Idler Roller Price: Essential Buying Guide
Idler rollers are pivotal components in the realm of conveyor systems, playing a crucial role in the seamless operation and longevity of conveyor belts. These cylindrical bars, strategically positioned along the conveyor’s length, not only support the weight of the materials being transported but also facilitate the smooth and continuous movement of the conveyor belt. The efficiency and durability of a conveyor system are significantly influenced by the quality and design of its idler rollers. Consequently, the idler roller price becomes a key consideration for businesses aiming to optimize their material handling operations without compromising on performance or incurring excessive costs. Understanding the impact of idler rollers on the overall functionality and cost-effectiveness of conveyor systems is essential for making informed decisions regarding their selection and implementation.
What is Idler Rollers and Their Impact on Idler Roller Price
Idler rollers are integral components of conveyor systems, designed to support the conveyor belt and facilitate the transport of materials across various industries. These rollers ensure the stability and efficiency of the conveyor belt, making them indispensable in material handling systems. The idler roller price is influenced by several factors, including the type, material, and specific application requirements.
Definition and Function:
Idler rollers serve multiple functions in conveyor systems. They provide crucial support to the conveyor belt, preventing sagging and ensuring smooth operation. Additionally, they help to distribute the load evenly, reducing wear and tear on the belt. Idler rollers also play a vital role in maintaining the belt’s alignment, preventing slippage and misalignment that could lead to operational disruptions. Specific examples of their function include supporting heavy mining materials, guiding agricultural produce, facilitating the movement of packed goods in warehouses, aiding in the transport of bulk materials in ports, and enhancing the efficiency of assembly lines in manufacturing plants.
Types of Idler Rollers:
- Plain Idler Rollers: The most common type, used primarily to support the belt and materials being conveyed. They are essential for the smooth operation of the conveyor system.
- Tapered Idler Rollers: These are designed to assist in belt tracking, preventing the belt from drifting off its intended path. They are particularly useful in curved sections of the conveyor.
- Rubber-Coated Idler Rollers: These rollers have a rubber coating that provides extra grip and reduces wear on the conveyor belt, ideal for environments where durability is key.
- Rubber Disc Idler Rollers: Equipped with rubber discs, these rollers are adept at preventing material buildup on the roller, which is crucial for maintaining belt cleanliness and efficiency.
- Rubber Screw Idler Rollers: Featuring a helical rubber pattern, these rollers are designed to aid in cleaning the belt and ensuring material does not stick to the belt, enhancing operational efficiency.
- Steel Screw Idler Rollers: Similar to rubber screw idlers but made of steel, these are used in more abrasive environments where additional cleaning action is needed to maintain belt health.
The idler roller price for each type varies based on the materials used, the complexity of the design, and the specific application requirements. Understanding these types and their functions is crucial for making informed decisions that balance cost with operational needs.
Key Factors Influencing Idler Roller Prices
The idler roller price is not a fixed value; it varies significantly based on several crucial factors. Understanding these can help in making informed decisions when purchasing idler rollers for conveyor systems.
Material Type and Quality:
The choice of material for idler rollers plays a pivotal role in determining their price. For instance, steel idler rollers are common due to their strength and durability, making them suitable for heavy-duty applications. Stainless steel rollers, on the other hand, offer corrosion resistance, essential in harsh environments. Rubber-coated rollers reduce wear on the conveyor belt and are ideal for handling delicate materials. Examples of materials include carbon steel for standard applications, stainless steel for food processing conveyors, rubber coatings for noise reduction, polyurethane for gentle material handling, and nylon for lightweight applications.
Size and Dimensions:
The dimensions of an idler roller, including its diameter and wall thickness, directly impact its price. Larger diameters and thicker walls typically indicate a more robust roller capable of handling heavier loads, thus costing more. Examples include small diameter rollers (e.g., 3 inches) for light-duty applications, standard sizes (e.g., 5 inches) for general use, larger diameters (e.g., 6 inches or more) for heavy-duty tasks, varying wall thicknesses for different load capacities, and custom lengths to fit specific conveyor widths.
Customization Options:
Custom features such as the choice of bearing brand, seal type, and wall thickness can also affect the idler roller price. High-quality bearings and specialized seals for extreme environments can increase costs but offer better performance and longevity. Customization might include sealed bearings for dusty environments, high-precision bearings for high-speed applications, thicker walls for increased durability, specialized seals for water exposure, and brand-specific bearings for compatibility with existing systems.
Complexity of Design:
Specialized idler rollers, such as self-aligning or impact idlers, often come with a higher price tag due to their complex design and the specific problems they address. Self-aligning idlers, for example, automatically adjust the belt alignment, reducing maintenance. Impact idlers have reinforced designs to absorb shock at loading points. Examples of design complexity include adjustable idlers for easy alignment, shock-absorbing idlers for load zones, spiral designs for cleaning, troughing idlers for bulk material support, and guide rollers for belt edge support.
Each of these factors contributes to the overall idler roller price, and understanding them can help buyers choose the right idler rollers that meet their system’s needs without exceeding their budget.
Analyzing Idler Roller Prices Around the Globe
The idler roller price varies significantly across different global markets, influenced by a myriad of factors including manufacturing standards, labor costs, and material availability. A closer look at these prices, especially with a focus on regions like India, reveals interesting patterns and insights.
Comparison of Idler Roller Prices in Different Markets:
When comparing idler roller prices, it’s evident that geographical location plays a crucial role. For instance, prices in India might be lower due to the availability of raw materials and lower labor costs. In contrast, European markets might exhibit higher prices due to stringent manufacturing standards and higher labor costs. A table comparing prices across these regions could look like this:
Impact of Manufacturing Standards:
Manufacturing standards significantly influence the idler roller price. For example, rollers produced under ISO standards might be priced higher due to the rigorous quality checks and material specifications. Examples include:
- ISO-certified rollers with precise dimensions and tolerances.
- CEMA standards in the USA, ensuring high durability and performance.
- DIN standards in Germany, known for meticulous engineering.
- AS standards in Australia, focusing on safety and reliability.
- JIS standards in Japan, emphasizing innovation and quality.
Labor Costs:
The cost of labor directly impacts the final price of idler rollers. In countries with higher wages, such as Germany or the USA, the production costs increase, leading to higher prices. Conversely, in regions with lower labor costs, like India or China, products can be priced more competitively.
Material Availability:
The availability and cost of raw materials also play a significant role in determining idler roller prices. For instance:
- Steel prices in China might be lower due to domestic production, reducing roller prices.
- The cost of importing rubber into Europe for rubber-coated rollers increases the final price.
- The availability of high-grade stainless steel in India for food-grade conveyors.
- The impact of tariffs on imported materials in the USA.
- Local availability of polyurethane in Germany for specialized rollers.
Understanding these factors and their impact on idler roller prices can help businesses and consumers make informed decisions, ensuring they find the right balance between cost, quality, and performance requirements.
New vs. Used Idler Rollers: Idler Roller Price Variations
When it comes to idler roller price, one significant distinction that impacts cost is the choice between new and used idler rollers. Both options have their advantages and considerations, especially in terms of price, wear and tear, and expected lifespan.
Price Differences:
New idler rollers come with the assurance of quality and longevity but at a higher price point. This investment is often justified by the reduced risk of breakdowns and the longer service life. On the other hand, used idler rollers can be significantly cheaper, making them an attractive option for budget-conscious operations. However, the lower idler roller price of used units can sometimes reflect hidden costs in terms of reduced efficiency and the potential need for more frequent replacements.
Considerations for Used Idler Rollers:
- Wear and Tear: Assessing the wear and tear on used idler rollers is crucial. For example, rollers from a low-duty operation might show minimal wear, making them a cost-effective choice. In contrast, rollers from a high-load environment might be near the end of their useful life.
- Lifespan: The remaining lifespan of used idler rollers can vary widely. A roller with minimal wear from a reputable source might offer considerable remaining service life, whereas one from a less reliable source might fail prematurely.
- Maintenance History: Understanding the maintenance history of used idler rollers can provide insights into their condition. Well-maintained rollers might still offer good performance, while neglected ones could pose risks.
- Compatibility: Ensuring that used idler rollers are compatible with your existing conveyor system is essential. Mismatched rollers can lead to operational issues and increased wear on the conveyor belt.
- Warranty and Support: Unlike new idler rollers, used ones often come with limited or no warranty. The absence of manufacturer support for used rollers can lead to challenges in addressing any issues that arise.
When considering the idler roller price, it’s important to weigh the initial savings of purchasing used rollers against the potential costs associated with their condition and lifespan. A thorough assessment and understanding of the specific requirements and challenges of your conveyor system are essential in making an informed decision that balances cost with operational efficiency and reliability.
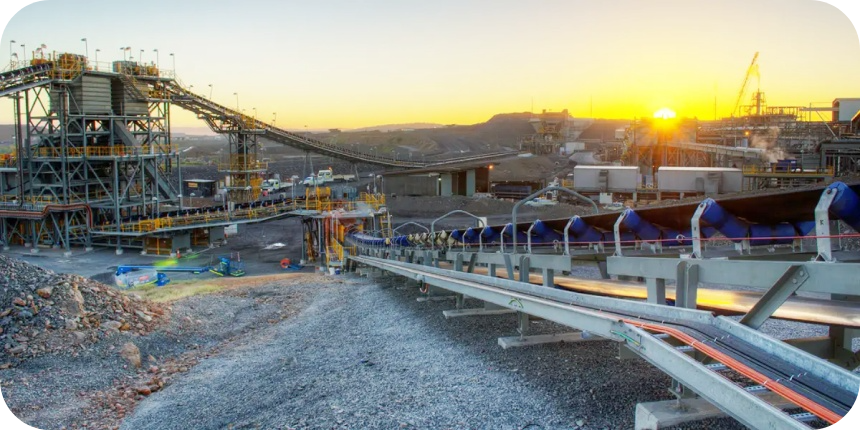
Idler vs. Roller: Impact on Idler Roller Price and Functionality
In the context of conveyor systems, the distinction between “idler” and “roller” is crucial for understanding their roles and how these affect the idler roller price. While both terms are often used interchangeably, they refer to different components within the conveyor system, each serving a unique purpose.
Clarification of Terms:
- Roller: This term broadly refers to any cylindrical component that rotates around an axis. Rollers are used in various applications beyond conveyor systems, including printing, manufacturing, and material handling processes.
- Idler: An idler is a specific type of roller designed for use in conveyor systems. Its primary function is to support the conveyor belt and the material being transported. Idlers do not drive the belt but are essential for maintaining its alignment and tension.
Function and Design Differentiation:
- Support vs. Drive: Idlers support the weight of the belt and the materials being conveyed, whereas drive rollers are responsible for propelling the conveyor belt forward.
- Placement: Idlers are strategically placed along the conveyor path to provide continuous support, whereas drive rollers are located at the endpoints of the conveyor system.
- Design Complexity: Idlers can have specialized designs, such as troughing, impact, or self-aligning idlers, to address specific challenges like load distribution, shock absorption, and belt alignment. Drive rollers, however, are designed to provide traction and power to the belt.
- Material Construction: Idlers may be constructed from various materials, including steel, rubber, or polyurethane, to suit different operational needs. Drive rollers often have high-friction surfaces or coatings to effectively move the belt.
- Maintenance Requirements: Idlers are designed for easy maintenance and replacement, given their critical role in belt support. Drive rollers, being part of the conveyor’s drive system, may require more complex maintenance procedures.
Understanding these distinctions is vital when considering the idler roller price, as the functionality, design complexity, and material construction of idlers directly influence their cost. Selecting the appropriate idler type for your conveyor system ensures optimal performance and longevity, ultimately affecting the overall operational efficiency and maintenance costs.
Conveyor Idler Roller Sizes and Their Impact on Idler Roller Price
The size of conveyor idler rollers plays a significant role in determining the idler roller price. Various standard sizes cater to different conveyor belt widths and load requirements, but custom sizes are often necessary for specific applications, influencing the overall cost.
Standard Conveyor Idler Roller Sizes:
Standard sizes of idler rollers are designed to match common conveyor belt widths, ranging from 18 inches to over 60 inches. The diameter of these rollers can vary, typically between 4 inches for light-duty applications and 6 inches or more for heavy-duty operations. The choice of size directly correlates with the intended use of the conveyor system, with larger rollers being capable of supporting heavier loads and wider belts.
Impact of Size and Scalability on Pricing:
- Custom Sizes: Custom-sized idler rollers, necessary for unique conveyor setups or specific material handling needs, often come at a higher price due to the additional manufacturing processes involved.
- Load Capacity: Larger rollers designed to support heavier loads require more material and robust construction, leading to higher costs. For example, a heavy-duty mining conveyor would need larger and more durable rollers compared to a light-duty warehouse conveyor, impacting the idler roller price.
- Belt Width Compatibility: Rollers must be appropriately sized to the width of the conveyor belt. Wider belts, common in bulk material handling, require longer rollers, which can increase the price due to the extra material and reinforcement needed.
- Material Throughput: High-capacity conveyors, moving large volumes of material, necessitate larger rollers for efficient operation. The increased size and durability requirements can elevate the idler roller price.
- Specialty Applications: Conveyors used in extreme environments or for transporting abrasive materials might need custom-sized rollers made from specialized materials, further influencing the cost.
Understanding the relationship between conveyor idler roller sizes and their impact on price is crucial for budgeting and operational planning. While standard sizes might offer cost savings due to mass production, custom applications requiring specific sizes and features can lead to higher prices, underscoring the importance of precise conveyor design and idler selection.
Selecting the Right Idler Roller and Maximizing Value for Idler Roller Price
Choosing the appropriate idler roller for your conveyor system is crucial for ensuring operational efficiency and getting the best value for the idler roller price. The selection process involves considering various factors that align with your system’s requirements and the specific materials being handled.
Tips for Selecting Idler Rollers:
- Assess Conveyor System Requirements: Evaluate the type of conveyor system you have, including belt width, speed, and the direction of material movement. For instance, high-speed systems might require idler rollers with precision bearings to reduce friction and wear.
- Understand Material Handling Needs: Consider the properties of the materials being conveyed. Heavy, abrasive materials such as ores might necessitate durable steel rollers, while delicate items like packaged goods could be better served by rubber-coated rollers to prevent damage.
- Consider Environmental Conditions: The operating environment can significantly impact idler roller selection. For outdoor or harsh environments, corrosion-resistant materials like stainless steel or coated rollers might be necessary to withstand the elements.
- Evaluate Load Requirements: The weight and distribution of the load are critical. Heavier loads require robust rollers with higher load-bearing capacities, possibly leading to a higher idler roller price but necessary for system longevity.
- Factor in Belt Tracking Needs: For systems prone to belt misalignment, selecting self-aligning idler rollers can help maintain belt position, reducing maintenance and potential downtime.
Lifecycle Costs and Maintenance Considerations:
Beyond the initial idler roller price, considering the total lifecycle costs of the rollers is essential for long-term value. This includes evaluating the expected lifespan of the rollers, maintenance requirements, and the ease of replacement. Rollers with a slightly higher upfront cost but lower maintenance needs and longer service life can offer better value over time compared to cheaper alternatives that require frequent replacements or repairs.
Maintenance requirements also play a significant role in overall cost-effectiveness. Idler rollers designed for easy access and replacement can reduce labor costs and downtime, contributing to a lower total cost of ownership. Additionally, choosing rollers from reputable manufacturers with solid warranties can provide added assurance and support, further ensuring value for the idler roller price paid.
Selecting the right idler roller involves a careful balance between immediate costs and long-term value. By considering the specific needs of your conveyor system and the materials it handles, along with the lifecycle costs and maintenance requirements, you can ensure that your investment in idler rollers delivers optimal performance and value.
Find the perfect conveyor idlers for your specific needs.
FAQs About Idler Roller Price
An idler roller is a fundamental component in conveyor systems, designed to support the conveyor belt and the material being transported along it. These rollers are cylindrical bars that run along and underneath the conveyor belt, facilitating smooth and continuous movement. Idler rollers play a crucial role in maintaining the belt’s alignment and tension, ensuring efficient operation of the conveyor system. They are strategically positioned within the conveyor framework and can be customized to meet specific application requirements, including variations in bearing types, sizes, and materials to suit different operational environments and loads. The use of idler rollers significantly reduces the wear and tear on the conveyor belt, extending its lifespan and minimizing maintenance needs.
The standard size of an idler roller can vary widely depending on the application, the width of the conveyor belt, and the specific requirements of the material handling system. However, common diameters for idler rollers range from 3 to 6 inches (about 76 to 152 mm), with lengths tailored to match the width of the conveyor belt they support. The spacing between idler rollers is also an important consideration and is typically determined based on the load the conveyor is designed to carry, with heavier loads requiring closer spacing to adequately support the belt and the material being conveyed. Manufacturers often provide a range of standard sizes but can also customize idler rollers to meet specific requirements, including larger or smaller diameters and varying lengths to accommodate unique conveyor designs and applications.
While the terms “idler” and “roller” are often used interchangeably in the context of conveyor systems, there is a distinction between them. A roller is a broad term that refers to any cylindrical bar that rotates around a central axis and can be used in various applications, not limited to conveyors. An idler, on the other hand, specifically refers to a type of roller that is used in a conveyor system to support the conveyor belt and the material being transported. Idlers do not drive the belt but are essential for maintaining its alignment and tension, ensuring smooth operation. Therefore, while all idlers can be considered rollers, not all rollers are idlers. The term “idler” highlights the roller’s specific function within a conveyor system.
Idler roller conveyors come in various types, each designed to fulfill specific functions within material handling systems. The most common types include:
Troughing Idlers: These are used on the carrying side of the conveyor and typically consist of three rollers arranged in a ‘trough’ formation to support the belt and material load, helping to maintain the belt’s shape and alignment.
Return Idlers: Positioned on the return side of the belt, these idlers support the belt as it loops back to the beginning of the conveyor system. They are usually flat and spaced further apart than troughing idlers.
Impact Idlers: Designed to absorb the shock and impact of heavy materials falling onto the conveyor belt, impact idlers are typically located at loading points and have rubber-coated rollers to reduce damage to the belt.
Self-aligning Idlers: These are used to correct any misalignment of the conveyor belt, ensuring it runs centrally along the conveyor. They can be positioned on both the carrying and return sides.
Guide Idlers: Installed on the sides of the conveyor belt, guide idlers prevent the belt from slipping off the rollers and assist in maintaining its path.
Each type of idler roller conveyor is engineered to address specific challenges within a conveyor system, from supporting and protecting the conveyor belt to ensuring its proper alignment and smooth operation.
Last Updated on July 9, 2024 by Jordan Smith
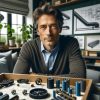
Jordan Smith, a seasoned professional with over 20 years of experience in the conveyor system industry. Jordan’s expertise lies in providing comprehensive solutions for conveyor rollers, belts, and accessories, catering to a wide range of industrial needs. From initial design and configuration to installation and meticulous troubleshooting, Jordan is adept at handling all aspects of conveyor system management. Whether you’re looking to upgrade your production line with efficient conveyor belts, require custom conveyor rollers for specific operations, or need expert advice on selecting the right conveyor accessories for your facility, Jordan is your reliable consultant. For any inquiries or assistance with conveyor system optimization, Jordan is available to share his wealth of knowledge and experience. Feel free to reach out at any time for professional guidance on all matters related to conveyor rollers, belts, and accessories.