The Versatility of Impact Roller Uses Across Industries
Impact rollers, often recognized as buffer rollers in the material handling and construction industries, play a pivotal role in enhancing the efficiency and longevity of conveyor systems and compaction equipment. These specialized rollers are designed to absorb the shock and stress caused by heavy materials falling onto conveyor belts or being compacted in construction projects, thereby preventing damage and wear. The versatility of impact roller uses spans across numerous sectors, including mining, agriculture, construction, and manufacturing, showcasing their critical importance in a wide array of industrial applications. This blog aims to delve into the multifaceted applications of impact rollers, providing readers with a comprehensive understanding of their significance in not only safeguarding equipment but also in optimizing operational processes across construction sites and conveyor systems. Through this exploration, we seek to illuminate the diverse ways in which impact rollers contribute to project efficiency and equipment durability.
Impact Roller Uses: Understanding the Buffer Roller
Impact rollers, commonly referred to as buffer rollers in various industrial applications, are integral components designed to mitigate the impact force exerted on conveyor belts and during compaction processes. These specialized rollers are engineered to absorb shock, distribute stresses evenly, and enhance the durability of the systems they are part of. This section aims to elucidate the design features of impact rollers and delineate their differences from conventional rollers, such as sheep’s foot rollers and vibratory rollers.
Design Features of Impact Rollers:
Impact rollers are characterized by their robust construction, which includes a series of rubber discs or rings mounted on a heavy-duty steel frame. These rubber elements are specifically designed to compress under load, effectively absorbing the impact energy of materials falling onto the belt or being compacted on the ground. The core design features of impact rollers include:
- Non-Cylindrical Geometry: Unlike traditional rollers, impact rollers may have a multi-sided, non-cylindrical shape to increase the impact area and ensure more uniform compaction or protection.
- Durable Materials: Constructed from high-grade rubber and reinforced with steel or composite materials for added strength and resilience.
- Adjustable Configuration: Some impact rollers offer adjustable spacing between the discs or rings, allowing for customization based on the specific application needs.
Differences Between Impact Rollers and Conventional Rollers:
What are the distinct features and applications of impact rollers compared to sheep’s foot and vibratory rollers highlights the specialized nature of impact roller uses. While all these rollers serve the fundamental purpose of compaction or protection, the choice between them depends on the specific requirements of the project, including the type of material being handled, the desired depth of compaction, and the efficiency needed. Impact rollers stand out for their ability to provide high-level shock absorption and stress distribution, making them indispensable in scenarios where protecting the conveyor belt or achieving uniform surface compaction is critical.
Application of Impact Rollers Uses in Construction
The use of impact rollers in construction projects is pivotal for ensuring the structural integrity and longevity of the built environment. Impact rollers, also known as impact compactors, play a crucial role in preparing the ground for construction by compacting soil, gravel, and asphalt. This section delves into the specific impact roller uses in construction, highlighting their advantages and comparing them with other compaction equipment like sheep’s foot rollers.
Impact Roller Uses in Compacting Soil, Gravel, and Asphalt
Impact rollers are essential in road construction and foundation preparation, where a solid and compact base is crucial. Here’s how they contribute to construction projects:
- Soil Compaction: Impact rollers are highly effective in compacting various soil types to create a stable and firm foundation for construction projects. They are particularly useful for compacting loose soil in large areas, ensuring uniform compaction depth and density.
- Gravel Compaction: In road construction, impact rollers play a vital role in compacting gravel layers, providing a solid base for the asphalt layers. Their heavy-duty design allows for efficient compaction, reducing the risk of settlement and ensuring the durability of the road surface.
- Asphalt Compaction: Although primarily used for soil and gravel, impact rollers can also be used in asphalt compaction, especially for large areas like parking lots or airport runways, where achieving uniform compaction is essential for surface longevity.
Advantages of Using Impact Rollers for Deep Compaction
Impact rollers are preferred for deep compaction projects due to several advantages:
- Efficiency: They can cover large areas quickly, making them ideal for projects with tight deadlines.
- Depth of Compaction: Impact rollers can achieve deeper compaction compared to traditional rollers, ensuring a more stable base for construction.
- Versatility: Suitable for a wide range of materials, from loose soil to gravel, enhancing their utility in diverse construction scenarios.
Impact Compactor in Ground Improvement Projects
In ground improvement projects, impact compactors are invaluable for their effectiveness in achieving the required compaction levels over extensive areas. They are particularly beneficial in projects requiring deep compaction to improve the load-bearing capacity of the soil, which is critical for the stability of structures like buildings, bridges, and roads.
Sheep’s Foot Roller vs. Impact Roller
When comparing impact rollers with sheep’s foot rollers, several factors come into play:
The application of impact rollers in construction is multifaceted, offering significant benefits in terms of efficiency, compaction depth, and versatility. Whether preparing the foundation for a new building, compacting the base layer of a road, or improving the ground for a large infrastructure project, impact rollers are a critical component of modern construction practices. Their advantages over traditional compaction methods, such as with sheep’s foot rollers, highlight their importance in achieving the structural integrity required in today’s construction standards.
Impact Roller Uses: Impact Rollers in Conveyor Systems
In the realm of material handling, the efficiency and longevity of conveyor systems are paramount. Impact rollers, or buffer rollers as they are sometimes known, play a crucial role in maintaining the integrity and performance of these systems. This section delves into the specific applications and benefits of impact rollers within conveyor systems, highlighting their importance in industrial settings.
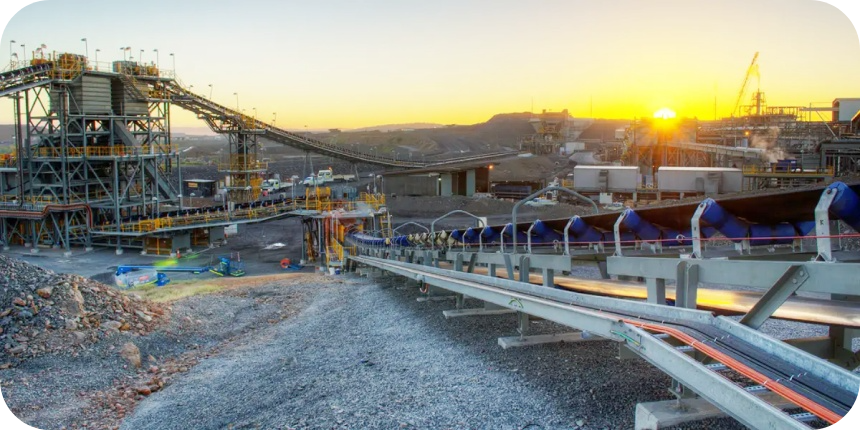
Impact Roller Conveyors:
At the heart of their functionality, impact rollers are designed to absorb the significant impact energy that occurs at the loading points of conveyor systems. When materials are dropped onto the conveyor belt from a height, the force exerted can cause damage to the belt and the system as a whole. Impact rollers are strategically placed at these critical points to cushion the blow, distributing the force over a larger area and thereby extending the life of the belt. This protective measure not only prevents premature wear and tear but also contributes to the overall efficiency of the conveyor system by minimizing downtime and maintenance needs.
Uses of Heavy-Duty Impact Rollers:
In industrial environments where the transportation of large, heavy materials is a daily operation, heavy-duty impact rollers are indispensable. These robust versions of impact rollers are engineered to withstand the extreme forces exerted by materials such as rocks, metal ores, and large volumes of bulk goods. Their enhanced durability and impact-absorbing capabilities ensure that conveyor belts can handle the added weight and stress without succumbing to damage. This is particularly vital in sectors like mining, quarrying, and heavy manufacturing, where the cost of equipment downtime can be substantial.
Carrier and Return Rollers:
Carrier (or carrying) and return rollers constitute the backbone of any conveyor system, providing continuous support for the conveyor belt and the materials being transported. Carrier rollers are positioned along the length of the conveyor to support the loaded belt from the carrying side, while return rollers support the belt on the return path. Despite their critical support roles, these rollers are not designed to handle the impact at loading points – this is where impact rollers come into play. Impact rollers enhance the functionality of carrier and return rollers by absorbing the initial shock of loading, thereby protecting the belt and ensuring a smooth transition of materials onto the conveyor. This synergy between impact rollers and carrier/return rollers is essential for maintaining the structural integrity of the conveyor system and ensuring optimal performance.
The use of impact rollers in conveyor systems is a testament to their versatility and effectiveness in safeguarding material handling infrastructure. By absorbing the impact at loading points, extending the lifespan of conveyor belts, and complementing the functions of carrier and return rollers, impact rollers are indispensable in ensuring the efficient operation of conveyor systems across various industrial landscapes.
Procurement and Maintenance of Impact Roller Uses
The procurement and maintenance of impact rollers are critical aspects that ensure the effectiveness and longevity of these essential construction tools. Impact rollers, utilized in a variety of applications for compacting soil, gravel, and asphalt, require careful selection and regular maintenance to perform their functions optimally. This section provides insights into purchasing buffer rollers and maintaining impact rollers for various uses.
Buffer Roller for Sale: Purchasing Tips
When looking to purchase a buffer roller, several factors must be considered to ensure that the equipment meets the specific needs of your projects. Here’s a table outlining key considerations:
Maintenance Recommendations
To ensure the longevity and efficiency of impact rollers across various applications, adhering to a comprehensive maintenance schedule is crucial. Here are recommended maintenance practices:
- Regular Inspection: Conduct routine inspections of the impact rollers for any signs of wear, damage, or deformation. Pay special attention to the roller surface, bearings, and mounting hardware.
- Cleaning: Keep the rollers clean from debris, soil, and other materials that could impair their function. Cleaning also helps in identifying any hidden damages that require attention.
- Lubrication: Regularly lubricate moving parts, such as bearings, to reduce friction and prevent wear. Use lubricants suitable for the roller’s operating conditions.
- Alignment Checks: Ensure the rollers are correctly aligned within the conveyor system. Misalignment can lead to uneven wear and reduced efficiency.
- Replacement of Worn Parts: Replace any parts that show significant wear or damage immediately. Using worn components can compromise the roller’s performance and lead to further damage.
- Record Keeping: Maintain detailed records of inspections, maintenance activities, and replacements. This documentation can help in identifying recurring issues and planning preventive maintenance.
By carefully considering the procurement factors and adhering to the recommended maintenance practices, you can enhance the performance and extend the service life of impact rollers. Proper procurement ensures that you select the most suitable roller for your specific needs, while diligent maintenance prevents downtime and ensures that the impact rollers continue to contribute effectively to the success of your construction projects.
Impact Roller Uses: Case Studies and Practical Applications
The versatility and effectiveness of impact rollers across various industries can be best understood through real-world case studies and practical applications. These examples not only showcase the significant contributions of impact rollers to project success but also highlight their adaptability to different operational challenges. Below, we delve into a few case studies that underscore the pivotal role of impact rollers in enhancing efficiency and durability in both construction and material handling projects.
Case Study 1: Road Construction and Compaction
In a large-scale road construction project in Western Australia, the use of impact rollers was instrumental in achieving the desired compaction levels for the road’s foundation. Traditional compaction methods were proving inadequate due to the soil’s high moisture content and variability. The introduction of heavy-duty impact rollers allowed for deeper compaction, reaching depths of up to 2 meters, significantly beyond what conventional rollers could achieve. This not only ensured a stable foundation for the road but also expedited the construction timeline by reducing the need for multiple passes with different rollers. The project’s success highlighted the impact roller’s capability to adapt to challenging soil conditions and deliver reliable results.
Case Study 2: Mining Operation Efficiency
In a mining operation in Queensland, the deployment of impact rollers on conveyor systems handling abrasive materials like coal and iron ore resulted in a marked improvement in belt longevity. The impact rollers were installed at key transfer points where the material drop was causing frequent belt failures. The buffer action of the impact rollers absorbed the energy of the falling materials, reducing wear and tear on the belt and associated downtime for repairs. This application demonstrated the impact roller’s critical role in maintaining continuous operations in harsh industrial environments.
Case Study 3: Landfill Compaction for Environmental Projects
An environmental reclamation project at a former landfill site utilized impact rollers to compact and stabilize the ground for a new public park. The challenge lay in the site’s heterogeneous fill material, which included a mix of soil, construction debris, and organic waste. Impact rollers provided the necessary deep compaction, ensuring a uniform compaction depth of up to 3 meters. This application showcased the impact roller’s ability to handle a variety of materials and contribute to sustainable development projects by preparing previously unusable land for public use.
Need Assistance with Impact Conveyor Roller Selection? Contact Us.
Case Study 4: Agricultural Land Improvement
In the agricultural sector, a farm faced issues with water retention and soil stability for its crop fields. The introduction of impact rollers for soil compaction and land leveling significantly improved the land’s water retention capability and provided a more stable base for planting. This not only increased crop yields but also reduced water usage, showcasing the impact roller’s contribution to improving agricultural efficiency and sustainability.
These case studies illustrate the broad spectrum of impact roller uses, from construction and mining to environmental reclamation and agriculture. Each example underscores the equipment’s ability to deliver tailored solutions to unique project challenges, affirming the impact roller’s status as a versatile and effective tool in both compaction and material handling applications.
FAQs about Impact Roller Uses
The primary purpose of an impact roller, also known as a buffer roller, is to absorb and dissipate the kinetic energy generated when materials are dropped onto a conveyor belt or during the compaction process in construction projects. This specialized type of roller is designed to protect the conveyor belt from damage caused by the high impact force of falling materials, thereby extending the belt’s lifespan and maintaining the efficiency of the conveyor system. In construction and earthworks, impact rollers are used to achieve deep compaction of soil, gravel, concrete, or asphalt, enhancing the stability and durability of the constructed surface or foundation. By distributing the impact energy over a larger area, impact rollers prevent excessive wear and tear on the equipment and ensure uniform compaction or material distribution, contributing to the overall success and longevity of the project.
Impact rollers find extensive application in two primary fields: material handling and construction compaction. In material handling, especially within conveyor systems, impact rollers are strategically placed at loading points where materials are transferred onto the belt. This placement is crucial for absorbing the shock and protecting the belt from damage due to the impact of heavy or sharp materials, thereby reducing maintenance costs and downtime. In the construction and earthworks sector, impact rollers are employed for compaction tasks. They are particularly effective in compacting large areas quickly and efficiently, reaching deeper soil layers than traditional compaction methods. This deep compaction capability makes impact rollers invaluable in preparing foundations for roads, buildings, and other infrastructure projects, ensuring a stable and durable base that meets engineering specifications and standards.
In a belt conveyor system, the impact roller is a critical component designed to absorb the shock and impact force when materials are loaded onto the conveyor belt. These rollers are typically installed at the conveyor’s feed points, where the material drop is the greatest, posing a risk of damage to the belt. Impact rollers consist of a series of robust, cushioned discs mounted on a heavy-duty frame, which allows them to effectively dissipate the energy from falling materials. This design minimizes the stress on the conveyor belt, preventing tears, punctures, and premature wear. By safeguarding the conveyor belt’s integrity, impact rollers play a vital role in maintaining operational efficiency, reducing repair and replacement costs, and ensuring continuous, smooth operation of the conveyor system.
Compaction rollers, including impact rollers, are essential tools in construction and earthworks for compacting soil, gravel, concrete, or asphalt to create a dense, stable, and flat surface. The primary use of compaction rollers is to increase the ground’s load-bearing capacity by reducing air gaps and voids within the soil or other materials, which enhances the strength and stability of the foundation for roads, buildings, and other structures. Compaction is a critical step in construction projects to prevent settlement, shifting, or collapse of the structure over time. Impact rollers, with their ability to achieve deep compaction, are especially useful for projects requiring a solid foundation laid to considerable depths. They ensure that the compacted surface can adequately support the weight and stress of the overlying structure, meeting the necessary safety and durability standards.
Last Updated on July 24, 2024 by Jordan Smith
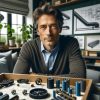
Jordan Smith, a seasoned professional with over 20 years of experience in the conveyor system industry. Jordan’s expertise lies in providing comprehensive solutions for conveyor rollers, belts, and accessories, catering to a wide range of industrial needs. From initial design and configuration to installation and meticulous troubleshooting, Jordan is adept at handling all aspects of conveyor system management. Whether you’re looking to upgrade your production line with efficient conveyor belts, require custom conveyor rollers for specific operations, or need expert advice on selecting the right conveyor accessories for your facility, Jordan is your reliable consultant. For any inquiries or assistance with conveyor system optimization, Jordan is available to share his wealth of knowledge and experience. Feel free to reach out at any time for professional guidance on all matters related to conveyor rollers, belts, and accessories.