Maximize Efficiency with Industrial Roller Conveyor Tables
Industrial roller conveyor tables play a pivotal role in streamlining operations across a myriad of industries, from manufacturing to logistics and beyond. These tables facilitate the efficient movement of goods through production lines and distribution centers, significantly enhancing productivity and operational flow. The versatility of industrial roller conveyor table is evident in the diverse range of prices, sizes, and types available, including both powered and gravity options, catering to various operational needs and budget constraints. Whether businesses are in the market for brand new installations or are considering the cost-effective route of acquiring used tables, the options are vast. The choice between powered roller conveyors, which provide automated movement of goods, and gravity roller conveyors, which utilize gravitational forces for movement, allows for customization according to specific industry requirements. This adaptability, combined with the availability of different dimensions to suit various spaces and applications, underscores the indispensable nature of industrial roller conveyor tables in enhancing efficiency and productivity in industrial settings.
Learn About Industrial Roller Conveyor Table Workbench
An industrial roller conveyor table is a crucial component in the framework of material handling within various sectors, designed to facilitate the seamless transit of goods across manufacturing floors, warehouses, and distribution centers. These tables are equipped with rollers to allow for the easy movement of items, enhancing operational efficiency by minimizing manual handling and thereby reducing labor costs and increasing productivity.
The industrial roller conveyor table comes in two primary types, each suited to different needs within the material handling process: heavy-duty gravity roller conveyors and powered roller conveyors. The key differences between these two types are highlighted below in a comparative table:
The versatility of an industrial roller conveyor table lies in its adaptability to different operational needs. Gravity roller conveyors are often selected for their simplicity and ease of maintenance, making them a cost-effective solution for many industries. In contrast, powered roller conveyors, with their ability to control the speed and direction of goods, offer a higher degree of precision and efficiency, essential for more complex or automated operations.
Beyond the basic differentiation between gravity and powered systems, industrial roller conveyor tables can be customized with various materials, roller sizes, and configurations to suit specific product types, weights, and operational environments. This versatility ensures that businesses can tailor their conveyor solutions to optimize throughput, enhance safety, and minimize downtime, thereby improving overall operational efficiency.
The industrial roller conveyor table is more than just a piece of equipment; it is a vital component of modern industrial operations, offering a blend of efficiency, versatility, and customization. Whether through the simple, gravity-driven movement of goods or the more complex, motorized control of product flow, these tables play a critical role in ensuring that industries can keep pace with the demands of production and distribution in an increasingly competitive market.
Types of Industrial Roller Conveyor Workbench
The industrial roller conveyor table is a critical component in the operational flow of numerous industries, facilitating smooth operation and efficient material handling. Understanding the various types of this equipment is vital for selecting an appropriate fit for specific activities. There are multiple variations, but here we will focus on three types: heavy-duty, power, and gravity roller conveyors.
Heavy-Duty Industrial Roller Conveyor Table
The heavy-duty industrial roller conveyor table is designed for environments that deal with weighty and large-sized products. These units are robust, built to withstand intense and continuous usage, while consistently delivering superior performance across many industries. They typically come with sturdy metal rollers and reinforced frames to support hefty materials. Industries ranging from automotive to heavy machinery prefer using this type of conveyor for their operations because of its high capacity and durability.

Power Industrial Roller Conveyor Table
The power industrial roller conveyor table is designed for smoother material handling operations. Unlike the passive flow in gravity roller conveyors, this type uses a motor to power the rollers and move items along the conveyor belt. This type offers total control over the speed and direction of the items, making it suitable for processes that require better handling precision. You can find these conveyors in industries requiring careful transport of products, such as electronics manufacturing and food processing.
Gravity Roller Industrial Conveyor Table
A gravity roller industrial conveyor table harnesses the force of gravity to move loads down the line. This type doesn’t rely on power or machinery to work, making it an energy-efficient and cost-effective solution for certain applications. The gravity roller conveyor table is particularly beneficial for warehousing activities and production lines where the work surface is inclined, and items can naturally slide from one point to another. Loading and unloading goods, order picking, assembly tasks, and packaging activities are commonplace uses for this type of conveyor.
Each of these conveyors – heavy-duty, power, and gravity – has its unique benefits and applications. When choosing an industrial roller conveyor table, factors such as the type of goods, their weight, operational efficiency, and safety requirements in your specific industrial environment must be taken into consideration. By doing so, businesses can optimize their operations, increase productivity, and enhance overall workplace efficiency.
Discover durable conveyor rollers. Inquire for details today!
Key Features and Specifications of Industrial Roller Conveyor Table
When delving into the key features and specifications of an industrial roller conveyor table, it’s crucial to understand the dimensions and technical details that make these systems so indispensable in industrial settings. The dimensions of an industrial roller conveyor table can vary widely to accommodate the vast range of applications and environments in which they operate. From compact models designed for tight spaces to expansive systems engineered for large-scale operations, the versatility in size ensures that there is a conveyor solution for every need.
The specifications of an industrial roller conveyor table go beyond mere dimensions, encompassing load capacity, roller diameter, materials used in construction, and the type of drive mechanism (gravity or powered). The load capacity is a critical specification, as it determines the weight and size of the items the conveyor can safely transport. Roller diameter affects the types of goods that can be conveyed, with larger rollers suitable for heavier and larger items. The choice of materials—whether steel, aluminum, or a combination thereof—impacts the durability, weight, and cost of the conveyor.
A heavy-duty design is paramount for ensuring the durability and longevity of an industrial roller conveyor table. This involves robust construction materials capable of withstanding the rigors of daily use in harsh industrial environments. Heavy-duty conveyors are designed to operate efficiently under continuous load and in conditions where lesser systems might falter. This resilience not only extends the lifespan of the conveyor but also minimizes maintenance requirements, ensuring a lower total cost of ownership over time.
Customization is another significant aspect of industrial roller conveyor tables, offering solutions tailored to specific operational needs. This can include adjustable heights for ergonomic operation, varying roller widths and spacings to accommodate different product sizes, and specialized coatings or materials for rollers to handle sensitive or unique items. The ability to customize these conveyors allows for seamless integration into existing workflows, enhancing efficiency without compromising on performance.
What is the key features and specifications of an industrial roller conveyor table is essential for selecting a system that meets the operational demands of any industrial application. The heavy-duty design ensures durability and longevity, while customization options provide the flexibility needed to address specific challenges and requirements. By prioritizing these aspects, businesses can invest in conveyor solutions that not only improve operational efficiency but also contribute to a safer and more productive work environment.

Price Guide and Buying Tips
Navigating the pricing landscape for an industrial roller conveyor table requires a clear understanding of the factors that influence costs and the distinction between new and used equipment options. The price of an industrial roller conveyor table can vary significantly based on size, load capacity, material construction, and whether the system is powered or gravity-fed. New conveyor tables, equipped with the latest technology and customization options, generally command higher prices, reflecting their increased efficiency, longevity, and the inclusion of modern safety features. On the other hand, used conveyor tables can offer substantial cost savings, making them an attractive option for budget-conscious buyers or operations where cutting-edge technology is not a critical requirement.
Evaluating Cost-Effectiveness
When considering the purchase of an industrial roller conveyor table, evaluating the cost-effectiveness involves more than just comparing price tags. It includes assessing the total cost of ownership, which encompasses initial purchase costs, maintenance expenses, and potential productivity gains or losses. A higher-priced conveyor might offer better durability and lower maintenance costs, translating to savings over time. Similarly, a conveyor that integrates seamlessly with your existing operations might offer productivity improvements that justify a higher initial investment.
Operational Requirements
Understanding your operational requirements is crucial in selecting the right industrial roller conveyor table. Consider the nature of the materials or products to be handled, the required speed of operations, and any specific environmental conditions (such as exposure to chemicals or extreme temperatures) that the conveyor needs to withstand. For operations requiring high-speed transportation of heavy goods, investing in a heavy-duty powered conveyor might be necessary, despite the higher cost. Conversely, for simpler, light-weight material handling tasks, a gravity conveyor could provide a cost-effective solution.
Buying Tips:
- Assess Your Needs: Clearly define what you need from your conveyor system in terms of capacity, speed, and type of goods transported. This assessment will guide your decision-making process.
- Research Suppliers: Look for reputable suppliers with a track record of providing quality conveyor solutions. Consider their after-sales support and warranty offerings.
- Consider Customization: Determine if customization options are necessary for your specific application. While custom features can increase costs, they might also significantly improve efficiency.
- Evaluate New vs. Used: Compare the prices and benefits of new versus used conveyor tables. Remember, while used tables can offer cost savings, they may come with increased maintenance needs or shorter lifespans.
- Total Cost of Ownership: Look beyond the purchase price to consider maintenance costs, durability, and the potential impact on productivity. A cheaper option that requires frequent repairs or slows down operations may end up being more expensive in the long run.
- Consult with Experts: Don’t hesitate to seek advice from industry experts or manufacturers. Their insights can help you avoid common pitfalls and select a conveyor table that meets your operational needs without exceeding your budget.
By following these tips and considering both the initial investment and ongoing operational costs, businesses can make informed decisions that balance budget constraints with performance requirements. This approach ensures the selection of an industrial roller conveyor table that not only meets immediate needs but also contributes to long-term operational success.
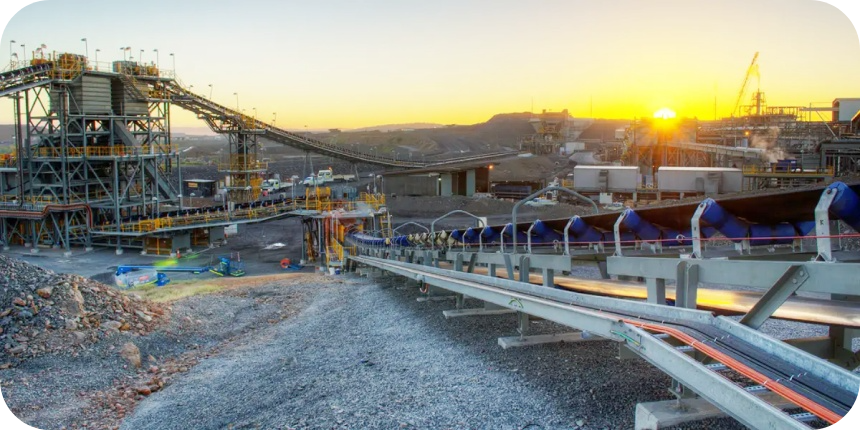
Advantages of Buying a Second-Hand Industrial Roller Conveyor Table
Opting for a second-hand industrial roller conveyor table can offer a plethora of benefits, particularly in terms of cost savings and immediate availability. This section delves into the advantages of purchasing used equipment such as gravity roller conveyors and heavy-duty roller tables, outlines how to assess their condition and value, and recommends reputable suppliers like GRAM Conveyor as an exemplary source for quality used conveyors.
Benefits and Cost Savings:
Purchasing a second-hand industrial roller conveyor table can significantly reduce initial capital expenditure, a crucial factor for startups and businesses looking to expand operations without overspending. The following table contrasts the benefits of buying used versus new equipment:
Assessing Condition and Value:
Evaluating the condition of a second-hand industrial roller conveyor table is pivotal to ensure it meets operational needs and offers value for money. Consider the following steps:
- Visual Inspection: Check for signs of wear and tear, corrosion, or damage to components that might affect functionality.
- Operational Test: If possible, observe the conveyor in operation to assess performance and identify any issues with movement or noise.
- Maintenance History: Request maintenance logs to understand how well the equipment has been cared for and to anticipate future maintenance needs.
- Manufacturer Reputation: Consider equipment from reputable manufacturers known for durability and longevity, ensuring a better investment.
- Warranty or Guarantee: Some used equipment may come with a limited warranty or guarantee, offering added peace of mind.
Reputable Suppliers:
Identifying reputable suppliers is crucial when purchasing a second-hand industrial roller conveyor table. GRAM Conveyor, for example, stands out as a supplier committed to offering quality used equipment. Known for their thorough inspection and refurbishment processes, GRAM Conveyor ensures that each piece of equipment is in optimal condition, providing buyers with confidence in their investment. Additionally, reputable suppliers often offer after-sales support and advice, further enhancing the value of purchasing used equipment.
Buying a second-hand industrial roller conveyor table presents an attractive option for businesses looking to maximize their budget while achieving operational efficiency. By carefully assessing the condition and value of used equipment and choosing reputable suppliers like GRAM Conveyor, businesses can enjoy significant cost savings, immediate availability, and the environmental benefits of reusing industrial machinery, all without compromising on quality or performance.
Installation, Maintenance, and Security of Industrial Roller Conveyor Table
Ensuring the smooth integration and operation of your industrial roller conveyor table within your facility requires attention to detail in installation, regular maintenance, and stringent adherence to safety protocols. Each of these aspects is crucial for maximizing efficiency and safeguarding the well-being of your workforce. Below, we delve into the fundamentals of installation, maintenance practices, and the security measures essential for heavy-duty roller conveyors.
Installation and Integration of Industrial Roller Conveyor Table
The installation process of an industrial roller conveyor table begins with a thorough assessment of your workspace and an understanding of the specific needs of your operations. This preparatory phase involves measuring the available space, identifying optimal placements to enhance flow efficiency, and ensuring that the conveyor aligns with existing systems. Professional installation teams often handle this process, as precise alignment and anchoring are crucial to prevent operational hiccups.
Key steps include:
- Layout planning: Mapping out the conveyor path, considering factors like workspace ergonomics and material handling flow.
- Assembly and positioning: Following manufacturer guidelines to assemble the conveyor sections and secure them in predetermined locations.
- Integration testing: Running tests to ensure the conveyor table interfaces seamlessly with other processing or packaging equipment, and making adjustments as necessary.
Maintenance Best Practices for Industrial Roller Conveyor Table
Maintaining an industrial roller conveyor table involves routine checks and preventative measures to ensure long-term operational efficiency and safety. Here are some best practices:
- Regular Inspection: Conduct periodic inspections to identify wear and tear on rollers, belts, and electrical components. Early detection of issues prevents costly downtime.
- Lubrication: Keep moving parts lubricated according to the manufacturer’s recommendations to minimize friction and prevent premature wear.
- Cleanliness: Ensure the conveyor surface and surroundings are kept clean to avoid debris accumulation that could hinder performance or damage the conveyor.
- Record Keeping: Maintain a log of maintenance activities, issues identified, and actions taken to resolve them. This documentation helps in predicting potential failures and planning preventive measures.
Safety Features and Protocols for Heavy-Duty Roller Conveyors
Safety protocols are paramount when operating an industrial roller conveyor table, especially those designed for heavy-duty applications. Employees should be trained on proper usage, emergency procedures, and the importance of personal protective equipment (PPE). Additional safety considerations include:
- Safety Guarding: Installing barriers or guards around moving parts to protect operators from pinch points and entanglements.
- Emergency Stops: Strategically placing emergency stop buttons along the conveyor line allows for immediate shutdown in case of an incident.
- Load Capacity Adherence: Respecting the specified load capacity of the conveyor prevents overloading, which can lead to equipment failure and safety risks.
- Regular Training: Ensuring all operators are adequately trained on the specific model of the conveyor, including its features and safety measures.
By prioritizing these installation, maintenance, and safety protocols, businesses can significantly enhance the performance and lifespan of their industrial roller conveyor table while maintaining a safe work environment for their employees.
FAQs about Industrial Roller Conveyor Table
A table conveyor, often referred to as a conveyor table or roller conveyor table, is a critical piece of equipment in the material handling industry. It consists of a series of rollers mounted on a frame which is designed to transport goods and materials across short or long distances within a facility. These conveyors leverage gravity or motor power to move items, providing a smooth, efficient pathway for the assembly, sorting, packaging, or inspection processes. The simplicity of their design offers versatility in application, allowing them to be used in a variety of industries including manufacturing, distribution centers, warehouses, and more. The primary advantage of table conveyors lies in their ability to facilitate the easy and safe movement of products, thereby enhancing operational efficiency, reducing manual labor, and minimizing the risk of workplace injuries.
The dimensions of conveyor rollers can vary widely to accommodate the needs of different industries and applications. However, there are some standard sizes that are commonly used within the sector. Typically, roller diameters can range from as small as 3/4 inch (about 19 mm) to as large as 8 inches (about 203 mm), with the most common sizes being between 1.9 inches (48 mm) and 3.5 inches (89 mm). The length of the rollers also varies, designed to match the width of the conveyor belt or the width of the materials being transported, and can range from a few inches to several feet. The choice of roller size is influenced by several factors including the weight and size of the items being conveyed, the type of material the roller is made from, and the specific requirements of the conveying system, such as speed and load capacity.
Conveyor rollers can be classified into several types based on their function, construction material, and the method of movement they provide. The most common types include:
Gravity Rollers: These rely on gravity to move items along the conveyor, making them most suitable for downward or inclined paths. They require no power source, making them cost-effective and easy to maintain.
Powered Rollers: Powered by motors, these rollers can move items along flat surfaces or against gravity. They are ideal for heavy loads or where controlled speeds and movement are necessary.
Grooved Rollers: Designed with grooves that can accommodate drive belts for powered conveyor systems, these rollers are used in tandem with powered rollers to move items.
Tapered Rollers: These are used in curves and corners of conveyor systems to maintain the alignment and orientation of the items being transported.
Impact Rollers: Placed at points where heavy items are loaded onto the conveyor, impact rollers are designed to absorb the shock and reduce damage to the conveyor belt.
The primary components of a roller conveyor include:
Rollers: The cylindrical elements that items glide over. They can be made from metal, plastic, or rubber, depending on the application.
Frame: Supports the rollers and provides structure to the conveyor system. Frames can be made from steel, aluminum, or other durable materials.
Bearings: Facilitate the smooth rotation of the rollers. Quality bearings are crucial for reducing friction and wear.
Drive Mechanism: In powered roller conveyors, this includes motors and gears that move the rollers. The mechanism can be chain-driven, belt-driven, or use direct-drive motors.
Control System: For automated systems, the control system regulates the speed, direction, and operation of the conveyor, often integrating with broader warehouse management or manufacturing systems.
Last Updated on June 28, 2024 by Jordan Smith
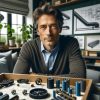
Jordan Smith, a seasoned professional with over 20 years of experience in the conveyor system industry. Jordan’s expertise lies in providing comprehensive solutions for conveyor rollers, belts, and accessories, catering to a wide range of industrial needs. From initial design and configuration to installation and meticulous troubleshooting, Jordan is adept at handling all aspects of conveyor system management. Whether you’re looking to upgrade your production line with efficient conveyor belts, require custom conveyor rollers for specific operations, or need expert advice on selecting the right conveyor accessories for your facility, Jordan is your reliable consultant. For any inquiries or assistance with conveyor system optimization, Jordan is available to share his wealth of knowledge and experience. Feel free to reach out at any time for professional guidance on all matters related to conveyor rollers, belts, and accessories.