Maximizing Conveyor Durability with Impact Roller Rubber Ring
In the realm of conveyor systems, impact rollers play a pivotal role in maintaining the integrity and efficiency of the belt conveyance process. These specialized rollers are strategically placed at points where material is loaded onto the belt, absorbing the shock and impact that could otherwise damage the belt and the system as a whole. A key innovation in the design of impact rollers is the incorporation of an impact roller rubber ring. These rubber rings significantly enhance the roller’s ability to absorb shock, distribute pressure evenly, and reduce the wear and tear on the conveyor belt. The addition of rubber rings transforms standard impact rollers into highly effective tools for prolonging the lifespan of conveyor systems, ensuring smooth operation and minimizing maintenance needs. This introduction to impact rollers with rubber rings highlights their critical importance in optimizing conveyor system performance and protecting valuable material handling infrastructure.
Understand the Impact Roller Rubber Ring
The impact roller rubber ring is a crucial component in the design of modern conveyor systems, particularly those subjected to heavy loads and high-impact forces. These rubber rings are fitted around the impact rollers, which are strategically placed at the loading points of a conveyor system where materials are dropped from a height. The primary function of the impact roller rubber ring is to absorb the shock and distribute the force of falling materials, thereby protecting the conveyor belt from damage and reducing wear on the rollers themselves.
Impact roller rubber rings are made from high-quality, durable rubber materials designed to withstand significant impact forces. These materials are selected for their elasticity, resistance to abrasion, and ability to return to their original shape after deformation. This resilience is key to their functionality, as the rubber rings must compress under impact to absorb energy and then rebound to maintain the integrity of the conveyor system’s operation.
The use of impact roller rubber rings in conveyor systems significantly enhances the functionality and longevity of the bumper roller. By cushioning the blow of materials, these rubber rings prevent the formation of cracks, splits, and other forms of damage to the conveyor belt, which can be costly to repair and result in downtime for the system. Furthermore, the rubber rings help to distribute the weight and impact of the materials more evenly across the roller surface, reducing concentrated wear and extending the life of both the rollers and the conveyor belt.
Moreover, the impact roller rubber ring plays a vital role in maintaining the efficiency of the conveyor system. By minimizing the impact force transferred to the conveyor structure, these rubber rings help to maintain the alignment and tension of the belt, ensuring smooth and consistent material flow. This not only improves the operational efficiency of the conveyor system but also reduces the energy consumption and maintenance requirements, contributing to a more sustainable and cost-effective material handling solution.
The impact roller rubber ring is an indispensable component of any high-impact conveyor system. Its ability to absorb shock, protect the conveyor belt, and enhance the overall functionality and longevity of the system makes it a critical investment for industries reliant on efficient and reliable material handling processes.
Key Components of Impact Roller Systems: The Role of the Impact Roller Rubber Ring
Impact roller systems are integral to the efficient operation of conveyor systems, especially in industries where heavy or abrasive materials are transported. These systems are designed to absorb the shock and distribute the load at points where materials are dropped onto the conveyor, thereby protecting the belt and the structure from damage. A critical component in these systems is the “impact roller rubber ring,” which plays a significant role in enhancing the functionality and longevity of the conveyor system. This section delves into the key components of impact roller systems, with a special focus on the impact roller rubber ring and its applications beyond traditional conveyor systems.
Overview of Impact Roller Conveyor Systems and Their Components
Impact roller systems consist of several key components, each contributing to the system’s overall effectiveness in absorbing impact and protecting the conveyor belt. These components include:
Impact Rollers: The primary component, these rollers are positioned at the loading points of the conveyor system where materials are dropped. They are designed to absorb the shock of falling materials, reducing the impact on the conveyor belt.
Rubber Rings: Fitted around the impact rollers, the impact roller rubber rings are made from high-quality, durable rubber. These rings enhance the impact absorption capabilities of the rollers, ensuring that the conveyor belt remains undamaged and operational over longer periods. The flexibility and resilience of the rubber rings allow for effective shock absorption, even under heavy loads.
Frame and Support Structure: The frame supports the impact rollers and is engineered to withstand the forces exerted during material loading. It is robust and designed for easy integration with the conveyor system.
Bearings and Shafts: High-quality bearings and shafts ensure that the impact rollers rotate smoothly, allowing for efficient energy absorption and material flow.
Microwave Rolling Rings and Their Unique Applications
While the impact roller rubber ring is primarily associated with conveyor systems, similar technology finds unique applications outside of this traditional context. One such application is in microwave rolling rings, an innovative use of rubber ring technology in microwave communication systems. These rings are used to enhance the stability and efficiency of rotating platforms in microwave antennas, ensuring precise alignment and reducing wear on moving parts. The principle of shock absorption and load distribution applied in impact roller systems is adapted to provide stability and precision in these high-tech applications.
The impact roller rubber ring is a testament to the versatility and importance of rubber in industrial applications. Its primary role in conveyor systems—to protect the belt and ensure efficient material handling—is paralleled by its utility in other areas where durability, shock absorption, and precise movement are crucial.
The key components of impact roller systems, particularly the impact roller rubber ring, are essential for the protection and efficiency of conveyor systems. Beyond their traditional use, the principles underlying their design and functionality extend to innovative applications, demonstrating the adaptability and importance of this technology in various industrial contexts.
The Function of Conveyor Roller and Return Roller: Impact Roller Rubber Ring
The conveyor system is a complex assembly of parts working in harmony to move materials efficiently from one point to another. Central to this system are the conveyor roller and return roller, each playing a pivotal role in the conveyor’s operation and longevity. Understanding how these components work, especially in conjunction with the impact roller rubber ring, is essential for optimizing conveyor performance and durability.
Load Roller Conveyors and Their Interaction with Impact Rollers
Load roller conveyors, also known as carrying rollers, are the backbone of the conveyor system. They are mounted along the length of the conveyor path and support the conveyor belt and the materials being transported. These rollers are designed to facilitate smooth movement of the belt with minimal friction and resistance, ensuring efficient material handling across various distances.
Impact rollers, equipped with impact roller rubber rings, are a specialized type of load roller placed at critical points along the conveyor, typically where material is loaded onto the belt. These locations are prone to high impact and stress as materials are dropped from a height, which can cause significant wear and damage to both the belt and the rollers. The impact roller rubber ring serves as a cushion that absorbs the shock of falling materials, distributing the force evenly across the roller and minimizing damage to the conveyor belt. This not only protects the conveyor belt from premature wear and tear but also helps maintain the alignment and integrity of the belt, contributing to the overall efficiency and longevity of the conveyor system.
Return Roller Conveyors and Their Significance
Return rollers, or return idlers, are positioned along the underside of the conveyor system. Their primary function is to support the return path of the conveyor belt after it has transported materials to their destination. Unlike load rollers, return rollers are not subject to the same level of direct impact from loaded materials. However, they are crucial for maintaining the tension and alignment of the conveyor belt, ensuring it runs smoothly and does not sag or veer off course.
The integration of impact roller rubber rings into return rollers is less common than in load rollers, as the need to absorb impact is significantly lower on the return side of the conveyor. However, the principles of durability and reduced wear apply universally across the conveyor system. Ensuring that return rollers are functioning correctly and are in good condition is vital for the overall health of the conveyor system. Worn or misaligned return rollers can lead to belt misalignment, increased friction, and, ultimately, premature belt failure.
Both conveyor rollers and return rollers are integral to the efficient operation of a conveyor system, with each serving a distinct but complementary function. The addition of impact roller rubber rings to load rollers at key points further enhances the system’s ability to handle materials smoothly and efficiently while extending the life of the conveyor belt and reducing maintenance needs. Understanding and maintaining these components are essential for any operation that relies on conveyor systems for material handling.
Catalog Insights: Rulmeca Roller and the Impact Roller Rubber Ring
The Rulmeca Roller catalog offers a comprehensive look into the company’s extensive range of conveyor components, with a particular focus on their innovative impact roller rubber ring solutions. These products stand out for their durability, efficiency, and ability to meet the rigorous demands of various industries. This section delves into the selections highlighted in the Rulmeca Roller Catalog PDF, emphasizing buffer roller options and comparing Rulmeca’s offerings to industry standards.
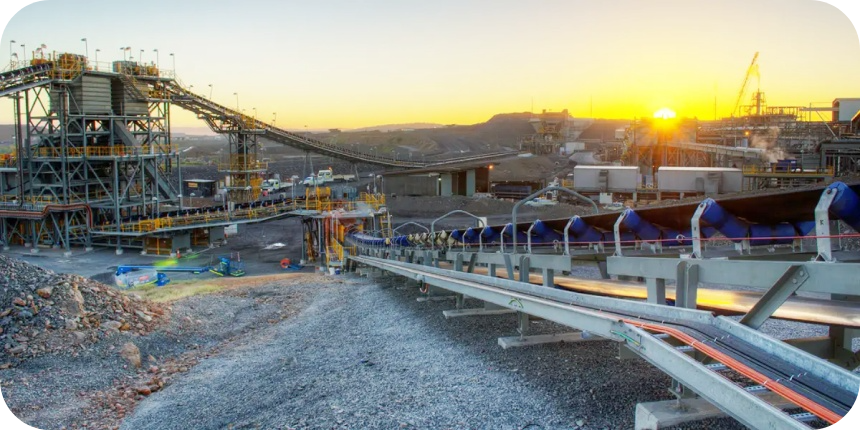
Highlighted Selections in the Rulmeca Roller Catalog
The Rulmeca catalog showcases a variety of impact roller options, each designed to cater to different operational needs and environments. The impact roller rubber ring models are particularly notable for their robust construction and superior performance in absorbing and dispersing the energy from material impacts. These rollers are essential in areas of the conveyor system where materials are loaded onto the belt, providing critical protection to both the conveyor belt and the structure of the conveyor system itself.
Key features of Rulmeca’s impact rollers include:
- High-quality rubber rings that offer exceptional resistance to wear and tear.
- A variety of sizes and configurations to suit different conveyor widths and load requirements.
- Advanced sealing technologies that protect the roller bearings from dust, water, and other contaminants, ensuring a longer service life.
Rulmeca Products Compared to Industry Standards
What makes Rulmeca’s impact roller rubber ring products unique is their commitment to quality and innovation. The use of high-grade materials and advanced manufacturing techniques results in rollers that offer superior performance and longevity compared to standard industry offerings. Additionally, Rulmeca’s focus on customization allows for more precise matching of roller specifications to the specific needs of each conveyor system, ensuring optimal performance and efficiency.
The Rulmeca Roller catalog provides valuable insights into the company’s range of impact roller rubber ring products, highlighting their advantages over standard industry options. With a focus on quality, durability, and customization, Rulmeca’s impact rollers offer an effective solution for protecting conveyor systems and ensuring smooth, efficient operation across various industrial applications.
Belt Conveyor Idler Pulley: Impact Roller Rubber Ring
The belt conveyor idler pulley plays a pivotal role in the conveyor system, acting as a critical support structure for both the conveyor belt and the materials it carries. These idlers are strategically placed along the conveyor path to ensure the belt operates smoothly and efficiently. Understanding the various types of idlers, including those equipped with impact roller rubber rings, is essential for optimizing conveyor performance and extending its operational life.
The Role of Belt Conveyor Idlers
Belt conveyor idlers are cylindrical rods that support the conveyor belt and guide it on its path, ensuring that it maintains the correct tension and alignment. These idlers are mounted on a frame and located at various points along the conveyor system. Their primary function is to provide a smooth surface for the belt to ride on, reducing friction and wear on the belt itself. By doing so, idlers significantly contribute to the efficiency of material transport and the longevity of the conveyor belt.
Types of Idlers and Their Applications
Idlers come in various designs, each tailored to meet specific operational needs within the conveyor system. Below is a table that outlines the different types of idlers, including those fitted with impact roller rubber rings, and their specific applications:
Impact idlers, particularly those with impact roller rubber rings, are of special interest due to their role in enhancing the durability of the conveyor system. The rubber rings serve as a cushion that absorbs the energy of falling materials, minimizing the impact on the belt and the idler structure. This not only protects the conveyor belt from premature wear and tear but also helps to distribute the load more evenly across the idler surface, reducing localized stress and extending the life of both the belt and the idlers.
Belt conveyor idler pulleys, especially those fitted with impact roller rubber rings, are indispensable components of the conveyor system. They ensure the smooth operation of the conveyor belt, protect it from damage, and contribute to the efficient transport of materials. Understanding the different types of idlers and their specific applications is crucial for designing and maintaining an effective conveyor system.
Mechanical Principles of Conveyor Belt Rollers: Enhancing Efficiency with the Impact Roller Rubber Ring
The engineering behind conveyor belt rollers is a fascinating study of physics, materials science, and mechanical design, all aimed at enhancing the efficiency, safety, and longevity of conveyor systems. These systems are vital in numerous industries, moving materials of all sizes and weights over varying distances. A key component in optimizing the performance and safety of these systems is the “impact roller rubber ring,” which plays a crucial role in absorbing shocks and distributing loads. This section delves into the mechanical principles of conveyor belt rollers and illustrates how impact roller rubber rings contribute to the overall efficiency and safety of conveyor systems.
Discovering the Engineering Behind Conveyor Belt Rollers
Conveyor belt rollers operate on the principle of reducing friction between the belt and the materials it carries. These rollers are mounted on a series of axles and are spaced at intervals that provide continuous support to the belt, helping to carry the load efficiently across distances. The rollers are designed to rotate freely, minimizing the effort required to move the belt and its load. This efficiency is achieved through precise engineering that considers factors such as roller diameter, material, and bearing type.
The mechanical design of conveyor rollers must also account for the load they will bear, the environment in which they operate (including temperature and potential exposure to chemicals or moisture), and the speed at which the conveyor will run. The choice of materials for both the rollers and their bearings is critical to ensuring that they can withstand the operational stresses without excessive wear.
How Impact Roller Rubber Rings Improve Efficiency and Safety
The inclusion of an impact roller rubber ring in conveyor systems introduces several mechanical advantages that enhance both efficiency and safety. These rubber rings are fitted around the impact rollers, located at points where material is loaded onto the conveyor. The primary function of these rings is to absorb the kinetic energy of falling materials, which reduces the shock and stress on both the conveyor belt and the rollers themselves.
Shock Absorption: The rubber material of the rings deforms slightly under impact, absorbing the energy of falling materials. This deformation is elastic, meaning the rubber returns to its original shape, ready to absorb the next impact. This elasticity reduces the peak forces transmitted to the structure of the conveyor system, thereby protecting it from damage.
Load Distribution: By spreading the force of impacts over a wider area, impact roller rubber rings help distribute the load more evenly across the belt. This distribution can prevent localized damage to the belt and reduce the risk of material spillage due to uneven loading.
Noise Reduction: The rubber material of the rings also serves to dampen noise generated at the loading points. This noise reduction contributes to a safer and more pleasant working environment for personnel operating near the conveyor.
Vibration Damping: Impact roller rubber rings help to dampen vibrations that could lead to wear and fatigue in the conveyor structure and the rollers themselves. By reducing vibration, the lifespan of the conveyor components is extended, and maintenance costs can be minimized.
The mechanical principles underlying the design and operation of conveyor belt rollers are integral to the efficiency and safety of conveyor systems. The addition of impact roller rubber rings represents a simple yet effective innovation that significantly enhances the performance of these systems. By absorbing shocks, distributing loads, reducing noise, and damping vibrations, these rubber rings protect both the conveyor system and the materials it transports, ensuring smooth, efficient, and safe operations across a wide range of industrial applications.
Guide Roller Conveyor: Leading the Way with Impact Roller Rubber Ring
The guide roller conveyor plays an essential role in the seamless operation of conveyor systems, ensuring that the conveyor belt follows the correct path and remains aligned throughout its course. This is particularly crucial in complex conveyor setups where the belt must navigate turns, inclines, or declines. The incorporation of the impact roller rubber ring into guide rollers further enhances their functionality, making them even more effective in maintaining the conveyor belt’s path under various operational conditions.
Function of Guide Roller Conveyor
Guide roller conveyors are strategically placed along the sides of the conveyor belt, serving as a boundary and guide to keep the belt on track. Their primary function is to prevent the conveyor belt from drifting or misaligning, which can lead to uneven wear, potential damage to the belt, and inefficiency in material transport. Guide rollers are especially important in sections of the conveyor system where directional changes occur, as these are points where the belt is most susceptible to misalignment.
The design of guide rollers varies depending on the specific requirements of the conveyor system. Some guide rollers are fixed, providing a constant guiding force in one direction, while others are adjustable, allowing for changes in the conveyor belt’s path as needed. The selection of guide roller type depends on factors such as the conveyor belt’s width, speed, and the nature of the materials being transported.
Impact of Rubber Rings on Guide Rollers
The integration of impact roller rubber rings into guide rollers introduces an additional layer of functionality and protection. These rubber rings, fitted around the guide rollers, offer several benefits:
Cushioning and Noise Reduction: The rubber rings provide a cushioning effect that reduces the impact and vibration as the conveyor belt interacts with the guide rollers. This not only protects the belt and rollers from wear but also significantly reduces operational noise, contributing to a more pleasant working environment.
Increased Friction: The rubber material of the impact roller rubber ring enhances the friction between the guide roller and the conveyor belt. This increased grip helps to correct minor misalignments more effectively, ensuring that the belt remains on its intended path.
Durability in Various Conditions: Rubber rings are resistant to various environmental factors, including moisture, dust, and chemicals, making them suitable for use in a wide range of industrial settings. Their durability ensures that guide rollers maintain their effectiveness in guiding the conveyor belt, even in harsh or variable conditions.
Versatility: The flexibility of rubber allows the impact roller rubber rings to adapt to slight variations in the belt’s path without causing damage or undue stress to the belt itself. This adaptability makes rubber ring-equipped guide rollers effective in various conveyor setups, from straight runs to complex configurations with multiple turns and elevation changes.
Guide roller conveyors equipped with impact roller rubber rings are instrumental in leading the way for conveyor belts, ensuring they follow the correct path with minimal risk of misalignment or damage. The addition of rubber rings enhances the functionality, durability, and effectiveness of guide rollers, making them an invaluable component in the efficient operation of conveyor systems across diverse industrial applications.
Submit Your Inquiry for deep impact rollerConveyor Roller Specifications and Pricing.
FAQs about Impact Roller Rubber Ring
Impact idlers are specialized components in conveyor systems designed to absorb the shock and distribute the force exerted by materials falling onto the conveyor belt at loading points. These idlers are crucial for protecting the conveyor belt from damage due to the high impact of heavy or sharp materials being loaded onto the belt. The primary function of impact idlers is to extend the lifespan of the conveyor belt and reduce maintenance costs by minimizing wear and tear.
Impact idlers achieve this by featuring a series of robust, cushioned rollers that are capable of compressing under the force of falling materials. This compression helps to dissipate the energy of the impact across a broader area, rather than allowing it to concentrate on a single point on the conveyor belt. By doing so, impact idlers prevent punctures, tears, and other forms of damage to the belt, ensuring smooth operation and reducing downtime for repairs. Additionally, they help in maintaining the structural integrity of the conveyor system by reducing the stress on other components.
Idlers in conveyor systems come in various types, each designed to fulfill specific roles within the conveyor’s operation. The main types of idlers include:
Carrying Idlers: These are the most common type of idlers, positioned along the length of the conveyor path to support the belt and the materials it carries. They can be flat or trough-shaped to suit the material being transported.
Return Idlers: Located on the underside of the conveyor, return idlers support the belt on its journey back to the start after offloading the materials. They help to maintain the belt’s tension and alignment.
Impact Idlers: Specifically designed to absorb the shock of materials falling onto the belt at loading points, impact idlers protect the belt from damage and extend its service life.
Self-Aligning Idlers: These idlers automatically adjust the belt’s position to keep it aligned, preventing it from drifting off the rollers. They are essential for maintaining the conveyor’s efficiency and preventing belt damage.
Guide Idlers: Installed on the sides of the conveyor belt, guide idlers help to control the belt’s lateral movement and keep it on track, especially in curved sections of the conveyor.
Each type of idler plays a vital role in the conveyor system, contributing to its overall efficiency, safety, and longevity.
An idler roller serves as a fundamental component of a conveyor system, providing support to the conveyor belt and helping to guide it along its intended path. The primary role of an idler roller is to offer a smooth, consistent surface for the conveyor belt to ride upon, which reduces friction and wear on the belt, thereby extending its lifespan. Idler rollers are strategically placed throughout the conveyor system to maintain the belt’s tension and alignment, ensuring efficient operation.
In addition to supporting the belt, idler rollers also play a crucial role in distributing the weight of the materials being conveyed. This distribution helps to prevent the belt from sagging or becoming misaligned under the load, which could lead to operational issues or damage to the belt and other conveyor components. By ensuring that the conveyor belt remains in optimal condition, idler rollers contribute to the smooth, uninterrupted flow of materials, enhancing the conveyor system’s productivity and reliability.
An idler in a conveyor system refers to a non-powered roller that supports the conveyor belt and the materials being transported. Idlers are strategically positioned along the conveyor’s length and are essential for maintaining the belt’s proper tension, alignment, and smooth operation. They come in various designs and types, each serving specific functions within the conveyor system, such as supporting the loaded belt (carrying idlers), supporting the belt on its return path (return idlers), absorbing impact at loading points (impact idlers), ensuring belt alignment (self-aligning idlers), and guiding the belt (guide idlers).
Idlers are critical to the efficiency and longevity of a conveyor system. They minimize wear on the conveyor belt, reduce operational noise, and help to distribute the load evenly. By doing so, idlers not only protect the conveyor belt from premature wear and potential damage but also contribute to the overall performance and reliability of the conveyor system, ensuring materials are moved efficiently from one point to another.
Last Updated on July 30, 2024 by Jordan Smith
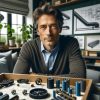
Jordan Smith, a seasoned professional with over 20 years of experience in the conveyor system industry. Jordan’s expertise lies in providing comprehensive solutions for conveyor rollers, belts, and accessories, catering to a wide range of industrial needs. From initial design and configuration to installation and meticulous troubleshooting, Jordan is adept at handling all aspects of conveyor system management. Whether you’re looking to upgrade your production line with efficient conveyor belts, require custom conveyor rollers for specific operations, or need expert advice on selecting the right conveyor accessories for your facility, Jordan is your reliable consultant. For any inquiries or assistance with conveyor system optimization, Jordan is available to share his wealth of knowledge and experience. Feel free to reach out at any time for professional guidance on all matters related to conveyor rollers, belts, and accessories.