The Impact of Idler Roller on Conveyor System Performance
Idler rollers are fundamental components in the realm of mechanical engineering and industrial design, playing a pivotal role in the smooth operation of conveyor systems and other machinery. Essentially, an idler roller is a type of wheel or gear that rotates to support and guide belts, chains, or other flexible materials, ensuring their efficient and uninterrupted movement across various applications. These rollers are critical in minimizing friction and wear, significantly enhancing the longevity and performance of mechanical systems. Found in a wide array of industries, including manufacturing, mining, automotive, and logistics, idler rollers are indispensable for their ability to facilitate the seamless transport of goods and materials, thereby optimizing productivity and operational efficiency. Their universal presence across different sectors underscores their importance in the modern industrial landscape.
The Basics of Idler Roller
Idler rollers are integral components within mechanical systems, designed to facilitate the movement and management of materials. These rollers serve a variety of functions, each contributing to the efficiency and reliability of conveyor systems and other machinery where they are employed. Understanding the definition, function, and significance of idler rollers is crucial for appreciating their role in industrial operations.
Definition and Function of Idler Rollers in Mechanical Systems
- Support and Guide Belts: Idler rollers provide critical support to conveyor belts, ensuring they remain aligned and taut during operation, preventing sagging and material spillage.
- Reduce Friction: By serving as the interface between the conveyor belt and the structure, idler rollers minimize friction, allowing for smoother belt movement.
- Facilitate Material Handling: They are essential in material handling systems, enabling the efficient transport of goods across different stages of production or distribution.
- Enhance System Longevity: By reducing wear on conveyor belts and associated machinery, idler rollers contribute to the extended lifespan of the entire system.
- Adaptability: Idler rollers can be customized to fit various conveyor widths, speeds, and material types, making them versatile components of many mechanical systems.
- Load Distribution: They help evenly distribute the weight of materials on the conveyor belt, which is crucial for maintaining balance and preventing undue stress on the system.
- Energy Efficiency: Properly functioning idler rollers can reduce the energy consumption of conveyor systems by allowing for smoother and less resistive operation.
- Maintenance and Replacement: Designed for easy maintenance and replacement, idler rollers ensure minimal downtime for mechanical systems, promoting continuous productivity.
The Significance of Idler Rollers in Ensuring the Efficient Operation of Conveyor Systems and Other Machinery
- Operational Efficiency: Idler rollers are pivotal in maintaining the high operational efficiency of conveyor systems, directly impacting the throughput and productivity of industrial operations.
- Safety: By ensuring the stable and predictable movement of conveyor belts, idler rollers contribute to the safety of the working environment, reducing the risk of accidents.
- Cost Savings: The energy efficiency and reduced wear on equipment facilitated by idler rollers translate into significant cost savings over the lifespan of the system.
- Quality Control: In applications where material quality is paramount, idler rollers help maintain the integrity of conveyed materials by preventing damage during transport.
- Noise Reduction: They contribute to a quieter operation of machinery, which is beneficial for meeting workplace regulations and improving the working environment.
- Versatility in Applications: From mining and agriculture to manufacturing and packaging, idler rollers are utilized across a broad spectrum of industries, underscoring their versatility.
- Customization and Flexibility: The ability to customize idler rollers for specific applications allows for the optimization of conveyor systems to meet unique operational requirements.
- Innovation and Development: Continuous advancements in idler roller technology contribute to the development of more efficient, durable, and reliable conveyor systems, driving progress in various sectors.
Idler rollers are not just simple components; they are the backbone of numerous mechanical systems, ensuring their efficient, safe, and cost-effective operation. Their design and functionality have a profound impact on the productivity and operational capabilities of industries worldwide.
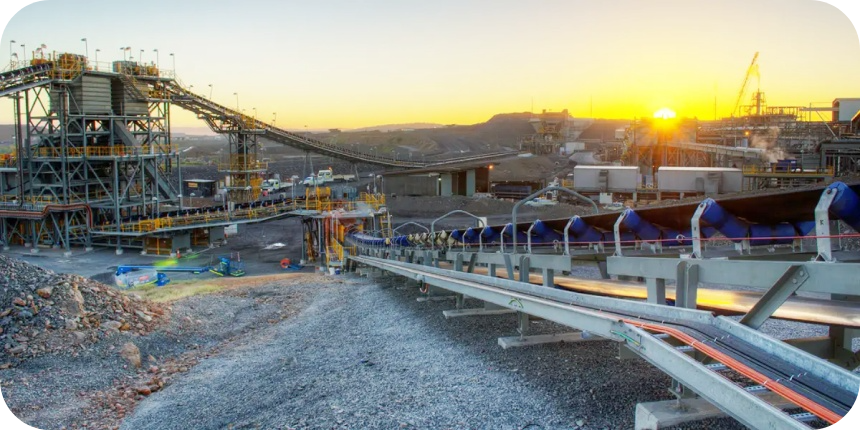
Types of Idler Roller
The diversity in idler roller types underscores their adaptability and importance across various industries. Each type of idler roller, from standard to specialized designs like heavy-duty or dead shaft idler rollers, offers unique benefits and is engineered to meet specific operational demands.
Standard Idler Rollers
Standard idler rollers are foundational to the operation of conveyor systems, providing reliable and efficient support for the conveyor belt and the materials it carries. These rollers are characterized by their versatility and durability, making them suitable for a wide range of applications.
- Ubiquitous Use: The backbone of countless conveyor systems, ensuring smooth operations across various sectors.
- Material Flexibility: Predominantly crafted from steel or aluminum, balancing strength with weight for optimal performance.
- Moderate Load Support: Designed to accommodate the everyday demands of material transport with ease.
- Adaptable Design: Their standardization does not hinder their ability to be tailored to specific belt widths and operational speeds.
- Ease of Maintenance: Simplified design allows for quick installation and replacement, reducing system downtime.
- Economic Viability: Provides a cost-effective solution for conveyor system requirements without compromising quality.
- Broad Applications: From manufacturing lines to distribution centers, they play a crucial role in material handling and logistics.
- Operational Efficiency: Their reliability and durability contribute significantly to the overall efficiency of conveyor systems.
Heavy-Duty Idler Rollers
Heavy-duty idler rollers are engineered to withstand the rigors of extreme operational conditions, including heavy loads and harsh environments. Their robust construction ensures longevity and reliability where it’s needed most.
- Superior Durability: Crafted to endure the toughest conditions, from abrasive materials to extreme climates.
- Reinforced Materials: Utilizing hardened steel or similar composites for unmatched strength and resilience.
- High Load Capacity: Capable of supporting substantial weights, essential for mining and construction applications.
- Environmental Adaptability: Designed to operate flawlessly in environments that would compromise lesser rollers.
- Extended Lifespan: The use of premium materials and design principles extends their operational life significantly.
- Specialized Applications: The go-to choice for sectors that demand the utmost in durability and performance.
- Low Maintenance Needs: Despite their rugged design, they are built for longevity with minimal upkeep.
- Customizable Features: Available in various dimensions and specifications to meet the unique demands of heavy-duty operations.
- Energy Efficient Operation: Their efficiency in operation can lead to reduced power consumption, even under heavy loads.
Dead Shaft Idler Rollers
Dead shaft idler rollers feature a unique design where the shaft remains stationary while the roller body rotates around it. This design offers several advantages in precision and load distribution.
- Innovative Design: The stationary shaft allows for a unique distribution of weight and operational stress.
- Enhanced Load Distribution: Provides even load distribution, crucial for high-speed and precision applications.
- Operational Precision: The fixed shaft contributes to greater control and accuracy in roller movement.
- High-Speed Compatibility: Excellently suited for applications requiring rapid material transport.
- Durability Plus: The design inherently enhances the roller’s durability and lifespan.
- Ideal for Specific Industries: Particularly favored in the printing and packaging sectors for their precision.
- Simplified Maintenance: Bearing replacement and maintenance are streamlined, thanks to the dead shaft design.
- Tailored Solutions: Offers customization options to meet specific operational requirements, including various coatings for added functionality.
Rubber-Coated and Ceramic Idler Rollers
Rubber-coated and ceramic idler rollers provide specialized solutions where additional protection and performance are required. These coatings offer benefits in noise reduction, impact absorption, and resistance to harsh chemicals.
- Material Advantages: Both rubber and ceramic coatings bring distinct benefits, including enhanced durability and operational quietness.
- Impact Protection: Rubber coatings excel in absorbing the impact, safeguarding the conveyor belt and materials.
- Chemical and Temperature Resistance: Ceramic rollers stand up to aggressive chemicals and extreme temperatures without compromise.
- Operational Quietness: Rubber coatings significantly reduce noise, contributing to a more pleasant and compliant work environment.
- Extended Wear Life: Both materials are highly resistant to wear, prolonging the life of the rollers and the conveyor belt.
- Critical Applications: Especially suited for industries where the integrity of conveyed materials is paramount.
- Customization Options: Available in a variety of sizes and coating thicknesses, ensuring the right fit for specific operational needs.
Each type of idler roller serves a specific purpose, enhancing the efficiency, safety, and reliability of conveyor systems and other machinery. Understanding the characteristics and applications of these rollers is crucial for selecting the right idler roller for your needs.
Specialized Idler Roller
Specialized idler rollers are designed to meet specific operational needs in various industrial applications. These rollers are tailored to enhance performance, durability, and efficiency in unique environments or under particular conditions. From heavy machinery like excavators to precise conveyor belt alignment, specialized idler rollers play crucial roles.
Idler Rollers for Excavators
Idler rollers for excavators are critical components designed to support and guide the track chain in heavy machinery. Their role is pivotal in ensuring the smooth operation and longevity of excavators operating in challenging environments.
- Support Track Chain: Provide essential support to the track chain, ensuring stable movement.
- Guide Tracks: Help guide the excavator tracks as they move over uneven terrain.
- Absorb Impact: Reduce the impact on the tracks when navigating rough surfaces, protecting the machinery.
- Enhance Durability: Specifically designed to withstand harsh conditions found in construction and mining sites.
- Prevent Track Slippage: Maintain the correct tension in the tracks, preventing slippage or derailing.
- Reduce Wear: Minimize the wear on tracks and track links, extending their service life.
- Improve Efficiency: Facilitate smoother operation of the excavator, enhancing operational efficiency.
- Customized Solutions: Available in various sizes and materials to match different excavator models and applications.
Track Rollers vs. Idler Rollers
While both track rollers and idler rollers are essential for the operation of tracked vehicles and machinery, they serve different functions. Understanding their differences is crucial for proper maintenance and operation.
Self-Aligning Idler Rollers
Self-aligning idler rollers are ingeniously designed to automatically maintain the alignment of conveyor belts, preventing slippage and misalignment that can lead to operational disruptions.
- Automatic Adjustment: Automatically adjust their position to maintain belt alignment.
- Prevent Belt Drift: Specifically designed to counteract the forces that cause conveyor belts to drift off course.
- Reduce Maintenance: Minimize the need for manual adjustments and inspections.
- Enhance Operational Efficiency: By keeping the belt aligned, they ensure smooth and efficient conveyor operations.
- Prolong Belt Life: Prevent uneven wear on the conveyor belt, extending its lifespan.
- Versatile Application: Suitable for various conveyor systems, regardless of belt width or speed.
- Innovative Design: Utilize a pivoting mechanism and guide rollers to steer the belt back to its correct path.
- Cost-Effective: By reducing maintenance and prolonging belt life, they offer a cost-effective solution for conveyor system management.
Specialized idler rollers, whether for heavy machinery like excavators or for precise applications like conveyor belt alignment, demonstrate the engineering ingenuity in adapting to specific industrial needs. Their design and functionality are pivotal in enhancing the performance and reliability of the equipment they serve.
Idler Roller in Automotive Applications
The integration of idler roller in automotive applications underscores their versatility and essential role beyond industrial conveyor systems. Their application in automotive training and simulation tools, particularly in car mechanic simulators, highlights the importance of understanding idler roller mechanics for future automotive technicians.
Idler Roller Car Mechanic Simulator
The Car Mechanic Simulator series has become an invaluable educational tool, offering a deep dive into the intricacies of car mechanics, including the pivotal role of idler rollers.
- Realistic Simulation: Provides a hands-on experience in diagnosing and fixing issues related to idler rollers in a virtual environment.
- Understanding Functionality: Helps users comprehend the critical function of idler rollers in vehicle belt systems, ensuring proper tension and alignment.
- Diagnostic Skills: Enhances diagnostic abilities by allowing users to identify common problems associated with faulty idler rollers, such as belt slippage or noise.
- Repair Techniques: Teaches effective repair and replacement techniques for idler rollers, crucial for maintaining vehicle performance.
- Component Identification: Aids in the identification of different types of idler rollers used in various vehicle models, enhancing parts knowledge.
- Interactive Learning: Engages users with interactive tasks involving idler rollers, promoting active learning and retention.
- Technical Proficiency: Builds technical proficiency in handling idler rollers, preparing users for real-world automotive repair scenarios.
- Safety Awareness: Emphasizes the importance of safety procedures when working with idler rollers and related components in automotive systems.
Idler Rollers in Car Mechanic Simulator 2021
The latest iteration of the simulator, Car Mechanic Simulator 2021, introduces several updates and changes regarding idler rollers, reflecting the advancements in automotive technology and repair techniques.
- Enhanced Realism: Improved graphics and physics engine offer a more realistic experience in diagnosing and repairing idler roller issues.
- Updated Models: Includes the latest car models and their specific idler roller configurations, providing up-to-date training material.
- Advanced Diagnostics: Features more sophisticated diagnostic tools for identifying issues with idler rollers, aligning with current automotive standards.
- Comprehensive Repair Options: Expands the range of repair options for idler rollers, including more detailed procedures and customization choices.
- Interactive Challenges: Introduces new challenges and scenarios focused on idler rollers, testing users’ skills and knowledge in a dynamic environment.
- Educational Content: Offers enriched educational content, including tutorials and guides on the latest best practices in idler roller maintenance and repair.
- Community Engagement: Allows users to share tips, tricks, and repair strategies for idler rollers within an active online community.
- Feedback System: Implements a feedback system for users to report and learn from real-life idler roller issues, enhancing the learning experience.
By incorporating idler rollers into automotive applications and simulations, these tools not only educate aspiring mechanics but also highlight the continuous evolution of automotive technology. Understanding and mastering the function and repair of idler rollers through such simulators can significantly impact vehicle maintenance and performance, preparing users for the complexities of modern automotive systems.
Request a Quote: Complete the form below to receive a customized quote for our conveyor rollers.
Technical Specifications and Standards of Idler Roller
The technical specifications and standards for idler rollers are crucial for ensuring quality, safety, and compatibility across various applications and international borders. These guidelines help maintain a uniform approach to the design, manufacturing, and trade of idler rollers.
HS Code for Idler Rollers
The Harmonized System (HS) code is a standardized numerical method of classifying traded products. The HS code for idler rollers plays a significant role in international trade by:
- Facilitating Trade: It simplifies the process of importing and exporting idler rollers by providing a universally recognized classification.
- Determining Tariffs: Helps in determining the applicable tariffs and taxes for idler rollers in different countries, affecting cost calculations.
- Compliance: Ensures that idler rollers meet the regulatory requirements of the importing country, avoiding legal issues.
- Tracking: Allows for the tracking of idler roller trade statistics globally, offering insights into market trends and demands.
- Quality Control: Assists in maintaining quality standards by ensuring that imported or exported idler rollers adhere to specific classifications.
- Customs Clearance: Streamlines the customs clearance process by providing clear, predefined categories for idler rollers.
- Market Analysis: Enables businesses to conduct market analysis and competitive research based on the trade flow of idler rollers.
- Product Identification: Simplifies the identification process for companies dealing with multiple parts and components, including idler rollers.
- Global Standardization: Promotes global standardization and understanding, facilitating easier communication and negotiation in international trade.
Design and Manufacturing Standards
The design and manufacturing of idler rollers are governed by various international and national standards to ensure their reliability, durability, and safety. These standards cover:
- Material Quality: Specifies the quality of materials used in idler and roller, ensuring they can withstand operational stresses.
- Dimensional Accuracy: Ensures that idler rollers are manufactured to precise dimensions for compatibility with conveyor systems.
- Load Capacity: Defines the minimum load capacities to guarantee that idler rollers can support the expected weights without failure.
- Environmental Resistance: Establishes requirements for idler rollers to perform under different environmental conditions, including temperature extremes and corrosive environments.
- Safety Guidelines: Provides guidelines to minimize risks associated with the operation and maintenance of idler rollers.
- Performance Testing: Outlines testing procedures to verify the performance and durability of idler rollers under simulated operational conditions.
- Manufacturing Processes: Recommends best practices in manufacturing processes to ensure the high quality and consistency of idler rollers.
- Quality Assurance: Includes quality assurance protocols to ensure that every idler roller meets the set standards before being deployed.
- Innovation and Improvement: Encourages continuous innovation and improvement in idler roller design and manufacturing to meet evolving industry needs.
Adhering to these technical specifications and standards is essential for manufacturers, suppliers, and users of idler rollers. It not only ensures the high quality and performance of idler rollers but also facilitates their smooth integration into various mechanical systems and applications worldwide.
How to Choose the Right Idler Roller
Selecting the appropriate idler roller is critical for the efficiency, longevity, and safety of conveyor systems. The decision involves considering a range of factors to ensure the idler roller meets the specific requirements of the application. Here are ten essential factors to consider when choosing the right idler roller for specific applications:
- Load Capacity: Evaluate the maximum load the idler roller must support. Choosing a roller with an appropriate load capacity is crucial to prevent premature failure.
- Belt Width: The width of the conveyor belt dictates the size of the idler roller. The roller must be compatible with the belt width to ensure effective support and alignment.
- Material Type: The construction material of the idler and roller affects its durability, weight, and suitability for different environments. Common materials include steel, aluminum, and plastic, each offering distinct advantages.
- Operational Speed: Consider the speed at which the conveyor will operate. High-speed applications may require specially designed idler rollers to reduce vibration and wear.
- Environmental Conditions: The operating environment, including temperature, humidity, and exposure to chemicals or corrosives, influences the choice of idlers and rollers material and coating.
- Belt Type: The type of conveyor belt (flat, modular, fabric, etc.) can impact the idler roller design needed for optimal performance and longevity.
- Impact Level: In applications where the conveyor system experiences high levels of impact (e.g., loading zones), selecting idler rollers designed to absorb and dissipate impact forces is essential.
- Maintenance Requirements: Consider the ease of maintenance and replacement. Idler rollers designed for easy access and quick replacement can significantly reduce downtime.
- Energy Efficiency: Some idler rollers are designed to minimize friction and energy consumption. For operations looking to reduce energy costs, these rollers can be an ideal choice.
- Regulatory and Safety Standards: Ensure the selected rollers and idlers comply with industry regulations and safety standards. Compliance not only ensures the safety of operations but also helps avoid potential legal issues.
By carefully considering these factors, you can select an idler roller that not only meets the specific needs of your application but also contributes to the overall efficiency and effectiveness of your conveyor system. The right idler roller selection is a critical step in optimizing conveyor performance and extending the lifespan of the system.
FAQs about Idler Roller
An idler roll, commonly referred to as an idler roller, is a crucial component in conveyor systems and various machinery. It is a cylindrical rod that serves multiple purposes, primarily to support and guide conveyor belts, chains, or other flexible materials. Idler rolls are strategically placed along the length of the conveyor system to ensure the belt remains tensioned and aligned, facilitating smooth and efficient material transport. These rollers are designed to rotate freely, reducing friction and wear on the conveyor belt, thereby extending the belt’s lifespan and enhancing the overall efficiency of the conveyor system. The design and material of idler rolls can vary significantly, depending on their specific application, including factors like load capacity, operational speed, and environmental conditions. Their simplicity in design belies their importance in the operation of conveyor systems, playing a vital role in industries such as mining, manufacturing, logistics, and packaging.
Idlers in conveyor systems serve several essential functions that contribute to the efficient operation of the conveyor. Their primary use is to provide support to the conveyor belt and the materials being transported. This support helps maintain the belt’s integrity and prevents sagging, which can lead to uneven material distribution and potential operational issues. Additionally, idlers help to control the belt’s tension and alignment, ensuring that it runs smoothly and stays on its intended path. This alignment is critical to prevent the belt from slipping off the rollers or becoming misaligned, which could cause damage to the belt and the conveyor structure. Idlers also play a role in reducing the conveyor system’s overall friction, making it easier for the drive motor to move the belt and, therefore, reducing energy consumption and operational costs. In summary, idlers are indispensable for the smooth, efficient, and cost-effective operation of conveyor systems.
Idler roller conveyors are categorized based on their design, functionality, and the specific applications they serve. The primary types include:
Standard Idler Rollers: The most common type used in various industries for general material handling needs.
Impact Idler Rollers: Designed with a robust build to absorb the impact of heavy or abrasive materials as they are loaded onto the conveyor.
Troughing Idler Rollers: Configured in a trough shape to cradle the conveyor belt and materials, optimizing load support and reducing spillage.
Return Idler Rollers: Positioned along the underside of the conveyor system to support the return path of the belt after it has conveyed materials.
Self-Aligning Idler Rollers: Equipped with a mechanism to automatically adjust the belt’s alignment, preventing drift and ensuring smooth operation.
Rubber-Coated Idler Rollers: Feature a rubber coating to reduce noise, absorb impact, and provide additional grip to prevent slippage.
Guide Idler Rollers: Used to guide the belt and keep it on track, especially in curved sections of the conveyor.
Each type of idler roller conveyor is designed to address specific operational challenges, ensuring the conveyor system functions efficiently under various conditions.
The size of conveyor idler rollers can vary widely depending on the application, the width of the conveyor belt, and the load it is designed to carry. Typically, idler roller diameters can range from as small as 3 inches (about 76 mm) to over 7 inches (about 178 mm) for heavy-duty applications. The length of the idler roller is usually determined by the width of the conveyor belt it supports, with standard sizes ranging from 18 inches (about 457 mm) for narrow belts to 96 inches (about 2438 mm) or more for wide belts used in bulk material handling. The spacing between idler rollers is another critical dimension that varies based on the type of material being conveyed and the load requirements, with closer spacing for heavy or impact loads to provide better support and reduce belt sag. Selecting the appropriate size and spacing of idler rollers is essential for optimizing the performance and longevity of the conveyor system.
Last Updated on July 22, 2024 by Jordan Smith
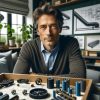
Jordan Smith, a seasoned professional with over 20 years of experience in the conveyor system industry. Jordan’s expertise lies in providing comprehensive solutions for conveyor rollers, belts, and accessories, catering to a wide range of industrial needs. From initial design and configuration to installation and meticulous troubleshooting, Jordan is adept at handling all aspects of conveyor system management. Whether you’re looking to upgrade your production line with efficient conveyor belts, require custom conveyor rollers for specific operations, or need expert advice on selecting the right conveyor accessories for your facility, Jordan is your reliable consultant. For any inquiries or assistance with conveyor system optimization, Jordan is available to share his wealth of knowledge and experience. Feel free to reach out at any time for professional guidance on all matters related to conveyor rollers, belts, and accessories.