Manual Steel Roller: The Metalworker’s Versatile Tool
In the realm of metalworking, the significance of tools cannot be overstated, especially when it comes to shaping and bending metal to precise specifications. Among these essential tools, the manual steel roller stands out for its versatility and fundamental role in the workshop. Serving as the backbone for a variety of bending tasks, manual steel rollers, including manual roll benders, ring rollers, and flat bar roller machines, offer a hands-on approach to metal forming. This traditional method allows artisans and fabricators to manipulate metal with precision, without the need for expensive, high-powered machinery. The focus on manual steel rollers in this guide underscores their importance in crafting everything from intricate art pieces to functional metal components, highlighting their indispensable role in both hobbyist and professional settings.
What Is Manual Steel Roller
A manual steel roller stands as a cornerstone in the toolkit of metalworkers and fabricators, offering a hands-on approach to bending and shaping metal. This tool’s essence lies in its simplicity and the direct control it offers, making it invaluable for a wide range of applications. Let’s explore the definition, functionality, various types, and the key features that make manual steel rollers indispensable in metalworking.
Definition and Functionality of Manual Steel Rollers
Manual steel rollers are fundamental tools designed for the manual bending and shaping of metal. These devices leverage mechanical advantage and human force to alter the form of metal materials. Here are several points highlighting their definition and functionality:
- Manual Operation: They operate without the need for electricity or hydraulic systems, relying instead on human effort to produce bends.
- Versatility: These rollers can handle a variety of metals, allowing for the creation of complex shapes including curves and angles.
- Precision: Skilled operators can achieve precise bends, making these tools suitable for detailed metalwork.
- Affordability: Their manual nature makes them more affordable than automated systems, ideal for small-scale operations.
- Portability: Being manually operated, these tools are often more compact and easier to move than their powered counterparts.
- Ease of Use: Designed with simplicity in mind, they can be used effectively by both novices and experienced metalworkers.
Types of Manual Steel Rollers
Exploring the types of manual steel rollers reveals the diversity of these tools, each tailored for specific bending tasks. From creating tight rings to bending large flat bars, the variety available ensures there’s a tool for every project.
- Roll Benders: Primarily used for creating smooth curves and circles in metal sheets and tubes.
- Ring Rollers: Specialize in forming metal into rings or circular shapes, perfect for ornamental work.
- Heavy-Duty Ring Rollers: Built for tougher materials and larger projects, these can handle more substantial bending tasks.
- Flat Bar Roller Machines: Focus on bending flat surfaces into curved shapes, essential for structural and decorative work.
- Section Rollers: Designed to bend various profiles, including angles, T-bars, and channels, offering versatility in metal shaping.
- Benchtop Models: Compact versions that are ideal for smaller workshops or hobbyists who require space efficiency.
- Floor Models: Larger, stand-alone units that provide greater capacity and leverage for heavy-duty bending operations.
- Specialized Rollers: Some models are designed for specific applications, such as creating scrollwork or bending wire.
Key Features and Design Elements of Manual Steel Rollers
The design and features of manual steel rollers are pivotal to their functionality and effectiveness in metalworking. These aspects determine the tool’s versatility, durability, and ease of use.
- High Carbon Steel Rolls: The heart of these tools, crafted for resilience and precision in bending operations.
- Adjustable Settings: Allow for the accommodation of various metal thicknesses and widths, enhancing the tool’s flexibility.
- Wire Grooves: Integrated grooves for bending wire and rod materials, expanding the tool’s application range.
- Gear Reduction Mechanism: Eases the bending process, especially for thicker materials, by multiplying the force applied.
- Portability and Compact Design: Essential for workshops where space is at a premium, these features make the tools easy to store and move.
- Durability: Constructed to endure the demands of metalworking, ensuring a long service life with minimal maintenance.
- Ease of Maintenance: Simpler mechanical design means easier upkeep and fewer breakdowns.
- Customization: The ability to add or modify dies and accessories, tailoring the tool to specific projects or materials.
- Safety Features: Includes aspects like protective guards and locking mechanisms to ensure operator safety during use.
- Ergonomic Design: Considerations for user comfort and efficiency, particularly in models used for extended periods.
The manual steel roller embodies the blend of traditional craftsmanship and modern engineering, providing a versatile and reliable solution for metal forming tasks. Whether for professional fabrication or hobbyist projects, understanding these tools’ types and features is crucial for selecting the right manual steel roller for your needs.
Advantages of Manual Steel Roller
The manual steel roller, a staple in the metalworking industry, offers a plethora of benefits that make it a preferred choice for many professionals and hobbyists alike. Its simplicity in design and operation belies the vast array of advantages it brings to the workshop. Here, we delve into the significant benefits that underscore the value of incorporating a manual steel roller into your metalworking arsenal.
- Cost-Effectiveness: One of the most compelling advantages of a manual steel roller is its affordability. Compared to their automatic counterparts, these machines are significantly less expensive, making them accessible to a wider range of users, from small workshops to hobbyists looking to expand their toolset without breaking the bank.
- Portability: The inherent design of manual steel rollers makes them lightweight and compact, allowing for easy relocation within the workshop or to different job sites. This portability is particularly beneficial for contractors or those who need to perform work in various locations.
- Ease of Use: With straightforward operation mechanisms, manual steel rollers are user-friendly, making them an excellent tool for beginners. The learning curve is minimal, allowing new users to quickly become proficient in bending and shaping metal.
- Versatility in Metalworking: Capable of handling a wide range of metals, including aluminum, copper, and stainless steel, manual steel rollers are incredibly versatile. This versatility enables users to work on diverse projects, from automotive parts to artistic metalwork, without the need for multiple specialized machines.
- Low Maintenance: Due to their mechanical nature and lack of electrical components, manual steel rollers require minimal maintenance. This reliability ensures that they are always ready for use, reducing downtime and increasing productivity.
- Precision and Control: Despite being manually operated, these rollers can achieve a high degree of precision. The direct control over the bending process allows for adjustments to be made on the fly, ensuring that the final product meets exact specifications.
- Energy Efficiency: Operating without the need for electricity, manual steel rollers are energy efficient. This not only reduces operational costs but also makes them an environmentally friendly option for metalworking.
- Durability: Built to last, manual steel rollers are typically constructed from high-quality materials designed to withstand the rigors of metal bending. This durability ensures that the machine can serve your metalworking needs for years to come, providing a high return on investment.
The manual steel roller offers a unique combination of cost-effectiveness, portability, ease of use, and versatility, making it an invaluable tool in the metalworking industry. Whether you’re a seasoned professional or just starting out, the benefits of incorporating a manual steel roller into your workshop are clear, providing the capability to bend and shape metal with precision and efficiency.
Manual Steel Roller Options
The manual steel roller, a fundamental tool in metalworking, offers a variety of configurations to cater to diverse project requirements. Each type is designed with specific tasks in mind, enhancing the precision, efficiency, and quality of metal forming. Let’s explore the detailed aspects of each option, highlighting their unique advantages and features.
Manual Roll Bender
At the core of metal fabrication, the manual roll bender stands out for its versatility and precision. It’s an indispensable tool for creating smooth bends in pipes, tubes, and rods, suitable for a wide array of projects.
- Versatility: Handles various materials, including steel, aluminum, and copper.
- Precision: Enables accurate bending, essential for projects with tight tolerances.
- Adjustability: Accommodates different sizes and thicknesses through adjustable settings.
- Ease of Use: Simple operation, accessible to all skill levels.
- Portability: Compact and lightweight, enhancing workshop mobility.
- Cost-Effectiveness: An economical option for small-scale operations.
- Durability: Built to last, ensuring long-term use and reliability.
Manual Ring Roller
The manual ring roller specializes in creating perfect rings and arcs, a favorite for ornamental metalwork. Its design focuses on detail and precision, making it a valuable asset for decorative projects.
- Specialization: Produces uniform rings and curved segments.
- Detail-Oriented: Ideal for intricate and decorative metalworking.
- Compact Design: Fits easily in any workshop space.
- Material Compatibility: Versatile across metal types and sizes.
- Customization: Adjustable for rings of various diameters.
- User Control: Manual operation for precise bending adjustments.
- Efficiency: Optimizes the production of circular metal components.
Heavy Duty Ring Roller
For projects requiring more robust materials, the heavy-duty ring roller provides the necessary power and durability. It’s engineered for industrial applications, where material thickness and strength are paramount.
- Enhanced Capacity: Handles thicker, stronger materials with ease.
- Robust Construction: Designed for heavy-duty tasks and longevity.
- Greater Force: Leverages additional power for industrial-grade metals.
- Versatility in Applications: Suitable for a range of heavy construction and manufacturing projects.
- Precision Engineering: Maintains accuracy with tough materials.
- Longevity: Resists wear from rigorous, continuous use.
- Investment Value: Delivers professional-grade performance, justifying its cost.
Manual Flat Bar Roller Machine
The manual flat bar roller machine excels in bending flat bars into precise shapes and angles, crucial for both structural and decorative metalwork. Its specific design ensures accuracy and creativity in flat bar projects.
- Specialization in Flat Bars: Tailored for precise bending operations.
- Adjustable Roller Distance: Accommodates various bar widths and thicknesses.
- Creative Flexibility: Facilitates the creation of complex designs.
- Manual Control: Allows for real-time bending adjustments.
- Sturdy Design: Provides consistent and reliable performance.
- Practicality: Essential for architectural and functional art projects.
- Space Efficiency: Compact size for easy storage.
Section Bender
The section bender is a versatile tool capable of manipulating different metal profiles, making it indispensable for creating structural components and custom fittings. Its ability to handle angles, channels, and T-bars expands the possibilities in metal fabrication.
- Multi-Profile Compatibility: Bends a variety of metal sections.
- Precision Bending: Ensures accurate angles and curves for structural integrity.
- Versatile Applications: Ideal for frames, supports, and bespoke fittings.
- Manual Operation: Offers hands-on control for custom requirements.
- Durable Construction: Engineered for multi-profile bending without damage.
- Adaptability: Features adjustable settings for diverse bending tasks.
- Efficiency: Enhances the metal section shaping process for projects.
Understanding the capabilities and applications of each manual steel roller option allows metalworkers to select the most appropriate tool for their specific needs, ensuring high-quality results and efficient project completion.
To Select the Right Manual Steel Roller
Selecting the ideal manual steel roller for your metalworking projects is a critical decision that impacts the quality, efficiency, and scope of your work. The right choice ensures that your projects are executed with precision and ease, while the wrong choice could limit your capabilities or result in subpar outcomes. To navigate this decision, it’s essential to consider a variety of factors that influence the performance and suitability of a manual steel roller for your specific needs. Additionally, understanding the distinctions between popular models and their intended applications can significantly aid in making an informed selection.
Factors to Consider
Before committing to a manual steel roller, it’s important to evaluate several key aspects of your metalworking practice and project requirements:
- Material Thickness: The thickness of the metal you intend to bend is paramount. Different rollers are engineered to handle specific ranges of material thickness.
- Width Capacity: The width of your materials also plays a crucial role. Ensure the chosen roller can accommodate the breadth of metal sheets or bars you frequently use.
- Bending Requirements: Different projects require different types of bends. Assess whether the roller can perform the specific bends needed for your work, such as radius bends, sharp angles, or complex curves.
- Material Type: The metal type affects the choice of roller, as different materials (aluminum, steel, copper) have varying degrees of hardness and flexibility.
- Project Complexity: The complexity of your projects may necessitate a roller with advanced features and greater versatility.
- Space Constraints: Consider the physical size of the roller and whether it will fit within your workspace without disrupting other operations.
- Budget: Manual steel rollers vary in price. Define your budget early on and seek the best option within your financial limits, balancing cost with the need for quality and durability.
- Durability and Quality: Opting for a roller constructed from high-quality materials ensures longevity and consistent performance, a crucial factor for long-term use.
Comparison of Popular Models and Their Applications
Understanding the landscape of available manual steel rollers and their specific strengths is key to choosing the right tool:
- Basic Manual Roll Benders: These are excellent for beginners and small-scale projects, offering simplicity and ease of use for light to medium gauge metals.
- Heavy-Duty Manual Ring Rollers: Designed for industrial strength and durability, these models are ideal for working with thicker materials in demanding environments.
- Manual Flat Bar Roller Machines: Specialized for precision bending of flat bars, these machines are indispensable for architectural and decorative metalwork.
- Section Benders: Offering the ability to bend various metal profiles, section benders are versatile tools for structural metalworking projects.
- Compact Benchtop Models: Perfect for workshops with limited space, these models provide precision bending capabilities without occupying much room.
- High-Capacity Floor Models: For larger projects requiring more power and capacity, these floor models offer the necessary leverage and versatility.
- Specialized Models for Artistic Work: Tailored for ornamental metalworking, these rollers allow for delicate bending and shaping, perfect for artistic creations.
By carefully assessing these factors and comparing the functionalities of various manual steel roller models, you can select a tool that not only meets the current demands of your projects but also accommodates future growth and diversification of your metalworking practice. The goal is to choose a manual steel roller that becomes an integral and versatile asset in your workshop, enhancing both the process and the products of your metalworking endeavors.
Pricing and Where to Buy Manual Steel Roller
Investing in a manual steel roller is a significant decision for any metalworker, affecting both the quality of work and the efficiency of operations. The market offers a wide range of pricing options, influenced by various factors from construction quality to brand reputation. Understanding these factors, along with knowing the best places to find manual steel rollers for sale, can help you make an informed purchase. Below, we delve into the intricacies of pricing, offer recommendations on where to find these essential tools, and provide tips for ensuring you buy a product that meets your needs in terms of quality, reliability, and warranty.
Overview of Manual Steel Roller Prices and Factors Influencing Cost
The cost of acquiring a manual steel roller is not fixed; it varies widely based on several key factors. Recognizing these can help you budget appropriately and identify the best value for your investment.
- Capacity and Size: The physical capabilities of the roller directly impact its price, with larger, more capable models commanding higher fees.
- Material and Construction: The durability and longevity of a roller are often reflected in its cost, with premium materials fetching higher prices.
- Brand and Manufacturer: Established brands with strong reputations for quality tend to offer their equipment at premium prices, though often with the justification of superior performance and reliability.
- Features and Versatility: Additional functionalities and the ability to handle a variety of bending tasks can also elevate the price of a manual steel roller.
Recommendations for Finding Manual Steel Rollers for Sale
Navigating the market for manual steel rollers requires a strategic approach to uncover the best deals and the most reliable equipment.
- Manufacturer Websites: Direct purchases from manufacturers can sometimes offer the best prices and warranty conditions.
- Industrial Supply Stores: These venues are excellent for comparing different models and brands in one place, whether online or in physical stores.
- Online Marketplaces: A wide selection of both new and used manual steel rollers can be found here, often at competitive prices.
- Auctions and Liquidation Sales: Such events can be goldmines for high-quality equipment at significantly reduced prices.
- Metalworking Forums and Communities: Engaging with these groups can lead to tips on great deals and reputable sellers.
- Trade Shows and Expos: These gatherings provide opportunities to negotiate deals directly with suppliers and manufacturers.
- Local Workshops and Schools: Occasionally, these places sell off older equipment at bargain prices.
- Refurbished Equipment Dealers: Specialized dealers can offer reconditioned equipment that combines quality with affordability.
Tips for Purchasing from Reputable Suppliers and Considerations for Quality and Warranty
Making a wise purchase involves more than just finding the right price; it’s about ensuring the equipment will serve your needs reliably over time.
- Research the Supplier: A reputable supplier is as important as the equipment itself, ensuring you receive a product that lives up to expectations.
- Inspect the Equipment: Whenever possible, a firsthand look at the equipment can provide insight into its condition and suitability for your projects.
- Ask About Warranty: Understanding the warranty offered, whether on new or used equipment, can provide peace of mind and protect your investment.
- Consider After-Sales Support: The availability of support after your purchase can be crucial for resolving any issues that arise.
- Negotiate: There’s often room for negotiation, especially in the used market or when dealing directly with suppliers at trade shows.
- Check for Compatibility: Ensure the manual steel roller fits your specific project needs and material types.
- Safety Features: Prioritize equipment that includes safety measures to protect users during operation.
- Future Needs: Consider whether the equipment can grow with your business or adapt to future project requirements.
By carefully considering these aspects of the purchase process, you can ensure that your investment in a manual steel roller is sound, providing you with a tool that enhances your metalworking capabilities and contributes to the success of your projects for years to come.
Popular Brands and Models of Manual Steel Roller
In the diverse landscape of metalworking tools, the manual steel roller occupies a crucial niche, offering the unique ability to manipulate metal into desired shapes with precision and control. The market boasts a variety of brands and models, each with its own set of features tailored to different metalworking needs. From heavy-duty industrial models to more compact versions for small-scale projects, the range of manual steel rollers available can cater to virtually any requirement. This section aims to shed light on some of the most reputable brands in the industry, known for their commitment to quality and reliability. By exploring selected models from these trusted manufacturers, we provide insights into the capabilities and applications of their manual steel rollers, helping you navigate the options and make an informed choice that aligns with your metalworking projects.
Introduction to Reputable Brands
Several brands stand out in the field of manual steel rollers for their innovation, durability, and performance. These manufacturers have earned their reputation through consistent quality and customer satisfaction:
- Baileigh Industrial: Recognized for its premium quality machinery, Baileigh Industrial offers a range of manual steel rollers designed to meet professional standards.
- Eagle Bending Machines: With a focus on heavy-duty performance, Eagle Bending Machines produces equipment capable of handling rigorous bending tasks with ease.
- Ercolina: Known for versatility and efficiency, Ercolina’s manual steel rollers are favored by professionals for their precision and ease of use.
- Woodward Fab: Catering to hobbyists and small workshops, Woodward Fab combines affordability with quality, making metalworking accessible to a wider audience.
- Harbor Freight: A go-to for budget-conscious buyers, Harbor Freight provides entry-level manual steel rollers that offer good value for light-duty projects.
- JET Tools: Emphasizing durability and user-friendliness, JET Tools’ manual steel rollers are designed to serve both novice and experienced metalworkers.
Highlighting Selected Models
Each of these brands offers models that stand out for their specific features and applications, catering to different segments of the metalworking market:
- Baileigh Industrial R-M10: This model exemplifies Baileigh’s commitment to quality, offering precision bending capabilities in a compact, user-friendly design. It’s ideal for small to medium projects, providing versatility without compromising on performance.
- Eagle Bending Machines CP30: Renowned for its robust construction, the CP30 effortlessly handles a variety of bending tasks. Its durability and reliability make it a preferred choice for professionals requiring high-capacity bending solutions.
- Ercolina TB60: Showcasing Ercolina’s innovative design, the TB60 model offers efficient bending of tubes and pipes with precision. It’s noted for its ease of operation and consistent production of accurate bends.
- Woodward Fab WFB2: For those seeking quality at an affordable price, the WFB2 from Woodward Fab is an excellent choice. Suited for hobbyists and small shops, it provides reliable bending capabilities for light to medium projects.
- Harbor Freight Compact Bender: An economical solution for basic bending needs, this compact bender from Harbor Freight is ideal for beginners and those working on small, non-commercial projects. It represents a practical entry point into metal bending.
- JET Tools JHPB-20: The JHPB-20 is built for durability and ease of use, reflecting JET Tools’ commitment to quality. Suitable for a broad range of bending tasks, it offers precision and reliability for workshops of all sizes.
By familiarizing yourself with the offerings from these reputable brands and understanding the specific features and capabilities of their standout models, you can make a well-informed decision when selecting a manual steel roller. Whether your focus is on professional-grade fabrication or hobbyist projects, the right manual steel roller can significantly enhance the quality and efficiency of your work, making it an invaluable addition to your metalworking toolkit.
DIY Projects and Applications with a Manual Steel Roller
The manual steel roller is not just a tool; it’s a gateway to creativity and innovation in the realm of metalworking. Whether you’re a seasoned professional or a DIY enthusiast, the versatility it offers can transform simple metal sheets into intricate designs and functional pieces. This section delves into the myriad of projects that can be realized with a manual steel roller, ranging from artistic endeavors to practical applications. Additionally, we provide essential tips to help you harness the full potential of this tool, ensuring that your workshop or garage becomes a hub of productivity and creativity.
Ideas for DIY Projects
Embarking on DIY projects with a manual steel roller can be both rewarding and challenging. Here are several project ideas that showcase the tool’s versatility:
- Garden Sculptures: Transform your garden into an art gallery with custom-made metal sculptures, bending and shaping metal to create abstract forms or realistic figures.
- Custom Automotive Parts: Tailor-make automotive parts that require precise curves and angles, enhancing both the functionality and aesthetics of vehicles.
- Metal Furniture: Venture into furniture making by designing pieces with metal elements that offer both strength and elegance.
- Architectural Details: Add a touch of sophistication to buildings with curved metal accents for gates, railings, and balconies.
- Musical Instruments: Explore the creation of musical instrument components, where precision bending can affect the instrument’s sound and performance.
- Light Fixtures: Design unique light fixtures or lamp bases, combining functionality with artistic expression.
- Sports Equipment: Custom-build sports equipment, ensuring durability and customizability for specific needs.
- Artistic Metal Panels: Create eye-catching metal panels for use as wall art or room dividers, experimenting with patterns and shapes.
Tips for Maximizing the Utility of a Manual Steel Roller
To make the most out of your manual steel roller, consider the following tips:
- Understand Material Limits: Knowing the capabilities of your roller is crucial to prevent damage and achieve the best results.
- Regular Maintenance: A well-maintained roller is more reliable and efficient, ensuring longevity and consistent performance.
- Practice Makes Perfect: Experimentation is key to mastering the art of metal bending, allowing you to understand the nuances of different materials.
- Safety First: Prioritizing safety ensures that your creative endeavors are not marred by accidents or injuries.
- Use the Right Accessories: Expanding your tool’s capabilities with accessories can open up new project possibilities.
- Plan Your Projects: A well-thought-out plan can streamline the process, saving time and resources.
- Mark Your Metal: Accuracy in marking leads to precision in the final product, enhancing the quality of your work.
- Leverage Templates: For complex or repetitive designs, templates can be invaluable for maintaining consistency.
- Join a Community: Engaging with a community of like-minded individuals can provide support, inspiration, and valuable insights.
The manual steel roller is a powerful ally in the world of metalworking, offering endless possibilities for creative and functional projects. By understanding its capabilities and applying these tips, you can unlock new dimensions of craftsmanship, turning raw materials into masterpieces of metalwork. Whether for personal satisfaction or professional advancement, the projects and applications achievable with a manual steel roller are limited only by your imagination.
Maintenance and Safety Tips for Manual Steel Roller
Owning a manual steel roller comes with the responsibility of regular maintenance and adherence to safety guidelines to ensure its longevity and optimal performance. Proper care not only extends the life of your equipment but also safeguards the operator from potential hazards. In this section, we delve into the essential maintenance practices and safety tips that are crucial for anyone operating a manual steel roller. By following these guidelines, you can maintain the efficiency of your tool and create a safer working environment.
Best Practices for Maintaining Manual Steel Rollers
- Regular Cleaning: After each use, clean your manual steel roller to remove any metal shavings, dust, or debris that could accumulate and cause wear over time.
- Lubrication: Apply lubricant to moving parts regularly to ensure smooth operation and prevent rust. Use a lubricant that’s suitable for metalworking equipment.
- Check for Wear and Tear: Inspect your roller for signs of wear, especially on the rollers and moving parts. Early detection of wear can prevent further damage.
- Tighten Loose Bolts and Nuts: Periodically check and tighten any bolts and nuts that may have loosened due to vibration during operation.
- Store Properly: When not in use, store your manual steel roller in a dry, covered area to protect it from moisture and dust.
- Follow Manufacturer’s Guidelines: Adhere to the maintenance schedule and recommendations provided by the manufacturer to ensure optimal performance.
- Seek Professional Repair: If you encounter any issues beyond basic maintenance, consult with a professional for repairs to avoid causing further damage.
Safety Guidelines While Operating Manual Steel Rollers
- Wear Protective Gear: Always wear appropriate safety equipment, including gloves, safety glasses, and steel-toed boots, to protect against injuries.
- Keep Hands Clear: Ensure that your hands and fingers are clear of the rollers and moving parts while operating the machine.
- Secure the Workpiece: Properly secure the metal being worked on to prevent it from slipping or causing injury.
- Maintain a Clean Workspace: Keep the area around the manual steel roller clear of clutter, tools, and debris to prevent tripping or other accidents.
- Be Aware of Your Surroundings: Be conscious of others in the vicinity while operating the roller to avoid accidental contact with the machine.
- Use the Equipment Properly: Operate the manual steel roller according to the manufacturer’s instructions and for its intended use only.
- Avoid Distractions: Stay focused on the task at hand while using the roller. Distractions can lead to mistakes and potential injuries.
- Regularly Inspect Safety Features: Check any safety guards or features for proper function and integrity. Replace or repair any components that are not in optimal condition.
By implementing these maintenance and safety practices, users of manual steel rollers can ensure that their equipment remains in top condition, reducing the risk of breakdowns and extending its lifespan. Moreover, adhering to these safety guidelines minimizes the risk of accidents and injuries, making the metalworking process safer and more enjoyable. Whether you’re a seasoned professional or a DIY enthusiast, taking care of your manual steel roller and operating it safely are paramount to achieving the best results in your metalworking projects.
FAQs about Manual Steel Roller
Using a manual sheet metal roller involves several steps to ensure precise and effective bending of metal sheets. First, you need to prepare your metal sheet by measuring and marking the areas where bends are required. Once ready, adjust the roller’s settings according to the thickness and width of your metal sheet. This usually involves setting the back roll to the desired radius and adjusting the front roll to control the bending process.
Begin by feeding the edge of the metal sheet into the roller. For most manual rollers, you’ll operate the machine using a hand crank or wheel, which moves the metal through the rollers. Apply steady pressure as you turn the crank, guiding the metal through to create the bend. It’s important to feed the metal through at a consistent rate to ensure an even bend.
After the initial pass, you may need to adjust the roller settings and pass the metal through multiple times to achieve the desired curvature. Always wear appropriate safety gear, such as gloves and eye protection, to prevent injuries. With practice, you’ll gain a better understanding of how different metals react to the bending process and how to adjust the roller settings for optimal results.
Manual roller bending machines offer several advantages, making them a valuable tool in metalworking. Firstly, they are cost-effective compared to their powered counterparts, making them accessible to hobbyists, small workshops, and educational settings. Their manual operation eliminates the need for electricity, reducing operational costs and allowing them to be used in any setting.
Another significant advantage is their simplicity and ease of use. Manual rollers require minimal training to operate, making them suitable for beginners while still offering the precision and control needed for complex projects. They are also highly versatile, capable of bending a wide range of metals and thicknesses, from thin sheets to thicker bars, depending on the model.
Portability is another benefit, as many manual bending machines are compact and lightweight, allowing for easy relocation within a workshop or to different job sites. Additionally, manual machines offer a direct feel for the bending process, giving the operator greater control over the outcome, which can be particularly beneficial for custom or artistic metalworking projects.
A metal roller, specifically designed for bending and shaping metal, is used in various applications across industries. Its primary function is to curve and bend metal sheets, bars, and tubes into specific shapes and angles required for manufacturing, construction, and artistic projects. Metal rollers are indispensable in creating components for automotive, aerospace, architectural, and decorative purposes.
In automotive and aerospace industries, metal rollers help in fabricating body parts, frames, and structural components that require precise curves and angles. In construction, they are used to produce metal beams, roofing, and decorative ironwork that form the backbone of buildings and infrastructure. Artisans and sculptors also rely on metal rollers to create intricate designs and sculptures, demonstrating the tool’s versatility in both industrial and creative applications.
Using a sheet metal rolling machine involves several key steps to ensure the successful bending of metal sheets. Start by determining the size and thickness of the sheet metal you intend to bend, as this will influence the machine’s settings. Adjust the roller’s spacing and tension to accommodate the metal sheet’s thickness, ensuring it’s snug but not overly tight, to prevent damage to the material.
Carefully feed the edge of the metal sheet into the machine, aligning it with any pre-marked lines or measurements for accuracy. Begin rolling the sheet through the machine by turning the handle or activating the mechanism, depending on the model. Apply steady pressure and guide the sheet through the rollers, adjusting the machine as necessary to achieve the desired curve or bend.
For complex shapes or tighter curves, it may be necessary to pass the sheet through the machine multiple times, adjusting the settings incrementally to refine the shape. Always wear appropriate safety gear, such as gloves and eye protection, to prevent injuries during operation. With practice, using a sheet metal rolling machine becomes a straightforward process, allowing for the efficient and precise bending of metal sheets for a variety of applications.
Last Updated on February 22, 2024 by Jordan Smith
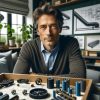
Jordan Smith, a seasoned professional with over 20 years of experience in the conveyor system industry. Jordan’s expertise lies in providing comprehensive solutions for conveyor rollers, belts, and accessories, catering to a wide range of industrial needs. From initial design and configuration to installation and meticulous troubleshooting, Jordan is adept at handling all aspects of conveyor system management. Whether you’re looking to upgrade your production line with efficient conveyor belts, require custom conveyor rollers for specific operations, or need expert advice on selecting the right conveyor accessories for your facility, Jordan is your reliable consultant. For any inquiries or assistance with conveyor system optimization, Jordan is available to share his wealth of knowledge and experience. Feel free to reach out at any time for professional guidance on all matters related to conveyor rollers, belts, and accessories.