Innovative Solutions: Hytrol Powered Roller Conveyors
Hytrol stands at the forefront of the conveyor industry, renowned for its innovative solutions that streamline operations across countless warehouses and distribution centers. Among its extensive product lineup, the Hytrol powered roller conveyor emerges as a pivotal tool in the realm of material handling and logistics. These conveyors are engineered to facilitate the smooth and efficient movement of goods, ranging from small parcels to bulky pallets, through various stages of processing and distribution. The integration of Hytrol’s powered roller conveyors into a facility’s workflow not only optimizes productivity but also significantly enhances operational reliability and flexibility. This makes them an indispensable asset in today’s fast-paced and demanding logistics environments, where efficiency and downtime reduction are paramount.
What is Hytrol Powered Roller Conveyor
Hytrol’s powered roller conveyor systems stand out in the material handling industry for their efficiency, reliability, and adaptability. These systems are designed to meet the diverse needs of various industries, from e-commerce fulfillment centers to manufacturing plants. Understanding the features of Hytrol powered roller conveyors and how they differ from gravity conveyors is crucial for businesses looking to optimize their operations.
Features of Hytrol Powered Roller Conveyors:
- Motorized Rollers: Unlike gravity conveyors that rely on slope and manual force, Hytrol powered roller conveyors use motorized rollers to move goods, providing consistent and controllable movement.
- Adjustable Speeds: These conveyors offer adjustable speeds, allowing for customized control over the flow of materials, which is essential for sensitive or time-bound operations.
- Load Capacity: Hytrol’s systems are designed to handle a wide range of load capacities, accommodating everything from lightweight packages to heavy pallets.
- Integration Capabilities: Easily integrated with other systems and technologies, Hytrol powered roller conveyors can be part of a complex automated solution, enhancing overall efficiency.
- Durability: Built with high-quality materials, these conveyors are designed for longevity and minimal maintenance, even in demanding industrial environments.
Differences from Gravity Conveyors:
- Power Source: Gravity conveyors rely on gravity and manual effort, while Hytrol’s powered systems use electric motors for movement.
- Control: Powered conveyors offer precise control over speed and direction, unlike gravity conveyors that depend on the slope and manual intervention.
- Flexibility in Layout: Hytrol’s powered systems can move goods uphill, horizontally, and around curves, providing more layout flexibility than gravity conveyors.
- Operational Efficiency: Powered roller conveyors can operate continuously, moving goods without manual assistance, leading to higher operational efficiency.
- Application Range: While gravity conveyors are typically used for simple, straight-line movement, powered roller conveyors can be customized for complex routing and sorting.
Key Advantages in Various Industries:
- E-Commerce: In fulfillment centers, Hytrol powered roller conveyors streamline the picking and packing process, significantly reducing order processing times.
- Manufacturing: These conveyors facilitate the smooth movement of parts and assemblies through production lines, enhancing efficiency and reducing manual handling.
- Distribution: In distribution centers, Hytrol’s systems optimize the sorting and routing of products, ensuring timely and accurate delivery.
- Pharmaceuticals: The precise control and gentle handling offered by powered roller conveyors are ideal for sensitive pharmaceutical products, maintaining integrity from production to packaging.
- Food and Beverage: Hytrol conveyors can be customized with food-grade materials and washdown capabilities, ensuring safe and hygienic handling of food products.
By integrating Hytrol powered roller conveyor systems into their operations, businesses across various industries can achieve significant improvements in efficiency, productivity, and reliability. These systems not only enhance material handling processes but also contribute to the overall optimization of supply chain operations.
Key Components and Specifications of Hytrol Powered Roller Conveyors
Delving into the key components and specifications of Hytrol powered roller conveyors reveals the intricate design and engineering that make these systems so effective in various material handling applications. Each component is crucial for the conveyor’s performance, durability, and adaptability to different operational needs.
Key Components of Hytrol Powered Roller Conveyors:
- Motorized Rollers: The heart of the Hytrol powered roller conveyor, these rollers are equipped with internal motors that provide the drive force necessary for moving materials along the conveyor path.
- Control Modules: These electronic units regulate the speed, direction, and operation of the motorized rollers, ensuring smooth and efficient conveyor performance.
- Frame and Structure: Made from durable materials like steel or aluminum, the frame supports the conveyor system and withstands the operational load, ensuring stability and longevity.
- Drive Belts: Connecting the motorized rollers to the drive system, these belts transfer power from the motor to the rollers, enabling the movement of goods.
- Sensors and Encoders: Integrated into the conveyor system, these components monitor and control the movement of items, ensuring precise positioning and optimal flow control.
Specifications Found in the Hytrol Conveyor Manual and Catalog:
The Hytrol conveyor manual and catalog provide detailed specifications that are essential for selecting, installing, and maintaining a powered roller conveyor system. These specifications include:
- Load Capacity: Specifies the maximum weight the conveyor can handle per roller, ensuring that the system is suitable for the intended application.
- Conveyor Speed: Details the range of speeds at which the conveyor can operate, allowing for customization based on the requirements of the material handling process.
- Roller Diameter and Spacing: Indicates the size of the rollers and the distance between them, which affects the types of items the conveyor can transport and their stability during movement.
- Conveyor Length and Width: Provides the dimensions of the conveyor, helping in planning the layout and integration of the system into existing operations.
- Electrical Requirements: Outlines the power needs and connectivity options for the conveyor, ensuring compatibility with the facility’s electrical infrastructure.
Understanding the key components and specifications of the Hytrol powered roller conveyor is crucial for businesses looking to invest in a reliable and efficient material handling solution. These details, found in the Hytrol conveyor manual and catalog, guide users in selecting the right conveyor system that meets their specific operational needs, ensuring optimal performance and a high return on investment.
Product Range and Applications of Hytrol Powered Roller Conveyors
The Hytrol powered roller conveyor lineup is diverse, catering to a wide array of material handling needs across various industries. Each model is designed with specific applications in mind, ensuring that businesses can find a solution that perfectly fits their operational requirements.
Different Models of Hytrol Powered Roller Conveyors:
- 138-NSP: Ideal for light-duty applications, this model features non-powered rollers with a simple chain drive mechanism, suitable for small packages and lightweight items.
- 190-NSP: A medium-duty conveyor that offers versatility and durability, perfect for handling boxes, cartons, and other moderate-weight goods in distribution centers.
- 190-LR: This belt-driven live roller conveyor is designed for heavier loads, providing reliable service in manufacturing plants where parts, components, and assemblies need to be moved.
- 190-LRC: A curved belt-driven live roller conveyor that allows for directional changes in the material flow, ideal for complex conveyor layouts in warehousing and distribution.
- ABLR: A heavy-duty live roller conveyor that is perfect for moving large and heavy items such as pallets and drums, commonly used in manufacturing and shipping industries.
Applications and Industries:
- E-Commerce Fulfillment: The 190-NSP and 190-LR models are extensively used in e-commerce fulfillment centers for sorting and transporting a wide range of products to packing stations.
- Manufacturing: The ABLR and 190-LR conveyors are ideal for assembly lines in manufacturing plants, moving components through various stages of assembly and quality control.
- Distribution and Logistics: The 190-LRC and 190-NSP models are commonly found in distribution centers, facilitating the efficient movement of goods from storage areas to loading docks.
- Pharmaceuticals: In the pharmaceutical industry, the 138-NSP and 190-NSP conveyors are used for transporting sensitive products under controlled conditions, ensuring safety and compliance with health regulations.
- Food and Beverage: The ABLR model, with its capability to handle heavy loads, is suitable for food and beverage manufacturing, moving bulk ingredients, and finished products through processing and packaging lines.
The Hytrol powered roller conveyor range offers solutions that enhance efficiency, reduce manual labor, and improve the overall flow of goods within various operational environments. From light-duty tasks in e-commerce fulfillment centers to heavy-duty applications in manufacturing and distribution, Hytrol’s conveyors are engineered to meet the diverse needs of modern industries, ensuring smooth and efficient material handling processes.
Pricing and Availability of Hytrol Powered Roller Conveyors
When considering the integration of a Hytrol powered roller conveyor into your material handling system, understanding the pricing and availability is crucial. The cost of these conveyors can vary widely based on several factors, and knowing these can help you make an informed decision that ensures value for your investment.
Factors Influencing Costs:
- Model and Specifications: The specific model of the Hytrol powered roller conveyor, such as the 138-NSP or the ABLR, significantly impacts the price. Higher capacity and more advanced features typically lead to higher costs.
- Length and Width: The dimensions of the conveyor affect the price, with longer and wider conveyors requiring more materials and thus costing more.
- Customization: Any modifications or custom features added to the standard models to meet specific operational needs can increase the price.
- Control Systems and Accessories: The inclusion of advanced control systems, sensors, and additional Hytrol Conveyor accessories for enhanced functionality can also add to the overall cost.
- Installation and Integration: The complexity of installing and integrating the conveyor into your existing system can influence the final price, especially if extensive modifications are required.
Tips for Getting the Best Value:
- Assess Your Needs: Clearly define your material handling requirements to avoid over-specifying or under-specifying your conveyor system. This ensures you pay only for the features you need.
- Consider Total Cost of Ownership: Look beyond the initial purchase price and consider factors such as energy efficiency, maintenance costs, and the potential for future upgrades. A slightly higher initial investment in a more efficient or durable system can lead to savings over time.
- Explore Financing Options: Hytrol and its network of integration partners may offer financing options that can help spread out the cost of the conveyor system, making it more manageable for your business.
- Leverage Hytrol’s Expertise: Utilize the knowledge and experience of Hytrol’s engineers and sales team to help design the most cost-effective solution for your needs. They can provide insights into the best models and configurations for your application.
- Plan for Scalability: If you anticipate future expansion, consider a modular Hytrol powered roller conveyor system that can be easily expanded or reconfigured. This flexibility can save significant costs and disruption compared to purchasing a new system.
By carefully considering these factors and tips, you can ensure that your investment in a Hytrol powered roller conveyor brings the best possible value and supports your operational goals effectively.
Installation, Maintenance, and Parts of Hytrol Powered Roller Conveyors
Proper installation, regular maintenance, and timely repairs are crucial for maximizing the lifespan and efficiency of your Hytrol powered roller conveyor. By adhering to the guidelines provided in the Hytrol conveyor parts manual and utilizing the comprehensive parts list, you can ensure your conveyor system operates at peak performance.
Installation Guidance:
The installation of a Hytrol powered roller conveyor should follow the detailed procedures outlined in the Hytrol conveyor parts manual. This manual provides step-by-step instructions, ensuring that each component is correctly assembled and integrated into your existing system. Key considerations include aligning the conveyor for smooth operation, securely fastening all parts, and ensuring that electrical connections comply with safety standards. It’s often beneficial to involve Hytrol’s certified technicians or authorized integration partners to facilitate a seamless installation process.
Maintenance Tips:
- Regular Inspections: Conduct routine inspections to identify any signs of wear or damage to the rollers, belts, and electrical components. Early detection of potential issues can prevent costly downtime.
- Lubrication: Keep moving parts, such as rollers and bearings, properly lubricated according to the specifications in the Hytrol conveyor parts manual. This reduces friction and wear, extending the life of these components.
- Cleanliness: Maintain cleanliness along the conveyor path to prevent debris accumulation, which can hinder roller movement and affect the conveyor’s efficiency.
- Belt Tension: Regularly check the tension of drive belts to ensure they are operating within the recommended parameters. Incorrect tension can lead to premature wear and reduced performance.
- Electrical System Checks: Monitor the conveyor’s electrical systems, including sensors and control modules, to ensure they are functioning correctly. Faulty electrical components can lead to operational disruptions.
Utilizing the Hytrol Conveyor Parts List:
The Hytrol conveyor parts list is an essential resource for maintaining and repairing your powered roller conveyor. This comprehensive list includes detailed diagrams and part numbers for every component of your conveyor system, making it easier to identify and order the correct replacement parts. When a part needs to be replaced, refer to the parts list to ensure compatibility and avoid the installation of incorrect components, which could cause further damage or reduce the system’s efficiency.
By following the installation guidance, adhering to maintenance best practices, and utilizing the Hytrol conveyor parts list for repairs, you can significantly enhance the reliability and longevity of your Hytrol powered roller conveyor. These proactive steps not only ensure optimal performance but also contribute to a safer and more productive material handling environment.
Choosing the Right Hytrol Powered Roller Conveyor for Your Needs
Selecting the appropriate Hytrol powered roller conveyor for your specific application involves careful consideration of various factors. Understanding these elements can help you make an informed decision, ensuring that the conveyor system you choose aligns perfectly with your operational requirements and objectives.
Factors to Consider:
- Load Characteristics: Consider the size, weight, and type of materials or products the conveyor will handle. Hytrol offers different powered roller conveyors designed to accommodate everything from lightweight packages to heavy pallets.
- Throughput Requirements: Assess the volume of goods that need to be moved over a particular period. Higher throughput rates might necessitate a conveyor with faster speeds and more robust construction.
- Operational Environment: The working conditions, such as temperature, humidity, and exposure to chemicals or contaminants, can influence the choice of conveyor. Some Hytrol powered roller conveyors are specifically designed to withstand harsh environments.
- Integration with Existing Systems: Ensure that the conveyor can be seamlessly integrated with your current material handling systems, both physically and in terms of software and controls.
- Future Scalability: Consider your long-term needs and potential for growth. A modular Hytrol powered roller conveyor system can be expanded or reconfigured as your business evolves.
Leveraging Hytrol Conveyor Locations and Expert Assistance:
Hytrol’s extensive network of authorized dealers and integration partners is a valuable resource when selecting the right conveyor system. These experts can provide:
- Personalized Consultations: Engage with Hytrol professionals who can assess your specific needs and recommend the most suitable powered roller conveyor models.
- Site Visits: In many cases, Hytrol representatives or authorized dealers can conduct site visits to better understand your operational layout and challenges.
- Custom Solutions: Leverage their expertise to customize a Hytrol powered roller conveyor system that addresses your unique requirements, from custom lengths and widths to specialized controls and software integration.
- Demonstrations and Prototyping: Some Hytrol locations or partners may offer demonstrations or prototyping services to give you a clearer picture of how a particular conveyor model would function in your facility.
- After-Sales Support: Benefit from ongoing support, training, and maintenance services to ensure your Hytrol powered roller conveyor continues to operate efficiently and effectively.
By carefully considering these factors and utilizing the wealth of knowledge and support available through Hytrol’s network, you can confidently choose the right powered roller conveyor system that will enhance your operations and support your business’s growth and success.
FAQs About Hytrol Powered Roller Conveyor
A powered roller conveyor is a material handling system designed to move goods efficiently through a manufacturing or distribution facility. Unlike gravity conveyors that rely on gravity to move items, powered roller conveyors use electric motors to drive the movement of rollers. This automation allows for the controlled transportation of various items, from small packages to large pallets, across flat or inclined paths. The versatility and efficiency of powered roller conveyors make them a vital component in the logistics and manufacturing sectors, facilitating smooth operations, reducing manual labor, and enhancing workflow.
Hytrol Conveyor Company, Inc., a leader in the conveyor industry, manufactures its products in Jonesboro, Arkansas, USA. With a strong commitment to innovation and quality, Hytrol has established a state-of-the-art manufacturing facility that spans over 700,000 square feet. This facility is equipped with advanced machinery and technology, enabling Hytrol to produce a wide range of conveyor systems and accessories. The company’s dedication to producing high-quality, American-made products has solidified its reputation in the material handling industry, making it a preferred choice for businesses seeking reliable conveyor solutions.
The conveyor manufacturing industry is competitive, with several key players known for their innovation, quality, and service. The top 5 conveyor manufacturers typically include:
Hytrol Conveyor Company: Renowned for its comprehensive range of conveyor systems tailored to various industries, Hytrol is a leading name in the field, known for its durable and efficient designs.
Dorner Conveyors: Dorner is recognized for its precision and customizable conveyor solutions, catering to small part handling and complex industrial applications.
Interroll: Specializing in rollers, drives, and modules for dynamic storage, Interroll is known for its energy-efficient and scalable solutions.
Daifuku: As one of the largest material handling companies, Daifuku offers a wide range of automated systems, including conveyors for different sectors.
BEUMER Group: BEUMER is a global provider of intralogistics systems for conveying, loading, palletizing, packaging, and more, known for its innovative and sustainable solutions.
These manufacturers stand out for their commitment to technological advancement, customer service, and the ability to cater to the diverse needs of industries worldwide.
The capacity of Hytrol conveyors varies widely depending on the specific model and application. Hytrol offers a range of conveyor systems designed to accommodate different load capacities and operational requirements. For instance, light-duty roller conveyors might handle loads up to 15 pounds per roller, while heavy-duty models can manage significantly more, with some capable of supporting up to 250 pounds per roller or more. The 190-NSP and 190-NSPEZ models, for example, are popular for their robustness, catering to various industrial needs. When selecting a Hytrol conveyor, it’s crucial to consider the weight, size, and type of materials to be transported to ensure optimal performance and longevity of the system. Hytrol provides detailed specifications and expert guidance to help customers choose the right conveyor for their specific needs.
Last Updated on May 29, 2024 by Jordan Smith
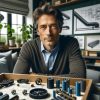
Jordan Smith, a seasoned professional with over 20 years of experience in the conveyor system industry. Jordan’s expertise lies in providing comprehensive solutions for conveyor rollers, belts, and accessories, catering to a wide range of industrial needs. From initial design and configuration to installation and meticulous troubleshooting, Jordan is adept at handling all aspects of conveyor system management. Whether you’re looking to upgrade your production line with efficient conveyor belts, require custom conveyor rollers for specific operations, or need expert advice on selecting the right conveyor accessories for your facility, Jordan is your reliable consultant. For any inquiries or assistance with conveyor system optimization, Jordan is available to share his wealth of knowledge and experience. Feel free to reach out at any time for professional guidance on all matters related to conveyor rollers, belts, and accessories.