Sizing and Customization of Large Conveyor Rollers
Conveyor rollers are pivotal components in the manufacturing and distribution sectors, facilitating the smooth and efficient transport of goods across numerous industries. The use of large conveyor rollers, in particular, has revolutionized the handling of heavy or bulky materials, ensuring that operations are both swift and less labor-intensive. These rollers are instrumental in industries such as mining, agriculture, automotive, and packaging, where they significantly enhance productivity and operational efficiency. By supporting substantial weights and reducing the friction and energy required to move objects, large conveyor rollers contribute to a more streamlined and cost-effective production process. This introduction delves into the critical roles and widespread applications of these robust systems in various commercial environments.
What are Large Conveyor Rollers
Conveyor rollers are cylindrical devices used in conveyor systems to support and move goods along a predefined path. They are designed to rotate with minimal friction, which helps in transporting items efficiently across various distances. Large conveyor rollers, in particular, are vital for operations that involve heavy or large-scale materials. These rollers are engineered to support higher loads and reduce operational stress, making them indispensable in industries where bulk handling and extensive movement of goods are routine.
The significance of large roller conveyor can be appreciated through several key examples:
- Mining Industry: In the mining sector, large conveyor rollers are used to transport materials such as ore and coal over long distances from the mining site to processing facilities. Their robust construction helps withstand the abrasive nature of raw materials and the outdoor environment.
- Port and Shipping Operations: Ports utilize large conveyor rollers to move bulk commodities like grains, ores, and coal onto ships. Their ability to handle enormous weights efficiently speeds up loading and unloading processes, reducing docking time.
- Steel Manufacturing: In steel mills, large conveyor rollers are essential for moving heavy steel products between different stages of production, from melting to rolling and finishing. The rollers must endure high temperatures and heavy loads, demonstrating their resilience and durability.
- Automotive Assembly Lines: These rollers are used to move parts and assembled vehicles through various stations. Large conveyor rollers facilitate the smooth transition of car components and fully assembled cars through the production line, ensuring a steady workflow and minimizing the risk of damage.
Understanding the functionalities and the critical nature of large conveyor rollers highlights their importance in maintaining efficient, continuous, and reliable operations across diverse industrial landscapes. Their ability to handle significant weights and operate under strenuous conditions is what makes them a cornerstone of modern industrial operations.
Characteristics and Advantages of Extra-Large Conveyor Rollers
Extra-large conveyor rollers are designed to handle exceptionally heavy loads and large-scale operations, distinguishing themselves by their oversized diameter and robust build. These features are critical for industries where both the weight and volume of materials are significantly higher than average. The advantages of extra-large conveyor rollers are numerous, contributing not only to operational efficiency but also to the longevity and reliability of the conveyor system.
Characteristics and Advantages:
- Enhanced Load Capacity: Extra-large conveyor rollers are built to support weights that standard rollers cannot, reducing the strain on the conveyor system and minimizing wear and tear.
- Reduced Maintenance Needs: Due to their robust construction, these rollers often require less frequent maintenance, helping to cut downtime and maintenance costs in industrial settings.
- Improved Stability and Safety: The larger surface area of extra-large rollers provides better stability for moving large or uneven loads, which enhances safety by preventing slips or misalignments.
- Versatility in Handling Diverse Materials: These rollers can accommodate a variety of materials, from heavy machinery parts to bulk commodities, making them versatile components in numerous industrial applications.
Specific Applications and Industry Use-Cases:
- Bulk Material Handling in Quarries and Mining: In the mining industry, extra-large conveyor rollers are used to transport large volumes of extracted materials, such as rock and ore, from the excavation sites to the processing area or storage facilities.
- Cargo Loading in Maritime Operations: Ports utilize extra-large conveyor rollers for the loading and unloading of heavy bulk goods such as metals, minerals, and grains from cargo ships, facilitating efficient dockside logistics.
- Aircraft Assembly and Transportation: In the aerospace industry, these rollers are crucial for the assembly lines where large parts of aircraft, such as fuselage sections and wings, need to be moved smoothly through various stages of assembly.
- Handling Large Paper Rolls in Pulp and Paper Mills: The pulp and paper industry relies on extra-large conveyor rollers to manage and transport huge rolls of paper through the production process, from the press section to the cutter.
The inclusion of extra-large conveyor rollers in these diverse industrial applications underscores their essential role in enhancing operational efficiency, ensuring safety, and reducing operational costs across various sectors. These rollers not only support the heavy-duty requirements but also adapt to the specific needs of different industries, proving their versatility and importance in modern industrial operations.
Heavy-Duty Features of Large Conveyor Rollers
Heavy-duty large conveyor rollers are engineered to endure the most demanding industrial conditions, offering both durability and efficiency. These rollers are designed with robust materials and a reinforced structure to withstand high loads and continuous operation, which are crucial in heavy-duty applications. The distinct characteristics and benefits of these rollers not only enhance productivity but also extend the equipment’s lifespan.
Description, Features, and Benefits:
- Enhanced Durability: Made from high-grade steel or reinforced composites, large conveyor rollers are designed to resist wear, corrosion, and deformation under heavy loads.
- Increased Load Capacity: These rollers can handle significantly more weight compared to standard rollers, facilitating the movement of heavy goods without compromising speed or safety.
- Reduced Operational Noise: Heavy-duty large conveyor rollers often feature precision bearings and smoother surfaces to minimize operational noise, an important factor in maintaining a more pleasant and compliant working environment.
- Low Maintenance Requirement: Due to their robust construction and the use of high-quality materials, these rollers require less frequent replacement and maintenance, thus reducing downtime and operational costs.
Role in High-Capacity and Rigorous Industrial Environments:
Large conveyor rollers play a pivotal role in environments where high-capacity and rigorous conditions are standard. For instance:
- Automotive Manufacturing: These rollers are used on assembly lines where they must support heavy auto parts and complete vehicles moving through the production process.
- Heavy Machinery Production: In the manufacture of heavy machinery, large conveyor rollers facilitate the transport of heavy components and assembled machines from one stage of production to another.
- Mining and Mineral Processing: The mining industry relies on these rollers to transport raw extracted materials, often under extreme conditions of dust, moisture, and varying temperatures.
- Logistics and Freight Terminals: In freight and logistics hubs, heavy-duty rollers are crucial for moving large containers and pallets of goods rapidly and efficiently from storage areas to loading docks.
In these high-capacity and rigorous settings, the reliability, strength, and efficiency of large conveyor rollers are key to maintaining continuous operations, minimizing disruptions, and ensuring that productivity targets are met. Their ability to perform under pressure and handle the intensive demands of industrial environments makes them indispensable in sectors where downtime can result in significant financial losses.
Industrial Applications of Large Conveyor Rollers
Industrial-grade large roller conveyor are tailored to meet the specific demands of various sectors that require the continuous movement of materials at a large scale. These rollers are constructed with durability and efficiency in mind, employing advanced materials and technology to ensure optimal performance under industrial conditions.
Overview of Build and Functionalities:
Large conveyor rollers used in industrial applications are typically made from robust materials like heavy-duty steel or specialized alloys designed to withstand harsh environments, including exposure to chemicals, extreme temperatures, and abrasive materials. The design of these rollers often includes thick-walled tubing and reinforced bearing housings to support greater loads and resist bending or deformation during operation.
The functionalities of these rollers are enhanced by precision engineering that ensures reduced friction and efficient load distribution. This allows the rollers to operate smoothly under substantial weight and at higher speeds without significant wear. The surfaces of these rollers might also be treated with coatings such as rubber, polyurethane, or other composites to enhance grip and reduce slippage of materials being transported.
Key Functional Benefits:
- High Load Capacity: Large conveyor rollers are specifically designed to handle more significant weights, crucial for industries such as mining, steel production, and bulk goods handling.
- Durability in Tough Environments: The construction materials and techniques used in these rollers enable them to resist the corrosive and abrasive conditions found in many industrial settings, prolonging their lifespan and reducing the need for frequent replacements.
- Efficiency in Operation: Enhanced design features like precision bearings and balanced rolling mechanisms ensure that these rollers deliver high efficiency. This contributes to reduced energy consumption and faster processing times, vital for maintaining productivity in fast-paced industrial operations.
- Customization Options: Given the varied needs across different industries, large conveyor rollers can be customized in terms of size, material, surface treatment, and bearing types, making them highly adaptable to specific industrial requirements.
By integrating large conveyor rollers into industrial conveyor systems, companies can achieve higher throughput and more reliable material handling, crucial for maintaining competitive advantage and operational excellence in demanding industrial environments. These rollers are fundamental components that help streamline operations, minimize maintenance downtime, and support the continuous, heavy-duty transport of materials across diverse industrial landscapes.
Different Size Options in Large Conveyor Rollers
Conveyor rollers are available in a range of sizes to accommodate the varied demands of different industries and applications. While large conveyor rollers typically cater to heavy-duty and high-capacity needs, it is essential to understand the full spectrum of available sizes and their specific uses. This section explores the variations in conveyor roller sizes, emphasizing the adaptability and functionality of each size category, from mini rollers to those with larger diameters.
Variations in Conveyor Roller Sizes:
- 1-inch Diameter Conveyor Roller: These small-diameter rollers are ideal for lightweight applications where space is limited and precise handling is necessary. They are commonly used in electronic, pharmaceutical, and food industries, where delicate handling of products is critical. Despite their small size, these rollers are built to maintain efficiency and can be equipped with high-performance materials to ensure durability.
- 4-inch Diameter Conveyor Roller: A more robust option, the 4-inch diameter rollers are suited for medium-duty applications. These rollers offer a good balance between size and capacity, making them suitable for manufacturing lines, packaging plants, and material handling in distribution centers. They can support heavier loads than the 1-inch rollers and are designed to withstand moderate use while providing reliable performance.
- Mini Conveyor Rollers: Specifically designed for applications where space constraints do not allow for standard roller sizes, mini conveyor rollers are used in various specialized applications. These might include small parts handling, such as moving individual components along assembly lines in the electronics industry or in postal sorting facilities. Mini rollers allow for the precise control and movement of small items, helping to optimize the automation processes and reduce manual handling.
Each of these size options plays a crucial role in its respective environment, demonstrating the versatility and importance of choosing the right type of conveyor roller for specific operational needs. While the focus often remains on large conveyor rollers due to their significant role in heavy-duty and industrial-scale operations, understanding the complete range of available sizes—including smaller diameters—ensures that businesses can select the most appropriate rollers that align with their specific handling requirements and operational constraints.
Whether it is the compact design of mini rollers or the robust build of larger diameters, the choice of conveyor roller size must be aligned with the application’s demands, ensuring efficiency, durability, and optimal performance across all facets of material handling and processing.
Price and Availability of Large Conveyor Rollers
Understanding the price and availability of large conveyor rollers is crucial for businesses that rely on these essential components for their operations. The cost of large conveyor rollers can vary significantly based on several factors, and their availability can be influenced by industry demands, manufacturing capabilities, and global supply chain conditions.
Comprehensive Discussion on the Cost:
The price of large conveyor rollers is determined by a combination of material costs, manufacturing complexity, and the scale of demand. Generally, these rollers are more expensive than their smaller counterparts due to the increased amount of material and the enhanced engineering required to ensure they can handle heavier loads and more strenuous conditions.
Factors Influencing the Price of Large Conveyor Rollers:
- Material Quality and Type: The choice of materials—whether steel, stainless steel, or composite materials—significantly affects the cost. Higher-quality materials that offer better durability and performance under extreme conditions tend to increase the price.
- Customization and Specifications: Custom features such as special coatings, tailored dimensions, and integrated sensor technology for monitoring purposes can also drive up costs. The more specific the customization, the higher the cost, as these modifications require additional design and manufacturing time.
- Production Volume: The quantity of rollers ordered can influence the unit price significantly. Bulk orders typically reduce the cost per unit due to economies of scale, whereas smaller orders might carry a premium.
- Market Fluctuations: External economic factors such as changes in raw material costs, labor rates, and logistical expenses due to geopolitical events or trade policies can affect the price of large conveyor rollers. Manufacturers must adjust their pricing to reflect these variable costs.
Availability:
The availability of large conveyor rollers can fluctuate based on industry trends, manufacturing lead times, and the global logistics network. In industries experiencing a boom, such as mining or large-scale manufacturing, the demand for these rollers can outpace supply, leading to longer lead times and potentially higher prices. Conversely, improvements in manufacturing technology and global supply chain efficiencies can enhance availability and possibly stabilize prices.
Both the price and availability of large conveyor rollers are dynamic and influenced by a complex set of factors. Businesses needing these components should stay informed about market trends and maintain flexible procurement strategies to manage costs effectively and ensure timely acquisition of these critical industrial elements.
Buying Large Conveyor Rollers
Purchasing large conveyor rollers involves careful consideration of various factors to ensure that the components not only fit the specific needs of your operation but also offer longevity and reliability. Here we explore insights on buying replacements for large conveyor rollers, essential factors to consider during the purchase, and information on finding conveyor belt rollers for sale.
Insights on Buying Replacements for Large Conveyor Rollers:
- Identify Wear Patterns: Before purchasing replacements, it’s important to assess the wear patterns of your current rollers. This can indicate if there are issues with your conveyor setup or if a different type of roller might be more suitable.
- Match Specifications Exactly: Ensure that the new rollers match the exact specifications of the ones being replaced, including diameter, length, bearing type, and load capacity, to maintain system efficiency and safety.
- Consider Upgrades: Evaluate whether upgrading to a more durable material or a roller with better performance features could improve your conveyor system’s overall efficiency and reduce future maintenance needs.
- Vendor Reputation and Support: Choose a supplier with a strong reputation for quality and customer support. Ensuring that the vendor offers after-sale services and technical support can be crucial for smooth operation.
Factors to Consider While Purchasing Large Conveyor Rollers:
- Application-Specific Requirements: Understand the specific demands of your application, such as load capacity, speed requirements, and environmental conditions (e.g., exposure to chemicals, temperature extremes).
- Material and Build Quality: Opt for rollers made from materials that can withstand your operation’s conditions. The build quality can significantly influence the lifespan and performance of the rollers.
- Maintenance Needs: Consider the ease of maintenance and the availability of spare parts. Rollers that are easier to maintain and repair can reduce downtime and operational costs.
- Certifications and Standards: Ensure that the rollers meet industry standards and certifications, which can be a testament to their quality and durability.
Information on Conveyor Belt Rollers for Sale:
When looking for conveyor belt rollers for sale, it’s advisable to start by searching reputable industrial supply companies and manufacturers specializing in conveyor systems. Many suppliers offer detailed online catalogs where you can view product specifications, compare options, and even request custom solutions. Additionally, attending industry trade shows or contacting industry associations can provide opportunities to see the latest products firsthand and establish direct relationships with manufacturers. Online forums and reviews can also offer insights into the quality and reliability of different brands and models.
When buying large conveyor rollers, it’s critical to conduct thorough research, understand the specific needs of your application, and choose a supplier that can provide high-quality products and sufficient support. This approach will help ensure that you receive rollers that are well-suited to your industrial environment and capable of supporting your operational goals efficiently.
Special Types of Large Conveyor Rollers and Their Applications
Special types of large conveyor rollers are designed to meet specific industry needs, offering unique functionalities that enhance operational efficiency and adaptability. Among these, gravity roller conveyors and rollers with brackets play crucial roles in various settings, each suited to particular applications due to their distinctive features.
Importance and Applications of Gravity Roller Conveyors:
Gravity roller conveyors are a fundamental component in material handling systems, utilizing natural forces to facilitate movement, thereby reducing energy costs and enhancing workflow efficiency. These conveyors are particularly important in applications where:
- Warehousing and Distribution: They are used for moving boxes, packages, and pallets through sorting and assembly processes, requiring minimal power and reducing operational costs.
- Manufacturing Assembly Lines: Gravity roller conveyors allow for the easy movement of parts and assemblies between workstations without the need for powered systems, making them cost-effective and easy to maintain.
- Loading and Unloading Areas: These conveyors streamline the loading and unloading processes at docks, helping to transfer goods from shipping containers or trucks to warehouse storage areas efficiently.
- Order Fulfillment Centers: Gravity roller conveyors facilitate the rapid movement of goods in picking and packing operations, improving order processing times and overall logistics efficiency.
Detailed Section on Conveyor Rollers with Bracket:
Conveyor rollers with brackets are another special type of roller designed to offer additional support and versatility within conveyor systems. The bracket allows the roller to be mounted and adjusted more easily, providing stability and alignment that is critical in maintaining the functionality of the conveyor system.
Key Features and Benefits:
- Versatility in Installation: Brackets allow for the flexible positioning of rollers, accommodating various conveyor designs and layouts.
- Enhanced Stability: The use of brackets ensures that rollers are securely mounted, reducing vibrations and misalignments that can disrupt conveyor operations.
- Ease of Maintenance: Rollers with brackets can be quickly removed and replaced, simplifying maintenance tasks and reducing downtime.
- Adaptability to Various Loads: The design can be customized to handle different weights and sizes of materials, making it suitable for industries ranging from light manufacturing to heavy construction.
These special types of large conveyor rollers—gravity rollers and rollers with brackets—demonstrate the diversity and adaptability of conveyor technology. By choosing the appropriate type of roller for their specific applications, industries can optimize their operations, reduce costs, and improve overall efficiency. Understanding these options allows businesses to make informed decisions that align with their operational needs and long-term strategic goals.
FAQs About Large Conveyor Rollers
Conveyor rollers are cylindrical components that fit into roller conveyors, enabling the movement of items along a predefined pathway with minimal effort. These rollers are primarily designed to facilitate the efficient transport of goods across various distances within a facility. They work by rotating around a central axis and can be made from various materials including metal, plastic, or rubber, depending on the application needs. The rollers are mounted on a frame and spaced appropriately to support the goods being conveyed without causing damage or excessive drag. This system is pivotal in industries like manufacturing, packaging, and logistics, where they streamline processes and increase productivity by moving items quickly and reliably through production lines or storage areas.
The size of conveyor rollers can vary significantly depending on their intended use and the specific requirements of the conveyor system they are part of. Roller diameters typically range from as small as less than an inch to over 10 inches. The most common diameters are between 1.9 to 3.5 inches for light to medium applications, with larger sizes available for heavy-duty tasks. The length of the rollers also varies and can be tailored to the width of the conveyor belt or material to be transported. The sizing is crucial as it affects the roller’s ability to support the conveyed materials and impacts the overall conveyor system’s efficiency and longevity. When selecting rollers, it’s essential to consider both the size and weight of the materials to ensure appropriate support and minimal wear and tear.
A roller conveyor is a type of conveyor system that uses a series of rollers mounted within a frame to transport materials across a defined area. Roller conveyors are versatile and can be used in various applications, from simple industrial products to complex manufacturing processes. They are particularly beneficial in environments where quick and efficient movement of goods is required. Roller conveyors can be powered by motors or can operate on gravity if installed at a decline. They come in several types, including straight, curved, and spiral conveyors, each designed to fulfill specific logistical needs. The choice between these types depends on factors like the layout of the facility, the nature of the items being transported, and the required speed of movement.
Idler rollers, which are used to support the conveyor belt and the material being transported, come in various sizes. The diameter of idler rollers typically ranges from 3 to 6 inches for standard applications, with larger rollers used in heavier-duty applications. The width of these rollers usually corresponds to the width of the conveyor belt they are supporting, ensuring that the belt remains stable and evenly supported throughout its length. The sizing of idler rollers is critical as it influences the belt’s tension and overall operational effectiveness. For optimal performance, it is important to choose idlers that appropriately match the load requirements and the operational conditions of the conveyor system. This sizing ensures that the conveyor operates smoothly and extends the lifespan of both the belt and the rollers.
Last Updated on April 16, 2024 by Jordan Smith
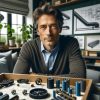
Jordan Smith, a seasoned professional with over 20 years of experience in the conveyor system industry. Jordan’s expertise lies in providing comprehensive solutions for conveyor rollers, belts, and accessories, catering to a wide range of industrial needs. From initial design and configuration to installation and meticulous troubleshooting, Jordan is adept at handling all aspects of conveyor system management. Whether you’re looking to upgrade your production line with efficient conveyor belts, require custom conveyor rollers for specific operations, or need expert advice on selecting the right conveyor accessories for your facility, Jordan is your reliable consultant. For any inquiries or assistance with conveyor system optimization, Jordan is available to share his wealth of knowledge and experience. Feel free to reach out at any time for professional guidance on all matters related to conveyor rollers, belts, and accessories.