Material Handling Roller Conveyor Maintenance Tips
Material handling systems are integral to the efficient operation of various industrial sectors, facilitating the smooth movement and storage of goods. Among these systems, the material handling roller conveyor stands out due to its versatility and efficiency. Roller conveyors are particularly significant because they enhance the automation and speed of production lines, distribution centers, and warehouses. They consist of rollers mounted in series, enabling the easy and quick transportation of heavy or bulky items across a facility. This technology not only streamlines operations but also minimizes labor costs and improves workplace safety. By focusing on the role of roller conveyors, industries can achieve more streamlined processes, leading to increased productivity and operational efficiency. This introduction explores the pivotal role these conveyors play in modern manufacturing and logistics environments.
The Basics of Roller Conveyors
Roller conveyors are fundamental components in material handling systems, enabling the automated and manual transportation of goods across various facilities. This section delves into the basic types of roller conveyors, focusing on gravity roller conveyors, and details their components and variations.
What is a Gravity Roller Conveyor?
A gravity roller conveyor is a type of material handling roller conveyor that uses the force of gravity to move items across a downward-sloping surface. This system is devoid of any motor or external power source, making it energy-efficient and cost-effective. The principle of operation involves placing objects on rollers which are set at a slight decline or manually pushed to initiate movement.
Gravity roller conveyors play a crucial role in material handling by facilitating the smooth movement of goods, especially in warehousing, distribution centers, and assembly lines.
- Loading and unloading trucks in shipping docks.
- Moving boxes through sorting areas in postal handling facilities.
- Transporting luggage at airports from check-in to baggage handling.
- Assembling lines in manufacturing plants for easy movement of parts.
- Streamlining the packaging process in food processing industries.
Key Components of Roller Conveyors
Understanding the key components of material handling roller conveyors is essential for optimizing their efficiency and durability. Here are the major parts:
Conveyor Rollers
Conveyor rollers are the cylindrical components that facilitate the movement of materials. They vary widely based on:
- Materials Used: Steel (for durability), plastic (for light weight), rubber-coated (for grip and noise reduction).
- Types: Tapered rollers (for curves), impact rollers (for absorbing shocks), and return rollers (for supporting the belt from the bottom).
Five examples of conveyor rollers include:
- Stainless steel rollers for corrosive environments like chemical plants.
- Polyurethane coated rollers for delicate surfaces to prevent damage.
- Grooved rollers for ensuring belt tracking in powered conveyor systems.
- High-temperature rollers for ovens and paint drying lines.
- Adjustable rollers for varying the width of the conveyor for different product sizes.
Roller Conveyor Table
The roller conveyor table refers to the framework that houses the rollers. It is crucial for supporting the conveyor system and can be customized to fit various operational needs. Key uses include:
- Adjustable height features for ergonomic handling.
- Mobile frames with casters for repositioning within a facility.
- Expandable sections for temporary increased capacity needs.
Five examples of roller conveyor table uses:
- In assembly lines to adjust the conveyor to the optimal height for workers.
- In retail backrooms for flexible goods handling.
- At packaging stations to accommodate different package sizes.
- For loading zones in warehouses to move goods between different areas.
- In sorting facilities to reconfigure layouts based on seasonal demands.
Heavy-duty Conveyor Rollers
Heavy-duty conveyor rollers are designed to handle higher loads and more intensive use than standard rollers. They typically feature thicker tubing and larger bearings. Specifications for heavy-duty rollers include higher load capacities, better impact resistance, and enhanced durability, suitable for industries like mining, heavy manufacturing, and bulk material handling.
Types of Roller Conveyors
Roller conveyors can be classified primarily into gravity and powered systems, each serving different operational needs.
Gravity Roller Conveyor
- Use: Best for lightweight packages and when low-cost material handling solutions are preferred.
- Advantages: Energy efficiency, low cost, and simplicity of design.
- Design Considerations: Slope, roller diameter, and load capacity need to be adjusted based on the application.
Powered Roller Conveyor
- Use: Ideal for heavy loads that require controlled movement, such as in automotive industries.
- Advantages: Can move large volumes of goods consistently with speed control.
- Design Considerations: Power requirements, motor placement, and control systems like sensors and automated guides.
A comparative table would display each type’s key characteristics side by side to aid in decision-making based on specific material handling requirements.
Applications of Material Handling Roller Conveyors
Material handling roller conveyors are versatile and essential tools in a wide array of industries, where they enhance efficiency and streamline the transport and handling of goods. This section highlights the diverse applications of these systems and provides detailed examples of scenarios where both gravity and powered roller conveyors play pivotal roles.
Material handling roller conveyors facilitate operations in countless environments, ranging from delicate electronic assembly lines to rugged industrial settings. Here are five key industries where roller conveyors are extensively used:
- Manufacturing: In automotive manufacturing, material handling roller conveyors transport parts between assembly stations, significantly reducing manual handling and speeding up the production line.
- Distribution and Logistics: E-commerce fulfillment centers use roller conveyors to sort and manage vast quantities of packages, ensuring that products are swiftly and accurately dispatched to customers.
- Food and Beverage: Conveyors in food processing plants move products through various stages of production, from initial processing to packaging, maintaining hygiene and efficiency.
- Pharmaceuticals: Roller conveyors are used in pharmaceutical manufacturing to transport sensitive materials through controlled environments, minimizing human contact and contamination risks.
- Airports: Baggage handling systems rely on gravity and powered roller conveyors to efficiently sort and deliver luggage to the correct flights, enhancing traveler satisfaction by reducing wait times and handling errors.
Example Scenarios Where Roller Conveyors Optimize Workflow and Efficiency
The functionality of material handling roller conveyors can be illustrated through various scenarios across different settings:
- Gravity Roller Conveyor in Retail Stockrooms: These conveyors are used to expedite the process of moving stock from delivery trucks to storage areas or to the sales floor, enabling quicker shelf stocking and more efficient use of staff resources.
- Powered Roller Conveyor in Automotive Assembly: In this scenario, powered roller conveyors transport car components along the assembly line. Each station along the line is designed to perform specific tasks, and the precise control of the conveyor speeds ensures a seamless assembly process.
- Gravity Roller Conveyor in Postal Sorting Facilities: Postal facilities utilize gravity roller conveyors to sort and route packages. As packages are loaded onto the conveyor, they naturally flow towards sorting bins, which are designated for various delivery routes, simplifying the sorting process.
- Powered Roller Conveyor in Electronics Manufacturing: These conveyors are used to gently transport delicate electronic devices, such as smartphones and tablets, through different stages of assembly. The controlled movement prevents damage to the sensitive components.
- Heavy-Duty Powered Roller Conveyor in Mining Operations: In mining, heavy-duty powered roller conveyors are crucial for moving large volumes of mined material over long distances. The robust design of these conveyors handles the heavy load and abrasive nature of mined ores and rocks, ensuring reliability and efficiency in harsh conditions.
Each of these examples showcases how material handling roller conveyors not only improve operational efficiency but also adapt to the specific needs of various industries, demonstrating their indispensable role in modern industrial and commercial environments.
Advantages of Implementing Material Handling Roller Conveyor in Operations
Implementing material handling roller conveyors in industrial and commercial settings brings numerous advantages, significantly enhancing operational efficiency, improving safety, and reducing costs. These systems are engineered to streamline the movement of goods through various stages of production and distribution, proving essential in numerous sectors.
Improved Safety
Material handling roller conveyors reduce the need for manual handling of goods, which decreases the risk of injuries related to lifting and moving heavy items. This automation not only protects workers from potential strains and accidents but also leads to a more organized workflow that minimizes hazards associated with human error and workplace clutter.
Increased Efficiency
The use of material handling roller conveyors facilitates a smoother, faster flow of materials. By automating the transport processes, businesses can ensure that goods are moved through production or distribution environments more swiftly and with less downtime. This increase in efficiency can lead to higher output rates and faster delivery times, which are critical in meeting consumer demands and maintaining competitive edges.
Cost Reduction
Roller conveyors are a cost-effective solution for many industries. They decrease the need for extensive manual labor, thereby reducing labor costs. Additionally, the robust design and minimal need for maintenance contribute to long-term savings. Energy costs are also lowered, especially with gravity roller conveyors that operate without power.
Advantages of Heavy-Duty Gravity Roller Conveyors
Heavy-duty gravity roller conveyors are specially designed to handle large and heavy materials, providing several specific advantages in industrial applications where robustness and durability are required. Here are five examples demonstrating the benefits of these conveyors in handling weighty materials:
- Mining and Quarrying: In mining operations, heavy-duty gravity roller conveyors transport large volumes of raw extracted materials such as ores and minerals. The rugged construction of these conveyors withstands the abrasive nature of such materials, reducing wear and maintenance requirements.
- Metal Manufacturing: Facilities dealing with metal fabrication and processing utilize these conveyors to move large metal parts and scrap. The high load capacity of heavy-duty rollers ensures that they can handle the substantial weight of metal products without faltering.
- Construction Material Handling: For transporting building materials like cement, bricks, or tiles, heavy-duty gravity roller conveyors provide a reliable means of movement from production to shipping areas. Their robust design prevents damage to the conveyor system under the heavy loads of construction materials.
- Automotive Assembly Lines: In the automotive industry, these conveyors are used to transport chassis and other heavy automobile components through the assembly line. Their ability to handle significant weights aids in maintaining a seamless and efficient assembly process.
- Warehouse and Distribution Centers: Heavy-duty conveyors are vital in warehouses for moving large and heavy goods such as appliances, furniture, or bulk containers. They enhance the efficiency of operations by allowing quick, effortless movement of heavy items across large spaces.
By integrating material handling roller conveyors into their operations, industries benefit from improved safety, enhanced efficiency, and substantial cost savings, all while handling a diverse range of material types and weights effectively. These advantages make roller conveyors an indispensable tool in modern manufacturing and distribution processes.
Buying Guide: New Vs. Used Material Handling Roller Conveyor
When investing in a material handling roller conveyor, choosing between new and used models is a significant decision that can impact both operational efficiency and budget. This section provides detailed guidance on what to consider when purchasing new versus used roller conveyors, including key tips and sourcing strategies.
Material Handling Roller Conveyor for Sale
Purchasing a new material handling roller conveyor offers several benefits, including the latest technology, warranty coverage, and the assurance of longevity and minimal wear. Here are key tips and considerations when looking to buy a new roller conveyor:
- Determine Specifications: Identify the size, load capacity, and type of roller conveyor (gravity or powered) that best suits your operational needs. Ensure the conveyor matches your product dimensions and weight requirements.
- Consider Customization Options: Many vendors offer customizable conveyor systems that can be tailored to specific operational needs, such as adjustable heights, motorized rollers, or specific roller materials like polyurethane for delicate handling.
- Evaluate Technology Integration: For advanced operations, consider roller conveyors with integrated technologies such as sensors, automated tracking systems, or programmable logic controllers (PLCs) that can optimize throughput and efficiency.
- Research Vendors: Look for reputable manufacturers known for quality and service. Some leading vendors include Hytrol, Dematic, and Interroll. Check their product range, support services, and customer reviews.
- Warranty and Support: Always check the warranty terms and what it covers. A good warranty can save costly repairs and maintenance down the line. Also, ensure the vendor offers adequate after-sales support and parts availability.
Used Material Handling Roller Conveyor
Opting for a used material handling roller conveyor can be a cost-effective choice, especially for businesses with limited budgets or those looking for short-term solutions. Here’s how to ensure you make a wise purchase:
- Assess the Condition: Examine the conveyor’s wear and tear. Check for rust, damage to the rollers, and the condition of the belt or frame. Ask about the age of the conveyor and its previous usage to gauge expected longevity.
- Ask for Maintenance Records: Reliable sellers should provide maintenance logs that detail past repairs and routine upkeep. This information can indicate how well the conveyor has been cared for and what issues might arise.
- Consider Retrofitting: Sometimes, used conveyors may need updates or modifications to fit your needs. Calculate these costs upfront to determine if the purchase is still cost-effective.
- Source from Reputable Dealers: Purchase from known and trusted sources that specialize in used material handling equipment. Companies like Surplus Industrial Supply and American Surplus are known for their extensive inventories and credibility.
- Inspect in Person or Virtually: If possible, inspect the conveyor in person or request a video inspection to check its operational state. This can prevent surprises and ensure you get a system that meets your expectations.
By considering these tips and strategies for both new and used material handling roller conveyors, businesses can make informed decisions that align with their operational requirements and budget constraints, ensuring that they invest in a conveyor system that will serve their needs efficiently and effectively.
Diving Deeper: Material Handling Roller Conveyor Parts and Maintenance
Understanding the components and maintenance needs of a material handling roller conveyor is crucial for ensuring its operational efficiency and longevity. This section delves into the essential parts of a roller conveyor, the different types of rollers available, and provides tips for regular maintenance.
Roller Conveyor Parts
The efficiency and functionality of a material handling roller conveyor rely heavily on its various components. Here’s an overview of the essential parts and their functions:
- Rollers: These are the primary moving parts that carry the load. They are typically cylindrical and rotate on their axes to facilitate the movement of materials.
- Frame: This structure supports the rollers and can be made from materials such as steel or aluminum, depending on the required strength and environmental considerations.
- Motor (for powered conveyors): Powers the rollers to move the materials along the conveyor. Motors can vary in size and power depending on the conveyor’s length and load capacity.
- Bearings: Reduce friction between the rollers and the frame, allowing smooth operation. Bearings need to be properly sealed to prevent dust and debris from causing wear.
- Drive Belts (for powered conveyors): Transmit power from the motor to the rollers. These need to be durable and are typically made from rubber or a rubber composite.
Conveyor Roller Types
Choosing the right type of roller is vital for optimizing the performance of a material handling roller conveyor. Here is a detailed look at various roller types and their applications:
- Gravity Rollers: Best used for light to medium loads where the conveyor is inclined or manually pushed.
- Grooved Rollers: Designed to interface with round belts on powered roller conveyors, often used in lightweight applications.
- Sprocketed Rollers: Feature sprockets that engage with a chain in powered conveyor systems, ideal for heavy loads.
- Tapered Rollers: Used on curves and corners of the conveyor system to maintain the orientation and alignment of packages.
- Impact Rollers: Located at conveyor loading and transfer points, they are designed to absorb the impact and reduce the wear on the conveyor.
Each type of roller has specific properties suited to different operational environments and requirements, ensuring the conveyor is tailored to the task at hand.
Regular Maintenance Tips
Regular maintenance is key to prolonging the efficiency and reliability of a material handling roller conveyor. Here are some simple maintenance steps:
- Regular Inspections: Perform frequent visual and manual checks to identify any signs of wear or damage such as cracks, misalignment, or accumulation of debris.
- Lubrication: Regularly lubricate bearings and rollers to ensure smooth operation. Use the correct type of lubricant as recommended by the manufacturer.
- Cleaning: Keep the conveyor clean from dust, dirt, and debris which can cause premature wear. Cleaning schedules should depend on the environment and usage levels.
- Tighten and Adjust: Regularly check and tighten any loose bolts and adjust rollers to ensure they are correctly aligned. Misalignment can lead to uneven wear and operational issues.
- Replace Worn Parts: Replace rollers, bearings, and belts as soon as they show signs of wear to prevent breakdowns and maintain performance.
Implementing these maintenance tips can greatly increase the lifespan and functionality of your material handling roller conveyor, leading to improved productivity and reduced downtime.
Incorporating Advanced Features in Material Handling Roller Conveyors
Enhancing material handling roller conveyors with advanced features can significantly increase their efficiency, accuracy, and integration capabilities. Modern conveyor systems can be equipped with a variety of sophisticated technologies that automate operations and improve the handling processes. Here, we explore some key advanced features that can be incorporated into material handling roller conveyors.
Sensors
Sensors play a crucial role in modern roller conveyors, enabling real-time tracking and control of the goods being transported. Types of sensors commonly used include:
- Photoelectric Sensors: Detect the presence, position, and size of products as they pass through the conveyor, enabling precise control over the sorting and distribution processes.
- Pressure Sensors: Monitor the weight of the products on the conveyor, ensuring that the load does not exceed the system’s capacity.
- Proximity Sensors: Used to detect the position of objects and adjust the speed of the conveyor to prevent collisions, especially in high-speed environments.
Automation
Automation is another significant feature that enhances the performance of material handling roller conveyors by reducing manual intervention and improving throughput.
- Automated Sorting Systems: Integrated with sensors, these systems can automatically sort products based on size, weight, or barcode information, directing them to different areas without human intervention.
- Automated Loading and Unloading: Conveyors can be equipped with robotic arms that automatically load and unload goods, reducing labor costs and increasing safety.
Integration with Other Handling Systems
For maximum efficiency, material handling roller conveyors can be integrated with other automated systems within a facility.
- Warehouse Management Systems (WMS): Integration with WMS allows for seamless data exchange, improving inventory management and reducing errors by aligning the conveyor operations with real-time inventory levels.
- Manufacturing Execution Systems (MES): This integration ensures that the material handling roller conveyor is synchronized with the production schedules, enhancing just-in-time manufacturing processes.
Advanced Controls
Sophisticated control systems are essential for optimizing the performance of roller conveyors, enabling precise adjustments to operations based on real-time data.
- Programmable Logic Controllers (PLC): These controllers can manage the entire conveyor system, adjusting speeds, starting and stopping sections of the conveyor as needed, based on the input from sensors and other data points.
- Human-Machine Interfaces (HMI): HMIs allow operators to monitor and control the conveyors from a central location, providing insights into performance metrics and diagnostics for quick troubleshooting.
By incorporating these advanced features into material handling roller conveyors, businesses can achieve a higher level of automation, reduce the need for manual labor, enhance safety, and ensure a high degree of integration with other systems. These improvements not only boost operational efficiency but also significantly contribute to the overall productivity and scalability of material handling operations.
FAQs About Material Handling Roller Conveyor
Roller conveyors are designed to facilitate the efficient transport of goods across various industrial environments, and they can be constructed from several different materials, each selected based on the specific needs of the application. The most commonly used materials include steel, aluminum, and plastic. Steel rollers are favored for their strength and durability, making them suitable for heavy loads and harsh conditions. Aluminum rollers offer a lighter alternative, beneficial in operations where weight is a concern, such as in manual handling or when the conveyor needs to be repositioned frequently. Plastic rollers are typically used for lighter loads and are valued for their quiet operation and corrosion resistance, which is particularly useful in environments where moisture or chemical exposure is an issue. Each material offers distinct advantages, and the choice depends on factors such as load weight, environmental conditions, and cost considerations.
Material handling conveyors are mechanical systems designed to transport materials, products, or goods efficiently from one location to another within a facility or between facilities. These conveyors are integral to numerous industrial sectors, including manufacturing, warehousing, distribution, and retail. They help streamline operations by automating the movement of materials, which reduces manual labor, improves safety, and increases efficiency. Material handling conveyors come in various types, including belt conveyors, roller conveyors, overhead conveyors, and pallet conveyors, each suited to specific tasks and operational environments. The use of these conveyors allows businesses to handle large volumes of goods quickly and with minimal human intervention, which can significantly enhance operational throughput and reduce costs.
The material handling capacity of a conveyor refers to the maximum load that it can transport effectively over a given period. This capacity is usually measured in tons per hour (tph) or kilograms per hour and is a critical factor in the design and selection of a conveyor system. The capacity depends on several factors including the type of conveyor, the width and speed of the belt or rollers, the motor’s power, and the physical properties of the materials being handled. For instance, heavier and bulkier materials may require a conveyor system with stronger motors and more robust construction. Ensuring that a conveyor is designed with adequate capacity is essential for preventing system overloads, which can lead to breakdowns and reduce the lifespan of the equipment.
The rollers on a conveyor are cylindrical components that rotate to move the conveyor belt or the materials placed directly on the rollers. They are a crucial part of roller conveyor systems and can be designed to handle various weights and types of materials. Rollers are spaced evenly along the length of the conveyor frame to support and propel the belt or items as needed. They can be made from metal, such as steel or aluminum, or from synthetic materials like plastic, depending on the application requirements. Rollers can also be specialized, such as grooved rollers for belt tracking, impact rollers for absorbing shocks, or tapered rollers for curves. The selection and maintenance of the rollers are vital to the efficient operation of the conveyor system, affecting both the movement efficiency and the longevity of the conveyor.
Last Updated on August 6, 2024 by Jordan Smith
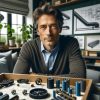
Jordan Smith, a seasoned professional with over 20 years of experience in the conveyor system industry. Jordan’s expertise lies in providing comprehensive solutions for conveyor rollers, belts, and accessories, catering to a wide range of industrial needs. From initial design and configuration to installation and meticulous troubleshooting, Jordan is adept at handling all aspects of conveyor system management. Whether you’re looking to upgrade your production line with efficient conveyor belts, require custom conveyor rollers for specific operations, or need expert advice on selecting the right conveyor accessories for your facility, Jordan is your reliable consultant. For any inquiries or assistance with conveyor system optimization, Jordan is available to share his wealth of knowledge and experience. Feel free to reach out at any time for professional guidance on all matters related to conveyor rollers, belts, and accessories.