Interroll Conveyor Rollers: Industry-Leading Quality
In the realm of material handling and logistics, Interroll stands out as a beacon of innovation and reliability, renowned for their comprehensive range of conveyor system solutions. At the heart of these solutions are the interroll conveyor rollers, a testament to the company’s commitment to quality, efficiency, and versatility. These rollers are integral to the seamless operation of conveyor systems across a multitude of industries, including food & beverage, warehousing, distribution, and the rapidly growing e-commerce sector. The significance of dependable conveyor components cannot be overstated, as they directly impact the efficiency of supply chains and the overall productivity of businesses. Interroll’s expertise and extensive product portfolio ensure that regardless of the specific requirements or challenges of an industry, there is always a high-quality, durable solution available to keep operations running smoothly and efficiently.
The Core of Interroll: Conveyor Rollers
Interroll’s prowess in the world of material handling is perhaps best exemplified through their flagship offering – the interroll conveyor rollers. These rollers are the backbone of countless conveyor systems worldwide, serving a wide array of industries with unmatched reliability and efficiency. Interroll’s catalog is distinguished by the depth and variety of its roller series, including but not limited to the Series 1100, 1200, 1700, and 3500. Each series is designed to meet specific operational needs, from lightweight applications to heavy-duty requirements, ensuring that every business can find the perfect fit for its conveyor system.
Among these, the 1700 series stands out for its exceptional versatility and widespread application. The interroll conveyor rollers from this series are engineered to accommodate a broad range of weights and speeds, making them suitable for a vast spectrum of environments – from the delicate handling of fragile goods in the food and beverage industry to the rigorous demands of distribution and e-commerce warehouses. The 1700 series exemplifies Interroll’s commitment to innovation, with features designed to enhance durability, reduce maintenance requirements, and increase energy efficiency.
The hallmark of Interroll’s design philosophy is the seamless integration of these rollers into existing systems, allowing for upgrades and expansions without the need for complete overhauls. This adaptability, coupled with the company’s rigorous testing and quality assurance processes, ensures that interroll conveyor rollers remain at the forefront of the industry, providing solutions that are not just effective but also sustainable and forward-thinking.
Innovative Solutions with Interroll Conveyor Rollers
In the dynamic landscape of conveyor technology, Interroll has consistently paved the way with its groundbreaking solutions, particularly in the domain of interroll conveyor rollers. Their innovative approach is not limited to the rollers themselves but extends to a comprehensive suite of products designed to enhance the efficiency, reliability, and flexibility of conveyor systems. Among these innovations, eight standout solutions reflect Interroll’s commitment to advancing conveyor technology:
- RollerDrive is a cornerstone of Interroll’s innovative offerings, providing a decentralized drive system that allows individual conveyor segments to be powered on demand. This not only reduces energy consumption but also enhances system efficiency and flexibility. The RollerDrive is particularly beneficial in sortation, distribution, and packaging lines, where precise control and variable speeds are essential.
- EC5000 Roller Drives offer an advanced level of energy efficiency and operational reliability. Designed for versatile applications, these drives are suitable for both light and heavy-duty conveyance, showcasing Interroll’s dedication to catering to a broad range of industry needs.
- The Modular Conveyor Platform (MCP) exemplifies how interroll conveyor rollers integrate seamlessly into comprehensive system solutions. MCP provides unmatched versatility and scalability, allowing businesses to adapt their conveyor systems to changing operational needs with minimal downtime.
- Dynamic Storage Solutions leverage the efficiency of Interroll’s rollers to optimize warehouse storage and retrieval processes. These solutions include pallet flow and carton flow systems, which significantly enhance the throughput and space utilization in warehousing operations.
- PolyVee Belts and belt drives complement Interroll’s rollers by providing a quiet, maintenance-free operation. They are ideal for sectors where noise reduction and low maintenance are critical.
- MultiControl is a smart, networked control solution for RollerDrive systems, enabling easy integration into existing warehouse management systems. This IoT-enabled device simplifies the setup and maintenance of conveyor systems, enhancing operational transparency and control.
- Drum Motors are designed for belt conveyors and provide a compact, efficient drive alternative. Interroll’s drum motors are known for their reliability, durability, and energy efficiency, making them a preferred choice for food processing, packaging lines, and intralogistics applications.
- Accessories and Components such as sensors, controllers, and power supplies are meticulously designed to complement the interroll conveyor rollers and drives, ensuring a holistic, high-performance conveyor system.
Interroll provides detailed documentation, including the RollerDrive manual, which offers comprehensive installation and maintenance guidance. This ensures that customers not only receive cutting-edge products but also the knowledge and support necessary to optimize their conveyor systems. Through these innovative solutions, Interroll demonstrates its unwavering commitment to pushing the boundaries of conveyor technology, offering scalable, energy-efficient, and reliable solutions that cater to the evolving needs of industries worldwide.
Interroll Conveyor Rollers: Customization and Technical Details
Understanding the customization and technical details of Interroll conveyor rollers is crucial to leveraging their full potential. These allow for tailored solutions to meet the specific needs of various industrial applications. With numerous options for technical customization, you can optimize Interroll conveyor rollers for your unique operational requirements.
Technical Customization Options
Interroll provides many technical customization options for its conveyor rollers. These include various endcap drive types such as ‘B – Both sides’ and ‘L – Left side’, catering to diverse layout requirements of conveyor systems. Further, Interroll conveyor rollers offer different roller materials, including polyvinyl chloride (PVC), stainless steel, and zinc-plated variants, ensuring suitability across varied environmental and operational conditions.
Moreover, a range of roller specifications like the outer diameter, wall thickness, and antistatic types ensures versatility across different application scenarios. By understanding these options, businesses can customize the Interroll conveyor rollers to their specific needs facilitating better performance and utility.
Significance of CAD Downloads
Besides customization options, Interroll also provides CAD downloads for their conveyor rollers. The provision of CAD downloads holds many advantages for businesses considering the implementation of Interroll conveyor rollers:
- Precision: CAD files provide accurate dimensions and details of the rollers, ensuring precision in planning.
- Compatibility: They can be seamlessly integrated into your existing CAD models.
- Customization: CAD downloads allow for easy customization, as per the size and layout specifications of your conveyor system.
- Efficiency: They streamline the planning and design process, therefore reducing project timelines.
- Resource Management: They allow for better resource allocation by providing estimates on material requirements and space utilization.
- Cost Estimation: They aid in accurate cost estimation and budget planning for the conveyor system installation.
- Visualization: They help visualize how the Interroll conveyor rollers will fit into your system.
- Simulation: They can be used to simulate conveyor system operations, which can help pinpoint potential issues before they happen.
- Collaboration: They facilitate better communication and collaboration between various teams involved in the project.
- Documentation: They serve as comprehensive technical documents for archive purposes and future references.
By utilizing CAD downloads and an array of technical customization options, businesses can tailor the Interroll conveyor rollers to suit their specific application needs. This encompasses not only their physical configuration but also the compatibility with the planning and implementation phases, ensuring optimal usage and function of the conveyor system.
Enhancing Operations with Interroll Conveyor Rollers Parts and Accessories
The efficiency and functionality of conveyor systems significantly depend not only on the core components but also on the quality and compatibility of their auxiliary parts and accessories. Interroll conveyor rollers, renowned for their reliability and performance, are complemented by a range of additional parts and accessories designed to enhance operation and provide comprehensive conveyor solutions.
Additional Parts and Accessories that Complement the Rollers
Interroll’s suite of products includes nine essential parts and accessories that seamlessly integrate with Interroll conveyor rollers, each designed to address specific operational needs:
- PolyVee Belt: This versatile drive solution ensures reliable power transmission. Its design maximizes engagement while minimizing wear and tear, improving the efficiency of powered roller conveyors.
- MultiControl for Controls: A smart, programmable control unit capable of managing up to four Interroll conveyor rollers simultaneously. It simplifies the integration of conveyor components into automated systems, offering precise control and monitoring of roller behavior.
- Drum Motors: These provide a compact and efficient drive system by integrating the motor inside the drum. Ideal for belt conveyors, they minimize space requirements and improve safety by eliminating external moving parts.
- RollerDrive: A compact motor integrated within the roller, offering a decentralized drive solution for modular conveyors. Its energy efficiency and simple control make it ideal for segments requiring variable speeds.
- Friction Wheels: Utilized in driving pallet conveyors, these wheels ensure a smooth and controlled transfer, optimizing the handling of heavy loads.
- Conveyor Stands and Mounts: High-quality supports that provide stability and adjustability to conveyor systems, accommodating various layouts and operational conditions.
- Sensor Rollers: Equipped with integrated sensors, these rollers monitor conveyor conditions in real-time, facilitating preventative maintenance and reducing downtime.
- Speed Controllers: Essential for gravity conveyors, they regulate the speed of goods to ensure safe and consistent movement.
- Side Guides and Rails: These parts enhance the guidance and control of products on the conveyor, ensuring efficient alignment and preventing spillage.
Availability of Replacement Parts
The availability of replacement parts and their critical importance cannot be overstated in maintaining the efficiency and longevity of conveyor systems. The following aspects highlight their significance:
- Minimizing Downtime: Quick access to replacement parts ensures rapid repairs, significantly reducing system downtime.
- Maintaining Performance: Regular replacement of worn or damaged parts keeps Interroll conveyor rollers running at optimum efficiency.
- Safety: Ensuring all components are in good working order decreases the risk of accidents and injuries.
- Cost-Effectiveness: Proactive maintenance and parts replacement can prevent costlier breakdowns and repairs in the future.
- Upgradability: With access to a wide range of parts and accessories, Interroll conveyor rollers can be easily upgraded or modified to meet evolving operational needs.
- Consistency: Genuine Interroll parts guarantee compatibility and performance, unlike generic components.
- Innovation: Leveraging advanced parts and accessories supports incorporation of new technologies into existing systems.
- Flexibility: A broad selection of parts enables tailor-fit solutions for unique application requirements.
- Compliance: Ensures the system meets industry standards and regulations.
- Sustainability: Efficient operation and reduced need for complete system replacements lower environmental impact.
By complementing Interroll conveyor rollers with specifically designed parts and accessories, businesses can significantly enhance the performance, reliability, and flexibility of their conveyor systems, ensuring they not only meet current operational demands but are also poised for future challenges and opportunities.
Interroll’s Global Reach: Distributors and Support for Interroll Conveyor Rollers
The global presence of Interroll conveyor rollers is supported by an extensive network of distributors and comprehensive support services that span the entire lifecycle of their products. This international footprint ensures that wherever your operations are located, access to high-quality Interroll conveyor rollers, parts, and expert assistance is never far away.
How to Find Interroll Distributors
Finding an Interroll distributor is streamlined and user-friendly, reflecting the company’s commitment to not just excellence in manufacturing but also in customer service and support. Here are key insights on how businesses can easily connect with Interroll’s extensive distributor network for their conveyor roller needs:
- Interroll Website: The official Interroll website features a ‘Distributor Locator’ tool, enabling customers to find authorized distributors by country or region. This tool is regularly updated to reflect the most current information.
- Regional Sales Offices: Interroll operates sales offices across different continents, including Europe, Asia, North America, and South America. These offices can directly guide you to local distributors of Interroll conveyor rollers.
- Industry Events and Tradeshows: Interroll often participates in major industry tradeshows worldwide, providing an excellent opportunity to connect with the Interroll team and learn more about finding distributors in your area.
- Direct Inquiry: For businesses unable to locate a distributor through other means, making a direct inquiry to Interroll’s customer service is highly encouraged. They offer multilingual support to aid international customers effectively.
Comprehensive Support Provided by Interroll
Alongside facilitating easy access to their products worldwide, Interroll provides comprehensive support that accompanies their Interroll conveyor rollers from the planning stage all the way through to implementation and maintenance. This support includes:
- Project Planning Assistance: Expert consultation to help select the right conveyor rollers and accessories for specific applications, emphasizing efficiency and sustainability.
- Technical Support: Access to experienced technical support teams for help with product specifications, installation guidance, troubleshooting, and optimization.
- Training and Education: Offering training sessions and materials to ensure customers and end-users can maximize the utility and longevity of their Interroll conveyor rollers.
- Maintenance and After-sales Service: Detailed maintenance guides and responsive after-sales service to ensure the rollers continue to operate efficiently over their lifespan.
- Innovation Sharing: Keeping clients informed about the latest developments and innovations in conveyor technology to help them stay ahead of the curve in logistics and material handling.
The essence of Interroll’s global reach is not just in making their Interroll conveyor rollers accessible worldwide but also in ensuring that wherever these products go, they are backed by unparalleled support and a wealth of expertise. This approach not only fortifies Interroll’s position as a leader in the conveyor industry but also enriches the operational capabilities of businesses across the globe.
FAQs about Interroll Conveyor Rollers
Conveyor rollers come in various designs, each tailored to serve specific functions within a conveyor system. The primary types include:
Gravity Rollers: These are the basic rollers which rely on gravity to move products along the conveyor. They are typically used in manual loading or unloading scenarios.
Driven Rollers: Connected to an external power source, driven rollers propel the conveyor belt and the material on it with ease, making them suitable for automated handling systems.
Grooved Rollers: They feature grooves that are meant for lineshafts or belts and are used in conjunction with other rollers to drive the conveyor.
Tapered Rollers: Ideal for bends or curves in conveyor systems, tapered rollers facilitate changes in direction by maintaining the alignment of the materials being transported.
Impact Rollers: Positioned at locations where items are loaded onto the conveyor, impact rollers absorb the shock and vibration, preventing damage to the conveyor itself.
Live Rollers: These are powered rollers that can be controlled to start and stop as needed and are often part of more complex materials handling setups.
Each of these roller types can be crafted from different materials such as metal, plastic, or rubber, depending on the application needs.
The formula for a conveyor roller refers to the calculations used to determine the dimensions and specifications of the rollers for them to function effectively within a conveyor system. The most fundamental and commonly used formulas pertain to the roller’s length, diameter, and the load they must support.
For example, to calculate the roller’s length, typically, you would take the width of the conveyor belt and add a specified clearance on each side, usually around 1/4 inch (6mm). The diameter of the rollers is often determined based on the size of the product, the capacity required, and the type of material being handled.
A general formula for roller capacity in lbs (C) is:
[ C = (3.1416 x (D/2)^2) x W x F ]
Where:
D is the diameter of the roller in inches
W is the weight of the product in pounds per cubic foot
F is the factor of safety (usually around 1.5-3)
These calculations must also take into account the maximum load per roller and the speed at which the conveyor will operate.
The spacing of conveyor rollers, also known as roller pitch, is a critical aspect of conveyor design and affects the overall performance and efficiency of the conveyor system. The proper roller spacing is typically determined based on the size of the load – the objects being transported on the conveyor.
As a general rule, at least three rollers should be under the product at any given time. The roller pitch can be calculated by dividing the length of the product being conveyed by three. For example, if you have a product that is 1200mm long, your maximum roller pitch would be 1200/3 = 400mm.
However, the precise spacing often depends on the product’s weight, shape, and bottom surface condition. Heavier items require closer spacing to ensure they’re adequately supported. Conversely, lightweight items can be conveyed with rollers spaced further apart, but the compromise might be on control and stability.
Remember that inadequate spacing may lead to unnecessary pressure on the conveyor rollers, potential damage to the conveyed products, and increased wear on the equipment.
Guide rollers for conveyor belts are specialized rollers designed to keep the conveyor belt properly aligned and on track. They are crucial for the long-term functionality of belt conveyors as they prevent the belts from drifting sideways, which could lead to uneven wear, belt damage, or spilling of materials.
Located on the sides of the conveyor system, guide rollers are typically positioned along the edges of the belt or where the belt may change direction. These rollers spin freely and act as guardrails to direct the belt’s motion. Importantly, while they do not drive the belt, their role in maintaining the belt’s path is essential to ensuring operational efficiency and reducing maintenance requirements.
The specifications of guide rollers, such as size, material, and spacing, can vary depending on the belt width, speed, load requirements, and environmental conditions of the conveyor system.
Last Updated on May 23, 2024 by Jordan Smith
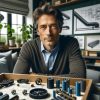
Jordan Smith, a seasoned professional with over 20 years of experience in the conveyor system industry. Jordan’s expertise lies in providing comprehensive solutions for conveyor rollers, belts, and accessories, catering to a wide range of industrial needs. From initial design and configuration to installation and meticulous troubleshooting, Jordan is adept at handling all aspects of conveyor system management. Whether you’re looking to upgrade your production line with efficient conveyor belts, require custom conveyor rollers for specific operations, or need expert advice on selecting the right conveyor accessories for your facility, Jordan is your reliable consultant. For any inquiries or assistance with conveyor system optimization, Jordan is available to share his wealth of knowledge and experience. Feel free to reach out at any time for professional guidance on all matters related to conveyor rollers, belts, and accessories.