Idler Rollers with Bearings: Design and Application
Idler rollers with bearings are essential components in the smooth operation of numerous mechanical systems and industrial machinery. These rollers primarily function to guide and support conveyor belts, reduce friction, and facilitate the effortless movement of materials across a wide range of industries. From mining and agriculture to automotive manufacturing, the reliability and efficiency of idler rollers with bearings directly impact production timelines and maintenance costs. Their strategic implementation in machinery not only extends the lifespan of the conveyor system but also enhances operational stability, making them indispensable in settings that require continuous, heavy-duty operation.
What Are Idler Rollers with Bearings
Idler rollers with bearings are essential mechanical components designed to facilitate the movement of conveyor systems by supporting and guiding conveyor belts. These rollers are crucial in ensuring the belt operates smoothly, handles materials efficiently, and lasts longer under continuous use. Below, we delve into the specifics of what idler rollers are, the types of bearings they use, and the materials that make them both effective and durable.
Definition of Idler Rollers
Idler rollers serve several functions within conveyor systems, each vital for different aspects of the conveyor’s operation:
- Support Function: Idler rollers primarily support the conveyor belt’s weight, especially in segments where the belt would otherwise sag under the load of the materials it carries. This support helps maintain tension and prevents damage under load.
- Guide and Align: These rollers ensure that the conveyor belt follows a consistent path, crucial for the belt’s longevity and the efficient movement of materials. Misalignment can lead to premature wear and operational issues.
- Load Distribution: By evenly distributing the load across the belt’s width, idler rollers help to prevent the belt from stretching unevenly and wearing prematurely, thus maintaining the belt’s integrity over time.
- Friction Reduction: The bearings within idler rollers minimize the resistance the belt faces as it rotates, which reduces the energy required to move the belt and thereby increases system efficiency.
- Speed Regulation: Controlling the speed of the conveyor belt is vital for both safety and efficiency; idler rollers play a key role in ensuring that the belt moves at a consistent, appropriate speed.
- Impact Absorption: At loading points, idler rollers absorb the shock and impact of materials as they are deposited onto the belt, protecting both the belt and the materials from damage.
- Versatility: Idler rollers are adaptable to a wide range of industrial environments, making them suitable for applications from light packaging lines to heavy-duty mining operations.
Types of Bearings Used in Idler Rollers
Bearings are integral to the functionality of idler rollers, as they must accommodate various loads and environmental conditions:
- Ball Bearings: Ideal for applications with lighter loads, ball bearings provide smooth and efficient operation with good speed capabilities, suitable for many general-purpose conveyor systems.
- Roller Bearings: Designed to carry heavier loads, roller bearings are more robust and durable, making them suitable for industrial environments with high-demand applications.
- Spherical Roller Bearings: These bearings are perfect for positions where misalignment might occur; they can handle both radial and axial loads and adjust to alignment errors.
- Tapered Roller Bearings: Excellent for heavy-duty applications, these bearings can support large radial and axial loads simultaneously, often used in bulk material handling.
- Sealed Bearings: Essential in environments where dust, dirt, and debris are prevalent, sealed bearings protect the rolling elements from contamination and extend the life of the roller.
- Precision Bearings: Utilized in high-speed applications where accuracy and low resistance are necessary, precision bearings ensure that the roller operates smoothly and reliably.
Key Materials and Construction Features
The choice of materials for idler rollers is determined by the application’s demands for durability, weight, and cost-effectiveness:
- Steel: The go-to material for most heavy-duty applications due to its strength and durability. Steel can handle significant weight and stress, making it suitable for industrial use.
- Aluminium: Lighter than steel, aluminium is easier to install and requires less energy to move, making it ideal for lighter-duty applications where weight is a concern.
- Nylon: Often used for the roller body, nylon reduces the overall weight and decreases operational noise, providing a quieter and lighter alternative to metal rollers.
- Zinc Coated Steel: Provides excellent corrosion resistance, vital in environments that are moist or chemically active, thus prolonging the roller’s lifespan.
- High-impact Polymers: Selected for their ability to absorb shocks and impacts, these polymers are often used in areas of the conveyor system that experience high levels of stress.
- Composite Materials: These materials blend properties such as lightness, strength, and cost-effectiveness, increasingly chosen to enhance the performance and durability of modern idler rollers.
Through the integration of well-chosen materials and precise bearing types, idler rollers with bearings are tailored to meet the diverse requirements of various industrial settings, ensuring efficient and reliable conveyor operations.
Common Uses of Idler Rollers with Bearings
Idler rollers with bearings play a pivotal role in numerous industrial applications. Their primary function is to support and guide conveyor belts, but they extend far beyond this basic utility. These components ensure smooth operations, efficient handling, and longevity in systems ranging from simple conveyor belts to complex automotive and heavy machinery applications. Let’s delve deeper into the versatile uses of idler rollers with bearings across various sectors.
Conveyor Systems
Conveyor systems are the backbone of many industries, ensuring materials are moved efficiently from one point to another. Idler rollers with bearings are critical in these systems:
- Material Handling Efficiency: They facilitate the smooth transport of diverse materials across extensive networks in warehouses and manufacturing plants, reducing bottlenecks.
- Load Support and Balance: Idler rollers evenly distribute the weight of materials on conveyor belts, preventing imbalances and reducing strain on the system.
- Operational Speed: By minimizing friction, these rollers allow conveyor belts to operate at optimal speeds, enhancing throughput and productivity.
- Maintenance Reduction: Well-functioning idler rollers reduce the need for frequent belt adjustments and replacements, lowering overall maintenance costs.
- Workplace Safety: Stable and reliable conveyor operations reduce workplace accidents associated with belt slippage or failures.
- Acoustic Management: Bearings in idler rollers are designed to operate quietly, crucial in maintaining a more comfortable and compliant working environment.
- Energy Efficiency: Efficient movement facilitated by high-quality rollers leads to lower energy consumption and operational costs.
Applications in Automotive Industries
In the automotive industry, idler rollers with bearings find extensive use, not just on production lines but also in component testing and handling systems:
- Vehicle Assembly Lines: These rollers support the smooth transition of vehicles across different assembly stages, from chassis assembly to final inspections.
- Durability Testing: Automotive components are tested on simulators that use idler rollers to replicate real-world stress and wear conditions.
- Parts Handling: Rollers ensure the delicate handling of automotive parts, preventing damage during movement and assembly.
- Paint Application: Essential in conveyor systems that move vehicles through automated paint booths, providing a steady pace for uniform application.
- Testing and Quality Assurance: Conveyors equipped with idler rollers transport vehicles to testing areas for final checks and quality assurance.
- Efficient Packaging: Rollers facilitate the movement of newly assembled vehicles to packaging areas, ensuring they are ready for shipment without delays.
- Distribution Systems: In distribution centers, rollers help in the sorting and loading of vehicles and parts for delivery.
Role in Heavy Machinery and Equipment
Heavy machinery and equipment across various industries rely on idler rollers with bearings for their robustness and durability:
- Mining Sector: Idler rollers are crucial in the conveyors that transport mined materials from deep within mines to the surface.
- Construction Projects: They are used in mobile conveyors that move materials across construction sites, aiding in building infrastructure.
- Agricultural Applications: In agriculture, these rollers support systems that handle everything from harvested crops to processed goods.
- Forestry and Logging: Idler rollers aid in the transport of logs and lumber in sawmills, ensuring smooth processing from cutting to distribution.
- Industrial Manufacturing: Heavy industrial settings, such as steel mills, utilize these rollers to move raw materials and heavy products efficiently.
- Recycling Facilities: They play a key role in the sorting and processing conveyors used in recycling operations, handling a variety of materials.
- Bulk Handling: From chemical plants to coal handling facilities, idler rollers ensure the safe and efficient transport of bulk materials.
These detailed insights into the uses of idler rollers with bearings highlight their indispensable role in enhancing operational efficiency, safety, and productivity across diverse industrial landscapes.
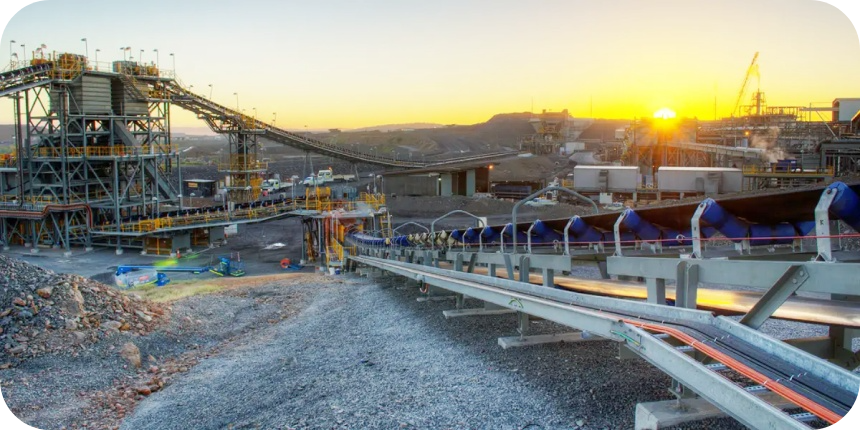
Types of Idler Rollers with Bearings
Idler rollers with bearings are integral components of conveyor systems, playing diverse roles depending on their design and material composition. Different types of idler rollers are suited to specific tasks and environments within industrial operations. We will explore three primary types of idler rollers—plain, dead shaft, and rubber-coated and steel screw idler rollers—each offering unique advantages and specialized functionalities.
Plain Idler Rollers
Plain idler rollers are the most common type used in conveyor systems due to their simplicity and effectiveness. They consist of a shell that rotates around a central shaft and is designed primarily for straightforward applications:
- Simplicity in Design: The basic structure makes them easy to manufacture and maintain.
- Cost-Effectiveness: Their simplicity also makes them more affordable compared to more specialized rollers.
- Versatility: Suitable for various industries, including manufacturing, packaging, and distribution.
- Durability: Constructed typically from steel or aluminum, offering strong resistance to wear and tear.
- Load Support: Effective in supporting the weight and stress of materials being transported.
- Low Maintenance: Due to fewer parts, they are less likely to need repairs.
- Easy Installation: Their straightforward design allows for easy installation and replacement.
- Efficiency: Helps in maintaining the speed and consistency of the conveyor belt’s movement.
Dead Shaft Idler Rollers
Dead shaft idler rollers have a stationary shaft with the roller body rotating around it. They are designed for applications requiring high load capacities and are commonly used in heavy-duty environments:
- High Load Capacity: The stationary shaft allows these rollers to handle greater loads.
- Reduced Wear on Bearings: The design minimizes wear on bearings, extending the roller’s lifespan.
- Stability in Operation: Offers greater stability under high-speed or variable load conditions.
- Customization Options: Can be customized with different materials and coatings based on application needs.
- Ideal for Harsh Environments: Commonly used in mining, aggregate, and other heavy industries.
- Precision: Provides more precise belt tracking and tensioning.
- Reduced Belt Slippage: Minimizes belt slippage, enhancing conveyor efficiency.
- Enhanced Bearing Protection: Often equipped with special seals and lubrication to protect bearings in harsh conditions.
Rubber-Coated and Steel Screw Idler Rollers
Rubber-coated and steel screw idler rollers are specialized for applications requiring additional grip and protection against wear. These rollers are particularly useful in handling delicate or abrasive materials:
- Increased Grip: The rubber coating provides extra grip, reducing slippage and misalignment.
- Abrasion Resistance: Rubber and steel coatings offer excellent protection against abrasion.
- Noise Reduction: Rubber reduces operational noise, making them ideal for quiet environments.
- Shock Absorption: The rubber material absorbs shocks, protecting the conveyor belt and materials.
- Application-Specific Designs: Available in various designs to suit specific handling needs.
- Enhanced Traction: Steel screw patterns increase traction in wet or slippery conditions.
- Longevity: Both materials extend the life of the rollers by protecting the core from damage.
- Ideal for Sensitive Materials: Rubber-coated rollers are gentle on materials that are prone to damage.
These distinct types of idler roller bearing are designed to meet a range of operational demands, each enhancing the efficiency and reliability of conveyor systems in different industrial scenarios. By choosing the appropriate type of idler roller, companies can optimize their material handling processes and extend the lifespan of their conveyor systems.
Selecting the Right Idler Rollers with Bearings
Choosing the appropriate idler rollers with bearings is crucial for ensuring the efficiency and longevity of conveyor systems. Each application may have unique requirements based on its operational context. Here are ten factors that need to be considered when selecting the right idler rollers with bearings to ensure optimal performance and durability:
- Load Capacity: Consider the maximum load the rollers must support. Rollers should be chosen based on their ability to handle the expected weight without deformation or failure.
- Environmental Conditions: The environment in which the rollers will operate can significantly affect their performance. Factors like moisture, temperature, and exposure to corrosive substances should guide the selection of materials and types of bearings.
- Speed Requirements: The speed at which the conveyor will operate must be matched with the capabilities of the rollers. High-speed applications may require specialized bearings to handle increased rotational forces.
- Belt Type Compatibility: The type of conveyor belt used (material, texture, width) should be compatible with the rollers to prevent wear on both the belt and the rollers.
- Abrasion Resistance: In environments where abrasive materials are handled, choosing rollers with high abrasion resistance is vital to prolong their life and maintain their functionality.
- Impact Resistance: For operations involving heavy or sharp objects that might impact the rollers, selecting rollers designed to absorb and withstand such forces is crucial.
- Maintenance Requirements: Consider how easy it is to maintain and replace the rollers. Rollers with low maintenance needs can reduce downtime and operational costs.
- Operational Noise: For environments where noise reduction is important, selecting rollers that operate quietly can be crucial. Materials and bearing types can influence the noise level produced by the rollers.
- Energy Efficiency: Rollers with high energy efficiency minimize the power needed to operate the conveyor. This can be achieved through precision-engineered bearings and high-quality roller designs.
- Lifespan and Durability: Evaluate the expected lifespan of the rollers under normal operating conditions. Rollers made from durable materials with robust construction are likely to last longer and offer better value for money.
Selecting the right idler rollers with bearings involves a careful analysis of these factors to ensure that the chosen rollers fit the specific needs of the conveyor system, contributing to its overall performance and reliability.
Top Picks for Idler Rollers with Bearings
Selecting the ideal idler rollers with bearings is essential for maximizing the performance and longevity of conveyor systems in specific applications. Different industries and operational conditions demand specialized rollers that can efficiently handle their unique challenges. Below, we explore a variety of top picks for idler rollers, specifically designed to meet the needs of various applications, ensuring operational efficiency and durability.
Best Idler Rollers with Bearings for Different Applications
- General Manufacturing: Steel idler rollers with sealed ball bearings are robust, offering long-term durability and requiring minimal maintenance. Ideal for environments with variable but controlled conditions, they maintain performance over long operational periods.
- Food Processing: Opt for stainless steel idler rollers with food-grade lubricated bearings, which provide excellent resistance to corrosion and are easy to clean. This choice helps meet strict hygiene standards crucial in food processing environments.
- Pharmaceuticals: In pharmaceuticals, where cleanliness and contamination control are paramount, nylon or polymer rollers with precision bearings minimize particulate generation and maintain a contaminant-free environment.
- Packaging Industry: Aluminum rollers equipped with low-friction bearings facilitate the quick and gentle handling of sensitive packaging materials, reducing the overall system weight and increasing speed without compromising the integrity of the packaging.
- Mining and Quarrying: For rugged outdoor environments like mining, heavy-duty steel rollers with spherical roller bearings are necessary. They are engineered to endure the tough conditions and heavy loads typical of mining operations.
- Agriculture: Agricultural settings require rollers that can handle exposure to the elements. Coated idler rollers with bearings that are resistant to dirt, moisture, and abrasive materials ensure reliable operation in outdoor and variable conditions.
Highlights of Heavy Duty Idler Rollers and Their Specific Advantages
Heavy-duty idler rollers are specifically designed to tackle the toughest tasks in the most demanding environments. These rollers are not only built to last but also to deliver exceptional performance under stress, making them indispensable for heavy industrial applications.
- Enhanced Load Capacity: Capable of supporting significantly heavier loads than standard rollers, these are ideal for sectors like mining where massive materials are a norm.
- High Impact Resistance: Engineered to absorb severe impacts from dropping heavy loads, which might otherwise damage conventional rollers.
- Longevity in Harsh Environments: Constructed from materials like hardened steel and equipped with special coatings, these rollers resist wear from abrasive particles and corrosive conditions, prolonging their service life.
- Superior Durability: Their build includes advanced bearing designs that endure continuous operation under extreme conditions, reducing the likelihood of failures.
- Reduced Downtime: Durable construction and reduced wear translate into fewer maintenance requirements and less frequent replacement, ensuring continuous system operations.
- Precision Engineering: These rollers provide precise belt alignment, which is critical for minimizing wear on the conveyor belt and extending its lifespan.
- High Efficiency: Advanced bearing technology in these rollers minimizes friction, which not only reduces energy costs but also enhances the overall efficiency of the conveyor system.
- Versatility: Customization options are available to suit specific environmental needs, including different materials and surface treatments, ensuring optimal performance.
- Cost-Effectiveness: While initial costs might be higher, the long-term operational savings due to minimal maintenance and replacements make them economically viable over time.
Understanding the specific advantages of each type of idler roller with bearings and their applications ensures that conveyor systems are both efficient and tailored to the specific needs of the industry, maximizing both performance and cost-effectiveness.
Where to Buy Idler Rollers with Bearings
When it comes to enhancing the efficiency and longevity of conveyor systems, choosing the right idler rollers with bearings is crucial. The process of purchasing these components, whether new or used, involves several considerations that can significantly impact their performance and your overall operational success. Below, we provide detailed advice on how to approach purchasing idler rollers with bearings and recommend some trusted suppliers and manufacturers known for their high-quality products.
Tips on Purchasing Idler Rollers with Bearings
Purchasing the right idler rollers with bearings involves more than just finding a supplier. It’s about ensuring that the rollers you choose will serve your specific needs effectively and last under the operational conditions they will face. Here are some refined tips:
- Assess Supplier Reliability: Opt for suppliers known for their reliability and consistency. Research their market presence and the longevity of their products in similar applications as yours.
- Verify Product Quality: Ensure that the rollers meet international or national standards for quality. Look for products with ISO certifications or similar endorsements that guarantee their performance.
- Consider Customization Options: Depending on your system’s requirements, check if the supplier can customize roller dimensions, materials, and bearing types to better suit your needs.
- Evaluate Warranty Offerings: A good warranty can be a testament to the quality of the rollers. Look for suppliers who offer substantial warranties that cover defects and performance guarantees.
- Compare Prices: While it’s tempting to go for the cheapest option, compare the features and benefits of each offer. Sometimes, spending a bit more upfront can save money in the long run by reducing maintenance costs.
- Check for Material Suitability: Match the roller materials to your environmental conditions—whether they need to be resistant to chemicals, heat, or water.
- Inspect Used Rollers Carefully: If purchasing used rollers, examine them for any signs of wear such as cracks or significant wear on the bearings and shell.
- Ask for References: Speak to other customers who have used the supplier’s rollers. Their experiences can provide valuable insights into the reliability and performance of the products.
- Consider Lead Times: Align the delivery schedules with your project deadlines to avoid any disruptions in your operations.
Recommended Suppliers and Manufacturers of Idler Rollers with Bearings
Selecting a reputable supplier or manufacturer is key to finding high-quality idler rollers that meet your specific requirements. Here are some well-regarded sources:
- Precision Pulley & Idler (PPI): Known for their robust design and exceptional customer service, PPI offers products tailored to demanding industrial environments.
- Rexnord: A leader in the conveyor component industry, Rexnord provides innovative solutions that improve durability and efficiency.
- Martin Sprocket & Gear: With decades of experience, Martin offers custom solutions and a wide range of material handling products that withstand various operational demands.
- Fenner Drives: Specializes in manufacturing high-precision rollers that provide excellent performance in critical applications.
- Luff Industries: They offer rollers designed to enhance conveyor performance while reducing operational costs through innovative design.
- Conveyor Components Company: Known for their reliable and innovative designs, they cater to a broad spectrum of industries with their conveyor accessories.
- Douglas Manufacturing: Douglas is celebrated for their durable products that focus on extending the lifespan and efficiency of conveyor systems.
When purchasing idler rollers with bearings, considering these detailed tips and choosing from recommended suppliers ensures you obtain components that not only meet but exceed your operational requirements, leading to improved productivity and reduced downtime.
Get in touch with us for detailed specifications and pricing on our Idler Rollers with Bearings. Submit your inquiry now.
Maintenance and Care of Idler Rollers with Bearings
Maintaining idler rollers with bearings is essential for the optimal performance and longevity of conveyor systems. Proper maintenance routines and effective troubleshooting are critical to prevent breakdowns and ensure continuous, efficient operations. Below, detailed guidance is provided on routine maintenance practices that can extend the lifespan of these components and on how to address common issues effectively.
Routine Maintenance Tips for Extending the Lifespan of Idler Rollers with Bearings
To ensure the continued effectiveness and longevity of idler rollers with bearings, a comprehensive maintenance strategy is crucial. Here are expanded maintenance tips:
- Regular Inspection: Conduct visual and manual inspections to identify wear, damage, or alignment issues. Schedule these inspections at regular intervals based on the operational intensity and environmental conditions.
- Lubrication: Use the correct type and amount of lubricant as specified by the manufacturer. Regularly check and replenish lubricant to avoid friction and overheating, which could lead to premature bearing failure.
- Cleaning: Remove debris and contaminants that could impair the functionality of the rollers. Use appropriate cleaning tools and solvents that will not damage the roller materials or bearings.
- Alignment Checks: Periodically check the alignment of the rollers to ensure they are parallel and level. This helps in minimizing wear and tear on the belt and rollers.
- Bearing Replacement: Implement a schedule for bearing inspection and replacement based on usage and performance. Early replacement of failing bearings can prevent further damage.
- Tension Monitoring: Regularly check and adjust the tension of the conveyor belt to prevent excessive load on the rollers and bearings.
- Environment Monitoring: Be aware of environmental changes such as temperature fluctuations, humidity, and exposure to corrosive substances, which can affect the performance of the rollers.
- Record Keeping: Keep detailed logs of all maintenance activities, including dates, specific actions taken, and any parts replaced. This can help in predicting wear trends and scheduling future maintenance.
- Training: Provide ongoing training for maintenance personnel to ensure they are up-to-date with the latest maintenance practices and safety protocols.
Common Issues and Troubleshooting Steps for Idler Rollers with Bearings
Recognizing and resolving common issues with idler rollers can significantly reduce downtime and repair costs. Here are detailed troubleshooting steps for common problems:
- Excessive Noise: Investigate the source of noise—typically it indicates bearing failure or misalignment. Realign the roller or replace bearings if necessary.
- Bearing Seizure: Check for lubrication issues or contamination. Replace the seized bearing and examine the environmental conditions to prevent future occurrences.
- Roller Misalignment: Assess and adjust the alignment using appropriate tools and techniques. Ensure that the mounting hardware is not worn or loose.
- Wear and Tear: Regularly replace rollers showing significant wear to maintain system efficiency and belt integrity.
- Accumulation of Debris: Implement a cleaning schedule that corresponds to the amount of debris typically encountered in the operating environment.
- Vibration Issues: Analyze the installation and operation to identify the cause of vibration. This could involve realigning rollers or replacing defective components.
- Overheating Bearings: Ensure that bearings are not over-lubricated or under-lubricated and check for any signs of dirt or debris ingress that could cause overheating.
By following these detailed maintenance tips and troubleshooting steps, you can ensure that your idler rollers with bearings continue to function effectively, supporting the overall productivity and safety of your conveyor system operations.
FAQs about Idler Rollers with Bearings
What is the function of an idler roller?
Idler rollers are key components in conveyor systems, designed to support the conveyor belt and the material being transported along the length of the conveyor. Their primary function is to provide stability and support, which helps maintain the integrity and efficiency of the conveyor system. Idler rollers help in evenly distributing the weight of the materials on the belt, reducing sagging and ensuring smooth, consistent motion. They also play a crucial role in minimizing the friction and wear on the conveyor belt, which significantly prolongs the belt’s life and reduces operational costs. Additionally, idler rollers assist in proper tracking of the conveyor belt, preventing it from drifting sideways and causing uneven wear or potential system malfunctions.
The terms “idler” and “roller” are often used interchangeably in the context of conveyor systems, but they refer to distinct components with specific roles. A roller is a broad term that refers to any cylindrical component which rotates around an axis and is used in various applications, including conveyors, printers, and more. In contrast, an idler specifically refers to a type of roller that is used in conveyor systems to support the belt and guide or drive the materials being transported. Idlers do not typically drive or move the belt themselves but are crucial in maintaining the belt’s alignment and tension within conveyor systems. Essentially, all idlers are rollers, but not all rollers are idlers.
Idler roller conveyors come in various types, each designed to meet specific operational needs and applications. The primary types include:
Flat Belt Idlers: Commonly used to support flat belts, especially in bulk material handling applications. They are typically spaced evenly to prevent the belt from sagging.
Troughing Idlers: Designed to form the belt into a trough shape, enhancing the belt’s capacity to hold materials and preventing spillage. These are often used in agricultural and mining industries.
Impact Idlers: Placed at points where material falls onto the belt to absorb the shock and impact, thus protecting the belt and other idlers from damage.
Return Idlers: Located on the underside of the conveyor belt to support the return path of the belt after it has conveyed its load.
Guide Idlers: Used to help the conveyor belt maintain a specific path and prevent it from drifting sideways.
Each type of idler serves a unique function and is strategically placed along the conveyor to ensure optimal performance and reduce wear and tear on the system.
The sizes of idler rollers can vary widely, depending on the specific application and the design of the conveyor system. Idler rollers are typically categorized by their diameter and length, which can range from a few inches to several feet. Common diameters for idler rollers are between 3 inches (about 76 mm) to 6 inches (about 152 mm), but in heavy-duty applications, rollers can be larger. The length of the idler also varies based on the width of the conveyor belt and can be tailored to fit specific needs. The choice of size is crucial as it affects the conveyor’s load capacity, belt speed, and overall system efficiency. Proper sizing of idlers is essential for effective belt support, minimizing wear, and ensuring operational stability.
Last Updated on August 15, 2024 by Jordan Smith
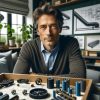
Jordan Smith, a seasoned professional with over 20 years of experience in the conveyor system industry. Jordan’s expertise lies in providing comprehensive solutions for conveyor rollers, belts, and accessories, catering to a wide range of industrial needs. From initial design and configuration to installation and meticulous troubleshooting, Jordan is adept at handling all aspects of conveyor system management. Whether you’re looking to upgrade your production line with efficient conveyor belts, require custom conveyor rollers for specific operations, or need expert advice on selecting the right conveyor accessories for your facility, Jordan is your reliable consultant. For any inquiries or assistance with conveyor system optimization, Jordan is available to share his wealth of knowledge and experience. Feel free to reach out at any time for professional guidance on all matters related to conveyor rollers, belts, and accessories.