Selecting the Perfect Knurled Steel Rollers
Knurled steel rollers are pivotal components in the realm of industrial machinery, known for their distinctive textured surface that offers unparalleled grip and traction. This unique feature makes them indispensable in applications requiring precise material handling and movement. The knurling on these rollers is not just about aesthetics; it plays a crucial role in enhancing the functionality of equipment, from feeding mechanisms in welding apparatus to guiding sheets in printing presses. The benefits of using knurled steel rollers extend beyond their immediate functionality, contributing to the efficiency and safety of industrial operations. Their robust construction and design adaptability make them a preferred choice for engineers and technicians looking to optimize their machinery’s performance.
The Advantages of Knurled Steel Rollers
Knurled steel rollers stand out in the industrial sector for their exceptional durability and longevity, especially in demanding heavy-duty environments. The knurled pattern etched onto the surface of these rollers is not merely decorative but serves multiple functional purposes across a wide array of machinery. Here are eight significant roles that the knurling on these rollers plays:
- Enhanced Grip: The primary advantage of knurled steel rollers is the increased grip they provide, ensuring materials are securely transported through machinery without slippage, which is crucial in precision tasks.
- Improved Traction: In applications like conveyor systems, the knurled texture improves traction, facilitating the smooth movement of goods, even in high-speed settings.
- Material Handling: For MIG welders, the knurling helps in the steady feeding of welding wire, contributing to consistent weld quality and reducing the risk of wire jamming or tangling.
- Printing Precision: In the printing industry, feed rollers with knurled surfaces ensure paper or other media is accurately fed into the printing press, enhancing print quality and alignment.
- Noise Reduction: The specific design of knurled patterns can also contribute to noise reduction within machinery, leading to a more pleasant working environment.
- Wear Resistance: Knurled steel rollers exhibit superior wear resistance, making them suitable for continuous operation over extended periods, thereby reducing the need for frequent replacements.
- Versatility: The versatility of knurling patterns allows these rollers to be customized for various applications, from textile machinery to packaging lines, tailoring their functionality to specific industry needs.
- Aesthetic and Functional Customization: Beyond their practical benefits, knurled rollers can also be customized aesthetically to fit the branding or design specifications of machinery, offering a dual advantage of functionality and visual appeal.
Knurled steel rollers provide a multitude of advantages that extend their utility beyond basic roller functions, making them an invaluable component in enhancing the efficiency, reliability, and output quality of various industrial machinery.
Applications of Knurled Steel Rollers
Knurled steel rollers are integral to a myriad of industrial applications, showcasing their versatility across diverse sectors. These rollers, distinguished by their textured surface, are particularly valued for their ability to enhance grip and precision in material handling and processing. Here are eight specialized applications and industries where knurled steel rollers prove indispensable:
- Welding Equipment: In welding, particularly with MIG welders, knurled steel rollers are crucial for feeding welding wire smoothly and consistently, preventing snags and ensuring uniform welds.
- Industrial Feed Systems: High-precision feed systems, such as those in Weinig woodworking machinery, rely on knurled rollers to accurately guide materials through the cutting and shaping processes.
- Printing Operations: Large-scale printing presses utilize knurled rollers to feed paper or other media with precision, ensuring accurate alignment and print quality across vast production runs.
- Textile Manufacturing: In the textile industry, knurled rollers are used to feed fabric through machines for printing, cutting, or embellishing, maintaining tension and alignment.
- Conveyor Systems: Various manufacturing plants employ knurled steel rollers in their conveyor systems to move products efficiently while minimizing slippage and product damage.
- Packaging Equipment: Packaging machinery, especially those requiring tight control over film or material feed, benefits from the grip provided by knurled rollers, ensuring seamless packaging processes.
- Food Processing: In food production lines, knurled rollers are used to transport ingredients or products through different stages of processing, often tailored with specific coatings to meet hygiene standards.
- Material Handling and Logistics: Warehouses and distribution centers use conveyor systems equipped with knurled steel rollers to handle a wide range of goods, from heavy boxes to delicate items, ensuring they are moved safely and efficiently.
The adaptability of knurled steel rollers to various industrial needs, from enhancing the functionality of welding equipment to ensuring the efficiency of large-scale printing and packaging operations, underscores their invaluable role. Their application across different industries highlights the universal need for reliable material handling solutions that knurled steel rollers adeptly fulfill.
Choosing the Right Knurled Steel Rollers
Factors to Consider
Selecting the appropriate knurled steel rollers for your industrial application is crucial to ensure efficiency, longevity, and compatibility with your machinery. Here are eight key factors to consider when making your selection:
- Load Capacity: Assess the maximum weight the rollers will need to support to prevent deformation or failure under load.
- Knurling Pattern: Different patterns provide varying levels of grip and traction, so choose one that suits your material handling needs.
- Material Compatibility: Ensure the roller material is compatible with the products it will contact, especially important in corrosive or high-temperature environments.
- Roller Diameter: The size of the roller affects its ability to handle certain loads and speeds, as well as its suitability for the space available in your machinery.
- Shaft Size: The shaft must be robust enough to support the roller and the load without bending.
- Surface Coating: Coatings can enhance durability, reduce noise, and prevent corrosion, so consider what surface treatments might benefit your application.
- Operating Environment: Factors like temperature, humidity, and exposure to chemicals should influence your choice, as they can affect roller performance and lifespan.
- Maintenance Requirements: Consider how easy the rollers are to clean, lubricate, and replace, as this will impact ongoing maintenance costs and downtime.
Tips
To find “knurled steel rollers near me” and ensure you’re getting a quality product that’s compatible with your machinery, follow these ten tips:
- Research Suppliers: Look for reputable suppliers with experience in your industry.
- Check Reviews: Read customer reviews to gauge the quality and reliability of the rollers and the supplier’s service.
- Ask for Recommendations: Consult with industry peers or forums for supplier recommendations.
- Verify Specifications: Ensure the supplier can provide rollers that meet all your specific requirements.
- Request Samples: If possible, obtain samples to assess quality and compatibility firsthand.
- Inquire About Customization: Some applications may require custom rollers, so check if the supplier offers this service.
- Consider Lead Times: Make sure the supplier can meet your timeline, especially if you need the rollers urgently.
- Evaluate After-Sales Support: Good after-sales service can be invaluable for resolving any issues that arise.
- Compare Prices: While not the only factor, price is important, so compare quotes from several suppliers to ensure you’re getting value for money.
- Visit the Supplier: If feasible, visit the supplier’s facility to get a better sense of their capabilities and quality control processes.
By carefully considering these factors and tips, you can make an informed decision when selecting knurled steel rollers, ensuring they meet your application’s needs and contribute to the smooth operation of your machinery.
Knurled Steel Rollers: Pricing and Availability
Knurled Steel Rollers Price and Factors Influencing Cost
When it comes to integrating knurled steel rollers into your industrial setup, understanding the nuances of pricing and availability is crucial for making informed procurement decisions. The “knurled steel rollers price” can vary significantly based on several key factors that go beyond mere material costs. Here’s a closer look at what influences the pricing and how to navigate the market for “knurled steel rollers for sale”:
- Material Quality: The grade and quality of steel used in the rollers directly impact the price. Higher-grade steels that offer better durability and resistance to wear and corrosion typically command higher prices.
- Custom Specifications: Custom-designed rollers, tailored to specific applications or machinery, often cost more due to the additional design and manufacturing efforts involved.
- Knurling Complexity: The intricacy of the knurling pattern and the precision required can affect the manufacturing process’s complexity, thereby influencing the cost.
- Surface Treatments: Additional surface treatments for enhanced performance, such as coatings for corrosion resistance or improved traction, can add to the overall cost.
- Quantity: Bulk orders may benefit from volume discounts, while smaller orders might carry a premium due to the fixed costs associated with setup and production.
- Supplier Reputation: Established suppliers with a track record of delivering high-quality products may charge more, reflecting their expertise and the reliability of their rollers.
- Market Demand: Fluctuations in demand for knurled steel rollers, driven by trends in the industries that use them, can also impact pricing.
- Geographical Location: The cost can vary depending on the location of the supplier and the associated shipping or import fees, especially for international purchases.
Information on Knurled Steel Rollers for Sale
When searching for “knurled steel rollers for sale,” consider the following to ensure you’re getting good value for your investment:
- Research Suppliers: Look for suppliers with a strong industry presence and positive customer feedback.
- Compare Quotes: Obtain quotes from multiple suppliers to compare prices and understand what’s included, such as warranties or after-sales support.
- Assess Total Cost of Ownership: Consider not just the purchase price but also the expected lifespan, maintenance requirements, and potential downtime costs.
- Verify Specifications: Ensure the rollers meet your exact needs in terms of size, knurling pattern, and load capacity to avoid additional costs down the line.
- Check Lead Times: Factor in the lead time to ensure it aligns with your project timelines, as delays can incur indirect costs.
By carefully evaluating these aspects, you can navigate the market for knurled steel rollers more effectively, ensuring you find a product that meets your technical requirements while offering the best value for your budget.
Maintenance and Care for Knurled Steel Rollers
Guidelines for Maintaining Heavy-duty Steel Rollers
Proper maintenance and care are paramount for maximizing the lifespan and efficiency of knurled steel rollers, especially those used in heavy-duty industrial applications. Here’s a step-by-step guide to maintaining these critical components:
- Regular Cleaning: Begin with routine cleaning to remove debris, dust, and any material buildup on the rollers. Use appropriate cleaning agents that won’t corrode or damage the steel or the knurling.
- Lubrication: Apply suitable lubricants to the roller bearings and any moving parts associated with the roller assembly to ensure smooth operation and to prevent wear and tear.
- Inspection: Conduct thorough inspections for signs of wear, damage to the knurling, or any deformation in the roller body. Pay special attention to the knurled surface, as damage here can significantly impact performance.
- Alignment Checks: Ensure that the rollers are correctly aligned within the machinery. Misalignment can lead to uneven wear and reduced effectiveness.
- Tightening Components: Check and tighten any loose components, including bolts and fasteners, to ensure the roller assembly remains stable during operation.
- Surface Treatment Checks: If the rollers have any protective coatings or treatments, inspect these for signs of wear or damage and reapply as necessary.
- Replacement of Worn Parts: Replace any components that show significant wear or damage, especially those that cannot be repaired or might compromise the roller’s functionality.
The Importance of These Maintenance steps
- Preventing Downtime: Regular maintenance helps avoid unexpected breakdowns that can halt production.
- Ensuring Product Quality: Well-maintained rollers contribute to consistent product quality by providing stable and precise material handling.
- Extending Roller Lifespan: Routine care reduces the need for frequent replacements, extending the lifespan of the rollers.
- Maintaining Efficiency: Clean and well-lubricated rollers operate more efficiently, reducing energy consumption and operational costs.
- Safety: Properly maintained rollers reduce the risk of accidents and injuries in the workplace.
- Preserving Knurling Effectiveness: Regular cleaning and inspection ensure the knurled pattern remains effective for gripping and moving materials.
- Cost Savings: Preventative maintenance is more cost-effective than emergency repairs or replacing severely damaged rollers.
By adhering to these maintenance guidelines, you can ensure your knurled steel rollers continue to perform optimally, contributing to the smooth and efficient operation of your industrial processes.
FAQs about Knurled Steel Rollers
When it comes to selecting the best material for steel rollers, the choice largely depends on the specific application and the environment in which the rollers will be used. Generally, steel rollers are favored for their strength, durability, and ability to withstand high loads and harsh conditions. Among steel options, carbon steel is commonly used for its balance of strength and cost-effectiveness, making it suitable for a wide range of industrial applications. However, for environments that demand higher resistance to corrosion and hygiene, stainless steel is the preferred choice. Stainless steel rollers offer excellent corrosion resistance, making them ideal for use in food processing, chemical industries, and outdoor applications where exposure to elements is a concern. Another factor to consider is the surface treatment or coating, which can enhance the roller’s properties, such as increased hardness, reduced friction, or resistance to specific chemicals. Ultimately, the best material for steel rollers is one that meets the performance requirements of the application while providing longevity and reliability.
Steel rollers are incredibly versatile components used across various industries for numerous applications. Their primary function is to facilitate the movement, processing, and handling of materials and products. In manufacturing and assembly lines, steel rollers are integral to conveyor systems, helping to transport goods efficiently from one stage of production to another. They are also used in heavy-duty applications such as mining, construction, and agriculture, where their durability and strength allow for the handling of large, heavy loads. In the printing and packaging industries, precision steel rollers are essential for feeding, transferring, and processing materials with accuracy. Additionally, steel rollers find applications in machine tools, roller mills for crushing and grinding, and in the textile industry for fabric processing. The specific use of steel rollers is determined by their design, including diameter, surface finish, and bearing type, which can be tailored to meet the unique requirements of each application.
Rollers can be made from a variety of materials, each selected for its unique properties and suitability for specific applications. Steel is one of the most common materials due to its strength, durability, and versatility. Within the category of steel, there are different types, including carbon steel for general-purpose use and stainless steel for applications requiring corrosion resistance. Beyond steel, rollers can also be made from aluminum, which offers a lightweight alternative with good corrosion resistance, making it suitable for applications where weight is a concern. Plastic rollers are another option, often used in environments requiring low noise, low weight, or specific chemical resistances, such as in food processing or pharmaceutical industries. Rubber-coated rollers are used where grip and cushioning are important, such as in material handling and printing applications. Additionally, specialized materials like silicon, nylon, and polyurethane are used for rollers requiring specific properties like high temperature resistance, non-marking surfaces, or enhanced durability. The choice of material is critical to the roller’s performance, longevity, and compatibility with the materials it will be in contact with.
Last Updated on March 7, 2024 by Jordan Smith
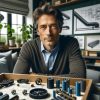
Jordan Smith, a seasoned professional with over 20 years of experience in the conveyor system industry. Jordan’s expertise lies in providing comprehensive solutions for conveyor rollers, belts, and accessories, catering to a wide range of industrial needs. From initial design and configuration to installation and meticulous troubleshooting, Jordan is adept at handling all aspects of conveyor system management. Whether you’re looking to upgrade your production line with efficient conveyor belts, require custom conveyor rollers for specific operations, or need expert advice on selecting the right conveyor accessories for your facility, Jordan is your reliable consultant. For any inquiries or assistance with conveyor system optimization, Jordan is available to share his wealth of knowledge and experience. Feel free to reach out at any time for professional guidance on all matters related to conveyor rollers, belts, and accessories.