most suitable conveyor for your application.
- Financing Options: Explore financing options if upfront costs are prohibitive, as many suppliers offer payment plans to spread out the expense.
Understanding the factors that influence the pricing of a Hytrol gravity roller conveyor and knowing where to find and how to choose the right model are essential steps in making an informed purchasing decision. This ensures that you invest in a conveyor system that meets your operational needs while staying within your budget.
Maintenance and Parts for Hytrol Gravity Roller Conveyor
Maintaining a Hytrol gravity roller conveyor is crucial for ensuring its longevity and efficiency in material handling operations. Regular maintenance not only prevents downtime but also extends the life of the conveyor. Knowing how to find and order replacement parts is equally important to keep the system running smoothly.
Common Maintenance Tasks:
- Regular Inspections: Conduct periodic inspections to check for wear and tear on rollers, frames, and axles. Look for signs of misalignment, damage, or excessive wear that could impede operation.
- Cleaning: Keep the conveyor clean from debris and dust that can accumulate on rollers and in bearings, potentially hindering movement and causing unnecessary wear.
- Lubrication: While many Hytrol gravity roller conveyor components are designed for low maintenance, some parts may require occasional lubrication to ensure smooth operation.
- Roller Replacement: Worn or damaged rollers should be replaced promptly to maintain efficient conveyor operation. Rollers should spin freely without resistance.
- Tightening and Adjustments: Regularly check and tighten any loose bolts and nuts to ensure the structural integrity of the conveyor. Adjust the tension and alignment of the conveyor as needed.
- Guard Rail Inspection: Ensure that guard rails are intact and securely attached. Damaged or missing guard rails can lead to product spillage or accidents.
- End Stop Checks: Verify that end stops are securely in place and functioning as intended to prevent materials from falling off the conveyor ends.
Finding and Ordering Replacement Parts:
- Hytrol’s Official Website: The most direct way to find replacement parts is through Hytrol’s official website, which often lists parts and their corresponding conveyor models.
- Authorized Hytrol Distributors: Authorized distributors have access to a wide range of Hytrol parts and can provide expert advice on the correct parts for your specific conveyor model.
- Parts Catalogs: Hytrol provides detailed parts catalogs that include diagrams and part numbers, making it easier to identify and order the correct components.
- Technical Support: Hytrol’s technical support can assist in diagnosing issues and recommending the appropriate replacement parts.
- Online Marketplaces: Some parts may be available through industrial equipment online marketplaces, though it’s crucial to ensure compatibility with your specific conveyor model.
- Serial Number: Have your conveyor’s serial number ready when ordering parts. This ensures that you receive components that are compatible with your specific model.
- Maintenance Manuals: Refer to the maintenance manual provided with your Hytrol gravity roller conveyor for detailed information on part numbers and replacement procedures.
- Custom Parts: For custom or modified conveyors, contact Hytrol or your distributor directly to ensure that you receive parts that fit your specific modifications.
Proper maintenance and timely replacement of parts are key to maximizing the performance and lifespan of your Hytrol gravity roller conveyor. By staying vigilant and proactive in maintenance efforts, you can ensure that your conveyor continues to operate efficiently and effectively, supporting your operational needs.
Additional Hytrol Conveyor Solutions Beyond the Hytrol Gravity Roller Conveyor
Exploring the extensive range of Hytrol’s conveyor solutions reveals options beyond the versatile Hytrol gravity roller conveyor, each designed to meet specific operational demands. These alternatives extend the capabilities of material handling systems, catering to various industrial applications with unique requirements.
Diverse Hytrol Conveyor Offerings:
- Powered Roller Conveyors: These systems employ motor-driven rollers, providing consistent and automated movement of goods, ideal for extensive and complex conveyor layouts.
- Accumulation Conveyors: Engineered to manage product flow by allowing items to accumulate without contact, these conveyors are crucial in preventing product damage and facilitating orderly processing.
- Pallet Handling Systems: Tailored for the movement of heavy and bulky items on pallets, these systems incorporate robust design elements to ensure safe and efficient pallet transport.
- Belt Conveyors: Utilizing a continuous belt surface, these conveyors offer a versatile solution for transporting a wide range of items, from small parts to large boxes.
- Sortation Conveyors: Designed for high-speed sorting of products into distinct lanes or areas based on specified criteria, enhancing efficiency in distribution and fulfillment centers.
Strategic Comparison and Selection:
- Operational Complexity: While the Hytrol gravity roller conveyor excels in straightforward applications, powered roller conveyors are better suited for intricate systems requiring automated product movement.
- Energy Dynamics: The passive nature of gravity conveyors offers energy savings, whereas powered systems, though energy-consuming, deliver continuous and controlled product flow.
- System Integration: Sortation and belt conveyors seamlessly integrate into complex material handling setups, offering advanced sorting capabilities and transport flexibility.
- Handling Capabilities: Pallet handling systems are uniquely designed for heavy loads, a contrast to the lighter applications typical of gravity roller conveyors.
- Product Sensitivity: Accumulation conveyors provide a solution for handling delicate items by preventing contact, an area where traditional gravity systems may fall short.
- Throughput Requirements: For operations demanding high throughput, sortation conveyors offer rapid and accurate sorting, surpassing the capabilities of manual or gravity-based systems.
- Layout Adaptability: Belt conveyors provide versatility in product type and size handling, making them suitable for a variety of applications, unlike the more size-specific gravity roller systems.
- Investment Considerations: The initial lower cost of gravity conveyors is balanced against the long-term efficiency and automation benefits provided by powered and specialized conveyor systems.
Choosing the appropriate Hytrol conveyor solution involves a careful assessment of your operational needs, considering factors such as automation level, product type, and throughput requirements. Each system offers unique benefits, from the simplicity and cost-effectiveness of the Hytrol gravity roller conveyor to the advanced capabilities of powered, accumulation, and sortation systems, ensuring there’s a Hytrol solution to meet every material handling challenge.
FAQs about Hytrol Gravity Roller Conveyor
The weight limit for a Hytrol conveyor varies significantly depending on the specific model and configuration of the conveyor system. Hytrol designs a wide range of conveyor systems, each tailored to meet different operational needs, including light-duty, medium-duty, and heavy-duty applications. For instance, a standard gravity roller conveyor might accommodate loads up to approximately 250 pounds per linear foot, whereas a heavy-duty pallet handling system could handle significantly more, often exceeding 2,000 pounds per pallet. It’s crucial to consult the specific product specifications or contact Hytrol directly to determine the exact weight capacity for a particular conveyor model. This ensures that the selected conveyor system is perfectly suited to the operational demands, optimizing efficiency and safety in material handling processes.
A gravity roller conveyor is a non-powered conveyor system that relies on gravity to move materials along its path. It consists of a series of rollers mounted within a frame, where the conveyor is slightly inclined or operators manually push the items to initiate movement. This type of conveyor is particularly advantageous for its simplicity, cost-effectiveness, and ease of installation and maintenance. Gravity roller conveyors are versatile and can be used in various settings, including warehouses, distribution centers, and manufacturing plants, to transport items ranging from small packages to large boxes. The system’s design allows for the addition of curves, gates, and merges, making it adaptable to a wide range of material handling layouts and requirements.
Hytrol Conveyor Company, Inc. is headquartered in Jonesboro, Arkansas, USA, where it operates a state-of-the-art manufacturing facility. The company takes pride in its American-made conveyor solutions, emphasizing quality, innovation, and craftsmanship. Hytrol’s extensive product line, including gravity roller conveyors, powered belt conveyors, and advanced sortation systems, is engineered and manufactured at this location. The company’s commitment to domestic manufacturing not only supports the local economy but also ensures strict quality control and quick response times for custom and standard conveyor solutions. This dedication to quality and service has established Hytrol as a leading conveyor manufacturer, trusted by businesses worldwide for efficient and reliable material handling systems.
Gravity conveyors offer several significant advantages, making them a popular choice for various material handling applications. Firstly, they are cost-effective, both in terms of initial investment and operational costs, as they do not require power to operate. This aspect also makes them environmentally friendly and suitable for operations looking to reduce their energy consumption. Secondly, gravity conveyors are known for their simplicity and reliability, with fewer moving parts compared to powered systems, leading to lower maintenance requirements and longer service life. Additionally, they are highly versatile and can be easily configured or reconfigured to meet the changing needs of a facility, including the addition of curves, merges, and gates. Their ease of installation and ability to accommodate a wide range of product sizes and weights further enhance their utility in diverse settings, from warehouses and distribution centers to manufacturing plants. Overall, gravity conveyors provide an efficient, flexible, and cost-effective solution for transporting goods within various material handling environments.
Last Updated on May 29, 2024 by Jordan Smith
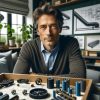
Jordan Smith, a seasoned professional with over 20 years of experience in the conveyor system industry. Jordan’s expertise lies in providing comprehensive solutions for conveyor rollers, belts, and accessories, catering to a wide range of industrial needs. From initial design and configuration to installation and meticulous troubleshooting, Jordan is adept at handling all aspects of conveyor system management. Whether you’re looking to upgrade your production line with efficient conveyor belts, require custom conveyor rollers for specific operations, or need expert advice on selecting the right conveyor accessories for your facility, Jordan is your reliable consultant. For any inquiries or assistance with conveyor system optimization, Jordan is available to share his wealth of knowledge and experience. Feel free to reach out at any time for professional guidance on all matters related to conveyor rollers, belts, and accessories.