Installation of Conveyor Belts, Tracking & Maintenance & Troubleshooting
The installation of conveyor belts is a critical task that can significantly impact the efficiency and safety of any material handling system. Proper installation ensures optimal performance, longevity, and safety of the conveyor system, making it imperative for businesses to prioritize this process. Various resources, including comprehensive PDF guides, detailed diagrams, instructional PowerPoint presentations, and in-depth installation manuals, are available to assist in this complex procedure. These resources provide valuable insights and step-by-step instructions to ensure that the conveyor belt install is conducted smoothly and effectively, adhering to industry standards and best practices. Whether you’re a seasoned professional or new to the field, leveraging these tools can make the installation process more manageable and successful.
Pre-Installation Considerations for the Installation of Conveyor Belt
Before the installation of conveyor belts begins, it’s crucial to lay the groundwork to ensure a seamless process. This phase is pivotal as it sets the stage for a successful installation, impacting the efficiency, safety, and longevity of the conveyor system.
Choosing the Right Conveyor Belt
Selecting the appropriate conveyor belt is paramount and involves considering various factors such as material, durability, speed requirements, and the nature of the items being conveyed. The right choice ensures compatibility with the system’s demands, reducing wear and tear and minimizing downtime for maintenance.
Choosing the right conveyor belt for your application involves several key considerations:
- Material Type: The material of the conveyor belt should be selected based on the type of goods it will carry. Common materials include rubber, PVC, fabric, and metal.
- Load Capacity: Consider the weight and size of the items the conveyor will handle. The belt must be able to support the load without stretching or breaking.
- Operating Environment: The environment where the conveyor will operate (temperature, humidity, exposure to chemicals) should influence the choice of belt material and design.
- Speed Requirements: The speed at which the conveyor operates must be compatible with the belt design to prevent slippage or premature wear.
- Maintenance Needs: Some belts are easier to maintain and more durable than others. Evaluate the long-term maintenance costs and ease of repair.
Selecting the right conveyor belt enhances efficiency, reduces maintenance costs, and increases the longevity of the conveyor system.
Conveyor Belt Types and Their Applications
Conveyor belts come in a myriad of types, each suited to different applications and industries. Understanding these variations is key to selecting the most appropriate belt for your needs.
Selecting Professional Conveyor Belt Installation Companies
The installation of conveyor belts is a specialized task that requires expertise and experience. Choosing a reputable installation company is critical. Look for providers with a proven track record, necessary certifications, and a commitment to safety and quality. When considering how to install a conveyor belt, professional installers not only ensure that the installation process is conducted efficiently but also provide valuable insights and recommendations to enhance the system’s performance and reliability.
The pre-installation phase is a critical step in the installation of conveyor belts, requiring careful consideration of the belt type, its application, and the selection of a skilled installation team. This foundational work is essential for a successful installation and the long-term success of the conveyor system.
Selecting a professional conveyor belt installation company involves considering several key factors:
- Experience and Expertise: Look for companies with a proven track record in installing the type of conveyor belt system you need.
- Certifications and Compliance: Ensure the company adheres to industry standards and safety regulations.
- Customer Reviews and References: Check testimonials and contact references to gauge the reliability and quality of service.
- Support and Maintenance Services: Choose companies that offer robust after-installation support and maintenance programs.
- Cost and Contract Terms: Compare quotes and understand the contract terms, ensuring they align with your project requirements and budget. Selecting a reputable and experienced provider will ensure a smooth installation and long-term operational efficiency.
Key Aspects That Need to Be Covered When Installing A Conveyor Belt
When installing a conveyor belt, there are several key aspects that need to be considered to ensure efficient operation and safety. Here’s a breakdown of the main points:
Site Preparation and Layout Planning:
- Ensure the installation site is prepared and clear of any obstacles.
- Plan the layout of the conveyor system to optimize the flow of materials and integrate with existing processes.
Foundation and Framework:
- Construct a solid foundation that can support the conveyor structure and the dynamic loads during operation.
- The framework should be aligned and leveled to prevent any misalignment, which can cause premature wear and tear.
Mechanical Installation:
- Assemble the conveyor sections according to the manufacturer’s guidelines.
- Install and align the rollers and the conveyor bed precisely to ensure smooth belt movement.
Belt Installation:
- Install the conveyor belt properly; this might involve threading the belt through the conveyor and joining the ends of the belt, typically by vulcanizing (splicing) or using mechanical fasteners.
- Ensure that the belt is tensioned correctly to prevent slippage and stretching.
Electrical and Controls Installation:
- Install and connect motors, drives, and controls. Ensure all electrical installations comply with national and local codes.
- Configure control systems, including emergency stops and interlocks for safety.
Testing and Commissioning:
- Test the conveyor system with trial runs to ensure everything operates smoothly.
- Make any necessary adjustments to the belt tension, alignment, and control settings.
Safety Measures:
- Install safety guards and barriers around moving parts.
- Clearly mark safety and emergency stop controls.
- Provide training for all operators on the safe operation of the conveyor.
Maintenance Planning:
- Establish a routine maintenance schedule to inspect the conveyor and its components.
- Keep a stock of critical spare parts to minimize downtime in case of component failure.
Addressing these aspects can help in installing a conveyor belt system that is safe, efficient, and durable, reducing potential downtime and maintenance costs over its operational life.
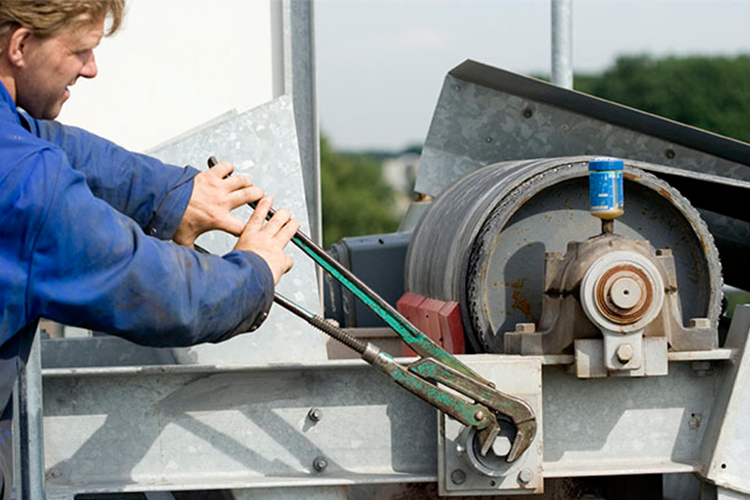
The Detailed Conveyor Belt Installation Process
The conveyor belt installation involves a meticulous process that ensures the system’s efficiency, safety, and longevity. Each step, from preparation to tensioning and tracking, requires careful attention to detail. Conveyor belt installers play a crucial role in this process, using their expertise to handle the complexities of installation, ensuring every component is precisely aligned and functioning optimally. Their skills are essential in preparing the site, installing the belt, and performing necessary adjustments to achieve proper tension and alignment, ultimately contributing to the conveyor system’s overall performance and reliability.
Step 1: Preparation for Installation of Conveyor Belt
Before the actual installation begins, several preparatory steps must be taken to ensure a smooth process:
- Storing the Replacement Belt: It’s crucial to store the new conveyor belt in a way that prevents conveyor belt damage. Keep it in a cool, dry place, away from direct sunlight and chemicals, to maintain its integrity.
- Transporting the Conveyor Belt: Transporting the belt to the installation site with care is essential to avoid any damage. Use appropriate lifting equipment and techniques to handle the belt’s weight and size.
- Tools and Equipment: Gather all necessary tools and equipment beforehand. This includes safety gear, cutting tools, fastening devices, and any manufacturer-specific tools for installation.
Step 2: Removal of the Old Belt
Removing the old belt is a critical step that must be done with caution:
- Safety Precautions and Procedures: Follow strict safety guidelines to protect all personnel involved in the removal process. Lockout and tagout procedures should be in place to prevent accidental startup of the conveyor system.
- Unlacing and Cutting the Old Belt: Carefully unlacing and cutting the old belt ensures that it can be removed without causing damage to the conveyor structure. This step should be done methodically to preserve the integrity of the conveyor frame and rollers.
Step 3: Installing the New Belt
The core of the installation process is putting the new belt in place:
- Positioning the Belt Roll: Position the roll so that the belt unwinds in the correct orientation, considering the top and bottom surfaces. This ensures that the carrying side of the belt is correctly placed.
- Mounting the Belt Roll: Depending on the site’s specifics, the belt roll might need to be mounted on a shaft or handled differently if space is limited. Ensure the roll is secure and stable before unrolling the belt.
- Threading the Belt: Carefully thread the belt onto the conveyor system, ensuring it passes over the correct rollers and pulleys. This step might require multiple personnel to guide the belt into place and prevent it from twisting or catching.
Step 4: Tensioning and Tracking
The final steps involve adjusting the belt for optimal operation:
- Adjusting Belt Tension: Proper tension is crucial for belt performance. Adjust the tension so that the belt operates smoothly without slipping or stretching. Follow the manufacturer’s guidelines to set the correct tension.
- Lacing the New Belt and Tracking Alignment: Once the belt is tensioned, lace it to secure the ends together. Then, begin the tracking process to ensure the belt runs centrally along the conveyor structure. Adjustments may be needed to the idlers and pulleys to achieve proper alignment.
The installation of conveyor belts is a complex process that requires precision and attention to detail. Following these steps ensures that the conveyor system operates efficiently and safely, extending the lifespan of the belt and minimizing downtime for maintenance.
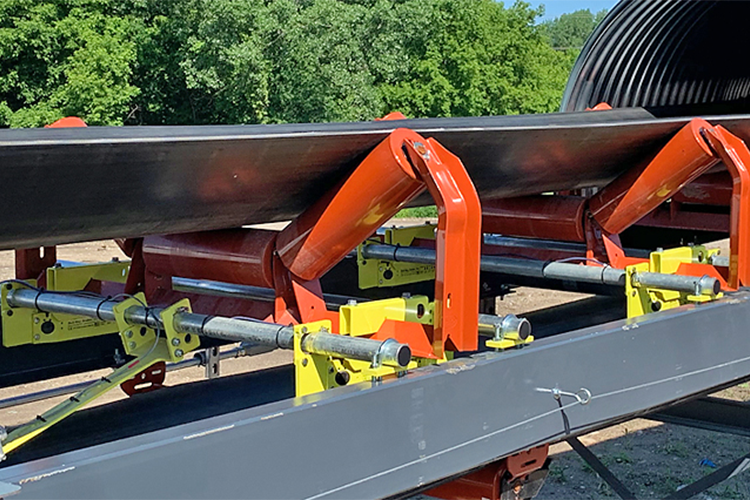
Installation With Pre-flaking of New Belt
Pre-flaking of a new conveyor belt refers to the process of preparing the belt before installation by applying a special coating or treatment to its surface. Here’s a detailed explanation of the installation process with pre-flaking of a new belt:
Preparation:
- Assessment: Evaluate the installation site and ensure it’s clean, dry, and free from debris.
- Belt Inspection: Examine the new conveyor belt for any defects or damage before pre-flaking.
Surface Treatment:
- Flaking: Apply a pre-flaking compound or coating to the belt surface. This compound is designed to enhance adhesion between the belt and the conveyor components.
- Uniform Application: Ensure the pre-flaking compound is evenly distributed across the entire belt surface to promote consistent adhesion.
Installation:
- Alignment: Align the conveyor components, including rollers, pulleys, and frames, according to the manufacturer’s specifications.
- Belt Placement: Carefully position the pre-flaked belt onto the conveyor structure, ensuring it is properly centered and tensioned.
- Joining: If the conveyor belt requires joining, use the appropriate method such as vulcanization or mechanical fasteners to create a secure splice.
Tensioning and Tracking:
- Tension Adjustment: Adjust the tension of the conveyor belt to the manufacturer’s recommended specifications to prevent slippage or stretching.
- Tracking: Ensure the belt tracks correctly on the conveyor system to prevent lateral movement and reduce wear on the belt edges.
Testing and Commissioning:
- Trial Run: Conduct a trial run of the conveyor system to ensure smooth operation and proper alignment.
- Adjustments: Make any necessary adjustments to the belt tension, tracking, and alignment based on the trial run results.
Pre-flaking of a new conveyor belt is an important step in the installation process as it helps to improve the adhesion between the belt and the conveyor components, resulting in better performance and longevity of the system.
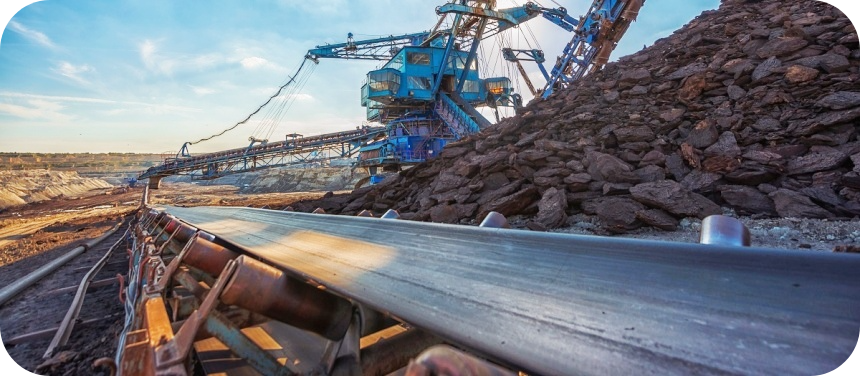
Ensuring Success After the Installation of Conveyor Belt
Following the installation of conveyor belts, the focus shifts to maintaining the system’s integrity and efficiency through diligent post-installation practices. This phase is crucial for maximizing the lifespan of the conveyor belt and ensuring the safety of operations.
Maintenance and Safety
Conveyor belt installation and maintenance jobs encompass a range of responsibilities essential for the smooth operation of conveyor systems. Here’s a detailed overview:
Maintenance Duties:
- Regular Inspections: Checking for wear and tear, misalignment, or other issues.
- Lubrication: Regularly applying lubricants to moving parts to reduce friction and prevent breakdowns.
- Repairs: Fixing or replacing damaged parts promptly to avoid downtime.
- Cleaning: Keeping the conveyor clean to prevent material build-up that can affect functionality.
Safety and Compliance:
- Safety Protocols: Adhering to safety standards to protect workers from machinery-related injuries.
- Record Keeping: Maintaining logs of maintenance activities and safety checks for compliance with industry regulations.
Professionals in this field need a blend of technical skills and attention to detail, as the efficiency of the conveyor greatly depends on the precision of installation and thoroughness of maintenance.
Troubleshooting Common Issues
Even with meticulous installation and maintenance, conveyor belts can encounter issues. Addressing common problems promptly can prevent more significant complications:
- Belt Slippage: Check tension and adjust as necessary. Inspect pulleys for wear and clean them to improve grip.
- Misalignment: Ensure the belt is correctly aligned on the pulleys and idlers. Adjust tracking if the belt drifts to one side.
- Blockages: Regularly inspect the belt and the conveyor path for debris that could cause blockages.
- Wear and Tear: Inspect the conveyor belt for signs of excessive wear, and replace sections as needed.
- Motor Issues: Listen for unusual noises or signs of strain in the conveyor motor, which could indicate a problem.
- Electrical Problems: Check electrical connections and controls for signs of wear or damage.
- Joint Failure: Inspect conveyor belt joints for signs of weakness or failure, and repair or replace as necessary.
- Roller and Idler Problems: Check for stuck or damaged rollers and idlers, and lubricate or replace them as needed.
- Material Spillage: Adjust skirts and scrapers to prevent material from spilling off the belt.
- Temperature Issues: For belts used in high or low-temperature environments, regularly check for material brittleness or softening.
When these issues exceed the scope of routine maintenance, or if the problem persists despite troubleshooting efforts, it’s time to call in professional maintenance services. Experts in conveyor belt systems can provide specialized knowledge and skills to address complex issues, ensuring the longevity and efficiency of the conveyor belt post-installation.
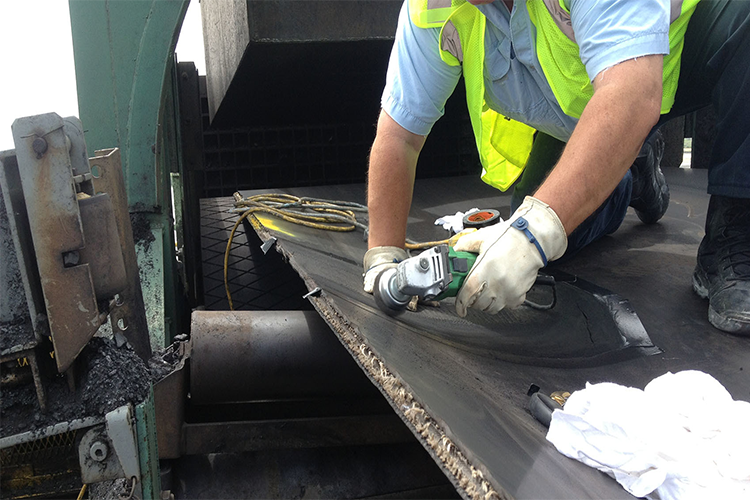
Further Reading for the Installation of Conveyor Belt
Selecting Reputable Conveyor Belt Installation and Maintenance Companies
When the need arises for professional assistance, choosing the right company is crucial. Consider the following factors to ensure you select a reputable service provider:
- Experience and Expertise: Look for companies with a proven track record in the conveyor belt industry. Their experience can be a significant asset in addressing complex challenges.
- Certifications and Qualifications: Reputable companies often hold certifications that validate their expertise and adherence to industry standards.
- Customer Reviews and Testimonials: Feedback from previous clients can provide valuable insights into the company’s reliability and quality of service.
- After-Sales Support: A company that offers robust after-sales support demonstrates a commitment to customer satisfaction and long-term service.
By carefully selecting service providers, you can ensure the long-term success and efficiency of your conveyor belt system. Whether you’re looking to deepen your knowledge or require professional assistance, the right resources and partners can make all the difference in the maintenance and operation of your conveyor belt post-installation.
Reputable Conveyor Belt Installation And Maintenance Company
- Gottstein Corporation
Gottstein Corporation provides comprehensive industrial services across North America, specializing in conveyor installations for various industries. They offer a wide range of conveyor types, including auger, belt, and cable conveyors, constructed from materials like stainless steel and aluminum. Gottstein Corporation excels in system integration, engineering services, and emergency on-site visits. Their expertise spans multiple industries, including food processing, agriculture, and chemical manufacturing, ensuring tailored solutions for each client’s needs. - Belt Tech, Inc.
Belt Tech, Inc. is renowned for its expertise in conveyor belt design, installation, repair, and maintenance. The company prides itself on delivering timely and reliable services to keep businesses operational. Belt Tech handles everything from emergency repairs to routine maintenance, ensuring conveyor systems are efficient and durable. Their services are particularly beneficial for industries requiring rapid response times and high-quality installations. - Ashworth Conveyor Belts
Ashworth is a global leader in the conveyor belt industry, offering installation, maintenance, refurbishment, and optimization services. Their holistic approach ensures conveyor systems operate at peak performance. Ashworth’s team provides on-site installation, system audits, and proactive maintenance programs to prevent costly downtime and enhance productivity. Their commitment to innovation and customer service has made them a trusted partner for companies worldwide. - Nationwide Belting Sales & Services
Nationwide Belting offers extensive conveyor belt services, including inspections, adjustments, and emergency repairs. With over 20 years of experience, their team is equipped to handle both minor and major conveyor issues, ensuring optimal performance. They provide nationwide services, ensuring that businesses across the U.S. can access their expertise. Safety and efficiency are top priorities, with MSHA and OSHA-certified technicians available 24/7. - MIR Inc.
MIR Inc. provides 24/7 conveyor belt repair and replacement services. Their team of trained technicians ensures minimal downtime by quickly addressing belt damage or breakdowns. MIR’s services include vulcanization, metal fasteners, and cold curing for temporary fixes. They also offer in-house custom fabrication to meet unique client needs, along with training seminars to help facility teams manage their conveyor systems effectively. - Viacore
Viacore specializes in proactive maintenance programs to enhance conveyor belt longevity and system performance. With over 30 locations across North America, they offer quick response times for repairs and installations. Viacore’s services include comprehensive system audits, emergency repairs, and customized maintenance plans to reduce downtime and improve productivity. Their expertise covers a wide range of industries, including mining, agriculture, and food processing. - Velocity Conveyor
Velocity Conveyor focuses on mechanical conveyor installations and maintenance, particularly for Hytrol conveyors. They offer turnkey services, including permits and inspections, ensuring compliance with safety regulations. Velocity Conveyor also installs hydraulic and pneumatic systems, providing a complete solution for material handling needs. Their team’s experience and certification make them a reliable partner for various installation projects. - Dorner Conveyors
Dorner provides installation and maintenance services for a variety of conveyor systems, including belt-over-belt and bottomless conveyors. Their preventative maintenance programs help avoid safety concerns and emergency repairs, keeping production lines running smoothly. Dorner’s expertise in custom-engineered solutions makes them a go-to for complex material handling challenges, serving industries like food handling and pharmaceuticals. - W.W. Cannon
W.W. Cannon offers comprehensive conveyor system repair and maintenance services. Their factory-trained technicians provide emergency repairs, routine maintenance, and system inspections to prevent breakdowns. W.W. Cannon’s services include belt tensioning, tracking adjustments, and splice repairs. They maintain a stock of essential parts to ensure quick resolutions and minimize downtime for their clients. - Flexco
Flexco is known for its high-quality conveyor belt maintenance and repair tools. Their services include belt tracking, tensioning, and splicing, ensuring safe and efficient conveyor operation. Flexco’s preventative maintenance programs help identify potential issues before they cause significant downtime. Their tools and expertise make them a trusted partner for industries requiring reliable conveyor system performance.
These companies are equipped to handle various conveyor belt needs, from installation and maintenance to emergency repairs and custom solutions, ensuring optimal performance and minimal downtime for their clients.
Upgrade your operations with our high-quality, durable conveyor belts.
FAQs about Installation of Conveyor Belt
Installing a conveyor system involves several key steps, starting from the design and layout planning to the actual assembly and testing of the system. Initially, it’s crucial to assess the operational needs, including the type of materials to be conveyed, the required speed, and the environmental conditions. Based on these assessments, a layout plan is created, detailing the path of the conveyor and the location of key components like drives, idlers, and turns.
The installation process begins with the construction of the conveyor frame. This structure must be level and aligned to ensure smooth operation. Once the frame is in place, the drive and idler rollers are installed. The drive unit, which powers the conveyor, is positioned at one end, while idler rollers, which support the belt, are spaced along the frame.
Electrical wiring and controls are then set up to manage the operation of the conveyor. This includes the installation of emergency stop systems, sensors, and control panels. After the mechanical and electrical components are installed, the conveyor belt is threaded onto the system. This step requires careful handling to avoid damage to the belt and ensure it is aligned correctly.
Finally, the system is tested to verify that all components are functioning correctly. This includes running the conveyor belt through its full range of operations to check for proper belt tension, alignment, and smooth operation of rollers and drives. Adjustments are made as necessary to optimize performance. Safety checks are also conducted to ensure that all safety features are operational.
Attaching a conveyor belt to a conveyor system is a critical step that requires precision and attention to detail. The process begins with the preparation of the belt ends. The ends must be cut straight and squared to ensure a proper joint. Depending on the type of belt and the application, different methods can be used to attach the belt ends. These methods include:
Mechanical Fastening: This involves the use of metal or plastic fasteners to join the belt ends. The fasteners are installed using a special tool that ensures they are evenly spaced and securely attached. This method is quick and allows for easy belt removal for maintenance or replacement.
Vulcanization: This is a more permanent method where the belt ends are spliced together using heat and pressure. The process involves applying a layer of uncured rubber to the belt ends, then heating them in a vulcanizing press. This creates a strong, seamless joint that is ideal for high-strength applications.
Cold Bonding: Similar to vulcanization, cold bonding uses adhesives to join the belt ends. The surfaces are prepared, adhesive is applied, and the ends are pressed together until the adhesive cures. This method is suitable for applications where heat cannot be used.
Regardless of the method used, it’s essential to ensure that the belt is tensioned correctly after attachment. This involves adjusting the conveyor’s take-up unit to apply the right amount of tension to the belt, preventing slippage and ensuring smooth operation.
Replacing a conveyor belt is a necessary maintenance task that ensures the efficiency and longevity of a conveyor system. The process involves several key steps:
Preparation: Before removing the old belt, ensure that the conveyor system is turned off and locked out to prevent accidental startup. Gather all necessary tools and equipment for the belt replacement.
Removal of the Old Belt: The old belt is detached from the conveyor by removing the mechanical fasteners or cutting the vulcanized splice. Care must be taken to avoid damaging the conveyor frame or rollers during this process.
Installation of the New Belt: The new belt is positioned around the conveyor system. If the system is long, the belt may need to be fed through the conveyor in sections. The belt ends are then prepared for joining, either by squaring them for mechanical fasteners or preparing them for vulcanization or cold bonding.
Joining the Belt Ends: The chosen method for attaching the belt ends is carried out. This could involve installing mechanical fasteners, vulcanizing, or cold bonding the ends together.
Tensioning the Belt: After the belt is joined, it’s tensioned to the manufacturer’s specifications. This is done by adjusting the take-up unit to apply the correct tension, ensuring optimal performance and preventing slippage.
Testing: The conveyor system is tested to ensure that the new belt is installed correctly. This includes checking for proper alignment, smooth operation, and correct tension. Adjustments are made as necessary to ensure the system operates efficiently.
Safety Checks: Finally, safety checks are conducted to ensure that all safety features of the conveyor system are functional and that the system is safe to operate.
Conveyor belts can be joined using several methods, each suited to different types of belts and operational requirements. The three primary methods are mechanical fastening, vulcanization, and cold bonding.
Mechanical Fastening: This method uses metal or plastic fasteners to join the belt ends. It’s a versatile and reversible method that allows for easy belt removal and is suitable for temporary or low-tension applications.
Vulcanization: Vulcanization creates a seamless and durable joint by splicing the belt ends together using heat and pressure. This method is ideal for high-tension applications and provides a smooth, uniform surface that minimizes the risk of belt snagging or catching on conveyor components.
Cold Bonding: Cold bonding uses adhesives to join the belt ends. This method is suitable for applications where vulcanization is not feasible. It provides a strong bond but requires precise surface preparation and curing time.
Last Updated on June 6, 2024 by Jordan Smith
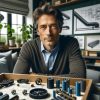
Jordan Smith, a seasoned professional with over 20 years of experience in the conveyor system industry. Jordan’s expertise lies in providing comprehensive solutions for conveyor rollers, belts, and accessories, catering to a wide range of industrial needs. From initial design and configuration to installation and meticulous troubleshooting, Jordan is adept at handling all aspects of conveyor system management. Whether you’re looking to upgrade your production line with efficient conveyor belts, require custom conveyor rollers for specific operations, or need expert advice on selecting the right conveyor accessories for your facility, Jordan is your reliable consultant. For any inquiries or assistance with conveyor system optimization, Jordan is available to share his wealth of knowledge and experience. Feel free to reach out at any time for professional guidance on all matters related to conveyor rollers, belts, and accessories.