Comprehensive Overview of Idler Roller Types
In the realm of material handling and conveyor systems, idler rollers stand as pivotal components, ensuring the seamless operation and longevity of conveyor belts. These cylindrical bars, known collectively as idler roller types, vary in design and function, each tailored to specific requirements of the conveyor system they serve. An idler roller, by definition, supports the conveyor belt and facilitates the transport of materials across vast distances within industrial settings. From mining operations to assembly lines, the efficiency and productivity of a conveyor system hinge significantly on the strategic selection and placement of these idler rollers. Understanding the diverse idler roller types is crucial for engineers and system designers to optimize the functionality and durability of conveyor systems, making them indispensable in the infrastructure of modern manufacturing and logistics.
The Basics of Idler Roller Types
Idler rollers, fundamental to the operation of conveyor systems, are cylindrical components designed to support the conveyor belt and the materials being transported. The variety of idler roller types caters to different functions and operational requirements, ensuring the conveyor system’s efficiency and longevity. Here are six specific examples of idler roller types, each serving a unique purpose within the conveyor system:
- Carrying Idlers: Support the weight of the belt and the material being conveyed, typically found in the carrying section of the conveyor.
- Return Idlers: Support the return side of the conveyor belt, helping to maintain its tension and structural integrity.
- Impact Idlers: Positioned at loading zones to absorb the shock and impact of falling materials, protecting the belt from damage.
- Self-Aligning Idlers: Used to correct any misalignment of the conveyor belt, ensuring it remains centered along the conveyor path.
- Guide Idlers: Prevent the conveyor belt from slipping off the rollers, maintaining its intended path.
- Spiral Idlers: Designed to reduce the buildup of materials on the belt, particularly useful in handling sticky or wet materials.
When comparing idler roller types to other types of rollers within conveyor systems, several differences become apparent. These distinctions are crucial for selecting the appropriate roller type for specific conveyor system needs. The comparison can be illustrated in a table format, highlighting key differences such as design purpose, placement within the conveyor system, and specialized functions.
This detailed exploration of idler roller types and their comparison to other rollers underscores the specialized roles idler rollers play in ensuring the efficient and smooth operation of conveyor systems.
Key Types of Idler Roller Types
Return Idler Rollers
Return idler rollers are crucial in supporting the return path of the conveyor belt, ensuring it remains tensioned and aligned. These rollers are typically plain and streamlined, facilitating the smooth passage of the belt back to the starting point without carrying materials.
- Flat Return Idlers: Commonly used in simple conveyor setups where additional support is needed on the return side.
- Rubber Disc Return Idlers: Employed in applications where sticky materials need to be prevented from adhering to the belt.
- Spiral Return Idlers: Ideal for removing residual materials from the belt, enhancing cleanliness and efficiency.
- V-Return Idlers: Used in high-speed and high-tension conveyor systems to provide enhanced belt support and stability.
- Self-Cleaning Return Idlers: Designed with features to reduce material build-up on the return belt.
- Urethane Return Idlers: Offer reduced belt wear in abrasive environments, extending the life of the conveyor belt.
Applications of return idler rollers span various industries, including:
- Mining: For transporting extracted materials back to the processing area.
- Agriculture: In grain conveyors, for returning the belt after depositing grain in storage facilities.
- Recycling Plants: Where belts return after disposing of materials for recycling.
- Manufacturing: In assembly lines, where products are transported across various stages of production.
Carrying Idler Rollers
Carrying idler rollers support the loaded conveyor belt and the materials being transported. Their design varies based on the application, including:
- Troughing Carrying Idlers: The most common type, forming a ‘trough’ to cradle the material, available in angles of 20°, 30°, and 45°.
- Flat Carrying Idlers: Used in applications where material spillage is not a concern, supporting the belt in a flat orientation.
- Impact Carrying Idlers: Positioned at loading points to absorb the shock of material drop, reducing belt damage.
- Garland Carrying Idlers: Consist of a string of idlers hung in a chain-like fashion, providing flexible belt support.
- Offset Carrying Idlers: Designed to alternate on either side of the conveyor, providing balanced support and reducing wear.
- Transition Carrying Idlers: Facilitate the smooth transition of the belt from flat to troughed sections at the conveyor’s head and tail.
Impact Idler Rollers
Impact idler rollers are designed to absorb the shock and impact at material loading points, protecting the belt and structure from damage.
- Standard Impact Idlers: Made with robust frames and cushioned rolls to absorb impact.
- Adjustable Impact Idlers: Allow for varying degrees of impact absorption, adaptable to different material weights.
- Barrel-Shaped Impact Idlers: Help in distributing the material load evenly across the belt width.
- Hybrid Impact Idlers: Combine features of different idler types for optimized impact absorption.
- Slide-On Impact Idlers: Easy to install and replace, minimizing downtime.
- Heavy-Duty Impact Idlers: Designed for extreme conditions, such as in mining and quarrying.
Specialized Idler Rollers
Rubber Disc Idler Rollers
Rubber disc idler rollers are equipped with rubber discs to minimize material build-up on the belt, ensuring smooth operation.
- Standard Rubber Disc Idlers: For general applications where minimal material stickiness is present.
- Variable Spacing Rubber Disc Idlers: The spacing of rubber discs can be adjusted based on the level of material shedding required.
- Segmented Rubber Disc Idlers: Feature segmented discs for easy replacement and maintenance.
- Bi-Directional Rubber Disc Idlers: Effective in reversible conveyor systems.
- Retractable Rubber Disc Idlers: Can be retracted for maintenance without stopping the conveyor.
- Anti-Vibration Rubber Disc Idlers: Reduce vibrations, prolonging the lifespan of the conveyor components.
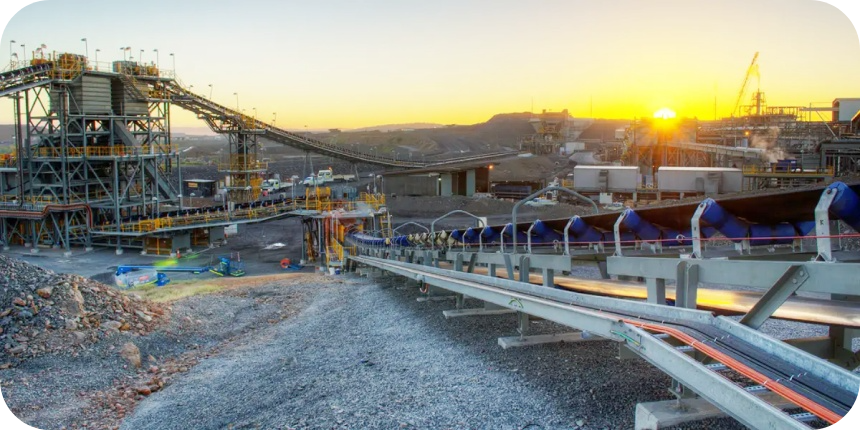
Tapered Idler Rollers
Tapered idler rollers are essential for maintaining belt alignment, especially in curved sections of the conveyor. Their conical shape helps steer the belt towards the center.
- Standard Tapered Idler Rollers: These are the most commonly used tapered rollers, designed for general applications where conveyor belts navigate through moderate curves. They provide reliable belt alignment in standard conveyor setups.
- Heavy-Duty Tapered Idler Rollers: Built for more demanding environments, such as mining or construction, these rollers are made from robust materials to withstand high loads and abrasive conditions, ensuring belt alignment in challenging applications.
- Adjustable Tapered Idler Rollers: These rollers feature an adjustable taper mechanism that allows for fine-tuning of the roller angle to accommodate varying conveyor belt widths and tension, providing precise belt alignment.
- Guide Roll Tapered Idlers: Specifically designed for extreme curve navigation, these idlers have a more pronounced taper and are often used in conjunction with guide rails to ensure that the belt stays on track in sharp or complex curved sections.
Rubber and steel screw idler rollers are designed with a helical pattern to aid in material removal and belt tracking. Examples include:
- Standard Rubber Screw Idlers: Provide gentle cleaning action suitable for sensitive materials.
- Aggressive Steel Screw Idlers: Offer more robust cleaning for sticky or wet materials.
- Fine-Pitch Screw Idlers: Ideal for light-duty cleaning and tracking.
- Coarse-Pitch Screw Idlers: Used for heavy-duty material removal.
- Combination Screw Idlers: Feature both rubber and steel sections for versatile performance.
- Adjustable Pitch Screw Idlers: Allow customization of the screw pattern to suit specific operational needs.
Heavy-Duty Idler Roller Types
In the demanding world of material handling, heavy-duty idler roller types are engineered to withstand extreme conditions and high-load applications, ensuring the resilience and longevity of conveyor systems. These robust idlers are constructed from durable materials and are designed to endure the harsh environments found in industries such as mining, quarrying, and bulk material handling.
Heavy-duty idler rollers are characterized by their enhanced structural integrity, high-quality bearings, and reinforced frames, making them capable of supporting substantial weights and resisting wear and tear. The design of these idler rollers often includes thicker walls, larger diameters, and specialized coatings to resist corrosion and abrasion.
One of the key features of heavy-duty idler roller types is their ability to operate efficiently under high stress without compromising performance. This is achieved through precision engineering, where every component is optimized for durability and strength. For instance, the bearings used in these rollers are typically sealed and lubricated for life, minimizing maintenance requirements and ensuring smooth operation under heavy loads.
Moreover, the selection of heavy-duty idler roller types is critical in applications where the conveyor belt carries sharp, abrasive materials that can cause significant wear. In such scenarios, the idler rollers may be equipped with impact rings or discs made from materials like polyurethane or rubber, which absorb shocks and reduce the impact on the roller surface.
Heavy-duty idler roller types are indispensable in settings that demand high performance and reliability. Their design and construction are focused on providing unparalleled support to conveyor systems, ensuring that they can withstand the rigors of heavy-duty operations while maintaining efficiency and prolonging the lifespan of the conveyor belt.
Customizable Options for Idler Roller Types
The adaptability of idler roller types to specific conveyor system requirements is crucial for optimizing performance, efficiency, and longevity. Customizable idler rollers offer the flexibility needed to tailor components to the unique demands of various applications, environments, and materials being handled. Here are six specific examples illustrating the importance of customization:
- Material Compatibility: Customizing idler rollers for compatibility with the materials being conveyed can significantly reduce wear and tear, especially with abrasive or corrosive materials.
- Load Capacity: Tailoring idler rollers to the specific weight requirements of the conveyed materials ensures structural integrity and operational reliability.
- Environmental Conditions: Customizing for extreme temperatures, moisture levels, or chemical exposures can enhance the durability and lifespan of idler rollers.
- Speed Requirements: High-speed conveyor systems may require specially designed idler rollers to reduce vibration and noise while maintaining stability.
- Operational Efficiency: Customized idler rollers can be designed for energy efficiency, reducing operational costs and environmental impact.
- Maintenance Needs: Idler rollers can be customized for ease of maintenance, including features like easy-access bearings or self-cleaning mechanisms to reduce downtime.
When it comes to the variables that can be customized in idler roller types, the options are extensive, ensuring that every aspect of the roller can be tailored to meet specific needs.
- Bearing Size and Type: Bearings can be selected based on load requirements, operational speeds, and environmental conditions to ensure optimal performance and longevity.
- Material Type: The roller shell and bearing housing materials can be chosen based on the application, with options including steel, stainless steel, aluminum, or composite materials for different durability and weight considerations.
- Seal Type: Seals protect the bearings from contaminants and can be customized to the level of protection required, from basic dust seals to labyrinth seals for high-dust environments.
- Roller Diameter and Wall Thickness: These can be adjusted to accommodate the weight of the materials being conveyed and the belt size, impacting the roller’s capacity and durability.
- Surface Treatment: Options like rubber coating, galvanization, or powder coating can be applied to the roller surface for increased grip, corrosion resistance, or wear protection.
- Shaft Configuration: The shaft end design can be customized for different mounting requirements, including fixed, floating, or threaded options for ease of installation and alignment.
Customizable options for idler roller types ensure that conveyor systems can be precisely tailored to meet the operational demands, environmental conditions, and maintenance practices of any application, enhancing overall system performance and reliability.
Choosing the Right Idler Roller Types
Selecting the appropriate idler roller types for a conveyor system is a critical decision that impacts its efficiency, durability, and maintenance requirements. Several key factors must be considered to ensure the optimal match between the idler rollers and the conveyor system’s needs.
- Material Type Being Conveyed: The nature of the materials (e.g., abrasive, corrosive, sticky, or heavy) directly influences the choice of idler roller types, necessitating rollers that can withstand the material’s characteristics without excessive wear or damage.
- Load Size and Weight: The weight of the materials being transported affects the required load-bearing capacity of the idler rollers. Heavier loads may necessitate heavy-duty or reinforced idler rollers to prevent deformation and ensure longevity.
- Conveyor Belt Design: The width, speed, and design of the conveyor belt (e.g., flat, troughed, or inclined) determine the suitable idler roller types and configurations to support and guide the belt effectively.
- Operating Environment: Conditions such as temperature extremes, moisture, dust, and chemical exposure require idler rollers with specific materials, seals, and coatings to ensure reliable operation under such environmental challenges.
- Operational Speed: High-speed conveyor systems demand idler rollers designed to minimize vibration and noise while maintaining stability and reducing energy consumption.
- Maintenance and Accessibility: The ease of maintenance and replacement of idler rollers is crucial, especially in high-throughput or critical-path applications. Selecting idler rollers with features that simplify maintenance can significantly reduce downtime and operational costs.
The importance of consulting idler roller charts and specifications (PDFs) cannot be overstated in the process of selecting the right idler roller types. These resources provide detailed information on the dimensions, load capacities, materials, and other critical specifications of various idler roller types. By referring to these charts and specifications, decision-makers can make informed choices based on empirical data, ensuring that the selected idler rollers are perfectly suited to the conveyor system’s requirements. This informed decision-making process helps in optimizing the conveyor’s performance, extending its service life, and minimizing maintenance needs, ultimately contributing to the overall efficiency and cost-effectiveness of the material handling operation.
Need a Sample of Idler Rollers? Let Us Know.
FAQs About Idler Roller Types
Idler rollers, integral components of conveyor systems, come in various types, each designed to fulfill specific functions and requirements. The primary types include:
Carrying Idlers: These are the most common type, positioned along the conveyor path to support the belt and the material being transported. They can be flat or troughed to contain the material on the belt.
Return Idlers: These support the return path of the belt and are usually flat, although designs may vary based on the conveyor’s needs, such as rubber disc return idlers for sticky materials.
Impact Idlers: Positioned at loading points, impact idlers are designed to absorb the shock of heavy materials being loaded onto the belt, protecting both the belt and the structure from damage.
Self-Aligning Idlers: These are used to correct any misalignment of the belt, ensuring it runs centrally along the conveyor path. They can be pivotally mounted or feature a self-aligning design to guide the belt back to its correct path.
Guide Idlers: Installed on the sides of the belt, guide idlers prevent the belt from slipping off the rollers and assist in maintaining its path.
Each type plays a crucial role in the conveyor’s overall functionality, ensuring efficient and uninterrupted operation.
Conveyor rollers are cylindrical components that facilitate the movement of conveyor belts or materials along the conveyor system. The main types include:
Drive Rollers: These are powered rollers connected to the conveyor’s motor, driving the belt or materials along the system.
Idler Rollers: These non-powered rollers support the conveyor belt and the material being conveyed. They vary in type, including carrying, return, impact, and self-aligning idlers.
Grooved Rollers: Designed with grooves, these rollers are used primarily in roller conveyors to support and move items along, especially in sorting and assembly operations.
Accumulation Rollers: These allow for the accumulation of materials on roller conveyors without exerting excessive pressure or causing damage, thanks to their ability to control the movement and accumulation of goods.
Coated Rollers: These rollers have a protective coating, such as rubber or polyurethane, to provide grip, reduce noise, and protect both the roller and the materials being conveyed.
Understanding the specific functions and applications of each roller type is essential for optimizing conveyor system design and operation.
Idlers can be classified based on their design, function, and application within the conveyor system. The primary classifications include:
Troughing Idlers: Designed with a series of rollers set at specific angles to form a trough, supporting the conveyor belt and material.
Flat or Straight Idlers: These support the belt in a flat layout and are commonly used in the return section of the conveyor.
Impact Idlers: Built with a robust design to absorb the impact of heavy or abrasive materials at loading points.
Self-Aligning Idlers: These automatically adjust the belt alignment, preventing drift and ensuring the belt runs centrally.
Guide or Side Idlers: Installed at the edges of the belt to prevent lateral movement and maintain the belt’s path.
Each classification serves a unique purpose, contributing to the conveyor system’s efficiency, safety, and longevity.
The primary purpose of idler rollers in a conveyor system is to support the conveyor belt and the material being transported. They play a crucial role in ensuring the smooth, efficient operation of the conveyor by:
Supporting the Weight: Idler rollers bear the weight of the belt and the materials, reducing friction and wear on the belt.
Maintaining Belt Tension: Properly spaced idlers help maintain the correct tension in the conveyor belt, essential for efficient operation.
Absorbing Impact: Specifically designed impact idlers absorb the shock at loading points, protecting the belt from damage and extending its life.
Guiding the Belt: Self-aligning and guide idlers ensure the belt remains centered and on its intended path, preventing drift and potential damage.
Facilitating Movement: By reducing resistance and friction, idlers allow for the smooth movement of the belt and materials, contributing to the conveyor system’s overall efficiency.
In essence, idler rollers are fundamental to the conveyor’s functionality, affecting its performance, reliability, and maintenance requirements.
Last Updated on July 23, 2024 by Jordan Smith
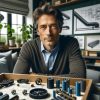
Jordan Smith, a seasoned professional with over 20 years of experience in the conveyor system industry. Jordan’s expertise lies in providing comprehensive solutions for conveyor rollers, belts, and accessories, catering to a wide range of industrial needs. From initial design and configuration to installation and meticulous troubleshooting, Jordan is adept at handling all aspects of conveyor system management. Whether you’re looking to upgrade your production line with efficient conveyor belts, require custom conveyor rollers for specific operations, or need expert advice on selecting the right conveyor accessories for your facility, Jordan is your reliable consultant. For any inquiries or assistance with conveyor system optimization, Jordan is available to share his wealth of knowledge and experience. Feel free to reach out at any time for professional guidance on all matters related to conveyor rollers, belts, and accessories.