Implement Sandwich Belt in Large Angle Belt Conveyor Systems
A large angle belt conveyor is a specialized type of conveyor designed to transport materials at steep angles. These conveyors are particularly significant in industries where space constraints or the need to move materials vertically are critical. The large angle belt conveyor is engineered to handle bulk materials efficiently, ensuring continuous operation even in challenging conditions. Its applications span various sectors, including mining, agriculture, and construction, where it helps in moving materials like ore, grain, and building supplies with ease. The design and functionality of large angle belt conveyors make them essential for optimizing productivity in these industries.
Conveyor Belt Angle Calculation for Large Angle Belt Conveyor
Calculating the conveyor belt angle is crucial for the optimal design and operation of a large angle belt conveyor. The angle of inclination determines the efficiency and capacity of material transport, influencing both operational costs and the lifespan of the conveyor system. Below, we delve into the detailed methods and considerations for calculating the conveyor belt angle in large angle belt conveyors.
Importance of Accurate Angle Calculation
Accurate calculation of the conveyor belt angle is essential for several reasons:
- Efficiency: The right angle ensures smooth and efficient material transport, minimizing spillage and reducing energy consumption.
- Capacity: A properly calculated angle maximizes the load-carrying capacity of the conveyor, optimizing throughput.
- Safety: Correct angle calculation helps prevent material rollback, which can cause blockages and safety hazards.
- Longevity: Proper angle determination reduces wear and tear on the conveyor components, extending the system’s operational life.
Basic Principles of Conveyor Belt Angle Calculation
1. Angle of Repose
The angle of repose of the transported material is a fundamental factor in calculating the conveyor belt angle. It is the steepest angle at which a pile of material remains stable without sliding. Understanding the angle of repose helps in determining the maximum safe incline for the conveyor belt.
2. Material Characteristics
The physical properties of the material, such as particle size, shape, moisture content, and bulk density, significantly influence the conveyor belt angle. Different materials have different flow properties, which must be considered to ensure efficient transport.
3. Belt Type and Surface
The type of belt and its surface characteristics also play a crucial role in angle calculation. For large angle belt conveyors, belts with textured surfaces or cleats (like chevron patterns) are often used to increase grip and prevent material slippage.
Methods for Calculating Conveyor Belt Angle
1. Empirical Formulas
Several empirical formulas have been developed based on extensive testing and industry experience. These formulas take into account material properties, belt type, and operational parameters to estimate the optimal conveyor belt angle.
2. Software Tools
Modern conveyor design software provides advanced tools for angle calculation. These tools use complex algorithms and simulations to analyze various factors and predict the best angle for the conveyor system. They also allow for the adjustment of parameters and real-time analysis to optimize the design.
3. Experimental Methods
In some cases, experimental methods are employed to determine the conveyor belt angle. This involves setting up test rigs with different angles and running trials with the actual material to observe behavior and performance. This method is particularly useful for unique materials or complex applications.
Considerations for Conveyor Belt Angle Calculation
1. Incline Limitations
While large angle belt conveyors are designed to operate at steep angles, there are practical limitations. The maximum incline angle is typically influenced by the material’s angle of repose and the belt’s design. Ensuring that the angle remains within these limits is critical for safe and efficient operation.
2. Load Distribution
The distribution of material load on the conveyor belt affects the angle calculation. Uniform loading helps maintain stability and reduces the risk of belt misalignment or excessive wear.
3. Environmental Factors
Environmental conditions, such as temperature, humidity, and exposure to elements, can impact the material’s behavior and, consequently, the conveyor belt angle. These factors should be considered during the design phase to ensure reliable operation under varying conditions.
Calculating the conveyor belt angle for large angle belt conveyors is a complex but essential process. By considering factors such as the angle of repose, material characteristics, belt type, and environmental conditions, operators can ensure efficient and safe material transport. Utilizing empirical formulas, software tools, and experimental methods can help achieve accurate calculations, optimizing the conveyor system’s performance and longevity.
Benefits of Using Large Angle Belt Conveyor
The implementation of large angle belt conveyors brings numerous advantages to various industries. These conveyors are designed to handle steep inclines and challenging transport conditions, providing efficient and reliable material movement. In this section, we explore the benefits of using large angle belt conveyors and their impact on industrial operations.
Increased Efficiency
Large angle belt conveyors are engineered to transport materials at steep angles, which enhances efficiency in several ways:
- Space Optimization: By allowing vertical or steep inclined transport, these conveyors minimize the footprint required for material movement. This is particularly beneficial in space-constrained environments such as underground mines or urban construction sites.
- Continuous Operation: The design of large angle belt conveyors ensures continuous material flow, reducing downtime and increasing overall productivity. This is crucial for industries that require consistent and uninterrupted material supply.
Versatility in Applications
The versatility of large angle belt conveyors makes them suitable for a wide range of applications:
- Mining: These conveyors are ideal for transporting ores, minerals, and overburden in mining operations, handling the rough and abrasive materials typically encountered in this industry.
- Agriculture: In the agricultural sector, large angle belt conveyors are used for moving grain, seeds, and other bulk agricultural products, facilitating efficient storage and processing.
- Construction: Construction sites benefit from the ability to transport materials such as sand, gravel, and cement at steep angles, optimizing space and reducing manual labor.
Cost-Effective Solution
Investing in large angle belt conveyors can lead to significant cost savings:
- Reduced Labor Costs: By automating the material transport process, these conveyors minimize the need for manual labor, leading to lower labor costs and increased operational efficiency.
- Lower Maintenance Costs: The robust design of large angle belt conveyors ensures durability and reliability, reducing the frequency and cost of maintenance. This is particularly important in harsh industrial environments where equipment is subjected to heavy use.
Enhanced Safety
Large angle belt conveyors contribute to a safer work environment:
- Reduced Manual Handling: By automating material transport, these conveyors reduce the need for manual handling, lowering the risk of workplace injuries associated with lifting and moving heavy materials.
- Stable Operation: The design features of large angle belt conveyors, such as textured surfaces and cleats, ensure stable operation and prevent material rollback, enhancing overall safety.
Environmental Benefits
Large angle belt conveyors offer several environmental benefits:
- Reduced Emissions: By minimizing the need for truck transport, these conveyors help reduce greenhouse gas emissions and lower the carbon footprint of material transport operations.
- Energy Efficiency: Modern large angle belt conveyors are designed to be energy-efficient, utilizing advanced technologies to optimize power consumption and reduce energy costs.
Scalability and Flexibility
The scalability and flexibility of large angle belt conveyors make them a valuable asset for growing industries:
- Expandable Systems: These conveyors can be easily expanded or modified to accommodate changes in production capacity or transport requirements, providing long-term value and adaptability.
- Customizable Design: Large angle belt conveyors can be customized to meet specific operational needs, including adjustments in length, angle, and load capacity, ensuring optimal performance for various applications.
The benefits of using large angle belt conveyors are extensive, ranging from increased efficiency and versatility to cost savings and enhanced safety. By optimizing space, reducing labor and maintenance costs, and providing a scalable and flexible solution, these conveyors offer significant advantages for various industries. Their environmental benefits further underscore their value in modern industrial operations. As industries continue to evolve, the implementation of large angle belt conveyors will play a critical role in enhancing productivity and sustainability.
Applications of Large Angle Belt Conveyor in Industry
Large angle belt conveyors are utilized in a wide range of industrial applications due to their ability to transport materials efficiently at steep inclines. Their unique design and operational capabilities make them suitable for various sectors, enhancing productivity and optimizing material handling processes. This section examines the different industrial applications of large angle belt conveyors and their role in improving efficiency.
Mining Industry
1. Ore Transport
Large angle belt conveyors are extensively used in the mining industry for transporting ores from extraction sites to processing plants. The ability to handle steep inclines allows for more direct transport routes, reducing travel time and operational costs. These conveyors are designed to withstand the harsh conditions of mining operations, ensuring reliable performance and durability.
2. Overburden Removal
In open-pit mining, large angle belt conveyors are employed to remove overburden (the layer of soil and rock covering valuable minerals). The steep incline capability of these conveyors enables efficient overburden removal, facilitating access to the mineral deposits and enhancing overall mining productivity.
Agriculture Industry
1. Grain Handling
In the agricultural sector, large angle belt conveyors are used for transporting grain from storage silos to processing units. The steep incline feature allows for vertical movement of grain, optimizing space utilization within storage facilities and ensuring efficient grain handling.
2. Bulk Product Transport
Large angle belt conveyors are also used for transporting other bulk agricultural products, such as seeds, fertilizers, and animal feed. Their ability to handle large volumes of materials at steep angles makes them ideal for agricultural operations, improving efficiency and reducing manual labor requirements.
Construction Industry
1. Material Transport
In construction, large angle belt conveyors are used to transport materials such as sand, gravel, cement, and concrete. The steep incline capability allows for efficient vertical movement of materials, reducing the need for manual handling and enhancing productivity on construction sites.
2. Waste Management
Large angle belt conveyors are also employed in construction waste management, transporting debris and waste materials from demolition sites to disposal areas. Their robust design ensures reliable performance in handling heavy and abrasive materials, contributing to efficient waste management practices.
Manufacturing Industry
1. Assembly Line Integration
In manufacturing, large angle belt conveyors are integrated into assembly lines to transport components and finished products. The ability to handle steep inclines allows for efficient vertical movement within the production facility, optimizing space and streamlining operations.
2. Packaging and Distribution
Large angle belt conveyors are used in packaging and distribution centers to move packaged goods to storage or loading areas. Their versatility and efficiency in handling different types of materials make them essential for smooth and continuous operations in manufacturing logistics.
Energy Sector
1. Coal Handling
In power plants, large angle belt conveyors are used for transporting coal from storage areas to the boilers. The ability to move coal at steep angles reduces the footprint required for coal handling systems, enhancing the overall efficiency of power generation operations.
2. Biomass Transport
Large angle belt conveyors are also utilized in biomass power plants to transport biomass materials, such as wood chips and agricultural waste, to the combustion chambers. The steep incline capability ensures efficient transport and continuous feed of biomass, supporting sustainable energy production.
Environmental Management
1. Recycling Operations
In recycling facilities, large angle belt conveyors are used to transport recyclable materials, such as paper, plastic, and metal, to sorting and processing units. The ability to handle diverse materials and steep inclines makes these conveyors ideal for efficient recycling operations.
2. Waste Treatment
Large angle belt conveyors are employed in waste treatment plants to move waste materials through various stages of treatment and processing. Their robust design and efficient operation contribute to effective waste management and environmental sustainability.
Transportation and Logistics
1. Port Operations
In ports and harbors, large angle belt conveyors are used to transport bulk materials, such as grain, coal, and minerals, from ships to storage areas. The steep incline capability allows for efficient vertical movement, optimizing space utilization and enhancing port operations.
2. Warehousing
Large angle belt conveyors are used in warehouses to move goods from loading docks to storage areas. Their ability to handle different types of materials and steep inclines makes them essential for efficient warehousing and inventory management.
Food Processing Industry
1. Raw Material Handling
In food processing plants, large angle belt conveyors are used to transport raw materials, such as grains, fruits, and vegetables, to processing units. The steep incline feature allows for efficient vertical movement of materials, optimizing space and improving processing efficiency.
2. Finished Product Transport
Large angle belt conveyors are also used to move finished food products to packaging and distribution areas. Their versatility and efficiency in handling different types of materials make them essential for smooth and continuous food processing operations.
Pharmaceutical Industry
1. Material Handling
In pharmaceutical manufacturing, large angle belt conveyors are used to transport raw materials and intermediate products through various stages of production. The ability to handle steep inclines and different types of materials ensures efficient material flow and optimized production processes.
2. Packaging and Distribution
Large angle belt conveyors are employed in pharmaceutical packaging and distribution centers to move packaged products to storage or loading areas. Their efficiency and reliability contribute to smooth and continuous operations in pharmaceutical logistics.
Large angle belt conveyors are versatile and efficient systems that play a critical role in various industrial applications. From mining and agriculture to construction and manufacturing, these conveyors enhance productivity, optimize space, and reduce manual labor requirements. Their ability to handle steep inclines and diverse materials makes them essential for modern industrial operations. As industries continue to evolve, the adoption of large angle belt conveyor will be pivotal in supporting efficient and sustainable material handling practices.
Design Features of Large Angle Belt Conveyor
Large angle belt conveyors, often referred to as steep angle conveyors or high-angle conveyors, are designed to transport materials efficiently at steep inclines. This capability is essential in various industries such as mining, construction, and agriculture, where space constraints and terrain challenges make conventional conveyor systems impractical. Here, we delve into the key design features that make large angle belt conveyors effective and reliable.
1. Belt Design and Material:
The belt is the most critical component of a large angle belt conveyor. It must be robust enough to handle the stresses associated with transporting materials at steep angles. Typically, the belts used in these conveyors are made from high-strength materials like steel-reinforced rubber or textile-reinforced rubber composites. These materials provide the necessary tensile strength and flexibility to withstand the operational demands.
Moreover, the belts are often equipped with a special surface texture or pattern, such as a chevron pattern, to enhance grip and prevent material slippage. This is crucial when dealing with granular or powdered materials that might otherwise slide back down the belt.
2. Cleats and Sidewalls:
To further prevent material slippage, large angle belt conveyors are fitted with cleats and sidewalls. Cleats are transverse barriers affixed to the belt at regular intervals. They help to create compartments that carry materials up steep inclines. Sidewalls, on the other hand, are raised edges along the sides of the belt. They prevent materials from spilling over the edges, ensuring a smooth and controlled transport process.
The design and spacing of cleats are critical, as they must balance between providing adequate material containment and maintaining belt flexibility. Sidewalls are generally made from flexible yet durable materials that can withstand the dynamic stresses encountered during operation.
3. Belt Tracking and Alignment:
Proper belt tracking and alignment are paramount to the effective operation of large angle belt conveyors. Misalignment can lead to excessive wear, increased energy consumption, and even belt failure. To address this, these conveyors are equipped with tracking and alignment devices, such as crowned pulleys, edge guide rollers, and automatic tracking sensors.
These devices help ensure that the belt runs centrally on the conveyor structure, reducing the risk of damage and prolonging the lifespan of the system. Automatic tracking systems are particularly beneficial as they continuously monitor and adjust the belt position, providing a real-time solution to potential misalignment issues.
4. Drive and Tensioning Systems:
The drive system of a large angle belt conveyor must be powerful enough to overcome the gravitational forces associated with steep inclines. This often necessitates the use of multiple drive units placed strategically along the conveyor route. These drives are typically electric motors connected to the belt via gear reducers and couplings.
Tensioning systems are equally important. They maintain the correct belt tension to ensure optimal contact between the belt and drive pulleys, which is essential for efficient power transmission. Common tensioning methods include gravity take-up systems, hydraulic tensioners, and screw-adjusted tensioners. Each method has its advantages, with the choice depending on the specific requirements of the conveyor system.
5. Structural Integrity:
Large angle belt conveyors are subjected to significant mechanical stresses, particularly at the transition points where the conveyor changes direction or inclination. Therefore, the structural integrity of the conveyor framework is crucial. It must be robust enough to withstand these stresses without excessive deflection or vibration, which could lead to operational inefficiencies or failure.
Typically, the framework is constructed from high-strength steel or aluminum alloys. It is designed to provide maximum support while minimizing weight, which is especially important in portable or mobile conveyor systems.
6. Safety Features:
Safety is a paramount concern in the design of large angle belt conveyors. To mitigate the risks associated with steep angle transport, these conveyors are equipped with various safety features. These include emergency stop systems, belt misalignment detectors, and anti-rollback mechanisms.
Emergency stop systems allow operators to halt the conveyor immediately in case of an emergency. Belt misalignment detectors provide early warning of potential tracking issues, allowing for prompt corrective action. Anti-rollback mechanisms, such as backstop bearings, prevent the belt from rolling backward in the event of a power failure, thereby preventing material spillage and potential injuries.
Implementing Sandwich Belt Conveyor in Large Angle Belt Conveyor Systems
The integration of sandwich belt conveyors into large angle belt conveyor systems represents a significant advancement in the handling of bulk materials. Sandwich belt conveyors are a unique type of conveyor that uses two belts, one on top and one on the bottom, to sandwich the material being transported. This configuration provides several benefits that enhance the performance and reliability of large angle belt conveyors.
1. Enhanced Material Containment:
One of the primary benefits of sandwich belt conveyors is their superior material containment. By sandwiching the material between two belts, these conveyors virtually eliminate the risk of material spillage. This is particularly advantageous in large angle belt conveyor systems, where maintaining material stability is challenging due to steep inclines.
The top and bottom belts exert a consistent pressure on the material, ensuring it remains securely in place throughout the transport process. This is especially useful when handling fine or powdered materials that are prone to slipping or dispersing.
2. Increased Transport Capacity:
Sandwich belt conveyors can significantly increase the transport capacity of large angle belt conveyor systems. The dual-belt design allows for a higher load capacity compared to single-belt systems. This is because the material is more securely held in place, allowing for steeper inclines and higher throughput rates.
This increased capacity is particularly beneficial in industries such as mining and quarrying, where large volumes of material need to be transported efficiently and quickly. By implementing sandwich belt conveyors, operators can achieve higher productivity and operational efficiency.
3. Improved Energy Efficiency:
Energy efficiency is a critical consideration in the design and operation of conveyor systems. Sandwich belt conveyors contribute to improved energy efficiency in large angle belt conveyor systems by reducing the frictional forces acting on the material. The dual-belt design ensures that the material is held securely, minimizing the slipping and rolling that can increase energy consumption.
Moreover, the consistent pressure applied by the top and bottom belts helps to maintain a steady flow of material, reducing the need for frequent starts and stops that can consume additional energy. This results in a more efficient and cost-effective operation.
4. Versatility and Flexibility:
Sandwich belt conveyors offer a high degree of versatility and flexibility. They can be easily integrated into existing large angle belt conveyor systems, allowing for seamless upgrades and expansions. This flexibility is particularly useful in industries where material handling requirements can change rapidly, such as construction and agriculture.
Additionally, sandwich belt conveyors can handle a wide range of materials, from fine powders to large aggregates. This versatility makes them an ideal solution for applications that involve diverse material types and transport conditions.
5. Reduced Maintenance Requirements:
Maintenance is a critical factor in the overall cost and reliability of conveyor systems. Sandwich belt conveyors can reduce maintenance requirements by minimizing wear and tear on the belts and other components. The dual-belt design distributes the load evenly, reducing the stress on individual components and extending their lifespan.
Furthermore, the improved material containment provided by sandwich belt conveyors reduces the accumulation of debris and spillage, which can cause wear and require frequent cleaning. This leads to lower maintenance costs and less downtime, enhancing the overall efficiency of the system.
The Role of Chevron Pattern Belt in Large Angle Belt Conveyor
The chevron pattern belt is a key component in the performance and efficiency of large angle belt conveyors. This belt design features a raised pattern of ridges, typically in a V-shaped or U-shaped configuration, that enhances the belt’s grip and material handling capabilities. Here, we explore the role of the chevron pattern belt in large angle belt conveyors and how it contributes to their overall effectiveness.
1. Improved Material Grip:
The primary function of the chevron pattern belt is to improve the grip on the transported material. The raised ridges create additional friction between the belt and the material, preventing slippage, especially on steep inclines. This enhanced grip is crucial for maintaining a consistent flow of material and preventing rollbacks, which can disrupt the operation and cause spillage.
The chevron pattern is particularly effective when handling granular or loose materials, such as sand, gravel, and agricultural products. The pattern helps to anchor these materials in place, ensuring they are transported smoothly and efficiently.
2. Enhanced Stability on Inclines:
Large angle belt conveyors often operate at steep inclines where conventional flat belts would struggle to maintain material stability. The chevron pattern belt addresses this challenge by providing additional traction that keeps the material in place even at high angles.
This enhanced stability is achieved through the unique design of the chevron pattern, which increases the contact area between the belt and the material. This larger contact area generates more friction, which helps to counteract the gravitational forces acting on the material and prevents it from slipping backward.
3. Versatility in Handling Different Materials:
The chevron pattern belt is highly versatile and can handle a wide range of materials, including fine powders, bulk solids, and large aggregates. This versatility makes it an ideal choice for large angle belt conveyors used in diverse industries such as mining, construction, and agriculture.
For example, in the mining industry, chevron pattern belts are used to transport ore and other minerals up steep inclines. In agriculture, they are used to move grain and other crops efficiently. The ability to handle different materials effectively enhances the operational flexibility and utility of large angle belt conveyors.
4. Reduced Material Spillage:
Material spillage is a common issue in conveyor systems, particularly when transporting materials at steep angles. The chevron pattern belt helps to mitigate this problem by providing additional containment for the material. The raised ridges act as barriers that prevent the material from sliding off the sides of the belt, reducing spillage and ensuring a cleaner operation.
This reduction in spillage not only improves the efficiency of the conveyor system but also reduces the need for cleanup and maintenance. This leads to lower operational costs and a safer working environment.
5. Durability and Longevity:
Chevron pattern belts are designed to be durable and long-lasting. The materials used in their construction, such as reinforced rubber and synthetic fibers, are chosen for their ability to withstand the harsh conditions often encountered in large angle belt conveyor applications.
The raised ridges of the chevron pattern also help to distribute the wear and tear more evenly across the belt surface. This reduces the likelihood of localized wear and extends the overall lifespan of the belt. As a result, operators can enjoy a more reliable and cost-effective conveyor system.
6. Customizable Designs:
Chevron pattern belts can be customized to suit specific application requirements. The height, spacing, and angle of the ridges can be adjusted to optimize the performance for different materials and transport conditions. This customization ensures that the belt provides the best possible grip and stability for each specific application.
For instance, materials with a tendency to roll or slide may require higher and closer-spaced ridges, while more stable materials may benefit from a lower, more widely spaced pattern. This ability to tailor the belt design enhances the versatility and effectiveness of large angle belt conveyors.
7. Integration with Other Conveyor Components:
The chevron pattern belt integrates seamlessly with other components of the large angle belt conveyor system. This includes drive and tensioning systems, tracking and alignment devices, and safety features. The belt’s design ensures that it works harmoniously with these components to provide a smooth and efficient transport process.
For example, the raised ridges of the chevron pattern belt are compatible with various types of cleats and sidewalls, enhancing material containment and stability. Additionally, the belt’s enhanced grip and stability reduce the need for frequent adjustments to the tracking and alignment devices, resulting in a more reliable and low-maintenance system.
The design features of large angle belt conveyors, the integration of sandwich belt conveyors, and the role of chevron pattern belts collectively contribute to the effectiveness and reliability of these systems. These innovations address the challenges of transporting materials at steep inclines, enhancing operational efficiency, and reducing maintenance requirements. As industries continue to seek more efficient and versatile material handling solutions, large angle belt conveyors, with their advanced design features and components, are poised to play an increasingly important role.
FAQs about Large Angle Belt Conveyor
The maximum angle for a belt conveyor, often referred to as the “angle of inclination” or “angle of repose,” depends on the material being transported and the belt design. Typically, conventional belt conveyors have a maximum angle of around 18 to 20 degrees. However, specialized belts with cleats or sidewalls can handle steeper inclines, sometimes up to 30 degrees or more. For extremely steep inclines, high angle belt conveyors are used, which can manage angles up to 90 degrees.
A high angle belt conveyor is a type of conveyor system designed to move materials at steep angles, often exceeding the limits of conventional conveyors. These conveyors can handle inclines up to 90 degrees, enabling vertical lifting of materials. High angle belt conveyors use specially designed belts with cleats or sidewalls to prevent material from slipping back. They are commonly used in mining, construction, and other industries where space constraints or the need for vertical transport make traditional conveyors impractical.
Conveyor angles vary depending on the type and design of the conveyor system. Conventional belt conveyors typically operate at angles between 0 and 20 degrees. Inclined belt conveyors can handle angles up to 30 degrees. For steeper inclines, high angle belt conveyors come into play, managing angles between 30 and 90 degrees. The choice of conveyor angle is influenced by factors such as material type, belt design, and the specific application requirements.
Creating a satisfactory 90 degree conveyor belt requires careful consideration of several factors:
Belt Design: Use a belt with appropriate cleats or sidewalls to prevent material rollback.
Material Handling: Ensure the material is suitable for vertical transport, with no risk of spillage or degradation.
Support and Stability: Implement strong support structures to maintain belt stability and alignment.
Motor and Drive System: Choose a motor and drive system capable of handling the increased load and stress of vertical lifting.
Safety Measures: Incorporate safety features such as emergency stops, guards, and sensors to protect operators and equipment. By addressing these aspects, a 90 degree conveyor belt can efficiently and reliably move materials in a vertical direction.
Last Updated on July 23, 2024 by Jordan Smith
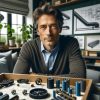
Jordan Smith, a seasoned professional with over 20 years of experience in the conveyor system industry. Jordan’s expertise lies in providing comprehensive solutions for conveyor rollers, belts, and accessories, catering to a wide range of industrial needs. From initial design and configuration to installation and meticulous troubleshooting, Jordan is adept at handling all aspects of conveyor system management. Whether you’re looking to upgrade your production line with efficient conveyor belts, require custom conveyor rollers for specific operations, or need expert advice on selecting the right conveyor accessories for your facility, Jordan is your reliable consultant. For any inquiries or assistance with conveyor system optimization, Jordan is available to share his wealth of knowledge and experience. Feel free to reach out at any time for professional guidance on all matters related to conveyor rollers, belts, and accessories.