How Surcharge Angle Impacts Idler Spacing Belt Conveyor
Understanding the importance of idler spacing in belt conveyors is crucial for efficient operation and longevity of the system. The idler spacing belt conveyor PDF provides detailed guidelines and best practices for determining the optimal spacing between idlers. Proper idler spacing ensures smooth material transport, reduces wear and tear on the belt, and enhances overall system performance. This comprehensive guide is an essential resource for engineers and operators looking to optimize their conveyor systems.
Overview of Idler Spacing Belt Conveyor PDF
Idler spacing in belt conveyors is a critical aspect of conveyor system design. It refers to the distance between consecutive idlers along the length of the conveyor. Idlers, also known as rollers, are cylindrical components that support and guide the conveyor belt. The spacing of these idlers is crucial because it directly affects the conveyor’s efficiency, belt life, and material handling performance.
Explanation of Idler Spacing in Belt Conveyors
Idler spacing is determined based on several factors, including the type of material being transported, the conveyor belt width, the load per unit length, and the conveyor’s operational speed. Proper idler spacing ensures that the belt is adequately supported, preventing sagging and minimizing wear and tear. Inadequate idler spacing can lead to belt misalignment, increased power consumption, and potential damage to both the belt and the conveyed material.
Idler spacing can vary depending on the type of idler used. There are different types of idlers, such as carrying idlers, return idlers, impact idlers, and training idlers, each serving a specific purpose. Carrying idlers support the loaded belt, return idlers support the empty belt, impact idlers are installed at loading points to absorb shock, and training idlers help maintain the belt’s alignment.
Importance of Proper Idler Spacing
Proper idler spacing is vital for several reasons:
- Belt Longevity: Correctly spaced idlers reduce the stress on the belt, thereby extending its lifespan.
- Operational Efficiency: Well-spaced idlers ensure smooth belt movement, reducing power consumption and improving overall efficiency.
- Material Handling: Consistent idler spacing prevents material spillage and ensures uniform material distribution on the belt.
- Maintenance Costs: By minimizing wear and tear, proper idler spacing reduces maintenance frequency and associated costs.
How to Find and Use Idler Spacing Belt Conveyor PDFs
Idler spacing belt conveyor PDFs are valuable resources for engineers and maintenance personnel. These documents typically contain detailed guidelines, calculations, and tables that help in determining the appropriate idler spacing for various conveyor systems.
To find these PDFs, one can search online databases, manufacturer websites, and industry publications. Once obtained, these documents can be used to:
- Calculate Idler Spacing: Utilize the provided formulas and tables to determine the optimal spacing based on specific conveyor parameters.
- Design New Systems: Reference the guidelines to design new conveyor systems with appropriate idler spacing from the start.
- Troubleshoot Existing Systems: Use the information to identify and correct issues related to improper idler spacing in existing conveyor setups.
Idler Spacing Belt Conveyor Dimensions
Key Dimensions Involved in Idler Spacing
Several key dimensions influence idler spacing in belt conveyors:
- Belt Width: The width of the conveyor belt dictates the size and number of idlers required.
- Idler Diameter: The diameter of the idlers affects the spacing, with larger diameters allowing for greater spacing.
- Load Capacity: The weight of the material being conveyed determines the load per unit length, influencing idler spacing.
- Belt Speed: Higher speeds may necessitate closer idler spacing to maintain belt stability.
- Conveyor Length and Incline: The overall length and incline of the conveyor also play a role in determining idler spacing.
Impact of Conveyor Dimensions on Idler Spacing
The dimensions of a conveyor system have a direct impact on idler spacing. For example, a wider belt requires more idlers to support its weight and prevent sagging. Similarly, a conveyor transporting heavy loads or operating at high speeds may need closer idler spacing to ensure adequate support and prevent belt damage.
The incline of the conveyor can also affect idler spacing. On inclined conveyors, idlers must be spaced closer together to counteract the gravitational forces acting on the belt and the material being transported. Conversely, on flat conveyors, idler spacing can be more generous.
Guidelines for Determining the Correct Dimensions
Determining the correct dimensions for idler spacing involves several steps:
- Assess the Material Characteristics: Consider the type, weight, and size of the material being transported.
- Evaluate Conveyor Specifications: Review the belt width, speed, and load capacity of the conveyor system.
- Consult Manufacturer Guidelines: Refer to the manufacturer’s recommendations for idler spacing based on the specific conveyor model and application.
- Perform Calculations: Use standard formulas and tables provided in idler spacing belt conveyor PDFs to calculate the optimal spacing.
- Consider Operational Conditions: Account for environmental factors such as temperature, humidity, and dust, which can affect conveyor performance and idler spacing.
Using an Idler Spacing Belt Conveyor Calculator
Idler Spacing Belt Conveyor Calculators
Idler spacing belt conveyor calculators are specialized tools designed to simplify the process of determining the optimal idler spacing for conveyor systems. These calculators use input parameters such as belt width, load capacity, belt speed, and material characteristics to provide accurate idler spacing recommendations.
How to Use These Calculators for Accurate Spacing
Using an idler spacing belt conveyor calculator involves the following steps:
- Input Conveyor Specifications: Enter the relevant details about the conveyor system, including belt width, load capacity, and belt speed.
- Enter Material Characteristics: Provide information about the material being transported, such as its weight, size, and abrasiveness.
- Adjust Operational Parameters: Modify any additional parameters such as incline angle, environmental conditions, and safety factors.
- Generate Results: The calculator processes the input data and generates recommended idler spacing values based on industry standards and best practices.
These calculators often come with user-friendly interfaces and may include visual aids such as diagrams and charts to help users understand the results better.
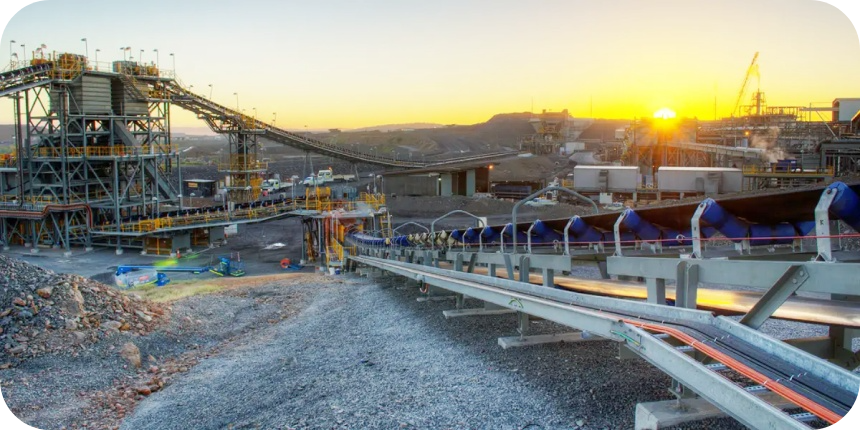
Benefits of Using a Calculator for Idler Spacing
The benefits of using an idler spacing belt conveyor calculator are numerous:
- Accuracy: Calculators provide precise idler spacing recommendations based on specific conveyor and material parameters, reducing the risk of human error.
- Efficiency: They save time by automating complex calculations and providing quick results.
- Consistency: Using a calculator ensures uniformity in idler spacing across different sections of the conveyor, enhancing system performance.
- Optimization: Calculators help optimize conveyor design by suggesting the most efficient idler spacing, leading to reduced operational costs and improved longevity.
- Troubleshooting: They can be used to diagnose and resolve issues related to improper idler spacing in existing conveyor systems.
Understanding and implementing proper idler spacing in belt conveyors is essential for efficient and reliable material handling operations. Resources such as idler spacing belt conveyor PDFs and calculators play a vital role in achieving optimal idler spacing, thereby enhancing conveyor performance and longevity. By following the guidelines and utilizing the available tools, engineers and maintenance personnel can ensure their conveyor systems operate at peak efficiency, with minimized downtime and maintenance costs.
Idler Spacing Belt Conveyor: Conveyor Idler Frame Dimensions
Importance of the Conveyor Idler Frame in Belt Conveyors
The conveyor idler frame is a critical component in belt conveyor systems, providing support and stability for the idlers and the conveyor belt. It ensures that the idlers are held in the correct position, maintaining the alignment and tension of the belt as it moves materials from one point to another. The idler frame’s robustness and precision are essential for preventing belt misalignment, minimizing wear and tear, and ensuring efficient material transport.
A well-designed idler frame contributes to the overall durability and performance of the conveyor system. It must be able to withstand the operational stresses and environmental conditions to which it is exposed. The idler frame also facilitates easy maintenance and replacement of idlers, reducing downtime and operational costs.
Key Dimensions of Conveyor Idler Frames
When considering idler spacing in a belt conveyor, the dimensions of the idler frame play a significant role. Key dimensions include:
- Frame Length: The length of the frame should match the width of the conveyor belt and accommodate the number of idlers required to support the belt and the load. The frame must be long enough to ensure proper support and alignment of the belt.
- Frame Height: The height of the frame must be sufficient to provide the necessary clearance for the idlers and the belt. This includes accounting for any potential sag in the belt and ensuring there is no interference with other components of the conveyor system.
- Frame Width: The width of the frame should align with the width of the idlers and the belt. It must provide adequate support to prevent any lateral movement of the idlers.
- Mounting Points: The placement and design of mounting points are crucial for securing the frame to the conveyor structure. These must be robust and precisely positioned to ensure stability and ease of installation.
- Material Thickness: The thickness of the material used for the frame affects its strength and durability. Frames made from thicker materials can withstand higher loads and more severe operating conditions.
How to Choose the Right Frame Dimensions for Your System
Choosing the right idler frame dimensions for your belt conveyor system involves several considerations:
- Conveyor Belt Width and Length: Ensure the frame dimensions match the width and length of the conveyor belt. The frame must support the entire width of the belt and be long enough to accommodate the required idler spacing.
- Load Capacity: Consider the weight and type of material being transported. Heavier loads require stronger frames with greater material thickness and robust construction.
- Environmental Conditions: Take into account the operating environment. For harsh conditions, such as exposure to corrosive materials or extreme temperatures, select frames made from materials that can withstand these conditions.
- Maintenance Requirements: Choose frames that allow easy access for maintenance and replacement of idlers. This helps minimize downtime and operational costs.
- Compatibility: Ensure the frame dimensions are compatible with other components of the conveyor system, such as the support structure and the idlers.
Idler Spacing Belt Conveyor: Surcharge Angle in Belt Conveyor Systems
Definition and Significance of the Surcharge Angle
The surcharge angle, also known as the angle of repose, is the maximum angle at which bulk materials can be piled on a belt conveyor without sliding off. It is a critical factor in the design and operation of belt conveyor systems as it influences the cross-sectional area of the load on the belt and, consequently, the capacity of the conveyor.
The surcharge angle depends on the properties of the material being conveyed, including particle size, shape, moisture content, and cohesiveness. Understanding the surcharge angle is essential for determining the appropriate idler spacing in belt conveyors, ensuring efficient and safe material transport.
How the Surcharge Angle Affects Idler Spacing
The surcharge angle directly affects the cross-sectional shape of the load on the conveyor belt, which in turn influences the idler spacing. Key considerations include:
- Load Distribution: A higher surcharge angle results in a more triangular load shape, which can place additional stress on the idlers. This requires closer idler spacing to provide adequate support and prevent belt sagging.
- Material Stability: Materials with a low surcharge angle are more prone to spillage, necessitating closer idler spacing to maintain stability and prevent material loss.
- Conveyor Capacity: The effective load capacity of the conveyor is influenced by the surcharge angle. Accurate calculation of the surcharge angle ensures optimal idler spacing, maximizing the conveyor’s load capacity and efficiency.
Methods to Measure and Adjust the Surcharge Angle
Measuring and adjusting the surcharge angle involves several steps:
- Material Testing: Conduct tests on the material to determine its angle of repose. This can be done by pouring the material onto a flat surface and measuring the resulting pile’s angle.
- Simulation: Use simulation software to model the material flow on the conveyor and determine the appropriate surcharge angle. This helps in optimizing the idler spacing and overall conveyor design.
- Adjusting Belt Speed and Tension: Fine-tune the belt speed and tension to achieve the desired surcharge angle. Properly adjusted belt speed and tension help maintain the material’s stability on the belt.
- Regular Monitoring: Continuously monitor the material flow and surcharge angle during operation. Make adjustments as necessary to maintain optimal performance and prevent spillage.
Idler Spacing Belt Conveyor: Types of Idlers in Belt Conveyor Systems
Overview of Various Types of Idlers Used in Belt Conveyors
Idlers are critical components in belt conveyor systems, providing support and guidance for the conveyor belt. There are several types of idlers, each serving specific functions:
- Carrying Idlers: Support the loaded side of the belt and ensure it remains flat and stable.
- Return Idlers: Support the empty side of the belt as it returns to the starting point.
- Impact Idlers: Positioned at loading points to absorb the impact of heavy loads and protect the belt.
- Troughing Idlers: Form a trough shape in the belt, ideal for carrying bulk materials.
- Training Idlers: Help maintain belt alignment by correcting any deviations in the belt’s path.
- Self-Aligning Idlers: Automatically adjust their position based on the belt’s movement to ensure continuous alignment.
Specific Functions of Each Type of Idler
- Carrying Idlers: These idlers support the load-bearing side of the conveyor belt. They ensure the belt remains flat and stable, preventing sagging and reducing wear and tear.
- Return Idlers: Located on the underside of the conveyor, return idlers support the empty belt as it returns to the starting point. They help maintain the belt’s alignment and prevent it from sagging.
- Impact Idlers: Positioned at loading points, impact idlers are designed to absorb the impact of heavy loads, protecting the belt from damage and extending its lifespan.
- Troughing Idlers: These idlers form a trough shape in the belt, which is ideal for carrying loose or bulk materials. They provide stability to the belt and minimize spillage.
- Training Idlers: Training idlers help correct any deviations in the belt’s alignment, ensuring it runs smoothly and stays on course. They are essential for reducing wear and tear and preventing operational disruptions.
- Self-Aligning Idlers: Self-aligning idlers automatically adjust their position based on the belt’s movement, ensuring continuous alignment without manual intervention. This enhances the efficiency and reliability of the conveyor system.
How Different Idlers Contribute to Optimal Belt Performance
Each type of idler plays a specific role in ensuring optimal belt performance:
- Carrying Idlers: By providing consistent support, carrying idlers prevent the belt from sagging and reduce wear and tear, extending the belt’s lifespan.
- Return Idlers: Return idlers maintain the belt’s alignment and prevent it from sagging, ensuring smooth operation and reducing maintenance costs.
- Impact Idlers: Impact idlers absorb the energy of heavy loads, protecting the belt from damage and reducing the frequency of repairs.
- Troughing Idlers: Troughing idlers ensure efficient transport of bulk materials by maintaining a stable and spill-free load.
- Training Idlers: Training idlers correct misalignment issues, ensuring the belt runs smoothly and reducing operational disruptions.
- Self-Aligning Idlers: Self-aligning idlers provide continuous alignment, enhancing the overall efficiency and reliability of the conveyor system.
The dimensions and idler spacing belt conveyor frames, the understanding of surcharge angles, and the selection of appropriate idlers are crucial for the efficient and reliable operation of belt conveyor systems. Properly designed and maintained conveyor systems contribute to increased productivity, reduced maintenance costs, and extended equipment lifespan. Understanding the nuances of idler spacing in belt conveyors and the roles of different idler types is essential for optimizing material handling operations and achieving long-term operational success.
Fill out the form to receive a quote for our idler spacing belt conveyor.
FAQs about Idler Spacing Belt Conveyor
The spacing between idlers in a conveyor system, also known as idler pitch, can vary depending on several factors such as the type of material being transported, the width and speed of the conveyor belt, and the specific requirements of the conveyor design. Generally, for carrying idlers on the load-bearing side of the conveyor, the spacing can range from 1 meter (3.3 feet) to 1.5 meters (5 feet). For return idlers on the non-load-bearing side, the spacing is typically wider, ranging from 2 meters (6.6 feet) to 3 meters (9.8 feet).
The specific spacing must be carefully calculated to ensure adequate support for the belt and the materials being transported. Too wide a spacing can lead to belt sagging and potential misalignment issues, while too narrow a spacing can result in unnecessary costs and increased friction. Regular maintenance and inspections are essential to ensure that the idlers remain properly spaced and aligned to prevent operational issues and prolong the lifespan of the conveyor belt.
The spacing for conveyor rollers, which are used in various types of conveyor systems, depends on factors such as the weight and size of the items being conveyed, the type of conveyor system, and the operational requirements. In roller conveyors, where the rollers are the primary support for the items being transported, the spacing is typically determined by the “rule of thumb” that at least three rollers should be in contact with the item at all times. This ensures smooth and stable movement.
For light-duty roller conveyors, the spacing between rollers can range from 75 mm (3 inches) to 150 mm (6 inches). For medium to heavy-duty applications, the spacing can range from 150 mm (6 inches) to 300 mm (12 inches). Close spacing is particularly important for handling smaller items to prevent them from falling through the gaps between rollers. Conversely, for larger and heavier items, wider spacing can be used to reduce the number of rollers required while still providing adequate support.
Trough rollers, also known as troughing idlers, are used in belt conveyor systems to form a trough shape in the conveyor belt, which is ideal for carrying bulk materials. The spacing of trough rollers depends on factors such as the belt width, the type and density of the material being transported, and the conveyor’s operating conditions.
Typically, trough rollers are spaced between 1 meter (3.3 feet) and 1.5 meters (5 feet) apart for standard applications. However, in heavy-duty applications where the belt is subjected to higher loads, the spacing may be reduced to provide additional support. For example, in mining and quarrying operations, trough roller spacing might be as close as 0.6 meters (2 feet) to 1 meter (3.3 feet) to handle the increased weight and abrasive nature of the materials.
Proper spacing of trough rollers is critical to prevent belt sagging, ensure efficient material transport, and minimize wear and tear on the belt. Regular inspections and adjustments are necessary to maintain the correct spacing and ensure the longevity of the conveyor system.
The number of idlers in a conveyor belt system depends on the length of the conveyor, the type of idlers used, and the specific design and operational requirements of the system. A typical conveyor belt system will have multiple sets of carrying idlers, return idlers, impact idlers, and, in some cases, training and self-aligning idlers.
To determine the number of idlers, the length of the conveyor is divided by the spacing between idlers. For example, if a conveyor is 100 meters (328 feet) long and the carrying idlers are spaced 1.2 meters (4 feet) apart, there would be approximately 83 sets of carrying idlers. Similarly, if the return idlers are spaced 3 meters (10 feet) apart, there would be around 33 return idlers.
In addition to the basic idlers, special idlers such as impact idlers at loading points and training idlers for belt alignment may also be included. The exact number of these idlers will depend on the conveyor’s specific requirements and operational conditions. Proper planning and calculation are essential to ensure that the conveyor belt is adequately supported throughout its length, ensuring smooth operation and longevity of the system.
Last Updated on August 16, 2024 by Jordan Smith
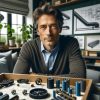
Jordan Smith, a seasoned professional with over 20 years of experience in the conveyor system industry. Jordan’s expertise lies in providing comprehensive solutions for conveyor rollers, belts, and accessories, catering to a wide range of industrial needs. From initial design and configuration to installation and meticulous troubleshooting, Jordan is adept at handling all aspects of conveyor system management. Whether you’re looking to upgrade your production line with efficient conveyor belts, require custom conveyor rollers for specific operations, or need expert advice on selecting the right conveyor accessories for your facility, Jordan is your reliable consultant. For any inquiries or assistance with conveyor system optimization, Jordan is available to share his wealth of knowledge and experience. Feel free to reach out at any time for professional guidance on all matters related to conveyor rollers, belts, and accessories.