Loose Steel Rollers: Key to Advanced Machinery Performance
Loose steel rollers, integral components in the realm of mechanical engineering and manufacturing, play a pivotal role across a myriad of industrial applications. These small yet powerful elements are crucial in facilitating smooth and efficient motion in machinery, ranging from automotive assemblies to conveyor systems. The versatility and reliability of loose steel rollers stem not only from their robust material composition but also from the diverse sizes and specifications in which they are available. This ensures a perfect fit for various operational needs, enhancing performance and longevity. As the demand for precision and durability in mechanical components escalates, the focus on sourcing these rollers from reputable suppliers becomes paramount. Availability, coupled with the right supplier, can significantly impact the operational efficiency and maintenance schedules of industrial machinery, making the choice of loose steel rollers a critical decision for engineers and procurement specialists alike.
What Are Loose Steel Rollers
Loose steel rollers, pivotal in the seamless operation of countless machines, embody the essence of mechanical efficiency and durability. These components, though small in size, play a monumental role in the functionality of various industrial systems. Here’s a deeper dive into their definition, explanation, and the critical roles they fulfill within machinery and equipment.
Definition and Explanation of Loose Steel Rollers
At the heart of many mechanical systems lie loose steel rollers, components that might seem inconsequential at first glance but are, in fact, foundational to industrial operations. Here are key points that define and explain their significance:
- Material Composition: Crafted from high-grade steel, loose steel rollers boast a composition that ensures resilience and longevity, often undergoing hardening processes to resist wear and tear.
- Versatility in Sizes: Their availability in diverse sizes and diameters makes them adaptable to a wide range of applications, from delicate precision instruments to robust industrial machinery.
- Precision Engineered: Manufactured with exacting tolerances, these rollers guarantee the smooth and efficient operation of equipment, minimizing mechanical discrepancies.
- High Load Capacity: Engineered to bear substantial loads, they are indispensable in heavy-duty applications where durability under stress is paramount.
- Customization: Beyond off-the-shelf varieties, loose steel rollers can be tailored to meet the nuanced requirements of specialized machinery, offering solutions that are as unique as the challenges they address.
- Surface Finish: The rollers’ surface can be finished in various ways to enhance their performance, including treatments to reduce friction and wear.
- Durability: Their steel construction not only confers strength but also ensures that they can withstand harsh operational environments without degradation.
- Cost-Effectiveness: Despite their superior quality and performance, these rollers remain an economically viable option, offering significant value over their operational lifespan.
The Role of Loose Steel Rollers in Machinery and Equipment
Loose steel rollers are not merely components; they are the linchpins of industrial efficiency and reliability. Their roles in machinery and equipment are as varied as they are vital:
- Facilitating Movement: They are the driving force behind the linear or rotational movement within machines, significantly reducing friction and wear between moving parts.
- Load Bearing: Essential in applications that demand the support and distribution of heavy loads, they ensure stability and balance.
- Precision Applications: In sectors where precision is non-negotiable, such as in aerospace or printing, loose steel rollers are key to achieving the exacting standards required.
- Enhancing Efficiency: By minimizing friction, these rollers not only improve the operational speed of machinery but also contribute to lower energy consumption and operational costs.
- Versatility: Their application is widespread, finding utility in conveyor systems, roller tables, bearings, and guide rails, among others.
- Maintenance Reduction: The robustness and reliability of loose steel rollers lead to decreased maintenance demands, ensuring machinery remains operational for longer periods.
- Custom Applications: They offer bespoke solutions to unique mechanical challenges, enabling the design and operation of custom machinery.
- Improving Product Lifespan: By facilitating smoother operations and reducing mechanical stress, these rollers indirectly contribute to extending the service life of the entire system.
Loose steel rollers stand as unsung heroes in the industrial landscape, their small stature belied by their immense impact on the efficiency, reliability, and longevity of mechanical systems.
Types of Loose Steel Rollers
Loose steel rollers are critical in various sectors, including automotive, aerospace, and manufacturing, due to their versatility and functionality. Each type serves specific operational needs, enhancing the performance and reliability of machinery.
Loose Needle Rollers
Loose needle rollers are precision elements designed for applications where space and weight are critical factors.
- High Load Capacity: They are capable of supporting high radial loads despite their small size, making them suitable for compact designs.
- Precision Applications: Ideal for high-precision machinery, such as gearboxes and engines, where they ensure smooth operation.
- Space-Saving Design: Their slender form factor allows for reduced space usage in machinery design, enabling more efficient use of available space.
- Reduced Friction: The small contact area with the raceway minimizes friction, leading to higher efficiency and reduced wear.
- Ease of Installation: Their simple cylindrical shape facilitates easy installation and maintenance.
- Cost-Effectiveness: Offers an economical solution for achieving high precision and load capacity in various applications.
Rounded End Loose Needle Rollers
Rounded end loose needle rollers are designed to mitigate stress concentration at the ends, enhancing the bearing life in dynamic applications.
- Reduced Stress Concentration: The rounded ends distribute stress more evenly, reducing the likelihood of premature failure.
- Enhanced Durability: This feature makes them more durable, especially in applications with oscillating movements.
- Improved Load Distribution: They provide better load distribution across the roller length, preventing edge loading.
- Versatility: Suitable for a wide range of applications, including automotive joints and pivot points.
- Smooth Operation: The rounded design promotes smoother operation in applications requiring frequent starts and stops.
- Application Specificity: Particularly beneficial in designs where the roller ends interface directly with other components.
Metal Roller Bearings
Metal roller bearings are robust components designed to carry heavy loads and facilitate smooth motion in a wide range of industrial applications.
- Durable Construction: Constructed from high-strength metals, these bearings are designed for longevity and reliability.
- Heavy-Duty Performance: Capable of handling heavy loads, making them ideal for industrial and construction machinery.
- High-Speed Capability: Engineered to perform well at high speeds, ensuring efficient operation of machinery.
- Resistance to Harsh Conditions: Their metal construction offers resistance to harsh environmental conditions, including high temperatures and corrosive substances.
- Versatile Applications: Used in everything from conveyor systems to automotive engines, showcasing their adaptability.
- Maintenance Efficiency: Designed for ease of maintenance, which is crucial for minimizing downtime in industrial settings.
Hardened Steel Roller
Hardened steel rollers are treated to enhance their hardness and wear resistance, making them suitable for the most demanding applications.
- Superior Wear Resistance: The hardening process increases their resistance to wear and abrasion.
- High Load Bearing: They can support higher loads without deformation, ensuring consistent performance.
- Long Service Life: The enhanced durability extends the operational lifespan of machinery.
- Resistance to Deformation: Ideal for applications where rollers are subject to high stress and potential deformation.
- Versatility in Use: Suitable for use in a variety of environments, including those with variable temperatures and loads.
- Cost Efficiency Over Time: Although the initial cost may be higher, the long-term savings in maintenance and replacement costs are significant.
Ball Bearing Rollers
Ball bearing rollers use spherical balls to reduce friction and handle both radial and axial loads, offering a versatile solution for many applications.
- Low Friction Operation: The spherical design minimizes contact area, reducing friction and wear.
- High-Speed Capability: Excellently suited for applications requiring high-speed operation with minimal noise and vibration.
- Radial and Axial Load Handling: Capable of supporting both types of loads, enhancing their applicability.
- Precision Movement: Offers precise movement and alignment, crucial for high-performance machinery.
- Ease of Replacement: Their standardized sizes and designs make replacement and maintenance straightforward.
- Wide Range of Applications: From small electronic devices to large industrial machinery, their versatility is unmatched.
Each type of loose steel roller offers unique advantages, making them indispensable in various industrial applications. The selection of the appropriate roller type depends on the specific requirements of the application, including load capacity, operational speed, and environmental conditions.
Sizes and Specifications of Loose Steel Rollers
The engineering world acknowledges loose steel rollers as indispensable components across a myriad of applications, where their size and specifications directly influence the efficiency, functionality, and durability of machinery. The precision with which these rollers are manufactured and selected for specific applications underscores their critical role in industrial operations. Let’s delve into the diversity of sizes available and the paramount importance of choosing the right size for specific applications.
Range of Sizes Available for Loose Steel Rollers
The manufacturing of loose steel rollers accommodates a broad spectrum of sizes, designed to meet the varied demands of industrial machinery:
- Extensive Diameter Range: From the minute to the significantly large, the diameter of loose steel rollers spans a wide range, ensuring suitability for both delicate and robust machinery.
- Varied Length Options: Lengths are just as varied as diameters, providing options for different load distributions and operational requirements.
- Customization Availability: For applications with unique requirements, custom sizes are available, offering tailored solutions that ensure optimal performance.
- Metric and Imperial Measurements: Catering to global standards, rollers are produced in both metric and imperial measurements, facilitating their use in international machinery designs.
- Precision Tolerances: Manufactured with strict tolerances, these rollers meet the high precision needed for specialized applications, minimizing operational variances.
- Diverse Surface Finishes: Options for surface finishes, such as polished or coated, allow for customization based on frictional and wear requirements.
- Wall Thickness Variations: The thickness of the roller’s wall can be selected based on the desired strength and load-bearing capacity, affecting the component’s durability.
- Specific Weight Capacities: Rollers are rated for different weight capacities, essential for matching the specific load requirements of various applications.
Importance of Selecting the Correct Size for Specific Applications
Choosing the appropriate size for loose steel rollers is not merely a matter of fit but a critical decision that impacts several facets of machinery operation:
- Optimal Load Distribution: Correct sizing ensures that loads are evenly distributed across the roller, enhancing longevity and preventing uneven wear.
- Achievement of Precision: In precision-critical applications, the right size is fundamental to achieving the desired accuracy and maintaining the integrity of the machinery’s operation.
- Ensured Fit and Compatibility: Proper sizing guarantees that rollers fit seamlessly within their designated machinery, eliminating issues of misalignment or inefficient operation.
- Operational Efficiency: The size of the roller influences the machinery’s efficiency, with the correct size minimizing friction and facilitating smoother operation.
- Extended Durability: Appropriately sized rollers are less prone to premature wear, contributing to the machinery’s overall durability and reliability.
- Noise Minimization: The right roller size can significantly reduce operational noise, an important consideration in environments where noise reduction is crucial.
- Simplified Maintenance: Correctly sized rollers streamline maintenance processes, reducing the likelihood of unexpected failures and simplifying the replacement procedure.
- Cost Savings: By enhancing operational efficiency and extending the lifespan of machinery components, selecting the correct size of loose steel rollers leads to considerable cost savings over time.
The selection of loose steel rollers in the appropriate size and specification is a nuanced process that demands careful consideration. It is a balance between the physical dimensions of the rollers and the operational demands of the machinery they are part of, ensuring that the chosen components contribute positively to the system’s overall performance and longevity.
Suppliers and Availability of Loose Steel Rollers
The market for loose steel rollers is vast and varied, with numerous suppliers offering a wide range of products to meet the diverse needs of industries. Whether you’re looking for loose steel rollers for sale or specific types like loose needle rollers, understanding where to find these components and how to select a reputable supplier is crucial.
Loose Steel Rollers for Sale
Finding loose steel rollers for sale involves navigating a complex market with many vendors. Here are key points to consider:
- Online Marketplaces: Platforms like Alibaba, Amazon Business, and eBay offer extensive listings from various suppliers worldwide.
- Manufacturer Websites: Direct purchases from manufacturers’ websites ensure you get genuine products and comprehensive support.
- Industrial Supply Stores: Local and online industrial suppliers often stock a wide range of rollers for immediate purchase.
- Specialized Distributors: Companies specializing in bearings and rollers can provide expert advice and a curated selection of products.
- Trade Shows: Industrial and manufacturing trade shows are great places to connect with suppliers and see products firsthand.
- Referrals: Recommendations from industry peers can lead you to trusted suppliers with proven track records.
- Direct Inquiries: Contacting manufacturers directly can sometimes yield custom solutions and better pricing for bulk orders.
Tips on Selecting a Reputable Supplier
- Quality Certifications: Look for suppliers with ISO certifications or other industry standards, ensuring product quality and reliability.
- Product Range: Choose suppliers with a wide product range, offering flexibility in selection and the possibility of one-stop shopping.
- Customer Service: Reputable suppliers provide excellent customer service, including product support and hassle-free returns.
- Technical Support: Suppliers that offer technical support and guidance on product selection are invaluable.
- Delivery and Lead Times: Consider suppliers with reliable delivery services and reasonable lead times.
- Customization Options: Suppliers offering customization can tailor products to your specific needs.
- Market Reputation: Research suppliers’ reputations through reviews, testimonials, and industry forums.
- Pricing and Payment Terms: Competitive pricing and clear payment terms are signs of a reputable supplier.
Loose Needle Rollers Suppliers
Choosing the right supplier for loose needle rollers requires careful consideration of several factors:
- Specialization: Look for suppliers specializing in needle rollers to ensure a high level of expertise.
- Quality Assurance: Suppliers should have strict quality control processes to guarantee product integrity.
- Material Knowledge: A good supplier understands the materials used in their products and can advise on the best options for specific applications.
- Engineering Support: Suppliers offering engineering support can assist in product selection and design considerations.
- Inventory Management: Reliable suppliers maintain sufficient stock levels to meet customer demands promptly.
- Global Reach: For international operations, suppliers with a global distribution network ensure product availability across different regions.
- After-Sales Support: Post-sale support, including troubleshooting and maintenance advice, is crucial.
- Compliance with Standards: Ensure suppliers comply with relevant industrial and safety standards.
- Innovative Solutions: Leading suppliers invest in research and development to offer innovative solutions that enhance product performance.
Leading Suppliers in the Industry
- Ball and Roller Store: Known for a wide range of quality products and excellent customer service.
- SKF: A global leader in bearings and related technologies.
- Timken: Renowned for high-performance bearings and mechanical power transmission products.
- NSK: Offers a broad portfolio of bearings, catering to various industrial needs.
- NTN: A leading bearing supplier with a focus on innovation and quality.
- Schaeffler: Provides precision components and systems for automotive and industrial applications.
- Koyo: Known for high-quality bearings and related products.
- INA: Specializes in rolling bearings, linear systems, and precision components for automotive applications.
Selecting the right supplier for loose steel rollers or loose needle rollers is a critical step that impacts the efficiency, reliability, and cost-effectiveness of your operations. By considering the points outlined above, you can make an informed decision that ensures you receive high-quality products tailored to your specific needs.
Advanced Applications of Loose Steel Rollers
The realm of industrial machinery is ever-evolving, with advancements in technology leading to the development of components that meet the demands of high-performance applications. Among these innovations, loose steel rollers have emerged as pivotal elements, especially when considering their role in oversize roller bearings. These specialized bearings cater to unique applications where standard sizes cannot deliver the required efficiency or durability.
Oversize Roller Bearings
Oversize roller bearings, which utilize loose steel rollers, are designed for applications that demand high load-bearing capacity and precision over large scale operations. Their unique characteristics make them indispensable in several advanced applications:
- Heavy Machinery: Essential in construction and mining equipment, where they withstand extreme loads and conditions.
- Wind Turbines: Used in the yaw and pitch bearings to manage the immense forces encountered by wind turbine blades.
- Marine Applications: Critical for ship propeller shafts and rudder assemblies, offering resistance to saltwater corrosion.
- Steel Mills: Employed in rolling mill machinery, capable of enduring the high temperatures and heavy loads of steel processing.
- Aerospace: Integral to the landing gear and engine components of aircraft, where reliability and performance are paramount.
- Railway Axles: Ensuring the smooth operation and safety of rail vehicles under varying loads and speeds.
- Telescopes: In large astronomical telescopes, facilitating precise movement and alignment of heavy optical components.
- Robotic Arms: Offering the strength and precision required for the movement and operation of industrial robotic systems.
Benefits of Using Oversize Bearings in Industrial Machinery
The incorporation of oversize roller bearings in industrial machinery brings a host of benefits:
- Enhanced Load Capacity: They significantly increase the load-bearing capacity, essential for heavy-duty applications.
- Improved Durability: Designed to withstand harsh conditions, oversize bearings ensure longevity and reliability.
- High Precision: Essential for applications requiring meticulous accuracy, such as in aerospace and robotics.
- Reduced Maintenance: Their robust design and construction minimize the need for frequent maintenance.
- Energy Efficiency: By reducing friction, they contribute to lower energy consumption in machinery operation.
- Versatility: Capable of accommodating radial and axial loads, making them suitable for a wide range of applications.
- Customization: They can be tailored to meet the specific requirements of an application, including size, load capacity, and environmental resistance.
- Safety: Enhances the safety of machinery by providing reliable performance under extreme conditions.
- Cost-Effectiveness: Despite the initial investment, their durability and efficiency lead to cost savings over the machinery’s lifespan.
The advanced applications of loose steel rollers in oversize roller bearings underscore their importance in modern industrial machinery. By offering unparalleled load capacity, durability, and precision, they enable the development and operation of equipment that meets the challenges of today’s demanding industrial environments.
How to Choose the Right Loose Steel Rollers
In the intricate landscape of industrial machinery, the selection of the right loose steel rollers is paramount. This choice not only influences the efficiency and functionality of the equipment but also its longevity and reliability. Understanding the nuanced factors that guide this selection process, as well as the critical importance of material, size, and roller type tailored to specific application needs, is essential for optimizing performance and ensuring operational success.
Factors to Consider When Selecting Loose Steel Rollers
The journey to selecting the ideal loose steel rollers for your machinery involves a comprehensive evaluation of several key factors. Each of these considerations plays a vital role in ensuring that the rollers you choose are perfectly aligned with your operational requirements and application specifics.
- Operational Load Capacity: Assessing the weight and type of load the rollers will bear is crucial. This ensures they can handle the operational stress without compromising performance.
- Environmental Conditions: The working environment’s specifics, such as exposure to corrosive materials, extreme temperatures, or moisture, dictate the material and protective coatings needed.
- Speed Necessities: The operational speed of the machinery influences the choice of rollers, with certain designs better suited to high-speed applications to reduce friction and wear.
- Dimensional Precision: For applications where precision is key, selecting rollers with strict dimensional tolerances is essential to maintain accuracy and efficiency.
- Material and Surface Compatibility: The roller material should be compatible with the surfaces they will contact and the environment they will operate in, to prevent premature wear or failure.
- Size and Installation Fit: Proper sizing is critical for seamless integration into machinery, affecting everything from load distribution to operational smoothness.
- Durability and Lifespan: Opt for materials and designs known for their durability and resistance to wear, ensuring a longer lifespan and reduced maintenance needs.
- Supplier Reliability: Choosing a reputable supplier guarantees that you receive high-quality rollers that meet your specifications and performance expectations.
Importance of Material, Size, and Roller Type Based on Application Needs
Delving deeper into the selection process, the material, size, and type of loose steel rollers must be carefully matched to the application’s unique demands. This alignment is crucial for maximizing the potential of your machinery and ensuring optimal performance.
- Material Properties: The choice of material impacts not just the roller’s durability but also its suitability for specific environments, such as corrosive or high-temperature conditions.
- Sizing Accuracy: Accurate sizing ensures that the rollers fit perfectly within the machinery, promoting efficient operation and preventing issues related to misalignment or excessive wear.
- Roller Type Suitability: Different roller types offer distinct advantages, from needle rollers for high-load, compact spaces to spherical rollers for multidirectional loads, making the selection critical.
- Unique Application Considerations: Specialized applications may have unique requirements, such as non-magnetic rollers for electronic equipment or insulated rollers for electrical applications.
- Maintenance Implications: The ease of maintenance and potential for replacement are influenced by the roller’s design and material, affecting overall operational costs.
- Cost vs. Performance: Evaluating the balance between initial costs and the long-term benefits of reduced maintenance and downtime is essential for cost-effective operations.
- Customization Flexibility: For highly specialized applications, the ability to customize roller materials, sizes, and types can be a deciding factor in achieving the desired performance.
Selecting the right loose steel rollers is a meticulous process that demands a thorough understanding of your machinery’s specific needs and operational conditions. By carefully considering these factors and aligning them with your application’s requirements, you can ensure the longevity, efficiency, and reliability of your industrial equipment.
FAQs about Loose Steel Rollers
Loose needle roller bearings are specialized mechanical components used in a variety of applications where high load capacity and reduced space are critical. Unlike complete needle roller bearings that come with rings or cages, loose needle rollers are simply the rolling elements, offering flexibility in design and application. These tiny, cylindrical rollers are adept at handling high radial loads efficiently, thanks to their large surface area that contacts the raceway.
Their primary use is found in automotive components such as transmissions, engines, and drivetrains, where they contribute to compact and lightweight designs without compromising on strength or load-bearing capacity. Additionally, loose needle rollers are utilized in industrial machinery, including gearboxes, pumps, and compressors, as well as in the aerospace industry for applications requiring precision and durability. The versatility of loose needle rollers makes them suitable for custom bearings, facilitating unique designs for specific application needs, such as in specialized machinery or equipment where standard bearings may not suffice.
When comparing roller bearings to ball bearings in terms of strength, it’s crucial to consider the specific application and the type of load involved. Roller bearings, which encompass cylindrical, tapered, spherical, and needle designs, generally offer a higher radial load capacity compared to ball bearings. This is because roller bearings have a larger contact area with the raceways, allowing them to distribute the load more efficiently and withstand greater forces.
However, “strength” in bearings also pertains to the ability to handle axial loads, where ball bearings often have the advantage, especially angular contact ball bearings designed for such purposes. Roller bearings, particularly cylindrical types, are primarily designed for radial loads and may require additional engineering, such as thrust bearings, to handle significant axial loads effectively.
The choice between roller and ball bearings ultimately depends on the application’s specific load requirements, space constraints, and desired lifespan. Roller bearings might be the preferred choice for heavy radial loads and where space allows, while ball bearings could be more suitable for applications requiring compact solutions and the accommodation of both radial and axial loads.
The comparison between needle bearings and ball bearings hinges on the application’s specific requirements, including load type, space availability, and speed. Needle bearings, a type of roller bearing, are designed with small diameter cylinders that provide a large contact area, making them ideal for high-load applications in limited spaces. They excel in situations where radial space is constrained but a high load capacity is required.
Ball bearings, on the other hand, are versatile components that can handle both radial and axial loads efficiently. They are better suited for applications that demand high-speed operation with minimal friction and wear. Ball bearings are also generally more durable and require less maintenance in high-speed applications compared to needle bearings.
Choosing between needle and ball bearings depends on the operational requirements. Needle bearings are preferable for compact, high-load applications where speed is not the primary concern. Ball bearings are more suited to applications requiring versatility, high speed, and the ability to handle a combination of radial and axial loads.
The term “traditional bearing” typically refers to ball bearings, the most common type of rolling-element bearings. The primary differences between needle bearings and traditional (ball) bearings lie in their design, load capacity, size, and application suitability.
Design: Needle bearings consist of slender and long cylindrical rollers, resembling needles, with a small diameter but a high length-to-diameter ratio. Traditional ball bearings contain spherical rolling elements (balls) between the inner and outer races.
Load Capacity: Needle bearings are designed to support high radial loads due to their larger contact surface area with the races. They generally do not support axial loads unless specifically designed as thrust needle bearings. Ball bearings can handle both radial and axial loads, making them versatile for various applications.
Application Suitability: Needle bearings are best suited for applications with high radial loads and limited space, such as in automotive components. Ball bearings are widely used in applications requiring the accommodation of both radial and axial loads, such as in electric motors and machinery.
Choosing between needle bearings and traditional bearings depends on the application’s specific requirements, including the type of load, space constraints, speed, and maintenance considerations.
Last Updated on May 17, 2024 by Jordan Smith
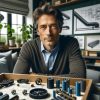
Jordan Smith, a seasoned professional with over 20 years of experience in the conveyor system industry. Jordan’s expertise lies in providing comprehensive solutions for conveyor rollers, belts, and accessories, catering to a wide range of industrial needs. From initial design and configuration to installation and meticulous troubleshooting, Jordan is adept at handling all aspects of conveyor system management. Whether you’re looking to upgrade your production line with efficient conveyor belts, require custom conveyor rollers for specific operations, or need expert advice on selecting the right conveyor accessories for your facility, Jordan is your reliable consultant. For any inquiries or assistance with conveyor system optimization, Jordan is available to share his wealth of knowledge and experience. Feel free to reach out at any time for professional guidance on all matters related to conveyor rollers, belts, and accessories.