Enhancing Conveyor Systems with Interroll Powered Rollers
Interroll stands at the forefront of the material handling industry, renowned for its pioneering approach to developing Interroll powered rollers. These advanced solutions are integral to modern conveyor systems, driving efficiency and reliability to new heights. As a global leader, Interroll’s commitment to innovation is evident in their range of powered rollers, designed to meet the dynamic needs of industries ranging from e-commerce and logistics to manufacturing and distribution. The introduction of Interroll powered rollers has revolutionized the way goods are transported within facilities, offering unparalleled control and flexibility. Their impact extends beyond mere transportation, enhancing operational workflows and contributing significantly to the optimization of material handling processes. Interroll’s powered rollers embody the synergy of performance, durability, and innovation, setting the standard for conveyor system components worldwide.
Interroll Roller Drive and Drum Motor Solutions in Interroll Powered Rollers
The realm of Interroll powered rollers is significantly enhanced by the company’s Roller Drive and Drum Motor solutions, each engineered to provide seamless, efficient operation in conveyor systems. These components are pivotal in transforming traditional conveyor setups into highly dynamic, automated systems.
Interroll Roller Drive Manual and Its Guidance
The “Interroll Roller Drive Manual” is a testament to Interroll’s commitment to supporting their clients through every step of the integration process of their powered rollers. This manual offers:
- Detailed Installation Instructions: Ensuring that the Interroll powered rollers are set up correctly to function at their peak from the get-go.
- Operational Guidelines: Providing users with the knowledge to utilize the full potential of the roller drive systems, optimizing conveyor performance.
- Maintenance Protocols: Outlining preventive maintenance schedules and procedures to prolong the life of the Interroll powered rollers and maintain consistent efficiency.
- Troubleshooting Tips: Offering solutions to common issues, enabling quick resolution and minimal downtime.
- Safety Precautions: Highlighting safety practices to protect both the equipment and the operators, ensuring a safe working environment.
Interroll Drum Motor Features and Benefits
Interroll’s drum motors stand out for their integration into belt conveyors and conveyor systems, offering a compact, efficient drive solution. Key features and benefits include:
- Space-Saving Design: The drum motor’s integration within the conveyor belt’s roller eliminates the need for external drive mechanisms, freeing up valuable space within the conveyor system.
- High Efficiency: Interroll powered rollers with drum motors are designed for optimal energy use, reducing operational costs and environmental impact.
- Low Maintenance: The enclosed design of the drum motor protects its internal components, resulting in lower maintenance needs and longer service life.
- Easy Integration: These drum motors are engineered for compatibility, ensuring they can be easily incorporated into existing or new conveyor systems without extensive modifications.
- Versatility: Suitable for a wide range of applications, from light-duty packaging lines to heavy-duty material handling systems, Interroll’s drum motors provide reliable performance across various industries.
Interroll’s Roller Drive and Drum Motor solutions exemplify the company’s innovative approach to material handling, offering robust, efficient, and user-friendly components. These solutions are integral to the functionality and success of Interroll powered rollers, driving the evolution of conveyor systems in diverse industrial landscapes.
The Versatility of Interroll Drive Rollers in Interroll Powered Rollers
The “Interroll powered rollers” are a testament to the versatility and adaptability that Interroll’s drive rollers bring to the material handling industry. These components are engineered to meet the diverse needs of modern conveyor systems, from zero pressure accumulation to continuous flow conveyors.
Applications in Zero Pressure Accumulation Conveyor Systems
Interroll’s drive rollers are pivotal in zero pressure accumulation (ZPA) conveyor systems, where they offer several key advantages:
- Individual Product Handling: Each section of the conveyor can control the movement of individual products, preventing collisions and ensuring gentle handling of sensitive items.
- Energy Efficiency: The rollers activate only when needed, conserving energy by reducing power consumption when sections of the conveyor are not in use.
- Scalability: Interroll powered rollers can easily adapt to changes in production volume, making them ideal for businesses experiencing growth or seasonal fluctuations.
- Integration with Sorting Systems: They seamlessly integrate with automated sorting systems, enhancing the efficiency of distribution centers and e-commerce fulfillment operations.
- Reduced Wear and Tear: By controlling the accumulation of products, these rollers minimize the wear and tear on both the conveyor system and the products being transported.
Applications in Continuous Conveyors
In continuous conveyor systems, Interroll powered rollers demonstrate their versatility through:
- Consistent Product Flow: They ensure a smooth and continuous flow of products, crucial for assembly lines and manufacturing processes where timing and synchronization are key.
- Variable Speed Control: The ability to adjust the speed of the rollers allows for precise control over the movement of goods, accommodating different stages of the production process.
- Low Maintenance: Their robust design and reliability result in lower maintenance requirements, minimizing downtime in critical production environments.
- Quiet Operation: Interroll powered rollers are designed for quiet operation, contributing to a more pleasant working environment, especially in facilities where noise levels are a concern.
- Flexibility in Layout Design: The compact and modular nature of these rollers allows for flexible conveyor layout designs, including curves, inclines, and declines, to fit the spatial constraints of any facility.
Interroll’s drive rollers exemplify the company’s commitment to providing innovative solutions that enhance the efficiency and flexibility of conveyor systems. The versatility of Interroll powered rollers makes them an indispensable component in the design of modern material handling solutions, capable of addressing the complex requirements of today’s industries.
Maintenance and Replacement Solutions for Interroll Powered Rollers
Maintaining the operational efficiency and reliability of conveyor systems equipped with Interroll powered rollers is paramount for businesses relying on seamless material handling processes. Interroll’s commitment to supporting their products extends to offering comprehensive maintenance and replacement solutions.
Interroll Replacement Parts
The availability of genuine Interroll replacement parts is crucial for the upkeep of Interroll powered rollers, ensuring that they continue to operate at peak performance.
- Drive Belts: Essential for the transmission of power in motorized rollers, ensuring smooth and efficient operation.
- Bearings: High-quality bearings are vital for the smooth rotation of rollers, reducing friction and wear over time.
- Control Cards: For powered rollers with integrated control systems, replacement control cards ensure the precise management of roller operation.
- O-Rings: Used in the assembly of rollers to maintain proper alignment and tension, ensuring consistent performance.
- Motor Assemblies: Complete motor assembly kits are available for replacing worn or damaged motors in powered rollers, restoring their original efficiency.
Access to these genuine parts not only prolongs the life of Interroll powered rollers but also maintains the integrity of the entire conveyor system, minimizing downtime and potential disruptions to operations.
Interroll 1700 Series Roller
The Interroll 1700 series roller is renowned for its durability and adaptability, making it a staple in high-performance roller conveyors across various industries.
- Robust Construction: Designed to withstand demanding industrial environments, ensuring long-term reliability and performance.
- Versatility: Capable of handling a wide range of products, from lightweight packages to heavy pallets, making them suitable for diverse applications.
- Ease of Replacement: Interroll ensures that replacement parts for the 1700 series rollers are readily available, simplifying maintenance and repair processes.
- Customization Options: The 1700 series offers various customization options, including different tube materials and surface treatments, to meet specific operational needs.
- Compatibility: These rollers are designed to seamlessly integrate with existing conveyor systems, reducing the need for extensive modifications when replacements are necessary.
Focusing on the maintenance and availability of replacement parts for Interroll powered rollers, particularly the 1700 series, highlights Interroll’s dedication to providing sustainable and reliable material handling solutions. This approach not only ensures the longevity of the rollers but also supports the continuous, efficient operation of conveyor systems critical to modern industry workflows.
Additional Interroll Roller Solutions in Interroll Powered Rollers
Beyond the core offerings of Interroll powered rollers, Interroll extends its expertise into additional solutions designed to enhance the functionality and integration of conveyor systems. These supplementary solutions underscore Interroll’s commitment to providing comprehensive material handling options.
Interroll Roller Track
The Interroll Roller Track stands out as a pivotal component in the suite of Interroll powered rollers solutions, designed to augment the efficiency of material handling processes.
- Heavy Load Capability: Engineered to accommodate substantial weights, the Interroll Roller Track ensures the seamless movement of heavy loads, making it an ideal choice for industries dealing with bulky or weighty products.
- Smooth Operation: The precision design of the roller track facilitates a smooth glide for goods, minimizing friction and resistance, which translates to reduced wear on both the products and the conveyor system.
- Versatile Applications: Whether integrated into manufacturing lines, distribution centers, or retail backrooms, the roller track’s versatility allows it to adapt to various operational contexts, enhancing workflow efficiency.
- Durability: Constructed with high-quality materials, the roller track is built to withstand the rigors of continuous operation, ensuring long-term reliability and performance.
- Integration Ease: Designed with compatibility in mind, the roller track seamlessly integrates with existing Interroll powered rollers setups, enhancing system functionality without the need for extensive modifications.
Interroll Roller CAD Download
In support of the engineering and design community, Interroll provides “Interroll Roller CAD Download” resources, a testament to their dedication to facilitating the integration of Interroll powered rollers into diverse conveyor systems. These resources offer:
- Detailed Models: CAD downloads provide intricate models of Interroll rollers, allowing for precise planning and integration into conveyor system designs.
- Customization Support: With access to CAD models, engineers can tailor their conveyor solutions to meet specific operational requirements, ensuring optimal system performance.
- Efficient Planning: The availability of downloadable models streamlines the design process, enabling quicker turnaround times from concept to implementation.
- Technical Insight: CAD models offer a deeper understanding of the rollers’ specifications and functionalities, aiding in the selection of the most suitable components for each application.
- Collaborative Design: These resources facilitate collaboration among project teams, ensuring that all stakeholders have access to accurate and up-to-date information, leading to more informed decision-making.
The “Interroll Roller Track” and “Interroll Roller CAD Download” resources exemplify Interroll’s holistic approach to material handling solutions, providing not only the physical components but also the technical support necessary for the successful implementation of Interroll powered rollers in various industrial settings.
FAQs About Interroll Powered Rollers
A powered roller conveyor system is an automated material handling solution designed to transport goods across short or long distances within a facility. Unlike traditional conveyor systems that rely on manual effort or gravity for movement, powered roller conveyors use electric motors embedded within the rollers or attached to the side to propel the conveyor belt and move the items placed on it. This system is highly efficient, allowing for controlled movement of goods with variable speeds, and can be easily integrated into existing warehouse management systems for streamlined operations. Powered roller conveyors are versatile and can handle a wide range of products, from small packages to large pallets, making them ideal for industries such as manufacturing, distribution, e-commerce, and more. Their automation capabilities not only enhance productivity but also reduce labor costs and minimize the risk of injury associated with manual handling.
Conveyor rollers come in various types, each designed to fulfill specific material handling requirements:
Gravity Rollers: These rely on gravity to move items and are typically used in applications where manual loading and unloading are feasible.
Powered Rollers: Equipped with internal motors, these rollers automate the movement of goods along the conveyor line.
Grooved Rollers: Designed with grooves that can accommodate round belts for driving the roller, suitable for lightweight packages.
Tapered Rollers: Used in curved sections of conveyor systems to maintain the alignment and orientation of the products.
Impact Rollers: Installed at conveyor loading points, these rollers are cushioned to absorb the impact of falling goods, protecting both the conveyor belt and the items.
Accumulation Rollers: Allow for the accumulation of products on the conveyor without causing damage or back pressure, ideal for sorting and merging operations.
Each type of roller offers unique benefits and is selected based on the specific needs of the conveyor system, such as the weight of the items, the desired speed of movement, and the nature of the operation.
Several manufacturers specialize in the production of motorized rollers for conveyor systems, with Interroll being one of the leading providers in the industry. Interroll offers a wide range of motorized rollers, known for their reliability, efficiency, and compatibility with various conveyor configurations. Other notable manufacturers include Hytrol, Dematic, and
Honeywell Intelligrated, each bringing their own innovations and design features to the market. These companies provide motorized rollers that cater to different industry needs, from light-duty applications in retail environments to heavy-duty use in manufacturing and distribution centers. When selecting a motorized roller provider, it’s essential to consider factors such as product quality, technical support, and the ability to customize solutions to fit specific operational requirements.
While roller conveyors are highly versatile and efficient, they do have certain limitations that may affect their suitability for some applications:
Limited Product Types: Roller conveyors are best suited for items with a flat bottom surface. Irregularly shaped or very small items may not move smoothly or could become lodged between rollers.
Inclines and Declines: Gravity roller conveyors, in particular, are less effective on inclines or declines, as items may move too quickly or not at all without additional control mechanisms.
Load Capacity: Each roller and conveyor frame has a specific load capacity. Overloading the system can lead to roller damage, system malfunctions, and potential safety hazards.
Noise Levels: Powered roller conveyors can generate significant noise, especially in high-speed applications, which may require additional measures for noise reduction in the workplace.
Maintenance Requirements: While generally low-maintenance, roller conveyors do require regular inspections and upkeep to ensure optimal performance, particularly for systems with numerous moving parts.
Cost: The initial setup cost for a powered roller conveyor system can be high, especially for customized solutions or extensive conveyor networks.
Understanding these limitations is crucial when designing or selecting a roller conveyor system to ensure it meets the operational needs and provides a reliable, efficient material handling solution.
Last Updated on May 23, 2024 by Jordan Smith
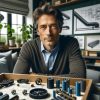
Jordan Smith, a seasoned professional with over 20 years of experience in the conveyor system industry. Jordan’s expertise lies in providing comprehensive solutions for conveyor rollers, belts, and accessories, catering to a wide range of industrial needs. From initial design and configuration to installation and meticulous troubleshooting, Jordan is adept at handling all aspects of conveyor system management. Whether you’re looking to upgrade your production line with efficient conveyor belts, require custom conveyor rollers for specific operations, or need expert advice on selecting the right conveyor accessories for your facility, Jordan is your reliable consultant. For any inquiries or assistance with conveyor system optimization, Jordan is available to share his wealth of knowledge and experience. Feel free to reach out at any time for professional guidance on all matters related to conveyor rollers, belts, and accessories.