Impact Roller Replacement: Best Practices for Reducing Downtime
Impact roller replacement is a critical maintenance procedure within conveyor systems, particularly vital in industrial and manufacturing environments where the smooth operation of the conveyor belt is essential. Essentially, impact rollers, also known as buffer rollers, play a pivotal role in absorbing the forces exerted on the conveyor belt, especially in the loading zone where materials are dropped onto the belt. This absorption capacity helps in reducing the wear and tear on the conveyor belt itself, extending its service life and ensuring efficient operation. The replacement of these rollers is not just about maintaining the integrity of the conveyor system but is also a preventive measure against potential breakdowns that could interrupt production lines. Understanding when and how to replace these impact rollers is key to maximizing the lifespan and efficiency of conveyor systems.
Impact Roller Replacement Cost
The cost of impact roller replacement can be influenced by a myriad of factors that are crucial for businesses to consider for both budgeting and operational planning. To simplify the complex pricing landscape, the following table categorizes these factors:
Incorporating high-quality rollers can seem expensive initially, but it is worth considering the long-term savings that can be achieved through investment in superior impact roller replacement options. High-quality impact rollers may reduce the frequency of replacements needed over time due to their enhanced wear resistance and improved durability. This saving on resources extends to less downtime due to maintenance and potentially lower labor costs over the lifespan of the conveyor system. Investing wisely in quality impact conveyor roller replacement is not merely a purchase—it’s an investment in continuous operational efficiency and sustainability.
Heavy Duty Impact Roller Replacement
In the world of industrial applications, heavy-duty impact roller replacement plays a significant role in maintaining the optimal operation of conveyor systems. Heavy-duty impact rollers are typically designed to absorb high levels of impact force and resist severe wear and tear, making them ideally suitable for environments where harsh load conditions or larger and heavier materials are a norm.
A conveyor system may require heavy-duty impact roller replacement for various reasons:
- Highly Abrasive Materials: Standard rollers may not withstand the continuous impact and abrasion from hard, sharp, or heavy materials. Therefore, strong and heavy-duty rollers become a necessity.
- Large Material Volume: A conveyor system handling large volumes of material routinely needs heavy-duty impact rollers to mitigate excess strain on the conveyor belt and other system components.
- Longer Operational Hours: Conveyor systems running for extended periods significantly benefit from heavy-duty rollers due to their enhanced longevity and fewer replacement needs.
- Harsh Environmental Conditions: Heavy-duty rollers possess robust construction, making them better suited to handle exposure to aggressive weather conditions, heavy dust, or corrosive elements.
Heavy-duty impact roller replacement offers invaluable benefits by enhancing performance in demanding environments, reducing maintenance time, extending conveyor system life, and ultimately leading to cost savings and increased productivity.
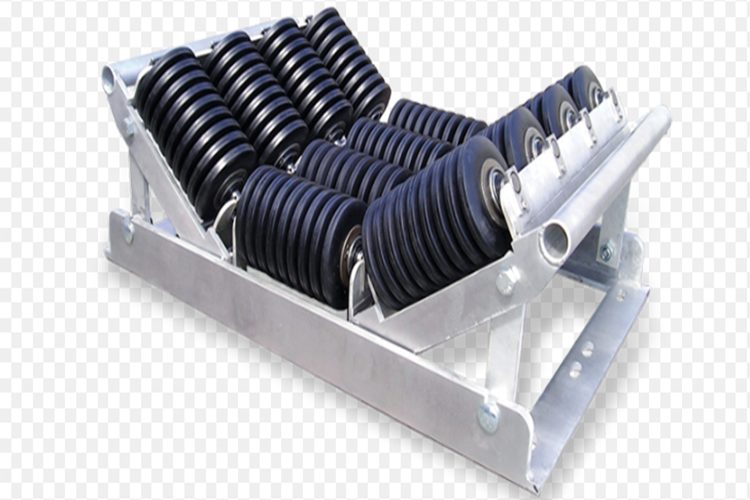
Step-by-Step Guide to Impact Roller Replacement
Impact roller replacement is a critical task that ensures the longevity and efficiency of conveyor systems. The following detailed steps outline how to safely and effectively replace a buffer (also known as impact) roller while also providing tips for choosing the right replacement for your system.
- Safety First: Before beginning any replacement work, ensure all machinery is powered off and locked out to prevent accidental activation. Wear appropriate personal protective equipment (PPE) such as gloves and safety glasses.
- Inspect and Identify: Carefully inspect the existing impact rollers to identify any signs of wear, damage, or malfunction. This will help you understand the extent of replacement needed.
- Measurement and Specification Confirmation: Measure the existing roller for diameter, length, and shaft size. Also, note the type (buffer/impact), material, and any specific features. Ensure the replacement roller matches these specifications to maintain system efficiency and safety.
- Removal of the Old Roller: Loosen and remove the fasteners or brackets holding the roller in place. Carefully slide out the old roller from the frame. This might require slight lifting or maneuvering of the conveyor belt.
- Installation of the New Roller: Slide the new impact roller into position, making sure it fits securely within the frame. Re-align the conveyor belt over the new roller, ensuring it sits evenly.
- Fastening and Securing: Re-attach any fasteners or brackets that hold the roller in its position. Double-check to ensure everything is tight and secure to prevent any unexpected shifts during operation.
- Functional Test: Once installed, conduct a manual test by rotating the roller to ensure it moves freely without resistance or obstruction. Follow with a live test by powering on the conveyor system and observing the replacement roller in action, ensuring smooth operation.
- Maintenance Record Update: Record the replacement in your maintenance log, noting the date of replacement and any observations. This helps in tracking performance and planning future preventive maintenance.
Tips for Choosing the Right Replacement Roller
- Match Specifications Precisely: Ensure the replacement roller matches the original specifications in terms of size, material, and type to maintain performance and safety standards.
- Quality Matters: Opt for high-quality materials that offer better durability and longevity, especially for heavy-duty applications.
- Consider Operational Conditions: Ensure the replacement roller is suitable for the environmental and operational conditions of your system. For instance, rollers used in wet or corrosive environments may require materials resistant to rust and corrosion.
- Vendor Research: Source replacement rollers from reputable vendors with positive reviews and reliable customer service to ensure you receive a product that meets industrial standards.
Following this comprehensive guide and tips will ensure the effective and safe replacement of impact rollers, thereby maintaining the operational efficiency of your conveyor system.
Reuse and Maintenance: Can You Reuse Your Impact Roller Replacement?
When it comes to impact roller replacement, an important consideration is whether the roller cover itself can be reused and under what conditions. Proper maintenance is crucial for prolonging the lifespan of roller covers, and in certain scenarios, reusing them can be both economically and environmentally beneficial.
Exploring Possibilities and Suggestions for Reusing Roller Covers:
- Assessment: The first step in determining if a roller cover can be reused is a thorough inspection. Look for signs of wear such as tears, deformation, or excessive wear patterns. A roller cover with minor wear and no structural damage could potentially be reused.
- Cleaning: Before reusing, the roller cover should be carefully cleaned to remove any debris, dust, or residual material that could affect its performance. Use appropriate cleaning agents that do not degrade the material of the cover.
- Repair: Minor damages like small tears or cuts can sometimes be repaired, depending on the material of the cover. Specialized repair kits are available for some types of roller covers. However, ensure that the repair can withstand the operational conditions of the roller.
- Performance Testing: Reconditioned or repaired roller covers should undergo performance testing to ensure they can still effectively absorb impact and function as intended. This might include weight or durability tests as per manufacturer guidelines.
Conditions Under Which the Roller Cover Can Be Reused:
- Material Integrity: The material of the roller cover must not have degraded to a point where it can no longer perform its function. Materials that have become brittle, overly soft, or exhibit extensive wear must be replaced.
- Operational Compatibility: The roller cover must still be suited for the specific operation. For example, if the material processed has changed or if there’s been an upgrade in the system, the old roller cover might no longer be appropriate.
- Safety Compliance: Any reused roller cover must still meet all safety standards. It should not introduce any risk of failure that could lead to operational hazards.
Maintaining Roller Covers for Potential Reuse:
- Regular Inspection: Schedule regular inspections of roller covers for early detection of wear and damage.
- Proper Cleaning: Develop a routine for cleaning roller covers, ensuring that accumulated materials do not cause premature wear.
- Rotation: If feasible, rotate roller covers within the system to ensure even wear patterns, which can extend their usability.
- Storage: When not in use, store roller covers in a cool, dry place away from direct sunlight or chemicals that might degrade the materials.
Considering these suggestions and maintaining roller covers diligently can optimize their lifecycle and potentially offer significant cost savings through reuse. However, the decision to reuse should always be balanced with operational efficiency and safety considerations.
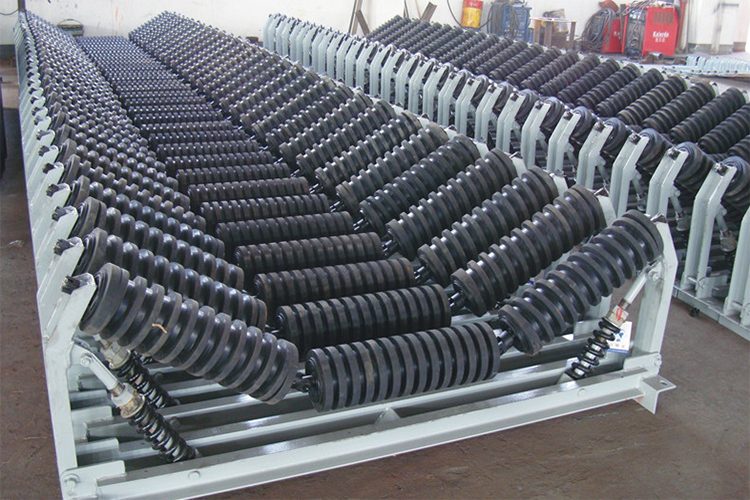
Roller Rocker and Its Adjustment in Impact Roller Replacement
In the context of impact roller replacement, understanding the role of roller rockers and their adjustment is crucial for ensuring the optimal performance and longevity of the machinery. Roller rockers are mechanical components that play a fundamental role in the function of various types of machinery, including engines and conveyor systems. Their primary purpose is to transfer motion, typically from a camshaft or similar mechanism, to another part like a valve or, in the case of conveyor systems, to assist in the effective transfer and absorption of impact forces.
Understand the Role of Roller Rockers in Machinery:
Roller rockers are designed to pivot on a shaft or fulcrum, acting as a lever to transfer force. In engine applications, they help in opening and closing valves by converting the camshaft’s rotational motion into linear motion. For conveying systems, especially in units dealing with significant impact forces, roller rockers can contribute to distributing and mitigating stress along the conveyor’s length. This aids in reducing wear and tear on the impact rollers, ensuring that they can effectively absorb shocks without degrading quickly.
Discuss Whether and Under What Circumstances the Roller Rocker Needs Adjustment:
- Wear and Tear: Over time, roller rockers can experience wear, particularly at pivot points and where they make contact with other components. This wear can affect their efficiency in transferring motion or forces, necessitating adjustment or replacement.
- Operational Efficiency: Any signs of inefficiency in the machinery’s operation, such as unusual noises, vibrations, or a decrease in performance, might indicate that the roller rocker system needs inspection and possible adjustment. For impact roller systems, this might mean the force is not being effectively transferred or absorbed.
- After Replacement of Related Components: Whenever impact rollers or adjacent machinery parts are replaced, it’s prudent to check and adjust the roller rockers if necessary. The new components may have different specifications or wear characteristics, requiring fine-tuning of the roller rockers for optimal interaction.
- Regular Maintenance: Even in the absence of obvious wear or performance issues, routine maintenance schedules should include checking and adjusting roller rockers as a preventative measure. This ensures they are always operating within desired parameters, reducing the likelihood of sudden failures.
Adjustment Procedure:
The adjustment process for roller rockers will vary significantly depending on the specific machinery they are used in. Generally, it involves:
- Loosening Adjustment Locknuts: Typically, roller rockers are adjusted by loosening locknuts that hold them in their operational positions.
- Adjusting Position or Tension: Depending on the design, the rocker may need repositioning or adjustment of tension to ensure correct operation. This may involve turning an adjustment screw or physically repositioning the rocker.
- Retightening Locknuts: Once adjusted, the locknuts are securely tightened to hold the rocker in its new position.
- Verification: Post-adjustment, the machinery should be tested (where possible, under load conditions) to verify that the adjustments have had the desired effect and that the system operates smoothly.
What is and appropriately adjusting roller rockers in the context of impact roller replacement is essential for maintaining the mechanical integrity and performance of the machinery in which they are utilized. Regular attention to these components can significantly extend the service life of the machinery and ensure it operates at peak efficiency.
Roller Rocker with Roller Cam: Compatibility and Requirements in Impact Roller Replacement
In the realm of impact roller replacement, the interplay between the roller rocker and the roller cam is a significant consideration, given its crucial role in machinery operation. Essentially, the roller rocker and the roller cam work together to convert rotational movement into linear movement, which is fundamental to the operation of many mechanical systems.
Check if Roller Rocker is Required When Using a Roller Cam:
When using a roller cam in a conveyor system or other machinery, a roller rocker’s compatibility and necessity are determined by a number of factors such as the functionality of the system, its design, and the operational environment. The advantage of using roller rockers in tandem with roller cams primarily lies in their ability to reduce friction and increase efficiency.
- System Design and Application: If the system’s design uses roller cams to drive movement and the application entails absorbing substantial impact forces, using a roller rocker in conjunction with the roller cam may be beneficial, facilitating smoother force transfer and reducing potential wear of the impact rollers, thereby prolonging their lifecycle.
- Friction Reduction: Roller rockers significantly reduce friction compared to their non-rolling counterparts, which can increase the life of the cam while also improving overall system efficiency. If friction is a concern in the current operation, a roller rocker becomes a key component.
Technical Insights on Performance and Wear Considerations:
When integrating roller rockers with roller cams in the context of impact roller replacement, the system’s performance and wear considerations are of prime importance. A well-designed and integrated system should ensure increased performance and minimized wear on both the roller cam and the impact rollers over time.
- Performance: With reduced friction between interacting parts, the combination of roller rockers and roller cams allows for smoother operation and potentially higher speeds, enhancing the system performance. They can also more effectively manage high-pressure conditions, boosting machinery resilience and durability without compromising on operational efficiency.
- Wear Considerations: The use of roller rockers reduces the sliding motion that traditionally occurs in mechanized systems, transforming it into a rolling action. This significantly diminishes surface wear on both the cam and the rocker, resulting in extended component longevity. However, it’s important to bear in mind the need for regular maintenance, including lubrication and inspection for all rolling components, to ensure they continue to function as intended.
As with all components in a mechanized system, the decision to use roller rockers with roller cams during impact roller replacement comes down to the specific application’s unique needs and demands. By thoroughly analyzing the operational context and potential benefits, one can make an educated decision about their incorporation, ensuring optimal operation and longevity of the overall system.
FAQs about Impact Roller Replacement
The standard size of an idler roller can vary widely depending on the conveyor system’s design and the purpose it serves. In general, the size of an idler roller is determined by the belt width it supports. For example, in industries following the Conveyor Equipment Manufacturers Association (CEMA) standards, idlers for belt conveyors can range from CEMA B, which supports belts less than 24 inches wide, to CEMA F, for belts over 60 inches. The diameters of idler rolls can also vary, with common sizes including 4, 5, 6, and 7 inches, while face widths match or exceed the belt width by a few inches to ensure full support.
The terms “roller” and “idler” are often used interchangeably in the context of conveyor systems, but they can denote slightly different components. A roller typically refers to the cylindrical part that rotates around an axis and can be a part of various machines or systems. An idler, meanwhile, is a specific kind of roller that is used in conveyor systems to support the conveyor belt and its load. Idlers do not drive or provide traction; they primarily provide a surface for the conveyor belt to slide over or rotate around to maintain tension and guide the belt efficiently on its path.
Conveyor rollers come in various sizes to accommodate different belt widths and loads. The diameter of conveyor rollers typically ranges from about 1.9 inches to 8 inches or more for heavy-duty applications. The width of these rollers usually corresponds to the width of the conveyor belts they are paired with and might be slightly wider to ensure proper belt support and alignment. Lengths of the rollers can also vary and are chosen based on the width of the conveyor system they are intended for. In addition to standard sizes, conveyor rollers can also be custom-made to fit the unique requirements of a particular conveyor system.
Rollers on a conveyor are commonly referred to as conveyor rollers or belt conveyor rollers. Specifically, based on their functionality within the system, they can be classified as drive rollers, idler rollers, or return rollers. Drive rollers are motorized and propel the belt and materials forward. Idler rollers provide support to the belt on the carrying side and often make up the majority of rollers in a conveyor system. Return rollers support the return side of the belt as it cycles back to the beginning of the conveyor system. The correct terminology will depend on the role the roller plays within the conveyor’s operation.
Last Updated on June 4, 2024 by Jordan Smith
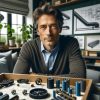
Jordan Smith, a seasoned professional with over 20 years of experience in the conveyor system industry. Jordan’s expertise lies in providing comprehensive solutions for conveyor rollers, belts, and accessories, catering to a wide range of industrial needs. From initial design and configuration to installation and meticulous troubleshooting, Jordan is adept at handling all aspects of conveyor system management. Whether you’re looking to upgrade your production line with efficient conveyor belts, require custom conveyor rollers for specific operations, or need expert advice on selecting the right conveyor accessories for your facility, Jordan is your reliable consultant. For any inquiries or assistance with conveyor system optimization, Jordan is available to share his wealth of knowledge and experience. Feel free to reach out at any time for professional guidance on all matters related to conveyor rollers, belts, and accessories.