Choosing the Right Impact Pad Belt Conveyor
An impact pad belt conveyor is a critical component in material handling systems, designed to protect conveyor belts from damage caused by heavy and sharp materials. Impact pads are strategically placed in areas where materials are loaded onto the belt, absorbing the shock and reducing wear and tear. These pads help in maintaining the integrity and performance of the conveyor belt, preventing costly downtime and extending the belt’s lifespan. By using an impact pad belt conveyor, industries can ensure smoother operations, minimize maintenance costs, and enhance overall efficiency. Understanding the role and benefits of impact pads is essential for optimizing conveyor system performance.
Impact Pad Belt Conveyor
The concept of an impact pad belt conveyor is integral to the efficient operation of conveyor systems in various industries. An impact pad is a crucial component designed to absorb the impact of materials being loaded onto the conveyor belt, thereby reducing wear and tear and prolonging the belt’s lifespan.
Importance of Properly Integrating Impact Pads Within Conveyor Frames for Optimal Belt Protection
The integration of impact pads within conveyor frames is vital for protecting the conveyor belt and ensuring the system’s longevity. Impact pads are typically installed at points where materials are loaded onto the conveyor belt. These areas are particularly susceptible to damage due to the high impact forces generated by falling materials.
Impact pads are made from durable materials such as rubber or polyurethane, designed to absorb and dissipate the energy from the falling materials. This absorption reduces the direct impact on the conveyor belt, minimizing the risk of tears, punctures, and other forms of damage. By protecting the belt in this way, impact pads help to extend the belt’s service life and reduce maintenance costs.
Proper integration of impact pads within the conveyor frames involves precise positioning and secure attachment. The pads must be placed at the exact points where the materials will impact the belt, ensuring maximum protection. Additionally, they must be securely attached to the frames to prevent them from shifting or becoming dislodged during operation. This secure attachment ensures that the impact pads can effectively perform their protective function without compromising the stability of the conveyor system.
Types of Impact Pads for Belt Conveyors
There are several types of impact pads available for belt conveyors, each designed to meet specific needs and applications. The choice of impact pad depends on factors such as the type of material being handled, the impact force, and the operating conditions of the conveyor system.
Rubber Impact Pads
Rubber impact pads are commonly used in conveyor systems due to their durability and excellent shock-absorbing properties. These pads are typically made from high-quality rubber compounds that can withstand the impact of heavy and abrasive materials. Rubber impact pads are ideal for applications where high impact resistance and longevity are required.
Polyurethane Impact Pads
Polyurethane impact pads offer superior impact absorption and wear resistance compared to rubber pads. They are particularly suitable for applications involving highly abrasive materials or extreme operating conditions. Polyurethane pads are known for their resilience and ability to maintain their protective properties over extended periods, even under harsh conditions.
Composite Impact Pads
Composite impact pads are made from a combination of materials, such as rubber and polyurethane, to provide a balance of impact absorption, wear resistance, and durability. These pads are designed to offer optimal protection in a wide range of applications, making them a versatile choice for many conveyor systems.
What is Impact Pad Belt Conveyor
In industrial settings, the efficiency and longevity of conveyor systems are paramount. One of the critical components that enhance the performance and durability of these systems is the impact pad. The impact pad belt conveyor system is designed to absorb the impact of heavy loads, reduce wear and tear, and maintain optimal alignment. In this context, the integration of advanced tracking systems such as the Tru-Trac conveyor belt tracking system further enhances the functionality and reliability of conveyor systems.
Tru-Trac Conveyor Belt Tracking System
Introduction to the Tru-Trac Conveyor Belt Tracking System and Its Benefits
The Tru-Trac conveyor belt tracking system is a state-of-the-art solution designed to address one of the most common issues in conveyor operations: belt misalignment. Misalignment can lead to significant problems, including belt damage, spillage, increased maintenance costs, and operational downtime. The Tru-Trac system provides a comprehensive solution to these issues by ensuring that the conveyor belt remains centered and aligned throughout its operation.
Key Benefits of the Tru-Trac System:
- Improved Belt Life: By maintaining proper alignment, the Tru-Trac system reduces the wear and tear on the belt edges, significantly extending the life of the conveyor belt.
- Reduced Maintenance Costs: Proper alignment minimizes the need for frequent adjustments and repairs, lowering maintenance costs and reducing downtime.
- Enhanced Safety: Misaligned belts can pose safety hazards, including the risk of spillage and equipment damage. The Tru-Trac system helps prevent these issues, ensuring a safer working environment.
- Increased Efficiency: By keeping the belt properly aligned, the system ensures smooth and uninterrupted operation, enhancing overall efficiency and productivity.
The Tru-Trac system utilizes a unique design that automatically adjusts to the belt’s movement, providing real-time tracking and correction. This proactive approach ensures that the belt remains centered, even in demanding applications.
Integration of Impact Pads with the Tru-Trac System for Enhanced Belt Alignment and Performance
Impact pads are integral components in conveyor systems, especially in areas where heavy loads are introduced onto the belt. These pads are designed to absorb the impact of the material being loaded, reducing the shock and minimizing the wear on the belt and supporting structure. The integration of impact pads with the Tru-Trac conveyor belt tracking system creates a robust solution that addresses both alignment and impact issues.
Benefits of Combining Impact Pads with the Tru-Trac System:
- Enhanced Impact Absorption: Impact pads are made from high-density materials such as rubber or polyurethane, providing excellent shock absorption. This reduces the risk of damage to the belt and other components, extending the overall life of the conveyor system.
- Improved Belt Alignment: The Tru-Trac system ensures that the belt remains centered, while the impact pads provide a stable and cushioned surface for the material to land on. This combination reduces the likelihood of belt misalignment caused by uneven loading.
- Reduced Belt Wear: The cushioning effect of the impact pads minimizes the direct contact between the belt and the material, reducing wear and tear. This is particularly beneficial in applications involving abrasive or heavy materials.
- Increased Load Capacity: With the combined benefits of impact absorption and proper alignment, conveyor systems can handle heavier loads more efficiently. This increases the system’s capacity and productivity.
How the Integration Works:
- Placement of Impact Pads: Impact pads are strategically placed at loading zones, where the material first makes contact with the belt. These pads provide a cushioned surface that absorbs the initial shock of the load.
- Real-Time Adjustment: The Tru-Trac system continuously monitors the belt’s position and makes real-time adjustments to ensure it remains centered. This proactive alignment reduces the risk of misalignment caused by uneven or heavy loads.
- Durability and Reliability: The combination of impact pads and the Tru-Trac system creates a durable and reliable conveyor solution. The impact pads protect the belt from damage, while the tracking system ensures consistent alignment, resulting in a more efficient and longer-lasting conveyor system.
How about Impact Pad Belt Conveyor
An impact pad belt conveyor is an essential component in various industrial applications, providing protection and longevity to the conveyor belt by absorbing the impact of materials during loading. This system integrates impact pads at critical points to enhance the durability and efficiency of the conveyor system.
Conveyor Idlers
Conveyor idlers play a crucial role in the smooth operation of a conveyor belt system. They are cylindrical rollers that support the conveyor belt and the material being transported, ensuring minimal friction and preventing sagging or misalignment. Understanding the function and importance of conveyor idlers is essential to appreciate the overall efficiency and longevity of an impact pad belt conveyor.
Overview of Conveyor Idlers and Their Role in Supporting and Guiding the Belt
Conveyor idlers are strategically positioned along the conveyor frame to provide continuous support to the moving belt. These idlers are usually spaced at regular intervals to distribute the load evenly and reduce the strain on the conveyor belt. They come in various types, each designed to serve a specific function within the conveyor system:
- Carrying Idlers: These idlers are located on the carrying side of the belt and support the weight of the material being transported. They help maintain the shape of the belt, preventing it from sagging under the load.
- Return Idlers: Positioned on the return side of the belt, these idlers support the empty belt as it returns to the loading point. They help keep the belt aligned and prevent it from flapping.
- Impact Idlers: Installed at loading points where the material first hits the belt, impact idlers are designed to absorb the shock and reduce the wear on the belt. They typically feature rubber rings or rollers that provide cushioning.
- Troughing Idlers: These idlers are used to shape the belt into a trough to better contain the transported material, reducing spillage and improving the belt’s load-carrying capacity.
- Self-aligning Idlers: These idlers are designed to automatically adjust and correct any misalignment of the belt, ensuring it runs straight and true along the conveyor frame.
The primary role of conveyor idlers is to provide support and guide the conveyor belt through its motion. By maintaining the belt’s alignment and shape, idlers reduce the friction between the belt and the conveyor structure, thereby minimizing wear and energy consumption.
Interaction Between Impact Pads and Conveyor Idlers for Improved Belt Stability and Longevity
The interaction between impact pads and conveyor idlers is critical for enhancing the performance and lifespan of an impact pad belt conveyor. Impact pads are installed at points where the material is loaded onto the conveyor belt. These pads absorb the energy from the falling material, protecting the belt from damage and reducing the stress on the idlers.
Impact pads are typically made from high-density rubber or polyurethane, materials known for their excellent shock-absorbing properties. They are placed directly below the loading zone, where they cushion the impact of the material and distribute the load evenly across the belt. This distribution is crucial for preventing localized wear and tear, which can lead to premature belt failure.
The integration of impact pads with impact idlers provides a dual layer of protection for the conveyor belt. While the impact pads absorb the initial shock, the impact idlers further reduce the impact force by providing additional cushioning and support. This combination ensures that the belt remains stable and aligned, even under heavy and continuous loading conditions.
Benefits of Impact Pad Belt Conveyor Systems
The use of impact pad belt conveyor systems offers numerous advantages that enhance operational efficiency, reduce maintenance costs, and improve safety in industrial settings.
Enhanced Belt Protection
The primary benefit of an impact pad belt conveyor is the enhanced protection it provides to the conveyor belt. By absorbing the impact energy from falling materials, impact pads prevent damage such as cuts, tears, and punctures. This protection is particularly important in industries that handle heavy or abrasive materials, where the risk of belt damage is high.
Reduced Maintenance Costs
Impact pads help reduce maintenance costs by minimizing the wear and tear on the conveyor belt and idlers. Without impact pads, the constant impact of falling materials can cause significant damage, leading to frequent repairs and replacements. By mitigating this impact, impact pads extend the lifespan of the belt and idlers, reducing the frequency of maintenance interventions and associated costs.
Improved Safety
An impact pad belt conveyor enhances safety in the workplace by maintaining the integrity of the conveyor belt. Damaged belts can pose significant safety risks, including the potential for belt breakage and material spillage. By protecting the belt from impact damage, impact pads help prevent these risks, ensuring a safer working environment.
Increased Operational Efficiency
By reducing belt damage and maintenance requirements, impact pads contribute to increased operational efficiency. Conveyor systems can operate more reliably and with less downtime, ensuring that production processes run smoothly and efficiently. This increased efficiency can lead to higher productivity and profitability for businesses that rely on conveyor systems.
Installation and Maintenance of Impact Pads and Conveyor Idlers
Proper installation and maintenance of impact pads and conveyor idlers are essential for ensuring their effectiveness and longevity. The installation process involves positioning the pads and idlers accurately at the impact zones and securing them firmly to the conveyor frames. Regular inspection and maintenance are also necessary to ensure that the pads and idlers remain in good condition and continue to provide adequate protection and support.
Installation Tips for Impact Pads and Conveyor Idlers
- Precision Placement: Ensure precise placement of the impact pads and idlers at the points where materials are loaded onto the conveyor belt. This ensures maximum protection and support.
- Secure Attachment: Use appropriate fastening methods to secure the pads and idlers firmly to the conveyor frames, preventing movement or dislodgment during operation.
- Follow Manufacturer Guidelines: Adhere to manufacturer guidelines for installation to ensure optimal performance and protection.
Maintenance Guidelines
- Regular Inspections: Conduct regular inspections to check for signs of wear or damage to the impact pads and idlers.
- Timely Replacements: Replace worn or damaged pads and idlers promptly to maintain effective protection and support for the conveyor belt.
- Cleanliness: Keep the impact pads and idlers clean and free from debris to ensure they can absorb impact energy and support the belt effectively.
The Types of Impact Pad Belt Conveyor
An impact pad belt conveyor is an essential component in various industrial applications, designed to protect and prolong the life of conveyor belts by absorbing the impact of materials during loading. This system integrates impact pads at critical points to enhance durability and efficiency.
Conveyor Belt Skirting
Conveyor belt skirting is a vital accessory in the overall conveyor system. It plays a crucial role in minimizing spillage and containing material on the conveyor belt, thereby improving the efficiency and cleanliness of the operation.
Explanation of Conveyor Belt Skirting and Its Function in Minimizing Spillage
Conveyor belt skirting is installed along the sides of the conveyor belt, particularly at loading and transfer points. It consists of a series of flexible barriers that extend downward from the conveyor frame to the belt surface. These barriers are typically made from rubber or other durable materials that can withstand the abrasive and corrosive nature of the transported materials.
The primary function of conveyor belt skirting is to seal the edges of the conveyor belt and prevent material spillage. During the loading process, as materials are dropped onto the belt, they often scatter and fall off the sides. Skirting creates a seal that keeps the materials on the belt, guiding them smoothly along the conveyor path without loss. This containment is crucial for maintaining a clean work environment and reducing material waste.
Additionally, conveyor belt skirting helps to minimize dust generation, which can be a significant issue in industries handling fine or dry materials. By containing the material, skirting reduces the amount of dust that escapes into the air, thereby improving air quality and reducing the need for extensive dust control measures.
Relationship Between Impact Pads and Belt Skirting in Enhancing Conveyor System Efficiency
The integration of impact pads with belt skirting significantly enhances the efficiency and longevity of an impact pad belt conveyor. These components work together to protect the conveyor belt and improve the overall performance of the system.
Protection and Load Distribution
Impact pads are installed at loading points to absorb the shock of falling materials, thereby protecting the conveyor belt from damage such as cuts, tears, and punctures. These pads are made from high-density rubber or polyurethane, which can absorb and dissipate the impact energy. This protective function is crucial for extending the life of the conveyor belt and reducing maintenance costs.
When used in conjunction with belt skirting, impact pads ensure that the materials are not only contained on the belt but also distributed evenly. The skirting keeps the materials centered on the belt, preventing them from spilling over the edges. This containment allows the impact pads to effectively absorb the load without excessive wear and tear on the belt edges.
Minimizing Material Loss and Improving Cleanliness
The combination of impact pads and belt skirting minimizes material loss during the loading process. Impact pads cushion the impact, reducing the bounce and scatter of materials, while skirting ensures that any displaced material is directed back onto the belt. This synergy is vital for maintaining a clean and efficient operation, as it reduces the need for manual cleanup and minimizes material waste.
Enhancing Operational Efficiency
By preventing spillage and protecting the belt from impact damage, the integration of impact pads and belt skirting enhances the overall operational efficiency of the conveyor system. Reduced spillage means less downtime for cleaning and fewer interruptions in the material flow. Additionally, protecting the belt from damage leads to fewer maintenance interventions and longer belt life, which further contributes to operational efficiency and cost savings.
Reducing Dust and Improving Safety
The combined use of impact pads and belt skirting also plays a significant role in reducing dust generation. Impact pads absorb the energy of falling materials, reducing the amount of dust generated upon impact. Belt skirting contains the materials and dust, preventing them from escaping into the air. This containment is crucial for maintaining a safe working environment, as excessive dust can pose health risks to workers and increase the risk of fire or explosion in certain industrial settings.
Benefits of Integrating Impact Pads and Belt Skirting
Integrating impact pads and belt skirting into an impact pad belt conveyor system offers numerous benefits that enhance performance, safety, and cost-effectiveness.
Enhanced Belt Protection
Impact pads provide a cushioning effect that protects the belt from the direct impact of falling materials. This protection is particularly important in industries that handle heavy or abrasive materials. Belt skirting complements this by containing the material and reducing edge wear.
Reduced Maintenance Costs
By minimizing belt damage and material spillage, the combination of impact pads and belt skirting reduces maintenance requirements. This reduction leads to lower maintenance costs and less downtime, allowing for more continuous and efficient operation.
Improved Safety and Cleanliness
The containment of materials and reduction of dust generation improve workplace safety and cleanliness. A cleaner environment reduces the risk of accidents and health issues related to dust exposure, while effective containment prevents slip hazards and keeps walkways clear.
Increased Operational Efficiency
The combined use of impact pads and belt skirting ensures that the conveyor system operates smoothly and efficiently. By reducing spillage and belt damage, these components contribute to uninterrupted material flow and consistent production rates.
Installation and Maintenance Considerations
Proper installation and maintenance of impact pads and belt skirting are crucial for optimizing their performance and ensuring the longevity of the conveyor system.
Installation Tips
- Accurate Positioning: Ensure that impact pads are precisely positioned at the loading points to maximize their effectiveness in absorbing impact.
- Secure Attachment: Use appropriate fastening methods to securely attach both impact pads and belt skirting to the conveyor frame, preventing displacement during operation.
- Compatibility: Choose impact pads and skirting materials that are compatible with the specific type of material being transported to ensure durability and effectiveness.
Maintenance Guidelines
- Regular Inspections: Conduct regular inspections to check for signs of wear or damage to impact pads and belt skirting.
- Timely Replacements: Replace worn or damaged components promptly to maintain effective protection and containment.
- Cleaning: Keep the skirting clean and free from buildup to ensure proper sealing and containment of materials.
FAQS about Impact Pad Belt Conveyor
Preventing conveyor belt damage involves several proactive measures and regular maintenance practices. Firstly, ensuring that the conveyor is properly aligned and that all rollers and pulleys are functioning correctly can prevent undue stress on the belt. Using impact rollers and idlers at high-impact zones can absorb the shock and reduce wear. Regular inspection and maintenance are crucial; this includes checking for any signs of wear, tears, or misalignment and addressing them promptly. Additionally, using high-quality materials for the belt and its components, such as impact pads and skirting, can significantly enhance the belt’s durability. Training employees on proper loading techniques and the importance of regular maintenance can also help in minimizing damage and prolonging the life of the conveyor belt.
Impact pad material refers to the specialized material used in impact beds or zones where the conveyor belt is subjected to high impact from loading materials. These materials are typically made from durable, wear-resistant substances such as rubber, urethane, or composite materials. The primary function of impact pad material is to absorb the shock and energy from the impact, protecting the conveyor belt and reducing maintenance costs. The choice of material depends on the nature of the materials being conveyed and the specific requirements of the conveyor system. High-quality impact pads ensure the longevity of the belt and smooth operation, making them a critical component in high-impact areas.
An impact idler for a conveyor is similar to an impact roller but is part of a series of closely spaced rollers that support the belt in areas where it is subjected to heavy loads or impacts. These idlers are equipped with rubber discs or rings that absorb the energy from the falling materials, reducing the stress on the conveyor belt. Impact idlers are essential in maintaining the integrity of the belt, especially in high-impact zones such as loading and transfer points. They help to distribute the load evenly, minimize belt deformation, and prevent costly maintenance issues. By incorporating impact idlers, conveyor systems can operate more efficiently and with less downtime.
An impact roller on a belt conveyor is a specific type of roller designed to absorb the energy and reduce the shock and vibration that occurs when heavy materials fall onto the conveyor belt. These rollers are typically placed at points where the conveyor receives the bulk load, such as transfer and loading areas. Impact rollers have a thick rubber covering around the steel core, which helps to cushion the belt and prevent damage. By minimizing the impact force, these rollers not only protect the conveyor belt from wear and tear but also ensure smoother operation, prolonging the overall lifespan of the conveyor system.
Last Updated on August 9, 2024 by Jordan Smith
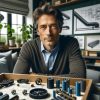
Jordan Smith, a seasoned professional with over 20 years of experience in the conveyor system industry. Jordan’s expertise lies in providing comprehensive solutions for conveyor rollers, belts, and accessories, catering to a wide range of industrial needs. From initial design and configuration to installation and meticulous troubleshooting, Jordan is adept at handling all aspects of conveyor system management. Whether you’re looking to upgrade your production line with efficient conveyor belts, require custom conveyor rollers for specific operations, or need expert advice on selecting the right conveyor accessories for your facility, Jordan is your reliable consultant. For any inquiries or assistance with conveyor system optimization, Jordan is available to share his wealth of knowledge and experience. Feel free to reach out at any time for professional guidance on all matters related to conveyor rollers, belts, and accessories.