Top Benefits of Using a Magnetic Pulley Belt Conveyor
The magnetic pulley belt conveyor is a revolutionary system in material handling and separation processes. This advanced conveyor technology integrates magnetic pulleys into standard belt conveyors, enhancing their capability to separate ferrous materials from non-ferrous materials efficiently. The significance of magnetic pulley belt conveyors lies in their ability to streamline operations, reduce the risk of damage to downstream equipment, and improve overall productivity. By effectively removing unwanted metal contaminants, these conveyors play a crucial role in maintaining product quality and safety across various industries, including recycling, mining, and food processing. The integration of magnetic pulleys into belt conveyors represents a significant advancement in conveying and separation technology.
What are Magnetic Pulley Belt Conveyors
Magnetic Head Pulleys and Their Role in Material Processing
Magnetic pulley belt conveyors are pivotal in modern material handling and separation processes, playing an essential role in a variety of industries. At the core of these systems are magnetic head pulleys, which are strategically placed at the discharge end of the conveyor belt. The primary function of these magnetic pulleys is to attract and separate ferrous materials from non-ferrous materials as they move along the conveyor belt. This separation is crucial in recycling operations, mining, aggregate processing, and other sectors where the purity of the final product is of utmost importance. By removing unwanted ferrous contaminants, magnetic pulley belt conveyors help ensure product quality and protect downstream equipment from potential damage.
The Basic Principles Behind How Magnetic Head Pulleys Work
The operation of magnetic head pulleys in a magnetic pulley belt conveyor system is based on fundamental magnetic principles. As the conveyor belt carries materials to the end of the conveyor, the magnetic pulley attracts ferrous materials due to its magnetic field. Non-ferrous materials, which are not affected by the magnetic field, continue to travel in their trajectory and fall off the end of the belt. In contrast, ferrous materials are held against the belt and carried around the pulley, eventually being discharged separately from the rest of the materials. This simple yet effective process ensures a high degree of separation efficiency, making magnetic pulley belt conveyors an invaluable asset in many industrial applications.
Components and Design Features That Make Magnetic Pulley Belt Conveyors Efficient
- Magnetic Strength and Field Configuration
The efficiency of a magnetic pulley belt conveyor is significantly influenced by the strength and configuration of the magnetic field. High-intensity magnets, often made from rare earth materials like neodymium, ensure robust magnetic attraction and effective separation of even the smallest ferrous particles. The design of the magnetic field, including its depth and reach, is optimized to maximize separation efficiency and ensure that all ferrous materials are captured.
- Durable Construction Materials
Magnetic head pulleys are typically constructed from durable materials such as stainless steel or heavy-duty cast iron. These materials are chosen for their resistance to wear and tear, ensuring the longevity and reliability of the conveyor system. The durability of the construction materials is crucial in environments where the conveyor is subjected to harsh conditions and abrasive materials.
- Adjustable Conveyor Speed
The ability to adjust the speed of the conveyor belt is another key feature that enhances the efficiency of a magnetic pulley belt conveyor. By controlling the belt speed, operators can optimize the separation process based on the type and volume of materials being processed. Slower speeds may be required for materials with a high concentration of ferrous particles, while faster speeds can be used for lighter loads with fewer contaminants.
- Easy Maintenance and Accessibility
Efficient magnetic pulley belt conveyors are designed with ease of maintenance in mind. Features such as accessible pulley housings, easy-to-replace magnetic components, and user-friendly control systems simplify routine maintenance tasks. Regular maintenance ensures that the conveyor operates at peak efficiency and minimizes downtime due to mechanical issues.
- Versatility in Application
Magnetic pulley belt conveyors are highly versatile and can be customized to suit a wide range of applications. This versatility is achieved through various design features, including adjustable magnetic strengths, different pulley sizes, and compatibility with various belt types. Whether used in recycling facilities, food processing plants, or mining operations, these conveyors can be tailored to meet specific industry needs and operational requirements.
Understanding the components and design features of magnetic pulley belt conveyors is essential for optimizing their performance and achieving efficient material separation. From the robust construction materials and powerful magnetic fields to the adjustable conveyor speeds and ease of maintenance, every aspect of these systems is designed to enhance efficiency and reliability. By integrating magnetic pulley belt conveyors into material handling processes, industries can significantly improve the quality and safety of their products, protect their equipment, and reduce operational costs.
Why Use Magnetic Pulley Belt Conveyors?
Efficiency in Separating Ferrous Materials from Non-Ferrous Materials
One of the primary reasons for utilizing a magnetic pulley belt conveyor is its unparalleled efficiency in separating ferrous materials from non-ferrous materials. This efficiency is crucial in industries where the purity of the final product is paramount, such as recycling, food processing, and mining. Magnetic pulley belt conveyors employ powerful magnets to attract ferrous materials, effectively removing them from the material stream. This process ensures that only non-ferrous materials continue along the conveyor, resulting in a cleaner, higher-quality output. For example, in a recycling facility, a magnetic pulley belt conveyor can quickly separate iron and steel from plastic and glass, streamlining the recycling process and increasing the value of the sorted materials.
Protection of Downstream Equipment from Metal Damage
Another significant advantage of using a magnetic pulley belt conveyor is the protection it provides to downstream equipment. Ferrous materials, if not removed, can cause substantial damage to machinery, leading to costly repairs and downtime. By incorporating magnetic pulleys, these conveyors capture and remove potentially damaging ferrous debris before it reaches sensitive equipment. For instance, in a mining operation, rocks and ores may contain metal fragments that could damage crushers, screens, and other processing equipment. A magnetic pulley belt conveyor ensures these ferrous contaminants are removed, thereby extending the lifespan of the machinery and reducing maintenance costs.
Reduction in Operational Costs Through Maintenance and Energy Savings
Magnetic pulley belt conveyors also contribute to significant reductions in operational costs through maintenance and energy savings. By efficiently removing ferrous materials, these conveyors minimize wear and tear on equipment, leading to lower maintenance requirements and costs. Additionally, the separation process is passive, requiring no additional energy consumption beyond that of the conveyor operation itself. This results in energy savings compared to more complex separation systems. For example, a manufacturing plant that processes large volumes of raw materials can benefit from reduced maintenance costs and lower energy bills by using magnetic pulley belt conveyors to handle and sort materials efficiently.
Five Examples of Operational Cost Reductions
- Reduced Maintenance Frequency
Magnetic pulley belt conveyors help reduce the frequency of maintenance by preventing ferrous materials from causing damage to conveyor belts and other machinery. This reduction in maintenance needs leads to lower labor costs and less downtime. For instance, a food processing plant using a magnetic pulley belt conveyor can reduce the frequency of belt replacements and machinery repairs, resulting in substantial cost savings over time.
- Extended Equipment Lifespan
By protecting downstream equipment from metal damage, magnetic pulley belt conveyors contribute to the extended lifespan of machinery. This longevity reduces the need for expensive replacements and upgrades. In a mining operation, the use of magnetic pulley belt conveyors can extend the operational life of crushers and screens, translating into long-term savings on equipment investments.
- Lower Energy Consumption
The passive nature of magnetic separation in pulley belt conveyors means that no additional energy is required to operate the magnetic pulleys. This leads to lower overall energy consumption compared to other separation methods, such as eddy current separators, which require additional power. A recycling facility can benefit from lower energy bills by utilizing magnetic pulley belt conveyors for material sorting.
- Minimized Production Downtime
Efficient removal of ferrous materials reduces the likelihood of equipment breakdowns, leading to minimized production downtime. Consistent operation without unexpected stoppages ensures that production schedules are maintained, and productivity is maximized. For example, a manufacturing plant that experiences fewer equipment failures due to the use of magnetic pulley belt conveyors can maintain steady production levels and avoid costly interruptions.
- Improved Product Quality
Magnetic pulley belt conveyors improve the quality of the final product by ensuring that ferrous contaminants are removed from the material stream. Higher product quality can lead to increased customer satisfaction and reduced returns or rejections. In the food processing industry, for instance, the use of magnetic pulley belt conveyors ensures that metal-free food products reach consumers, enhancing brand reputation and reducing the risk of costly recalls.
The use of magnetic pulley belt conveyors offers numerous benefits, including efficient separation of ferrous materials from non-ferrous materials, protection of downstream equipment from metal damage, and significant reductions in operational costs through maintenance and energy savings. By incorporating these advanced conveyor systems, industries can enhance productivity, ensure product quality, and achieve long-term cost savings. The examples provided illustrate how magnetic pulley belt conveyors can be a valuable asset in various industrial applications, making them a smart investment for any material handling and processing operation.
Finding the Best Magnetic Pulley Belt Conveyor for Sale
Selecting the right magnetic pulley belt conveyor for your needs is a critical decision that can impact your operational efficiency and product quality. When looking for the best magnetic pulley belt conveyor for sale, it’s essential to consider several key criteria to ensure you make an informed choice.
Criteria for Choosing the Best Magnetic Pulley Belt Conveyor
- Magnetic Strength
The strength of the magnetic field is a crucial factor in the performance of a magnetic pulley belt conveyor. Stronger magnets will provide more effective separation of ferrous materials from non-ferrous materials. It’s essential to choose a conveyor with magnets that match the requirements of your specific application, whether it involves small ferrous particles or larger metal contaminants.
- Belt Width and Speed
The width of the conveyor belt and the speed at which it operates are also important considerations. The belt width should be appropriate for the volume and type of material being processed. Additionally, the speed of the belt should be adjustable to optimize the separation process for different materials and operating conditions.
- Durability and Construction Materials
The construction materials of the conveyor, particularly the magnetic pulley, should be durable and resistant to wear and tear. Stainless steel and heavy-duty cast iron are commonly used materials that ensure longevity and reliability, even in harsh industrial environments.
- Ease of Maintenance
Maintenance requirements can significantly impact the long-term cost and efficiency of a conveyor system. Look for designs that offer easy access to the magnetic pulleys and other components for routine maintenance and repairs. Features such as quick-release mechanisms and modular components can simplify maintenance tasks.
- Customization Options
Every application has unique requirements, so the ability to customize the conveyor system is essential. Options for customization might include different magnetic strengths, pulley sizes, and belt types, allowing you to tailor the system to your specific needs.
Magnetic Pulley Belt Conveyor Price
The cost of a magnetic pulley belt conveyor can vary widely depending on several factors. Understanding these factors can help you budget effectively and ensure you get the best value for your investment.
Factors Influencing the Cost
- Magnetic Strength and Type
Stronger magnets and those made from rare earth materials like neodymium are more expensive but offer superior performance. The type of magnet used can significantly impact the overall cost of the conveyor system.
- Size and Capacity
Larger conveyors with wider belts and higher capacity are generally more expensive. The size and capacity you need will depend on the volume of material you plan to process and the space available in your facility.
- Customization and Features
Custom features such as adjustable belt speeds, specific pulley sizes, and additional automation can increase the cost of the conveyor. However, these features can also enhance the system’s efficiency and productivity, providing a good return on investment.
- Brand and Manufacturer
Reputable manufacturers with a history of quality and reliability may charge a premium for their products. Investing in a well-known brand can provide peace of mind and potentially lower maintenance and repair costs over time.
- Installation and Maintenance Costs
The cost of installation and ongoing maintenance should also be factored into your budget. Some conveyors may require professional installation, while others are designed for easier, do-it-yourself setup.
Magnetic Pulley Belt Conveyor Manufacturers
Choosing the right manufacturer is just as important as selecting the right conveyor. Here are five reputable manufacturers and what sets them apart.
- Eriez
Eriez is known for its high-quality magnetic separation equipment. Their magnetic pulley belt conveyors are renowned for their durability and efficiency. Eriez offers a wide range of customizable options, ensuring their conveyors meet specific industry needs.
- Dings Company Magnetic Group
Dings Company has a long history of manufacturing reliable and robust magnetic pulleys. Their products are designed for heavy-duty applications and are known for their excellent performance and long service life.
- Bunting Magnetics
Bunting Magnetics offers innovative magnetic pulley belt conveyors with advanced features like high-intensity magnets and user-friendly maintenance options. Their products are used in various industries, including recycling, mining, and food processing.
- Walker Magnetics
Walker Magnetics specializes in high-performance magnetic separation solutions. Their magnetic pulley belt conveyors are designed for efficient material handling and separation, with a focus on reducing operational costs and improving product quality.
- IMI (Industrial Magnetics, Inc.)
IMI provides a range of magnetic pulley belt conveyors that are highly customizable to meet specific customer requirements. They are known for their robust construction and reliable performance, making them a popular choice in multiple industries.
Selecting and purchasing the right magnetic pulley belt conveyor involves careful consideration of various factors, including magnetic strength, belt width, durability, maintenance requirements, and customization options. Understanding the factors that influence cost and choosing a reputable manufacturer are also crucial steps in making an informed decision. By taking these elements into account, you can find a magnetic pulley belt conveyor that meets your operational needs and provides long-term value.
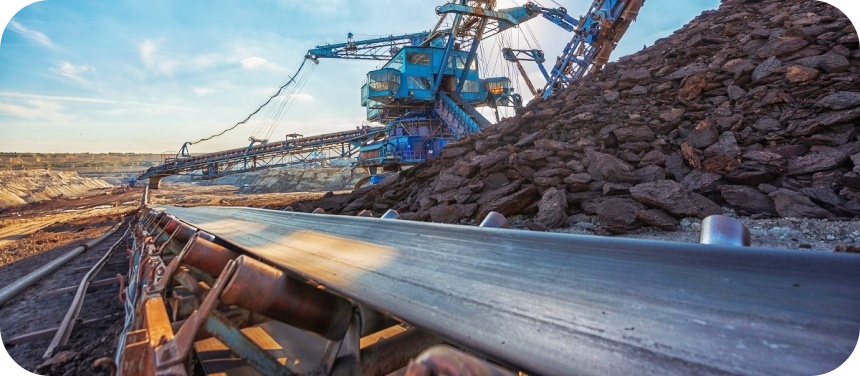
Integration into Existing Systems About Magnetic Pulley Belt Conveyors
Integrating Magnetic Pulley Belt Conveyors into Existing Conveyor Setups
Integrating a magnetic pulley belt conveyor into an existing conveyor system can significantly enhance material handling efficiency and separation processes. However, successful integration requires careful planning and consideration of several key factors to ensure seamless operation and maximum benefits.
Assessment of Current System
Before integrating a magnetic pulley belt conveyor, it’s crucial to thoroughly assess the current conveyor system. Identify the areas where the magnetic pulley will be most effective, such as the discharge end where material separation is most critical. Evaluate the existing conveyor’s dimensions, speed, and load capacity to ensure compatibility with the new magnetic pulley belt conveyor. For example, if your current system handles a high volume of mixed materials, placing the magnetic pulley at the end of the conveyor line can efficiently separate ferrous contaminants before final processing.
Compatibility with Existing Equipment
Ensure that the magnetic pulley belt conveyor is compatible with the existing equipment. This includes matching the belt width and speed with the current conveyor system. For instance, if your current conveyor operates at a high speed, selecting a magnetic pulley with adjustable speed settings will help maintain synchronization and optimal performance. Additionally, verify that the magnetic strength of the pulley aligns with the material types processed in your facility.
Modifications and Enhancements
In some cases, integrating a magnetic pulley belt conveyor may require modifications to the existing setup. This could involve adjusting the conveyor frame, adding support structures, or upgrading control systems. For example, in a recycling plant, adding a magnetic pulley may necessitate reinforcing the conveyor frame to handle the additional weight and ensuring that the control system can manage the new component.
Testing and Calibration
Once the magnetic pulley belt conveyor is installed, conduct thorough testing and calibration to ensure it operates correctly. This includes adjusting the magnetic field strength, belt speed, and pulley position to achieve optimal separation efficiency. Testing should be done with various material types to fine-tune the system for consistent performance. For instance, a mining operation might test the conveyor with different ore grades to ensure effective separation of ferrous and non-ferrous materials.
Training and Documentation
Provide comprehensive training for operators and maintenance personnel on the new system. This includes understanding how the magnetic pulley belt conveyor works, how to adjust settings, and how to perform routine maintenance. Proper training ensures that the system is used effectively and reduces the risk of operational issues. Additionally, maintain detailed documentation of the integration process, including installation procedures, calibration settings, and maintenance schedules.
Considerations for Installation and Ensuring Optimal Operation
1. Structural Integrity
Ensure that the conveyor structure is robust enough to support the additional weight and stress of the magnetic pulley. This may involve reinforcing existing support structures or installing additional supports. For example, in a heavy-duty industrial setting, reinforcing the conveyor frame can prevent structural failures and maintain operational stability.
2. Power Supply and Electrical Integration
The magnetic pulley belt conveyor requires a reliable power supply. Ensure that the electrical system can support the additional load and that all connections are secure and compliant with safety standards. For instance, upgrading the power supply to accommodate the magnetic pulley’s energy requirements ensures consistent operation and prevents electrical issues.
3. Safety Measures
Implement safety measures to protect workers and equipment. This includes installing safety guards, emergency stop buttons, and ensuring that the magnetic field does not interfere with other equipment. For example, placing safety guards around the magnetic pulley prevents accidental contact and ensures a safe working environment.
4. Regular Maintenance and Inspections
Regular maintenance is critical for the optimal operation of the magnetic pulley belt conveyor. Schedule routine inspections to check for wear and tear, adjust settings, and replace worn components. For example, in a food processing plant, regular inspections ensure that the magnetic pulley remains clean and free of contaminants, maintaining food safety standards.
5. Monitoring and Adjustments
Continuously monitor the performance of the magnetic pulley belt conveyor and make adjustments as needed. Use sensors and control systems to track the efficiency of material separation and conveyor operation. For instance, in a recycling facility, monitoring systems can detect variations in material flow and automatically adjust the magnetic field strength for optimal separation.
Integrating a magnetic pulley belt conveyor into existing systems requires careful planning, assessment, and modifications to ensure compatibility and optimal performance. By considering factors such as structural integrity, power supply, safety measures, and regular maintenance, industries can enhance their material handling processes and achieve efficient separation of ferrous materials. Proper training and documentation further ensure that the system is used effectively, maximizing its benefits and operational longevity. Through these steps, the integration of a magnetic pulley belt conveyor can lead to significant improvements in productivity, product quality, and cost savings.
Applications of Magnetic Pulley Belt Conveyors
Detailed Examples and Case Studies from Industries Benefiting from Magnetic Pulley Systems
Magnetic pulley belt conveyors play a crucial role in various industries by enhancing material handling and separation processes. These conveyors are designed to efficiently remove ferrous contaminants from material streams, ensuring product quality and protecting downstream equipment. Here are detailed examples and case studies from different industries that benefit from the use of magnetic pulley belt conveyors.
Recycling Industry
In the recycling industry, the separation of ferrous materials from mixed waste streams is essential for efficient processing and high-quality output. A prominent recycling facility implemented a magnetic pulley belt conveyor to enhance the separation process. Before installation, the facility faced challenges with ferrous contaminants in their plastic and glass recyclables, leading to equipment damage and product degradation.
After integrating the magnetic pulley belt conveyor, the facility experienced significant improvements. The magnetic pulley effectively removed steel and iron from the waste stream, resulting in cleaner recyclables. This not only improved the quality of the final product but also reduced wear and tear on other machinery, cutting maintenance costs and downtime.
Mining Industry
Mining operations often involve processing large volumes of ore containing both ferrous and non-ferrous materials. A mining company operating in South America incorporated magnetic pulley belt conveyors to improve their material separation efficiency. The primary goal was to protect crushers and screens from damage caused by ferrous debris.
The implementation of high-intensity magnetic pulley belt conveyors at the discharge points of their primary crushers resulted in the effective removal of ferrous contaminants. This not only protected the downstream equipment from damage but also increased the overall efficiency of the processing plant. The reduction in equipment downtime and maintenance costs led to substantial operational savings.
Food Processing Industry
In the food processing industry, ensuring that food products are free from metal contaminants is critical for safety and regulatory compliance. A food processing plant in Europe integrated magnetic pulley belt conveyors into their production line to address contamination concerns. The plant processed bulk grains, which often contained small ferrous particles from harvesting and transportation equipment.
By installing magnetic pulley belt conveyors, the plant was able to efficiently remove these metal contaminants. The high-intensity magnetic pulleys ensured that even the smallest ferrous particles were captured and separated. This resulted in higher product purity, compliance with food safety standards, and enhanced consumer safety. The plant also reported fewer product recalls and customer complaints, boosting their brand reputation.
Aggregate Industry
The aggregate industry requires robust solutions for separating ferrous materials from crushed stone and gravel. A large construction aggregate producer in North America faced issues with metal contamination in their products, which damaged machinery and compromised product quality. They adopted magnetic pulley belt conveyors to tackle this problem.
The installation of these conveyors led to effective separation of ferrous materials from the aggregate. The result was a cleaner, higher-quality product that met industry standards. Additionally, the reduction in metal contaminants extended the lifespan of crushers and screens, lowering maintenance costs and increasing production efficiency.
Waste Management
Waste management facilities benefit significantly from magnetic pulley belt conveyors for sorting ferrous materials from municipal solid waste. A waste management company in Asia incorporated these conveyors into their sorting lines to improve the efficiency of their recycling processes.
The magnetic pulley belt conveyors enabled the facility to effectively separate iron and steel from other waste materials. This improved the purity of recyclable materials and reduced the volume of non-recyclable waste. The facility reported a notable increase in recycling rates and a reduction in landfill costs. Additionally, the improved separation process enhanced the safety and efficiency of the waste sorting operations.
Insights into Real-World Applications and Outcomes
The real-world applications of magnetic pulley belt conveyors demonstrate their versatility and effectiveness across various industries. These conveyors provide reliable solutions for material separation, ensuring product quality, protecting equipment, and reducing operational costs.
In recycling facilities, magnetic pulley belt conveyors enhance the purity of recyclables, reduce machinery wear, and lower maintenance costs. Mining operations benefit from reduced equipment damage and increased processing efficiency. In the food processing industry, these conveyors ensure product safety and regulatory compliance, leading to higher consumer trust and fewer recalls. The aggregate industry sees improved product quality and extended machinery lifespan, while waste management facilities achieve higher recycling rates and lower landfill costs.
The outcomes from these applications highlight the value of magnetic pulley belt conveyors in improving operational efficiency, ensuring product integrity, and achieving cost savings. By effectively separating ferrous materials from non-ferrous materials, these conveyors play a crucial role in various industrial processes, making them an indispensable tool for modern material handling and separation needs.
Maintenance, Care, and Lifespan of Magnetic Pulley Belt Conveyors
Routine Maintenance Recommendations to Ensure Longevity
Proper maintenance is crucial for ensuring the longevity and optimal performance of a magnetic pulley belt conveyor. Regular upkeep not only extends the lifespan of the equipment but also enhances its efficiency and reliability. Here are key routine maintenance recommendations to keep your magnetic pulley belt conveyor in top condition:
- Regular Inspection
Conduct regular inspections of the conveyor system to identify any signs of wear, damage, or misalignment. Check the magnetic pulley for any build-up of ferrous materials, as this can reduce its effectiveness. Inspect the belt for signs of wear and tear, such as fraying or cracking. Regular inspections help in early detection of potential issues, allowing for timely repairs and maintenance.
- Cleaning and Lubrication
Keep the conveyor system clean to prevent the accumulation of dust, debris, and ferrous particles. Clean the magnetic pulley regularly to maintain its magnetic strength and separation efficiency. Lubricate the moving parts of the conveyor, such as bearings and rollers, to reduce friction and wear. Proper lubrication ensures smooth operation and prevents overheating.
- Belt Tension and Alignment
Ensure that the conveyor belt is properly tensioned and aligned. Incorrect belt tension can lead to slippage, reduced efficiency, and increased wear. Use tensioning devices and alignment tools to maintain the correct belt position and tension. Regularly check and adjust the belt tension and alignment to prevent premature wear and improve performance.
- Magnetic Field Strength
Periodically check the magnetic field strength of the pulley to ensure it remains effective in separating ferrous materials. Over time, magnets can lose their strength due to various factors, including exposure to extreme temperatures and mechanical stress. Use a gauss meter to measure the magnetic field strength and replace the magnetic pulley if necessary.
- Component Replacement
Regularly replace worn or damaged components, such as belts, bearings, and rollers. Keeping spare parts on hand can minimize downtime and ensure quick repairs. Follow the manufacturer’s recommendations for component replacement intervals to maintain optimal conveyor performance.
Durability Considerations and How to Maximize the Life of Your Conveyor
The durability of a magnetic pulley belt conveyor depends on several factors, including the quality of materials used, the operating environment, and the maintenance practices employed. Here are some considerations and strategies to maximize the life of your conveyor:
- Quality Materials
Investing in high-quality materials for the construction of the conveyor system can significantly enhance its durability. Magnetic pulleys made from robust materials like stainless steel or heavy-duty cast iron can withstand harsh operating conditions and resist wear and corrosion. Additionally, using high-strength magnets, such as neodymium, ensures long-lasting magnetic performance.
- Protective Coatings and Treatments
Applying protective coatings and treatments to the conveyor components can enhance their resistance to corrosion, abrasion, and chemical damage. For example, in industries where the conveyor is exposed to corrosive substances, using corrosion-resistant coatings on the pulley and belt can prolong their lifespan. Similarly, abrasion-resistant coatings can protect the belt from wear caused by abrasive materials.
- Environmental Control
Controlling the operating environment can significantly impact the durability of the conveyor system. Minimize exposure to extreme temperatures, humidity, and corrosive substances. In environments with high levels of dust or debris, consider installing dust collection systems to keep the conveyor clean and reduce wear.
- Load Management
Avoid overloading the conveyor system, as excessive weight can cause undue stress on the belt, pulleys, and other components. Ensure that the load capacity of the conveyor matches the requirements of your operation. Implement load management practices, such as distributing the load evenly across the belt and avoiding sudden surges in material flow.
- Operator Training
Proper training for operators and maintenance personnel is essential for the longevity of the conveyor system. Train staff on the correct operating procedures, maintenance practices, and safety protocols. Well-trained personnel can identify potential issues early, perform routine maintenance effectively, and operate the conveyor within its design parameters.
Routine maintenance, careful attention to durability considerations, and strategic practices can significantly extend the life and enhance the performance of a magnetic pulley belt conveyor. Regular inspections, cleaning, lubrication, and component replacement are essential maintenance tasks that ensure the system operates efficiently and reliably. Investing in quality materials, applying protective coatings, controlling the operating environment, managing loads, and providing proper training are key strategies for maximizing the durability of the conveyor. By following these recommendations, industries can achieve long-term cost savings, reduce downtime, and maintain high standards of material handling and separation efficiency with their magnetic pulley belt conveyors.
Learn more about our high-performance conveyor belt options.
FAQs About Magnetic Pulley Belt Conveyors
A magnetic pulley works by utilizing a magnetic field to attract and separate ferrous materials from a material stream. The magnetic pulley is installed at the discharge end of a conveyor belt. As the material on the belt reaches the magnetic pulley, ferrous materials are attracted to the magnetic field and are held against the belt. As the belt continues around the pulley, the ferrous materials are carried away from the rest of the material and discharged separately. Non-ferrous materials, which are not affected by the magnetic field, continue to move along the conveyor belt and fall off at the end. This separation process is highly effective for removing unwanted metal contaminants from a material stream, ensuring cleaner and higher-quality output.
A magnetic belt conveyor works by integrating magnetic pulleys or magnetic plates into a standard conveyor belt system to separate ferrous materials from non-ferrous materials. The magnetic elements, either as pulleys at the conveyor’s ends or as plates beneath the belt, generate a magnetic field that attracts ferrous metals. As the material moves along the conveyor belt, the magnetic field captures ferrous particles, holding them against the belt. At the discharge point, the magnetic pulley retains the ferrous materials while the non-ferrous materials are discharged normally. The ferrous materials are then carried further along the belt and released into a separate collection area. This process effectively removes metal contaminants from the material stream, enhancing product purity and protecting downstream equipment from damage.
Belt conveyors utilize various types of pulleys to achieve different functions and optimize the conveyor system’s performance. The main types of pulleys include:
Head Pulley: Located at the discharge end of the conveyor, the head pulley drives the conveyor belt. It is powered by a motor and ensures the movement of the belt and the materials on it.
Tail Pulley: Positioned at the opposite end of the conveyor, the tail pulley is responsible for redirecting the belt back towards the head pulley. It helps maintain tension and alignment.
Snub Pulley: Positioned near the head or tail pulley, snub pulleys increase the belt’s contact angle with the drive pulley, enhancing traction and reducing belt slippage.
Take-Up Pulley: This pulley is used to maintain proper belt tension by adjusting its position to accommodate belt stretch and wear. It can be manual or automatic.
Bend Pulley: Installed along the conveyor, bend pulleys change the direction of the belt, helping it navigate the conveyor system layout.
Each pulley type plays a specific role in ensuring the smooth operation and efficiency of the belt conveyor system.
A magnetic drum pulley is a type of magnetic separator that is installed at the discharge end of a conveyor belt to remove ferrous materials from a material stream. It consists of a drum shell that rotates around a fixed magnetic core. As the conveyor belt carries materials over the magnetic drum, the magnetic field attracts and captures ferrous particles, holding them against the drum’s surface. Non-ferrous materials continue to move along the belt and fall off at the end. The captured ferrous materials are carried around the drum and released into a separate collection area once they move out of the magnetic field’s influence. Magnetic drum pulleys are widely used in recycling, mining, and aggregate processing industries to enhance material purity, protect downstream equipment, and improve overall processing efficiency. They offer a continuous and automatic solution for separating ferrous contaminants from bulk materials.
Last Updated on July 16, 2024 by Jordan Smith
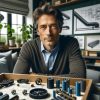
Jordan Smith, a seasoned professional with over 20 years of experience in the conveyor system industry. Jordan’s expertise lies in providing comprehensive solutions for conveyor rollers, belts, and accessories, catering to a wide range of industrial needs. From initial design and configuration to installation and meticulous troubleshooting, Jordan is adept at handling all aspects of conveyor system management. Whether you’re looking to upgrade your production line with efficient conveyor belts, require custom conveyor rollers for specific operations, or need expert advice on selecting the right conveyor accessories for your facility, Jordan is your reliable consultant. For any inquiries or assistance with conveyor system optimization, Jordan is available to share his wealth of knowledge and experience. Feel free to reach out at any time for professional guidance on all matters related to conveyor rollers, belts, and accessories.