When to Replace Lagged Head Pulley Components
A lagged head pulley is a crucial component in conveyor systems, designed to increase friction between the pulley and the conveyor belt. This enhanced grip prevents belt slippage, ensuring smooth and efficient operation. The lagging, typically made from rubber or ceramic, also protects the pulley from wear and tear caused by abrasive materials. By improving traction and extending the lifespan of the pulley, a lagged head pulley plays a vital role in maintaining the reliability and performance of conveyor systems in various industrial applications. Proper maintenance of lagged head pulleys is essential for optimal system efficiency.
Lagged Head Pulley Sizes
Lagged Head Pulley Sizes: Detailed Discussion on Available Sizes and Applications
Lagged head pulleys are critical components in conveyor systems, designed to improve traction, reduce slippage, and enhance the overall efficiency of material handling processes. The size of a lagged head pulley can significantly influence its performance and suitability for specific applications. In this section, we will explore the various sizes of lagged head pulleys available and their applications across different industries.
Small Lagged Head Pulleys
Small lagged head pulleys typically range from a few inches to one foot in diameter. These pulleys are designed for light to medium-duty applications where space constraints and lighter loads are prevalent.
Applications:
- Food Processing: Small lagged head pulleys are used in food processing lines to handle lightweight products such as baked goods, snacks, and packaged foods. The smaller size allows for precise control and smooth operation within compact machinery.
- Pharmaceuticals: In pharmaceutical manufacturing, small lagged head pulleys facilitate the transport of delicate items like pills, capsules, and medical devices, ensuring gentle handling and maintaining product integrity.
- Packaging: These pulleys are essential in packaging lines where they assist in the movement of small to medium-sized packages, ensuring consistent speed and positioning for accurate packaging processes.
Medium Lagged Head Pulleys
Medium-sized lagged head pulleys generally range from one to three feet in diameter. These pulleys are versatile and suitable for a wide range of medium-duty applications across various industries.
Applications:
- Manufacturing: Medium lagged head pulleys are commonly used in manufacturing plants to transport components and finished products along assembly lines. Their size provides a balance between load capacity and operational flexibility.
- Warehousing: In warehouses, these pulleys help move boxes, crates, and other packaged goods efficiently. The medium size accommodates a variety of belt widths and load types, making them ideal for general material handling tasks.
- Agriculture: These pulleys are employed in agricultural operations to handle materials such as grains, seeds, and produce. They support conveyor systems that transport agricultural products from harvesting points to processing facilities.
Large Lagged Head Pulleys
Large lagged head pulleys range from three feet to over six feet in diameter. These heavy-duty pulleys are designed for applications that require the transport of large volumes of materials and can handle substantial loads.
Applications:
- Mining: In the mining industry, large lagged head pulleys are essential for transporting mined materials such as coal, ore, and minerals. Their robust design allows them to withstand the harsh conditions and heavy loads typical of mining operations.
- Quarrying: These pulleys are used in quarries to move bulk materials like stone, gravel, and sand. The large size ensures that the conveyor systems can operate efficiently and handle high throughput rates.
- Bulk Material Handling: Large lagged head pulleys are crucial in bulk material handling facilities, such as ports and industrial plants, where they transport large quantities of raw materials like cement, chemicals, and grains over long distances.
Custom Sizes
In addition to standard sizes, custom-sized lagged head pulleys are available to meet specific operational requirements. Customization options include adjusting the diameter, width, and lagging material to suit unique applications and environmental conditions.
Applications:
- Specialized Manufacturing: Custom lagged head pulleys are designed for specialized manufacturing processes that require specific dimensions and performance characteristics.
- Research and Development: In R&D facilities, customized pulleys are used to test new materials and production techniques, ensuring that the conveyor systems can adapt to experimental conditions.
- Special Projects: Custom pulleys are employed in unique projects where conventional sizes do not meet the operational needs due to specific load requirements or spatial constraints.
Lagged head pulley sizes vary significantly to accommodate the diverse needs of different industries. Small, medium, and large pulleys each serve specific applications, ensuring efficient material handling and operational efficiency. Custom-sized pulleys offer additional flexibility for specialized operations, providing tailored solutions to meet unique requirements. Understanding the appropriate lagged head pulley sizes for your application is crucial for optimizing performance, enhancing productivity, and ensuring smooth operational flow.
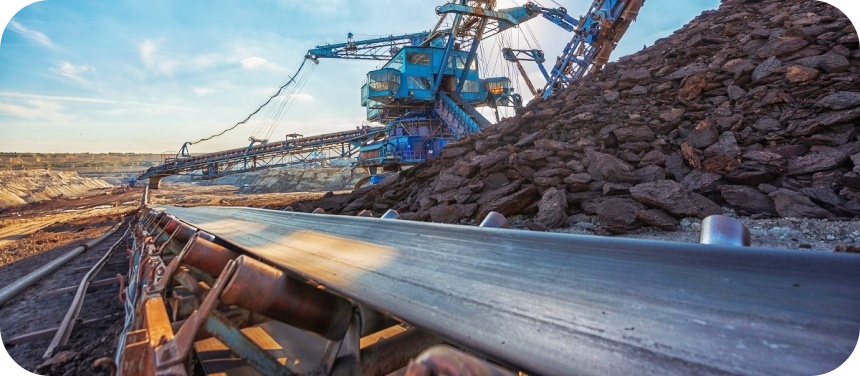
Lagged Head Pulley Replacement
Lagged Head Pulley Replacement: Guide to Maintaining Efficient Conveyor Operations
Replacing a lagged head pulley is a crucial maintenance task that ensures the continued efficiency and reliability of a conveyor system. Over time, wear and tear can degrade the performance of the pulley, leading to slippage, reduced traction, and potential downtime. This section provides a comprehensive guide on when and how to replace lagged head pulleys, ensuring optimal performance and longevity of your conveyor system.
When to Replace a Lagged Head Pulley
Identifying the right time to replace a lagged head pulley is essential for preventing unexpected failures and maintaining efficient operations. Here are some key indicators that a replacement is necessary:
- Excessive Wear and Tear: Inspect the lagging for signs of excessive wear, such as grooves, cracks, or chunks missing from the rubber or ceramic surface. Severe wear can compromise traction and lead to slippage.
- Decreased Performance: If you notice a significant decrease in the performance of the conveyor system, such as increased belt slippage, reduced material transport efficiency, or unusual noises, it may be time to replace the pulley.
- Visible Damage: Physical damage to the pulley, such as dents, bends, or misalignment, can affect its functionality. Regular inspections can help detect these issues early.
- Routine Maintenance Schedule: Adhering to a regular maintenance schedule that includes periodic replacement of pulleys can prevent failures and extend the life of the conveyor system.
How to Replace a Lagged Head Pulley
Replacing a lagged head pulley involves several steps to ensure a safe and effective process. Here is a step-by-step guide:
- Safety Precautions: Ensure that the conveyor system is shut down and locked out to prevent accidental startups. Wear appropriate personal protective equipment (PPE), such as gloves, safety glasses, and hard hats.
- Remove the Belt: Loosen the tension on the conveyor belt and carefully remove it from the pulley. Secure the belt in a safe position to prevent it from falling or getting damaged.
- Disconnect the Pulley: Remove any guarding or covers around the pulley. Disconnect the pulley from the drive mechanism, including any coupling, shaft, or mounting bolts.
- Extract the Pulley: Carefully extract the pulley from its position. Use appropriate lifting equipment, such as hoists or cranes, to handle large or heavy pulleys. Ensure that the pulley is supported securely during removal.
- Inspect the System: Before installing the new pulley, inspect the conveyor system for any additional wear or damage. Check the bearings, shafts, and mounting brackets for signs of wear or misalignment.
- Install the New Pulley: Position the new lagged head pulley in place and secure it to the drive mechanism. Ensure that all bolts and couplings are tightened to the manufacturer’s specifications.
- Reinstall the Belt: Reinstall the conveyor belt onto the new pulley and adjust the tension as needed. Ensure that the belt is aligned correctly to prevent tracking issues.
- Test the System: Perform a test run of the conveyor system to ensure that the new pulley is functioning correctly. Check for proper alignment, tension, and performance. Address any issues that arise during the test run.
Tips for Effective Replacement
- Use High-Quality Components: Always use high-quality replacement pulleys and components to ensure durability and reliability. Inferior products can lead to premature failures and increased maintenance costs.
- Follow Manufacturer Guidelines: Adhere to the manufacturer’s guidelines and specifications for pulley replacement. This ensures that the installation is done correctly and safely.
- Regular Inspections: Conduct regular inspections of the conveyor system to identify potential issues early. Addressing minor problems before they escalate can prevent costly downtime and repairs.
- Maintain Spare Parts Inventory: Keep an inventory of spare pulleys and essential components to facilitate quick replacements when needed. This minimizes downtime and ensures that the conveyor system can resume operations promptly.
Lagged head pulley replacement is a critical maintenance task that ensures the continued efficiency and reliability of conveyor systems. By identifying the right time for replacement and following a systematic approach, you can maintain optimal performance and prevent unexpected failures. Regular inspections, adherence to manufacturer guidelines, and the use of high-quality components are essential for successful pulley replacements. Ensuring that your conveyor system is equipped with well-maintained pulleys contributes to overall operational efficiency and productivity.
Lagged Head Pulley for Sale
Lagged Head Pulley for Sale: Tips on Finding and Purchasing
Finding the right lagged head pulley for sale involves considering various factors to ensure you purchase a product that meets your operational needs and budget. This section provides tips on where to find lagged head pulleys for sale, what to consider when buying, and how to ensure you make a wise investment.
Where to Find Lagged Head Pulleys for Sale
- Manufacturers’ Websites: Many manufacturers offer direct sales through their websites. Visiting the websites of reputable manufacturers allows you to explore their product range, specifications, and pricing. Purchasing directly from the manufacturer can also provide assurances of quality and support.
- Industrial Supply Companies: Industrial supply companies often stock a wide range of conveyor components, including lagged head pulleys. These suppliers may offer both new and used pulleys, providing options to suit different budgets and needs.
- Online Marketplaces: Platforms such as eBay, Amazon, and specialized industrial marketplaces list various conveyor components, including lagged head pulleys. These platforms provide the convenience of comparing multiple options, reading reviews, and making purchases from the comfort of your location.
- Local Distributors: Local distributors and dealers of industrial equipment can be a valuable resource for finding lagged head pulleys. These distributors often have in-depth knowledge of the products they sell and can provide personalized recommendations based on your specific requirements.
- Trade Shows and Industry Events: Attending trade shows and industry events allows you to connect with manufacturers and suppliers directly. These events provide opportunities to see products firsthand, discuss your needs with experts, and negotiate pricing.
What to Consider When Buying Lagged Head Pulleys
- Size and Specifications: Ensure that the lagged head pulley you choose matches the size and specifications required for your conveyor system. Consider factors such as diameter, width, and lagging material to ensure compatibility and optimal performance.
- Material Quality: The quality of the materials used in the pulley affects its durability and performance. High-quality lagging materials, such as rubber or ceramic, provide better traction and wear resistance, leading to longer service life.
- Brand Reputation: Purchasing from reputable brands and manufacturers ensures that you receive a high-quality product. Established brands have a track record of reliability and performance, reducing the risk of premature failures.
- Customization Options: Some applications may require custom-sized pulleys or specific features. Check if the supplier offers customization options to tailor the pulley to your unique requirements.
- Warranty and Support: Consider the warranty and support offered by the supplier. A comprehensive warranty and responsive customer support provide peace of mind and assistance in case of any issues with the pulley.
- Price and Budget: While price is an important consideration, it should not be the sole factor in your decision. Balance the cost with the quality and features of the pulley to ensure you get the best value for your investment.
Tips for a Successful Purchase
- Conduct Thorough Research: Take the time to research different suppliers, read reviews, and compare products. Thorough research helps you make an informed decision and choose a pulley that meets your needs.
- Request Quotes: Contact multiple suppliers to request quotes for the lagged head pulley you need. Comparing quotes allows you to find competitive pricing and identify any additional costs, such as shipping or customization fees.
- Verify Supplier Credentials: Ensure that the supplier is reputable and has a history of delivering high-quality products. Check for certifications, industry affiliations, and customer testimonials to verify their credibility.
- Inspect the Product: If possible, inspect the pulley before purchase to ensure it meets your quality standards. For online purchases, request detailed photos and specifications from the seller.
- Plan for Future Needs: Consider purchasing additional pulleys or spare parts to have on hand for future replacements. Planning for future needs can prevent downtime and ensure continuous operation.
Finding the right lagged head pulley for sale involves careful consideration of size, specifications, material quality, brand reputation, customization options, and price. By leveraging various sources such as manufacturers’ websites, industrial supply companies, online marketplaces, local distributors, and trade shows, you can find a suitable pulley that meets your operational needs. Conducting thorough research, requesting quotes, verifying supplier credentials, inspecting the product, and planning for future needs are essential steps to ensure a successful purchase. Investing in high-quality lagged head pulleys contributes to the efficiency and reliability of your conveyor system, enhancing overall productivity.
Lagged Head Pulley: Weld-On Head Pulley Lagging
Explanation of Weld-On Head Pulley Lagging
Weld-on head pulley lagging is a specialized type of lagging applied to conveyor head pulleys to enhance their performance and durability. Unlike traditional lagging methods that use adhesives to attach lagging materials, weld-on lagging involves welding metal or other materials directly onto the pulley surface. This creates a robust, permanent bond that can withstand extreme operating conditions.
Benefits of Weld-On Head Pulley Lagging
Enhanced Durability
One of the primary benefits of weld-on head pulley lagging is its enhanced durability. The welded attachment ensures that the lagging material remains securely in place, even under heavy loads and in harsh environments. This durability reduces the need for frequent maintenance and replacement, leading to lower long-term costs.
Improved Traction
Weld-on lagging significantly improves the traction between the conveyor belt and the pulley. This increased grip helps prevent belt slippage, ensuring efficient and reliable conveyor operation. Enhanced traction is particularly beneficial in applications involving wet, oily, or otherwise challenging conditions where traditional lagging might fail.
Resistance to Wear and Tear
The materials used in weld-on head pulley lagging are often chosen for their resistance to wear and tear. This resistance is crucial in industries such as mining, construction, and heavy manufacturing, where the conveyor systems are exposed to abrasive materials. Weld-on lagging protects the pulley surface, extending its lifespan and maintaining optimal performance.
How Weld-On Head Pulley Lagging is Applied
The process of applying weld-on head pulley lagging involves several critical steps to ensure a secure and effective installation:
Surface Preparation
The first step is to prepare the surface of the head pulley. This involves cleaning the pulley to remove any dirt, grease, or old lagging material. Proper surface preparation is essential for ensuring a strong bond between the pulley and the lagging material.
Cutting and Shaping
The lagging material, often in the form of metal plates or strips, is cut and shaped to fit the dimensions of the pulley. This step requires precision to ensure that the material covers the pulley surface adequately and fits securely.
Welding
The shaped lagging material is then welded onto the pulley surface. Skilled welders use specific techniques to ensure that the material is attached securely and evenly. The welding process creates a strong bond that can withstand the rigors of continuous operation.
Finishing
After welding, the lagged head pulley is inspected to ensure that the lagging material is securely attached and that there are no defects. Any rough edges or imperfections are smoothed out to ensure that the pulley operates smoothly and efficiently.
Weld-on head pulley lagging offers significant advantages in terms of durability, traction, and resistance to wear and tear. By securely attaching the lagging material through welding, this method ensures long-lasting performance even in the most demanding environments. Proper application of weld-on lagging is critical to maximizing these benefits and ensuring the reliable operation of conveyor systems.
Lagged Head Pulley: Types of Pulley Lagging
Pulley lagging is an essential aspect of conveyor system maintenance, designed to enhance the performance and longevity of the pulleys. There are several types of pulley lagging, each offering unique benefits and suited to different applications. This section provides an overview of the most common types of pulley lagging, including rubber, ceramic, and weld-on lagging.
Rubber Lagging
Description
Rubber lagging is one of the most widely used types of pulley lagging. It involves applying a layer of rubber to the surface of the pulley to increase friction and reduce slippage. Rubber lagging is available in various thicknesses and patterns, including diamond, herringbone, and plain.
Benefits
- Improved Traction: Rubber lagging provides excellent grip, preventing belt slippage and ensuring efficient operation.
- Shock Absorption: The rubber material helps absorb shocks and vibrations, reducing wear on the conveyor belt and pulley.
- Versatility: Rubber lagging is suitable for a wide range of applications, from light to heavy-duty conveyor systems.
Ceramic Lagging
Description
Ceramic lagging involves embedding ceramic tiles or segments into a rubber matrix applied to the pulley surface. The ceramic tiles provide additional hardness and resistance to wear, making this type of lagging ideal for harsh operating conditions.
Benefits
- Enhanced Durability: Ceramic lagging offers superior resistance to abrasion and wear, extending the life of the pulley and belt.
- High Friction: The ceramic tiles create a high-friction surface, significantly reducing belt slippage.
- Optimal Performance: Ceramic lagging is ideal for applications involving heavy loads, high speeds, and abrasive materials.
Weld-On Lagging
Description
Weld-on lagging, as described in the previous section, involves welding metal or other materials directly onto the pulley surface. This method provides a permanent and robust bond that can withstand extreme conditions.
Benefits
- Permanent Attachment: The welded bond ensures that the lagging material remains securely in place, even under heavy use.
- Superior Wear Resistance: Weld-on lagging materials are chosen for their resistance to wear and tear, making them suitable for the most demanding applications.
- High Traction: The lagging material provides excellent grip, improving the efficiency and reliability of the conveyor system.
Each type of pulley lagging offers unique benefits, and the choice depends on the specific needs of the application. Rubber lagging is versatile and cost-effective, making it suitable for a wide range of uses. Ceramic lagging provides enhanced durability and friction, ideal for harsh environments. Weld-on lagging offers the most robust and permanent solution, perfect for extreme conditions where other types of lagging may fail.
Understanding the different types of pulley lagging and their benefits is crucial for selecting the right solution for your conveyor system. Whether you choose rubber, ceramic, or weld-on lagging, ensuring proper installation and maintenance is key to maximizing the performance and lifespan of your conveyor components.
Lagged Head Pulley: What is Pulley Lagging
In-Depth Look at Pulley Lagging
Pulley lagging is a critical process in the maintenance of conveyor systems, designed to improve the performance and lifespan of the pulleys. This section provides an in-depth look at what pulley lagging is, its purpose, and how it enhances pulley performance.
What is Pulley Lagging?
Pulley lagging involves applying a layer of material to the surface of conveyor pulleys. This material can be rubber, ceramic, or metal, depending on the specific requirements of the application. The primary goal of lagging is to increase the friction between the pulley and the conveyor belt, preventing slippage and ensuring smooth operation. Lagging also protects the pulley from wear and damage caused by the abrasive materials transported on the conveyor belt.
Purpose of Pulley Lagging
Increased Friction
One of the main purposes of pulley lagging is to increase the friction between the pulley and the conveyor belt. This increased traction helps prevent belt slippage, which can lead to inefficient operation, increased wear on the belt and pulley, and potential system downtime. By improving grip, lagging ensures that the conveyor system operates smoothly and efficiently.
Protection from Wear
Pulley lagging protects the pulley surface from wear and tear caused by the abrasive materials transported on the conveyor belt. This protection is crucial in industries such as mining, construction, and heavy manufacturing, where the conveyor systems are exposed to harsh conditions. By reducing wear, lagging extends the lifespan of the pulleys and the entire conveyor system.
Shock Absorption
In addition to increasing friction and protecting the pulley, lagging also provides shock absorption. The lagging material helps absorb the impact of the conveyor belt, reducing vibrations and noise. This absorption reduces the stress on the conveyor components, minimizing wear and tear and enhancing the overall performance of the system.
How Pulley Lagging Improves Performance
Enhanced Efficiency
By preventing belt slippage and ensuring smooth operation, pulley lagging enhances the efficiency of the conveyor system. Improved traction means that the conveyor belt can move materials more effectively, reducing the energy required to operate the system and increasing productivity.
Reduced Maintenance Costs
Pulley lagging reduces the wear and tear on both the pulleys and the conveyor belt, leading to lower maintenance costs. The protection provided by the lagging material means that the pulleys and belts need to be replaced less frequently, resulting in cost savings over time. Additionally, reduced maintenance requirements mean less downtime, further increasing operational efficiency.
Learn more about our Conveyor Belt quality and performance.
Extended Equipment Lifespan
The protective benefits of pulley lagging extend the lifespan of the conveyor system components. By shielding the pulleys from wear and damage, lagging ensures that the equipment remains in good condition for longer. This extended lifespan reduces the need for frequent replacements and contributes to the overall cost-effectiveness of the conveyor system.
Pulley lagging is a vital process in the maintenance and operation of conveyor systems. By increasing friction, protecting the pulley from wear, and providing shock absorption, lagging improves the performance and lifespan of the conveyor components. Understanding the purpose and benefits of pulley lagging is essential for ensuring the efficient and reliable operation of conveyor systems in various industrial applications. Whether using rubber, ceramic, or weld-on lagging, proper application and maintenance are key to maximizing the advantages of this crucial process.
FAQs about Lagged Head Pulley
Head pulley lagging refers to the layer of material applied to the surface of the head pulley in a conveyor system. This layer, typically made of rubber or ceramic, is designed to increase the friction between the pulley and the conveyor belt. By improving traction, lagging helps to prevent belt slippage, which can lead to inefficient operation and increased wear and tear on the conveyor system. Additionally, lagging can protect the pulley from damage caused by abrasive materials, extending the lifespan of the equipment. Different types of lagging materials are available, each offering various benefits depending on the specific application and environmental conditions.
The purpose of a lagged pulley is to enhance the performance and longevity of a conveyor system. Lagging serves several important functions:
Increased Friction: By adding a layer of material with a high coefficient of friction, lagging improves the grip between the pulley and the conveyor belt. This increased traction helps to prevent belt slippage, ensuring smooth and efficient operation.
Protection: Lagging protects the surface of the pulley from wear and tear caused by the abrasive materials transported on the conveyor belt. This protection reduces the risk of damage and extends the life of the pulley.
Reduced Belt Wear: The improved grip provided by lagging reduces the stress and strain on the conveyor belt, minimizing wear and tear. This can lead to longer belt life and reduced maintenance costs.
Noise Reduction: Lagged pulleys can help to dampen vibrations and reduce noise generated by the conveyor system, contributing to a quieter working environment.
The lagging of belt pulleys involves applying a layer of material, such as rubber, ceramic, or polyurethane, to the surface of the pulleys in a conveyor system. This process enhances the pulley’s performance by increasing its friction with the conveyor belt, preventing slippage, and protecting the pulley from wear and damage. There are several types of pulley lagging, each designed to meet specific needs:
Rubber Lagging: Commonly used for general applications, rubber lagging provides good friction and is relatively cost-effective. It is suitable for both drive and non-drive pulleys.
Ceramic Lagging: Ideal for high-tension applications, ceramic lagging offers excellent wear resistance and increased friction. It is often used in mining and heavy-duty industrial settings where the conditions are harsh.
Polyurethane Lagging: Known for its durability and resistance to chemicals, polyurethane lagging is suitable for environments where exposure to oils, chemicals, and other corrosive substances is common.
Diamond Pattern Lagging: This type of lagging features a diamond-shaped pattern that enhances grip and reduces belt slippage, making it ideal for drive pulleys.
By selecting the appropriate type of lagging for the specific application, conveyor systems can achieve improved performance, reduced maintenance, and longer service life.
Lagging a pulley involves several steps to ensure that the process is done correctly and effectively. Here is a general guide on how to lag a pulley:
Preparation: Clean the surface of the pulley thoroughly to remove any dirt, grease, or old lagging material. This step is crucial to ensure proper adhesion of the new lagging material. Use appropriate cleaning agents and tools to achieve a clean surface.
Measurement and Cutting: Measure the circumference and width of the pulley to determine the size of the lagging material needed. Cut the lagging material to the appropriate dimensions, ensuring that it fits the pulley surface accurately.
Adhesive Application: Apply a suitable adhesive to both the pulley surface and the back of the lagging material. Ensure even coverage to promote strong adhesion. The type of adhesive used will depend on the lagging material and the operating conditions of the conveyor system.
Lagging Installation: Carefully position the lagging material onto the pulley, starting at one end and working your way around. Press the material firmly onto the pulley surface, ensuring that there are no air bubbles or gaps. Use a roller or similar tool to apply even pressure and secure the lagging in place.
Seam Sealing: If the lagging material has seams, seal them with an appropriate seam sealer to prevent moisture and debris from getting underneath the lagging. This step helps to prolong the life of the lagging and the pulley.
Curing and Setting: Allow the adhesive to cure and set according to the manufacturer’s instructions. This process may take several hours, during which the pulley should not be used.
Inspection and Testing: Once the adhesive has fully cured, inspect the lagging for any defects or areas that may need additional attention. Conduct a test run of the conveyor system to ensure that the lagging is functioning correctly and providing the desired traction and protection.
Last Updated on July 30, 2024 by Jordan Smith
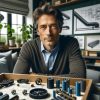
Jordan Smith, a seasoned professional with over 20 years of experience in the conveyor system industry. Jordan’s expertise lies in providing comprehensive solutions for conveyor rollers, belts, and accessories, catering to a wide range of industrial needs. From initial design and configuration to installation and meticulous troubleshooting, Jordan is adept at handling all aspects of conveyor system management. Whether you’re looking to upgrade your production line with efficient conveyor belts, require custom conveyor rollers for specific operations, or need expert advice on selecting the right conveyor accessories for your facility, Jordan is your reliable consultant. For any inquiries or assistance with conveyor system optimization, Jordan is available to share his wealth of knowledge and experience. Feel free to reach out at any time for professional guidance on all matters related to conveyor rollers, belts, and accessories.