Conveyor Impact Roller: Industry’s Backbone
What is a Conveyor Impact Roller?
Conveyor impact rollers are essential components in a material handling system. They provide crucial functionality which we’ll explore in this section.
Definition of a Conveyor Impact Roller
As the name suggests, a conveyor impact roller is a specially designed-component of the conveyor belt. Its primary function is to absorb the impact load of material transferred onto the belt, protecting the belt from potential damage due to the heavy weight of the material. Essentially, it acts as a buffer between the materials being transported and the conveyor belt itself. The quality and durability of a conveyor impact roller significantly influence the longevity and efficiency of a conveyor system in industrial settings.
Importance of a Conveyor Impact Roller
The significance of a conveyor impact roller must be balanced in material handling systems. These rollers play a vital role in ensuring that the impact roller for belt conveyor can withstand the impact of heavy or sharp materials without any severe harm. They help to minimize wear and tear on the belt, thereby reducing the need for frequent maintenance or replacement of the belt. Without the conveyor impact roller, the life of the conveyor belt could be significantly shortened, leading to increased operational costs and possible downtime.
The Role of Conveyor Impact Rollers
Conveyor impact rollers are integral components of conveyor belt systems, efficiently shielding them from significant damage and preventing unnecessary downtime.
Conveyor Impact Roller: Protector of Conveyor Belts
- Role of Conveyor Impact Roller: The primary role of the conveyor impact roller is to safeguard the conveyor belt impact roller from potential damage resulting from heavy loads and impacts during material handling.
- Impact Absorption: The conveyor impact roller absorbs the sudden force when materials of substantial weight or irregular shape are dropped onto the conveyor belt. This preventative mechanism ensures the belt remains undamaged and functions optimally in the long run.
- Material Trajectory: Additionally, the conveyor impact roller is responsible for maintaining the material’s trajectory, ensuring that materials are uniformly distributed on the belt, further reinforcing consequential protection to the conveyor belt.
The Conveyor Impact Roller: Absorbing Forces and Shocks
- Dispersion of Energy: The conveyor impact roller holds a significant role in absorbing and dispersing energy. This dispersion function helps reduce the strain on individual points on the belt, thereby sustaining the integrity of the belt and the system.
- Protective Function: By absorbing short-term immediate impact and reducing long-term degradation, conveyor impact rollers provide a crucial function in preserving the health and longevity of the conveyor belt system.
- Enhancement of Operations: The protective and supportive role of conveyor impact rollers doesn’t just prolong the lifespan of impact roller belt conveyor, but also contributes to their smooth and efficient operation, enhancing the overall productivity of the industrial processes they are part of.
Types of Conveyor Impact Rollers
The effective functionality of conveyor impact rollers in protecting conveyor belts and ensuring smooth operations of material handling systems can significantly correlate with the specific type used. This section provides an overview of the different materials from which these rollers are constructed, as well as the variety of sizes and designs available to meet the specific requirements of different conveyor systems.
Materials Used in Manufacturing Conveyor Impact Rollers
The selection of material to manufacture a conveyor impact roller significantly influences its durability, efficiency, and suitability for a specific application. The most prevalent materials used are:
- Steel Rollers: These are considered robust and resistant to higher impact loads. The steel conveyor impact roller is the go-to for many heavy-duty material handling applications. Not only are they tough and durable, but they also offer good heat resistance and can handle extreme weather conditions.
- Rubber-coated Rollers: For applications that require a more gentle approach or where noise reduction is a significant factor, rubber-coated conveyor impact rollers are best fitted. These cushion the materials being transported, reducing the impact on the conveyor belt, and offering minimal noise during operation.
- Polyurethane Rollers: These conveyor impact rollers stand out in applications where durability, abrasion resistance, and low noise are important. Polyurethane rollers provide exceptional resistance to wear, chemicals, and harsh environmental conditions.
Conveyor Impact Roller Sizes and Custom Design Solutions
When selecting the right conveyor impact roller, considering the variety of sizes and custom designs available is crucial for optimizing the performance and longevity of conveyor systems. Here is a breakdown of key points in a more intuitive dot and bold format:
Variety of Sizes:
- Conveyor impact rollers are available in a range of diameters and lengths to suit various belt widths and material handling capacities.
- The choice depends on factors like material type, conveyor speed, and load capacity. Proper sizing ensures optimal performance and minimizes wear and tear on the belt.
Custom Design Solutions:
- Tailored to Specific Needs: Custom design solutions allow for belt conveyor impact idler roller to be precisely tailored to specific operational requirements, enhancing efficiency and durability.
- Material Compatibility: Ensuring the impact roller conveyor materials are compatible with the materials being conveyed can significantly reduce wear and increase longevity.
- Environmental Considerations: Custom-designed rollers can take into account environmental conditions such as extreme temperatures, moisture, and exposure to chemicals, ensuring optimal performance and durability.
Choosing the correct size and opting for custom-designed conveyor impact rollers can lead to improved conveyor system performance, reduced maintenance costs, and extended equipment life.
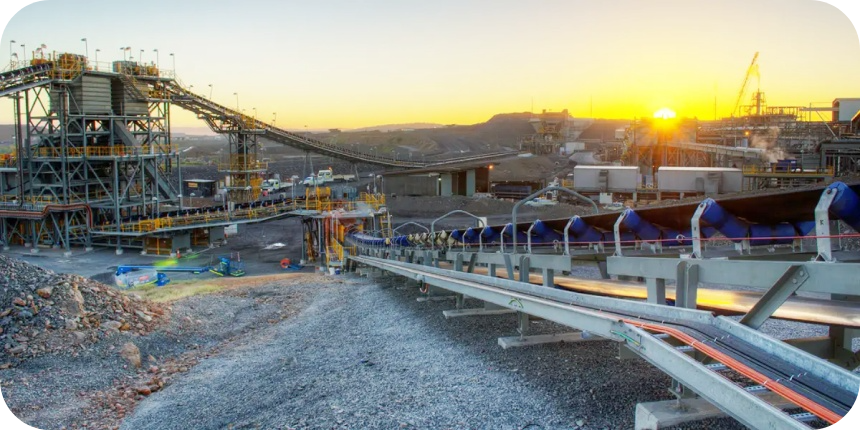
Selection Criteria for Conveyor Impact Rollers
Selecting the appropriate conveyor impact roller is pivotal for the efficiency, safety, and longevity of a conveyor system. Various factors must be considered to ensure the conveyor roller impact meets the specific needs of material handling operations. Below, we delineate these factors in a structured manner, focusing on essential criteria including load capacity, belt speed, material type, and environmental conditions, followed by elucidating the importance of choosing the right size and type of roller for optimal system performance.
Factors to Consider in Impact Roller Selection
The selection of the right conveyor impact roller is guided by several critical factors, each playing a unique role in the conveyor system’s overall functionality and durability. Herein, we present these factors in the form of a table for a comprehensive and quick reference:
Factor | Description |
---|---|
Load Capacity | The maximum weight the conveyor impact roller can support. Chosen based on the weight of materials to be handled. |
Belt Speed | The speed at which the conveyor belt operates. The roller must be capable of handling the dynamics of varying speeds. |
Material Type | The type of materials being transported affects choice—consider abrasion resistance, chemical compatibility, and impact resistance. |
Environmental Conditions | Factors such as temperature, humidity, and exposure to chemicals or corrosives dictate the material and design of the impact roller. |
Importance of the Right Size and Type
The optimal performance and longevity of the conveyor system significantly depend on selecting the right size and type of conveyor impact roller. This selection critically influences its effectiveness and operational efficiency:
- Customization for Efficiency: Custom sizing and type ensure compatibility with specific operation demands, including belt width, load capacity, and operational speed, leading to enhanced efficiency.
- Minimization of Wear and Tear: Adequately sized and appropriately selected conveyor impact rollers can significantly reduce wear and tear on both the belt and rollers, extending their service life.
- Optimization of Material Handling: The right size and type of roller ensure that materials are transported smoothly, reducing spillage and improving material handling efficiency.
Careful consideration of these selection criteria is essential for engineering a conveyor system that is not only efficient but also durable and reliable. By prioritizing the right specifications for the impact conveyor roller, operations can achieve higher productivity and lower maintenance costs, ensuring a robust return on investment.
Conveyor Impact Roller Maintenance and Replacement
The longevity and performance of conveyor systems heavily rely on the regular maintenance and timely replacement of conveyor impact rollers. Proper attention to the state of your conveyor impact rollers can prevent costly downtime and maintain efficiency in your material handling operations. Detailed below are proactive tips on maintaining these components, indicators for when they need to be replaced, and guidelines for executing replacements safely and effectively.
Maintenance Tips for Prolonging Roller Life
Keeping your conveyor impact rollers in peak condition involves a regular maintenance routine. The following points offer actionable tips for maintenance:
- Regular Cleaning: Frequent cleaning to remove debris, dust, and accumulated material which can cause wear and tear.
- Lubrication: Ensuring proper lubrication of the rollers to minimize friction and prevent seizing which might lead to premature failure.
- Inspection Schedule: Implement a routine inspection schedule to check for signs of wear, alignment issues, or damage to the conveyor impact roller.
- Operational Load Monitoring: Consistently monitor the load being carried by the system and adjust if it exceeds the rated capacity of the rollers to avoid overburdening.
Signs Indicating the Need for Roller Replacement
Recognizing when a conveyor impact roller has reached the end of its service life is key to maintaining your conveyor system’s integrity:
- Visible Damage: Dents, cracks, or other visible signs of damage on the conveyor impact roller surface could indicate the need for replacement.
- Abnormal Noise: Excessive or abnormal noise such as squeaking or grinding when the rollers are in motion could signal worn-out bearings or misalignment.
- Rotation Issues: Rollers that appear to have difficulty rotating or do not rotate at all need attention and possibly replacement.
- Wear Patterns: Uneven wear patterns suggest misalignment or uneven load distribution and can necessitate the replacement of the impacted rollers.
Safe and Efficient Replacement of Impact Rollers
When the replacement of a conveyor impact roller is deemed necessary, the process should be carried out with a focus on safety and efficiency:
- Power Down: Ensure the conveyor system is properly locked out and tagged out before beginning any replacement work.
- Proper Tools and Equipment: Use the correct tools and equipment recommended by the roller manufacturer for the replacement procedure.
- Replacement Protocol: Follow a set protocol for removal of the old roller and installation of the new one, which includes proper alignment and tensioning of the belt.
- Post-Replacement Inspection: Conduct a thorough inspection once the new conveyor impact roller is installed to confirm it is secured, aligned, and functioning correctly.
Following these guidelines for maintenance, recognizing the signs of necessary replacement, and safely conducting the replacement of conveyor impact rollers can significantly reduce unplanned downtime and contribute to a more productive and cost-efficient operation.
Advancements in Conveyor Impact Roller Design
The domain of materials handling has seen significant strides in technology, particularly in the development of the conveyor impact roller. These advancements not only improve the functional capabilities of conveyor systems but also aim to introduce efficiencies that can lead to cost savings over time. Below, we delve into some of the latest insights in conveyor impact roller innovations such as energy-saving features and self-correction mechanisms, and discuss how these enhancements contribute to improved overall performance and maintenance reductions.
Innovations in Impact Roller Technology
Recent technological developments have revolutionized conveyor impact roller design, making them more sophisticated than ever before:
- Energy-Efficient Designs: Advancements such as precision bearings and optimized roller shapes have reduced rolling resistance, thus conserving energy. New materials and coatings are also being used to decrease friction.
- Self-Aligning Features: Engineers have introduced intelligent self-aligning conveyor impact rollers that help correct belt misalignment issues automatically, preventing belts from drifting off-course and reducing the risk of damage and downtime.
- Advanced Material Composition: The creation of new composite materials has resulted in lighter, stronger, and more wear-resistant rollers that require less power to operate and have a longer lifespan.
- Integrated Sensors: Incorporation of smart technology with sensors that monitor the conveyor impact roller performance, predict maintenance needs, and alert operators to potential issues before they escalate.
These cutting-edge developments in conveyor impact roller technology mark a turning point in conveyor system management, promising not just enhanced longevity but also unprecedented levels of operational intelligence.
Contribution to Enhanced Performance and Cost Reduction
The aforestated enhancements to the conveyor impact roller design are instrumental in both elevating system performance and driving down maintenance-related expenditures:
- Reduced Energy Consumption: Impact rollers with energy-efficient designs need less power to operate, which translates to reduced energy bills and a smaller carbon footprint for the operation.
- Extended Equipment Lifespan: The improved durability of advanced-material rollers means replacements are needed less frequently, thereby saving on both the parts themselves and the associated labor costs.
- Decreased Downtime: The self-aligning technology and real-time monitoring mitigate operational disruptions by pre-empting alignment issues and identifying maintenance needs early, thus minimizing unscheduled downtime.
- Improved Material Handling: Advanced rollers provide more consistent and reliable operation, ensuring materials are transported without spillage or damage, leading to reduced material waste and better product quality.
The modern advancements in conveyor impact roller design are demonstrably beneficial to the functionality and fiscal health of conveyor systems, granting operators a higher degree of control and optimization of their operations. With ongoing research and innovation in this space, the future promises even greater efficiencies and operational enhancements.
Conveyor Impact Roller Suppliers and Availability
In the realm of materials handling and conveyor systems, the conveyor impact roller plays a crucial role in maintaining the efficiency and longevity of the conveyor belts. This guide details the landscape of suppliers and manufacturers of conveyor impact rollers, illuminates the process of finding and purchasing these essential components, and underscores the significance of expert guidance in selecting the optimal roller for specific system requirements.
Identifying Quality Suppliers and Manufacturers
When in search of a conveyor impact roller, the market presents a plethora of suppliers and manufacturers. However, focusing on quality and reliability is paramount in choosing the right provider:
- Reputation and Reviews: Look for suppliers with a strong reputation in the industry, supported by positive reviews from past customers.
- Product Range: Select manufacturers that offer a wide product range, which indicates their capability to cater to diverse needs and custom requirements.
- Quality Certifications: Prioritize suppliers with recognized quality certifications like ISO, which assure compliance with high manufacturing standards.
- After-sales Support: Consider the level of after-sales support offered, as this is crucial for maintenance and any potential need for replacements.
By concentrating on these factors, businesses can effectively narrow down their list of potential suppliers and manufacturers, ensuring a more informed decision-making process regarding where to source conveyor impact rollers.
Procuring Impact Rollers: New vs. Used Options
New Conveyor Impact Rollers | Used Conveyor Impact Rollers | |
---|---|---|
Quality | Brand new, top condition, latest technology | Condition varies, quality check necessary, may lack the latest features |
Performance | Guaranteed to perform optimally | Performance may vary based on usage |
Cost | Higher initial investment | More cost-effective, budget-friendly choice |
Availability | Readily available from the manufacturer | Depends on availability in the used equipment market |
Warranty | Comes with manufacturer warranty | May lack warranty |
Suitability | Ideal for operations demanding reliability and high efficiency | Suitable for less intensive operations or those with tight budgets |
Environment Impact | Manufacturing new rollers consumes resources | Buying used is more environmentally friendly as it promotes reuse and recycling |
This table gives a side-by-side comparison that illustrates the key differences and factors to consider when deciding between new and used conveyor impact rollers.
The Importance of Expert Consultation
Before finalizing a purchase, consulting with industry experts can be instrumental in selecting the best conveyor impact roller for a specific system. This step ensures that:
- System Compatibility: The chosen rollers are compatible with the system’s design and operational parameters.
- Performance Optimization: Experts can recommend rollers that optimize performance, based on the conveyor system’s speed, load capacity, and material type.
- Cost-Efficiency: Guidance from experienced professionals can lead to more cost-effective choices, striking the right balance between initial investment and long-term benefits.
Engaging with experts who possess in-depth knowledge of conveyor systems and components can lead to more informed purchasing decisions, maximizing the efficiency and productivity of the conveyor system with suitably chosen conveyor impact rollers.
Navigating the supplier landscape, considering new versus used options, and leveraging expert advice are all strategic steps in procuring the right conveyor impact rollers. These considerations ensure that businesses can maintain optimal conveyor system performance while addressing both budgetary constraints and operational needs.
Conveyor Impact Roller Cost Considerations
When planning to upgrade or set up a conveyor system, understanding the cost implications of conveyor impact rollers is crucial. The price of these components can significantly affect the overall budget of your conveyor system. This section elaborates on the various factors that influence the cost of conveyor impact rollers and guides balancing cost with the essential attributes of quality and performance.
Factors Affecting Conveyor Impact Roller Price
Several aspects contribute to the cost of conveyor impact rollers, making some options more expensive than others:
- Material: The choice of material (e.g., steel, plastic, or rubber) plays a significant role in determining the price. High-strength alloys and specialized coatings that offer superior durability and wear resistance tend to increase the cost.
- Size: Larger rollers or those with unique dimensions tailored for specific applications can also add to the expense due to the increased material usage and the complexity of manufacturing.
- Technology Features: Rollers equipped with advanced features like energy-efficient designs, integrated sensors for monitoring, or self-aligning capabilities command a higher price. These technologies offer long-term savings and improved performance but require a larger initial investment.
By assessing these factors, businesses can understand the variances in conveyor impact roller pricing and make informed purchasing decisions based on their specific operational needs and budget.
Balancing Cost with Quality and Performance
Investing in conveyor impact rollers requires a careful balance between initial costs and the long-term benefits of quality and performance. Consider the following tips to achieve this balance:
- Assess Total Cost of Ownership (TCO): Look beyond the purchase price to consider the lifetime cost of the rollers, including maintenance, energy usage, and potential downtime. Cheaper upfront options may not always be cost-effective in the long run.
- Prioritize Critical Features: Determine which features are essential for your operation and willing to invest in. This might include durability for heavy-duty applications or energy efficiency for long-running operations.
- Seek Expert Advice: Consult with suppliers or industry experts to understand the best options for your specific needs. They can provide valuable insights into how different conveyor impact roller types will perform in your operational environment.
By meticulously evaluating these considerations, businesses can optimize their investment in conveyor impact rollers, ensuring that they select options that provide the best balance of cost, quality, and performance to meet their operational requirements.
Implementing the Right Conveyor Impact Rollers
The integration of conveyor impact rollers into an existing conveyor system is a strategic step toward enhancing the performance and efficiency of material handling operations. This section delves into practical advice for the successful implementation of conveyor impact rollers and highlights the importance of aligning this process with the total system requirements and operational goals.
Advice on Integrating Conveyor Impact Rollers
Successfully incorporating conveyor impact rollers into an existing system requires careful planning and consideration of the following aspects:
- System Assessment: Conduct a thorough assessment of your current conveyor system to identify areas where impact rollers can provide the most benefit, such as in transfer points where materials are dropped onto the conveyor belt. Understanding these zones helps in determining the specific type and specifications of impact rollers needed.
- Customization for System Compatibility: Ensure that the chosen conveyor impact rollers are compatible with the dimensions, belt type, and operational speed of your existing setup. In some cases, custom-sized rollers may be necessary to achieve the best fit and performance.
- Professional Installation: Engage with professional technicians for the installation process to ensure that the conveyor impact rollers are correctly positioned and securely fitted. Proper installation is critical to prevent any operational issues and to maximize the benefits of the rollers.
- Test and Adjust: After installation, run tests under normal operating conditions to verify that the conveyor impact rollers are functioning as expected.
Adjustments may be required to fine-tune their performance to the specific demands of your system.
Focusing on these key areas ensures the successful integration of conveyor impact rollers, ultimately leading to improved material handling efficiency and reduced wear on the conveyor belt.
Total System Requirements and Operational Goals
Before implementing conveyor impact rollers, consider the broader implications for your entire conveyor system and how these components align with your operational objectives:
- System Efficiency: Evaluate how conveyor impact rollers will contribute to overall system efficiency. For example, the right rollers can reduce belt wear and energy consumption by minimizing the impact force of falling materials.
- Operational Reliability: Consider the impact of new rollers on the reliability of your conveyor system. High-quality conveyor impact rollers can increase uptime and reduce the need for frequent maintenance.
- Long-Term Performance Goals: Align the choice of conveyor impact rollers with your long-term performance and productivity goals. Rollers that offer enhanced durability and performance under your specific operational conditions can provide a better return on investment by extending the service life of your conveyor system.
- Compliance and Safety: Ensure that the chosen rollers comply with industry standards and contribute to a safer working environment. Implementing the right conveyor impact rollers can help reduce the risk of system failures and accidents caused by material spillage or belt misalignment.
By giving careful thought to these considerations, businesses can make informed decisions about the implementation of conveyor impact rollers, ensuring that they complement the total system requirements and contribute positively towards achieving operational goals.
CONTACT US
Let us help you find a better solution!
FAQs about Conveyor Impact Roller
Which roller is used to apply or remove tension on the belt?
Tensioning Rollers or Take-Up Rollers are used to apply or remove tension on the conveyor belt. They are adjustable rollers that help maintain the correct tension in the belt, which is crucial for smooth operation and to prevent belt slippage.
What is the impact idler in a belt conveyor?
An Impact Idler is a type of idler roller specifically designed to absorb the shock and impact of materials falling onto the conveyor belt. These idlers often feature a special design, such as cushioning or impact-resistant materials, to protect the belt and extend the lifespan of both the belt and the conveyor system.
What is the purpose of a roller on a belt buckle?
Rollers on a belt buckle are typically used to facilitate smooth and easy adjustment of the belt. They help reduce friction and make it easier to slide the belt through the buckle, allowing for more precise and comfortable fit adjustments.
How do conveyor rollers work?
Conveyor rollers work by providing a surface on which the conveyor belt can move. They support the weight of the material being transported and help the belt travel smoothly. Rollers can be driven (powered by motors) or idle (not driven). The rollers reduce friction between the belt and the conveyor frame, ensuring efficient material handling and movement.
ls a roller on a conveyor belt a pinch point?
Yes, rollers on a conveyor belt can be considered pinch points. They pose a risk of injury if body parts or clothing get caught between the rollers. Proper safety measures, such as guards and emergency stop mechanisms, should be implemented to minimize the risk of injury.
Why are conveyor belts fitted with multiple rollers?
Conveyor belts are fitted with multiple rollers for several reasons:
Support: Multiple rollers distribute the load evenly across the belt, preventing sagging and ensuring proper support.
Reduce Friction: Rollers reduce the friction between the belt and the conveyor structure, allowing for smoother movement and reducing the wear on the belt.
Alignment: Rollers help maintain proper belt alignment, preventing drifting and misalignment.
Load Handling: For heavy loads, multiple rollers provide additional support to prevent damage to the belt and extend the conveyor’s lifespan.
Which roller is used to track a conveyor belt?
Tracking Rollers or Guide Rollers are used to track a conveyor belt. They ensure the belt remains centered and aligned during operation, preventing it from drifting off the sides of the conveyor.
What is a snub roller on a conveyor?
A Snub Roller is used to increase the contact area between the conveyor belt and the drive pulley, improving the grip and driving efficiency. It helps to change the direction of the belt and increase belt tension around the drive pulley.
What are the three types of rollers?
Gravity Rollers: Operate using gravity to move items on inclined or horizontal conveyors.
Powered Rollers: Driven by motors to move items, suitable for both horizontal and inclined conveyors.
Chain-Driven Rollers: Utilize chains to drive the rollers, often used for heavy-duty applications.
Why use conveyor rollers?
Support and Guidance: Rollers support and guide the conveyor belt, facilitating smooth material handling.
Reduce Friction: Rollers reduce friction between the belt and the conveyor frame, leading to more efficient movement.
Distribute Load: They distribute the load evenly across the belt to prevent sagging and damage.
Enhance Belt Life: By minimizing wear and tear on the belt, rollers help extend its lifespan.
What are the parts on a conveyor?
Belt: The continuous loop that carries materials.
Rollers: Support and guide the belt, including idler rollers, drive rollers, and return rollers.
Pulleys: Include drive pulleys and tail pulleys that help in moving the belt.
Frame: The structural support of the conveyor system.
Drive Motor: Powers the conveyor belt.
Idlers: Support the belt and are positioned along the conveyor’s length.
Take-Up Devices: Adjust the tension of the belt.
Conveyor Belt: The moving surface that transports materials.
What is a return roller?
Return Rollers are a type of idler roller that supports the conveyor belt on the return side (the underside of the conveyor). They help in guiding and supporting the belt as it returns to the start of the conveyor system.
What are guide rollers for conveyor belts?
Guide Rollers are used to keep the conveyor belt aligned and prevent it from drifting off-center. They are positioned along the edges of the conveyor belt and help ensure that the belt runs straight and true throughout the conveyor system.
What are the limitations of roller conveyors?
Limited Incline Capability: Roller conveyors are not suitable for steep inclines.
Heavy or Abrasive Materials: Can cause wear and tear on the rollers if not designed for heavy or abrasive materials.
Maintenance: Requires regular maintenance to ensure smooth operation and prevent issues like misalignment or roller failure.
Noise: Can be noisy, especially with metal rollers.
Why use a roller conveyor?
Efficiency: Facilitates efficient and smooth movement of goods along the conveyor system.
Versatility: Can handle a variety of load sizes and types, from small packages to heavy items.
Low Maintenance: Generally requires less maintenance compared to other conveyor types.
Cost-Effective: Simple design often results in a lower initial cost and operational expenses.
What is the lifespan of a conveyor roller?
The lifespan of a conveyor roller varies depending on factors like load, usage conditions, and maintenance. Typically, rollers can last from 5 to 10 years, but this can vary significantly based on application and environment.
Where are conveyor rollers used?
In heavy industries such as mining, conveyor rollers are crucial for efficient material handling. They are used extensively in conveyor systems to transport bulk materials like ores, coal, and aggregates across various stages of processing. Conveyor rollers support the conveyor belt and facilitate the smooth movement of heavy loads, reducing friction and wear on the system. In mining operations, rollers are designed to withstand harsh conditions, including high impact, abrasive materials, and extreme temperatures. They are also employed in stackers, reclaimers, and other bulk handling equipment to ensure continuous and reliable operation. The durability and efficiency of conveyor rollers contribute significantly to optimizing production processes and minimizing downtime in these demanding industrial environments.
What is the difference between powered and unpowered roller conveyors?
Powered Roller Conveyors: Utilize motors to drive the rollers, moving items automatically. Suitable for applications requiring consistent and controlled movement.
Unpowered Roller Conveyors (Gravity Conveyors): Rely on gravity or manual force to move items. Generally simpler and less expensive, but require inclines or manual pushing.
How do powered rollers work?
Powered Rollers are driven by electric motors through a system of gears, belts, or chains. The motors turn the rollers, which then move the conveyor belt or items placed on the conveyor. This system allows for controlled and automated material handling.
How heavy is a conveyor roller?
The weight of a conveyor roller varies based on its size, material, and design. Typical roller weights range from a few pounds (for small, lightweight rollers) to several hundred pounds (for heavy-duty rollers).
What is the spacing for roller conveyor rollers?
Roller spacing typically ranges from 3 to 6 inches (75 to 150 mm) depending on the load requirements and type of material being transported. Closer spacing is used for lighter loads, while wider spacing is used for heavier items to provide additional support.
What is the main purpose of a roller?
The main purpose of a roller is to support and guide the conveyor belt, facilitate smooth material handling, and reduce friction between the belt and the conveyor frame. Rollers help in maintaining the belt’s alignment, distributing the load evenly, and ensuring efficient operation of the conveyor system.
What is impact roll?
An Impact Roll refers to a roller designed to handle high-impact forces, such as those experienced in loading zones or areas where materials drop onto the conveyor belt. It helps absorb and cushion the impact, protecting the conveyor belt and system.
Why are rollers used?
Rollers are used to:
Support and guide the conveyor belt.
Reduce friction between the belt and the conveyor frame.
Distribute the load evenly to prevent sagging.
Facilitate smooth and efficient material handling.
Protect the conveyor belt and system from excessive wear and damage.
What is the impact roller on a belt conveyor?
An Impact Roller on a belt conveyor is designed to absorb and mitigate the impact of materials falling onto the conveyor belt, especially in loading and unloading areas. It helps reduce the stress and damage to the belt and other conveyor components.
What is an idle roller?
An Idle Roller (or Idler Roller) is a non-powered roller that supports and guides the conveyor belt, helping to maintain its alignment and support the return side of the belt. It does not drive the belt but helps in reducing friction and wear.
What is the advantage of roller support?
The advantages of roller support include:
Load Distribution: Rollers help evenly distribute the load across the conveyor system, preventing belt sagging and excessive wear.
Reduced Friction: By providing a smooth surface for the belt to move over, rollers reduce friction, improving efficiency and extending the lifespan of the conveyor belt.
Enhanced Alignment: Rollers help maintain proper belt alignment, preventing drifting and ensuring smooth operation.
Improved Efficiency: Facilitates easier movement of materials and reduces the amount of manual effort required to move items.