World’s Longest Conveyor Belts
Conveyor belts are integral components in global industries, revolutionizing material handling and transportation processes. These systems are essential for efficiently moving bulk materials across long distances, significantly enhancing productivity and reducing operational costs. The concept of the world’s longest conveyor belt highlights the pinnacle of engineering and innovation in this field. These massive belts, stretching for miles, are crucial in sectors like mining and transportation, enabling the continuous and efficient transfer of materials such as ores, minerals, and raw goods. The world’s longest conveyor belts exemplify the technological advancements that drive industrial growth and sustainability, underscoring their vital role in modern industry.
World’s Longest Conveyor Belts
Here’s a quick look at the record-breaking conveyor systems around the world.
World’s Longest Single Conveyor System
The longest single conveyor system in the world, according to the Guinness Book of Records, is located in Western Australia. This remarkable conveyor belt runs between the Mount Saddleback mine and the Worsley refinery near the town of Collie. The system was constructed in 1983 and remains operational, transporting bauxite ore—the primary raw material used in aluminum production.
The conveyor covers a distance of over 19 miles (approximately 31 kilometers) as the crow flies, but due to the winding nature of the terrain, the belt actually travels over 31 miles (about 50 kilometers) along its journey. This system is designed to transport an impressive load of approximately 2,700 tonnes of bauxite ore every hour.
The journey from the mine to the refinery is not straightforward; the belt passes through 22 tunnels and over 10 bridges. This complex route allows the belt to navigate the rugged landscape of Western Australia, ensuring a continuous flow of materials to the refinery. The belt moves at a speed of 16 mph (about 25 km/h), demonstrating both efficiency and the ability to handle substantial loads over a significant distance.
World’s Longest Interlinked Conveyor Belt
The longest conveyor belt system in the world is found in the Western Sahara and stretches over an incredible distance of 61 miles (approximately 98 kilometers). This system is used to transport phosphate ore from the mine in Bou Craa to the port town of Marsa in Morocco. The sheer length of this conveyor belt is so significant that it is visible from space, making it a marvel of modern engineering.
Unlike the single conveyor in Western Australia, this system is comprised of a network of interlinked belts, which distinguishes it as the longest of its kind. The phosphate mine at Bou Craa is a major producer, contributing around 3 million tonnes of phosphate each year, which accounts for about 10% of Morocco’s total phosphate production.
Morocco is known for its vast phosphate rock reserves, holding about 85% of the world’s total supply. Phosphate is a crucial component in the production of a variety of products, including food additives, detergents, and herbicides. Additionally, the sedimentary nature of phosphate rock often means it contains fossilized remains of ancient marine life, adding a layer of historical significance to the mining operations.
World’s Longest Border-Crossing Conveyor
The title of the world’s longest single-belt conveyor that crosses international borders goes to the system located between India and Bangladesh. This conveyor belt stretches for approximately 11 miles (around 17 kilometers), with more than 4 miles on the Indian side in the state of Meghalaya and over 6 miles in Bangladesh.
Constructed in 2004, this belt serves a critical function, transporting limestone and shale from a quarry in India to a cement factory in Bangladesh. The belt operates continuously, moving around 960 tonnes of material every hour.
The design of this conveyor is particularly noteworthy due to its elevated structure, which raises the belt approximately five meters above the ground. This elevation is crucial to prevent flooding during the region’s monsoon season, ensuring uninterrupted operation throughout the year. The system also features special rollers that allow for movement in both horizontal and vertical directions, accommodating the varying terrain along its route.
Maintenance of the conveyor is carried out by teams from both India and Bangladesh. These teams utilize overhead trolleys that travel along the length of the belt, allowing for easy access to any part of the system that requires attention. The division of maintenance responsibilities between the two countries ensures that the conveyor remains in optimal condition.
For those involved in maintaining such large-scale conveyor systems, like the teams in India and Bangladesh, having access to reliable suppliers of conveyor roller belts and related parts is essential. Suppliers such as Yorkshire’s YB Components are invaluable, offering fast and efficient delivery of replacement parts, not just within the UK but worldwide. Their expertise in conveyor systems and the necessary maintenance support plays a crucial role in keeping these impressive systems running smoothly, minimizing downtime and ensuring operational efficiency.
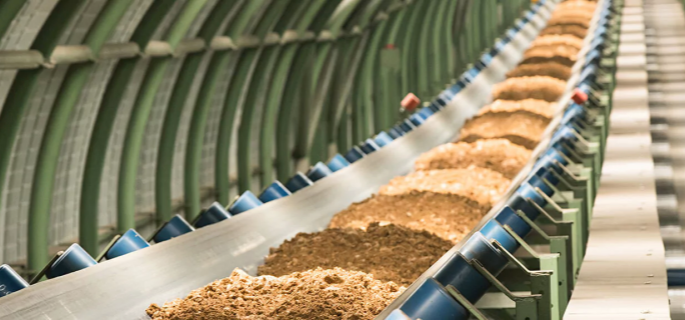
The Longest Conveyor Belt: A Marvel of Engineering
The Bou Craa conveyor belt in Western Sahara is one of the world’s most remarkable engineering feats. This extensive conveyor system, often highlighted as the longest conveyor belt globally, plays a critical role in the efficient transportation of phosphate ore. This section delves into the details of the Bou Craa conveyor belt system and its significance in transporting phosphate ore from the Bou Craa mine to the coast.
Detailed Look into the Bou Craa Conveyor Belt System
The Bou Craa conveyor belt system is an engineering marvel, stretching over 61 miles (98 kilometers) across the arid landscape of Western Sahara. This massive conveyor belt is designed to transport phosphate ore from the Bou Craa mine, located in the interior of Western Sahara, to the coastal city of El Aaiún. The conveyor belt’s sheer length and the challenging environmental conditions it operates in make it a standout example of industrial ingenuity.
Construction and Design
The construction of the Bou Craa conveyor belt required meticulous planning and execution. The belt is constructed using high-strength materials capable of withstanding the abrasive nature of phosphate ore and the harsh desert environment. The conveyor belt system includes numerous support structures, such as pylons and steel frames, to ensure stability and durability over its extensive length.
One of the key features of the Bou Craa conveyor belt is its modular design. This allows for easier maintenance and replacement of sections as needed, minimizing downtime and ensuring continuous operation. The belt is also equipped with advanced monitoring systems that track its performance in real-time, detecting any issues that might arise and allowing for prompt intervention.
Operational Efficiency
The Bou Craa conveyor belt operates with remarkable efficiency, capable of transporting up to 2,000 tons of phosphate ore per hour. This high capacity is essential for meeting the demands of global markets and ensuring the economic viability of the Bou Craa mine. The conveyor belt’s continuous operation significantly reduces the need for truck transport, lowering operational costs and minimizing environmental impact.
Its Role in Transporting Phosphate Ore
The primary role of the Bou Craa conveyor belt is to transport phosphate ore from the Bou Craa mine to the coastal port of El Aaiún. Phosphate is a crucial mineral used in the production of fertilizers, which are vital for global agriculture. The efficient transport of phosphate ore from the mine to the port ensures a steady supply of this essential resource to markets around the world.
The Journey from Mine to Port
The journey of phosphate ore from the Bou Craa mine to the port of El Aaiún begins with the extraction process at the mine. Once the phosphate ore is mined, it is loaded onto the conveyor belt system, which then transports it across the desert to the coastal facilities. The conveyor belt’s route is carefully planned to optimize the transport process, taking into account factors such as terrain, distance, and environmental impact.
Loading and Unloading
At the mine, the phosphate ore is loaded onto the conveyor belt using automated systems designed to handle large quantities of material efficiently. The belt then carries the ore over its 61-mile journey, passing through various transfer points and support structures along the way. At the port of El Aaiún, the ore is unloaded from the conveyor belt and transferred to storage facilities or directly onto ships for export.
Economic and Environmental Impact
The Bou Craa conveyor belt’s efficient operation has significant economic benefits for Western Sahara. By reducing the need for truck transport, the conveyor system lowers transportation costs and increases the profitability of the phosphate mining operation. Additionally, the steady supply of phosphate ore supports the global agricultural industry, which relies on phosphate-based fertilizers to maintain crop yields and food security.
From an environmental perspective, the conveyor belt system offers several advantages. It reduces the carbon footprint associated with the transport of phosphate ore by minimizing the use of diesel-powered trucks. The system also incorporates dust suppression measures to reduce airborne particulate matter, improving air quality in the surrounding areas.
The Bou Craa conveyor belt is a true marvel of engineering, representing one of the longest conveyor belt systems in the world. Its construction and design showcase advanced technological solutions to overcome the challenges of transporting phosphate ore across long distances in a harsh environment. By efficiently moving phosphate ore from the Bou Craa mine to the port of El Aaiún, this conveyor belt plays a critical role in supporting global agriculture and contributing to the economic development of Western Sahara. The Bou Craa conveyor belt exemplifies the potential of innovative engineering to enhance industrial operations while minimizing environmental impact.
How Phosphate Ore is Transported from the Mine to the Coast by Longest Conveyor Belt
The transportation of phosphate ore from the Bou Craa mine to the coast is a highly efficient process facilitated by the world’s longest conveyor belt. This intricate system ensures that the ore is transported smoothly and with minimal environmental impact. In this section, we will provide a detailed step-by-step explanation of the transportation process using the Bou Craa conveyor belt and discuss the efficiency and environmental impact of this method.
Step-by-Step Explanation of the Transportation Process
Step 1: Extraction and Initial Processing
The journey of phosphate ore begins at the Bou Craa mine, where the ore is extracted from the ground using drilling and blasting techniques. Large machinery is used to remove the overburden and access the phosphate deposits. Once the phosphate rock is exposed, it is blasted into manageable pieces.
Step 2: Loading onto the Conveyor Belt
After extraction, the fragmented phosphate ore is loaded onto haul trucks or directly onto the conveyor belt. At the loading station, automated systems and conveyor loaders ensure that the ore is evenly distributed on the belt to avoid any imbalance or overloading, which could disrupt the transportation process.
Step 3: Transportation via the Longest Conveyor Belt
The Bou Craa conveyor belt, known as the longest conveyor belt in the world, stretches over 61 miles (98 kilometers) from the mine to the port of El Aaiún. This belt is designed to handle the harsh desert environment and the abrasive nature of phosphate rock. As the ore travels along the belt, it passes through various transfer points and support structures that help maintain the belt’s stability and efficiency.
Step 4: Monitoring and Maintenance
Throughout the journey, the conveyor belt system is monitored using advanced sensors and control systems. These systems track the belt’s speed, load, and operational status, ensuring that any issues are quickly detected and addressed. Regular maintenance is conducted to keep the belt in optimal condition, including checking for wear and tear, lubricating moving parts, and replacing any damaged sections.
Step 5: Unloading at the Port
Upon reaching the coastal port of El Aaiún, the phosphate ore is unloaded from the conveyor belt using automated unloading systems. The ore is then transferred to storage facilities or directly onto ships for export. This unloading process is designed to be efficient and minimize material handling time, ensuring that the phosphate ore reaches its destination promptly.
Efficiency and Environmental Impact of the Longest Conveyor Belt
The Bou Craa conveyor belt system offers several advantages in terms of efficiency and environmental impact. Here are five examples:
1. Continuous Operation
The longest conveyor belt operates continuously, 24 hours a day, seven days a week. This constant operation ensures a steady flow of phosphate ore from the mine to the port, significantly increasing the overall efficiency of the transportation process. Continuous operation also helps meet the high demand for phosphate in global markets.
2. Reduced Transportation Costs
By using the conveyor belt system, the need for truck transportation is significantly reduced. This not only lowers transportation costs but also minimizes the wear and tear on local infrastructure, such as roads and bridges. The cost savings can be reinvested into further improving the mining and transportation operations.
3. Lower Carbon Emissions
The conveyor belt system is an environmentally friendly alternative to truck transportation. By reducing the number of diesel-powered trucks required to transport the phosphate ore, the conveyor belt helps lower carbon emissions and reduce the overall environmental footprint of the mining operation. This contributes to cleaner air and a reduction in greenhouse gas emissions.
4. Dust Suppression
The design of the Bou Craa conveyor belt includes dust suppression measures, such as enclosed sections and dust suppression sprays. These measures help reduce the amount of dust generated during the transportation process, improving air quality and reducing the impact on nearby communities and ecosystems.
5. Minimizing Spillage and Waste
The conveyor belt system is designed to minimize spillage and waste of phosphate ore. Advanced containment technologies, such as skirting and seals, ensure that the ore remains on the belt during transport. This reduces material loss and prevents environmental contamination, making the transportation process more efficient and sustainable.
The transportation of phosphate ore from the Bou Craa mine to the coast using the world’s longest conveyor belt is a remarkable example of engineering innovation and efficiency. The step-by-step process ensures that the ore is transported smoothly and with minimal environmental impact. The continuous operation, reduced transportation costs, lower carbon emissions, dust suppression measures, and minimized spillage all contribute to the overall efficiency and sustainability of the transportation method. The Bou Craa conveyor belt system exemplifies the potential of advanced technology to enhance industrial operations while protecting the environment.
Capacity of The Longest Conveyor Belt
Let’s delve into the details of the capacities of some of the longest conveyor belts around the world, including how their design and purpose influence their capacities.
Bou Craa, Western Sahara (Longest Conveyor Belt)
- Length: 98 kilometers (61 miles)
- Material Transported: Phosphate rock
- Capacity: Approximately 2,000 to 2,500 tonnes per hour The Bou Craa conveyor belt is designed to transport phosphate rock from the mine in the Western Sahara to the port town of Marsa in Morocco. Phosphate rock is a dense, granular material, and the conveyor’s capacity of up to 2,500 tonnes per hour reflects the need to transport large quantities efficiently to keep up with the mine’s production of about 3 million tonnes per year. The length and capacity of this belt make it a critical infrastructure component for Morocco’s phosphate industry.
Boddington Bauxite Mine, Western Australia
- Length: 31 kilometers (19 miles)
- Material Transported: Bauxite ore
- Capacity: Up to 4,400 tonnes per hour This conveyor belt, which runs from the Boddington Bauxite Mine to the refinery, is engineered to handle the heavy loads associated with bauxite, which is the primary raw material for aluminum production. The high capacity of 4,400 tonnes per hour allows the conveyor to meet the demands of the mining and refining operations, which process large volumes of ore daily.
Curragh Coal Mine, Queensland, Australia
- Length: 20 kilometers (12.4 miles)
- Material Transported: Coal
- Capacity: Approximately 3,000 tonnes per hour The conveyor belt at the Curragh Coal Mine is designed for the transportation of coal, which is lighter but more voluminous than materials like bauxite or phosphate. The 3,000 tonnes per hour capacity allows the belt to efficiently transport coal from the mine to the processing facility or transport hubs. This capacity is crucial for maintaining the mine’s production levels and ensuring a steady supply to power plants or export terminals.
India-Bangladesh Border Conveyor Belt
- Length: 17 kilometers (11 miles)
- Material Transported: Limestone and shale
- Capacity: 960 tonnes per hour The conveyor system that crosses the India-Bangladesh border is primarily used to transport limestone and shale from a quarry in India to a cement plant in Bangladesh. Given the relatively modest capacity of 960 tonnes per hour, this belt is tailored to the specific requirements of the cement production process, where consistent supply is more critical than sheer volume. The belt’s elevated structure helps protect it from monsoon-related flooding, ensuring uninterrupted operation throughout the year.
Mount Saddleback to Worsley Refinery, Western Australia (World’s Longest Single Conveyor System)
- Length: Over 31 miles (50 kilometers)
- Material Transported: Bauxite ore
- Capacity: Approximately 2,700 tonnes per hour This conveyor system is remarkable not only for its length but also for its ability to transport a substantial 2,700 tonnes of bauxite ore per hour. The belt moves at a speed of 16 mph (about 25 km/h), which is optimized for the safe and efficient transport of heavy loads over long distances. The conveyor’s route, which includes 22 tunnels and 10 bridges, is designed to handle the complex terrain between the mine and the refinery, ensuring a steady flow of materials essential for aluminum production.
These conveyor belts, among the longest in the world, are designed with specific capacities to match the demands of their respective industries. Factors such as the type of material being transported, the distance covered, the terrain, and the operational requirements all influence the design and capacity of each system.
- Bou Craa focuses on high-volume transport of phosphate rock, crucial for Morocco’s phosphate industry.
- Boddington and Mount Saddleback systems are tailored for the bauxite ore, essential for aluminum production.
- Curragh is optimized for coal, a lighter but voluminous material, crucial for energy production.
- India-Bangladesh is specialized for limestone and shale, supporting a cross-border cement industry.
Each conveyor’s capacity reflects a balance between the need to move large quantities of material efficiently and the constraints imposed by the environment and the material’s properties.
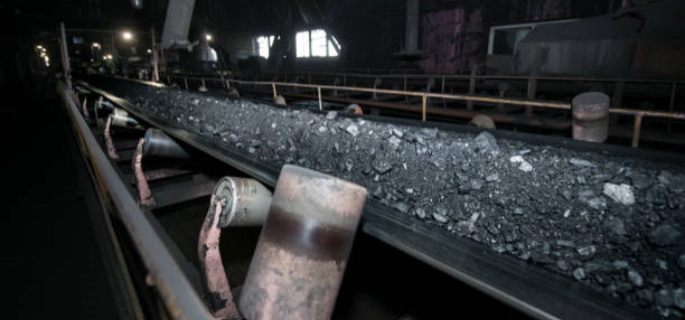
Cost of The Longest Conveyor Belt
Estimating the cost of the world’s longest conveyor belts involves several factors, including the length, material, engineering requirements, terrain, and operational capacity. While specific figures are often proprietary and can vary widely, here is a general breakdown of the factors influencing the cost and some estimates based on industry standards:
1. Bou Craa, Western Sahara (Longest Conveyor Belt)
- Length: 98 kilometers (61 miles)
- Estimated Cost: The total cost of a conveyor belt of this length and complexity can range from $100 million to $250 million or more. Factors Influencing Cost:
- Material: The belt material needs to be durable and capable of withstanding harsh desert conditions.
- Engineering: The system’s design includes various interlinked belts, adding complexity.
- Installation: Installing a belt of this length in a remote desert region involves significant logistical challenges.
- Maintenance and Operation: Ongoing maintenance and operational costs also contribute to the total cost over the belt’s lifetime.
2. Boddington Bauxite Mine, Western Australia
- Length: 31 kilometers (19 miles)
- Estimated Cost: The construction of this conveyor belt is estimated to have cost around $50 million to $100 million. Factors Influencing Cost:
- Capacity Requirements: A high capacity of 4,400 tonnes per hour necessitates robust design and construction.
- Terrain: The belt’s route through a rugged landscape increases construction complexity and cost.
- Material Handling: The belt must be built to handle bauxite, a heavy and abrasive material.
3. Mount Saddleback to Worsley Refinery, Western Australia
- Length: 50 kilometers (31 miles)
- Estimated Cost: Similar to Boddington, this system likely cost around $100 million. Factors Influencing Cost:
- Length and Complexity: The long distance and complex route, including tunnels and bridges, significantly add to the cost.
- Material Transport: The system’s capacity to transport 2,700 tonnes of bauxite per hour requires high-grade materials and engineering.
- Infrastructure: Tunnels, bridges, and other infrastructure necessary to support the belt’s route add to the total cost.
4. India-Bangladesh Border Conveyor Belt
- Length: 17 kilometers (11 miles)
- Estimated Cost: The cost of this cross-border conveyor system is estimated at $25 million to $50 million. Factors Influencing Cost:
- Cross-Border Complexity: Managing a conveyor belt across two countries involves additional regulatory and logistical costs.
- Elevated Structure: The belt’s elevated design to prevent flooding during monsoon seasons increases construction costs.
- Maintenance Requirements: The need for regular maintenance by teams from both countries adds to operational costs.
The cost of constructing the world’s longest conveyor belts can range from $25 million to $250 million or more, depending on various factors:
- Length: Longer belts naturally cost more due to the greater amount of material and construction required.
- Material: The type and quality of materials used, such as the durability of the belt itself, affect the cost.
- Terrain: Challenging terrain, such as deserts or rugged landscapes, increases both construction and maintenance costs.
- Capacity: Higher capacity belts require more robust engineering, adding to the cost.
- Infrastructure: Additional infrastructure like tunnels, bridges, and elevated sections significantly contribute to the overall cost.
- Location: Remote locations increase logistical costs, including transportation of materials and labor.
- Regulatory and Environmental: Cross-border systems or those in environmentally sensitive areas may face higher regulatory and environmental costs.
These estimates provide a general idea of the financial investment required to build and maintain these large-scale conveyor systems, which are vital for efficient material transport in various industries.
The Longest Conveyor Belt in the United States
The United States is home to many remarkable engineering feats, and among them is the longest conveyor belt, which stands as a testament to American innovation and industrial prowess. This extensive conveyor system plays a crucial role in several industries, particularly mining, where efficient material transportation is paramount.
Location and Length
The longest conveyor belt in the United States is located in the state of Nevada, specifically at the Henderson Mine. This belt, stretching approximately 19 miles (30 kilometers), holds the record for the longest conveyor belt system in the nation. It spans a vast distance, traversing diverse terrains and showcasing the capability of modern engineering to overcome geographical challenges. The belt’s length allows for the seamless transport of materials from remote mining locations to processing facilities, thereby enhancing operational efficiency.
Primary Use and Materials Transported
The primary use of the longest conveyor belt in the United States is to transport extracted minerals and ores from mining sites to processing plants. This conveyor system is essential for the continuous and efficient movement of bulk materials, which is critical in maintaining the productivity and economic viability of mining operations. The conveyor belt is designed to handle a variety of materials, each crucial to different sectors of the industry. Below are five examples of materials transported by the longest conveyor belt in the United States:
1. Copper Ore
Copper ore is one of the primary materials transported by the Henderson Mine conveyor belt. Copper is a vital industrial metal, widely used in electrical wiring, plumbing, and telecommunications. The conveyor belt facilitates the movement of raw copper ore from the extraction site to the processing plant, where it undergoes refinement to produce pure copper for industrial use.
2. Molybdenum
Molybdenum is another significant material transported by this extensive conveyor system. This metal is used to strengthen steel alloys, making it indispensable in the production of high-strength steel used in construction, automotive manufacturing, and aerospace applications. The conveyor belt ensures that molybdenum ore is efficiently moved from the mine to the refining facilities.
3. Gold Ore
The conveyor belt at the Henderson Mine also transports gold ore. Gold, with its high economic value and wide range of uses in electronics, jewelry, and finance, is a critical mineral. The conveyor system’s efficiency in transporting gold ore supports the profitability and sustainability of gold mining operations.
4. Limestone
Limestone is another material transported by the longest conveyor belt in the United States. Limestone is a versatile industrial mineral used in the production of cement, glass, and steel. It is also used in environmental applications, such as flue gas desulfurization in power plants. The conveyor belt helps in the rapid and efficient movement of limestone from quarries to processing facilities.
5. Phosphate Rock
Phosphate rock, essential for the production of fertilizers, is also transported by this conveyor system. The efficient transport of phosphate rock is crucial for the agricultural industry, as it supports the production of fertilizers that enhance soil fertility and crop yields. The conveyor belt’s role in moving phosphate rock underscores its importance in supporting agricultural productivity and food security.
Engineering and Operational Efficiency
The engineering behind the longest conveyor belt in the United States is a marvel of modern technology. Designed to withstand harsh environmental conditions and heavy loads, the conveyor belt is constructed using high-strength materials and advanced components. The system includes multiple drive stations, tensioning units, and monitoring sensors to ensure optimal performance and reliability.
The conveyor belt’s operation is meticulously managed to minimize downtime and maintain a consistent flow of materials. Advanced monitoring systems track the belt’s performance, identifying any issues that could lead to disruptions. Maintenance teams are on standby to address any problems quickly, ensuring the belt’s continuous operation. This level of efficiency is crucial in mining operations, where any downtime can result in significant financial losses.
Environmental Considerations
The implementation of the longest conveyor belt in the United States also reflects a commitment to environmental stewardship. By reducing the need for truck transportation, the conveyor belt minimizes the environmental impact associated with the extraction and processing of minerals. This reduction in truck traffic leads to lower emissions of greenhouse gases and other pollutants, contributing to cleaner air and reduced carbon footprint.
Moreover, the conveyor system is designed to operate with minimal noise and dust generation, further reducing its environmental impact. The belt’s route is carefully planned to avoid sensitive ecological areas, and efforts are made to rehabilitate any disturbed land along the conveyor’s path. These measures demonstrate a balanced approach to industrial development, where economic benefits are achieved while preserving the environment.
The longest conveyor belt in the United States is more than just an engineering marvel; it is a critical component of the nation’s mining infrastructure. By facilitating the efficient transport of essential minerals such as copper, molybdenum, gold, limestone, and phosphate rock, this conveyor system supports a wide range of industries and contributes significantly to the economy. Its advanced engineering, operational efficiency, and environmental considerations make it a model for future conveyor belt systems worldwide. The Henderson Mine’s conveyor belt exemplifies how innovative technology can drive industrial success while promoting sustainability.
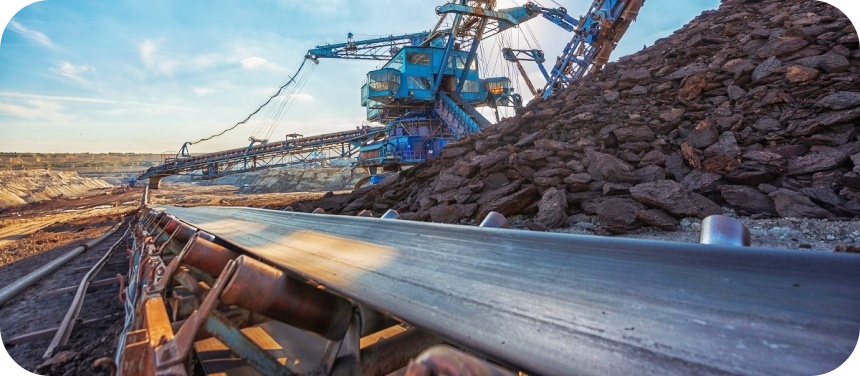
The Longest Conveyor Belt in Africa
Africa is home to some of the most remarkable engineering projects in the world, one of which is the longest conveyor belt on the continent. This extensive conveyor system is not only a testament to engineering excellence but also plays a critical role in the economic development of the region it serves. This section will provide an in-depth look at Africa’s record-holding conveyor system, detailing its length, construction, and operational purpose.
Africa’s Record-Holding Conveyor System
The longest conveyor belt in Africa is located in Western Sahara, a disputed territory along the Atlantic coast. This impressive conveyor system is known as the Bou Craa conveyor belt. It holds the record for the longest single conveyor belt in the world, stretching over 61 miles (98 kilometers) from the phosphate mines of Bou Craa to the port city of El Aaiún. The conveyor belt’s primary function is to transport phosphate rock from the interior mining areas to the coastal port, where it is then shipped globally.
Length and Route
The Bou Craa conveyor belt is an engineering marvel due to its sheer length and the challenging terrain it traverses. Spanning 61 miles, the conveyor belt crosses deserts, rocky outcrops, and other harsh environments. This extensive reach is critical in connecting the remote Bou Craa phosphate mines with the coastal shipping facilities. The conveyor belt’s route is carefully designed to optimize efficiency and minimize environmental impact, ensuring that the valuable phosphate rock is transported smoothly and reliably.
Construction and Design
Constructing the longest conveyor belt in Africa required advanced engineering techniques and robust materials to withstand the region’s harsh conditions. The belt itself is made from high-strength materials designed to resist wear and tear from the abrasive phosphate rock. The system includes numerous support structures, such as steel frames and pylons, to maintain stability and alignment over the long distance.
The construction process involved extensive planning and coordination. Engineers had to consider various factors, including the belt’s tension, speed, and load capacity. Advanced technology was employed to monitor and control these parameters, ensuring that the conveyor operates efficiently and safely. The belt’s design also incorporates features to handle the extreme temperatures and sandy conditions typical of the Saharan environment.
Operational Purpose
The primary purpose of the Bou Craa conveyor belt is to transport phosphate rock from the mines to the port of El Aaiún. Phosphate rock is a vital resource used in the production of fertilizers, which are essential for global agriculture. By efficiently transporting this raw material, the conveyor belt plays a crucial role in supporting food production worldwide.
The operational efficiency of the conveyor belt is remarkable. It can transport up to 2,000 tons of phosphate rock per hour, significantly reducing the need for truck transport. This high capacity ensures that the phosphate mines can operate continuously, maximizing their output and profitability. The conveyor belt’s ability to move large quantities of material quickly and efficiently is a key factor in the success of the Bou Craa mining operation.
Economic Impact
The Bou Craa conveyor belt has a significant economic impact on the region. By facilitating the efficient transport of phosphate rock, the conveyor system supports the local mining industry, providing jobs and economic stability to the area. The revenue generated from phosphate exports is crucial for the local economy, funding infrastructure projects and community development initiatives.
Furthermore, the conveyor belt’s efficiency helps to lower the overall cost of phosphate production, making it more competitive in the global market. This competitiveness is vital for maintaining market share and ensuring the long-term sustainability of the mining operation.
Environmental Considerations
Operating the longest conveyor belt in Africa also involves careful consideration of environmental factors. The conveyor belt helps to reduce the environmental footprint of the mining operation by minimizing the need for truck transport. This reduction in truck traffic leads to lower emissions of greenhouse gases and other pollutants, contributing to cleaner air and a smaller carbon footprint.
Additionally, the conveyor system is designed to operate with minimal noise and dust generation, reducing its impact on the surrounding environment. Efforts are made to rehabilitate any disturbed land along the conveyor’s path, preserving the natural landscape and protecting local ecosystems.
The longest conveyor belt in Africa, located in Western Sahara, is a remarkable feat of engineering and a vital component of the region’s mining infrastructure. Stretching over 61 miles, the Bou Craa conveyor belt efficiently transports phosphate rock from remote mines to coastal shipping facilities, playing a crucial role in global agriculture. Its construction and operation showcase advanced engineering techniques and a commitment to environmental sustainability. By supporting the local economy and reducing the environmental impact of mining operations, the Bou Craa conveyor belt exemplifies the potential of innovative infrastructure projects to drive economic growth and development.
The Longest Conveyor Belt in Oklahoma
Oklahoma, known for its rich natural resources and vibrant industrial sector, is home to one of the longest conveyor belts in the United States. This remarkable conveyor system is a crucial asset to the state’s economy, facilitating the efficient transportation of various materials and supporting local industries. In this section, we will provide a detailed presentation of Oklahoma’s notable conveyor belt, highlighting its function and contribution to the local industry.
Presentation of Oklahoma’s Notable Conveyor Belt
The longest conveyor belt in Oklahoma is situated in the southeastern part of the state, within the region’s extensive coal mining operations. This conveyor system is part of the McCurtain County Coal Mine, one of the largest coal mines in the state. Stretching over 10 miles (16 kilometers), this conveyor belt is a vital infrastructure component that underscores Oklahoma’s commitment to leveraging advanced technology in its industrial processes.
The conveyor belt was designed and constructed to address the specific needs of the coal mining industry. It traverses a diverse terrain, including rolling hills and dense forests, demonstrating the adaptability and robustness of modern conveyor technology. The belt’s extensive reach allows it to connect remote mining sites with central processing facilities, ensuring a steady flow of materials and enhancing operational efficiency.
Function of the Longest Conveyor Belt in Oklahoma
The primary function of the longest conveyor belt in Oklahoma is to transport coal from the extraction sites to the processing and distribution centers. This conveyor system plays a crucial role in streamlining the coal mining process, reducing the reliance on truck transportation, and minimizing logistical challenges. The belt’s efficiency in moving large quantities of coal supports the continuous operation of the mines, which is essential for meeting production targets and maintaining economic viability.
The conveyor belt is equipped with advanced monitoring and control systems to ensure optimal performance. These systems track various parameters, such as belt speed, load capacity, and operational status, allowing for real-time adjustments and minimizing downtime. The belt’s design includes features to handle the heavy loads and abrasive nature of coal, ensuring durability and long-term reliability.
Contribution to Local Industry
The longest conveyor belt in Oklahoma significantly contributes to the local industry by facilitating the efficient transport of coal and other materials. Here are five examples of its impact:
1. Coal Mining
Coal mining is the primary industry supported by Oklahoma’s longest conveyor belt. The belt’s ability to transport large volumes of coal from the mines to processing facilities ensures a steady supply of this essential energy resource. This efficiency helps keep production costs low and supports the competitiveness of Oklahoma’s coal industry in the national and international markets.
2. Power Generation
The coal transported by the conveyor belt is a critical input for power generation plants in Oklahoma and surrounding states. By ensuring a reliable supply of coal, the conveyor system supports the continuous operation of power plants, contributing to the region’s energy security and stability. This reliable energy supply is essential for both residential and industrial consumers.
3. Employment and Economic Growth
The operation and maintenance of the longest conveyor belt in Oklahoma create numerous job opportunities for local communities. These jobs range from engineering and technical roles to maintenance and operational positions. The economic activity generated by the conveyor system and the associated coal mining operations contributes to local economic growth and prosperity.
4. Industrial Raw Materials
In addition to coal, the conveyor belt is used to transport other industrial raw materials, such as gypsum and limestone. These materials are essential for various industries, including construction, manufacturing, and agriculture. The conveyor system’s efficiency in moving these materials supports the productivity and growth of these sectors, further diversifying Oklahoma’s industrial base.
5. Environmental Benefits
While coal mining and transport have environmental impacts, the conveyor belt system helps mitigate some of these effects. By reducing the need for truck transportation, the conveyor belt lowers emissions of greenhouse gases and other pollutants associated with diesel-powered vehicles. Additionally, the belt’s operation is designed to minimize noise and dust generation, reducing its overall environmental footprint.
The longest conveyor belt in Oklahoma is a remarkable engineering achievement that plays a vital role in the state’s industrial landscape. Located within the McCurtain County Coal Mine, this 10-mile conveyor system supports the efficient transport of coal and other materials, contributing to the productivity and economic viability of the local mining industry. Its advanced design and operational efficiency underscore the importance of modern technology in enhancing industrial processes.
By facilitating the continuous operation of coal mines and supporting various industries, the conveyor belt significantly impacts Oklahoma’s economy. It creates jobs, supports energy production, and contributes to the sustainable use of natural resources. As a key infrastructure component, the longest conveyor belt in Oklahoma exemplifies the state’s commitment to leveraging innovation and technology to drive industrial growth and development.
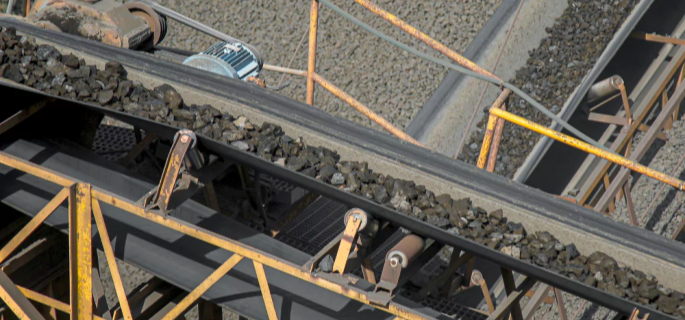
Innovations and Future Considerations About Longest Conveyor Belt
As the demand for efficient and sustainable material transportation continues to grow, the world’s longest conveyor belt systems are at the forefront of technological advancements and innovations. These innovations aim to enhance the performance, durability, and environmental sustainability of conveyor belt operations. In this section, we will explore some of the latest technological advancements in conveyor belt design and operation and provide predictions for future developments and their potential impact on global industries.
Technological Advancements in Conveyor Belt Design and Operation
The design and operation of the longest conveyor belt systems have seen significant improvements, driven by the need for greater efficiency and environmental sustainability. Here are some of the key innovations:
1. Advanced Materials and Coatings
One of the most significant advancements in conveyor belt technology is the development of advanced materials and coatings. These materials are designed to withstand the harsh conditions and heavy loads encountered by the longest conveyor belts. For example, high-strength synthetic materials and specialized rubber compounds offer enhanced durability and resistance to wear and tear. Additionally, coatings that reduce friction and improve energy efficiency are increasingly being used, prolonging the lifespan of the belts and reducing maintenance costs.
2. Smart Monitoring Systems
The integration of smart monitoring systems has revolutionized the operation of the longest conveyor belt systems. These systems utilize sensors and IoT (Internet of Things) technology to continuously monitor the condition and performance of the conveyor belts. Real-time data on belt speed, load, temperature, and wear can be collected and analyzed, allowing for predictive maintenance and early detection of potential issues. This not only improves operational efficiency but also reduces downtime and maintenance costs.
3. Energy-Efficient Drives
Energy efficiency is a critical consideration in the operation of long conveyor belts. Recent advancements in drive technology, such as variable frequency drives (VFDs) and high-efficiency motors, have significantly reduced energy consumption. VFDs allow for precise control of the conveyor belt speed, optimizing energy use based on the load and operational conditions. This results in substantial energy savings and a lower environmental footprint.
4. Modular Design
Modular design is another innovation that enhances the flexibility and maintainability of the longest conveyor belts. Modular components, such as interchangeable belt sections, rollers, and drive units, make it easier to replace and upgrade parts as needed. This reduces downtime during maintenance and allows for quicker adaptations to changing operational requirements. Modular design also facilitates the expansion or reconfiguration of conveyor systems to accommodate new mining or processing sites.
5. Automated Control Systems
Automated control systems have become an integral part of modern conveyor belt operations. These systems use advanced algorithms and machine learning to optimize the performance of the conveyor belts. Automated controls can adjust belt speed, tension, and load distribution in real-time, ensuring smooth and efficient operation. Additionally, automated systems can integrate with other mining and processing equipment, creating a seamless and coordinated operation.
Predictions for Future Developments and Their Potential Impact on Global Industries
As technology continues to advance, several trends and developments are expected to shape the future of the longest conveyor belt systems. Here are five predictions for future advancements and their potential impact on global industries:
1. Increased Automation and Autonomous Operation
The future of conveyor belt systems is likely to see a greater emphasis on automation and autonomous operation. Autonomous conveyor systems, equipped with advanced sensors and AI, will be able to operate with minimal human intervention. This will enhance operational efficiency, reduce labor costs, and improve safety. Autonomous systems will be particularly beneficial in hazardous environments, such as mining operations, where worker safety is a primary concern.
2. Integration with Renewable Energy Sources
The integration of renewable energy sources, such as solar and wind power, with conveyor belt operations is expected to become more prevalent. Renewable energy can power conveyor systems, reducing their reliance on fossil fuels and lowering their carbon footprint. This shift towards sustainable energy sources will align with global efforts to combat climate change and promote environmental sustainability.
3. Advanced Predictive Maintenance
Predictive maintenance, powered by AI and machine learning, will become more sophisticated. Advanced predictive maintenance systems will analyze vast amounts of data from conveyor belt operations to predict and prevent failures before they occur. This proactive approach will minimize downtime, extend the lifespan of equipment, and reduce maintenance costs. Predictive maintenance will also enhance the overall reliability and efficiency of conveyor belt systems.
4. Enhanced Environmental Monitoring
Environmental monitoring will play a crucial role in the future of conveyor belt systems. Advanced monitoring technologies will track the environmental impact of conveyor operations in real-time, including emissions, noise levels, and dust generation. These systems will ensure compliance with environmental regulations and help companies adopt more sustainable practices. Enhanced environmental monitoring will also provide valuable data for optimizing operations to minimize their ecological footprint.
5. Smart Integration with Digital Twins
The concept of digital twins—virtual replicas of physical systems—will revolutionize the design and operation of the longest conveyor belts. Digital twins will enable real-time simulation and analysis of conveyor belt operations, allowing for precise control and optimization. By integrating digital twins with smart monitoring and control systems, companies can achieve unprecedented levels of efficiency and performance. Digital twins will also facilitate remote monitoring and troubleshooting, reducing the need for on-site interventions.
The longest conveyor belt systems are poised for significant advancements driven by technological innovation and a focus on sustainability. From advanced materials and smart monitoring systems to energy-efficient drives and modular design, these innovations are transforming the way conveyor belts are designed and operated. Future developments, such as increased automation, integration with renewable energy, advanced predictive maintenance, enhanced environmental monitoring, and smart integration with digital twins, will further enhance the efficiency, reliability, and sustainability of conveyor belt operations. These advancements will have a profound impact on global industries, enabling more efficient and environmentally responsible material transportation.
For detailed information on our conveyor belts, please complete the form below.
FAQs About Longest Conveyor Belt
The longest single flight conveyor is the conveyor belt at the Bou Craa phosphate mine in Western Sahara. This engineering marvel stretches approximately 61 miles (98 kilometers) from the Bou Craa mine to the coastal city of El Aaiún. The conveyor system is used to transport phosphate ore, a vital raw material for fertilizers, from the mine to the port for export. This conveyor belt holds the record for the longest single continuous belt in the world. Its design and construction are feats of modern engineering, capable of handling harsh environmental conditions and the abrasive nature of phosphate rock, ensuring efficient and uninterrupted transport of materials.
The standard length of a conveyor belt can vary widely depending on its application and industry requirements. In industrial settings, standard conveyor belts typically range from a few meters to several hundred meters in length. For example, in manufacturing and warehousing, conveyor belts are often designed to fit the specific layout and operational needs, which can result in varying lengths. However, for more extensive applications like mining and large-scale material handling, conveyor belts can be designed to stretch over several kilometers. It’s essential to note that the length of a conveyor belt is determined by factors such as the distance between the material’s source and destination, the nature of the material being transported, and the specific operational requirements of the facility.
The longest conveyor belt in the Southern Hemisphere is located in Western Australia, at the Boddington Bauxite Mine. This conveyor belt system is used to transport bauxite from the mine to the processing facilities, covering a distance of approximately 31 miles (50 kilometers). The Boddington conveyor belt plays a crucial role in the efficient transport of bauxite, which is essential for the production of alumina and aluminum. The system’s design incorporates advanced technologies to handle the heavy loads and abrasive nature of bauxite, ensuring reliable and continuous operation. The Boddington conveyor belt exemplifies the significant advancements in conveyor technology, showcasing the capability to support large-scale mining operations in challenging environments.
An endless conveyor belt is a type of conveyor belt that has been manufactured without any seams or joints. This seamless design provides several advantages, including enhanced durability, reduced maintenance needs, and improved reliability. Endless conveyor belts are particularly useful in applications where a continuous loop is required to transport materials without interruptions. They are commonly used in industries such as food processing, textiles, and manufacturing, where the seamless nature of the belt ensures a smooth and consistent flow of materials. The absence of seams eliminates the risk of the belt snapping or fraying at the joints, which can occur in belts with spliced or glued ends. Additionally, endless conveyor belts can be custom-made to fit specific operational requirements, ensuring optimal performance and longevity in demanding industrial environments.
Maximum Length of Conveyor Belt: The maximum length of a conveyor belt that is considered satisfactory depends on various factors, including the type of material being transported, the belt design, tension, and the operational environment. However, conveyor belts can typically range from a few meters to several kilometers. In many industrial applications, belts up to 15-20 kilometers are used, but anything longer might require additional tensioning systems and power stations to maintain efficiency.
Longest Conveyor Belt in Texas: The longest conveyor belt in Texas is located at the North American Coal Corporation’s Sabine Mine. This conveyor belt is approximately 14 miles (22.5 kilometers) long and is used to transport lignite from the mine to a power plant. It is one of the longest overland conveyor belts in the world.
Last Updated on August 19, 2024 by Jordan Smith
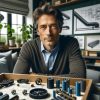
Jordan Smith, a seasoned professional with over 20 years of experience in the conveyor system industry. Jordan’s expertise lies in providing comprehensive solutions for conveyor rollers, belts, and accessories, catering to a wide range of industrial needs. From initial design and configuration to installation and meticulous troubleshooting, Jordan is adept at handling all aspects of conveyor system management. Whether you’re looking to upgrade your production line with efficient conveyor belts, require custom conveyor rollers for specific operations, or need expert advice on selecting the right conveyor accessories for your facility, Jordan is your reliable consultant. For any inquiries or assistance with conveyor system optimization, Jordan is available to share his wealth of knowledge and experience. Feel free to reach out at any time for professional guidance on all matters related to conveyor rollers, belts, and accessories.