Material Handling with Lightweight Gravity Roller Conveyors
In the realm of material handling and logistics, gravity roller conveyors have long stood as pillars of efficiency and reliability. These systems facilitate the smooth and effortless transportation of goods across warehouse floors, production lines, and packing areas, leveraging gravity to minimize operational costs and energy use. Within this spectrum, the lightweight gravity roller conveyor emerges as a particularly advantageous solution. Tailored for businesses seeking not just efficiency but also unmatched flexibility, these conveyors are designed to be easily moved, reconfigured, or expanded based on shifting demands and spatial constraints. Their lightweight nature does not compromise on durability; instead, it opens up a world where swift adjustments are possible, ensuring that workflow interruptions are kept to a minimum. For companies looking to streamline their operations while maintaining the ability to adapt to future challenges, embracing lightweight solutions marks a forward-thinking choice.
The Essentials of Lightweight Gravity Roller Conveyors
In the realm of material handling and logistics, lightweight gravity roller conveyors stand as a testament to efficiency and adaptability. These systems, characterized by their simplicity and effectiveness, harness the force of gravity to facilitate the movement of goods across short to medium distances. This section delves into the defining features of light duty gravity roller conveyors and underscores their aptness for light to medium load applications. Moreover, it will highlight seven key benefits derived from the use of lightweight materials in their construction, shedding light on their ease of installation and reconfiguration capabilities.
Features Defining Lightweight Gravity Roller Conveyors
Lightweight gravity roller conveyors are ingeniously designed systems that consist of rollers mounted in a frame. The rollers are spaced at intervals calculated to support goods of various sizes and shapes. These conveyors operate without the need for an external power source, relying instead on gravity and the manual effort of operators to move goods along the conveyor path. The defining features of these conveyors include their simplicity, efficiency, and the use of lightweight yet durable materials in their construction. This design philosophy ensures that the conveyors are not only easy to handle and reconfigure but also capable of withstanding the demands of light to medium load applications without compromise.
Benefits of Using Lightweight Materials in Conveyor Construction
- Ease of Installation: Lightweight gravity roller conveyors can be installed with minimal effort and without the need for specialized heavy lifting equipment. This significantly reduces setup times and costs.
- Flexibility in Reconfiguration: The use of lightweight materials means these conveyors can be easily moved and reconfigured to meet the changing needs of a business. This adaptability is particularly beneficial in dynamic operational environments.
- Reduced Shipping Costs: Lightweight conveyors are less costly to ship compared to their heavier counterparts. This can lead to significant savings, especially for businesses that require frequent relocations of their material handling systems.
- Lower Energy Consumption: Although these conveyors primarily rely on gravity, any supplementary power assistance required (for inclines, for example) demands less energy due to the reduced mass of the conveyor system.
- Enhanced Worker Safety: The lightweight nature of these conveyors minimizes the risk of injury during installation, reconfiguration, and daily operations. This contributes to a safer workplace and reduced workers’ compensation claims.
- Cost-Effective Maintenance and Repair: Maintenance and repair tasks are less labor-intensive and can be performed more quickly and economically. The reduced weight reduces wear on components, further lowering maintenance costs over time.
- Eco-Friendly: Lightweight materials often have a smaller environmental footprint in terms of both production and transportation. Additionally, the energy efficiency and recyclability of these materials contribute to more sustainable operations.
Lightweight gravity roller conveyors offer an array of advantages stemming from their design and the materials used in their construction. Their simplicity, combined with the ease of installation, flexibility, and cost-effectiveness, makes them an ideal choice for businesses looking to optimize their material handling processes while keeping operational costs in check. As industries continue to evolve, the role of lightweight gravity roller conveyors in facilitating efficient, adaptable, and sustainable material handling solutions is set to grow, underscoring their importance in the logistics and manufacturing sectors.
Navigating the Market: Lightweight Gravity Roller Conveyor Manufacturers
In the diverse and competitive realm of material handling equipment, selecting the right lightweight gravity roller conveyor can significantly impact operational efficiency and cost-effectiveness. This section offers a comprehensive overview of leading manufacturers that specialize in light duty gravity roller conveyors, highlighting their commitment to quality, innovation, and reliability. Additionally, we’ll delve into the unique attributes that set certain manufacturers apart in the production of efficient and durable lightweight conveyor systems, providing valuable insights for businesses looking to make an informed purchasing decision.
Leading Manufacturers of Lightweight Gravity Roller Conveyors
The market for lightweight gravity roller conveyors is populated with a variety of manufacturers, each bringing their own strengths and innovations to the table. These companies range from established giants in the industry to nimble startups that prioritize cutting-edge technologies and sustainable materials. What they have in common is a dedication to producing high-quality conveyors that meet the diverse needs of industries such as e-commerce, logistics, manufacturing, and more.
Key players in this field are recognized for their engineering excellence, which allows for the creation of conveyors that are not only lightweight but also robust enough to handle the demands of daily operations. They leverage advanced materials and manufacturing processes to ensure that their products offer longevity, ease of maintenance, and flexibility in application.
What Sets Certain Manufacturers Apart
Several factors contribute to the prominence of certain lightweight gravity roller conveyor manufacturers in the market:
- Innovative Design: The most successful manufacturers constantly refine their designs to improve efficiency, reduce costs, and enhance usability. This might include the development of modular systems that can be easily expanded or reconfigured as business needs change.
- Quality Materials: The choice of materials is crucial in the construction of lightweight conveyors. Leading manufacturers often use high-grade aluminum, reinforced plastics, or specialized alloys that provide an optimal balance between weight and durability.
- Customization Capabilities: Understanding that no two operations are exactly alike, standout manufacturers offer extensive customization options. This ensures that each conveyor system is tailored to the specific requirements of the application, whether it involves unique dimensions, roller types, or integration with existing systems.
- Sustainability Focus: As businesses increasingly prioritize sustainability, manufacturers that incorporate eco-friendly materials and processes into their production lines gain a competitive edge. This includes the use of recyclable materials and energy-efficient manufacturing techniques.
- Customer Support and Service: Exceptional customer service, from initial consultation and design to installation and after-sales support, is a hallmark of leading manufacturers. This comprehensive approach ensures that customers not only receive a product that fits their needs but also the knowledge and support necessary to maximize its value over time.
Navigating the market of lightweight gravity roller conveyor manufacturers requires an understanding of the unique offerings and strengths of each contender. By focusing on innovation, quality, and reliability, businesses can partner with manufacturers that not only meet their current needs but also support their growth and adaptation in an ever-changing operational landscape. The right manufacturer can provide a lightweight conveyor system that enhances efficiency, reduces costs, and contributes to a more effective and sustainable operation.
Cost Considerations: Lightweight Gravity Roller Conveyor Price Points
Investing in a lightweight gravity roller conveyor system is a significant decision that impacts both the efficiency of your operations and your company’s bottom line. Understanding the cost considerations and what influences the price points of these systems is crucial for budgeting and ensuring you receive the best value for your investment. This section provides a detailed analysis of the price range for light duty gravity roller conveyors and identifies the key factors that influence cost. Additionally, we offer ten practical tips for budgeting effectively and maximizing the return on your investment in a lightweight gravity roller conveyor system.
Analyzing Price Range and Influencing Factors
The cost of lightweight gravity roller conveyors can vary widely based on several factors, making it essential for potential buyers to understand what contributes to these variances. Generally, prices can range from a few hundred to several thousand dollars per section, depending on the specifics of the system required.
Key Factors Influencing Cost:
- Material: The type of materials used (e.g., aluminum, steel, reinforced plastics) significantly affects the price. Lightweight and durable materials often come at a premium.
- Length and Width: The dimensions of the conveyor directly impact the cost. Longer and wider systems require more materials and, consequently, are more expensive.
- Customization: Custom features tailored to specific operational needs, such as adjustable heights, special roller types, or coatings, can increase the price.
- Load Capacity: Conveyors designed to handle heavier loads need stronger materials and more robust construction, leading to higher costs.
- Brand and Quality: Established brands known for quality and durability might command higher prices, but they also offer peace of mind regarding reliability and lifespan.
- Additional Features: Accessories and enhancements, like guide rails, stops, or accumulation features, add to the overall cost.
Tips for Budgeting and Maximizing Value
- Define Your Requirements: Clearly outline your needs before shopping. Over-specifying can lead to unnecessary costs, while under-specifying can result in a system that doesn’t meet your operational needs.
- Consider Total Cost of Ownership: Look beyond the initial purchase price to consider maintenance, repair, and operational costs over the conveyor’s lifespan.
- Get Multiple Quotes: Obtain quotes from several manufacturers to compare prices and offerings.
- Assess Modularity: Choose a system that can grow and change with your business to avoid future replacement costs.
- Prioritize Quality Over Price: Investing in a high-quality system can reduce long-term costs related to downtime, repairs, and replacements.
- Look for Financing Options: Some manufacturers offer financing plans that can help spread out the investment cost.
- Consider Second-Hand Options: For operations with less demanding requirements, high-quality used conveyors can provide significant savings.
- Evaluate Lead Times: Longer lead times can indirectly increase costs by delaying operations. Consider the value of quicker delivery times.
- Leverage Negotiation: Don’t hesitate to negotiate pricing, especially if ordering in bulk or if the project has unique aspects that could lead to a long-term partnership with the manufacturer.
- Plan for Future Needs: Investing a little more upfront for a scalable system can save money as your business grows, avoiding the need for a completely new conveyor system down the line.
By taking these price points and tips into account, businesses can make informed decisions when investing in a lightweight gravity roller conveyor system. Careful planning and consideration will ensure that you not only fit the system within your budget but also secure a solution that enhances operational efficiency and provides the best return on investment.
Top Picks: Best Lightweight Gravity Roller Conveyor Models
In the search for the most efficient, durable, and user-approved lightweight gravity roller conveyors, several models stand out from the competition. This curated list represents the pinnacle of design and functionality in the lightweight gravity roller conveyor market. By highlighting the key features and advantages of each selected model, we aim to guide potential buyers through their decision-making process, ensuring they find a conveyor system that meets their operational needs while offering the best value for investment.
Model 1: FlexiRoll Compact
Key Features:
- Constructed from high-grade aluminum for a perfect balance between lightness and strength.
- Modular design allows for easy expansion or reconfiguration.
- Features a unique quick-release mechanism for fast and efficient roller replacement.
Advantages:
- Exceptionally lightweight, making it easy to move and install without specialized equipment.
- The modular system caters to businesses looking for scalability in their operations.
- Durable construction ensures long-term reliability with minimal maintenance.
Model 2: EcoSlide 2.0
Key Features:
- Utilizes eco-friendly, recycled plastic components without compromising on durability.
- Innovative roller design reduces friction, enhancing efficiency in material handling.
- Adjustable leg supports for varying heights and applications.
Advantages:
- Sustainable choice for environmentally conscious businesses.
- Lower operational noise compared to traditional models, improving workplace conditions.
- Versatility in application due to adjustable height features.
Model 3: Durabilt DX-200
Key Features:
- Heavy-duty steel frame construction with a lightweight design for easy maneuverability.
- Powder-coated finish for increased resistance to wear and corrosion.
- High load capacity compared to other lightweight models.
Advantages:
- Combines the durability of heavier conveyors with the flexibility of lightweight models.
- Suitable for environments with high throughput or heavier loads.
- Long-lasting durability with minimal maintenance requirements.
Model 4: Streamline S1 Series
Key Features:
- Sleek design with an ultra-light frame, ideal for tight spaces and clean environments.
- Integrated guide rails to ensure smooth and straight product movement.
- Easy-to-use tension adjustment for quick customization.
Advantages:
- Aesthetically pleasing design fits well in customer-facing environments or cleanrooms.
- Ensures products remain on track, reducing the risk of jams or disruptions.
- Quick adjustments save time and improve operational efficiency.
Model 5: QuickShift QL-100
Key Features:
- Tool-free assembly system allows for rapid setup and disassembly.
- Features a wide range of roller options, including plastic, steel, and cushioned rollers.
- Lightweight composite materials for frame and rollers, reducing overall weight.
Advantages:
- Ideal for temporary or changing setups, such as events or flexible manufacturing lines.
- Tailorable to a wide range of products and materials.
- Offers a significant reduction in manual handling due to its extreme lightness.
This selection of lightweight gravity roller conveyor models showcases the diversity and innovation within the market. Each model has been chosen for its unique blend of features that cater to different operational needs, from sustainability and durability to flexibility and ease of use. By considering the key advantages and features of these top picks, businesses can make a well-informed decision that aligns with their specific requirements, ensuring a successful and cost-effective investment in their material handling infrastructure.
Beyond the Lightweight Gravity Roller Conveyor
When considering the optimization of a material handling system, the value of accessories and enhancements cannot be overstated. These additions transform a simple lightweight gravity roller conveyor into a comprehensive system that addresses a variety of operational needs. Among the most beneficial enhancements are gates and tables, each serving to expand the functionality and efficiency of the conveyor system. This section will delve into the specific benefits of gravity roller conveyor gates and the roles of gravity roller tables in augmenting lightweight conveyors, ultimately facilitating a wide range of sorting, packing, and assembly tasks.
Gravity Roller Conveyor Gates: Enhancing Operational Flexibility
Conveyor gates are pivotal in creating access points within conveyor lines, allowing for the safe and easy movement of personnel and equipment across the conveyor path. When integrated with lightweight gravity roller conveyors, these gates offer several benefits:
- Safety: Gates provide a secure and designated crossing point for employees, reducing the risk of accidents associated with crossing over or under conveyor lines.
- Efficiency: They allow for quick and easy access across the conveyor line, minimizing downtime and disruption to operations.
- Flexibility: Conveyor gates can be locked in an open or closed position, adapting to the operational needs of the moment.
- Space-saving: Especially in tight spaces, the ability to open a conveyor section when needed helps conserve valuable floor space.
- Ease of Installation: Many gates are designed for easy integration into existing conveyor systems, requiring minimal modifications.
- Modularity: Like the conveyors they accompany, gates are often modular, allowing for reconfiguration as operational needs evolve.
- Customization: Gates can be customized in size and materials to match the specifications of the lightweight gravity roller conveyor system, ensuring a seamless fit and operation.
Gravity Roller Tables: Extending Functionality
Gravity roller tables play a critical role in enhancing the utility of lightweight conveyors, serving in capacities ranging from sorting and packing to assembly. Here are nine roles these tables can fulfill:
- Sorting: Tables can be set up at the end of conveyor runs for manual or automated sorting operations.
- Packing: Designated packing areas with roller tables facilitate efficient packing processes, directly alongside the movement of goods.
- Assembly: Utilizing tables as workstations allows for the assembly of products as they move along the conveyor system.
- Inspection: Tables provide a stable platform for the inspection of goods for quality control purposes.
- Accumulation: Roller tables can serve as accumulation points for goods, enabling temporary storage without disrupting the flow of other items.
- Integration: They can be integrated with scales for weighing goods in transit, streamlining the process.
- Directional Changes: Tables can assist in redirecting goods to different conveyor lines or work areas.
- Buffer Zones: Creating buffer zones with tables helps manage the flow of goods, preventing bottlenecks.
- Ergonomics: Adjustable height tables improve ergonomics, reducing strain on workers and increasing productivity.
Incorporating gates and tables into a lightweight gravity roller conveyor system not only enhances its functionality but also significantly improves operational flexibility, safety, and efficiency. By understanding and leveraging these enhancements and accessories, businesses can create a more integrated and versatile material handling solution that meets the demands of today’s dynamic operational environments.
From 10 to 12 Roller Conveyors in Lightweight Gravity Roller Conveyor Systems
Selecting the right lightweight gravity roller conveyor involves understanding various specifications that directly impact its performance in material handling applications. Among these specifications, roller size and spacing play pivotal roles in determining the conveyor’s suitability for light-duty versus heavy-duty applications. This section offers a detailed exploration of these specifications, with a particular focus on the comparative analysis of 10 and 12 roller conveyors. By dissecting these aspects, we aim to provide a clear guideline on when to choose one over the other, based on specific material handling needs.
Significance of Roller Size and Spacing
Roller size and spacing are critical specifications that affect the conveyor’s ability to handle different types of loads:
- Roller Size: The diameter of the rollers influences the conveyor’s capacity to support weight. Larger rollers can support heavier loads, reducing the strain on individual rollers and the conveyor frame.
- Roller Spacing: The distance between each roller (also known as roller pitch) affects the smoothness of the transit and the types of items the conveyor can handle efficiently. Closer spacing provides better support for smaller items, preventing them from tipping or getting stuck.
These specifications are crucial in designing a system that meets the demands of light-duty versus heavy-duty applications. Light-duty conveyors, often utilized for smaller items or lower volume applications, can afford to have smaller rollers and wider spacing. In contrast, heavy-duty conveyors require larger rollers and closer spacing to accommodate heavier loads and ensure stability.
Comparative Analysis of 10 and 12 Roller Conveyors
When deciding between a 10 and a 12 roller conveyor, understanding the nuances of each setup becomes vital:
- 10 Roller Conveyors: These conveyors typically feature rollers with a smaller diameter and are spaced further apart. They are best suited for light to medium loads where the bottom surface of the conveyed items is relatively flat and spans multiple rollers. The advantage of 10 roller conveyors is their cost-effectiveness and suitability for a wide range of light-duty applications, including packaging and assembly lines.
- 12 Roller Conveyors: With a denser roller arrangement, 12 roller conveyors offer enhanced support and stability, making them ideal for heavier loads or items with irregular bottoms. The closer spacing ensures that items maintain balance and do not sag or become damaged during transit. This type of conveyor is recommended for applications requiring the transportation of heavier goods, such as warehouse operations and heavier manufacturing processes.
When to Choose One Over the Other
The choice between a 10 and a 12 roller conveyor depends on several factors:
- Nature of the Load: For lighter, uniformly shaped items, a 10 roller conveyor may suffice. For heavier or irregularly shaped items, a 12 roller conveyor provides better support.
- Load Weight: Evaluate the average weight of the items being transported. Heavier loads will necessitate the use of a 12 roller conveyor to distribute the weight more evenly and ensure longevity of the system.
- Cost Considerations: While 12 roller conveyors offer greater support, they are also more costly due to the higher number of rollers required. Budget constraints may influence the choice, especially if the operational requirements can be met with a 10 roller system.
- Operational Flexibility: Consider future needs. If there is potential for handling a wider variety of items or heavier loads, opting for a 12 roller conveyor from the outset could provide greater operational flexibility.
Understanding the specifications and comparative advantages of 10 and 12 roller conveyors in lightweight gravity roller conveyor systems is essential for making an informed decision tailored to your material handling needs. This analysis ensures that the chosen conveyor not only meets current operational demands but also offers scalability and adaptability for future requirements.
Collapsible and Wide Roller Conveyors in Lightweight Gravity Roller Conveyor Systems
Within the versatile world of light duty gravity roller conveyors, specialized solutions like collapsible and wide roller conveyors provide unique advantages and applications tailored to meet specific operational needs. These innovative systems extend the functionality of standard conveyors, offering solutions for businesses with fluctuating space requirements or those handling larger items. This section delves into the advantages of collapsible roller conveyors for businesses seeking portability and flexibility, as well as the applications of wide roller conveyors in managing larger items or enhancing throughput in a lightweight gravity roller conveyor system.
Advantages of Collapsible Roller Conveyors
Collapsible roller conveyors are designed for versatility and ease of use, catering to businesses with variable space requirements or those in need of portable conveyor solutions. Here are six notable advantages:
- Space Efficiency: Collapsible designs allow for easy storage when the conveyor is not in use, freeing up valuable floor space for other operations.
- Portability: Equipped with wheels and foldable mechanisms, these conveyors can be easily relocated to where they are needed most, enhancing workflow flexibility.
- Quick Setup and Breakdown: Their design facilitates rapid deployment and dismantling, minimizing downtime and enabling quick responses to operational demands.
- Adaptability: They can be extended, curved, and configured to suit various applications and spaces, making them ideal for temporary setups or dynamic work environments.
- Cost-Effectiveness: By maximizing the use of space and adapting to multiple uses, collapsible conveyors represent a cost-efficient solution for businesses with fluctuating demands.
- Ease of Integration: These systems can seamlessly integrate with existing conveyor setups, expanding their functionality without the need for permanent installations.
Applications of Wide Roller Conveyors
Wide roller conveyors expand the capabilities of lightweight gravity roller conveyor systems, particularly in handling larger items or increasing throughput. Their applications include:
- Handling Large Items: The increased width provides stable support for bulky or wide loads, preventing tipping and ensuring smooth transportation.
- Increased Throughput: The ability to handle multiple items side-by-side or larger items means higher volumes can be moved efficiently.
- Versatile Material Handling: Suitable for a range of industries, including manufacturing, distribution, and warehousing, where large items or high volumes are common.
- Improved Worker Safety: The stable and supportive platform reduces the risk of items falling or causing obstructions, creating a safer work environment.
- Efficient Sorting and Distribution: Wide conveyors offer more space for sorting operations, making them ideal for distribution centers dealing with a variety of product sizes.
- Integration with Automated Systems: Their size and capacity make wide roller conveyors well-suited for integration into automated systems, where they can serve as the backbone for material movement.
Collapsible and wide roller conveyors represent specialized solutions within the framework of lightweight gravity roller conveyor systems, offering unique benefits and applications tailored to specific business needs. Whether the priority is flexibility and portability or handling larger items and increasing throughput, these specialized conveyor options provide efficient, adaptable, and scalable solutions. Their implementation can significantly enhance operational efficiency, safety, and flexibility, making them invaluable assets in a comprehensive material handling strategy.
Lightweight Gravity Roller Conveyors for Sale
Selecting the right lightweight gravity roller conveyor is pivotal for optimizing your business’s material handling processes. The decision encompasses more than just the immediate need; it requires foresight into future demands and a thorough understanding of available options. Here are ten pieces of advice to guide you in choosing the appropriate lightweight gravity roller conveyor for your business, considering both current and future material handling needs. Additionally, we provide insights on where to find these conveyors for sale, catering to a range of budgets with new, used, and refurbished options, including used gravity roller conveyor for sale.
Advice for Selecting the Right Conveyor
- Assess Your Material Handling Needs: Evaluate the types of items you plan to transport, including their size, weight, and shape. This will determine the required specifications for the conveyor.
- Consider Future Expansion: Choose a system that can be easily expanded or modified as your business grows or as your operational needs change.
- Quality Over Cost: While budget constraints are real, opting for a conveyor made from high-quality materials can save you money in the long run due to lower maintenance and replacement costs.
- Ease of Integration: Select a conveyor that can be easily integrated with your existing systems and processes, ensuring seamless operations.
- Space Considerations: For businesses with limited space, collapsible or modular conveyors that can be reconfigured as needed may be the best option.
- Vendor Reputation: Research manufacturers and vendors to ensure you’re buying from a reputable source that offers quality products and reliable customer service.
- Maintenance and Support: Look for conveyors that are easy to maintain and for vendors who provide comprehensive after-sales support.
- Safety Features: Ensure the conveyor includes necessary safety features to protect your employees and materials.
- Customization Options: Consider whether you need a conveyor that offers customization options to meet specific operational requirements.
- Environmental Impact: If sustainability is a concern for your business, look for conveyors made from eco-friendly materials or those designed for energy efficiency.
Where to Find Conveyors for Sale
- Manufacturers: Purchasing directly from manufacturers is often the best way to get new, customizable options. Many offer consultations to help you choose the right model for your needs.
- Industrial Supply Companies: These vendors typically offer a range of material handling equipment, including new and sometimes used conveyors.
- Online Marketplaces: Websites like eBay and specialized industrial equipment platforms can be good sources for finding used or refurbished conveyors at lower prices.
- Auctions: Industrial auctions, both online and in-person, can provide opportunities to purchase heavy-duty conveyors at significantly reduced costs.
- Refurbished Equipment Dealers: Some dealers specialize in refurbishing material handling equipment, offering a middle ground between new and used in terms of cost and quality.
Making the right choice in a lightweight gravity roller conveyor involves a careful assessment of your current and future needs, a thorough exploration of available options, and a consideration of budget constraints. By following the advice outlined above and exploring the various sources for conveyors, you can secure a system that enhances operational efficiency, meets your material handling requirements, and provides lasting value for your business.
Last Updated on May 22, 2024 by Jordan Smith
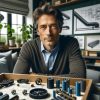
Jordan Smith, a seasoned professional with over 20 years of experience in the conveyor system industry. Jordan’s expertise lies in providing comprehensive solutions for conveyor rollers, belts, and accessories, catering to a wide range of industrial needs. From initial design and configuration to installation and meticulous troubleshooting, Jordan is adept at handling all aspects of conveyor system management. Whether you’re looking to upgrade your production line with efficient conveyor belts, require custom conveyor rollers for specific operations, or need expert advice on selecting the right conveyor accessories for your facility, Jordan is your reliable consultant. For any inquiries or assistance with conveyor system optimization, Jordan is available to share his wealth of knowledge and experience. Feel free to reach out at any time for professional guidance on all matters related to conveyor rollers, belts, and accessories.