Adopting the Right Techniques for Impact Roller Compaction
In the domain of construction, the critical task of soil stabilization is often achieved through compaction—a process aimed at increasing the density and stability of soil for construction readiness. Among the spectrum of compaction methods, impact roller compaction marks its prominence by utilizing a mechanized system that delivers high-energy blows to the ground, distinctly different from traditional methods that apply uniform pressure. This innovative technique involves an impact roller striking the ground surface with significant force, effectively compacting and densifying the soil beneath to desired levels. The striking advantage of impact roller compaction over conventional techniques lies in its ability to reach deeper soil layers, enhancing compaction depth and efficiency. Thus, while both traditional and impact roller methods strive to fortify ground for construction, impact roller compaction offers a specialized approach for achieving deeper, more durable soil stabilization.
The Science Behind High Energy Impact Roller Compaction
The practice of impact roller compaction serves as a cornerstone in the realm of modern construction, particularly when it comes to soil stabilization and ground preparation. This specialized method utilizes machinery equipped with heavy drums, designed to deliver a sequence of high-energy impacts to the soil surface, thus enhancing its density and stability. Let’s delve deeper into the nuances of this process, its distinction from traditional methods, and its implications on equipment design due to the risk of high-energy impact injuries.
Explanation of High Energy Impact Roller Compaction Process
Impact roller compaction leverages the dynamic force of heavyweight rollers to exert concentrated blows onto the soil. These rollers are often outfitted with protrusions (such as feet) or may even be smooth, depending on the specific compaction requirements. The process not only compacts the soil but also meticulously rearranges soil particles for optimal density. The operation rhythmically imparts high-energy impacts, causing a deeper and more uniform compaction compared to static methods. This technique is pivotal in projects demanding superior ground stability, where traditional compaction methods might fall short.
Comparison with Conventional Methods
A comparative analysis between impact roller compaction and traditional compaction techniques can illuminate their distinct operational mechanisms and efficacy:
High Energy Impact Injury and Equipment Design
In the design of equipment for impact roller compaction, the specter of high-energy impact injuries stands as a crucial consideration. Here are five pertinent aspects:
- Enhanced Safety Features: Equipment must encompass advanced safety features to protect operators from the high-energy impacts that are characteristic of this process.
- Operator Comfort: Vibration dampening and noise reduction technologies are essential to mitigate the physical toll on operators and circumvent potential hearing damage or hand-arm vibration syndrome.
- Structural Integrity: The machinery’s design necessitates a robust construction to withstand the repeated high-energy impacts without compromising operational integrity or longevity.
- Emergency Stop Mechanisms: Quick-response emergency stop features are critical to immediately halt operations in case of an unsafe situation, thereby preventing possible injuries.
- Training and Awareness: Given the specialized nature of impact roller compaction, comprehensive operator training on safety protocols and equipment handling is indispensable to minimize the risk of high-energy impact injuries.
Through understanding the mechanics behind impact roller compaction, distinguishing its benefits over conventional methods, and acknowledging the significance of impact injuries in equipment design, stakeholders can better navigate the complexities of modern construction projects. This knowledge fosters a safer, more efficient approach to achieving ground stability and readiness for construction endeavors.
Types of Impact Roller Compaction
Understanding the lingo is crucial when discussing impact roller compaction. Specifically, knowing the difference between impact rollers, sheep foot rollers, and pad foot or carrying rollers can significantly enhance your comprehension of the process. Let’s delve into each of these types, outlining their features, highlighting their benefits, and illustrating their applications in the realm of construction work.
Features and Benefits of Each Roller Type
Below is a detailed introduction to different types of impact roller compaction including impact rollers, sheep foot rollers, and carrying rollers, along with their respective features and benefits, presented in table format.
Applications of Impact Roller Compaction
Impact roller compaction’s versatility makes it an essential part of several construction scenarios. Here are three key applications:
- Construction Site Preparation: From roadways to industrial constructions, impact roller compaction is instrumental in achieving the ground stability and uniformity needed before any construction begins.
- Landfill Compaction: Impact rollers are effective in compacting waste materials in landfills, optimizing space utilization and preventing waste settlement over time.
- Embankment Construction: In the construction of embankments or dams, where soil reinforcement is critical, impact roller compaction delivers the superior, deeper compaction needed for ensuring structural stability.
Understanding the nuances of various roller types, benefits, and specific applications under the broad domain of impact roller compaction can enhance the decision-making process for optimum compaction and successful construction outcomes.
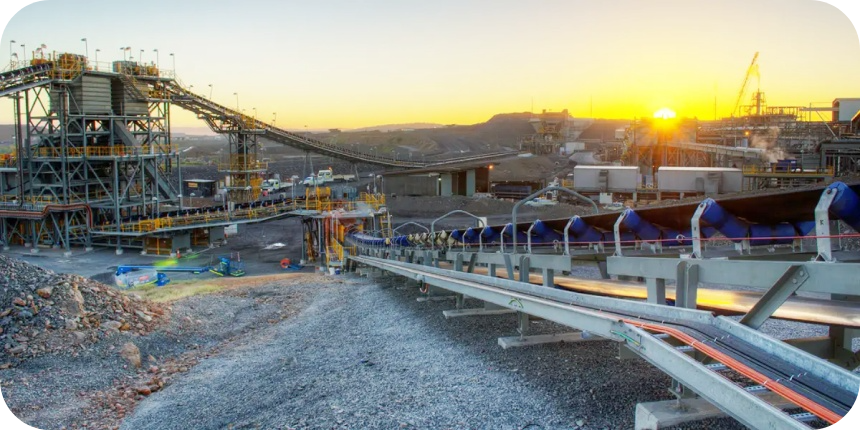
Impact Roller Compactions in the Market
When delving into the market for impact roller compaction equipment, there are numerous factors that prospective buyers need to consider to ensure that they select a machine that is conducive to their project’s success. This section aims to provide an in-depth look at what to focus on when confronting the vast array of options and illustrates the inherent advantages of using top-notch impact rollers for soil compaction. Furthermore, it offers guidance on how to choose the ideal impact roller compaction machinery tailored to meet the specific needs and challenges of your endeavor.
What to Look for in Impact Roller Compaction Equipment
Investing in an impact roller compaction machine, like any significant capital outlay, demands due diligence and a keen eye for detail. Here are a few aspects you should consider:
- Output and Performance: Verify the compaction output—how much ground can the roller cover efficiently and effectively?
- Engine Power and Efficiency: A more powerful engine can offer better compaction but also consider fuel efficiency and environmental impact.
- Durability and Maintenance: Equipment with a solid build and easy access to parts can reduce downtime and maintenance costs.
- Manufacturer Reputation and Support: Well-regarded manufacturers usually provide better after-sales support and warranties.
- Operator Safety and Comfort: Features that contribute to the operator’s safety and reduce fatigue can yield better performance and more consistent results.
Advantages of High-Quality Impact Rollers
The utilization of superior impact roller compaction machinery brings forth a plethora of benefits, prime among them include:
- Maximum Efficiency: High-quality rollers achieve faster soil compaction, thus saving on labor hours and operational costs.
- Greater Depth of Compaction: Ensuring the ground is compacted at deeper layers provides a more stable base for any construction project.
- Longevity: Premium machines are more resilient and tend to have a longer operational life due to higher quality materials and construction.
- Reduced Repair Frequency: Reliable machinery translates to fewer breakdowns and, consequently, less downtime and repair costs.
Selecting the Right Impact Roller Compaction for Your Project
Finding the perfect fit for your project can make all the difference in your outcomes. When selecting impact roller compaction equipment, here’s what to weigh:
- Project Size and Scope: Assess the project’s scale to determine the compaction power required.
- Soil Types on Site: Different rollers are optimized for different soil types—ensure the one you choose aligns with your site’s conditions.
- Flexibility and Adaptability: Consider if the equipment offers the versatility to handle varied tasks of your overall project.
- Budget: While cost is always a consideration, remember that cheaper options might lead to increased costs over the lifespan of the machinery.
By adhering to these tailored instructions, you will be equipped with the necessary insights to navigate the impact roller compaction market, discerning the perfect match for your project’s specific needs.
Impact Roller Compaction Technique
The impact roller compaction technique is a pivotal method in the construction and engineering fields, especially when it comes to preparing ground for various structures like roads, buildings, and embankments. This technique involves using specialized machinery to compact soil, thereby increasing its density and stability. Here, we’ll dive into a comprehensive guide on the process of impact roller compaction, discuss its efficiency compared to other compaction methods, and examine the variables that influence its effectiveness.
Step-by-Step Guide on the Impact Roller Compaction Process
The procedure of impact roller compaction encompasses several critical steps, ensuring that the soil reaches an optimal level of compaction. Following is a detailed exploration of this process:
- Preliminary Site Assessment: Before the commencement of compaction, a thorough evaluation of the site is necessary to understand soil types, moisture levels, and the area’s topography.
- Equipment Selection: Based on the preliminary assessment, the appropriate impact roller compaction machinery is selected, tailored to the soil characteristics and project requirements.
- Initial Compaction Passes: The compaction process begins with the roller making several passes over the area to be compacted, applying dynamic impacts to the soil.
- Moisture Adjustment (if required): In some cases, water may be added or removed from the soil to achieve the optimum moisture content for effective compaction.
- Final Compaction Passes: Additional passes are made until the desired soil density is achieved, confirmed through on-site density testing methods.
Efficiency of Rolling Dynamic Compaction
The impact roller compaction technique stands out for its efficiency, particularly when working with certain soil types or in large open spaces. This efficiency is attributable to:
- Depth of Compaction: Impact rollers can compact soil to greater depths compared to traditional rollers, making them ideal for projects requiring a stable foundation.
- Uniform Density Achievement: The dynamic nature of the impact allows for more uniform compaction across the site.
- Time and Cost Efficiency: The method is faster and, in many cases, more cost-effective, especially for large-scale projects because it requires fewer passes to achieve the desired compaction level.
Variables Influencing the Effectiveness of Compaction
Several key factors can influence the effectiveness of impact roller compaction, among them:
- Soil Type: Cohesive soils (clays) and non-cohesive soils (sands and gravels) react differently to compaction forces. Impact rollers are generally more effective on non-cohesive soils.
- Moisture Content: Optimal moisture content is crucial for effective compaction; too much or too little can hinder the process.
- Compaction Energy: The weight of the roller and the height from which it impacts the soil directly affect compaction effectiveness. Higher energy levels typically result in better compaction.
By understanding these variables and meticulously planning the compaction process, project managers and engineers can maximize the success of impact roller compaction techniques in their projects, ensuring the groundwork is laid for solid, stable construction.
Benefits of High Energy Impact Roller Compaction
The impact roller compaction method has revolutionized the field of construction and civil engineering, providing substantial advantages over traditional soil compaction techniques. Through the implementation of high-energy impact roller compaction, multiple benefits have been observed, including operational efficiency, enhanced depth of compaction, and remarkable effectiveness on a variety of soil types. This detailed exploration will compare the method with traditional compaction approaches and spotlight case studies demonstrating the successful application of high-energy impact roller compaction.
Operational Efficiency of Impact Roller Compaction
The efficiency gain experienced with high-energy impact roller compaction is multifold and includes:
- Reduced Compaction Time: With more significant energy imparted into the ground, each pass with an impact roller can cover a larger area in less time than traditional rollers.
- Fuel and Cost Savings: Greater efficiency equates to lower fuel consumption and operational costs over the lifespan of a project.
- Less Labor Intensive: Decreased reliance on manpower translates to reduced labor costs and minimized human error in the compaction process.
Enhanced Depth of Compaction
Deep compaction is critical in stabilizing the underlying soil for heavy structures, and high-energy impact roller compaction delivers distinct advantages in this aspect:
- Deeper Compaction Layers: This technique can achieve greater soil particle rearrangement at depths not possible with traditional methods.
- Strength and Stability: Greater depths of compaction ensure a more stable base, offering better load-bearing capability for infrastructure developments.
- Long-term Durability: A thoroughly compacted foundation is less susceptible to issues like differential settlement, which can affect the longevity of structures.
Effectiveness on Various Soil Types
One of the main reasons for the popularity of high-energy impact roller compaction is its versatility across different soil conditions:
- Range of Soil Adaptability: Impact rollers can effectively compact both cohesive and non-cohesive soils, which covers a broad spectrum of ground materials encountered in construction sites.
- Compaction in Challenging Conditions: Even in soils with higher moisture content or irregular particle sizes, this compaction method is capable of producing consistent compaction results.
Comparison with Traditional Compaction Methods
When evaluating the performance of high-energy impact roller compaction against traditional soil compaction techniques, several differences become apparent:
- Compaction Energy: High-energy impact rollers deliver far greater compaction force to the soil with each pass than traditional rolling or ramming equipment.
- Uniformity and Quality Control: The consistent application of energy ensures a more uniform compaction, leading to improved quality control in the compaction process.
- Environmental Impact: As high-energy rollers can achieve desired results with fewer passes, the environmental impact of the project, in terms of emissions and energy expenditure, is often lower.
Noteworthy Case Studies
Illustrating the effectiveness of high-energy impact roller compaction, several case studies underscore the practical applications and results:
- Airport Runway Projects: In several instances, impact rollers were used to prepare the sub-base for airport runways, where rigorous compaction standards are required to handle the heavy traffic of aircraft landings and take-offs.
- Large Infrastructure Developments: For instance, the use of this technology in constructing the base layers for major roadways and highway embankments has been noted to significantly reduce subsequent maintenance.
- Mining Operations: In creating firm bases for heavy machinery in mining operations, impact rollers have proven to reduce the settling period, allowing for faster operational deployment.
The advantages of high-energy impact roller compaction are evident across various areas of its application, leading to its growing preference over traditional soil compaction methods in many large-scale construction and engineering projects.
Impact Roller Compaction Conveyor Systems
The innovative integration of impact roller compaction technology into conveyor systems has brought forth a set of advancements in construction and manufacturing sectors. These systems, utilizing the principles of impact roller compaction, are designed to enhance operational efficiencies, minimize conveyor damage, and ensure the smooth handling of materials. This detailed exploration delves into the workings of impact roller compaction conveyors, their crucial role in various industries, and a comparative study with traditional conveyor systems.
How Impact Roller Compaction Conveyors Work
Impact roller compaction conveyors are specialized equipment that incorporates rollers designed to exert compaction forces on materials as they are transported. The core components of these systems include:
- Compaction Rollers: Positioned strategically along the conveyor belt, these rollers apply downward force on the material, compacting it as it moves.
- Belt System: The conveyor belt, designed to withstand the forces applied by the compaction rollers, transports materials efficiently through the compaction process.
- Regulation of Force: The compaction force applied by the rollers can be adjusted based on the material type and desired compaction level, offering flexibility across applications.
Role in Reducing Conveyor Damage and Maintaining Efficiency
Incorporating impact roller compaction in conveyor systems plays a pivotal role in mitigating wear and prolonging the lifespan of the system:
- Even Distribution of Materials: By compacting materials, impact rollers ensure an even distribution across the conveyor, reducing pressure points and minimizing wear.
- Enhanced Material Handling: Compacted materials are less prone to shifting or spillage during transport, leading to smoother operations and reduced maintenance.
- Operational Efficiency: The system’s ability to compact materials on the move eliminates the need for separate compaction processes, streamlining workflows and conserving energy.
Comparison with Traditional Conveyor Systems
When contrasted with conventional conveyor systems, impact roller compaction conveyors offer distinct advantages:
- Material Compaction Capability: Unlike traditional conveyors, these systems can compact materials in transit, enhancing process efficiency and reducing the need for additional equipment.
- Reduced Wear and Tear: The even material distribution and reduced spillage in impact roller compaction conveyors contribute to lower maintenance costs and a longer service life for the conveyor system.
- Versatility and Efficiency: Impact roller compaction conveyors are adaptable to a range of materials and compaction requirements, making them suitable for diverse industrial applications, unlike traditional conveyors which may require different systems for varying tasks.
Operating and Maintenance Tips for Impact Roller Compaction
Effectively utilizing impact roller compaction equipment not only enhances the compaction process but also extends the lifespan of the machinery and ensures the safety of the operators. By adhering to established best practices for operation, committing to regular maintenance routines, and integrating strict safety protocols, operators can significantly contribute to the productivity and longevity of their impact roller compaction machinery. This guide highlights essential tips and considerations to achieve optimal performance.
Best Practices for Operating Impact Roller Compaction
Operating impact roller compaction equipment demands attention to technique as much as it does to the task at hand, with certain practices being pivotal for efficiency:
- Pre-Operation Inspection: Always conduct a thorough check of the compactor before use, ensuring all components are intact, and no signs of wear or damage that could affect operation.
- Optimal Speed and Passes: Adhere to recommended speed settings and number of passes for different soil types to ensure uniform and effective compaction. Over-compaction or under-compaction can compromise soil stability.
- Even Overlaps: Ensure overlaps of roller passes are consistent to avoid uneven compaction, which may lead to instability in the compacted area.
Maintenance Tips to Keep Your Impact Compactor Running Smoothly
Regular maintenance is crucial for the longevity and efficiency of impact roller compaction equipment. Key maintenance activities include:
- Routine Checks: After each use, inspect the roller for any visible signs of wear or damage, especially checking the hydraulic systems and roller surfaces.
- Lubrication: Regularly lubricate moving parts as specified by the manufacturer to prevent friction that can lead to premature wear.
- Cleaning: Ensure the roller and compaction area are cleaned post-operation to prevent material buildup, which can affect performance during subsequent uses.
Safety Considerations to Prevent High Energy Impact Injuries
The powerful nature of impact roller compaction equipment necessitates a stringent approach to safety to prevent accidents and injuries:
- Personal Protective Equipment (PPE): Operators and any personnel within the vicinity of the compaction operation should wear appropriate PPE, including hard hats, safety glasses, and hearing protection.
- Training and Awareness: All operators must receive comprehensive training on the proper use of impact roller compaction equipment and be made aware of potential hazards.
- Safe Operation Zone: Establish and enforce a safe perimeter around the operating area to ensure bystanders and non-essential personnel are at a safe distance from the machinery during operation.
Deciding Between Buy or Rent Impact Roller Compaction Equipment
For those in the construction industry, the decision to buy or rent impact roller compaction equipment is a critical one, with long-term financial and project implications. This is a strategic choice that impacts the course of a project’s trajectory as well as the company’s asset management. Below, we consider the vital factors that should influence this decision and weigh the benefits and drawbacks of each option concerning impact roller compaction equipment.
Factors to Consider for Impact Roller Compaction Choices
Several core considerations must be carefully evaluated to inform the decision on whether to buy or rent impact roller compaction equipment:
- Project Duration and Frequency: Assess the length of your current project and the frequency of future projects requiring a compactor. Purchasing may be justified if use will be regular and long-term.
- Capital and Cash Flow: Consider if the upfront capital expenditure aligns with your financial strategy or if renting is preferable to preserve capital and cash flow.
- Maintenance and Storage: Owning impact roller compaction equipment necessitates maintenance and storage, adding to ownership costs. Evaluate if you have the capabilities to manage these responsibilities.
- Technology and Performance: Buying equipment can be advantageous if using the latest technology and peak performance is crucial for your operations. Renting allows for flexible access to different types of compactors as needed.
- Cost-Benefit Analysis: Perform a cost-benefit analysis that compares the total cost of ownership versus the cost of renting over the lifespan of the equipment or for the duration of the project.
Renting vs. Buying: Pros and Cons for Impact Roller Compaction Equipment
The debate between renting and buying impact roller compaction equipment hinges on a nuanced understanding of each option’s advantages and disadvantages:
Pros of Renting
- Lower Initial Costs: Renting avoids a significant upfront investment, which can be especially beneficial for one-off projects or infrequent compaction needs.
- Maintenance and Upkeep: The rental company typically handles maintenance, repairs, and storage, reducing the burden on the renter.
- Flexibility: Renting allows users to choose specific impact roller compaction equipment for different projects without committing to one model.
Cons of Renting
- Higher Long-Term Cost: For prolonged or frequent use, rental costs can exceed the purchase price over time.
- Availability: Dependence on rental availability can pose a risk to project timelines and productivity.
Pros of Buying
- Asset Ownership: Purchasing impact roller compaction equipment means it’s available whenever it’s needed and can be considered a long-term asset.
- Cost-Efficiency Over Time: For ongoing and multiple projects, owning the equipment can be less expensive in the long haul.
- Resale Value: There is potential for recovering some cost through resale or trade-in on newer models.
Cons of Buying
- Upfront Financial Commitment: Buying equipment requires considerable capital outlay and may entail financing costs.
- Ongoing Expenses: Owners are responsible for all maintenance, repair, and storage costs, compounding the total expenditure.
The choice between buying or renting impact roller compaction equipment should be approached from a strategic perspective, with a thorough assessment of project-specific needs, financial implications, and long-term business goals. Both renting and owning have their respective places within the operational framework of different companies and projects, and the right choice balances cost, utility, and flexibility to align with the broader objectives of the business.
Fill out the form below to get a custom quote for our Impact Roller Compaction.
FAQs about Impact Roller Compaction
Determining the best roller for compaction primarily depends on the type of material being compacted and the specific requirements of the project. The three commonly used rollers include the smooth wheeled roller, suitable for compacting granular materials and pavements; the sheep’s foot roller, ideal for compacting cohesive soils like clay; and the pneumatic tired roller, preferred for compacting asphalt and bituminous materials. For large-scale projects requiring high density, a vibratory roller may be the best choice as it uses vibrations to enhance compaction depth and efficiency. Each roller type has its unique advantages, and the best choice integrates the material properties, project scale, and compaction specifications to achieve the desired compaction level.
The impact method of compaction is a dynamic soil compaction technique that involves dropping a heavy weight from a predetermined height onto the soil surface. This repeated dropping action creates high-intensity compaction waves that densify the soil layers. Often employed for larger construction sites and in preparations for foundations, the impact method is effective in compacting a variety of soil types, especially those that are more resistant to static compaction methods. The key advantage of this method is its ability to achieve deeper and more uniform soil compaction compared to traditional rolling or kneading methods, making it suitable for ensuring the stability and weight capacity of the foundation soil.
The roller compaction method is a process commonly used in construction and roadworks to densify soil, gravel, concrete, or asphalt with the aid of a heavy roller. This method involves the use of static or vibrating rollers to apply direct pressure and vibration to the material, causing the particles to rearrange and pack closer together, resulting in increased density and strength of the ground. Roller compactors come in various types – including smooth drum, sheep’s foot, and pneumatic – each tailored for specific materials and compaction needs. Roller compaction is essential for constructing stable foundations, roadways, and surfaces by ensuring the materials are compacted to desired specifications, preventing settling and providing structural integrity.
Impact rollers and vibratory rollers are both designed to compact materials, but they operate using different mechanisms and are preferred for different applications. Impact rollers create compaction by repeatedly delivering strong vertical forces onto the soil or material, simulating the effects of dropping a heavy weight from a height. This method is particularly useful for deeply compacting soil and is often used in groundwork preparations for large construction projects.
Vibratory rollers, on the other hand, use a combination of weight and high-frequency vibrations to compact materials. The vibrations cause the particles in the soil or asphalt to rearrange and settle closer together, resulting in compaction. Vibratory rollers are highly effective on a variety of materials, including both cohesive soils and granular materials, and are preferred for road construction projects and similar applications where a smooth, dense surface is required. The main difference between the two lies in the mechanism of action—impact for deep compaction through force and vibration for surface compaction through rearrangement of particles.
Last Updated on July 31, 2024 by Jordan Smith
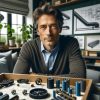
Jordan Smith, a seasoned professional with over 20 years of experience in the conveyor system industry. Jordan’s expertise lies in providing comprehensive solutions for conveyor rollers, belts, and accessories, catering to a wide range of industrial needs. From initial design and configuration to installation and meticulous troubleshooting, Jordan is adept at handling all aspects of conveyor system management. Whether you’re looking to upgrade your production line with efficient conveyor belts, require custom conveyor rollers for specific operations, or need expert advice on selecting the right conveyor accessories for your facility, Jordan is your reliable consultant. For any inquiries or assistance with conveyor system optimization, Jordan is available to share his wealth of knowledge and experience. Feel free to reach out at any time for professional guidance on all matters related to conveyor rollers, belts, and accessories.