Engineering Feat: Longest Conveyor Belt in the World
The longest conveyor belt in the world represents a marvel of modern engineering, exemplifying advancements in material transport technology. Spanning incredible distances, these conveyor belts are crucial for efficiently moving materials over vast areas, significantly reducing the need for traditional transportation methods. The longest conveyor belt in the world showcases the pivotal role these systems play across various industries globally, from mining to manufacturing. These belts not only enhance operational efficiency but also contribute to environmental sustainability by minimizing carbon footprints. The implementation of the longest conveyor belt in the world demonstrates the intersection of innovation and practicality in contemporary industrial applications.
The Titans of Transport: Top 10 Longest Conveyor Belt in the World
Conveyor belts are essential for efficient material transport across various industries, significantly enhancing productivity and operational efficiency. The longest conveyor belt in the world sets the benchmark for engineering feats, showcasing how advanced technology can optimize large-scale industrial processes. This section provides an overview of the top ten longest conveyor belts in the world, comparing their lengths, industries served, and geographic locations.
1. Bou Craa, Western Sahara
The Bou Craa conveyor belt holds the title of the longest belt conveyor in the world. Stretching over 98 kilometers (61 miles) from the phosphate mines of Bou Craa to the port city of El-Aaiun, it is a vital infrastructure for the phosphate industry. The belt plays a crucial role in transporting phosphate rock from the inland mines to the coast for export, significantly reducing the need for road or rail transport.
2. Boddington Bauxite Mine, Australia
The Boddington Bauxite Mine in Western Australia is home to one of the longest conveyor belts in the world, measuring around 31 kilometers (19 miles). This belt is integral to the mining operations, moving bauxite from the mine to the refinery efficiently and with minimal environmental impact. The belt’s design and length demonstrate the mining industry’s reliance on conveyor technology to streamline operations and improve productivity.
3. Nammuldi Iron Ore Mine, Australia
Another Australian marvel, the Nammuldi Iron Ore Mine, features a conveyor belt that stretches approximately 20 kilometers (12 miles). This belt is essential for transporting iron ore from the mine to the processing plant, facilitating the seamless movement of raw materials. The Nammuldi conveyor system exemplifies how the mining sector leverages long conveyor belts to enhance operational efficiency and reduce transportation costs.
4. Shondoni Mine, South Africa
The Shondoni Mine in South Africa boasts a conveyor belt system that extends for about 20 kilometers (12 miles). This belt is crucial for moving coal from the mine to the processing facilities, ensuring a steady supply of raw materials. The Shondoni conveyor belt highlights the importance of efficient transport systems in the coal mining industry, reducing the need for trucks and minimizing environmental impact.
5. Collahuasi, Chile
In Chile, the Collahuasi copper mine operates one of the longest conveyor belts in the world, measuring 17 kilometers (10.6 miles). This belt is vital for transporting copper ore from the mine to the processing plant, enhancing the mine’s productivity. The Collahuasi conveyor system illustrates the significance of conveyor belts in the copper mining sector, where efficient material handling is crucial for meeting production targets.
6. Los Pelambres, Chile
Another Chilean example, the Los Pelambres copper mine, features a conveyor belt that stretches 16 kilometers (10 miles). This belt is essential for moving copper ore from the mine to the processing facilities, optimizing the transport process. The Los Pelambres conveyor highlights how the mining industry relies on long conveyor belts to streamline operations and improve efficiency.
7. El Abra, Chile
El Abra, one of Chile’s significant copper mines, operates a conveyor belt system that extends for 14 kilometers (8.7 miles). This belt is crucial for the efficient transport of copper ore, demonstrating the vital role of conveyor systems in the mining industry. The El Abra conveyor belt underscores the importance of long-distance material transport solutions in large-scale mining operations.
8. Dahej, India
In India, the Dahej port features a conveyor belt that measures 10 kilometers (6.2 miles). This belt is instrumental in transporting bulk materials such as coal and bauxite from the port to various industrial sites. The Dahej conveyor system highlights the role of long conveyor belts in port operations, facilitating efficient material handling and reducing reliance on traditional transport methods.
9. Rössing Uranium Mine, Namibia
The Rössing Uranium Mine in Namibia operates a conveyor belt that extends for 9 kilometers (5.6 miles). This belt is vital for transporting uranium ore from the mine to the processing plant, ensuring a steady flow of raw materials. The Rössing conveyor system illustrates the importance of efficient transport solutions in the uranium mining industry, where safety and reliability are paramount.
10. Fosbucraa, Western Sahara
The Fosbucraa conveyor belt, located in Western Sahara, stretches over 7 kilometers (4.3 miles). This belt is crucial for the phosphate industry, transporting phosphate rock from the mines to the processing facilities. The Fosbucraa conveyor system demonstrates how long conveyor belts can optimize material transport in challenging environments, reducing the need for traditional transport methods.
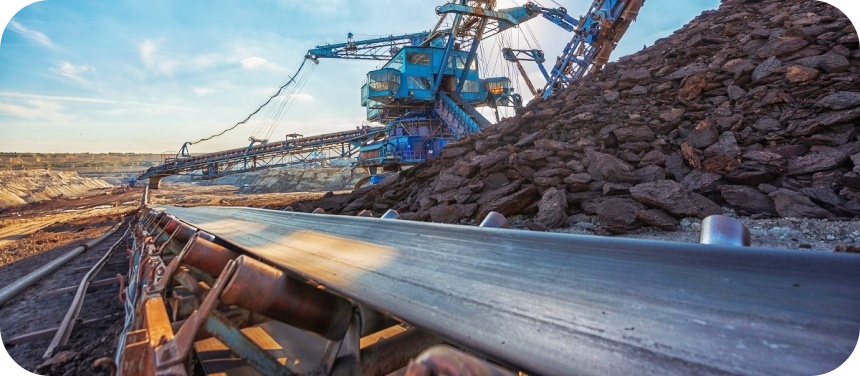
Table: Comparison of the Longest Conveyor Belts
These conveyor belts represent the pinnacle of engineering excellence, illustrating the critical role of long-distance transport solutions in various industries. The longest conveyor belt in the world, along with others in this list, showcases the importance of advanced technology in optimizing material handling, reducing environmental impact, and enhancing operational efficiency across diverse industrial applications.
Navigating the Phosphorus Conveyor Dilemma Via Longest Conveyor Belt in the World
Phosphorus is a crucial element for agricultural productivity, and its transport is vital for ensuring a steady supply to global markets. The world’s longest conveyor belt system plays a significant role in transporting phosphorus from mines to processing facilities and export terminals. However, this system is not without its challenges and environmental considerations. This section will address these issues, providing five examples to illustrate the complexities involved in transporting phosphorus via conveyor belts.
Challenges and Environmental Considerations
1. Dust Emissions and Air Quality
One of the primary challenges of transporting phosphorus via conveyor belts is the emission of dust particles. Phosphorus in its raw form can generate significant amounts of dust when transported over long distances. This dust can affect air quality, posing health risks to nearby communities and workers.
Example: Bou Craa, Western Sahara
The Bou Craa conveyor belt, the longest conveyor belt in the world, transports phosphorus over a distance of 98 kilometers. Despite advanced engineering, the system faces challenges related to dust emissions. To mitigate this, dust suppression technologies such as water sprays and windbreaks are employed. However, maintaining these systems in the harsh desert environment adds to operational costs and complexity.
2. Environmental Impact on Surrounding Ecosystems
The impact of conveyor belt systems on surrounding ecosystems is another significant consideration. The construction and operation of these systems can disrupt local wildlife habitats and natural landscapes.
Example: Bou Craa’s Impact on the Sahara Desert
The Bou Craa conveyor belt cuts through the Sahara Desert, an ecosystem home to unique flora and fauna. The belt’s presence has altered the natural landscape, affecting animal migration patterns and plant growth. Efforts to minimize these impacts include designing the belt to follow existing natural contours and implementing reforestation projects to restore affected areas.
3. Energy Consumption and Carbon Footprint
The operation of long conveyor belts requires substantial energy, contributing to the carbon footprint of the phosphorus supply chain. Finding ways to reduce energy consumption is essential for making these systems more sustainable.
Example: Boddington Bauxite Mine, Australia
The conveyor belt at the Boddington Bauxite Mine, while primarily used for bauxite, provides insight into energy consumption challenges. Operating over 31 kilometers, the system consumes significant power. Implementing energy-efficient motors and renewable energy sources, such as solar panels, can help reduce the carbon footprint, a strategy that could be applied to phosphorus transport systems like Bou Craa.
4. Maintenance and Operational Costs
Long conveyor belts require continuous maintenance to ensure efficient operation. The harsh environments where these belts often operate, such as deserts or tropical regions, can accelerate wear and tear, increasing maintenance costs.
Example: Maintenance Challenges at Bou Craa
The Bou Craa conveyor belt system operates in a harsh desert environment, where sand and extreme temperatures can cause significant wear on mechanical components. Regular maintenance is crucial to prevent breakdowns and ensure smooth operation. This includes frequent inspections, replacement of worn parts, and the use of durable materials designed to withstand harsh conditions.
5. Political and Social Considerations
The regions where phosphorus conveyor belts operate often face political and social challenges. These can include disputes over land use, the impact on local communities, and broader geopolitical issues.
Example: Political Context of Bou Craa
The Bou Craa phosphate mine and its conveyor belt are located in Western Sahara, a region with ongoing territorial disputes. The political situation affects the operation and security of the conveyor belt system. Ensuring the safety of the infrastructure and the people working on it requires careful negotiation and cooperation with local authorities and communities.
Mitigation Strategies
To address these challenges and environmental considerations, several mitigation strategies can be implemented:
- Advanced Dust Control Technologies: Utilizing state-of-the-art dust suppression systems, such as enclosed conveyor belts and electrostatic precipitators, can help reduce dust emissions significantly.
- Environmental Impact Assessments: Conducting thorough environmental impact assessments before construction can help identify potential disruptions to ecosystems and allow for the development of strategies to minimize these impacts.
- Energy Efficiency Measures: Implementing energy-efficient technologies and incorporating renewable energy sources can reduce the carbon footprint of long conveyor belts. This includes using energy-efficient motors, optimizing belt design to reduce friction, and harnessing solar or wind power.
- Robust Maintenance Programs: Developing comprehensive maintenance programs that include regular inspections, preventive maintenance, and the use of durable materials can extend the lifespan of conveyor belts and reduce operational costs.
- Community Engagement and Political Negotiation: Engaging with local communities and stakeholders, and navigating the political landscape through diplomacy and collaboration, can help address social and political challenges. This includes ensuring fair land use practices, providing benefits to local communities, and maintaining open lines of communication with authorities.
Transporting phosphorus via the longest conveyor belt in the world involves navigating a complex array of challenges and environmental considerations. From dust emissions and ecosystem impacts to energy consumption and political issues, each aspect requires careful management and innovative solutions. By implementing advanced technologies, conducting thorough impact assessments, and engaging with stakeholders, it is possible to mitigate these challenges and ensure the sustainable operation of these critical transport systems. The Bou Craa conveyor belt serves as a prime example of how modern engineering can address these issues, paving the way for more sustainable and efficient phosphorus transport in the future.
At the Heart of Phosphate Mining: Longest Conveyor Belt in the World
Phosphate mining is a critical industry for global agriculture, as phosphorus is an essential component of fertilizers that help sustain crop yields and food production. At the heart of this industry lies the world’s largest phosphate mine, which not only drives significant economic activity but also showcases remarkable advancements in mining and conveyor technology. This section will dive into the operations and global impact of this colossal mine, emphasizing its dependency on the longest conveyor belt in the world.
Overview of the World’s Largest Phosphate Mine
The Bou Craa mine, located in Western Sahara, is the largest phosphate mine in the world. This mine is operated by the National Moroccan Phosphate Company (OCP) and produces millions of tons of phosphate rock annually. The Bou Craa mine is a cornerstone of the global phosphate supply chain, providing raw materials essential for the production of fertilizers used worldwide.
Dependency on Conveyor Technology
The Bou Craa mine’s operations are heavily dependent on an extensive conveyor belt system, which includes the longest conveyor belt in the world. This 98-kilometer-long belt transports phosphate rock from the mine site to the coastal city of El-Aaiun, where the material is processed and shipped to global markets. The conveyor belt system is a critical component of the mine’s logistics, enabling efficient and cost-effective transport of large quantities of phosphate.
Longest Conveyor Belt in the World
The longest conveyor belt in the world is not just an engineering marvel; it is also a vital piece of infrastructure for the Bou Craa mine. The belt significantly reduces the need for road or rail transport, minimizing environmental impact and operational costs. The belt’s ability to transport phosphate over such a long distance is a testament to the advancements in conveyor technology and its importance in modern mining operations.
Operations of the Bou Craa Mine
Mining Process
The phosphate mining process at Bou Craa begins with the extraction of phosphate rock from the earth. This involves drilling and blasting to break up the rock, which is then loaded onto trucks and transported to the initial crushing facility. The crushed rock is then conveyed to the processing plant where it undergoes further crushing, washing, and screening to produce high-quality phosphate concentrate.
Conveyor System Integration
The integration of the conveyor system into the mining process is seamless and highly efficient. After the initial crushing, the phosphate rock is loaded onto the conveyor belt, which transports it across the desert to El-Aaiun. This conveyor system operates continuously, 24 hours a day, ensuring a steady flow of material from the mine to the port.
Maintenance and Monitoring
Maintaining the longest conveyor belt in the world is a complex task that requires constant monitoring and maintenance. The harsh desert environment poses challenges such as sand intrusion, extreme temperatures, and mechanical wear and tear. The mine employs a team of engineers and technicians who regularly inspect the belt, perform preventive maintenance, and make necessary repairs to ensure uninterrupted operation.
Global Impact of Bou Craa Phosphate Mine
Economic Contributions
The Bou Craa mine is a major economic driver in the region and for Morocco as a whole. It provides employment opportunities for thousands of people and generates significant revenue through the export of phosphate rock. The mine’s operations have a ripple effect on the local economy, supporting businesses and services that cater to the mining industry and its workforce.
Agricultural Significance
Phosphates from the Bou Craa mine play a crucial role in global agriculture. The high-quality phosphate rock is used to produce fertilizers that enhance soil fertility and increase crop yields. This, in turn, supports food security and agricultural productivity worldwide. Countries across Africa, Europe, and Asia rely on phosphate imports from Bou Craa to meet their agricultural needs.
Environmental and Social Considerations
While the Bou Craa mine and its conveyor belt system bring significant economic benefits, they also raise environmental and social considerations. The large-scale extraction and transport of phosphate rock can impact local ecosystems and communities. The mine operators have implemented measures to mitigate environmental impacts, such as dust control systems and efforts to minimize land disturbance. Additionally, the company engages with local communities to address social concerns and ensure that the benefits of mining are shared.
The Future of Phosphate Mining at Bou Craa
The future of phosphate mining at Bou Craa is closely tied to advancements in technology and sustainable practices. Ongoing investments in conveyor technology aim to enhance efficiency and reduce the environmental footprint of mining operations. Research and development efforts are focused on improving the durability and performance of the conveyor belt system, ensuring it can continue to operate effectively in the challenging desert environment.
The Bou Craa mine, home to the longest conveyor belt in the world, is a cornerstone of the global phosphate industry. Its operations exemplify the integration of advanced technology and efficient logistics in large-scale mining. The mine’s significant economic contributions, agricultural importance, and efforts to address environmental and social considerations highlight its pivotal role in the global supply chain. As technology continues to evolve, the Bou Craa mine and its conveyor belt system will remain at the forefront of the phosphate mining industry, driving progress and sustainability in this vital sector.
Bou Craa: A Conveyor Belt Like No Other Longest Conveyor Belt in the World
The Bou Craa conveyor belt system stands as an unparalleled engineering marvel, playing a pivotal role in the global phosphate supply chain. Known as the longest conveyor belt in the world, it spans an impressive 98 kilometers (61 miles) across the harsh landscape of the Western Sahara desert. This section takes an in-depth look at Bou Craa’s conveyor belt system, reflecting on its engineering, capabilities, and crucial role in phosphate transport, with five specific examples to illustrate its significance.
Engineering Marvel
The construction of the Bou Craa conveyor belt system required innovative engineering solutions to overcome the challenges posed by the desert environment. The belt is designed to withstand extreme temperatures, abrasive sand, and strong winds, ensuring continuous operation despite harsh conditions.
Durability in Extreme Conditions
The belt material is composed of high-strength rubber and steel, capable of withstanding temperatures ranging from freezing cold at night to scorching heat during the day. This durability is critical for preventing wear and tear that could disrupt the transport of phosphate rock.
Capabilities of the Conveyor System
The Bou Craa conveyor belt system is not just remarkable for its length but also for its capabilities in transporting vast quantities of phosphate rock efficiently and sustainably.
High Transport Capacity
The conveyor belt system can transport approximately 2,000 tons of phosphate rock per hour. This high capacity is essential for meeting the global demand for phosphate, particularly in the agricultural sector where it is a key component of fertilizers.
Crucial Role in Phosphate Transport
The efficiency and reliability of the Bou Craa conveyor belt are crucial for the economic viability of the phosphate mining operations and the broader supply chain.
Reducing Transportation Costs
By transporting phosphate rock directly from the mines to the processing facilities in El-Aaiun, the conveyor belt system significantly reduces the need for truck or rail transport. This reduction in transportation costs translates into lower production costs and competitive pricing for phosphate products in the global market.
Environmental Benefits
The Bou Craa conveyor belt system also offers environmental benefits by minimizing the ecological footprint of phosphate transport.
Lower Carbon Emissions
The conveyor belt’s continuous operation reduces the need for fossil fuel-powered vehicles, thereby lowering carbon emissions associated with phosphate transport. This is particularly important in the context of global efforts to combat climate change and reduce greenhouse gas emissions.
Operational Efficiency
The seamless integration of the conveyor belt into the phosphate mining and processing operations enhances overall efficiency and productivity.
Streamlined Logistics
The conveyor belt system is synchronized with the mining and processing schedules, ensuring that phosphate rock is continuously supplied to the processing plant without delays. This streamlined logistics approach maximizes the efficiency of the entire production process, from extraction to shipment.
The Bou Craa conveyor belt system, as the longest conveyor belt in the world, exemplifies the pinnacle of engineering innovation and operational efficiency in the mining industry. Its ability to transport vast quantities of phosphate rock across a challenging desert environment highlights its crucial role in sustaining the global phosphate supply chain. The durability of the belt in extreme conditions, its high transport capacity, and its contributions to reducing transportation costs and carbon emissions are testament to its significance. Furthermore, the operational efficiency it provides through streamlined logistics ensures that the Bou Craa mine remains a key player in the global phosphate market. As the demand for phosphate continues to grow, the importance of this extraordinary conveyor belt system will only increase, solidifying its status as an indispensable asset in the world of industrial transport.
The Bou Craa Mine and Its Lifeline: The Longest Conveyor Belt in the World
The Bou Craa mine, situated in the heart of the Western Sahara, is renowned not only for its vast phosphate reserves but also for its reliance on the longest conveyor belt in the world. This remarkable conveyor system is more than just a transport mechanism; it is the lifeline of the mine, integral to its operations and overall success. This section will examine how the Bou Craa mine is inherently linked to its conveyor system, highlighting operational dependencies and the scale of transport, with five specific examples to illustrate its significance.
Operational Dependencies
The Bou Craa mine’s operations are intricately connected to the conveyor belt system, which ensures the continuous and efficient transport of phosphate rock from the mine to the processing facilities.
Continuous Supply Chain
The conveyor belt provides a continuous supply of phosphate rock to the processing plant in El-Aaiun, eliminating the need for intermittent and less efficient transportation methods such as trucks or rail. This continuous supply chain is essential for maintaining the productivity and profitability of the mining operations.
Scale of Transport
The scale at which the Bou Craa conveyor belt operates is staggering, reflecting the sheer volume of phosphate that needs to be moved from the mine to the coast.
High Volume Transport
The conveyor belt system is capable of transporting around 2,000 tons of phosphate rock per hour. This high volume transport capacity is crucial for meeting both domestic and international demand for phosphate, ensuring that the mine can operate at optimal efficiency.
Economic Impact
The economic viability of the Bou Craa mine is heavily dependent on the efficiency of the conveyor belt system, which helps to minimize costs and maximize output.
Cost Efficiency
By using the conveyor belt system, the Bou Craa mine significantly reduces the cost of transporting phosphate rock. Traditional methods such as trucking would not only be more expensive but also less reliable. The conveyor belt, therefore, plays a vital role in keeping operational costs low and maintaining the mine’s competitive edge in the global market.
Environmental Considerations
The conveyor belt system also contributes to reducing the environmental impact of the mining operations, making it a more sustainable option.
Reduced Carbon Footprint
The use of the conveyor belt reduces the need for fossil fuel-powered transportation, thereby lowering the carbon footprint of the mining operations. This is particularly important in the context of increasing environmental regulations and the global push towards more sustainable industrial practices.
Maintenance and Reliability
Maintaining the conveyor belt system is crucial for the uninterrupted operation of the Bou Craa mine. Regular maintenance ensures that the system remains reliable and efficient.
Maintenance Strategies
The harsh desert environment poses significant challenges to the maintenance of the conveyor belt. Sand, extreme temperatures, and mechanical wear require a robust maintenance strategy that includes regular inspections, timely repairs, and the use of durable materials designed to withstand these conditions. The reliability of the conveyor belt is essential for avoiding costly downtimes and ensuring a steady flow of phosphate rock.
The Bou Craa mine’s success is inextricably linked to the longest conveyor belt in the world. This conveyor system is the lifeline of the mine, facilitating the efficient transport of phosphate rock over a distance of 98 kilometers. The operational dependencies of the mine on this system highlight the importance of continuous and high-volume transport, which is essential for meeting global demand. The economic impact of the conveyor belt is evident in the cost savings it provides, while its environmental benefits contribute to a reduced carbon footprint. Moreover, the maintenance strategies employed ensure the reliability and longevity of the system, critical for the uninterrupted operation of the mine.
As phosphate remains a vital resource for agriculture and various industries, the role of the Bou Craa conveyor belt will continue to be of paramount importance. The integration of advanced technology and sustainable practices in the operation of this conveyor system sets a benchmark for mining operations worldwide. The longest conveyor belt in the world is not just a feat of engineering; it is the backbone of the Bou Craa mine, exemplifying the intersection of efficiency, sustainability, and economic viability in the mining industry.
Longest Conveyor Belt in the World: Navigating Environmental and Political Terrains
Large-scale conveyor systems, such as the longest conveyor belt in the world at Bou Craa, play a pivotal role in modern industrial operations. However, their implementation and operation come with significant environmental and political implications. This section will discuss the broader environmental impacts of such systems and the political nuances in regions like Bou Craa, providing five specific examples to illustrate these complexities.
Environmental Impacts
1. Habitat Disruption and Biodiversity Loss
The construction and operation of extensive conveyor belts can lead to habitat disruption and biodiversity loss. The physical footprint of the conveyor system can fragment habitats, affecting local wildlife and plant species.
Bou Craa’s Impact on the Sahara Desert Ecosystem
The Bou Craa conveyor belt cuts through the Western Sahara desert, an ecosystem home to various species adapted to harsh desert conditions. The construction of the belt has disrupted these habitats, leading to changes in animal migration patterns and plant growth. Efforts to mitigate these impacts include creating wildlife corridors and replanting native vegetation along the belt’s path.
2. Dust and Air Quality
Transporting materials such as phosphate rock generates dust, which can have adverse effects on air quality and human health. Dust control measures are essential to minimize these impacts.
Dust Suppression at Bou Craa
At Bou Craa, dust suppression systems, including water sprays and windbreaks, are used to reduce dust emissions from the conveyor belt. These measures help protect the health of workers and nearby communities while minimizing the environmental footprint of the mining operations.
3. Energy Consumption and Carbon Footprint
Large-scale conveyor systems require substantial energy to operate, contributing to their carbon footprint. Improving energy efficiency and incorporating renewable energy sources can help mitigate this impact.
Energy Efficiency Initiatives
To reduce the energy consumption of the Bou Craa conveyor belt, energy-efficient motors and variable frequency drives are used. Additionally, there are ongoing efforts to integrate renewable energy sources, such as solar power, to further reduce the system’s carbon footprint.
4. Water Usage
Water is often used in dust suppression and material washing processes, which can strain local water resources, especially in arid regions.
Water Management at Bou Craa
In the arid environment of Western Sahara, water management is critical. The Bou Craa mine employs water recycling systems to minimize freshwater usage. Additionally, advanced dust suppression technologies that require less water are being explored to reduce the overall water footprint.
5. Landscape Alteration and Aesthetic Impact
The presence of a large conveyor belt system can alter the natural landscape, impacting the visual aesthetics of the region. This can affect local tourism and the cultural value of the landscape.
Visual Impact Mitigation
At Bou Craa, efforts have been made to integrate the conveyor system into the natural landscape as much as possible. This includes designing the belt to follow natural land contours and implementing landscaping projects to restore areas affected by construction.
Political Nuances
1. Territorial Disputes
The location of large-scale conveyor systems can intersect with areas of territorial disputes, complicating their operation and management.
Western Sahara Dispute
The Bou Craa mine and its conveyor belt are situated in Western Sahara, a region with a long-standing territorial dispute between Morocco and the Polisario Front. This dispute adds a layer of complexity to the operation of the mine and the conveyor system, requiring careful navigation of political sensitivities and compliance with international regulations.
2. Local Community Relations
Building and operating conveyor systems in regions with local communities requires careful management of relations to ensure mutual benefits and minimize conflicts.
Community Engagement at Bou Craa
OCP, the operator of the Bou Craa mine, engages with local communities to address their concerns and ensure that the benefits of mining are shared. This includes providing employment opportunities, investing in local infrastructure, and supporting community development projects.
3. Regulatory Compliance
Operating in different regions requires compliance with a variety of environmental and political regulations, which can be complex and multifaceted.
Environmental Regulations
At Bou Craa, the mine and conveyor system must comply with both Moroccan environmental regulations and international standards. This includes conducting regular environmental impact assessments, implementing mitigation measures, and adhering to best practices in environmental management.
4. Economic Dependencies
The economic stability of regions hosting large conveyor systems can be heavily dependent on the operation of these systems, leading to political and economic pressures.
Economic Impact on Western Sahara
The Bou Craa mine is a significant economic driver in Western Sahara, providing jobs and revenue. This economic dependency creates pressure to maintain continuous operation and address any disruptions quickly to avoid economic instability.
5. International Relations
The operation of large-scale conveyor systems can influence international relations, especially in regions with strategic resources like phosphate.
Diplomatic Considerations
The export of phosphate from Bou Craa is crucial for many countries’ agricultural sectors. This creates a diplomatic dimension to the operation of the conveyor belt, as maintaining stable and reliable exports is important for international relations and trade agreements.
The longest conveyor belt in the world at Bou Craa exemplifies the intricate balance between technological advancement and environmental stewardship, as well as the complex political landscapes in which such systems operate. Addressing the environmental impacts through innovative solutions and navigating political nuances with careful diplomacy are essential for the sustainable operation of these vital industrial infrastructures. As global demand for resources like phosphate continues to grow, the lessons learned from Bou Craa can inform the development and management of similar systems worldwide, ensuring they contribute positively to both local and global contexts.
Fill out the inquiry form for pricing, specifications, and availability of our conveyor belts.
FAQs About Longest Conveyor Belt in the World
The longest single flight conveyor is the conveyor system used at the Bou Craa phosphate mine in Western Sahara. This remarkable engineering feat stretches over 98 kilometers (61 miles) from the phosphate mines in Bou Craa to the port city of El-Aaiun. This conveyor belt system is designed to transport phosphate rock efficiently across a vast distance, minimizing the need for truck or rail transport. The length and efficiency of the Bou Craa conveyor system make it an essential component in the global supply chain for phosphate, a critical element in agricultural fertilizers. The Bou Craa conveyor is not only notable for its length but also for its ability to operate continuously in the harsh desert environment, showcasing the advancements in conveyor belt technology.
The strongest conveyor belt in the world is the PHOENOCORD St 7500, produced by Phoenix Conveyor Belt Systems GmbH. This belt is designed to handle extreme loads and conditions, making it ideal for use in mining operations and other heavy-duty applications. The PHOENOCORD St 7500 is constructed with high-tensile steel cords, providing it with unparalleled strength and durability. This conveyor belt can carry loads over long distances and through challenging environments, ensuring reliable and efficient material transport. The development of such strong conveyor belts has revolutionized industries that rely on the movement of heavy materials, enhancing productivity and safety. The PHOENOCORD St 7500’s robustness ensures minimal downtime and maintenance, making it a cost-effective solution for large-scale industrial operations.
The length of a conveyor belt can vary significantly depending on its application and the specific requirements of the operation it serves. Conveyor belts can range from a few meters to several kilometers in length. For example, the longest single flight conveyor belt in the world, located at the Bou Craa phosphate mine in Western Sahara, stretches over 98 kilometers (61 miles). In contrast, conveyor belts used in manufacturing or assembly lines may be only a few meters long. The design and length of a conveyor belt are determined by factors such as the distance materials need to be transported, the type of materials being moved, and the operational environment. Customization is key to ensuring that a conveyor belt system meets the specific needs of an industrial process, providing efficient and reliable material handling.
An endless conveyor belt is a type of conveyor belt that is made in a continuous loop without any joints or seams. This design provides several advantages, including increased durability, reduced maintenance, and improved reliability. Endless conveyor belts are often used in applications where the belt needs to operate without interruptions and where joint failure could lead to significant operational downtime. They are commonly found in industries such as food processing, automotive manufacturing, and packaging, where consistent and reliable belt performance is crucial. The absence of joints in an endless conveyor belt eliminates the weak points typically found in spliced belts, ensuring smoother operation and reducing the risk of belt failure. The seamless design also helps in maintaining hygiene standards in industries like food processing, where contamination risks must be minimized.
Last Updated on August 13, 2024 by Jordan Smith
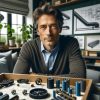
Jordan Smith, a seasoned professional with over 20 years of experience in the conveyor system industry. Jordan’s expertise lies in providing comprehensive solutions for conveyor rollers, belts, and accessories, catering to a wide range of industrial needs. From initial design and configuration to installation and meticulous troubleshooting, Jordan is adept at handling all aspects of conveyor system management. Whether you’re looking to upgrade your production line with efficient conveyor belts, require custom conveyor rollers for specific operations, or need expert advice on selecting the right conveyor accessories for your facility, Jordan is your reliable consultant. For any inquiries or assistance with conveyor system optimization, Jordan is available to share his wealth of knowledge and experience. Feel free to reach out at any time for professional guidance on all matters related to conveyor rollers, belts, and accessories.