Essential King Conveyor Belt Parts: Functions and Roles
King conveyor belt is a top-tier solution designed to meet the diverse needs of multiple industries. Renowned for their durability and efficiency, King conveyor belts are used in manufacturing, logistics, mining, and many other sectors. These conveyor belts are engineered to handle heavy loads and harsh environments, ensuring seamless operations. Available for sale, King conveyor belts offer unparalleled performance and reliability, making them an ideal choice for businesses looking to enhance their material handling processes. Invest in a King conveyor belt today and experience the difference in quality and functionality.
Key Features of King Conveyor Belt for Sale
King conveyor belts are renowned for their exceptional quality and robust construction, making them a preferred choice for various industrial applications. When considering a King conveyor belt for sale, it is essential to understand its key features and specifications, as these attributes significantly contribute to its performance and durability. Here, we detail the essential features and specifications of King conveyor belts and explain the benefits these features provide in industrial applications.
High-Quality Materials
One of the standout features of King conveyor belts is the use of high-quality materials in their construction. These belts are typically made from premium rubber compounds, reinforced with synthetic fibers such as polyester or aramid. The choice of materials ensures that King conveyor belts are durable, flexible, and resistant to wear and tear. This high-quality construction makes them suitable for a wide range of demanding industrial environments, from mining to manufacturing.
Exceptional Durability
Durability is a critical feature of King conveyor belts. The robust materials and advanced manufacturing processes used in these belts ensure they can withstand heavy loads, abrasive materials, and harsh operating conditions. This durability translates to a longer lifespan, reducing the need for frequent replacements and minimizing downtime. Industries that require continuous operation, such as automotive manufacturing and food processing, benefit greatly from the durability of King conveyor belts.
Heat and Chemical Resistance
King conveyor belts are designed to resist high temperatures and exposure to chemicals. This feature is particularly important in industries such as chemical processing, food processing, and metalworking, where belts are often exposed to harsh environments. The heat resistance ensures that the belts can operate efficiently even in high-temperature applications, while the chemical resistance prevents degradation and maintains belt integrity, even when exposed to corrosive substances.
Superior Flexibility
Flexibility is another essential feature of King conveyor belts. These belts are designed to bend and flex without cracking or losing their structural integrity. This flexibility is crucial for applications that involve complex conveyor systems with multiple curves and inclines. The ability to maintain flexibility under various conditions ensures smooth and efficient material handling, reducing the risk of belt failure and operational interruptions.
High Load Capacity
King conveyor belts are engineered to handle high load capacities, making them suitable for heavy-duty industrial applications. The reinforced construction provides the necessary strength to support heavy materials without stretching or breaking. This high load capacity is beneficial in industries such as mining, construction, and bulk material handling, where the belts must transport large volumes of materials efficiently.
Low Maintenance Requirements
One of the significant advantages of King conveyor belts is their low maintenance requirements. The high-quality materials and robust construction reduce the frequency of repairs and replacements, saving time and maintenance costs. Additionally, the belts are designed for easy cleaning and inspection, ensuring that they remain in optimal condition with minimal effort. This feature is particularly beneficial in industries with stringent hygiene standards, such as food processing and pharmaceuticals.
Customization Options
King conveyor belts offer a range of customization options to meet specific industrial needs. Businesses can choose from various belt widths, lengths, and thicknesses, as well as different surface finishes and patterns. This customization ensures that the belts are perfectly suited to the unique requirements of each application, enhancing overall efficiency and performance. Whether it’s a textured surface for improved grip or a smooth finish for easy material movement, King conveyor belts can be tailored to meet specific operational needs.
Energy Efficiency
Energy efficiency is an increasingly important consideration in industrial operations, and King conveyor belts are designed with this in mind. The low-friction surface of the belts reduces the energy required to move materials, contributing to overall energy savings. This energy efficiency not only reduces operational costs but also aligns with sustainable practices by minimizing the environmental impact of industrial activities.
Safety Features
Safety is a paramount concern in industrial settings, and King conveyor belts are designed to enhance workplace safety. Features such as anti-slip surfaces, flame resistance, and reduced noise levels contribute to a safer working environment. These safety features are particularly important in industries such as mining and construction, where the risk of accidents is higher. By prioritizing safety, King conveyor belts help businesses protect their workforce and comply with safety regulations.
Reliable Performance
Reliability is a key feature of King conveyor belts. These belts are designed to deliver consistent performance, ensuring smooth and efficient material handling. The high-quality construction and advanced engineering minimize the risk of belt failures and operational disruptions, providing businesses with a dependable material handling solution. This reliability is crucial for maintaining productivity and meeting production targets in various industrial applications.
King conveyor belts for sale offer a range of essential features and specifications that ensure their durability, flexibility, and performance in demanding industrial environments. High-quality materials, exceptional durability, heat and chemical resistance, superior flexibility, high load capacity, low maintenance requirements, customization options, energy efficiency, safety features, and reliable performance make King conveyor belts a preferred choice for various industries. By understanding these key features, businesses can make informed decisions and select the right conveyor belt to meet their specific needs, ensuring efficient and reliable material handling operations.
How to Choose the Right King Conveyor Belt for Sale
Selecting the right King conveyor belt for sale is a crucial decision that can significantly impact the efficiency, safety, and longevity of your material handling system. To make an informed choice, it is essential to consider various factors such as load capacity, material composition, and environmental conditions. This section provides guidance on choosing the appropriate King conveyor belt for specific needs and discusses the key factors to consider.
Assessing Load Capacity
The load capacity of the conveyor belt is one of the most critical factors to consider. It is essential to choose a belt that can handle the maximum load of your application without stretching or breaking. Factors to consider include:
- Weight of Materials: Determine the average and maximum weight of the materials that the belt will transport. Ensure that the chosen belt can support these weights without compromising performance.
- Belt Width and Thickness: Wider and thicker belts typically offer higher load capacities. Select a belt width and thickness that match the load requirements of your application.
- Reinforcement Layers: Consider the number of reinforcement layers in the belt. Multi-ply belts with multiple layers of reinforcement provide added strength and load-bearing capacity.
Material Composition
The material composition of the conveyor belt is another crucial factor that affects its performance and durability. Different materials offer varying levels of heat resistance, chemical resistance, and flexibility. Key considerations include:
- Heat Resistance: If your application involves high temperatures, choose a belt made from heat-resistant materials such as EPDM (Ethylene Propylene Diene Monomer) or PTFE (Polytetrafluoroethylene). These materials can withstand elevated temperatures without degrading.
- Chemical Resistance: For applications exposed to chemicals or corrosive substances, select a belt with chemical-resistant properties. PTFE and certain rubber compounds offer excellent resistance to chemicals, ensuring the belt’s longevity and performance.
- Abrasion Resistance: In environments with abrasive materials, choose a belt with high abrasion resistance. Materials such as SBR (Styrene-Butadiene Rubber) provide good wear resistance, reducing the risk of belt damage.
Environmental Conditions
The operating environment plays a significant role in determining the right King conveyor belt for your application. Consider the following environmental factors:
- Temperature: Assess the ambient and operational temperatures of your environment. Ensure that the selected belt can handle these temperatures without losing its structural integrity or performance.
- Humidity and Moisture: In humid or wet environments, choose a belt with moisture-resistant properties to prevent degradation and slippage.
- Exposure to UV Light: If the conveyor belt will be exposed to direct sunlight or UV light, select a belt with UV-resistant properties to prevent material degradation.
Considering Conveyor System Configuration
The configuration of your conveyor system also influences the choice of conveyor belt. Key aspects to consider include:
- Belt Length and Width: Ensure that the belt dimensions match the specifications of your conveyor system. The length and width of the belt should be compatible with the system’s design.
- Belt Speed: Determine the speed at which the belt will operate. Some belts are designed for high-speed applications, while others are better suited for slower speeds. Select a belt that can handle the operational speed without compromising performance.
- Inclines and Curves: If your conveyor system includes inclines or curves, choose a flexible belt that can navigate these configurations without issues. Flexibility is crucial for ensuring smooth material movement and reducing the risk of belt failure.
Customization Options
Customization options allow you to tailor the conveyor belt to your specific needs. Consider the following customization aspects:
- Surface Finish: Choose a surface finish that matches the material handling requirements. Smooth surfaces are ideal for transporting fine materials, while textured surfaces provide better grip for bulkier items.
- Edge Profiles: Select edge profiles that prevent material spillage and enhance belt performance. Custom edge profiles can be designed to match specific application needs.
- Special Coatings: Consider special coatings that enhance the belt’s properties, such as anti-static coatings for electronics manufacturing or anti-microbial coatings for food processing.
Maintenance Requirements
Understanding the maintenance requirements of the conveyor belt is essential for ensuring long-term performance and reducing operational costs. Key maintenance considerations include:
- Ease of Cleaning: Choose a belt that is easy to clean and maintain, especially in industries with stringent hygiene standards.
- Inspection and Repair: Consider the ease of inspecting and repairing the belt. Belts with modular designs or easily accessible components simplify maintenance tasks.
- Durability: Select a belt with high durability to reduce the frequency of repairs and replacements, minimizing downtime and maintenance costs.
Cost Considerations
While the initial cost of the conveyor belt is an important factor, it is essential to consider the long-term cost implications. A higher upfront investment in a high-quality belt may result in lower maintenance costs and a longer lifespan, making it a cost-effective choice in the long run. Balance the initial investment with the long-term benefits to make an informed decision.
Manufacturer Reputation
Finally, consider the reputation of the manufacturer when selecting a King conveyor belt for sale. Reputable manufacturers offer high-quality products backed
by technical support and warranties. Research customer reviews, testimonials, and industry certifications to ensure that the manufacturer is reliable and trustworthy.
Choosing the right King conveyor belt for sale involves careful consideration of load capacity, material composition, environmental conditions, conveyor system configuration, customization options, maintenance requirements, cost implications, and manufacturer reputation. By evaluating these factors, businesses can select the appropriate conveyor belt to meet their specific needs, ensuring efficient and reliable material handling operations in various industrial applications.
Installation Guide for King Conveyor Belt Replacement
Replacing a King conveyor belt is a critical task that requires careful planning and execution to ensure a smooth and efficient installation process. Proper installation is essential for maintaining the performance and longevity of the conveyor belt, reducing downtime, and minimizing operational disruptions. This section provides a step-by-step guide for replacing a King conveyor belt and includes tips for ensuring a successful installation.
Step 1: Prepare for Replacement
Before starting the replacement process, it is essential to prepare adequately. This preparation includes gathering the necessary tools and equipment, ensuring that the replacement belt is the correct size and type, and planning the installation to minimize downtime. Key preparation steps include:
- Gather Tools and Equipment: Ensure that you have all the necessary tools and equipment for the installation, including wrenches, screwdrivers, belt clamps, a belt tensioning device, and safety gear.
- Verify Belt Specifications: Double-check the specifications of the replacement belt to ensure it matches the requirements of your conveyor system, including length, width, thickness, and material.
- Plan Downtime: Schedule the replacement during planned maintenance downtime to minimize disruptions to production. Coordinate with production teams to ensure a smooth transition.
Step 2: Shut Down and Secure the Conveyor System
Safety is a top priority when replacing a conveyor belt. Before beginning the installation, shut down the conveyor system and secure it to prevent accidental startup. Key safety steps include:
- Turn Off Power: Ensure that the power supply to the conveyor system is turned off and locked out to prevent accidental activation.
- Secure the Conveyor: Use safety locks or tags to secure the conveyor system and prevent unauthorized access during the replacement process.
- Wear Safety Gear: Wear appropriate safety gear, including gloves, safety glasses, and protective clothing, to protect against potential hazards.
Step 3: Remove the Old Conveyor Belt
Carefully remove the old conveyor belt from the system. This process involves releasing the tension, disconnecting the belt from the pulleys, and carefully sliding it out. Key removal steps include:
- Release Belt Tension: Use the belt tensioning device to release the tension on the old belt. This step is crucial for safely removing the belt without causing damage to the system.
- Disconnect Belt Ends: Disconnect the belt ends from the pulleys and any other attachment points. Carefully loosen and remove any fasteners or clips holding the belt in place.
- Slide Out the Belt: Carefully slide the old belt out of the conveyor system, taking care not to damage any components or create sharp bends in the belt.
Step 4: Inspect Conveyor Components
Before installing the new belt, inspect the conveyor components for wear or damage. This inspection helps identify any issues that may affect the performance of the new belt. Key inspection steps include:
- Check Rollers and Pulleys: Inspect rollers and pulleys for signs of wear, misalignment, or damage. Ensure that they rotate smoothly and are free from debris.
- Inspect Frame and Structure: Check the conveyor frame and structure for any signs of damage or corrosion. Repair or replace any damaged components as needed.
- Examine Bearings and Fasteners: Inspect bearings and fasteners for wear or looseness. Tighten or replace any loose or worn components to ensure the system’s stability.
Step 5: Install the New King Conveyor Belt
Carefully install the new King conveyor belt, ensuring that it is properly aligned and tensioned. Key installation steps include:
- Position the Belt: Position the new belt in the conveyor system, ensuring that it is properly aligned with the pulleys and rollers. Use belt clamps to hold the belt in place during installation.
- Connect Belt Ends: Connect the belt ends using the appropriate fastening method, such as mechanical fasteners or vulcanization. Ensure that the connection is secure and properly aligned.
- Apply Tension: Use the belt tensioning device to apply the correct amount of tension to the belt. Proper tensioning is crucial for preventing slippage and ensuring smooth operation.
Step 6: Conduct a Test Run
After installing the new belt, conduct a test run to ensure that it operates smoothly and efficiently. Key test run steps include:
- Check Alignment: Ensure that the belt is properly aligned and centered on the pulleys and rollers. Adjust the alignment as needed to prevent tracking issues.
- Monitor Tension: Verify that the belt tension is within the recommended range. Adjust the tension if necessary to achieve optimal performance.
- Inspect for Issues: Monitor the belt during the test run for any signs of issues, such as slippage, misalignment, or unusual noises. Address any problems promptly to prevent further damage.
Step 7: Perform Final Adjustments
After the test run, perform any final adjustments to ensure that the conveyor system operates at peak efficiency. Key adjustment steps include:
- Fine-Tune Alignment: Make any final adjustments to the belt alignment to ensure that it tracks properly and does not drift to one side.
- Verify Tension: Recheck the belt tension and make any necessary adjustments to achieve the recommended tension level.
- Secure Components: Ensure that all components, including fasteners, clamps, and covers, are securely in place and properly tightened.
Step 8: Document the Replacement
Document the replacement process, including any adjustments made and any issues encountered. This documentation helps track the maintenance history of the conveyor system and provides valuable information for future replacements. Key documentation steps include:
- Record Belt Specifications: Note the specifications of the new belt, including length, width, thickness, and material.
- Document Adjustments: Record any adjustments made during the installation and test run, including alignment and tension adjustments.
- Log Maintenance Details: Include details of any repairs or replacements made to the conveyor components during the replacement process.
Step 9: Resume Normal Operation
After completing the replacement and ensuring that the conveyor system operates smoothly, resume normal operation. Monitor the system closely during the initial operation to ensure that the new belt performs as expected and address any issues that arise promptly.
Replacing a King conveyor belt requires careful planning, attention to detail, and adherence to safety protocols. By following this step-by-step guide, businesses can ensure a smooth and efficient installation process, maintaining the performance and longevity of the conveyor system. Proper preparation, thorough inspections, careful installation, and detailed documentation are key to a successful belt replacement, minimizing downtime and ensuring reliable material handling operations.
Common Signs That Indicate the Need for King Conveyor Belt Replacement
Maintaining a king conveyor belt system in optimal condition is critical for ensuring operational efficiency and minimizing downtime. Over time, however, even the most robust conveyor belts will exhibit signs of wear and tear. Recognizing these signs early can prevent unexpected failures and prolong the lifespan of your equipment. Here are some common signs that indicate the need for a king conveyor belt replacement:
1. Visible Cracks and Fraying
One of the most apparent indicators that a conveyor belt needs replacement is the presence of visible cracks or fraying along the belt’s edges. Cracks can occur due to constant flexing and stress, while fraying usually results from rubbing against other components or improper tracking. Regularly inspecting the belt’s surface and edges for these signs can help in identifying the need for a replacement before a major failure occurs.
2. Uneven Wear Patterns
Uneven wear patterns on a conveyor belt can signal issues with alignment or loading practices. If the belt shows more wear on one side compared to the other, it might be due to misalignment of the rollers or pulleys. This uneven wear can compromise the belt’s integrity and efficiency, necessitating a replacement to restore proper function.
3. Belt Slippage
Belt slippage is another common sign of a deteriorating conveyor belt. Slippage can be caused by a loss of tension, worn pulleys, or a belt that has stretched beyond its usable length. If you notice that the belt is not moving as smoothly or is slipping on the pulleys, it’s time to inspect and possibly replace the belt.
4. Unusual Noise
A well-maintained king conveyor belt should operate relatively quietly. If you start hearing unusual noises such as squeaking, grinding, or rattling, it could indicate that the belt or its components are worn out. Noise can result from misaligned parts, inadequate lubrication, or a belt that is rubbing against other components. Identifying the source of the noise and addressing it promptly can help determine if a replacement is necessary.
5. Material Carryback
Material carryback refers to the remnants of conveyed material that stick to the belt and are carried back along its return path. Excessive carryback can cause build-up on the belt and other components, leading to increased wear and operational issues. If your conveyor belt is not effectively shedding material, it might be worn or damaged, indicating a need for replacement.
6. Increased Maintenance Requirements
If you find that your conveyor belt requires increasingly frequent maintenance to keep it running smoothly, it might be a sign that the belt is nearing the end of its lifespan. High maintenance demands can be due to cumulative wear and tear that compromises the belt’s performance, making replacement a more cost-effective solution.
7. Deformation or Stretching
Over time, a conveyor belt can become deformed or stretched beyond its original dimensions. This deformation can result from prolonged exposure to heavy loads, heat, or harsh environmental conditions. A belt that has lost its shape or elasticity may no longer function effectively and should be replaced to maintain system efficiency.
Monitoring and Assessing Conveyor Belt Condition
To ensure timely replacement and avoid unexpected failures, it’s essential to establish a regular monitoring and assessment routine for your king conveyor belt. Here are some tips on how to effectively monitor and assess the condition of your conveyor belt:
- Regular Visual Inspections: Conduct regular visual inspections of the belt and its components. Look for signs of wear, damage, and misalignment.
- Performance Monitoring: Keep track of the conveyor belt’s performance metrics, such as speed, load capacity, and operational noise. Any significant changes can indicate underlying issues.
- Maintenance Logs: Maintain detailed logs of all maintenance activities, including repairs, adjustments, and parts replacements. These logs can help identify recurring issues and predict when a replacement might be necessary.
- Professional Assessments: Schedule periodic assessments by a professional conveyor belt technician. Their expertise can provide a more thorough evaluation of the belt’s condition and recommend appropriate actions.
By staying vigilant and proactive in monitoring your king conveyor belt, you can ensure its longevity and optimal performance.
Essential King Conveyor Belt Parts and Their Functions
A king conveyor belt system comprises several key components, each playing a vital role in ensuring the belt’s performance, durability, and efficiency. Understanding these components and their functions can help in maintaining the system and troubleshooting issues more effectively. Here are the essential parts of a king conveyor belt system and their functions:
1. Conveyor Belt
The conveyor belt is the most critical component of the system. It is responsible for carrying materials from one point to another. Conveyor belts are typically made from rubber, PVC, or other durable materials designed to withstand various operating conditions. The belt’s quality and design significantly impact the overall performance and lifespan of the conveyor system.
2. Pulleys
Pulleys are essential components that support and guide the conveyor belt. There are two main types of pulleys in a conveyor system: drive pulleys and idler pulleys. Drive pulleys are connected to the motor and provide the necessary traction to move the belt, while idler pulleys help maintain tension and support the belt along its path.
3. Rollers
Rollers support the conveyor belt and help reduce friction as the belt moves. They are typically spaced along the conveyor frame and can be either stationary or rotating. Rollers play a crucial role in maintaining the belt’s alignment and ensuring smooth operation.
4. Motor
The motor provides the necessary power to drive the conveyor belt. It is usually connected to the drive pulley via a gearbox and drive shaft. The motor’s specifications, such as horsepower and speed, determine the conveyor belt’s operating capacity and efficiency.
5. Frame
The frame is the structural backbone of the conveyor system. It supports all other components and provides a stable platform for the belt to operate. Frames are typically made from steel or aluminum and are designed to withstand the stresses and loads encountered during operation.
6. Bearings
Bearings are used to support the rotating shafts and reduce friction. They are crucial for the smooth operation of pulleys and rollers. High-quality bearings can extend the lifespan of these components and reduce maintenance requirements.
7. Tensioning System
The tensioning system ensures that the conveyor belt maintains the proper tension during operation. Proper tension is crucial for preventing slippage and ensuring efficient power transmission. Tensioning systems can be manual or automatic, depending on the design of the conveyor system.
8. Cleaning Devices
Cleaning devices, such as belt scrapers and brushes, are used to remove material carryback and keep the belt clean. These devices help prevent build-up on the belt and other components, reducing wear and maintenance requirements.
9. Safety Guards
Safety guards are protective devices that prevent accidental contact with moving parts of the conveyor system. They are essential for ensuring the safety of personnel working around the conveyor belt.
Understanding the functions of these essential components can help in maintaining the king conveyor belt system more effectively and troubleshooting issues when they arise.
Maintenance Tips for King Conveyor Belt Parts
Proper maintenance is key to ensuring the longevity and efficient operation of a king conveyor belt system. Regular care and attention to the various components can prevent unexpected breakdowns and reduce overall maintenance costs. Here are some practical maintenance tips for king conveyor belt parts:
1. Regular Inspections
Conduct regular inspections of all conveyor belt components, including the belt itself, pulleys, rollers, and bearings. Look for signs of wear, damage, and misalignment. Early detection of issues can prevent more significant problems down the line.
2. Lubrication
Proper lubrication is essential for reducing friction and wear on moving parts such as bearings and rollers. Use high-quality lubricants recommended by the manufacturer and follow a regular lubrication schedule. Over-lubrication can be as detrimental as under-lubrication, so apply the correct amount.
3. Cleaning
Keep the conveyor belt and its components clean to prevent material build-up and reduce wear. Use appropriate cleaning methods and devices, such as belt scrapers and brushes, to remove debris and carryback. Regular cleaning can also help identify potential issues before they become serious problems.
4. Tension Adjustment
Maintain proper tension on the conveyor belt to prevent slippage and ensure efficient power transmission. Regularly check and adjust the tensioning system according to the manufacturer’s specifications. An over-tensioned belt can cause excessive wear, while an under-tensioned belt can slip and reduce efficiency.
5. Alignment
Ensure that all components, including the belt, pulleys, and rollers, are properly aligned. Misalignment can cause uneven wear and reduce the lifespan of the conveyor belt. Use alignment tools and techniques recommended by the manufacturer to keep everything in proper order.
6. Component Replacement
Replace worn or damaged components promptly to prevent further damage to the conveyor system. This includes replacing worn belts, pulleys, rollers, and bearings. Keeping spare parts on hand can reduce downtime and ensure quick repairs when needed.
7. Monitoring System Performance
Regularly monitor the performance of the conveyor system, including speed, load capacity, and operational noise. Any significant changes in these metrics can indicate underlying issues that need to be addressed. Use monitoring tools and systems to keep track of performance and identify trends over time.
8. Professional Maintenance
Schedule regular maintenance and assessments by a professional conveyor belt technician. Their expertise can provide a more thorough evaluation of the system’s condition and recommend appropriate actions. Professional maintenance can also ensure that all components are maintained according to industry standards.
By following these maintenance tips, you can ensure the longevity and efficient operation of your king conveyor belt system. Regular care and attention to the various components can prevent unexpected breakdowns and reduce overall maintenance costs.
Last Updated on June 6, 2024 by Jordan Smith
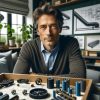
Jordan Smith, a seasoned professional with over 20 years of experience in the conveyor system industry. Jordan’s expertise lies in providing comprehensive solutions for conveyor rollers, belts, and accessories, catering to a wide range of industrial needs. From initial design and configuration to installation and meticulous troubleshooting, Jordan is adept at handling all aspects of conveyor system management. Whether you’re looking to upgrade your production line with efficient conveyor belts, require custom conveyor rollers for specific operations, or need expert advice on selecting the right conveyor accessories for your facility, Jordan is your reliable consultant. For any inquiries or assistance with conveyor system optimization, Jordan is available to share his wealth of knowledge and experience. Feel free to reach out at any time for professional guidance on all matters related to conveyor rollers, belts, and accessories.